Selecting the Right Plastic Conveyor Roller Bearings for Your System
Plastic conveyor roller bearings have revolutionized the way industries handle materials and products on conveyor systems. These bearings, made from durable plastic materials, offer a lightweight, corrosion-resistant, and low-maintenance solution for smooth and efficient conveyor operations. The evolution of conveyor bearings from traditional metal to plastic materials highlights the industry’s shift towards more sustainable and cost-effective solutions. Plastic materials not only reduce the overall weight of the conveyor system, enhancing energy efficiency, but also offer excellent resistance to environmental factors, making plastic conveyor roller bearings a preferred choice in sectors such as food processing, packaging, and manufacturing. Their significance extends beyond just functionality; they represent a move towards innovative, high-performance materials in conveyor technology.
Key Manufacturers and Suppliers of Plastic Conveyor Roller Bearings
In the realm of industrial machinery, plastic conveyor roller bearings stand out as pivotal components, ensuring the smooth and efficient operation of conveyor systems. These bearings are specifically designed to withstand the rigors of conveyor applications, offering durability, reduced maintenance, and a quieter operation compared to their metal counterparts. This article delves into the key manufacturers and suppliers of plastic conveyor roller bearings, spotlighting 8 leading entities in this sector, including notable bridge bearing suppliers and UK bearing manufacturers.
Leading Manufacturers and Suppliers
- Markes Bearings & Specialties Ltd.: Renowned for their innovative approach, Markes Bearings & Specialties Ltd. has carved a niche in the market with their high-quality plastic conveyor roller bearings. Their product range is celebrated for its durability and efficiency, making them a preferred choice among various industries.
- Bridgeway Technologies Inc.: As a prominent bridge bearing supplier, Bridgeway Technologies Inc. has expanded its expertise into the realm of conveyor bearings, offering specialized plastic conveyor roller bearings that are designed for heavy-duty applications, ensuring longevity and reliability.
- UK Bearings Ltd.: Standing out among UK bearing manufacturers, UK Bearings Ltd. offers a diverse array of plastic conveyor roller bearings tailored to meet the specific needs of different conveyor systems, emphasizing customization and quality.
- Polymer Bearing Solutions Co.: Specializing in plastic bearings, Polymer Bearing Solutions Co. provides a wide range of plastic conveyor roller bearings that are known for their corrosion resistance and lightweight properties, enhancing conveyor system efficiency.
- ConveyorTech Industries: With a focus on conveyor components, ConveyorTech Industries offers plastic conveyor roller bearings that are engineered for optimal performance, reducing downtime and maintenance costs for businesses.
- Advanced Bearing Materials LLC: This company is at the forefront of material innovation, producing plastic conveyor roller bearings that are not only durable but also capable of operating in extreme environments, making them suitable for a wide range of industrial applications.
- EcoRoll Bearing Corp.: EcoRoll Bearing Corp. is dedicated to sustainability, offering eco-friendly plastic conveyor roller bearings that do not compromise on performance, catering to environmentally conscious businesses.
- Precision Polymer Engineering: Known for their precision-engineered products, Precision Polymer Engineering provides plastic conveyor roller bearings that are highly accurate and reliable, ensuring smooth operations in various conveyor systems.
Diversity of Offerings
Each of these 8 brands brings something unique to the table, from Markes Bearings’ focus on innovation to Bridgeway Technologies’ expertise in heavy-duty applications. The diversity in their offerings ensures that businesses can find the perfect plastic conveyor roller bearings to meet their specific requirements, whether they are looking for durability, customization, eco-friendliness, or precision engineering.
The landscape of plastic conveyor roller bearings is rich with variety and innovation, thanks to the contributions of these key manufacturers and suppliers. Their commitment to quality, diversity, and specialized solutions continues to drive advancements in conveyor technology, making operations smoother and more efficient across various industries.
Types of Plastic Conveyor Roller Bearings
Plastic conveyor roller bearings play a pivotal role in the efficient operation of conveyor systems, offering a lightweight, corrosion-resistant, and cost-effective solution for facilitating smooth motion. These bearings are designed to withstand various operational environments, from light-duty applications to the most demanding industrial settings. Below, we delve into the different series and types of plastic conveyor roller bearings, highlighting their unique features and applications.
