Conveyor Return Roller: Part of Conveyor System
Return rollers play a pivotal role in the seamless operation of conveyor systems, serving as the unsung heroes that support the return path of the conveyor belt. These components are crucial for maintaining the belt’s integrity and ensuring the system’s overall efficiency. Positioned beneath the conveyor belt, return rollers help to stabilize the belt’s return section, preventing sagging and ensuring it remains aligned and tensioned properly. This not only prolongs the life of the conveyor belt but also contributes to the smooth and efficient transport of materials. The significance of return rollers extends beyond mere support; they are key to minimizing wear and tear on the conveyor belt, thereby reducing downtime and maintenance costs. Their role in the conveyor system underscores the importance of selecting high-quality return rollers to maintain optimal performance and reliability.
What Are Return Rollers
Return rollers are an integral component of conveyor systems, designed to support the underside or the return path of the conveyor belt. These rollers ensure that the belt travels back to the starting point in a smooth and controlled manner, ready to be loaded again. The primary function of a return roller is to provide support to the conveyor belt when it is not carrying any load, thereby preventing any unnecessary sagging or slack that could lead to operational issues or conveyor belt damage.
The distinction between return rollers and carrying rollers is crucial for understanding their roles within a conveyor system. While both are essential for the conveyor’s operation, they serve different purposes. Here’s a comparison displayed in a table format:
Feature | Return Roller | Carrying Roller |
---|---|---|
Position | Mounted beneath the conveyor belt on the return path | Positioned above the belt on the carrying side |
Function | Supports the empty returning belt | Supports the belt while it carries the load |
Load | Does not directly support the material load | Directly supports and transports the material load |
Design | Often simpler, as they are not subject to the same load stresses | More robust to withstand the weight and impact of the materials being conveyed |
Understanding the role and design differences between return rollers and carrying rollers is essential for the efficient and effective design, operation, and maintenance of conveyor systems. Each type of roller is specifically engineered to fulfill its role, ensuring the longevity and reliability of the conveyor system as a whole.
What Are Conveyor Return Rollers
Conveyor return rollers play a crucial role in the overall efficiency and reliability of conveyor systems. They support the empty side of the belt after the material has been discharged, ensuring smooth and continuous operation. This guide will explore the functions, types, and benefits of conveyor return rollers.
Functions of Conveyor Return Rollers
Conveyor return rollers primarily support and guide the conveyor belt, preventing it from sagging or misaligning. They help maintain proper belt tension, reduce friction, and minimize wear and tear on the belt. Additionally, return rollers contribute to the overall stability and efficiency of the conveyor system by ensuring the belt runs smoothly and consistently.
Types of Conveyor Return Rollers
Flat Return Rollers:
- Description: These are the most common type of return rollers, featuring a flat surface that supports the belt.
- Uses: Ideal for general-purpose conveyor systems handling a wide range of materials.
V-Return Rollers:
- Description: These rollers have a V-shaped configuration, providing additional belt support and alignment.
- Uses: Suitable for long conveyor belts or systems carrying heavy loads, where additional belt stability is required.
Rubber Disc Return Rollers:
- Description: These rollers feature rubber discs spaced along the roller, which help to clean the belt and prevent material buildup.
- Uses: Best for applications where material carryback and buildup are common, such as in mining or aggregate industries.
Spiral Return Rollers:
- Description: These rollers have a spiral configuration that aids in belt cleaning and reducing material buildup.
- Uses: Ideal for conveyor systems handling sticky or cohesive materials.
Benefits of Conveyor Return Rollers
Improved Belt Tracking:
- Return rollers help maintain proper belt alignment, reducing the risk of belt misalignment and associated downtime.
Reduced Wear and Tear:
- By supporting the belt and minimizing sagging, return rollers reduce friction and extend the lifespan of the conveyor belt.
Enhanced Efficiency:
- Properly functioning return rollers ensure smooth and consistent belt operation, improving the overall efficiency of the conveyor system.
Lower Maintenance Costs:
- With reduced belt wear and improved belt tracking, maintenance requirements and associated costs are minimized.
