Innovative Designs from Your Flat Impact Conveyor Roller Factory
In the vast and varied landscape of industrial operations, conveyor rollers stand as unsung heroes, playing pivotal roles across numerous sectors. From mining and agriculture to manufacturing and logistics, these components ensure the smooth and efficient movement of goods and materials, marking their critical importance in enhancing productivity and operational efficiency. Amidst the diverse types of conveyor rollers, the flat impact conveyor roller factory produces a specific kind that is indispensable in environments where conveyor systems are subject to heavy loads and significant impact. Flat impact conveyor rollers are designed to absorb shocks and distribute forces evenly, protecting the conveyor belt and extending its lifespan. Their unique role in mitigating damage and maintaining the integrity of conveyor systems underlines their value in industrial applications where durability and reliability are paramount.
Comprehensive Guide to Flat Impact Conveyor Roller Factory Products
In the realm of material handling and industrial conveyance, the efficiency and longevity of a conveyor system significantly depend on the types and quality of rollers it employs. Among these, flat impact conveyor rollers stand out for their specialized design and functionality, tailored to mitigate the challenges of handling heavy or impact-intensive loads. Manufactured by dedicated flat impact conveyor roller factories, these components are pivotal in enhancing conveyor performance and durability.
Definition and Explanation of Flat Impact Conveyor Rollers
Flat impact conveyor rollers are a distinct category of conveyor rollers designed to absorb and distribute the forces generated by falling or heavy materials at loading points. Unlike their rounded counterparts, these rollers have a flat surface that interfaces with the conveyor belt, offering unique advantages in specific industrial applications.
- Origin and Manufacturing: Flat impact conveyor rollers are produced by specialized factories, known as flat impact conveyor roller factories, dedicated to creating robust components for conveyor systems. These factories employ advanced engineering and materials science to craft rollers that meet stringent industry standards.
- Design Philosophy: Unlike standard rollers, flat impact conveyor rollers are designed with a flat surface that evenly distributes weight and impact across their width, ensuring a balanced load distribution.
- Material Composition: Typically constructed from heavy-duty materials such as reinforced steel or high-impact polymers, these rollers are built to withstand significant stress without deformation.
- Surface Treatment: To enhance durability and reduce wear, the surface of these rollers often undergoes special treatments, such as coating with abrasion-resistant materials or galvanization.
- Bearing Integration: High-quality bearings are integral to flat impact conveyor rollers, facilitating smooth rotation under heavy loads and minimizing maintenance requirements.
- Customization Capability: Flat impact conveyor roller factories offer customization options to cater to specific operational needs, including varying roller lengths, diameters, and material types.
- Compliance with Standards: These rollers are manufactured in compliance with international standards, ensuring compatibility with a wide range of conveyor systems and operational environments.
- Environmental Resistance: Engineered to perform in diverse environments, flat impact conveyor rollers are resistant to water, chemicals, and temperature variations, making them suitable for use in harsh industrial conditions.
The Specific Function of Flat Impact Conveyor Rollers in Absorbing Shocks and Impacts
The core functionality of flat impact conveyor rollers lies in their ability to protect the conveyor system from the damaging effects of heavy loads and sharp impacts. This protection is not just about preserving the conveyor belt but extends to the entire system, including the rollers themselves, the frame, and associated structures.
- Direct Impact Absorption: The primary role of these rollers is to take the brunt of the impact from materials as they drop onto the conveyor, shielding the belt and underlying structures.
- Uniform Force Distribution: The flat surface of these rollers ensures that impact forces are distributed evenly across the belt’s width, preventing localized stress points and wear.
- Vibration Dampening: By absorbing shocks, these rollers also reduce the vibrations that can lead to structural fatigue and noise pollution in the workplace.
- Extended Belt Life: Protecting the conveyor belt from impacts directly contributes to its longevity, reducing the frequency and cost of belt replacements.
- Operational Stability: The stability provided by these rollers enhances the conveyor’s ability to handle heavy and uneven loads without disruption or spillage.
- Maintenance Reduction: The durability and impact resistance of these rollers translate to fewer maintenance interruptions and lower long-term operational costs.
- Safety Enhancements: By reducing spillage, vibration, and noise, flat impact conveyor rollers contribute to a safer and more pleasant working environment.
- Increased Load Capacity: The enhanced durability and impact resistance allow the conveyor system to handle heavier loads, increasing throughput and efficiency.
