Custom Solutions: Rubber Coated Conveyor Rollers
In the intricate tapestry of industrial machinery, rubber coated conveyor rollers stand out as vital components in a myriad of sectors. These specialized rollers, embraced for their durability and grip, play a pivotal role in optimizing the conveyor system’s function. The significance of rubber coated conveyor rollers spans across packaging, manufacturing, and material handling industries, where they ensure the smooth and efficient transport of goods. Their rubber coating not only minimizes wear and tear on the conveyor belts but also reduces the noise, making them an indispensable part of a quiet and effective operation. Choosing the correct type of roller for the intended application is not merely a matter of performance, but also one of cost-efficiency and maintenance. Therefore, understanding the specific needs of your application is essential in selecting the right rubber coated conveyor rollers that will enhance productivity and reduce downtime.
What are Rubber Coated Conveyor Rollers
Rubber coated conveyor rollers embody a core component—typically steel or plastic—sheathed in a rubber layer. This marriage of materials imparts these rollers with a multitude of benefits crucial to efficient material handling systems. Below are eight key advantages of using rubber coated conveyor rollers:
- Enhanced Grip: The rubber coating provides increased friction between the roller and the conveyor belt, ensuring that the belt moves smoothly without slippage.
- Noise Reduction: These rollers operate more quietly than their metal counterparts, contributing to a more pleasant work environment.
- Decreased Wear: Rubber’s natural resilience protects both the rollers and the conveyor belt from wear, extending the life of the equipment.
- Shock Absorption: The rubber coating can absorb impacts from materials being loaded onto the conveyor, reducing damage to both the products and the system.
- Corrosion Resistance: Rubber coated rollers can withstand exposure to chemicals and moisture that might otherwise corrode metal rollers.
- Improved Traction: In wet or dry conditions, the rubber surface ensures consistent traction, which is critical for the movement of materials.
- Versatility: Rubber rollers can be used with a wide range of products and weights, making them suitable for various applications.
- Customizability: With different types of rubber available, the rollers can be customized to suit specific operational needs.
Different types of rubber coatings and their applications can be summarized in the following table:
Type of Rubber Coating | Hardness | Applications | Benefits |
---|---|---|---|
Natural Rubber | Soft to Hard | General use, packaging | Economical, good physical properties |
Neoprene | Soft to Hard | Outdoor, oily materials | Oil and weather-resistant |
Nitrile | Medium to Hard | Oil exposure, recycling industries | Excellent oil resistance |
Silicone | Very Soft to Medium | High-temperature environments | Heat resistance, non-stick properties |
Polyurethane | Soft to Very Hard | Precision equipment, delicate materials | Abrasion-resistant, non-marking |
EPDM | Medium to Hard | Outdoor, weather-prone applications | Excellent ozone and weather resistance |
Viton | Hard | Chemical processing | Chemical resistance, high-temperature capacity |
Hypalon | Medium to Hard | Chemical exposure, extreme environments | Chemical and temperature resistant |
Each type of rubber offers unique characteristics, making rubber coated conveyor rollers versatile tools capable of handling a variety of industrial challenges. From the simple transport of goods to complex processing systems, rubber coated conveyor rollers are indispensable in creating an efficient and reliable material handling system.
Selecting the Best Rubber Coated Conveyor Rollers
Selecting the best rubber coated conveyor rollers is a critical decision that affects the efficiency and durability of your conveyor system. Here are 12 tips to guide you through the selection process:
- Assess the Load: Consider the weight of the items the conveyor will carry. The rollers must be able to support the load without deforming.
- Evaluate the Environment: Factors like temperature, exposure to chemicals, and moisture can impact roller performance. Choose a rubber material compatible with the operational environment.
- Determine the Roller Diameter: Larger diameters are typically used for heavier loads, while smaller ones are for lighter loads and tighter turns.
- Select the Right Rubber Type: Different rubber types offer various benefits, such as abrasion resistance or chemical resistance. Match the rubber type to your specific needs.
- Consider Roller Length: Ensure the roller length is suitable for the width of the materials to be handled.
- Check the Traction Requirements: The rubber coating should provide the necessary grip for the products being moved.