Conveyor return rollers are essential components in any conveyor system, contributing to the smooth and efficient operation of the belt. By understanding the different types and benefits of return rollers, you can make informed decisions to optimize your conveyor system for maximum productivity and reliability.

Types of Return Rollers
The return roller is a fundamental component of conveyor systems, providing critical support for the return side of the conveyor belt. Various types of return rollers are designed to meet specific operational needs, enhancing performance and extending the lifespan of the conveyor system. This section explores the different types of return rollers, including their features, applications, benefits, and roles in conveyor systems.
Standard Return Rollers
Standard return rollers are the most commonly used type in conveyor systems.
Basic Features:
- Cylindrical shape designed for general support of the return belt.
- Manufactured from steel or high-density polyethylene (HDPE) for durability.
- Equipped with sealed bearings to prevent dust and water ingress.
- Designed for easy installation and minimal maintenance.
- Available in various diameters and lengths to suit different belt widths.
- Often coated with anti-corrosive materials for extended life in harsh environments.
Applications:
- Widely used in light to medium-duty conveying systems.
- Suitable for industries such as mining, agriculture, and manufacturing.
- Ideal for material handling tasks involving non-abrasive materials.
- Commonly found in package handling and distribution centers.
- Used in both indoor and outdoor conveyor setups.
- Applicable in environments where noise levels are not a critical concern.
Return Rollers with Rubber Rings
Return rollers with rubber rings offer enhanced performance in noise reduction and impact absorption.
Benefits:
- Significantly reduce operational noise, improving the working environment.
- Absorb shocks and impacts, protecting the belt and the roller from damage.
- Prevent material build-up on the roller surface, ensuring smooth belt movement.
- Increase grip on the return belt, reducing slippage and misalignment.
- Ideal for use in applications involving abrasive materials.
- Extend the lifespan of the conveyor belt by minimizing wear and tear.
- Suitable for use in wet conditions, as rubber provides excellent water resistance.
- Reduce vibration, which can lead to reduced maintenance costs.
- Environmentally friendly, as rubber rings can be replaced, extending the roller’s life.
- Enhance overall system efficiency by maintaining consistent belt tension and alignment.
Self-Cleaning Return Rollers
Self-cleaning return rollers are designed to maintain cleanliness by automatically removing debris and residues.
Design Features:
- Feature specialized surfaces or profiles that dislodge and repel material build-up.
- Often incorporate spiral or helical rubber discs that clean the belt as it moves.
- Constructed with durable materials resistant to wear and abrasion.
- Designed for easy replacement of wear components.
- Engineered to work in a variety of environmental conditions, including wet and sticky applications.
- Available in different sizes to accommodate various belt widths and speeds.
Advantages:
- Significantly reduce maintenance downtime by minimizing cleaning requirements.
- Prevent material build-up that can lead to belt misalignment and increased wear.
- Enhance safety by reducing the risk of material spillage and slip hazards.
- Improve the lifespan of both the belt and the roller by reducing abrasive contact.
- Ensure consistent belt tension and alignment, contributing to efficient operation.
- Ideal for applications in industries such as mining, where material carryback is a common issue.
Impact Return Rollers
Impact return rollers are specifically designed to absorb the impact at loading points, protecting the belt and system from damage.
Role:
- Feature reinforced designs and materials capable of withstanding high impact forces.
- Often equipped with rubber discs or sleeves to cushion the impact and distribute the load evenly.
- Help to stabilize the belt immediately after the loading point, preventing material spillage and belt sag.
- Extend the service life of the conveyor belt by reducing stress and impact at critical points.
- Essential for heavy-duty applications where large, heavy materials are loaded onto the conveyor.
- Contribute to smoother operation and reduced downtime by preventing belt damage.
- Enhance overall system reliability, particularly in industries such as mining, quarrying, and bulk material handling.
- Can be combined with other specialized rollers to optimize conveyor performance in challenging conditions.
- Reduce the need for frequent belt repairs and replacements, leading to cost savings.
- Improve safety by preventing sudden shocks and jolts that can lead to system failures or accidents.
Rubber Return Rolls
Basic Features
- Material Composition:Made from high-quality rubber, providing durability and resistance to wear and tear.Core material typically consists of steel or other robust metals to ensure strength and longevity.