- System Protection: Beyond the belt, these rollers help protect the entire conveyor system, including frames and supports, from the damaging effects of heavy impacts.
Flat impact conveyor rollers are a critical innovation in the field of conveyor technology, offering a blend of durability, efficiency, and protection that is essential for modern industrial operations. Their development and refinement continue to be a focus for flat impact conveyor roller factories committed to meeting the evolving needs of industries worldwide.
What Is the Role of Flat Impact Conveyor Roller Factory Products
Roller conveyors are integral to the seamless operation of various industries, facilitating the efficient transport of goods across short and long distances within manufacturing plants, warehouses, and distribution centers. The design and functionality of roller conveyors can vary significantly, but the basic principles of operation remain consistent, providing a foundation for understanding how these systems leverage the capabilities of components produced by a flat impact conveyor roller factory.
Basic Principles Behind Roller Conveyor Operation
- Gravity-Driven Movement: Many roller conveyors operate on the principle of gravity, where the conveyor is slightly inclined, allowing goods to move from a higher to a lower point without the need for motor power.
- Powered Rollers: In contrast, powered roller conveyors use motors to turn the rollers, propelling materials along the conveyor belt at a consistent speed and direction, which is essential for synchronizing with automated processes.
- Manual Propulsion: Some roller conveyors are designed for manual operation, where workers push or pull goods along the rollers, offering flexibility in environments where power is unavailable or automation is unnecessary.
- Load Distribution: Rollers are spaced evenly along the conveyor frame to support and distribute the weight of goods, preventing sagging and ensuring smooth transport.
- Friction Reduction: Rollers minimize the friction between the conveyor surface and the goods being transported, reducing the effort required to move heavy items.
- Modular Design: Roller conveyors often feature a modular design, allowing for easy expansion, reconfiguration, or integration with other conveyor systems to meet changing operational needs.
- Material Compatibility: The materials used to manufacture rollers, such as steel, plastic, or rubber, are selected based on the nature of the goods being transported, environmental conditions, and the need for impact resistance.
- Maintenance and Accessibility: Designed for easy maintenance, roller conveyors allow for quick replacement of individual rollers or sections, minimizing downtime and maintaining productivity.
The Role of Flat Impact Conveyor Rollers Within the Conveyor System
Produced by specialized flat impact conveyor roller factories, flat impact conveyor rollers play a critical role in enhancing the functionality and durability of roller conveyors, especially in applications involving heavy loads or significant impact forces.
- Shock Absorption: These rollers are specifically designed to absorb the shock and impact of heavy goods being loaded onto the conveyor, protecting both the goods and the conveyor belt from damage.
- Enhanced Durability: Manufactured with robust materials and designed to withstand significant forces, flat impact conveyor rollers contribute to the overall durability of the conveyor system.
- Load Distribution: The flat surface of these rollers ensures an even distribution of weight, reducing wear and tear on the conveyor belt and extending its lifespan.
- Noise Reduction: By absorbing impacts, these rollers operate more quietly than standard rollers, contributing to a more pleasant and safer working environment.
- Vibration Dampening: Flat impact conveyor rollers help to dampen vibrations caused by the movement of heavy or irregularly shaped goods, maintaining the stability of the conveyor system.
- Operational Efficiency: The impact absorption capabilities of these rollers allow the conveyor system to handle heavier loads more efficiently, increasing throughput and productivity.
- Protection of Conveyor Belt: By preventing direct impacts on the conveyor belt, these rollers extend the belt’s service life, reducing the need for frequent repairs or replacement.
- Reduced Maintenance Costs: The durability and impact resistance of flat impact conveyor rollers lead to lower maintenance costs and less downtime for the conveyor system.
- Customization and Compatibility: Flat impact conveyor roller factories offer rollers in various sizes and materials, ensuring compatibility with a wide range of conveyor systems and operational requirements.
Roller conveyors rely on the fundamental principles of gravity, powered operation, and manual propulsion to move goods efficiently. The inclusion of flat impact conveyor rollers, a product of specialized factories, significantly enhances the system’s ability to handle heavy loads and absorb impacts, ensuring the longevity and reliability of the conveyor system in demanding industrial environments.
Key Features of Flat Impact Conveyor Rollers from a Flat Impact Conveyor Roller Factory
In the intricate world of conveyor systems, the choice of rollers can significantly influence efficiency, durability, and operational costs. Among the various types available, flat impact conveyor rollers stand out for their specialized design and functionality. Produced by dedicated flat impact conveyor roller factories, these rollers are engineered to meet the rigorous demands of industries requiring the transport of heavy or impact-laden materials. Let’s delve into the materials and design aspects that make these rollers a critical component in enhancing conveyor system performance.
