Installation Tips for Roller Trough Belt Conveyors
A roller trough belt conveyor is a type of conveyor system specifically designed for efficient and reliable material transportation. It features rollers that support a trough-shaped belt, ensuring the secure and continuous movement of heavy or bulky materials. The primary function of a roller trough belt conveyor is to facilitate the smooth transfer of goods across industrial settings.
Common applications include mining, construction, recycling facilities, and manufacturing plants, where they transport raw materials, finished products, and everything in between. By streamlining logistics, a roller trough belt conveyor becomes indispensable for optimizing productivity and minimizing operational costs across multiple sectors.
Design Features of Roller Trough Belt Conveyors
Detailed Exploration of Trough Belt Conveyor Design
The roller trough belt conveyor has become indispensable across industries due to its adaptable, robust, and efficient design. This system’s architecture aims to maximize the safe and seamless transportation of various materials. Referencing comprehensive sources like the “trough belt conveyor design pdf,” we find several crucial design aspects that ensure optimal performance.
- Belt Material
The belt is crafted from various materials like rubber, PVC, polyester, and steel cord, each offering specific benefits. Rubber belts provide flexibility and strength, while PVC belts offer chemical resistance. Polyester belts add tensile strength, and steel cord belts excel in handling heavy loads. - Frame Construction
Conveyor frames are designed using steel, aluminum, or stainless steel, depending on the application’s demands. Steel frames provide high durability, aluminum frames are lightweight and corrosion-resistant, and stainless steel is ideal for hygienic environments. - Troughing Idlers
The troughing idlers are a series of rollers set at an angle to form the trough shape, guiding and supporting the belt. The angle is adjustable, typically ranging from 20 to 45 degrees, providing versatile load handling. These idlers ensure materials remain securely in the trough, minimizing spillage. - Drive and Tensioning System
Powerful motors drive the belt, while tensioning systems keep it taut. This combination ensures consistent movement even under heavy loads. The drive system is designed for variable speed control to accommodate different operational requirements. - Loading and Discharge Mechanisms
Loading chutes and discharge points are carefully engineered to minimize material loss. Impact beds are often used to cushion the belt during loading, and discharge chutes are designed for smooth material flow. - Safety and Monitoring
Modern roller trough belt conveyors incorporate various safety features like emergency stop buttons, guardrails, and fire detection systems. Advanced monitoring systems detect belt misalignment or slippage to prevent downtime.
Importance of Troughing Idlers and Their Role in the Conveyor System
- Material Containment
Troughing idlers are pivotal in shaping the belt into a U-shaped trough, ensuring secure material containment and reducing spillage. - Load Distribution
They distribute the load evenly across the belt, preventing undue stress and extending the belt’s service life. - Reduced Belt Damage
By providing consistent support, troughing idlers reduce localized wear and tear, protecting the belt from premature damage. - Energy Efficiency
Proper alignment and support from troughing idlers reduce drag, leading to energy savings. - Smooth Material Flow
The shape formed by the troughing idlers ensures that the material flows smoothly, maintaining production efficiency. - Adaptability
Troughing idlers can be adjusted to different angles to accommodate varying material types and loads, providing flexibility in conveyor system design.
Types and Variations of Roller Trough Belt Conveyors
Roller trough belt conveyors are essential components in various industries, used predominantly for moving bulk materials efficiently over long distances. Below, we delve into the types and variations of these systems, focusing on new versus used options, different conveyor types, and the role of return rollers.
Comparison Between New and Used Roller Trough Belt Conveyors
When selecting a roller trough belt conveyor, one significant decision is choosing between new and used models. This choice can impact both cost and performance. Here’s a comparative table outlining key differences:
Feature | New Roller Trough Belt Conveyor | Used Roller Trough Belt Conveyor |
---|---|---|
Cost | Higher initial investment | Lower initial cost but potential hidden maintenance costs |
Availability | Longer lead times due to manufacturing | Readily available |
Reliability | Higher, with warranty coverage | Varies, dependent on previous usage |
Lifespan | Longer, with latest technology | Shorter, with possible wear and tear |
Technology | Latest features and efficiencies | May lack recent upgrades |
Overview of Different Types
Roller trough belt conveyors come in various designs, each suited to specific logistical requirements and material characteristics. The primary types include:
- Flat Belt Conveyors: These are versatile and can carry a wide range of items from different industries. They consist of a flat belt surface that moves over a series of rollers, ideal for boxes, packages, and other rigid materials.