- Design and Construction:Smooth surface design to prevent belt damage and reduce friction.Available in various diameters and lengths to fit different conveyor systems.Incorporates sealed bearings to protect against dust and moisture, ensuring smooth operation.
- Performance Characteristics:High resistance to abrasion and impact, extending the lifespan of the rolls.Excellent shock absorption capabilities, reducing noise and vibration during operation.Ability to withstand harsh environmental conditions, including extreme temperatures and exposure to chemicals.
- Maintenance and Installation:Easy to install and replace, minimizing downtime.Low maintenance requirements due to durable construction and protective features.
Applications
- Material Handling Systems:Used in various industries, including mining, construction, and manufacturing, to support conveyor belts in material handling systems.Ideal for transporting bulk materials such as coal, ore, gravel, and sand.
- Recycling Plants:Employed in recycling facilities to handle the movement of recyclable materials efficiently.Helps in the smooth transportation of different types of waste, including plastics, metals, and paper.
- Agricultural Sector:Utilized in agricultural conveyors for moving grains, seeds, and other agricultural products.Ensures efficient and safe handling of materials in farming operations.
- Food Processing Industry:Applied in food processing plants where hygiene and material handling efficiency are critical.Suitable for transporting raw and processed food items while maintaining cleanliness and preventing contamination.
- Quarry and Aggregate Operations:Essential in quarries and aggregate plants for conveying stones, aggregates, and minerals.Supports heavy-duty conveyor systems that handle large volumes of materials.
- Port and Dock Facilities:Used in port and dock facilities for loading and unloading cargo from ships.Assists in the smooth operation of conveyor systems handling various types of goods and materials.
- Power Generation Plants:Integral to coal-fired power plants for transporting coal to different stages of the power generation process.Ensures continuous and efficient movement of coal, contributing to the overall efficiency of the plant.
The selection of the appropriate return roller type is crucial for optimizing conveyor system performance, extending equipment lifespan, and ensuring efficient material handling. Each type of return roller offers unique benefits tailored to specific operational requirements and environmental conditions.

Return Roller Sizes and Specifications
When it comes to optimizing the efficiency and longevity of a conveyor system, selecting the right return roller size is paramount. The return roller plays a crucial role in supporting the belt on its return path and is essential for maintaining belt integrity and system reliability. This section delves into the common sizes of return rollers and their impact on conveyor performance and material handling.
Common Sizes and Selection Criteria
Return rollers come in various diameters and lengths, typically ranging from 2 inches to 8 inches in diameter, with lengths varying to match the width of the conveyor belt. The most common sizes include 4-inch, 5-inch, and 6-inch diameters. When choosing the right size for your conveyor system, consider the following factors:
- Belt Width: The width of the conveyor belt dictates the minimum length of the return roller. A general rule is that the roller should be at least 3 inches wider than the belt width to ensure proper support.
- Load Capacity: Heavier loads require rollers with larger diameters to reduce the belt’s curvature around the roller, which minimizes wear and extends the belt’s life.
- Conveyor Speed: High-speed conveyor systems may need larger rollers to reduce the rotation speed, decreasing bearing wear and extending the roller’s lifespan.
Impact of Roller Size on Conveyor Performance
The size of the return roller significantly influences conveyor performance and material handling efficiency. Key impacts include:
- Belt Support: Adequate roller size ensures proper conveyor belt support, reducing sagging and minimizing material spillage.
- Wear and Tear: Larger rollers distribute the load more evenly, reducing the wear on both the belt and the roller itself.
- Energy Efficiency: Appropriately sized rollers reduce the conveyor system’s energy consumption by decreasing friction and resistance.
- Noise Reduction: Larger rollers can operate more quietly, contributing to a more pleasant working environment.
- Maintenance Requirements: Choosing the right roller size can lower maintenance needs by reducing the rate of wear and tear on the conveyor components.
The selection of the right return roller size is a critical decision that impacts the efficiency, durability, and operational costs of a conveyor system. By considering factors such as belt width, load capacity, and conveyor speed, you can choose a return roller that enhances your system’s performance and reliability.