Introduction to Different Series and Types
Plastic conveyor roller bearings come in various series and types, each tailored for specific applications and operational demands. Two notable series are the KTES and KTS, which are distinguished by their design, material composition, and intended use. Here’s a closer look at these series:
Series | Description | Applications |
---|---|---|
KTES | Engineered for high load capacities and durability, KTES bearings are made from advanced thermoplastic materials. | Suitable for heavy-duty applications such as mining conveyors, automotive assembly lines, and packaging machinery. |
KTS | Designed for lighter loads, KTS bearings offer excellent wear resistance and low friction. | Ideal for food processing equipment, pharmaceutical conveyors, and other clean or light-duty environments. |
Heavy-Duty Plastic Conveyor Roller Bearings
Heavy-duty plastic conveyor roller bearings are specifically designed to endure the rigors of demanding industrial environments. These bearings are constructed from high-performance plastics that can withstand high loads, abrasive materials, and corrosive chemicals. Their robust design ensures longevity and reliability in applications where metal bearings might fail due to rust or wear.
Applications of heavy-duty plastic conveyor roller bearings include:
- Mining and Quarrying: In the abrasive and dusty conditions of mining and quarry operations, heavy-duty plastic bearings offer resistance to particulate ingress and reduced maintenance needs.
- Agricultural Equipment: Farm machinery requires bearings that can handle exposure to dirt, moisture, and corrosive materials. Heavy-duty plastic bearings meet these needs with their durability and corrosion resistance.
- Food Processing: In environments where cleanliness and resistance to corrosive cleaning agents are paramount, these bearings provide a non-corrosive, easily cleanable solution.
- Marine Applications: The marine environment demands bearings that can resist saltwater corrosion. Heavy-duty plastic bearings are ideal for this application due to their inherent resistance to salt and water.
- Packaging Machinery: High-speed packaging lines need bearings that can endure continuous operation and varying loads without failure. Heavy-duty plastic bearings offer the required durability and reliability.
- Airport Baggage Handling: The constant load and high throughput of airport baggage systems necessitate bearings that can withstand heavy loads and continuous operation.
- Automotive Manufacturing: The automotive production line, with its heavy components and high precision requirements, benefits from the robustness and reliability of heavy-duty plastic bearings.
- Recycling Facilities: The harsh conditions and varying materials handled in recycling plants require bearings that are resistant to abrasion and capable of handling heavy loads.
In each of these applications, heavy-duty plastic conveyor roller bearings provide a solution that balances performance with durability, ensuring that conveyor systems can operate efficiently and with minimal downtime, even in the most challenging conditions.
Innovative Features and Advancements in Plastic Conveyor Roller Bearings
The realm of plastic conveyor roller bearings is witnessing significant innovations and advancements, aimed at enhancing performance, durability, and operational efficiency. These developments are not just about the materials used but also about the engineering designs and features that make these bearings more adaptable, reliable, and suited to a wide range of industrial applications. Let’s delve into some of the innovative features and advancements that are setting new standards in the performance of plastic conveyor roller bearings.
Refined Grooved Ball Bearings
One of the key advancements in the design of plastic conveyor roller bearings is the introduction of refined grooved ball bearings. These bearings are engineered with precision grooves that significantly reduce friction and wear, thereby enhancing the bearing’s efficiency and lifespan. The grooves are meticulously designed to ensure that the balls roll smoothly within the bearing, minimizing resistance and energy consumption. This innovation is particularly beneficial in applications where speed and load capacity are critical factors, as it ensures that the conveyor system operates smoothly and reliably over extended periods.
DIN Ball Bearings for Enhanced Performance
Another notable advancement is the integration of DIN (Deutsches Institut für Normung) standard ball bearings into plastic conveyor roller bearings. DIN standards are globally recognized for ensuring high quality, reliability, and compatibility. By incorporating DIN ball bearings, manufacturers are able to offer products that meet stringent international standards for performance and durability. These bearings are designed to withstand higher loads and speeds, making them ideal for demanding industrial applications. The precision and quality control associated with DIN standards also mean that these bearings offer superior performance and a longer service life.
Corrosion-Resistant 316 Stainless Balls in Maintenance-Free Operations
The use of corrosion-resistant 316 stainless steel balls in plastic conveyor roller bearings is a significant advancement towards maintenance-free operations. Stainless steel 316 is known for its excellent resistance to corrosion and rust, making it an ideal choice for bearings used in harsh or corrosive environments. This material ensures that the bearings remain operational even when exposed to water, chemicals, or other potentially damaging substances. The incorporation of 316 stainless balls in plastic conveyor roller bearings not only extends the life of the bearings but also reduces the need for frequent maintenance and replacement, thereby lowering operational costs and downtime.
The innovative features and advancements in plastic conveyor roller bearings, such as refined grooved ball bearings, DIN ball bearings, and the use of corrosion-resistant 316 stainless balls, are revolutionizing the way these bearings are used in conveyor systems. These innovations enhance performance, durability, and operational efficiency, making plastic conveyor roller bearings more adaptable and reliable for a wide range of industrial applications. As technology continues to evolve, we can expect to see further improvements that will set new benchmarks in the design and functionality of plastic conveyor roller bearings.