- Closed Belt Conveyors: Designed to contain the material and protect it from the environment, these conveyors are perfect for handling powdery or granular materials. They prevent spillage and contamination, making them ideal for sensitive or hazardous products.
- Trough Screw Conveyors: These conveyors use a helical screw enclosed within a trough to move granular or semi-solid materials. They are especially useful in chemical, agriculture, and food processing industries, where precision and containment are critical.
Specifics on Return Rollers and Their Utility
Return rollers are an integral part of the roller trough belt conveyor system. Positioned along the return path of the belt, these rollers support the belt and prevent sagging, which is crucial for maintaining belt integrity and prolonging its lifespan. Key aspects of return rollers include:
- Material: Typically made from durable materials like steel or rubber, depending on the application’s needs.
- Placement: Strategically placed to support empty sections of the belt and reduce the belt’s wear and tear.
- Functionality: Helps to ensure smooth operation and alignment of the conveyor belt, which is vital for efficient material transport.
Understanding these different aspects of roller trough belt conveyors can help in making informed decisions about which type suits a particular application, balancing factors such as cost, operational needs, and material characteristics.
Manufacturers and Market Leaders of Roller Trough Belt Conveyor
Leading Roller Trough Belt Conveyor Manufacturers
In the ever-evolving world of conveyor technology, the demand for roller trough belt conveyors continues to rise. As industries seek efficient, versatile, and reliable conveyor systems, market leaders have emerged, driving innovation and quality. Here is an overview of seven notable manufacturers that have significantly impacted the roller trough belt conveyor landscape, including companies like Titan Conveyors.
- Titan Conveyors
Known for their extensive product range, Titan Conveyors focuses on offering tailored solutions for a wide array of industrial needs. Their roller trough belt conveyors are engineered for durability and adaptability, making them a preferred choice across various sectors. - Dorner
Dorner emphasizes versatility and modularity, with conveyor systems that can be easily integrated into existing workflows. Their roller trough belt conveyors feature high-end materials and construction techniques, ensuring superior performance. - Flexco
Renowned for their conveyor system components, Flexco also provides comprehensive conveyor solutions. Their roller trough belt conveyors integrate seamlessly with their belt fasteners and cleaners, delivering cohesive and efficient operations. - Hytrol
With a strong reputation in the logistics sector, Hytrol’s roller trough belt conveyors are designed to meet the stringent demands of distribution centers and warehouses, emphasizing speed, accuracy, and reliability. - Interroll
Specializing in material handling, Interroll’s products are recognized for their energy efficiency and precision. Their roller trough belt conveyors are built to optimize workflow while minimizing maintenance requirements. - Rexnord
Rexnord’s roller trough belt conveyors are engineered for tough environments, offering exceptional durability. They focus on reducing operational costs by extending the lifespan of their conveyor systems. - Martin Engineering
Martin Engineering is known for their comprehensive conveyor system solutions. Their roller trough belt conveyors incorporate advanced engineering practices to improve material flow, increase throughput, and minimize spillage.
Insights into What Sets These Manufacturers Apart
- Customization
Leading manufacturers provide highly customizable roller trough belt conveyor systems, allowing clients to adapt these conveyors to their unique needs. - Quality Materials
Premium materials ensure longevity and reliability, reducing downtime and maintenance costs. - Innovation in Design
Engineers at these companies are constantly innovating, developing advanced designs that increase efficiency and productivity. - Energy Efficiency
A strong focus on energy efficiency helps clients reduce operational costs while achieving environmental sustainability. - Integrated Systems
Their conveyor systems integrate seamlessly with other material handling equipment, offering complete end-to-end solutions. - Industry-Specific Solutions
Whether it’s logistics, manufacturing, or food processing, these manufacturers design systems tailored to specific industry needs. - Robust Technical Support
Comprehensive customer support ensures clients receive assistance in installation, maintenance, and system optimization. - Modular Configurations
Modular conveyor systems offer flexibility, enabling easy reconfiguration to meet changing production requirements. - Global Reach
These manufacturers have a global presence, ensuring localized support and rapid response times for their roller trough belt conveyor clients worldwide.