Application of Return Rollers
Return rollers play a vital role in the smooth operation of conveyor systems. They are designed to support the empty side of the conveyor belt and ensure it remains in the correct position after discharging the material load. This guide explores the various applications of return rollers across different industries and conveyor setups.
General Applications
Material Handling:
- Return rollers are widely used in material handling systems to support and guide conveyor belts carrying various types of materials, from lightweight packages to heavy bulk goods.
Mining Industry:
- In mining operations, return rollers are essential for supporting conveyor belts that transport ores, coal, and other extracted materials. They help maintain belt stability and reduce the risk of belt misalignment.
Aggregate and Construction:
- Return rollers are employed in aggregate and construction conveyor systems to transport sand, gravel, and construction debris. They ensure that the conveyor belt runs smoothly and efficiently, even under heavy loads.
Manufacturing:
- In manufacturing plants, return rollers are used to support conveyor belts that move products through various stages of production. They help maintain consistent belt tension and alignment, ensuring smooth operation.
Recycling:
- Recycling facilities use return rollers to support conveyor belts that carry recyclable materials such as paper, plastics, and metals. Proper support from return rollers helps prevent belt sagging and misalignment, facilitating efficient sorting and processing.
Specific Applications
Long Conveyor Systems:
- In long conveyor systems, return rollers are crucial for maintaining belt alignment over extended distances. They prevent the belt from sagging and ensure it remains centered, reducing the risk of damage and downtime.
High-Speed Conveyors:
- For high-speed conveyor systems, return rollers help reduce belt vibrations and maintain smooth operation. This is essential for preventing material spillage and ensuring accurate product handling.
Heavy Load Conveyors:
- Return rollers designed for heavy load applications provide additional support to prevent belt sagging under the weight of heavy materials. They are often reinforced to handle the increased load.
Inclined and Declined Conveyors:
- In inclined or declined conveyor systems, return rollers help maintain belt tension and alignment, preventing slippage and ensuring smooth material transport.
Harsh Environments:
- Return rollers used in harsh environments, such as mining or outdoor applications, are often equipped with special coatings or materials to resist corrosion and wear. This enhances their durability and performance under challenging conditions.
Benefits of Using Return Rollers
Enhanced Belt Tracking:
- Return rollers help maintain proper belt alignment, reducing the risk of belt misalignment and associated downtime.
Reduced Wear and Tear:
- By supporting the belt and minimizing sagging, return rollers reduce friction and extend the lifespan of the conveyor belt.
Increased Efficiency:
- Properly functioning return rollers ensure smooth and consistent belt operation, improving the overall efficiency of the conveyor system.
Lower Maintenance Costs:
- With reduced belt wear and improved belt tracking, maintenance requirements and associated costs are minimized.
Return rollers are essential components in conveyor systems across various industries. Their application ensures the smooth, efficient, and reliable operation of conveyor belts, supporting a wide range of materials and operating conditions. By understanding the specific applications and benefits of return rollers, businesses can optimize their conveyor systems for maximum productivity and longevity.
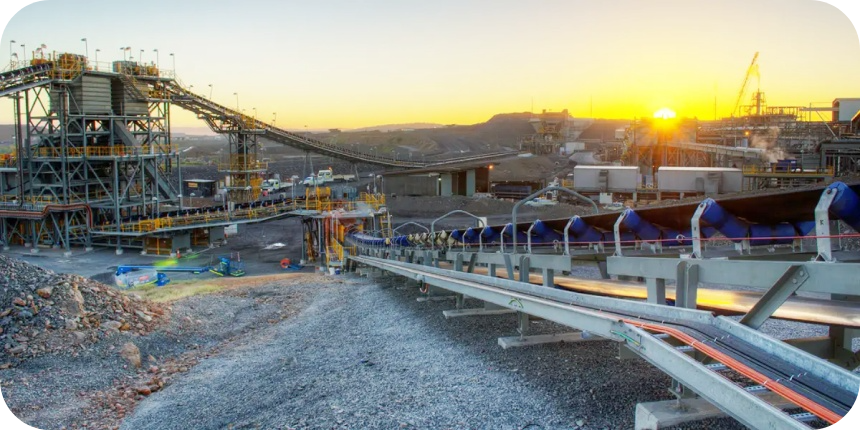
Return Roller Materials and Durability
The choice of material for a return roller is a critical factor that directly influences its durability, performance, and suitability for various operational environments. This section explores the different materials used in return roller manufacturing and provides insights into their durability and maintenance considerations.
