Comprehensive Protection with Rubber Impact Rollers
In the dynamic arena of the conveying equipment industry, rubber impact rollers stand out as pivotal components designed to enhance the efficiency and longevity of conveyor systems. These rollers, characterized by their robust construction and the strategic incorporation of rubber elements, play a crucial role in managing the physical stress and impacts experienced during material handling operations. The significance of a rubber impact roller cannot be overstated; it ensures the smooth transition of materials across various stages of processing and transportation, minimizing wear and tear on the conveyor belt and thereby extending its service life. This not only promotes operational efficiency but also substantially reduces the need for frequent maintenance and replacements, driving down operational costs. The indispensability of rubber impact rollers in material handling systems highlights their critical role in optimizing conveyor performance, safeguarding the integrity of transported goods, and enhancing overall system reliability. This foundational understanding sets the stage for deeper exploration into the nuances of selecting, implementing, and maintaining these essential components within a myriad of industrial applications.
What are Rubber Impact Rollers?
Definition and Core Characteristics
Rubber impact rollers are specialized components designed for use in conveyor systems, where they significantly contribute to the longevity and efficiency of the material handling process. Featuring a robust core surrounded by thick, impact-absorbing rubber, these rollers are engineered to withstand substantial loads and repeated impacts. The heavy-duty nature of a rubber impact roller makes it ideally suited for critical points along the conveyor line, such as loading zones and transfer points, where materials are dropped from height, potentially causing wear or damage to the system.
Role and Functionality in Conveyor Systems
Impact Absorption and Protection
The primary function of a rubber impact roller is to absorb the kinetic energy generated when materials are dropped onto the conveyor belt, minimizing the risk of damage to the belt surface and structure. By dissipating impact forces, these rollers play a pivotal role in extending the service life of the conveyor system. The protective layer of rubber not only cushions the blow but also reduces the noise and vibration associated with material loading, contributing to a safer and more pleasant working environment.
Enhanced Conveyor Efficiency and Longevity
Installation of rubber impact rollers at critical points along the conveyor belt assists in maintaining the integrity and alignment of the belt, ensuring smooth and uninterrupted operation. This efficiency in operation minimizes downtime caused by maintenance and repairs, leading to increased productivity. Moreover, by protecting the belt from premature wear and tear, rubber impact rollers contribute to the overall longevity of the conveyor system, making them a cost-effective solution for businesses looking to optimize their material handling operations.
Rubber impact rollers are indispensable components within conveyor systems, with a design that emphasizes durability and an operational role focused on protection and efficiency. Their inclusion in material handling systems underscores a commitment to maintaining the quality and longevity of conveyor belts, ultimately contributing to the operational effectiveness and cost-efficiency of industrial operations.
Rubber Impact Roller Key Components and Design
Aspect | Description |
---|---|
Industry Standards | Rubber impact rollers are designed according to industry-defined standards. These standards specify the dimensions, material quality, and operational capabilities of the rollers, ensuring compatibility and performance. |
Customization | Despite adhering to industry standards, manufacturers offer customization options to meet specific application needs. Variations can include rubber compound hardness, disc thickness, and disc spacing to optimize performance. |
The construction and design of a rubber impact roller highlight a balance between standardization and customization. This balance ensures that while the rollers are universally dependable, they can also be precisely adapted to enhance performance and longevity in specific applications. The deliberate assembly of rubber discs on a durable steel core, guided by industry standards but flexible to customization, underpins the roller’s ability to protect conveyor systems effectively across a vast array of industrial contexts.
Applications of Rubber Impact Rollers
Rubber impact rollers are instrumental in enhancing the efficiency and durability of conveyor systems. Their applications span across various crucial areas, prominently including loading zones and transfer point applications. Through their design and functionality, these rollers play a pivotal role in safeguarding the conveyor belt against potential damages arising from material impacts. Let’s delve deeper into the specifics of their applications and protective capabilities.
Utilization in Loading Zones
Loading zones are areas of heightened stress for conveyor systems, where materials are typically dropped from a height onto the conveyor belt. This activity subjects the belt and its support system to substantial impact forces, which can lead to premature wear and tear or even immediate damage if not properly managed. The deployment of a rubber impact roller in these zones illustrates a proactive approach to preserving the integrity of the conveyor system. These rollers, with their robust design featuring rubber discs mounted on a durable steel core, absorb the energy from falling materials, significantly mitigating the stress encountered by the conveyor belt. As such, the installation of rubber impact rollers in loading zones is a strategic move to extend the lifespan of the conveyor belt and minimize maintenance requirements.