Materials and Design Aspects
- Material Durability: Constructed from materials like high-grade steel or impact-resistant polymers, these rollers are built to endure the rigors of heavy industrial use without succumbing to wear and tear.
- Design Efficiency: The flat surface design is not merely aesthetic; it serves to distribute the weight and impact across a broader area, minimizing damage to the conveyor belt.
- Bearing Quality: Integral to their operation, the bearings within these rollers are selected for their ability to provide smooth rotation under heavy loads, ensuring consistent conveyor movement.
- Surface Treatments: To further enhance their longevity, these rollers may undergo surface treatments for increased resistance to abrasion, corrosion, and other environmental factors.
- Customization Options: Recognizing the varied needs of different conveyor systems, flat impact conveyor roller factories offer customization in terms of size, material, and design.
- Shock Absorption Features: Some models include built-in shock absorbers, adding an extra layer of protection against impact forces.
- Sealing Technology: Advanced sealing techniques protect the internal components from dust, water, and contaminants, crucial for maintaining performance in challenging environments.
- Maintenance Considerations: Designed with ease of maintenance in mind, these rollers ensure that upkeep is straightforward, reducing downtime.
- Adaptability: Engineered to perform across a spectrum of environmental conditions, ensuring reliability whether indoors, outdoors, or in varying climates.
Advantages of Using Flat Impact Conveyor Rollers
The incorporation of flat impact conveyor rollers into a system is not just a matter of preference but a strategic decision to enhance operational efficiency and longevity. Here are the advantages that underscore their importance:
- Conveyor Belt Preservation: The design and functionality of these rollers play a pivotal role in extending the life of conveyor belts, safeguarding against premature wear and tear.
- Efficiency Gains: Their ability to handle heavy loads smoothly translates into increased operational efficiency, allowing for faster and more reliable material transport.
- Operational Continuity: The robust construction and low maintenance requirements of these rollers minimize disruptions, ensuring continuous operation.
- Workplace Safety: By reducing noise and vibration, these rollers contribute to a safer work environment, mitigating potential hazards associated with conveyor operation.
- Economic Benefits: The long-term cost savings realized through reduced maintenance, fewer replacements, and enhanced system reliability make these rollers a wise investment.
- Gentle Material Handling: The shock-absorbing properties protect sensitive materials during transport, reducing the risk of damage.
- System Versatility: The wide range of customization options allows these rollers to be tailored to specific operational needs, enhancing system versatility.
- Resilience: Designed to withstand harsh conditions, these rollers ensure reliable performance regardless of environmental challenges.
- Standard Compliance: Meeting industry standards, these rollers guarantee compatibility with a broad array of conveyor systems, simplifying integration and upgrades.
By choosing flat impact conveyor rollers from a reputable flat impact conveyor roller factory, businesses can significantly improve the resilience, efficiency, and cost-effectiveness of their conveyor systems. These rollers not only protect the conveyor belt and reduce maintenance needs but also enhance the overall productivity and safety of material handling operations.
To Choose the Right Flat Impact Conveyor Roller Factory
In the intricate ecosystem of material handling and logistics, the choice of a flat impact conveyor roller factory is not merely a procurement decision but a strategic one. This choice impacts everything from the operational efficiency and safety of your conveyor systems to the long-term sustainability and cost-effectiveness of your operations. Given the critical role that flat impact conveyor rollers play in absorbing shocks and distributing loads, selecting a factory that meets your needs in terms of quality, reliability, and service is paramount. Here are the factors to consider and the importance of industry standards and certifications in making an informed decision.
Factors to Consider
When embarking on the selection process, it’s essential to evaluate potential factories based on several key criteria:
- Quality of Products: The durability and performance of flat impact conveyor rollers hinge on the quality of materials and manufacturing processes used. High-quality rollers ensure longevity and reliability.
- Reliability and Reputation: Investigate the factory’s track record. A history of satisfied customers and successful projects is indicative of a reliable partner.
- Customization Options: Operational demands vary widely. The factory’s ability to customize rollers to specific requirements is crucial for optimal system performance.
- Compliance with Standards: Adherence to international and national manufacturing standards guarantees product quality and safety.