Materials Used in Return Roller Manufacturing
- Steel: Steel is the most common material used for return rollers due to its high strength and durability. It is suitable for heavy-duty applications and can withstand harsh operational conditions.
- Rubber-Coated: Rubber-coated rollers offer additional grip and protection for the conveyor belt. The rubber coating helps in absorbing impacts and reducing noise, making these rollers ideal for applications where noise reduction is essential.
- High-Density Polyethylene (HDPE): HDPE rollers are lightweight and resistant to corrosion and abrasion. They are well-suited for environments where chemical exposure or moisture is a concern.
- Composite Materials: Composite rollers, made from a combination of materials like fiberglass, resin, and other plastics, offer a balance between weight and strength. They are resistant to corrosion, making them suitable for corrosive environments.
- Stainless Steel: Stainless steel rollers are used in food processing, pharmaceuticals, and other industries where hygiene and resistance to corrosion are paramount.
- Aluminum: Aluminum rollers are lightweight and used in applications where weight reduction is crucial, such as in mobile conveyor systems.
Durability and Maintenance Considerations
The durability of a return roller is influenced by its material, design, and the environment in which it operates. Here are eight maintenance considerations to ensure the longevity of your return rollers:
- Regular Inspection: Regularly inspect rollers for signs of wear, damage, or misalignment, regardless of the material.
- Lubrication: Ensure that rollers with bearings are properly lubricated to reduce friction and prevent premature wear.
- Cleaning: Keep the rollers clean, especially in environments where dust, debris, or chemicals may accumulate on the roller surface.
- Environmental Protection: Use rollers made from materials that are suited to the operational environment. For example, use stainless steel or composite rollers in corrosive environments.
- Load Capacity: Do not exceed the recommended load capacity of the rollers, as excessive loads can lead to deformation or failure.
- Impact Management: In high-impact areas, consider using rubber-coated or specially designed impact rollers to absorb shocks and protect the roller and conveyor belt.
- Temperature Considerations: Ensure that the material of the roller can withstand the operational temperature range. For example, HDPE rollers may not be suitable for high-temperature applications.
- Replacement Schedule: Establish a maintenance and replacement schedule based on the expected lifespan of the rollers and the specific demands of your operation.
By selecting the appropriate material for your return roller and adhering to proper maintenance practices, you can enhance the efficiency and longevity of your conveyor system. Each material offers unique benefits, and the choice should be based on the specific requirements of your application and the environmental conditions in which the system operates.

Guide and Impact Rollers in the Context of Return Rollers
While the primary focus is often on the return roller for its role in supporting the conveyor belt on its return path, guide and impact rollers also play crucial roles in the overall functionality and longevity of conveyor systems. These specialized rollers work in conjunction with return rollers to ensure smooth and efficient conveyor operations.
Role of Guide Rollers in Maintaining Belt Alignment
Guide rollers are essential in maintaining proper conveyor belt alignment, which is crucial for the longevity and efficiency of the conveyor system. Here are eight key roles they play:
- Preventing Belt Drift: Guide rollers prevent the conveyor belt from drifting off its intended path, reducing the risk of edge damage and misalignment.
- Minimizing Wear: By keeping the belt aligned, guide rollers minimize wear and tear on both the belt and the return rollers, extending their service life.
- Enhancing Safety: Proper belt alignment reduces the risk of belt-related accidents, enhancing overall workplace safety.
- Improving Material Handling: Aligned belts ensure that materials are transported efficiently, reducing spillage and improving handling accuracy.
- Reducing Downtime: By preventing misalignment-related issues, guide rollers contribute to reduced maintenance downtime.
- Increasing Energy Efficiency: Well-aligned belts require less energy to operate, as there is less friction and resistance involved.
- Supporting Heavy Loads: Guide rollers provide additional support for heavy loads, ensuring that the belt remains aligned under increased strain.