- Inspect the Hardness: Rubber hardness, measured in durometer, affects the grip and wear resistance. Choose the hardness that best suits your application.
- Opt for Quality Bearings: Good quality bearings ensure smooth roller operation and extend the roller’s lifespan.
- Examine the Wall Thickness: The thickness of the rubber coating can affect the roller’s ability to absorb impacts and provide traction.
- Look for Custom Grooving: If necessary, opt for rollers with custom grooving to enhance grip or align the belt.
- Understand the Maintenance Requirements: Consider how easy the rollers are to maintain and clean, as this will affect their performance over time.
- Compare Pricing and Quality: While cost is an important factor, it should be balanced against the quality and expected lifespan of the rollers.
In addition to the above tips, here are 6 factors that affect the performance and lifespan of rubber coated conveyor rollers:
- Quality of Rubber Material: High-quality rubber will resist wear and tear better, maintaining performance over time.
- Proper Installation: Incorrect installation can lead to uneven wear and premature failure.
- Regular Maintenance: Routine inspections and cleaning can prevent build-up that may damage the rollers.
- Operating Conditions: Extreme temperatures or corrosive materials can degrade rubber faster if it’s not suited for those conditions.
- Roller Design: The design of the roller should match the application to ensure it can handle the stress of operation without failure.
- Load Distribution: Uneven distribution of weight across the rollers can lead to increased wear and reduced lifespan.
Careful consideration of these tips and factors when selecting your rubber coated conveyor rollers will lead to a more efficient, durable, and cost-effective conveyor system.
The Cost Factor of Rubber Coated Conveyor Rollers
Understanding the cost dynamics of rubber coated conveyor rollers is essential for businesses aiming to optimize their operational budget while maintaining efficiency and longevity in their conveyor systems. The price points of rubber coated conveyor rollers can vary widely, influenced by several key factors that need to be considered to gauge the overall value and cost-effectiveness of the investment.
Factors Influencing Cost
- Material Quality: The type of rubber and core material (steel, stainless steel, or plastic) used significantly affects the cost. High-quality materials that offer enhanced durability and performance characteristics typically command higher prices.
- Manufacturing Process: Advanced manufacturing processes that ensure precise coating thickness and uniformity can also add to the cost. However, they contribute to roller longevity and reduced maintenance needs.
- Customization: Customized rollers designed to meet specific operational requirements, such as unique dimensions, rubber compounds, or hardness levels, can be more expensive than standard options.
- Volume: The order quantity can influence the price per unit, with larger orders often benefiting from economies of scale.
- Supplier: Prices can also vary based on the supplier’s location, reputation, and the additional services they offer, such as consultation, installation, and after-sales support.
- Market Fluctuations: Raw material costs and market demand can cause fluctuations in roller prices over time.
Cost-Effectiveness vs. Performance and Longevity
When evaluating the cost of rubber coated conveyor rollers, it’s crucial to consider the balance between initial expense and the long-term value they provide. Investing in higher-priced rollers with superior quality and durability can lead to significant savings over time, thanks to reduced downtime, lower maintenance costs, and extended service life. In contrast, opting for the cheapest available option might result in frequent replacements and higher operational costs in the long run.
Moreover, the right selection of rubber coated conveyor rollers can enhance the efficiency of conveyor operations, ensuring smooth material handling and protecting both the conveyor belt and the goods being transported. This operational efficiency not only contributes to a more productive workflow but also to the overall longevity of the conveyor system.
While the initial cost is an important consideration, evaluating the performance, durability, and the specific needs of your operation will guide you to make a more informed, cost-effective decision regarding rubber coated conveyor rollers. Balancing these factors ensures that the investment contributes positively to the operational efficiency and bottom line of your business.
Manufacturers and Availability of Rubber Coated Conveyor Rollers
In the realm of material handling and logistics, the choice of rubber coated conveyor rollers is pivotal for maintaining operational efficiency. Several manufacturers stand out for their quality, innovation, and reliability. Below, we explore six prominent manufacturers of rubber coated conveyor rollers and offer guidance on finding local suppliers to meet your specific needs.
