Choosing the Best Rubber Conveyor Rollers
In the realm of material handling and manufacturing, rubber conveyor rollers stand out as pivotal components that significantly bolster operational efficiency across various industries. These rollers, central to the mechanics of conveyor systems, facilitate the smooth and efficient transport of goods and materials, minimizing friction and wear. The significance of rubber conveyor rollers extends beyond their basic function of movement; they are instrumental in reducing operational noise, enhancing safety, and ensuring the longevity of conveyor belts through their gentle yet firm grip. Employed in sectors ranging from food processing to heavy manufacturing, these rollers adapt to different environmental conditions and loads, underscoring their versatility and critical role in industrial operations. By optimizing the conveyor systems that are the lifelines of production lines, rubber conveyor rollers play an indispensable part in maintaining the continuous flow of operations, thereby directly impacting productivity and operational cost-effectiveness.
The Role of Rubber Conveyor Rollers in Material Handling
What Are Rubber Conveyor Rollers?
Rubber conveyor rollers are cylindrical components made from a core, usually metal or plastic, that is coated with a rubber exterior. This rubber coating is designed to grip and move materials along conveyor systems with minimal slippage, reducing damage to both the materials being transported and the conveyor belt itself. The resilience and durability of the rubber allow these rollers to provide a smooth, efficient movement across a wide range of conditions and temperatures, making them a versatile choice for many industries. From moving delicate items in a packaging facility to handling rough materials in a mining operation, rubber conveyor rollers are essential for efficient operations.
Importance in Various Industries
The utility of rubber conveyor rollers is evident across various sectors due to their ability to enhance process efficiency and safety.
- Manufacturing: In the manufacturing industry, rubber conveyor rollers are crucial for the assembly lines, where they transport parts and finished products smoothly. Their ability to absorb vibrations helps in handling fragile items without causing damage.
- Food Processing: The food processing industry benefits from these rollers due to their compliant nature, which is essential for maintaining hygiene and preventing contamination. The rubber material is easy to clean and can be made to resist food acids, fats, and oils.
- Packaging: Rubber conveyor rollers ensure that packaging materials are handled delicately to prevent damage. Their grip reduces slippage of items, ensuring accurate and efficient packaging processes.
- Mining and Quarrying: In the harsh environments of mining and quarrying, these rollers offer durability and resistance to abrasion, chemicals, and temperature variations, making them ideal for conveying raw materials.
- Logistics and Distribution: These sectors rely on rubber conveyor rollers for the sorting, loading, and unloading of goods. The rollers’ shock-absorbing properties minimize damage during handling, thereby optimizing the distribution process.
In each of these industries, rubber conveyor rollers play an integral role in streamlining operations, enhancing productivity, and reducing operational costs. Their adaptability to various environmental conditions and ability to handle a wide range of materials make them an indispensable component of modern material handling systems.
Types and Benefits of Rubber Conveyor Rollers
Types of Rubber Rollers
Rubber conveyor rollers come in various designs and materials to suit different industrial needs, including:
- Standard Rubber Rollers: These are the most commonly used rollers, suitable for general material handling needs. They are versatile, affordable, and effective in various applications.
- Heavy-Duty Rubber Rollers: Designed for environments where durability and strength are paramount. These rollers can handle heavier loads and more abrasive conditions, making them ideal for mining and construction industries.
- Food-Grade Rubber Rollers: Specifically manufactured for the food processing industry, these rollers meet strict hygiene standards. They are resistant to oils, fats, and cleaning chemicals.
- Temperature-Resistant Rubber Rollers: Made with special rubber compounds that can withstand extreme temperatures, both high and low. These are essential in industries like metalworking and plastics manufacturing, where temperatures can vary widely.
- Anti-Static Rubber Rollers: Essential in industries where static electricity could pose a hazard or affect sensitive materials. They help to safely dissipate static charges during the conveyor process.
