Sustainable Solutions: Roller Conveyor with Plastic Rollers
In today’s fast-paced industrial landscape, the importance of efficient material handling systems cannot be overstated. At the heart of these systems lies the innovative use of roller conveyor with plastic rollers, a cornerstone in the seamless operation of various sectors including manufacturing, logistics, and retail. These conveyors offer a myriad of benefits such as reduced friction, minimal maintenance requirements, and enhanced durability. Their lightweight nature, combined with the inherent corrosion resistance of plastic, makes them an ideal choice for a wide range of applications. From assembly lines to distribution centers, roller conveyors with plastic rollers are pivotal in optimizing workflow, improving safety, and reducing operational costs. This introduction delves into the crucial role these conveyors play across industries, underscoring their significance in not just enhancing operational efficiency but also in fostering a more sustainable and cost-effective approach to material handling.
The Basics of Roller Conveyor with Plastic Rollers
Understanding the basic structure and functionality of roller conveyors with plastic rollers is essential for leveraging their full potential in any industrial setting. At its core, a roller conveyor with plastic rollers consists of a series of cylindrical rollers made from high-grade plastic, mounted in a frame. These rollers can rotate freely, allowing goods to glide over them with minimal effort.
- Frame Construction: The backbone of any roller conveyor with plastic rollers is its frame, which is typically made from steel or aluminum. This frame provides the necessary support for the plastic rollers and can be configured in straight or curved sections to accommodate various layouts.
- Plastic Rollers: The rollers themselves are the most critical component. Made from durable plastics like polypropylene or high-impact polyethylene, these rollers offer a smooth surface that reduces friction and wear on transported goods.
- Drive Mechanisms: While many roller conveyor with plastic rollers operate on gravity alone, others are powered by motors. These drive mechanisms can control the speed at which goods are moved, ensuring a consistent flow of materials.
- Supporting Bearings: Inside each roller, bearings help to reduce rotational friction, allowing the rollers to turn freely even under heavy loads. These bearings are crucial for the longevity and efficiency of the conveyor.
- Adjustable Stands and Rails: To accommodate different sizes of goods and to ensure they are transported safely, roller conveyor with plastic rollers often include adjustable stands and side rails. These components can be customized to fit the specific needs of any operation.
Roller conveyors with plastic rollers are designed for versatility and ease of use. Their basic structure, comprising a sturdy frame, durable plastic rollers, efficient drive mechanisms, supporting bearings, and adjustable components, makes them an indispensable tool in various industries for streamlining operations and enhancing productivity.
The Benefits of Using Roller Conveyor with Plastic Rollers
The integration of plastic rollers in roller conveyors presents a suite of advantages that cater to efficiency, durability, and cost-effectiveness in material handling processes. The unique properties of plastic rollers make roller conveyor with plastic rollers a preferred choice in numerous industrial applications. Here, we explore these benefits through various examples:
- Reduced Friction: Plastic rollers inherently have a smoother surface compared to their metal counterparts, which significantly reduces the friction between the conveyor and the goods it transports. This leads to a smoother operation, less wear and tear on both the goods and the conveyor, and a decrease in the energy required to move items along the conveyor.
- Minimal Maintenance: Roller conveyors with plastic rollers require considerably less maintenance than those with rollers made of other materials. Plastic is resistant to corrosion, does not require lubrication, and can withstand exposure to many chemicals, making these conveyors ideal for use in harsh environments.
- Noise Reduction: Plastic rollers operate much more quietly than metal rollers. This reduction in noise contributes to a better working environment for employees and is particularly beneficial in operations where noise levels are a concern, such as in packaging facilities or distribution centers.
- Lightweight and Easy to Install: The lightweight nature of plastic rollers simplifies the assembly and installation of roller conveyors with plastic rollers. This not only reduces the initial setup time but also makes any necessary adjustments or reconfigurations easier to manage.
