Roller Trough Efficiency in Modern Conveyor Systems
In the intricate world of conveyor system operations, roller troughs stand out as essential components, instrumental in shaping conveyor belts into efficient material-carrying troughs. These troughs play a critical role in ensuring materials are transported safely and efficiently, minimizing spillage and enhancing the overall capacity of conveyor systems. Roller troughs are not just pivotal for maintaining material containment; they also significantly contribute to the alignment and longevity of conveyor belts, underscoring their importance in industrial environments. This article delves into the various types and functions of roller troughs, providing valuable insights into how they optimize conveyor system performance. By focusing on the design and application of roller troughs, we aim to illuminate their critical role in improving material handling processes, ensuring readers gain a comprehensive understanding of their significance within conveyor systems.
What are Roller Troughs and Their Importance
Roller troughs are a fundamental component within conveyor systems, designed with a distinct purpose: to shape the conveyor belt into a trough form. This unique configuration is pivotal for the efficient transportation of materials across various distances and elevations. By molding the belt into a concave shape, roller troughs ensure that materials are centralized and securely contained during movement, thereby increasing the volume of materials that can be transported while minimizing spillage.
Defining Roller Troughs and Their Functions
At its core, a roller trough consists of a series of idlers arranged in such a way that they support the conveyor belt and form it into a trough. These idlers are strategically positioned and angled to maintain the belt’s trough shape, ensuring that materials remain within the confines of the belt’s edges. This design is especially critical in the bulk material handling industry, where the secure transport of materials is paramount. By enabling the conveyor belt to carry a larger volume of material, roller troughs significantly enhance the efficiency and productivity of conveyor systems.
The Importance of Roller Troughs in Ensuring Material Safety and Enhancing Conveyor Efficiency
The significance of the roller trough extends beyond merely shaping the conveyor belt – it plays a crucial role in ensuring material safety and enhancing the overall efficiency of the conveyor system. By preventing material spillage, roller troughs not only reduce waste and the need for additional cleanup but also protect the conveyor belt and mechanical components from potential damage caused by loose material. Furthermore, by ensuring that materials are centrally located on the belt, roller troughs contribute to more stable and balanced material transport, reducing the risk of accidents and improving overall operational safety.
Additionally, the efficient design of roller troughs aids in reducing the energy consumption of conveyor systems. By facilitating smoother material flow and reducing belt resistance, these components can lead to significant energy savings, contributing to more sustainable and cost-effective operations. In essence, the roller trough is indispensable for industries reliant on conveyor systems for material transport, providing a crucial solution for improving safety, efficiency, and operational sustainability.
Types of Roller Troughs
Understanding the different types of roller troughs is essential for selecting the right components for varying conveyor system applications. Each type is designed to fulfill a specific role within the conveyor’s functionality and efficiency, from transporting materials to maintaining the conveyor belt’s integrity.
Troughing Idler Rollers
Troughing idler rollers are the foundation of the roller trough system and are pivotal in maintaining the belt’s concave shape. They are primarily located on the conveying side of the belt, situated in a c-shaped formation to ensure materials remain centered and secure during transport. Troughing idlers are crucial for bulk material handling industries, such as mining and agriculture, where large quantities of material need to be moved efficiently and safely. The smooth operation of the conveyor system heavily relies on the robust design and strategic placement of these idlers.
Troughing Idler Rollers: Design and Functionality
Troughing idler rollers are uniquely crafted components designed to shape the conveyor belt into a trough-like form. This design is essential for stabilizing and securing the materials being transported over various distances. Traditionally, a troughing idler set consists of three rollers: a central flat roller flanked by two angled side rollers. The precise degree of angling on the side rollers is crucial; it dictates the depth and shape of the trough formed by the conveyor belt, influencing both the volume of material the belt can carry and the stability of that material during transport.
The design and functionality of troughing idler rollers are pivotal in industries that manage bulk material handling. They are typically employed in sectors like mining, agriculture, and construction, where large quantities of materials—ranging from ores to grains to building aggregates—need to be moved efficiently and without loss. The roller trough configuration reduces spillage by keeping the materials centered and contained within the bounds of the moving belt.
The Critical Role of Troughing Idler Rollers in Bulk Material Handling
In the context of roller trough systems, the significance of troughing idler rollers cannot be overstated. Positioned on the conveying side of the conveyor belt, these rollers are fundamental to the operational integrity of bulk material handling processes. They not only facilitate the transportation of large volumes of materials but also ensure the safety and durability of the conveyor system itself.