- Technical Support and Service: Effective post-sale support, including technical assistance and maintenance services, is essential for the smooth operation of your conveyor system.
- Lead Times and Delivery: Timely delivery is critical to maintaining project schedules and operational timelines. Evaluate the factory’s commitment to meeting delivery deadlines.
- Cost-Effectiveness: While initial cost is a consideration, assess the overall value proposition, including lifecycle costs and potential savings from reduced maintenance and downtime.
- Environmental and Social Responsibility: Partnering with a factory that prioritizes sustainable practices and social responsibility aligns with modern business ethics and may fulfill corporate social responsibility goals.
Importance of Industry Standards and Certifications
Selecting a factory that adheres to recognized industry standards and holds relevant certifications is not just about ticking compliance boxes; it’s about ensuring a partnership that brings tangible benefits:
- Quality Assurance: Standards and certifications are a testament to a factory’s commitment to maintaining high-quality production processes and outcomes.
- Safety Compliance: Certified products meet established safety criteria, reducing the risk of workplace accidents and enhancing the safety of your operations.
- Operational Reliability: Standards cover performance under various conditions, ensuring that rollers can withstand the demands of your specific environment.
- System Compatibility: Standardized products ensure compatibility with a wide range of conveyor systems, facilitating integration and upgrades.
- Installation Efficiency: Compliance with standards simplifies the installation process, saving time and reducing costs.
- Access to Global Markets: Certifications may be required for operation in certain regions or industries, enabling you to expand your market reach.
- Mitigation of Liability Risks: Using certified components can help mitigate legal and financial risks associated with equipment failures.
- Environmental Considerations: Standards often encompass environmental protection measures, supporting your sustainability objectives.
- Cost Savings Over Time: The long-term reliability and durability of certified products can lead to significant cost savings by reducing the need for frequent replacements and maintenance.
The selection of a flat impact conveyor roller factory is a critical decision that requires careful consideration of various factors, including quality, customization options, and adherence to industry standards. Choosing the right factory ensures not only the smooth operation of your conveyor systems but also supports broader operational and strategic goals.
Flat Impact Conveyor Roller Factory for Sale: What to Look For
In the dynamic world of conveyor systems, the quest for a reliable flat impact conveyor roller factory for sale is more than a mere procurement task; it’s a strategic endeavor crucial for maintaining the seamless operation of your material handling processes. The right factory not only ensures the supply of high-quality rollers but also supports your operational goals through innovative solutions and comprehensive service. As you navigate this critical decision, here are nuanced tips and considerations for identifying a factory that aligns with your operational needs and standards for quality and compatibility.
Tips on Finding Flat Impact Conveyor Roller Factories for Sale
Embarking on the search for a flat impact conveyor roller factory requires a methodical approach, focusing on factors that contribute to long-term operational success:
- Industry Presence: A factory’s presence and reputation in the industry can be a testament to its reliability and quality of products. Look for those with positive industry recognition.
- Innovation and R&D: Factories that prioritize innovation and invest in research and development tend to offer more advanced and efficient solutions, enhancing your conveyor system’s performance.
- Product Diversity: A wide product range suggests the factory’s capability to meet diverse operational demands, providing you with options to best suit your specific needs.
- Adaptability and Customization: The ability of a factory to adapt and customize products according to customer specifications is crucial for addressing unique operational challenges.
- Quality of Construction: The durability and performance of the rollers are directly influenced by the quality of materials and construction, making this a critical area of assessment.
- Compliance and Certification: Factories adhering to industry standards and holding certifications demonstrate a commitment to quality and safety, crucial for your operations.
- Support Services: Effective after-sales support, including technical assistance and maintenance services, ensures ongoing operational efficiency and problem resolution.
- Sustainability Efforts: Ethical and sustainable manufacturing practices reflect a factory’s commitment to environmental responsibility and can align with your company’s values.
- Client Testimonials and Case Studies: Real-world feedback and success stories offer insights into the factory’s ability to deliver on its promises, highlighting reliability and effectiveness.
Assessing Quality and Compatibility
Delving deeper into the specifics of flat impact conveyor rollers, it’s essential to evaluate aspects that directly impact their integration and performance within your conveyor system:
- Examine Material Quality: High-quality materials are foundational to the durability and longevity of conveyor rollers, necessitating a thorough evaluation.
- Assess Innovative Design Features: Design elements that enhance functionality, such as improved impact absorption and load distribution, can significantly benefit your operations.