- Cost-Effectiveness: Initially, roller conveyors with plastic rollers may present a more economical option due to the lower cost of plastic materials. Additionally, the long-term savings in maintenance, energy, and replacement costs contribute to their overall cost-effectiveness.
When it comes to plastic conveyor rollers with bearings, their significance cannot be understated in ensuring the efficient and smooth operation of the conveyor:
- Enhanced Load Support: Bearings allow the plastic rollers to rotate freely, minimizing the effort required to move heavy loads. This capability is crucial in industries where heavy or bulky items are routinely handled.
- Durability Under Load: The combination of plastic rollers with high-quality bearings can support significant weights without deforming or breaking. This durability ensures that the conveyor can handle a variety of goods without compromising performance.
- Precision Movement: Bearings contribute to the precision movement of goods along the conveyor, which is vital in automated systems where exact positioning is required.
- Reduced Energy Consumption: The efficiency of plastic rollers with bearings leads to lower energy consumption. This is because the conveyor can move goods along with minimal resistance, thereby requiring less power.
- Longevity: Bearings extend the lifespan of plastic rollers by reducing wear and tear. This means that roller conveyors with plastic rollers can remain in operation for longer periods without the need for replacements, offering significant savings over time.
The adoption of roller conveyor with plastic rollers, especially those outfitted with bearings, offers tangible benefits ranging from reduced operational costs and maintenance to improved worker safety and environmental compliance. These advantages make them an invaluable component in the optimization of material handling and distribution operations across various sectors.
Types of Roller Conveyor with Plastic Rollers
The versatility of roller conveyors with plastic rollers is evident in the variety of types available, each designed to meet specific industrial needs. From compact systems for small spaces to robust solutions for heavy loads, these conveyors offer flexibility and efficiency. Below, we delve into three primary types:
Used Roller Conveyor with Plastic Rollers:
For businesses looking to optimize their operations cost-effectively, used roller conveyors with plastic rollers present a viable option. These second-hand conveyors can offer the same benefits as their new counterparts, such as reduced friction and maintenance, at a fraction of the cost. Buyers interested in these cost-saving solutions should inspect the condition of the rollers and frame closely to ensure they meet operational requirements.
Small Roller Conveyor with Plastic Rollers:
Ideal for spaces where efficiency is key but the area is limited, small roller conveyors with plastic rollers are designed to be compact yet effective. These systems are perfect for:
- Assembly Lines: Small conveyors can fit into tight spaces, making them ideal for assembly line operations where components need to be passed between workers or stations efficiently.
- Packaging Stations: Compact conveyors are perfect for packaging areas where products need to be moved short distances for wrapping, boxing, or labeling.
- Pharmaceuticals: In the pharmaceutical industry, where cleanliness and precision are paramount, small conveyors with non-corrosive plastic rollers are ideal for moving small batches of products through production or packaging processes.
- Electronics Manufacturing: Given their gentle handling, these conveyors are suited for transporting delicate electronic components between assembly stages without damage.
- Retail Backrooms: Small conveyors can optimize the limited space in retail backrooms, facilitating the quick sorting and movement of goods.
Heavy Duty Roller Conveyor with Plastic Rollers:
When it comes to moving larger, heavier items, heavy-duty roller conveyors with plastic rollers are engineered to withstand the demands of such tasks. These conveyors are characterized by:
- Reinforced Frames: Stronger materials and construction methods are used to ensure the frame can support heavy loads.
- Thicker Rollers: The plastic rollers are designed to be thicker and more durable to prevent deformation under heavy weights.
- High-capacity Bearings: Bearings capable of supporting increased loads are used to ensure smooth roller operation under the weight.
- Wider and Longer Configuration: To accommodate larger items, these conveyors are built wider and can be extended longer than standard models.
- Adjustable Speed Settings: Many heavy-duty conveyors come with variable speed settings to handle different types of goods effectively without causing damage.