Application in Transfer Point Applications
Transfer points represent another critical juncture within conveyor systems where materials are transferred from one belt to another, or from a different type of machinery onto the belt. The dynamics of this process often introduce additional impact forces and abrasion risks to the conveyor belt. Rubber impact rollers are strategically placed at these points to absorb and dissipate the energy generated during material transfer, thereby minimizing the potential for belt damage. By cushioning the point of impact, these rollers not only protect the belt but also contribute to a smoother transition of materials, enhancing the overall efficiency of the conveyor system.
Protection of the Conveyor Belt from Material Impact
The fundamental design and operational principle of a rubber impact roller revolve around its capacity to protect the conveyor belt from the damaging effects of material impact. By absorbing the shock and distributing the forces more evenly across their surface, these rollers significantly reduce localized stress and abrasion on the belt. This protective mechanism is crucial in extending the operational life of the conveyor belt, reducing downtime for repairs and replacements, and consequently, lowering operational costs. In essence, the rubber impact roller acts as a guardian of the conveyor belt, ensuring its longevity and optimal performance in the face of routine challenges encountered during material handling processes.
Rubber impact rollers are vital components in conveyor systems, particularly in high-impact areas such as loading zones and transfer points. Their ability to absorb and mitigate impact forces serves as a safeguard against conveyor belt damage, underscoring their importance in maintaining operational efficiency and reducing maintenance needs in various material handling applications.
Types of Rubber Impact Rollers
Distinct applications and varying environmental conditions necessitate the availability of different types of rubber impact rollers. These range from special-design varieties built to meet specific operational or environmental demands to the versatile impact troughing idlers, recognized for preventing build-up of sticky material on the conveyor system.
Special-Design Rubber Impact Rollers
The special-design rubber impact roller is tailored to address unique circumstances or challenges that standard designs may not handle optimally. Examples include:
- Waterproof Rollers: These are designed to prevent intrusion of water that could compromise the roller’s operation or lifespan, typically used in applications involving water or high humidity.
- Rollers for Extreme Climate Conditions: In regions with extremely high or low temperatures, ordinary rubber may lose its desirable properties. These rubber impact rollers utilize special compounds to maintain their resilience and effectiveness.
- High-Speed Rollers: For applications involving fast-moving conveyor belts, these rollers are balanced and assembled to minimize vibration, extending their operational life and preventing potential wear on the conveyor system.
- Low-Noise Rollers: In environments where noise control is essential, these rollers are optimized for quiet operation, reducing the overall noise output of the conveyor system.
- Chemical-Resistant Rollers: For applications that involve corrosive or otherwise chemically harsh conditions, these rollers are designed with materials resistant to chemical degradation, maintaining their performance and durability despite the severe operating conditions.
Impact Troughing Idlers
Impact troughing idlers are a variant of the rubber impact roller that excels in environments where sticky materials that could adhere to the conveyor belt are handled. They feature tough yet flexible rubber discs that not only absorb the impact of falling materials but also flex sufficiently to dislodge any accumulated substances, preventing build-up. With their unique trough-shaped arrangement, these rollers also maximize the conveyor belt’s carrying capacity. This design, combined with the efficient shedding of sticky substances, contributes to maintaining the operational efficiency and longevity of the conveyor system under challenging conditions.
The range of rubber impact roller types showcases the adaptability of this component to various operational demands and environmental conditions. With their customizable design options and the specialized capabilities of variants such as the impact troughing idlers, rubber impact rollers continue to play a vital role in the diverse range of applications across the material handling industry.