Pricing and Purchasing Tips on Roller Trough Belt Conveyor
Factors Influencing the Price of Roller Trough Belt Conveyors
When considering a roller trough belt conveyor, several factors directly impact its price. Understanding these can help you make an informed purchasing decision:
- Belt Material
The type of belt material significantly affects pricing. Premium belts, such as those with steel cords or specialized coatings for chemical resistance, will cost more than standard rubber belts. - Conveyor Length and Width
Longer and wider conveyors naturally require more materials and components, leading to higher costs. - Frame Material
Conveyor frames made of stainless steel or special corrosion-resistant alloys will be pricier than standard steel or aluminum. - Motor and Drive System
Conveyors with sophisticated drive systems or higher horsepower motors suitable for heavy-duty operations typically have a higher price tag. - Customizations
Any additional features, like custom loading/discharge points, monitoring systems, or modular configurations, will add to the cost. - Shipping and Installation
Depending on location, shipping, installation, and commissioning costs can vary widely, particularly for long-distance or international transport.
Tips on Where to Find Roller Trough Belt Conveyors for Sale and How to Assess Their Value
- Manufacturer Websites
Check directly with manufacturers for the most accurate information on product specifications and pricing. - Authorized Distributors
Distributors often carry a broad range of brands and can provide comparative insights. - Trade Shows and Exhibitions
Industry events allow you to meet multiple vendors and inspect various models firsthand. - Online Marketplaces
These are useful for comparing prices across different suppliers. - Refurbished Equipment Suppliers
Consider suppliers who sell refurbished conveyor systems if you’re on a tighter budget. - Request Quotes
Asking for quotes from multiple vendors helps gauge the market rate. - Inspect Belt Quality
The belt should be inspected for quality, thickness, and material type to ensure durability. - Verify Frame Strength
Ensure the frame is structurally sound, particularly for heavy-load applications. - Check Drive System
Evaluate the motor, gearbox, and drive system for efficient and reliable operation. - Inquire About Support
Post-purchase support, like technical assistance and spare parts availability, is crucial. - Investigate Warranty
Confirm the warranty terms, including what components and repairs are covered. - Seek Reviews
Research customer reviews or request references from the vendor to verify the product’s reputation.
Advice on Selecting the Right Conveyor for Specific Industrial Needs
- Load Capacity
Choose a conveyor that can handle your required load volume and weight without excessive wear. - Material Compatibility
Ensure the belt material is suitable for the specific materials you need to transport. - Operational Speed
Match the conveyor’s speed to your production needs for efficient workflow. - Environmental Conditions
Select a conveyor built for your environment, such as food-grade for hygiene or corrosion-resistant for harsh chemicals. - Space Constraints
Consider the conveyor’s footprint and ensure it fits well within your available space. - Energy Efficiency
Opt for energy-efficient drive systems to reduce operational costs over time. - Maintenance Requirements
Evaluate maintenance needs and choose a design that minimizes downtime. - Modularity
If your production needs frequently change, modular systems offer easier reconfiguration. - Automation Capability
Automated systems improve accuracy and efficiency if your operations involve repetitive tasks. - Compliance
Ensure the conveyor meets industry standards and regulatory compliance for your sector.
Installation and Maintenance of Roller Trough Belt Conveyor
Guidance on the Installation Process of Roller Trough Belt Conveyors
Proper installation is key to ensuring the efficient operation of any roller trough belt conveyor. Follow these guidelines to facilitate a smooth setup:
- Site Preparation
Survey the installation area for proper leveling and alignment. Ensure the site is free from obstructions and has sufficient space for the conveyor’s footprint. - Foundation Construction
If needed, construct a solid foundation or structure to support the conveyor frame. The foundation should accommodate the conveyor’s weight and the load it will carry. - Frame Assembly
Begin by assembling the conveyor frame, securing all components with bolts and welds as per manufacturer guidelines. Use a spirit level to maintain horizontal alignment. - Idler Installation
As part of how to install a conveyor belt, install troughing idlers at specified intervals. Ensure they are correctly angled and aligned to prevent belt misalignment during operation. - Belt Placement
Carefully position the belt over the frame and idlers. Secure one end to the drive drum and the other to the take-up pulley. - Drive and Tensioning Setup
Attach the drive system, ensuring that motors and gearboxes are properly secured. Adjust the tensioning system to ensure the belt remains taut without over-tensioning. - Loading and Discharge Points
Install the loading and discharge points, ensuring a smooth material flow. If necessary, add impact beds at loading zones to cushion the belt. - Final Adjustments and Testing
Inspect the entire system for alignment and secure fittings. Conduct a test run without a load to identify and correct any operational issues before full-scale production.