Prominent Manufacturers
- Fastrax Conveyor Rollers: Known for their comprehensive range of high-quality rollers, Fastrax offers rubber coated options designed for durability and performance. They specialize in both standard and custom solutions, catering to a wide array of industries.
- American Roller: A leader in the field, American Roller prides itself on its advanced coating technologies and materials science expertise. Their rubber coated rollers are engineered for optimal grip and wear resistance, suitable for demanding industrial applications.
- CAS Rollers: With a focus on precision and durability, CAS Rollers delivers rubber coated rollers that improve conveyor system efficiency. Their products are tailored to meet specific environmental challenges, such as temperature extremes and chemical exposures.
- Conveyor Rollers by Rollex: Rollex is renowned for its engineering excellence and innovative solutions in conveyor technology. Their rubber coated rollers are designed for smooth operation and minimal maintenance, enhancing system longevity.
- Pinnacle Roller: Pinnacle offers a diverse lineup of rubber coated conveyor rollers, emphasizing custom solutions. Their commitment to quality and customer service makes them a preferred supplier for specialized applications.
- Omni Metalcraft Corp: Omni Metalcraft Corp’s rubber coated rollers are crafted for superior performance across various applications. Their emphasis on durability and efficiency makes their rollers a staple in the conveyor industry.
Finding Suppliers Near Me
When searching for “rubber coated conveyor rollers near me,” consider the following aspects to ensure you partner with a supplier that meets your needs:
- Local Presence: A supplier with a local presence can offer quicker delivery times and more accessible support. This proximity can be crucial for urgent needs and maintenance support.
- Customization Capabilities: Look for suppliers who offer customization options that align with your specific requirements, whether it’s roller size, rubber type, or application-specific features.
- Quality and Reliability: Assess the manufacturer’s reputation for quality and reliability. This can often be gauged through customer testimonials, case studies, or industry certifications.
- Consultative Approach: A supplier that takes a consultative approach to understand your needs and challenges can provide more value, ensuring you receive the optimal solution for your application.
- After-Sales Support: Consider the level of after-sales support offered. Reliable maintenance and repair services can significantly extend the lifespan of your rollers and reduce operational downtime.
Selecting the right manufacturer or local supplier for rubber coated conveyor rollers is more than a transaction; it’s a partnership that can affect the efficiency and productivity of your operations. By considering these factors, you can ensure that you choose a provider capable of meeting your needs with high-quality solutions and support.
Purchasing and Sales of Rubber Coated Conveyor Rollers
When it comes to enhancing your conveyor system, selecting the right rubber coated conveyor rollers is a critical decision. Whether upgrading existing equipment or designing a new system, understanding the purchasing options and how to assess the quality and warranties of these components is essential. This section explores the avenues for acquiring rubber coated conveyor rollers and provides tips for ensuring you make a sound investment.
Purchasing Options
New Rollers: Purchasing new rubber coated conveyor rollers directly from manufacturers or authorized distributors is the most straightforward option. This approach guarantees access to the latest technology, materials, and design innovations. Buyers can expect full warranties and comprehensive support, from specification through to after-sales service.
Used Rollers: For operations with budget constraints or less demanding applications, used rubber coated conveyor rollers can offer a cost-effective solution. Available through industrial surplus stores, online marketplaces, or from companies updating their systems, used rollers can still provide significant service life. However, careful inspection and understanding of the previous application are crucial to ensure suitability and performance.
Assessing Quality and Warranties
- Material Specifications: Verify that the rubber and core materials meet the required specifications for your application. High-quality materials are the foundation of roller durability and performance.
- Manufacturing Standards: Look for rollers manufactured according to recognized industry standards. This ensures they have been produced with attention to quality and consistency.
- Warranty Coverage: Understand the warranty provided with the rollers. A comprehensive warranty can offer peace of mind and protection against manufacturing defects.
- Supplier Reputation: Research the supplier’s reputation within the industry. Companies with a positive track record are more likely to provide reliable products and stand behind their offerings.
- Customization Options: Ensure that the supplier can offer customization that matches your specific needs. Customized rollers designed for your application will likely perform better and last longer.