Advantages of Rubber Coatings
Rubber-coated drive rollers offer several advantages over their conventional counterparts, significantly enhancing their application and longevity. Below is a comparative table highlighting the benefits of rubber coatings:
Feature | Rubber-Coated Rollers | Conventional Materials |
---|---|---|
Grip and Traction | High grip reduces slippage, improving efficiency. | Lower grip can lead to slippage and inefficiency. |
Noise Reduction | The rubber material absorbs sound, reducing operational noise. | Harder materials tend to be noisier. |
Durability | Resistant to wear and tear, extending lifespan. | More prone to damage and wear. |
Shock Absorption | Provides cushioning, reducing impact on materials handled. | Less cushioning, potentially damaging goods. |
Chemical Resistance | Can be formulated to resist various chemicals. | May degrade when exposed to certain chemicals. |
Temperature Resistance | Withstands extreme temperatures without degrading. | May warp or crack under extreme conditions. |
These advantages underscore why rubber conveyor rollers are favored in many industries. Their grip and traction capabilities ensure materials are moved efficiently without slippage, enhancing productivity. The noise reduction properties of rubber improve the work environment, making it safer and more pleasant for personnel. Moreover, the durability and shock absorption provided by rubber coatings protect both the conveyor system and the materials being transported, leading to reduced maintenance costs and longer service life. Chemical and temperature resistance further ensures that rubber conveyor roller can be used in a variety of environments without degrading, offering a versatile solution to many material handling challenges.

Choosing the Right Rubber Conveyor Rollers
Selecting the appropriate rubber conveyor roller is critical for ensuring operational efficiency, longevity, and cost-effectiveness of your material handling system. Here are important considerations to guide your selection process.
Price Considerations
The cost of rubber conveyor rollers can vary widely based on several factors. Understanding these can help you budget effectively and choose the best option for your needs:
- Material Quality: Higher quality rubber materials that offer better durability and resistance to wear, chemicals, and temperature extremes typically cost more.
- Customization: Custom-designed rollers to fit specific operational needs or non-standard sizes can increase the price.
- Quantity: Ordering in bulk often reduces the per-unit cost, making large orders more economical.
- Manufacturer: Prices can vary significantly between manufacturers based on their production methods, materials used, and brand reputation.
- Technical Features: Additional features like anti-static properties, food-grade certifications, or temperature resistance can add to the cost.
Identifying Heavy Duty Options
For operations that demand the utmost in durability and performance, heavy-duty rubber conveyor rollers are essential. Characteristics to look for include:
- Thicker Rubber Coating: Provides extra protection against wear and tear, ideal for handling abrasive materials.
- Reinforced Core: A stronger core material, like steel, ensures the roller can support heavier loads without deforming.
- High-Quality Bearings: Ensures smooth operation under heavy loads and reduces maintenance needs.
- Chemical Resistance: Necessary for environments where the rollers may be exposed to corrosive substances.
- High-Temperature Tolerance: Essential for operations involving heat, ensuring the rubber does not degrade prematurely.
These rollers are particularly useful in industries like mining, construction, and metal processing, where the demands on material handling systems are rigorous.
Near Me: Finding the Right Supplier
Locating a reliable supplier of high-quality rubber conveyor rollers requires consideration of several factors:
- Local Manufacturers: Start by searching for manufacturers within your region to save on shipping costs and facilitate easier communication and site visits.
- Industry Reputation: Look for suppliers with positive reviews and testimonials from businesses in similar industries.
- Product Range: Choose a supplier with a wide range of products and the ability to provide custom solutions if needed.
- Technical Support: A supplier that offers comprehensive technical support can assist with selecting the right rollers and provide maintenance tips.
- After-Sales Service: Consider suppliers who offer good warranty terms and after-sales service to address any issues that may arise post-purchase.
By carefully considering these factors, you can ensure that you select the right conveyor roller rubber for your operations, balancing cost, performance, and durability to meet your specific needs.