- Ensure System Compatibility: Compatibility with your existing conveyor setup is non-negotiable for seamless integration and optimal performance.
- Review Performance Data: Performance testing results can offer objective insights into the rollers’ reliability and efficiency under operational stresses.
- Verify Load Handling Capabilities: The rollers’ ability to support your system’s load requirements is critical for maintaining throughput and avoiding system strain.
- Understand Maintenance Needs: Opting for rollers designed for low maintenance can reduce operational costs and minimize downtime, enhancing overall efficiency.
- Look for Warranty Protection: Warranties and guarantees provide a safety net against potential defects and performance issues, offering peace of mind.
- Gather User Feedback: Insights from current and former customers can shed light on the real-world performance and reliability of the factory’s products, guiding your decision-making process.
Selecting the right flat impact conveyor roller factory is a multifaceted process that goes beyond basic product specifications to encompass factors like innovation, compatibility, and service. By carefully considering these aspects, you can partner with a factory that not only meets but exceeds your expectations, ensuring the long-term success and efficiency of your conveyor systems.
Flat Impact Conveyor Roller Factory Near Me
Finding a flat impact conveyor roller factory in close proximity to your operations is not just a logistical preference but a strategic advantage. The convenience of having a manufacturer nearby transcends mere geography, embedding itself into the very fabric of operational efficiency, responsiveness, and collaborative innovation. In today’s fast-paced industrial environment, where every second and every penny counts, the localization of your supply chain components, such as flat impact conveyor rollers, can significantly impact your bottom line and operational agility. Here are strategies to effectively locate a nearby factory and the multifaceted benefits that such a partnership can yield.
Strategies for Locating Nearby Flat Impact Conveyor Roller Manufacturers
Navigating the industrial landscape to find a local flat impact conveyor roller factory requires a blend of traditional methods and modern digital strategies:
- Local Industrial Listings: Start with local business directories and industrial listings that categorize manufacturers by region, offering a straightforward way to identify nearby factories.
- Chamber of Commerce: Your local Chamber of Commerce is a valuable resource for identifying local manufacturers, providing insights into reputable businesses in your area.
- Industry Networking Events: Participating in local industry networking events, seminars, and workshops can connect you with regional manufacturers and suppliers.
- B2B Marketplaces: Utilize B2B marketplaces that offer advanced search functionalities, allowing you to filter results by location and specific manufacturing capabilities.
- Consulting with Industry Experts: Engaging with consultants or industry experts who have an in-depth understanding of the conveyor manufacturing landscape can lead to personalized recommendations.
- Utilizing Social Media: LinkedIn and other professional social networks can be instrumental in discovering and connecting with local manufacturers.
Benefits of Partnering with a Local Factory
The decision to partner with a local flat impact conveyor roller factory brings with it a cascade of operational, economic, and strategic advantages:
- Streamlined Logistics: Proximity reduces logistical complexities, leading to faster delivery times and lower transportation costs.
- Enhanced Communication: Local partnerships facilitate easier, more effective communication, allowing for real-time discussions and quicker decision-making.
- Rapid Response to Demand Fluctuations: Being close to your supplier means you can respond more swiftly to changes in demand, maintaining optimal inventory levels.
- Personalized Inspections and Quality Assurance: The ability to personally visit the factory for inspections or quality assurance processes ensures that the products meet your exact standards.
- Development of Strategic Relationships: Proximity fosters stronger business relationships, enabling collaborative efforts on product development and customization.
- Economic Contributions: Supporting local businesses contributes to the local economy, promoting growth and sustainability within your community.
- Adaptability and Flexibility: Local manufacturers are often more willing and able to adapt to your changing needs, offering flexible production schedules and order quantities.
- Sustainability: Shorter supply chains are generally more sustainable, reducing the carbon footprint associated with transportation and logistics.
- After-Sales Support and Service: Access to prompt after-sales support and service is greatly improved, ensuring any issues are resolved quickly and efficiently.
Choosing to source your flat impact conveyor rollers from a nearby factory is a strategic decision that extends beyond mere convenience, embedding itself into the core of your operational efficiency and supply chain resilience. By employing targeted strategies to locate a suitable local manufacturer and understanding the comprehensive benefits of such a partnership, businesses can significantly enhance their competitive edge and operational sustainability.