- Adapting to Changes: Guide rollers can adapt to changes in load and operational conditions, maintaining alignment across various scenarios.
Impact Rollers and Their Importance in Protecting the Belt at Loading Zones
Impact rollers are strategically placed at conveyor loading zones to absorb the shock and impact of material falling onto the belt. Their importance cannot be overstated:
- Shock Absorption: Impact rollers dissipate the energy generated when materials are loaded onto the conveyor, protecting the belt from damage.
- Belt Protection: By absorbing the impact, these rollers prevent punctures, tears, and indentations on the conveyor belt, especially important in the case of sharp or heavy materials.
- Extending Belt Life: The cushioning effect of impact rollers extends the operational life of the conveyor belt, reducing the need for frequent replacements.
- Reducing Spillage: Impact rollers help stabilize the load as it lands on the belt, reducing bounce and material spillage.
- Maintaining System Integrity: By protecting the belt, impact rollers help maintain the overall integrity and efficiency of the conveyor system.
- Enhancing Performance: Impact rollers ensure that the conveyor system can handle a wide range of materials and operational demands without compromising performance.
- Cost Savings: The protective role of impact rollers leads to cost savings by reducing maintenance, repair, and replacement expenses.
- Versatility: Impact rollers are designed to suit various applications and materials, making them versatile components of conveyor systems.
While the return roller is vital for the support and smooth operation of the return side of the conveyor belt, guide and impact rollers are equally important for maintaining belt alignment and protecting the belt at loading zones. Together, these components ensure the efficiency, safety, and longevity of conveyor systems.
Return Roller Rental and Purchase Options
Deciding whether to rent or purchase return rollers can significantly impact the operational efficiency and financial health of a project. This section explores the scenarios where renting or buying might be more advantageous and delves into the factors influencing this decision.
When to Consider Renting vs. Buying Return Rollers
Renting Return Rollers might be the preferred option under certain circumstances:
- Short-Term Projects: For projects with a limited duration where the long-term ownership of return rollers does not justify the investment.
- Trial Purposes: When wanting to test the performance of a specific type of return roller before committing to a purchase.
- Budget Constraints: When upfront capital expenditure is limited, renting can provide access to necessary equipment without a significant initial investment.
- Flexibility: Rental agreements can offer the flexibility to upgrade or change return rollers as project requirements evolve.
Buying Return Rollers is often more suitable when:
- Long-Term Use: For operations where conveyor systems are a permanent fixture and will be used extensively over the years.
- Custom Requirements: When specific, customized return rollers are needed to meet unique operational needs that rental options cannot fulfill.
- Cost-Effectiveness Over Time: Purchasing can be more cost-effective in the long run for continuous or repeated use, eliminating recurring rental fees.
- Asset Ownership: Owning return rollers can be an asset to the company, adding value to the business’s operational infrastructure.
Factors Influencing the Decision
- Project Duration: Short-term projects may benefit more from renting, while long-term projects might justify the purchase.
- Budget: Limited budgets may lean towards renting as it requires less upfront investment compared to purchasing.
- Specific Needs: Custom or highly specialized return rollers might not be available for rent, necessitating a purchase.
- Operational Flexibility: Renting offers the ability to adapt to changing project needs without the commitment of purchase.
- Maintenance and Upkeep: Owning return rollers means taking on the responsibility for maintenance, whereas rental agreements often include maintenance services.
- Storage and Transportation: Consider the costs and logistics of storing and transporting return rollers if purchased. Renting can alleviate these concerns.
- Financial Strategy: Purchasing can be a capital investment with depreciation benefits, while renting is an operational expense that might fit better with certain financial strategies.
- Market Availability: The availability of return rollers for rent in the market can influence the decision. In areas with limited rental options, purchasing might be the only viable option.
The decision to rent or purchase return rollers hinges on a careful assessment of project-specific factors such as duration, budget, and operational needs. Both options have their merits, and the choice should align with the strategic goals and financial considerations of the project or operation.

Return Roller Prices and Budgeting
Understanding the pricing of return rollers is crucial for effective budgeting in conveyor system projects. The cost of return rollers can vary widely based on several factors. This section will explore the key elements that influence return roller pricing and provide practical tips for budgeting effectively.