Each type of roller conveyor with plastic rollers serves a specific purpose, addressing the unique needs of various industries. From cost-conscious second-hand options and space-saving small conveyors to robust heavy-duty models, there’s a solution to enhance efficiency in virtually any material handling scenario.
DIY: Building a Roller Conveyor with Plastic Rollers
For DIY enthusiasts interested in customizing their material handling solutions, constructing a roller conveyor with plastic rollers can be a rewarding project. This guide provides a step-by-step approach to building your own PVC roller conveyor, highlighting necessary materials and safety precautions to ensure a successful build.
Materials Needed:
- PVC pipe for rollers (diameter and length depending on your specific needs)
- Metal or wooden frame materials
- Roller bearings suited for PVC pipes
- Axles (metal rods or bolts that fit the bearings and PVC pipes)
- Brackets and screws for assembling the frame and attaching rollers
- Tools (saw, drill, screwdriver, measuring tape, etc.)
Step-by-Step Guide:
- Design Planning: Begin by determining the size and layout of your conveyor. Consider the space where it will be used and the size of items it will transport. Sketch your design, noting the dimensions of the frame and the spacing between rollers.
- Frame Construction: Cut your metal or wood to the desired lengths for the frame. Assemble the frame using brackets and screws, ensuring it is sturdy and level. The frame’s stability is crucial for the smooth operation of your roller conveyor with plastic rollers.
- Preparing PVC Rollers: Cut the PVC pipes to your desired roller length. Ensure each piece is cut straight to avoid wobbling. Sand the edges to remove any burrs for safe handling.
- Installing Bearings and Axles: Insert bearings into each end of the PVC pipes. The bearings should fit snugly to ensure smooth rotation. Slide an axle through the bearings. These axles will rest on brackets attached to the frame, allowing the rollers to spin freely.
- Mounting Rollers to the Frame: Attach brackets to the frame at the appropriate intervals to hold the axles. Position the PVC rollers on the axles and secure them in place. Ensure there is minimal friction and the rollers can turn freely.
- Final Adjustments and Testing: Once all rollers are mounted, test the conveyor by manually rolling an item along it. Make any necessary adjustments to ensure smooth movement. Check for any areas where friction might be increased and apply lubrication if needed.
Safety Precautions:
- Wear protective gear (gloves, safety glasses) during construction to prevent injuries.
- Ensure all tools are used according to the manufacturer’s instructions.
- When cutting or drilling, secure materials properly to prevent slipping.
Building your own roller conveyor with plastic rollers can be a fulfilling DIY project that provides a customized solution for your material handling needs. By following these steps and adhering to safety precautions, you can construct a functional and efficient conveyor system tailored to your specific requirements.
Roller Conveyor Accessories and Additional Features for Roller Conveyor with Plastic Rollers
When optimizing the functionality of roller conveyor with plastic rollers, incorporating specific accessories and additional features can significantly enhance their efficiency and adaptability to various operational needs. Below are some beneficial extras and special conveyor types, along with examples of their applications:
Beneficial Extras:
- Roller Conveyor Tables: These tables are designed to extend the surface area of your conveyor system, providing additional space for sorting, assembly, or inspection tasks. They are particularly useful in packaging and assembly lines where additional workspace is required adjacent to the moving conveyor.
- Side Guides: Installing side guides along the edges of roller conveyors with plastic rollers ensures that goods are correctly aligned and do not veer off the path. This is essential in automated systems where precise placement is critical for downstream operations.
- Conveyor Belts: For roller conveyors that handle very small items or those that need to be transported in specific orientations, attaching a belt over the plastic rollers can prevent slippage and misalignment, ensuring smooth transport from start to finish.
- Adjustable Stands: Adjustable stands allow the height of the conveyor to be modified according to the operational requirements. This flexibility is crucial in facilities where the conveyor needs to interface with other equipment of varying heights.