The strategic placement of troughing idler rollers along the conveying path helps maintain the optimal shape of the conveyor belt, crucial for preventing the spillage of materials. This arrangement also contributes to the even distribution of load throughout the belt’s length and width, which enhances the longevity of the belt by preventing undue stress and wear in any single area. Moreover, by ensuring that the belt operates within its ideal form—neither too stretched nor too slack—these rollers play a vital role in the smooth and efficient operation of the conveyor system, reducing downtime and maintenance needs.
In essence, the role of troughing idler rollers within the roller trough system is multifaceted. Beyond merely shaping the conveyor belt, they are instrumental in optimizing the performance, safety, and sustainability of bulk material transport processes. Through their innovative design and strategic placement, they embody a critical solution for the challenges of modern material handling.
Return Rollers
The purpose of return rollers is to support the belt on its return path after material discharge. These rollers are critical for maintaining belt tension and ensuring proper alignment, which are key factors for the efficient operation of conveyor systems. To enhance safety and the longevity of the belt, return roller guards are often employed to protect the rollers from material build-up and to prevent accidents, making them a necessary feature in roller trough design for a safe and reliable conveyor operation.
What Are Return Rollers?
Return rollers are an essential component of the roller trough system, designed to support the underside, or return path, of the conveyor belt. These rollers are strategically placed along the length of the conveyor system, ensuring that the belt remains stable and maintains a consistent path as it loops back to the beginning of the conveyor line after depositing materials. The primary function of return rollers is to provide a smooth surface for the conveyor belt to glide over, reducing friction and wear on both the belt and the system. By minimizing resistance and drag, return rollers contribute to the overall efficiency of the conveyor operation, ensuring materials are transported seamlessly from point A to point B.
Necessity of Return Rollers for Belt Tension and Alignment
The operational integrity of a conveyor belt heavily relies on its tension and alignment, aspects in which return rollers play a critical role. Proper tensioning of the conveyor belt is crucial for efficient material transport and to prevent slippage at the drive rollers. Return rollers help maintain the appropriate level of tension by ensuring that the belt is supported uniformly across its entire return path. This uniform support prevents sagging and ensures the belt does not become overstretched or excessively taut, which could lead to mechanical failures.
In addition to tension regulation, return rollers are indispensable for maintaining the alignment of the conveyor belt. Misalignment can lead to uneven wear on the belt edges, material spillage, and increased energy consumption due to higher friction. By facilitating a stable return path, return rollers ensure that the belt remains correctly aligned with the conveyor structure, reducing the risk of operational disturbances and prolonging the lifespan of the conveyor system.
Importance of Return Roller Guards in Conveyor Operations
Safety in conveyor operations cannot be overstated, and return roller guards play a significant role in ensuring a safe work environment. These guards are designed to shield the return rollers and the moving conveyor belt from accidental contact, protecting workers from potential injury. Besides safeguarding personnel, return roller guards also prevent materials from becoming trapped between the rollers and the belt, which could cause damage to the belt and lead to operational disruptions.
The installation of return roller guards is considered a best practice in managing roller trough systems. It exemplifies the industry’s commitment to safety while highlighting the emphasis placed on preventive measures to ensure the continued efficiency and reliability of conveyor operations. Through these protective measures, industries can mitigate risks associated with conveyor usage, thereby enhancing the overall safety and productivity of material handling processes.
Impact Rollers
Impact rollers are strategically placed at conveyor loading points to absorb the shock and stress of falling materials. This type of roller is designed to reduce the force at which materials drop onto the belt, which is essential in preventing excessive wear and tear on the conveyor belt. Impact rollers are vital in extending the longevity of the conveyor system, playing a significant role in preserving the belt’s structural integrity and ensuring smooth operation over time.
Overview of Impact Rollers and Their Shock Absorption Function
Impact rollers—also known as impact idlers—are designed to be located at the loading points of a conveyor system, the areas where material is transferred onto the conveyor belt. Given the potentially heavy and sharp nature of bulk materials being transferred, their sudden drop onto the belt can generate a high level of physical stress on the conveyor system. Without adequate protection, the associated shock and impact may lead to premature wear and tear on the conveyor belt, chipping, or even more substantive damage.
This is where the impact rollers step in. Graduated in terms of their diameters and lined with rubber rings or sleeves, these rollers serve the crucial function of absorbing those shocks. This reduces the immediate impact on the belt, maintaining system efficiency and longevity.