- Technical Support: Assess the level of technical support available. Reliable suppliers offer support from selection through to installation and maintenance, ensuring your system operates optimally.
- Performance Reviews: Look for customer reviews or case studies that demonstrate the performance and reliability of the rollers in similar applications. Real-world feedback can provide valuable insights into how the rollers will perform in your operation.
Choosing the right rubber coated conveyor rollers involves careful consideration of your system’s needs, the quality and reliability of the components, and the support provided by the supplier. By following these tips and exploring both new and used purchasing options, you can secure the best solution for your conveyor system, ensuring efficient operation and long-term reliability.
Specialty Rubber Coated Rollers in Conveyor Systems
Specialty rubber coated conveyor rollers cater to specific operational needs, offering enhanced functionality beyond standard rollers. Among these, rubber coated drive rollers hold a pivotal role in the smooth and efficient operation of conveyor systems. These rollers are designed not just to support and move the conveyor belt but also to drive it, providing the necessary traction to move materials along the production line.
Specialized Use of Rubber Coated Drive Rollers
Rubber coated drive rollers are integral in applications where precise control of movement is crucial. The rubber coating provides increased friction between the roller and the conveyor belt, ensuring that the belt does not slip, especially under heavy loads or at high speeds. This is particularly important in environments where variations in load or conditions can otherwise lead to inefficiencies or disruptions in the conveyor operation.
Advantages of Using Industrial Rubber Rollers with Bearings
- Reduced Vibration and Noise: The rubber coating on these rollers absorbs operational vibrations and noise, leading to a quieter and smoother operation.
- Enhanced Durability: The addition of bearings to rubber coated rollers significantly extends their service life by reducing wear on the roller itself, making them a cost-effective solution over time.
- Improved Load Distribution: Bearings within the rollers ensure that the weight of the conveyed materials is evenly distributed, reducing stress and strain on the conveyor system.
- Increased Operational Efficiency: The combination of rubber and bearings allows for a more efficient transfer of power from the drive unit to the conveyor belt, enhancing overall system performance.
- Better Traction and Control: Rubber coatings provide superior traction, preventing slippage and contributing to more precise control over the movement of materials.
- Resistance to Environmental Factors: Industrial rubber rollers with bearings are better equipped to withstand harsh conditions, including exposure to chemicals, moisture, and temperature variations.
- Ease of Maintenance: Rollers designed with bearings are generally easier to replace or repair, minimizing downtime and maintenance costs.
- Versatility: These rollers can be customized with various types of rubber and bearing configurations to suit different applications and operational requirements.
The specialized use of rubber coated drive rollers in conveyor systems enhances the efficiency, durability, and reliability of material handling operations. Industrial rubber rollers with bearings offer a suite of advantages that contribute to the smooth, efficient, and cost-effective movement of goods, making them an essential component in modern manufacturing and distribution environments. By carefully selecting the right type of specialty rollers, businesses can achieve significant improvements in their operational performance and productivity.
Services and Maintenance for Rubber Coated Conveyor Rollers
The longevity and efficiency of rubber coated conveyor rollers largely depend on the quality of service and maintenance they receive. Locating services such as “rubber roller coating near me” plays a crucial role in maintaining the operational integrity of conveyor systems. Proximity to service providers ensures prompt maintenance and repair, minimizing downtime and preserving the conveyor system’s longevity.
Why Location Matters for Maintenance
- Quick Response Times: Proximity to maintenance services means faster response times for repairs, reducing system downtime.
- Ease of Access to Spare Parts: Local providers are likely to have quicker access to necessary spare parts or materials for rubber coating, speeding up the repair process.
- Cost Savings: Engaging local service providers can reduce transportation costs associated with sending rollers out for maintenance or waiting for service personnel to travel to your site.
- Personalized Service: Building a relationship with a local service provider can lead to more personalized service and tailored maintenance plans based on your specific operational needs.
Importance of Regular Maintenance
- Prevents Downtime: Regular maintenance identifies and rectifies potential issues before they lead to system failures, preventing costly downtime.
- Ensures Efficiency: Keeping rollers in optimal condition ensures the conveyor system operates at peak efficiency, saving energy and reducing wear on other components.