- Roller Stops and Brakes: These accessories can be installed to control the flow of goods, allowing them to be stopped at specific points along the conveyor for inspection, processing, or accumulation before moving on.
Special Types of Conveyors:
- Gravity Roller Conveyors with Plastic Rollers: These conveyors rely on gravity to move items along, making them an energy-efficient option. They are best suited for operations where products can move smoothly downhill or along a flat surface with minimal force.
- Flexible Roller Conveyors: These conveyors are designed to be extendable and flexible, allowing them to be adjusted in length and sometimes curved paths. They’re ideal for warehouses and loading docks where space is a premium and the paths of goods need to be changed frequently.
- Accumulation Conveyors: Equipped with mechanisms that allow products to accumulate at certain points without causing back pressure or damage. They’re perfect for staging areas before packaging or shipping.
- Powered Roller Conveyors: These are fitted with motors to move goods along at a consistent speed, which is essential for synchronizing different parts of the production process. They are particularly useful when transporting heavy loads or when precise control over the speed of movement is required.
- Ball Transfer Tables: Although not a conveyor in the traditional sense, ball transfer tables complement roller conveyors by allowing goods to be rotated or redirected manually with minimal effort. They’re often used at packaging stations or in areas where goods need to be oriented differently.
Incorporating these accessories and features into roller conveyor with plastic rollers can significantly increase their utility, making them more adaptable to the specific needs of a wide range of industrial applications. From enhancing operational efficiency to ensuring the safe transport of goods, these additions are invaluable for optimizing conveyor systems.
Where to Buy Roller Conveyor with Plastic Rollers
For businesses and individuals in the market for roller conveyors with plastic rollers, whether new or used, there are several purchasing options available. Each option offers its own advantages, from personalized service to a wide selection of products. Here’s a look at where you can find these versatile conveyors:
Online Retailers:
Online marketplaces and specialized e-commerce sites are prime destinations for buying roller conveyors with plastic rollers. These platforms offer a broad range of products from various manufacturers, allowing for easy comparison of specifications, prices, and reviews. Benefits include convenience, competitive pricing, and direct shipping to your facility. Popular online retailers include Amazon, eBay, and Alibaba, as well as industry-specific sites such as Uline and Global Industrial.
Manufacturers’ Websites:
Purchasing directly from the manufacturer’s website can provide access to the latest models of roller conveyors with plastic rollers and bespoke solutions tailored to specific industry needs. This option often allows for customization in terms of size, roller type, and conveyor configuration. Manufacturers also provide expert advice, installation services, and after-sales support.
Industrial Supply Companies:
Companies specializing in industrial equipment offer a range of roller conveyors with plastic rollers. Companies like Grainger, MSC Industrial Supply, and Fastenal have both online and physical stores, providing the flexibility of browsing products online and the option to speak with a sales representative for personalized advice.
Local Dealers and Distributors:
For those who prefer to inspect the conveyor systems in person before making a purchase, local dealers and distributors offer this opportunity. They typically have showrooms where customers can view different models of roller conveyor with plastic rollers, ask questions, and arrange for delivery and installation services. Local dealers are also a good source for purchasing used equipment, often providing maintenance and refurbishment services to ensure the conveyor is in good working condition.
Trade Shows and Industrial Expos:
Trade shows and industrial expos are excellent venues for exploring a wide variety of roller conveyors with plastic rollers. These events allow you to see the latest innovations in conveyor technology, compare products from different vendors, and negotiate deals directly with manufacturers or distributors. Additionally, trade shows offer networking opportunities with industry experts and peers who can provide insights and recommendations.
When looking to purchase roller conveyor with plastic rollers, it’s important to consider the specific requirements of your operation, including the size, weight, and type of materials to be transported. Whether opting for the convenience of online shopping, the personalized service of local dealers, or the direct access to manufacturers, there are ample options to find the perfect conveyor solution to meet your needs.