Compatibility and Applications of Plastic Conveyor Roller Bearings
The versatility and adaptability of plastic conveyor roller bearings are key factors that contribute to their widespread use across various industries. These bearings are designed to be compatible with standard industrial tube and pipe sizes, ensuring they can be easily integrated into existing conveyor systems without the need for extensive modifications. This section explores the compatibility of plastic conveyor roller bearings with common conveyor components and highlights 8 specific applications where these bearings excel.
Compatibility with Industrial Tubes and Pipes
Plastic conveyor roller bearings are engineered to fit seamlessly within a wide range of industrial tube and pipe diameters. This compatibility is crucial for ensuring that the bearings can be used in a diverse array of conveyor systems, from small-scale assembly lines to large-scale distribution centers. Manufacturers typically offer bearings that are designed to fit standard tube sizes, such as those specified in the ISO, ASTM, and DIN standards, among others. This universal design approach allows for the easy replacement of bearings in existing systems and simplifies the process of designing new conveyor setups.
Applications in Conveyor Systems
- Gravity Roller Conveyors: These conveyors rely on gravity to move items across flat or slightly inclined paths. Plastic conveyor roller bearings are ideal for this application due to their low friction and durability, ensuring smooth movement of goods.
- Driven Rollers: In conveyor systems where rollers are powered, either by belts, chains, or motorized drives, plastic conveyor roller bearings provide the necessary low-friction rotation, enabling efficient and consistent movement of items.
- Packaging Lines: Packaging operations benefit from the use of plastic conveyor roller bearings due to their quiet operation and resistance to corrosion, which is particularly useful in food and pharmaceutical packaging environments.
- Sorting Systems: Automated sorting systems, which are essential in distribution centers and logistics operations, rely on plastic conveyor roller bearings for their precision and reliability, ensuring accurate and efficient sorting of items.
- Assembly Lines: In manufacturing settings, assembly lines utilize plastic conveyor roller bearings for their smooth operation and ability to withstand repetitive motions, contributing to a streamlined production process.
- Food Processing: The corrosion-resistant properties of plastic conveyor roller bearings make them suitable for food processing applications, where exposure to water and cleaning agents is common.
- Airport Baggage Handling: The durability and low maintenance requirements of plastic conveyor roller bearings are advantageous in the demanding environment of airport baggage handling systems.
- Agricultural Equipment: In agricultural settings, where equipment is often exposed to dirt, moisture, and corrosive materials, plastic conveyor roller bearings offer a robust solution that can withstand harsh conditions.
The compatibility of plastic conveyor roller bearings with standard industrial tubes and pipes, combined with their versatility across a wide range of applications, underscores their importance in the efficient operation of conveyor systems. From gravity rollers to complex sorting systems, these bearings provide the reliability, durability, and performance necessary to meet the demands of various industries. As conveyor technology continues to evolve, the role of plastic conveyor roller bearings in facilitating smooth and efficient material handling is set to remain indispensable.
Accessories and Spare Parts for Plastic Conveyor Roller Bearings
Ensuring the longevity and efficiency of conveyor systems involves not just selecting the right plastic conveyor roller bearings but also equipping them with the appropriate accessories and spare parts. This comprehensive approach guarantees that the conveyor system remains operational, minimizes downtime, and maintains efficiency across various applications.
Introduction to the Wide Range of Accessories and Conveyor Spare Parts
The ecosystem of accessories and spare parts for plastic conveyor roller bearings is vast, catering to the diverse needs of different conveyor systems. These components range from simple seals and shields that protect the bearings from contaminants and moisture, to more complex parts like adapter sleeves and housing units that facilitate the precise mounting of bearings. Additionally, lubrication options such as grease fittings can be critical for certain applications, ensuring that bearings operate smoothly over their service life.
Key accessories and spare parts include:
- Seals and Shields: These prevent the ingress of dust, dirt, and moisture, which can degrade the performance of the bearings and lead to premature failure.
- Adapter Sleeves: Used to secure bearings onto shafts of varying diameters, ensuring a tight and precise fit.
- Housing Units: Provide a protective enclosure for the bearings, supporting them and aligning them correctly in the conveyor system.
- Lubrication Fittings: Essential for the maintenance of bearings, allowing for the easy application of lubricants to reduce friction and wear.
Importance of Having the Right Parts for Maintenance and Efficiency
The availability and selection of the right accessories and spare parts for plastic conveyor roller bearings are crucial for several reasons:
- Maintenance: Regular maintenance is vital for the longevity of conveyor systems. Having the right spare parts on hand reduces downtime, allowing for quick replacements and repairs.