- Extends Roller Lifespan: Routine inspections and maintenance extend the life of rubber coated conveyor rollers by ensuring the rubber coating remains intact and functional.
- Improves Safety: Well-maintained rollers reduce the risk of accidents and injuries associated with equipment malfunctions.
- Maintains Product Quality: Consistent roller performance prevents damage to materials being conveyed, maintaining product quality.
- Compliance with Standards: Regular maintenance ensures that your conveyor system complies with industry standards and regulations, avoiding potential fines and liabilities.
- Optimizes Performance: Maintenance allows for adjustments and optimizations to be made to the conveyor system, improving overall performance and adaptability to changing operational needs.
- Cost-Efficiency: Investing in regular maintenance is cost-effective in the long run, as it avoids the higher costs associated with major repairs or replacements due to neglect.
Finding Servicing and Maintenance Providers
Finding a reputable provider for the maintenance of rubber coated conveyor rollers involves several steps:
- Research Local Services: Use online searches, industry directories, and recommendations to compile a list of local service providers.
- Check Credentials and Experience: Look for providers with a proven track record and expertise specifically with rubber coated conveyor rollers.
- Consider Comprehensive Service Packages: Some providers offer comprehensive maintenance packages that can provide better value and ensure ongoing support.
- Evaluate Customer Reviews and Testimonials: Feedback from other customers can give you insights into the reliability and quality of the service provider’s work.
Regular maintenance and timely servicing are non-negotiable aspects of ensuring the efficiency, safety, and longevity of rubber coated conveyor rollers and the systems they support. By prioritizing these practices and choosing the right service providers, businesses can significantly enhance their operational continuity and productivity.
Industry Spotlight on Rubber Coated Conveyor Rollers
Rubber coated conveyor rollers are indispensable across a broad spectrum of industries, each with its unique demands and challenges. This section highlights four case studies showcasing the pivotal role these rollers play in various sectors and examines how industrial rubber roller manufacturers tailor their products to meet these diverse needs.
Case Studies Across Industries
- Packaging and Distribution: In the fast-paced world of packaging and distribution, rubber coated conveyor rollers ensure the gentle handling of fragile items while maintaining the speed and efficiency required to meet demanding schedules. Their enhanced grip reduces slippage, ensuring packages remain stable and are accurately sorted and directed.
- Food Processing: The food industry demands not only efficiency but also compliance with stringent hygiene standards. Rubber coated conveyor rollers in this sector are often made from food-grade materials that are easy to clean and resist contamination. Their durability withstands the rigorous cleaning protocols necessary to meet health and safety regulations.
- Automotive Manufacturing: Automotive plants use rubber coated conveyor rollers to move heavy parts and assemblies through the production line. The rubber coating absorbs shocks and prevents damage to components, while the robust design of these rollers supports the weight and abuse of metal parts and tools.
- Printing and Paper Processing: In printing and paper mills, precision and care are paramount. Rubber coated conveyor rollers provide the necessary gentle touch to move delicate paper products without causing tears or creases. Their precise manufacturing ensures even pressure distribution, critical for quality printing and paper finishing.
Meeting Sector Demands: The Role of Manufacturers
Industrial rubber roller manufacturers play a crucial role in meeting the specific needs of each sector. They achieve this through:
- Material Innovation: Manufacturers continuously innovate rubber compounds to enhance performance characteristics like heat resistance, chemical resistance, and wear durability, ensuring rollers can withstand sector-specific challenges.
- Custom Engineering: Understanding that each industry has unique needs, manufacturers offer custom-engineered solutions. This might involve specific roller dimensions, rubber hardness levels, or specialized coatings.
- Quality Assurance: Rigorous testing and quality assurance protocols ensure that rubber coated conveyor rollers meet the high standards required in each industry. Manufacturers often hold certifications that attest to their commitment to quality and safety.
- Consultative Approach: Top manufacturers take a consultative approach to their business relationships, working closely with clients to understand their operational challenges and tailor solutions that offer the best return on investment.