How Impact Rollers Prolong Belt Lifespan
The importance of impact rollers for prolonging conveyor belt lifespan within a roller trough system cannot be undersold. With each material drop on the conveyor belt, the force transferred creates high-stress points on the belt surface. Over time, these pressure points can lead to structural wear and tear, cracking, and eventually, belt failure. Undoubtedly, the costs of such failures—in terms of both operational downtime and component replacements—can be significant.
Impact rollers act as a protective layer between the bulk materials and the belt. The robust structure and the rubber lining of these rollers give them a resilient shock-absorbing capacity, mitigating the force of each impact and distributing it evenly across the belt surface. By doing so, impact rollers effectively reduce concentrated stress points, minimizing wear and tear and prolonging the belt’s operational life.
In the demanding environment of bulk material handling, the presence of impact rollers in a roller trough system offers assurance of smoother operations, lesser interruptions, and extended lifespan of the critical components of conveyor systems.
Conveyor Idler Rollers
Conveyor idler rollers include a variety of rollers like return idlers, which contribute to the general functionality of conveyor systems. Their role extends to supporting the belt and the material being transported, whether on the carrying side or along the return section. The PPI idlers catalog provides a broad selection of idler options, catering to different needs based on conveyor belt width, load capacity, and operational environment, ensuring there’s a suitable conveyor idler for every application that requires the efficiency and reliability of a robust roller trough system.
Conveyor Idler Rollers: The Unsung Workhorses
Idler rollers, or simply idlers, are a range of specialized rollers that maintain the stability and efficient operation of the conveyor system within a roller trough setup. Influencing the shape, alignment, tension, and surface support of the conveyor belt, these components are truly the unsung workhorses of the conveyor system.
One such variant is the return idler roller. Positioned to support the return path of the conveyor belt, these rollers ensure that the belt remains in a stable path as it makes its return journey after depositing carried materials. Correctly installed and functioning return idler rollers allow a smooth and friction-reduced glide-over for the conveyor belt, extending the belt’s life and overall conveyance efficiency.
The PPI Idlers Catalog: A Pantheon of Idler Options
For those seeking a range of idler options, the PPI (Precision Pulley & Idler) Idlers catalog serves as an invaluable resource. The catalog boasts an array of idler configurations, each tailored to specific needs within a roller trough system. With an impressive lineup of designs including troughing idlers, return idlers, impact idlers, and more, the catalog enables the user to select an idler type that best fits their conveyor system requirements.
PPI’s commitment to quality and durability ensures that each idler option offered in the catalog stands up to the highest standards of operation. Whether you’re handling fine grains or large rocks, lighter loads or heavy-duty mass, the PPI idlers catalog provides a spectrum of solutions, each designed to enhance the efficiency, reliability, and longevity of conveyor operations within a roller trough system.
While conveyor idler rollers might be unassuming in their appearance, their strategic role within the roller trough system cannot be underestimated. From the varied types of idlers to the copious options available in the PPI idlers catalog, the universe of conveyor idlers is vast, underscoring the complexity and precision involved in material handling processes.
Selection of Roller Troughs: Factors and Considerations
For the smooth and efficient operation of conveyor systems, choosing the right roller trough is of paramount importance. Numerous factors, including the size, material, and application requirements, come into play when deciding on an ideal roller trough. Additionally, taking into account the roller trough size for compatibility with the conveyor belt width and material load is crucial. We also delve into the significance of incorporating the conveyor return roller protective cover into your roller trough system.
Sizing, Material, and Application Requirements: Key Considerations in Roller Trough Selection
When it comes to selecting the ideal roller trough, the size, material, and application requirements are vital considerations that directly influence the performance and longevity of the conveyor system. The size of the roller trough should align with the conveyor belt’s width and the load it carries—too wide, and you risk unnecessary expenditure and space utilization, too narrow, and the system’s efficiency and safety could be compromised.
Moreover, the material from which the roller trough is made is another significant consideration. From steel and plastic to composite materials, the choice depends on factors such as the nature of the materials being transported, environmental conditions, and the level of wear and tear the system is likely to face.
Ultimately, the application requirements offer the final say in roller trough selection. A roller trough that excels in lightweight, indoor material handling may falter in heavy-duty outdoor applications, so understanding the specific needs and challenges of your operation is fundamental to making the right choice.
The Pivotal Role of Conveyor Return Roller Protective Cover
One often overlooked but vital component to consider when choosing a roller trough is the conveyor return roller protective cover. This protective cover plays a critical role in ensuring worker safety and preventing accidents. Positioned over the return rollers, these covers not only minimize the risk of accidental contact with moving parts but also prevent materials from becoming wedged between the belt and rollers, mitigating potential system disruptions and belt damage.