Factors Affecting Return Roller Pricing
- Material: The construction material of the return roller significantly impacts its price. Steel rollers are generally cost-effective, while specialized materials like stainless steel or composite materials can be more expensive due to their enhanced properties.
- Size: The size of the return roller, including its diameter and length, affects the price. Larger rollers require more material and are typically more expensive.
- Type: The specific type of return roller (standard, rubber-coated, self-cleaning, impact) also influences the cost. Specialty rollers designed for specific functions, like impact absorption or self-cleaning, can be pricier than standard rollers.
- Quality and Durability: High-quality rollers that offer greater durability and longevity may come with a higher initial cost but can provide savings in the long term through reduced maintenance and replacement needs.
- Brand and Manufacturer: The reputation and location of the manufacturer can affect pricing. Well-known brands might charge more, but they often offer better quality assurance and customer support.
- Quantity: The quantity of rollers needed can also impact the price, with bulk orders often qualifying for discounts.
Tips for Budgeting for Return Rollers
- Assess Requirements Carefully: Clearly define the project’s needs, including the type and specifications of the return rollers required, to avoid overspending on unnecessary features.
- Get Multiple Quotes: Obtain quotes from several suppliers to compare prices and negotiate better deals.
- Consider Total Cost of Ownership: Look beyond the initial purchase price to consider maintenance, durability, and potential downtime costs.
- Budget for Quality: Investing in higher-quality rollers can reduce long-term costs associated with maintenance, replacements, and downtime.
- Plan for Spare Parts: Include a budget for spare rollers and parts to minimize downtime in case of unexpected failures.
- Look for Bulk Discounts: If your project requires a large number of rollers, explore bulk purchasing options to leverage potential discounts.
- Factor in Delivery Costs: Include the cost of shipping and handling in your budget, as this can vary significantly depending on the supplier’s location and the order size.
- Consider Rental Options: For short-term needs or projects with uncertain requirements, renting rollers might be a more cost-effective solution.
- Allocate a Contingency Fund: Set aside a portion of the budget to cover unexpected costs or price fluctuations.
- Stay Informed About Market Trends: Keep an eye on market trends and price fluctuations to time your purchases during favorable conditions.
By understanding the factors that influence return roller pricing and applying strategic budgeting practices, you can ensure that your conveyor system project is cost-effective without compromising on quality or performance.
Installation and Maintenance of Return Rollers
Proper installation and maintenance are crucial for the longevity and optimal performance of return rollers in conveyor systems. This section provides basic guidelines for installing return rollers and offers maintenance tips to ensure they continue to operate efficiently over time.
Basic Installation Guidelines for Return Rollers
- Preparation: Before installation, ensure that the conveyor frame is level and square. This foundational step is crucial for the proper alignment of the return rollers.
- Spacing: Adhere to the manufacturer’s recommended spacing for return rollers. Proper spacing prevents belt sag and ensures even distribution of the load.
- Alignment: Return rollers must be aligned perpendicular to the direction of the belt travel. Misaligned rollers can cause the belt to track off-center, leading to premature wear and potential damage.
- Secure Mounting: Fasten the rollers securely to the conveyor frame to prevent movement or vibration during operation. Use the appropriate hardware as specified by the manufacturer.
- Testing: After installation, rotate the rollers manually to ensure they move freely without resistance or binding. This check helps identify any installation issues that need to be addressed.
- Initial Operation: Run the conveyor belt at a low speed to observe the behavior of the return rollers. Make any necessary adjustments to ensure smooth operation.
Maintenance Tips to Ensure Longevity and Optimal Performance
- Regular Inspections: Conduct regular inspections of return rollers to identify signs of wear, damage, or misalignment. Early detection of issues can prevent more significant problems down the line.
- Lubrication: Follow the manufacturer’s recommendations for lubricating the roller bearings. Proper lubrication reduces friction, wear, and the risk of overheating.
- Cleaning: Keep the return rollers clean, especially in environments where dust, debris, or corrosive materials are present. Build-up on the rollers can affect their performance and lead to premature failure.