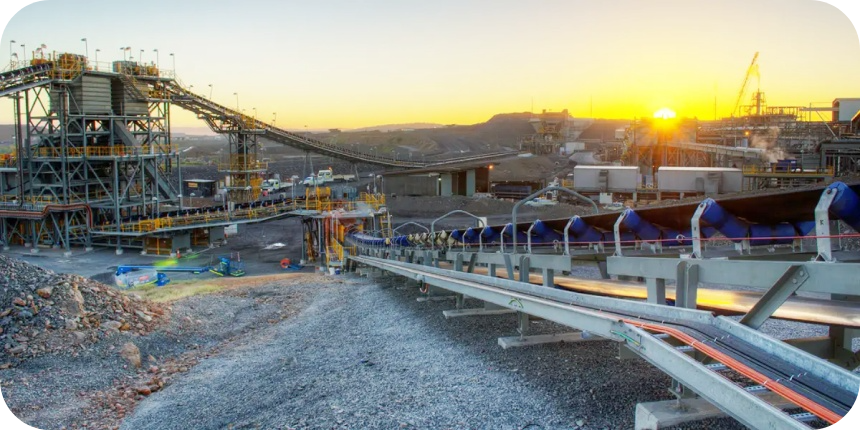
Rubber Impact Roller Selection Guide
Selecting the right rubber impact roller is critical to ensuring the efficiency, longevity, and reliability of conveyor systems. This guide outlines the essential factors to consider when choosing rubber impact rollers for carrying roller conveyor belts, return roller conveyors, idler rollers for belt conveyors, and guide roller conveyors. Moreover, it highlights the significance of application needs and environmental conditions, guiding users towards making informed decisions that result in optimal conveyor system performance.
Factors to Consider When Selecting Rubber Impact Rollers
A multitude of factors must be taken into account to ensure the selection of the most suitable rubber impact roller for your specific application, including:
- Type of Conveyor System: Different types of conveyor systems, such as carrying roller conveyor belts, return roller conveyors, idler rollers for belt conveyors, and guide roller conveyors, have distinct requirements that influence the selection of rubber impact rollers. The role of the roller within the conveyor system (e.g., reducing belt wear, absorbing impact at loading points) will guide the choice of roller design and material composition.
- Load Characteristics: Consider the size, weight, and the nature of the materials being transported. Heavier loads or materials with sharp edges require more durable rollers with high-impact absorption qualities to prevent damage to the conveyor belt and the rollers themselves.
- Operating Speed: The speed at which the conveyor will operate influences the selection of rollers. High-speed applications may necessitate rollers designed to minimize vibration and noise.
- Environmental Conditions: Temperature, humidity, exposure to chemicals, and weather conditions are critical environmental factors that impact the choice of rubber impact rollers. For example, extreme temperatures might require rollers made from special rubber compounds designed to retain their properties under such conditions.
The Importance of Application Needs and Environmental Conditions
Understanding specific application needs and environmental conditions is paramount to selecting the right rubber impact roller. This involves:
- Assessing Application Requirements: Consider the unique challenges and requirements of the application, such as the need for low-noise operation, resistance to sticky material build-up, or compatibility with food-grade materials. Each application may demand specific features from the rollers to ensure optimal performance.
- Evaluating Environmental Challenges: The environment in which the conveyor will operate can significantly affect roller longevity and effectiveness. For instance, rollers used in outdoor settings must be able to withstand weather variations, while those used in chemical plants need to resist corrosion. Selecting rollers designed to thrive under your specific environmental conditions will help ensure the durability and efficiency of your conveyor system.
Meticulously considering the various factors outlined in this rubber impact roller selection guide and understanding the particular demands of your application and environment will facilitate the choice of the most appropriate rollers. Such careful selection is essential to optimizing the performance and durability of your conveyor system, ultimately contributing to smoother operations and reduced maintenance costs.
Rubber Impact Roller Installation and Maintenance
To ensure a functional and efficient conveyor system, proper rubber impact roller installation and maintenance are vital. Taking steps to correctly install your rubber impact roller and follow relevant maintenance recommendations will contribute to a long, trouble-free service life of the roller, enhancing the efficiency and reliability of your conveyor system. This guide outlines general steps for their installation and maintenance.
Rubber Impact Roller Installation Guidelines
Correct installation of a rubber impact roller encompasses several steps:
- Understanding the Conveyor System’s Design: Before installing, it’s crucial to understand the design and operation of your conveyor system. This knowledge will guide you on where to place the rubber impact rollers, particularly in high-impact areas, such as loading zones and transfer points.
- Preparing the Installation Site: Ensure that the area where the rubber impact roller will be installed is clean and free from debris. Any physical obstructions in the installation area could negatively affect the performance of the roller and the conveyor system.
- Following Manufacturer’s Instructions: Each rubber impact roller may come with unique installation instructions from the manufacturer—following these procedures guarantees that the roller is mounted correctly and optimally.
- Checking Roller Alignment: After installation, it’s crucial to verify that the rubber impact roller is correctly aligned with the conveyor system’s path. Misalignment can lead to premature wear and tear or potential system failure.