Best Practices for Maintaining Efficiency and Prolonging the Life of the Conveyor
- Regular Inspections
Conduct routine inspections to check for wear and tear in the belt, idlers, drive systems, and frame. Look out for misalignment, unusual noise, and overheating. - Belt Tracking
Monitor belt tracking regularly. Adjust the tension and alignment of the belt to prevent uneven wear. - Lubrication
Apply lubricant to moving parts, like bearings and gearboxes, to minimize friction and extend their lifespan. - Cleanliness
Keep the conveyor system clean, particularly around the loading and discharge zones. Spilled material can cause damage to the belt and rollers if not removed promptly. - Component Replacement
Replace worn components like idlers, bearings, and belts as soon as they show signs of degradation. Preventive replacement can minimize downtime. - Training and Documentation
Train operators on proper usage and safety protocols. Maintain detailed maintenance logs to track issues and service intervals.
These best practices ensure your roller trough belt conveyor operates efficiently and remains productive over its lifespan.
FAQs about Roller Trough Belt Conveyor
A trough conveyor belt is a type of conveyor system designed to carry loose bulk materials efficiently. It consists of a belt that is configured in a trough-like shape using angled idlers known as troughing idlers. These idlers support the belt and help form a U-shaped cross-section that cradles the material, preventing spillage and enabling smooth transport. Trough conveyor belts are extensively used in industries like agriculture, mining, and construction to move grain, coal, sand, and other granular or powdery materials. The angle of the trough typically ranges from 20 to 45 degrees, ensuring the safe and steady conveyance of materials over long distances.
A troughing roller is a component of a conveyor system, specifically designed to shape the conveyor belt into a trough. It consists of multiple rollers arranged at an angle to form the belt into a U-shape, creating a trough that holds loose materials securely as they are transported. The troughing roller assemblies are usually placed at regular intervals along the conveyor frame to provide consistent support and prevent the belt from sagging. They come in varying angles, such as 20°, 35°, and 45°, to accommodate different material types and conveyor specifications. Troughing rollers are critical in preventing material spillage and ensuring smooth, efficient transport in applications like mining, grain processing, and recycling.
A roller belt conveyor is a type of conveyor system that utilizes rollers placed underneath a moving belt to support and transport various materials. The rollers minimize friction and provide a stable base for the belt, which in turn carries items from one point to another. These conveyors are versatile and suitable for transporting light to heavy materials, including boxes, packages, and bulk goods. They can also be designed to handle items on both flat and inclined planes, making them widely applicable in manufacturing, logistics, and distribution centers. Roller belt conveyors can feature straight, curved, and inclined sections, providing flexibility in system layout and accommodating complex production workflows.
A roller conveyor is a material handling system that uses a series of rollers placed in a frame to transport items. Unlike a roller belt conveyor, which employs a moving belt, a roller conveyor moves items directly on the rollers themselves. They come in two main types: gravity roller conveyors and powered roller conveyors. Gravity roller conveyors rely on gravity or manual pushing to move items along the frame, making them ideal for lightweight goods. Powered roller conveyors use motorized rollers or belts to automatically transport items and are suitable for heavier loads or where automation is required. Roller conveyors are commonly used in warehousing, packaging, and manufacturing industries due to their efficiency and adaptability to different material types and sizes.
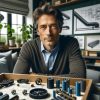
Jordan Smith, a seasoned professional with over 20 years of experience in the conveyor system industry. Jordan’s expertise lies in providing comprehensive solutions for conveyor rollers, belts, and accessories, catering to a wide range of industrial needs. From initial design and configuration to installation and meticulous troubleshooting, Jordan is adept at handling all aspects of conveyor system management. Whether you’re looking to upgrade your production line with efficient conveyor belts, require custom conveyor rollers for specific operations, or need expert advice on selecting the right conveyor accessories for your facility, Jordan is your reliable consultant. For any inquiries or assistance with conveyor system optimization, Jordan is available to share his wealth of knowledge and experience. Feel free to reach out at any time for professional guidance on all matters related to conveyor rollers, belts, and accessories.