Attributes of High-Quality Rubber Conveyor Rollers
High-quality rubber conveyor rollers are integral to the efficiency and longevity of conveyor systems. Understanding the key attributes that define their quality can significantly impact your operations’ productivity and maintenance costs.
Rubber Rollers with Bearings
The incorporation of bearings into rubber rollers is critical for their functionality, affecting performance in several ways:
- Reduced Friction: High-quality bearings minimize friction between the roller and its axle, allowing smoother rotation and reducing energy consumption.
- Increased Load Capacity: Bearings distribute the load more evenly across the roller, enhancing its ability to handle heavier materials without deformation or failure.
- Enhanced Durability: Quality bearings can significantly extend the life of rubber conveyor rollers by protecting against wear and tear, even in high-speed applications.
- Lower Maintenance Needs: Rollers equipped with superior bearings require less maintenance, as they are less prone to breakdowns and wear-related issues.
- Improved Precision: Bearings ensure that the roller moves precisely along its intended path, crucial for applications where material alignment and placement are key.
These factors underscore the importance of selecting rubber conveyor rollers with high-quality bearings for any application where efficiency and reliability are paramount.

Rubber Drive Roller Design
The design of rubber drive rollers is another critical aspect that influences their performance.
- Rubber Material Composition: The type of rubber and its compound can affect the roller’s grip, resistance to chemicals, temperature, and abrasion. Selecting the right rubber material is crucial for specific operational environments.
- Surface Texture: The surface texture of the roller can be customized to match the application’s needs—smooth for gentle handling of delicate items, or textured for increased grip on slippery materials.
- Core Material and Construction: The core material, whether metal or plastic, and its construction, affects the roller’s strength and weight. A strong, lightweight core improves efficiency and reduces wear on the conveyor system.
- Dimensional Accuracy: Precision in the roller’s dimensions ensures it fits perfectly within the conveyor system, maintaining alignment and reducing the risk of malfunctions.
- Balance: A well-balanced roller minimizes vibration and uneven wear, extending the lifespan of both the roller and the conveyor system.
High-quality rubber conveyor rollers that combine the right bearings and thoughtful design considerations offer superior performance and durability, significantly impacting the overall efficiency of conveyor systems.
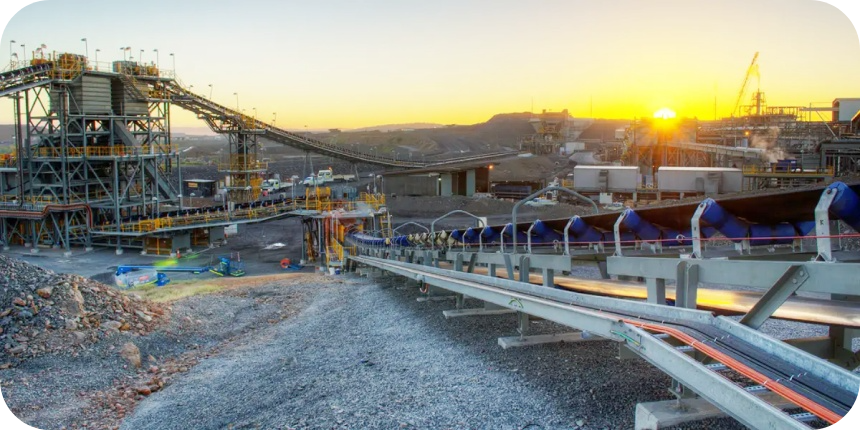
Purchasing Rubber Conveyor Rollers
Selecting the right rubber conveyor rollers is a crucial decision that can impact the efficiency, cost, and longevity of your conveyor system. Here we’ll explore the considerations for choosing between new and used rollers, as well as tips for finding high-quality rollers on sale.