FAQs About Roller Conveyor with Plastic Rollers
Plastic rollers are cylindrical components made from various types of plastic materials, designed to facilitate the smooth movement of items across a surface. They are a crucial part of roller conveyors, where they are mounted within a frame to support and transport goods with minimal effort. Plastic rollers are celebrated for their lightweight, corrosion-resistant properties, and their ability to operate quietly compared to metal rollers. They come in different sizes and types, each suited for specific applications based on weight capacity, environmental conditions, and desired friction levels. Their use spans a wide range of industries, including manufacturing, logistics, and retail, optimizing workflows and enhancing efficiency in material handling processes.
Conveyors utilize various types of rollers to transport materials smoothly and efficiently. The choice of roller type often depends on the application, load requirements, and environmental factors. The most common types include:
Plastic Rollers: Used for their lightweight, corrosion-resistant properties, ideal for light to medium loads.
Steel Rollers: Preferred for their strength and durability, suitable for heavy loads and high-impact applications.
Rubber-Coated Rollers: These provide added grip and reduce noise, making them suitable for delicate or slippery items.
Grooved Rollers: Designed to handle belts for powered conveyor systems, ensuring the belt stays in place.
Stainless Steel Rollers: Best for corrosive environments such as food processing or chemical industries.
Each type of roller offers distinct advantages, and the choice will largely depend on the specific needs of the conveyor system, including the materials being transported and the environment in which the conveyor operates.
The best plastic material for rollers depends on the specific requirements of the application, including load capacity, environmental conditions, and the need for resistance to chemicals or wear. Common plastics used include:
Polypropylene (PP): Known for its excellent chemical resistance and lightweight properties, suitable for light to medium loads.
High-Density Polyethylene (HDPE): Offers great impact resistance and durability, ideal for harsh operating conditions.
Ultra-High Molecular Weight Polyethylene (UHMWPE): Provides outstanding wear resistance and low friction, perfect for heavy-duty applications.
Nylon: Offers a good balance of strength and wear resistance, suitable for applications requiring durability and reduced friction.
Acetal (Delrin): Known for its low friction and high stiffness, ideal for precision applications requiring smooth operation.
Each material offers unique benefits, and the selection should be based on a thorough assessment of the conveyor system’s operational requirements.
A flexible roller conveyor is designed for versatility and adaptability, featuring segments that can be expanded, contracted, and curved to fit various spaces and applications. This type of conveyor is especially useful in environments where space is limited or the layout requires frequent changes. Common uses include:
Loading and Unloading: Ideal for dock areas where space is at a premium, and paths may need to be adjusted based on the vehicle or cargo.
Packaging and Assembly Lines: Flexible conveyors can be reconfigured to accommodate changes in production processes or to connect different stages of assembly and packaging.
Distribution Centers: They can adapt to various space requirements, facilitating the movement of goods between different areas or levels.
Retail and Order Fulfillment: Offers the flexibility needed to adjust to changing inventory locations and packing stations.
Event Logistics: Perfect for temporary setups where conveyance systems need to be deployed quickly and adapted to different spaces.
The flexibility and ease of reconfiguration make flexible roller conveyors a valuable tool in dynamic operational environments where adaptability is key to efficiency.
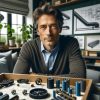
Jordan Smith, a seasoned professional with over 20 years of experience in the conveyor system industry. Jordan’s expertise lies in providing comprehensive solutions for conveyor rollers, belts, and accessories, catering to a wide range of industrial needs. From initial design and configuration to installation and meticulous troubleshooting, Jordan is adept at handling all aspects of conveyor system management. Whether you’re looking to upgrade your production line with efficient conveyor belts, require custom conveyor rollers for specific operations, or need expert advice on selecting the right conveyor accessories for your facility, Jordan is your reliable consultant. For any inquiries or assistance with conveyor system optimization, Jordan is available to share his wealth of knowledge and experience. Feel free to reach out at any time for professional guidance on all matters related to conveyor rollers, belts, and accessories.