- Adjustment and Realignment: Periodically check the alignment of the return rollers and make adjustments as needed. Proper alignment is essential for the efficient operation of the conveyor system.
- Replacement of Worn Parts: Replace worn or damaged rollers promptly to maintain the integrity of the conveyor system. Delaying replacement can lead to further damage and increased operational costs.
- Record Keeping: Maintain records of maintenance activities, including inspections, lubrications, adjustments, and replacements. This documentation can help track the performance and maintenance needs of the return rollers over time.
- Training: Ensure that personnel responsible for maintenance are properly trained in the care and upkeep of return rollers. Knowledgeable staff can more effectively identify and address issues.
- Use of Proper Tools: Utilize the correct tools and equipment for maintenance tasks to prevent damage to the return rollers and ensure the safety of maintenance personnel.
By following these installation and maintenance guidelines, you can enhance the performance and extend the lifespan of your return rollers, contributing to the overall efficiency and reliability of your conveyor system.
Looking for reliable conveyor rollers? Send us your inquiry now and discover our extensive range!
FAQs about Return Roller
What is a return roller?
A return roller, part of a conveyor system’s framework, plays a pivotal role in supporting the return path of the conveyor belt. This component ensures the belt moves smoothly and remains aligned, preventing sagging on the underside. Return rollers are strategically placed along the conveyor’s length, maintaining tension and contributing to the belt’s longevity. Their design and placement are crucial for minimizing wear and tear, reducing operational noise, and enhancing overall system efficiency. Manufacturers offer various return roller types, including standard, rubber-coated, and self-cleaning options, each tailored to specific operational needs and environmental conditions. The choice of return roller significantly impacts the conveyor system’s maintenance requirements, operational costs, and longevity.
A conveyor idler is a critical component of a conveyor system, designed to support the conveyor belt and the material being transported along the belt’s length. Idlers are cylindrical rods that rotate freely and are spaced at regular intervals along the conveyor frame. Their primary function is to provide a smooth surface for the belt to ride on, reducing friction and wear. Conveyor idlers come in various types, including carrying idlers, which support the weight of the material on the belt, and return idlers, which support the empty belt on its return journey. The design and spacing of idlers play a significant role in determining the conveyor’s efficiency, belt wear rate, and the need for maintenance.
A conveyor belt itself is not a pulley, but it operates in conjunction with pulleys in a conveyor system. Pulleys are wheel-like components that the conveyor belt wraps around. They are located at the ends of the conveyor structure and serve to drive the belt and change its direction. The drive pulley, powered by a motor, provides the force that moves the belt and the materials it carries. The tail pulley, located at the opposite end, acts as a guide to redirect the belt back along the return path. While the conveyor belt is the moving surface that transports materials, pulleys are the components that provide the necessary rotation and tension to keep the belt moving efficiently.
Idlers are typically made from durable materials capable of withstanding the operational demands of a conveyor system. The most common material used for idler construction is steel, known for its strength, durability, and resistance to wear. Steel idlers can handle heavy loads and are suitable for various industrial applications, including mining, agriculture, and manufacturing. In environments where corrosion or chemical exposure is a concern, idlers may be made from or coated with materials like stainless steel, rubber, or high-density polyethylene (HDPE). These materials offer additional protection against corrosive substances and reduce the risk of material buildup on the idler surface, ensuring smooth belt operation and extended equipment life.
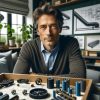
Jordan Smith, a seasoned professional with over 20 years of experience in the conveyor system industry. Jordan’s expertise lies in providing comprehensive solutions for conveyor rollers, belts, and accessories, catering to a wide range of industrial needs. From initial design and configuration to installation and meticulous troubleshooting, Jordan is adept at handling all aspects of conveyor system management. Whether you’re looking to upgrade your production line with efficient conveyor belts, require custom conveyor rollers for specific operations, or need expert advice on selecting the right conveyor accessories for your facility, Jordan is your reliable consultant. For any inquiries or assistance with conveyor system optimization, Jordan is available to share his wealth of knowledge and experience. Feel free to reach out at any time for professional guidance on all matters related to conveyor rollers, belts, and accessories.