New vs. Used Rubber Conveyor Rollers
The decision between purchasing new or used rubber conveyor rollers depends on various factors including budget, application requirements, and operational demands. Here’s a comparative overview to guide your choice:
Aspect | New Rubber Conveyor Rollers | Used Rubber Conveyor Rollers |
---|---|---|
Cost | Higher initial investment. | More affordable upfront cost. |
Condition | Pristine, with no wear. | May show signs of wear; condition varies. |
Warranty | Often come with a manufacturer's warranty. | Usually sold as-is, with no warranty. |
Lifespan | Longer, as they start with no wear. | Shorter, due to pre-existing wear. |
Availability | May require wait time for production and delivery. | Often readily available for immediate use. |
Customization | Custom sizes and specifications can be ordered. | Limited to what is available; no customization. |
When to Consider Each Option:
- New Rollers: Ideal for critical applications where maximum reliability and lifespan are essential. Also suitable when specific customizations or dimensions are needed.
- Used Rollers: Best for short-term solutions, non-critical applications, or operations where budget constraints are a significant factor.
Rubber Conveyor Rollers for Sale
Finding high-quality rubber conveyor rollers for sale requires a balance between cost and quality.
- Manufacturer Direct: Purchasing directly from manufacturers can ensure quality and allow access to customization options. It also offers the possibility of better pricing for bulk orders.
- Industrial Supply Stores: Both online and brick-and-mortar industrial suppliers often have a range of conveyor rollers available, including specials and discounts on bulk purchases.
- Used Equipment Dealers: Reputable dealers in used industrial equipment can be a source for high-quality, used rubber conveyor rollers. Always inspect the condition or inquire about any refurbishments.
- Online Marketplaces: Websites that specialize in industrial equipment or general online marketplaces can have listings for both new and used rollers. Be cautious and ensure the seller is reputable.
- Trade Shows and Auctions: Industry trade shows and auctions can be excellent places to find deals on both new and used rubber conveyor rollers. They offer the opportunity to inspect the rollers firsthand or inquire about the specifics directly from the seller or manufacturer.
Regardless of where you choose to purchase your rubber conveyor rollers, always prioritize quality and suitability for your specific application to ensure the best return on investment and system efficiency.
Installation and Maintenance Best Practices for Rubber Conveyor Rollers
Ensuring the durability and efficiency of rubber conveyor rollers is pivotal to maintaining the operational integrity of conveyor systems. Here are essential guidelines for the installation and maintenance of these rollers to maximize their life cycle and operational efficiency.
Ensuring Durability and Efficiency
- Proper Installation: The correct installation of rubber conveyor rollers is foundational to their performance and longevity. Ensure that rollers are aligned perfectly parallel to the conveyor frame to prevent uneven wear. It’s also crucial that they’re installed with the correct tension to avoid slippage or excessive pressure on the bearings.
- Regular Inspection: Routine inspections are necessary to identify wear and tear, misalignment, or any build-up of materials on the rollers. Such issues, if unaddressed, can lead to more significant problems, including operational inefficiencies and potential breakdowns. Inspections should be conducted at regular intervals, depending on the operational load and environment.
- Cleaning Procedures: Keeping the rubber conveyor rollers clean is essential, especially in industries where contaminants are prevalent. Dirt, debris, and other materials can adhere to the rubber, reducing its grip and leading to inefficiencies. Use appropriate cleaning agents that won’t degrade the rubber material, and implement a regular cleaning schedule.
- Lubrication of Bearings: Although the rubber part of the roller may not require lubrication, the bearings within do. Regular lubrication of the bearings prevents friction, overheating, and wear, significantly extending the life of the rollers. Use the correct lubricant recommended by the manufacturer, as incorrect types can cause damage.
- Replacement Strategy: Even with the best care, rubber conveyor rollers will eventually wear out and need replacement. Having a replacement strategy is crucial to avoid prolonged downtime. This includes keeping a stock of critical spare parts and knowing the average lifespan of your rollers under normal operating conditions. Plan for replacements before failures occur to maintain continuous operation.