FAQs about Flat Impact Conveyor Roller Factory
Conveyor rollers are manufactured by specialized companies that focus on producing various components for conveyor systems. These manufacturers range from large multinational corporations to small, specialized engineering firms. The production of conveyor rollers involves precision engineering and the use of durable materials to ensure they can withstand the demands of continuous operation in different industrial environments. Manufacturers of conveyor rollers often offer a wide range of products to cater to different types of conveyor systems, including gravity rollers, driven rollers, and impact rollers, among others. These companies not only provide standard sizes but also offer customization options to meet specific operational requirements. When selecting a manufacturer for conveyor rollers, it’s important to consider factors such as the company’s reputation, the quality of their products, their manufacturing capabilities, and their ability to provide after-sales support and technical assistance. Leading manufacturers stay at the forefront of technology and innovation, continuously improving their products to enhance efficiency, durability, and performance.
The impact roller in a belt conveyor is a specialized type of roller designed to absorb the shock and stress of heavy materials falling onto the conveyor belt at loading points. These rollers are strategically placed in the sections of the conveyor where material is loaded, helping to protect the belt from damage that could be caused by the significant impact of dropping materials. Impact rollers are typically more robust than standard rollers and are often covered with rubber or equipped with shock-absorbing features to effectively dissipate the energy from falling objects. The primary purpose of impact rollers is to extend the lifespan of the conveyor belt by preventing tears, punctures, and excessive wear. By doing so, they play a crucial role in maintaining the efficiency and reliability of the conveyor system, reducing downtime, and minimizing maintenance costs. Impact rollers are essential components in industries where heavy, abrasive materials are handled, such as mining, quarrying, and aggregate production.
Conveyor rollers come in various types, each designed to fulfill specific functions within a conveyor system. The main types include:
Gravity Rollers: These rollers rely on gravity to move products and are typically used in manual loading and unloading applications. They are cost-effective and suitable for lightweight materials.
Driven Rollers: Powered by motors or chains, driven rollers move materials along the conveyor system without manual intervention, ideal for automated processes.
Impact Rollers: Positioned at loading zones, impact rollers absorb the shock of heavy materials falling onto the belt, protecting it from damage.
Grooved Rollers: Designed with grooves that can accommodate round belts for driving the roller, these are used in lightweight applications.
Tapered Rollers: Used in curved sections of conveyors, tapered rollers ensure materials stay on track around bends.
Return Rollers: These rollers support the return side of the conveyor belt and can be plain or fitted with rubber discs to remove accumulated debris.
Each type of roller is selected based on the specific requirements of the conveyor system, including the weight of the materials being transported, the direction and speed of movement, and the environmental conditions of the operation.
While roller conveyors are versatile and widely used in various industries, they have certain limitations that may affect their suitability for some applications:
Limited Material Types: Roller conveyors are most efficient with rigid and flat-bottomed items. Irregularly shaped, very small, or extremely heavy items may not move smoothly.
Inclines and Declines: Gravity roller conveyors, in particular, are limited in their ability to handle steep inclines or declines without manual assistance or additional equipment.
Speed Control: Controlling the speed of items on gravity roller conveyors can be challenging, especially for lightweight products that may move too quickly or unevenly.
Maintenance: Roller conveyors require regular maintenance to ensure smooth operation. Debris, wear, and tear on the rollers can lead to system inefficiencies or breakdowns.
Noise: Depending on the design and the materials being transported, roller conveyors can generate significant noise, which may require mitigation measures in certain environments.
Cost: While gravity roller conveyors are relatively inexpensive, powered roller conveyors can be costly to install and operate, especially for customized systems.
Despite these limitations, roller conveyors remain a popular choice for material handling due to their efficiency, simplicity, and adaptability to various operational needs.
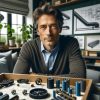
Jordan Smith, a seasoned professional with over 20 years of experience in the conveyor system industry. Jordan’s expertise lies in providing comprehensive solutions for conveyor rollers, belts, and accessories, catering to a wide range of industrial needs. From initial design and configuration to installation and meticulous troubleshooting, Jordan is adept at handling all aspects of conveyor system management. Whether you’re looking to upgrade your production line with efficient conveyor belts, require custom conveyor rollers for specific operations, or need expert advice on selecting the right conveyor accessories for your facility, Jordan is your reliable consultant. For any inquiries or assistance with conveyor system optimization, Jordan is available to share his wealth of knowledge and experience. Feel free to reach out at any time for professional guidance on all matters related to conveyor rollers, belts, and accessories.