- Sustainability Focus: With increasing attention on environmental sustainability, manufacturers are also innovating in eco-friendly materials and production methods, without compromising on the performance or durability of the rollers.
Rubber coated conveyor rollers are a testament to the intricate balance between industrial demand and innovative manufacturing solutions. Through tailored engineering and a deep understanding of the operational challenges across various sectors, manufacturers of these rollers provide critical support to the backbone of global industries, enhancing efficiency, safety, and productivity.
Types and Customization of Rubber Coated Conveyor Rolles
The versatility of rubber coated conveyor rollers lies not only in their application across industries but also in the variety of types and customization options available. These rollers are designed to meet the exacting requirements of various industrial applications, ensuring optimal performance, durability, and efficiency.
Types of Rubber Rollers
Natural Rubber Rollers: Ideal for general applications, these rollers offer good elasticity, tensile strength, and resistance to abrasions and cuts. They are widely used in industries such as agriculture, packaging, and manufacturing.
Nitrile Rubber Rollers: Known for their resistance to oil, grease, and chemicals, nitrile rubber rollers are suited for use in the automotive, printing, and textile industries, where exposure to oils and chemicals is common.
Silicone Rubber Rollers: With excellent heat resistance, silicone rollers are the go-to choice for applications involving high temperatures. They are often found in the plastics, food processing, and medical industries.
Polyurethane Rollers: Offering outstanding abrasion resistance and load-bearing capacity, polyurethane rollers are used in material handling, packaging, and heavy-duty industrial applications.
EPDM Rollers: These rollers are characterized by their resistance to weathering, ozone, and UV rays, making them suitable for outdoor applications and industries requiring long-term exposure to harsh environmental conditions.
Customization Process
The customization of rubber coated conveyor rollers is a meticulous process that begins with understanding the specific needs of the application. This involves considering factors such as load capacity, speed requirements, environmental conditions, and the materials being handled.
- Consultation: The process typically starts with a consultation between the client and the manufacturer to discuss the operational requirements and challenges.
- Material Selection: Based on the consultation, the manufacturer recommends the most appropriate rubber compound and core material. This decision is crucial for ensuring the roller’s performance and longevity.
- Design and Engineering: Engineers design the roller, taking into account dimensions, required tolerances, and any special features like grooves for tracking or drive bands. Advanced CAD software and simulation tools are often used to optimize the design.
- Prototype and Testing: For critical applications, a prototype may be produced and tested under operational conditions. This step ensures that the customized roller meets all specified requirements before full-scale production begins.
- Manufacturing: With the design finalized and tested, manufacturing begins. Modern manufacturing techniques, such as CNC machining and precision molding, are employed to ensure high-quality and consistency.
- Quality Control: Throughout the manufacturing process, rigorous quality control measures are in place to ensure that each roller meets the strict criteria set out during the consultation phase.
- Delivery and Installation Support: Once manufactured, the rollers are delivered, and in some cases, the manufacturer provides installation support to ensure optimal performance from the outset.
- After-Sales Service: Reliable manufacturers offer comprehensive after-sales support, including maintenance tips, spare parts, and repair services, ensuring the long-term success of the customization project.
Customization allows rubber coated conveyor rollers to be perfectly tailored to the unique demands of each application, ensuring that each system operates at its best. By leveraging the expertise of manufacturers and engaging in the customization process, businesses can achieve significant operational improvements, contributing to increased productivity and efficiency.
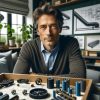
Jordan Smith, a seasoned professional with over 20 years of experience in the conveyor system industry. Jordan’s expertise lies in providing comprehensive solutions for conveyor rollers, belts, and accessories, catering to a wide range of industrial needs. From initial design and configuration to installation and meticulous troubleshooting, Jordan is adept at handling all aspects of conveyor system management. Whether you’re looking to upgrade your production line with efficient conveyor belts, require custom conveyor rollers for specific operations, or need expert advice on selecting the right conveyor accessories for your facility, Jordan is your reliable consultant. For any inquiries or assistance with conveyor system optimization, Jordan is available to share his wealth of knowledge and experience. Feel free to reach out at any time for professional guidance on all matters related to conveyor rollers, belts, and accessories.