By following these guidelines, businesses can ensure their rubber conveyor rollers maintain peak efficiency and durability, thereby safeguarding the continuous operation of their conveyor systems. Proper care and maintenance not only extend the life of the rollers but also contribute to the overall efficiency and safety of the material handling operations.

Partnering with Manufacturers for Rubber Conveyor Rollers
Creating strong partnerships with manufacturers of rubber conveyor rollers is crucial for securing high-quality components tailored to specific operational needs. These collaborations can lead to improved product performance, customization options, and potential cost savings.
Rubber Roller Manufacturers Near Me
Engaging with local manufacturers for rubber conveyor rollers offers several advantages, including easier communication, faster delivery times, and potential cost savings on shipping. To effectively engage with local manufacturers:
- Research and Referrals: Start with a thorough online search for manufacturers in your area and check industry forums for referrals. Personal recommendations can provide insights into the reliability and quality of a manufacturer’s products.
- Visit Facilities: If possible, visit the manufacturing facilities to get a firsthand look at their operations, quality control processes, and the materials they use. This visit can also help in assessing the manufacturer’s capacity to handle your orders.
- Discuss Customization Options: Clearly communicate your specific needs regarding dimensions, material specifications, and any other unique requirements. A good manufacturer should be able to offer customization options that meet these needs.
- Evaluate Customer Service: The level of customer service is crucial, especially when dealing with customized products. Responsive and helpful customer service is a good indicator of a reliable supplier.
- Assess Flexibility and Scalability: Ensure the manufacturer can scale production up or down based on your needs and is flexible enough to handle last-minute changes or urgent orders.
Industrial Rubber Roller Manufacturer Insight
When choosing an industrial rubber roller manufacturer, it’s important to look for certain qualities that signify their capability and reliability:
- Experience and Expertise: Manufacturers with a long-standing presence in the industry typically have a wealth of experience and have refined their production processes for optimal quality.
- Quality Assurance: Look for manufacturers that adhere to strict quality standards and possess certifications relevant to your industry. This commitment to quality assures that the rollers meet or exceed operational requirements.
- Material Variety: A manufacturer with access to a wide range of rubber materials can offer rollers that are best suited for your specific application, whether it requires resistance to chemicals, heat, or abrasion.
- Innovative Solutions: Manufacturers that invest in research and development are more likely to offer innovative solutions that can enhance the performance and lifespan of your conveyor rollers.
- After-Sales Support: Comprehensive after-sales support, including technical assistance, maintenance advice, and warranty coverage, is essential for ensuring long-term satisfaction with your purchase.
Partnering with the right manufacturer for rubber conveyor rollers can significantly impact the efficiency, reliability, and cost-effectiveness of your conveyor systems. Taking the time to carefully select a manufacturer based on these criteria will ensure you receive high-quality components that meet your exact needs.
Top Rubber Conveyor Roller Manufacturers
Here is a list of some of the leading manufacturers of rubber conveyor rollers known for their quality products and reliable services:
GRAM Conveyor
- Overview: GRAM Conveyor specializes in the manufacture of conveyor idlers and related products, including high-quality rubber conveyor rollers.
- Key Products: Rubber impact rollers, Heavy Duty Rollers Conveyor, Conveyor Impact Roller,Ceramic Conveyor Rollers.
- Industries Served: Mining, cement and aggregates.
Flexco
- Overview: Flexco is a global leader in conveyor belt maintenance products, offering a wide range of rollers, including rubber conveyor rollers.
- Key Products: Rubber-coated rollers, impact rollers, return rollers.
- Industries Served: Mining, industrial, manufacturing, and logistics.
Continental Conveyor Ltd.
- Overview: Continental Conveyor is a recognized manufacturer of material handling systems and equipment, including conveyor rollers.
- Key Products: Heavy-duty rubber conveyor rollers, steel roller assemblies.
- Industries Served: Mining, agriculture, manufacturing, and bulk handling.