Rubber Impact Roller Maintenance Tips
Regular maintenance promotes a long, trouble-free life for your rubber impact roller:
- Routine Inspection: Regular visual checks can uncover potential issues. Look out for abnormal signs such as excessive roller wear, wobbling during operation, or accumulation of materials on the roller.
- Cleaning: It’s advisable to clean the rubber impact roller periodically to prevent material build-up, which could impair its performance or damage the conveyor belt over time.
- Replace Worn Out Rollers: When signs of significant wear and tear are noticed, prepare to replace the roller. Prolonging usage of a worn-out rubber impact roller can lead to a conveyor system malfunction.
- Follow Manufacturer’s Maintenance Guidelines: Manufacturers often provide detailed maintenance procedures for their products. Following these instructions will help preserve the rubber impact roller’s operational effectiveness and extend its lifespan.
Proper installation and maintenance of a rubber impact roller are paramount to maintaining the optimal performance of your conveyor system. Following these guidelines will significantly contribute to the rubber impact roller’s longevity and the overall efficiency and reliability of your conveyor system.
Rubber Impact Roller Pricing and Acquisition
Understanding the cost implications and acquisition avenues for a rubber impact roller is essential for budgeting and operational planning in industries where conveyor systems are pivotal. This section delves into the nuances of rubber impact roller pricing, highlighting the variables that affect costs, and offers practical advice on locating and procuring used rubber impact rollers—a cost-effective alternative for budget-conscious operations.
Rubber Impact Roller Price Ranges and Cost Influencers
The price of a rubber impact roller can vary widely based on several factors:
- Material Quality and Type: The type of rubber and the quality of materials used in manufacturing the roller significantly influence its price. High-grade, durable rubber materials designed for specific environmental conditions or applications (e.g., high temperature, chemical resistance) often come at a higher cost.
- Size and Complexity: Larger rollers or those with complex designs tailored for specific conveyor configurations tend to cost more due to the increased amount of material and the complexity of manufacturing processes involved.
- Manufacturer and Brand: Prices can also vary between manufacturers and brands. Premium brands known for superior quality and reliability might charge more for their rubber impact rollers compared to lesser-known companies.
- Additional Features: Features such as special coatings for enhanced wear resistance, noise reduction capabilities, or custom engineering to meet specific operational requirements can add to the cost.
Finding and Purchasing Used Rubber Impact Rollers
For operations looking to economize without compromising on functionality, acquiring used rubber impact rollers can be a wise choice. Here are tips on where to find and how to purchase these:
- Industry Auctions and Liquidation Sales: These are excellent venues to find used rubber impact rollers, often at significantly reduced prices. Keep an eye on auctions and sales from closed or restructuring industries similar to yours.
- Online Marketplaces: Websites and forums catering to industrial equipment often list used rubber impact rollers. Sites like eBay, Craigslist, or specialized industrial equipment resellers can be great resources.
- Directly from Companies: Sometimes companies upgrading their conveyor systems sell their old rollers directly. Networking with industry peers can uncover these opportunities.
- Inspect Before Buying: When purchasing used rubber impact rollers, it’s crucial to inspect them thoroughly for wear, damage, or any signs of failure. If possible, seek information about the roller’s operational history and reason for sale.
- Consider Refurbishment: In some cases, used rollers can be refurbished to extend their service life. Investigate refurbishment costs as part of your purchasing decision to ensure it’s economically viable.
Accurately understanding the pricing dynamics of rubber impact rollers and exploring the market for used options can lead to substantial savings and strategic procurement decisions. Armed with knowledge about what influences rubber impact roller costs and how to navigate the acquisition of used rollers, businesses can optimize their conveyor system investments while adhering to budgetary constraints.
Request a Quote: Get pricing information tailored to your needs.
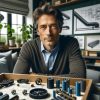
Jordan Smith, a seasoned professional with over 20 years of experience in the conveyor system industry. Jordan’s expertise lies in providing comprehensive solutions for conveyor rollers, belts, and accessories, catering to a wide range of industrial needs. From initial design and configuration to installation and meticulous troubleshooting, Jordan is adept at handling all aspects of conveyor system management. Whether you’re looking to upgrade your production line with efficient conveyor belts, require custom conveyor rollers for specific operations, or need expert advice on selecting the right conveyor accessories for your facility, Jordan is your reliable consultant. For any inquiries or assistance with conveyor system optimization, Jordan is available to share his wealth of knowledge and experience. Feel free to reach out at any time for professional guidance on all matters related to conveyor rollers, belts, and accessories.