- Efficiency: Properly maintained bearings with the correct accessories operate more efficiently, reducing energy consumption and wear on the conveyor system.
- Cost Savings: Investing in quality spare parts and accessories can lead to significant cost savings over time. By extending the life of the conveyor system and reducing the need for frequent replacements, companies can lower their operational costs.
- Customization: The wide range of accessories allows for the customization of conveyor systems to meet specific operational requirements, enhancing performance and adaptability to different environments.
The role of accessories and spare parts in the maintenance and efficiency of plastic conveyor roller bearings cannot be overstated. By ensuring that the right components are available and utilized, businesses can significantly improve the performance and reliability of their conveyor systems, leading to smoother operations and reduced maintenance costs.
Choosing the Right Plastic Conveyor Roller Bearings for Your Conveyor System
Selecting the appropriate plastic conveyor roller bearings is a critical decision that can significantly impact the efficiency, reliability, and overall performance of your conveyor system. Given the variety of conveyor types and the diverse applications they serve, understanding how to choose the right bearings is essential. This guide will provide insights into making informed decisions and the importance of consulting with manufacturers or suppliers for precise dimensions and specifications.
Guide on Selecting the Appropriate Bearings
When it comes to choosing the right plastic conveyor roller bearings, several factors need to be considered to ensure compatibility with your conveyor system and its intended application. Here are key considerations:
- Load Capacity: Assess the maximum load the conveyor will carry. Bearings must be selected based on their ability to support the load without compromising performance or lifespan.
- Speed Requirements: The operational speed of the conveyor affects the choice of bearings. High-speed applications may require bearings designed for minimal friction and heat generation.
- Environmental Conditions: Consider the environment in which the conveyor will operate. Factors such as temperature, moisture, exposure to chemicals, and the presence of abrasive materials dictate the need for bearings made from materials that can withstand these conditions.
- Maintenance and Durability: Opt for bearings that offer ease of maintenance and durability, especially in applications where downtime can be costly. Bearings with self-lubricating features or those made from materials resistant to wear and corrosion can be advantageous.
- Compatibility: Ensure that the bearings are compatible with the existing conveyor system components, such as shafts and roller tubes. This includes considering the dimensions, mounting configurations, and any specific design requirements.
Tips on Consulting with Manufacturers or Suppliers
- Provide Detailed Requirements: When consulting with manufacturers or suppliers, be clear about your conveyor system’s specific needs, including load, speed, and environmental conditions.
- Ask for Custom Solutions: If standard bearings do not meet your requirements, inquire about custom-designed bearings that can offer a better fit for your application.
- Seek Technical Support: Leverage the technical expertise of manufacturers or suppliers to understand the nuances of bearing selection and application.
- Consider Future Needs: Discuss potential future changes in your conveyor system’s operation that might affect the bearing requirements, ensuring that your choice is scalable and adaptable.
- Quality Assurance: Inquire about the quality testing and assurance processes in place for the bearings. Opt for products that come with a warranty or guarantee for added peace of mind.
- Cost vs. Value: While cost is an important consideration, focus on the value that the bearings will bring to your operation in terms of reliability, durability, and maintenance savings.
- Lead Times and Availability: Confirm the availability and lead times for the bearings to ensure they meet your project timelines.
- After-Sales Support: Check the level of after-sales support offered, including technical assistance, availability of spare parts, and the process for handling any issues that may arise.
Choosing the right plastic conveyor roller bearings requires careful consideration of your conveyor system’s specific needs and consulting with experts to ensure that the bearings you select will deliver optimal performance and value. By following these guidelines and leveraging the expertise of manufacturers or suppliers, you can make an informed decision that enhances the efficiency and reliability of your conveyor system.
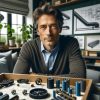
Jordan Smith, a seasoned professional with over 20 years of experience in the conveyor system industry. Jordan’s expertise lies in providing comprehensive solutions for conveyor rollers, belts, and accessories, catering to a wide range of industrial needs. From initial design and configuration to installation and meticulous troubleshooting, Jordan is adept at handling all aspects of conveyor system management. Whether you’re looking to upgrade your production line with efficient conveyor belts, require custom conveyor rollers for specific operations, or need expert advice on selecting the right conveyor accessories for your facility, Jordan is your reliable consultant. For any inquiries or assistance with conveyor system optimization, Jordan is available to share his wealth of knowledge and experience. Feel free to reach out at any time for professional guidance on all matters related to conveyor rollers, belts, and accessories.