Precision Pulley & Idler (PPI)
- Overview: PPI is a leading supplier of idlers, pulleys, and conveyor components, known for their high-quality rubber conveyor rollers.
- Key Products: Rubber disc return rollers, impact rollers, and standard rubber-coated rollers.
- Industries Served: Aggregate, mining, coal, and industrial applications.
Canning Conveyor Co. Ltd.
- Overview: Canning Conveyor offers a comprehensive range of conveyor components and systems, including specialized rubber conveyor rollers.
- Key Products: Rubber-covered rollers, troughing rollers, return rollers.
- Industries Served: Mining, quarrying, recycling, and material handling.
These manufacturers are renowned for their innovation, quality, and customer service in the conveyor roller industry. Whether you need rollers for mining, manufacturing, or logistics, these companies offer a variety of solutions to meet your specific needs.
Customization and Specialty Products for Rubber Conveyor Rollers
Customization and the development of specialty products are key differentiators when selecting conveyor roller rubber for specific applications. Tailored solutions can significantly enhance performance, durability, and efficiency, addressing unique operational challenges.
Specialty Formulations
Manufacturers of rubber conveyor rollers often offer custom and specialty formulations to meet specific operational needs. These formulations can vary widely in terms of rubber composition, hardness, and resistance properties. For instance:
- Chemical Resistant Formulations: For industries where rollers are exposed to harsh chemicals, a rubber formulation that can withstand such environments is crucial to prevent degradation.
- High Grip Formulations: In applications where slippage is a concern, such as on steep conveyors or with smooth surface materials, a high grip rubber can be used to enhance traction.
- Anti-Static Formulations: In environments where static electricity could pose a hazard, such as in explosive atmospheres or when handling sensitive electronics, anti-static rubber formulations help to safely dissipate electrical charges.
- Food-Grade Formulations: For the food processing industry, rubber formulations that are non-toxic, resistant to food acids, fats, and cleaning agents, and compliant with food safety regulations are essential.
- High Temperature Resistant Formulations: Rollers operating in high-temperature environments need rubber coatings that can withstand prolonged exposure to heat without losing their mechanical properties or degrading.
Temperature and Environmental Resilience
The selection of rubber coatings for conveyor rollers must consider environmental factors, especially temperature, to ensure optimal performance and longevity.
- Bakery and Food Processing: Rollers in these industries need to resist high temperatures from ovens and cooling systems without degrading.
- Cold Storage and Freezers: Rubber coatings must remain flexible and operational in sub-zero temperatures, maintaining their grip and not becoming brittle.
- Outdoor Mining and Quarrying: Rollers are exposed to a wide range of temperatures and weather conditions, requiring materials that can withstand extreme heat, cold, and UV exposure.
- Chemical Manufacturing: Exposure to chemicals and varying temperatures demands rubber coatings that are not only chemically resistant but also stable across a broad temperature range.
- Automotive Manufacturing: The high-temperature environments, particularly near painting and drying ovens, require rollers that can perform consistently without softening or degrading.
Customization and the ability to withstand environmental challenges are crucial in extending the lifespan and enhancing the efficiency of rubber conveyor rollers. By considering these factors and working closely with manufacturers for tailored solutions, businesses can significantly improve their operational processes.
Need custom conveyor rollers for your business? Reach out to us today and get a free quote!
FAQs About Rubber Conveyor Rollers
Conveyor systems utilize various types of rollers to facilitate the efficient transport of materials across different sections of the manufacturing, packaging, or distribution areas. The choice of roller type depends on the application, load requirements, and environmental conditions. Common types include metal rollers, plastic rollers, and rubber conveyor rollers. Rubber conveyor rollers are particularly valued for their durability, grip, and ability to reduce noise and vibration.Rubber conveyor rollers offer enhanced grip and protection, improving performance and safeguarding products in various manufacturing processes. They are made by coating a metal or plastic core with rubber, making them versatile for handling a wide range of materials under different operational conditions. These rollers can be custom-designed to meet specific requirements, such as high temperature, chemical resistance, or food-grade quality, enhancing the conveyor system’s efficiency and reliability across various industries.
Rubber rollers are used in a myriad of applications across numerous industries due to their versatility and beneficial properties. They play a crucial role in conveyor systems, where they help in the smooth and efficient transport of goods by providing excellent grip and reducing slippage and damage to the materials being moved. Beyond conveyors, rubber rollers are integral to printing and packaging machinery, where they facilitate the transfer of ink and precise placement of labels or packaging materials. In manufacturing, they are used in processes that require the application of coatings, adhesives, or varnishes. The rubber material’s flexibility allows for uniform application and pressure distribution. Additionally, rubber rollers are used in agricultural machinery, textile production, and paper processing industries, showcasing their adaptability and effectiveness in various operational contexts.
The price of a 5-inch rubber roller can vary significantly based on several factors, including the type of rubber material used, core material, manufacturing quality, and any custom features or specifications. Basic off-the-shelf 5-inch rubber rollers might start at a relatively modest price for simple applications. However, prices can increase for rollers designed for specialized applications, such as high-temperature environments, chemical resistance, or heavy-duty use. Customizations, such as specific rubber compounds, precision engineering, and additional features like anti-static properties, can further affect the cost. It’s advisable to contact manufacturers or suppliers directly for accurate pricing based on your specific requirements, considering that bulk orders or ongoing supply agreements might also influence the final price.
The rubber material used for conveyor rollers is selected based on the application’s specific needs, including the environment in which the roller will operate, the materials it will come into contact with, and the mechanical demands of the application. Common types of rubber materials include natural rubber, neoprene, nitrile, silicone, and polyurethane. Each type offers distinct properties:
Natural Rubber is known for its elasticity, tensile strength, and resistance to abrasion, making it suitable for general-purpose rollers.
Neoprene offers excellent chemical stability and flexibility over a wide temperature range, ideal for harsh environmental conditions.
Nitrile is resistant to oils and chemicals, making it perfect for use in the petroleum and chemical processing industries.
Silicone can withstand high temperatures and is often used in applications involving heat.
Polyurethane is highly durable and resistant to wear, tear, and various chemicals, suitable for heavy-duty applications.
Manufacturers often provide custom rubber formulations tailored to meet specific operational requirements, enhancing performance, durability, and the overall efficiency of the conveyor system.
Making rubber rollers involves several steps. First, select the appropriate rubber material, such as natural or synthetic rubber, and formulate it based on specific requirements. Next, mix the rubber with other components to create a uniform blend. Then, process the blended rubber through a calendering machine to produce rubber sheets of the desired thickness. Following this, wrap the rubber sheets around a metal core and use either hot or cold pressing methods for molding and vulcanizing, ensuring the rubber adheres firmly to the core. Finally, machine and grind the molded rubber roller to achieve the required dimensions and surface finish. The entire process requires precise control of temperature, pressure, and time to ensure the quality and performance of the rubber rollers. These rollers are widely used in industries such as printing, textiles, and papermaking.
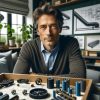
Jordan Smith, a seasoned professional with over 20 years of experience in the conveyor system industry. Jordan’s expertise lies in providing comprehensive solutions for conveyor rollers, belts, and accessories, catering to a wide range of industrial needs. From initial design and configuration to installation and meticulous troubleshooting, Jordan is adept at handling all aspects of conveyor system management. Whether you’re looking to upgrade your production line with efficient conveyor belts, require custom conveyor rollers for specific operations, or need expert advice on selecting the right conveyor accessories for your facility, Jordan is your reliable consultant. For any inquiries or assistance with conveyor system optimization, Jordan is available to share his wealth of knowledge and experience. Feel free to reach out at any time for professional guidance on all matters related to conveyor rollers, belts, and accessories.