In industries where worker safety is paramount, the conveyor return roller protective cover emerges as an unsung hero. An effective cover will not interfere with the operation of the roller trough system but rather integrate seamlessly, providing a necessary layer of protection that can significantly reduce the risk of unfortunate incidents.
To summarize, the process of selecting the right roller trough requires a comprehensive understanding of various factors. Evaluating these considerations carefully will aid in choosing the roller trough that will serve you best for the long haul, enhancing the overall efficiency and safety of your operation.
Where to Buy Roller Troughs
Investing in the right roller trough, including components such as impact rollers, conveyor return rollers, and return idler rollers, necessitates careful thought and reliable vendors. Resources like the PPI idlers catalog greatly simplify the process by offering quality selections and detailed specifications.
Ensuring Value: Factors to Consider When Purchasing Roller Troughs
When looking to acquire the appropriate roller trough or its components, several considerations come into play. Here are four key suggestions:
- Research Integrity: Evaluate the reputation and customer reviews of your potential vendors. Prior customers’ experiences with a vendor can provide valuable insight into the quality of products and service you can expect.
- Quality Check: High-quality components can differ significantly in performance and longevity compared to cheaper alternatives. Ensure that the roller trough and related components like impact rollers, conveyor return rollers, and return idler rollers meet industry standards.
- Diversity in Products: Choosing vendors offering a varied range of products gives you the flexibility to pick the ideal fit for your specific application needs, hence enhancing system efficiency.
- After-sales Services: A vendor that provides after-sales services such as maintenance and repairs is an invaluable asset. The need for these services can arise unexpectedly and having a trusted vendor at hand to address these needs can save time and avoid unnecessary trouble.
Reliable Vendors and the PPI Idlers Catalog: Quality Selections at your Fingertips
From a plethora of vendors available, identifying a reliable one is crucial. For high-standard choices, the Precision Pulley & Idler (PPI) Idlers catalog is a laudable call-out. PPI is renowned for its wide range of top-tier conveyor components. Its idlers catalog offers a comprehensive list of roller trough products, including impact rollers, conveyor return rollers, and return idler rollers – each designed to enhance the performance and lifespan of your conveyor system.
Purchasing from reliable vendors and consulting resources like the PPI idlers catalog ensure you invest in roller trough components that deliver quality, longevity, and, ultimately, value for your money. By choosing wisely, you can ensure the efficiency of your conveyor system and its capability to withstand the challenges of your operational needs.
FAQs about Roller Trough
A trough roller, also known as a troughing idler, forms a critical part of a conveyor belt system. Designed in a C-shaped configuration, the trough roller provides a concave support structure for the conveyor belt. This form ensures that carried materials stay within the center of the belt, preventing spillage and promoting efficient material transport.
The design of a trough roller typically includes three rollers arranged in a pattern that forms the shape of a trough. The central roller is often horizontally aligned, while the two side rollers are strategically angled to create the ‘trough’ for the belt to lie in. The angles and dimensions can vary depending on the specific material handling requirements. In this setup, the trough roller not only guides and supports the conveyor belt but also plays a central role in maintaining the belt’s alignment and preventing its sagging in operating conditions.
The rollers on a conveyor are typically categorized as “idlers”. An idler can represent a wide variety of conveyor system rollers used to support the conveyor belt and the load carried on the belt. There are numerous kinds of idlers, each serving a specific purpose within the conveyance system. Key idler types include:
Troughing idlers: form a concave structure to keep the material on the conveyor belt.
Impact idlers: absorb the shock of heavy material loads being dropped onto the belt.
Return idlers: support the underside or ‘return’ section of the conveyor belt.
In essence, these idler rollers make the movement of the conveyor belt possible, offering support, shaping the belt path, and managing alignment and tension for optimal material conveyance.
A conveyor trough refers to the format or formation of a conveyor system established to manage the efficient transportation of bulk materials. In a conveyor trough, the belt is shaped in a concave manner, usually by a set of specifically angled rollers called troughing idlers or trough rollers. This trough-shaped belt structure is designed to securely hold and transport materials, preventing spillage during the conveyance process.
Whether transporting fine grains, gravel, or large rocks, the conveyor trough setup allows a wide array of materials to be securely moved along the conveyor route. The design of a conveyor trough can vary in angle and dimensions based on specific material handling needs, the load size, and the type of materials being transported.
A roller conveyor is a form of conveyor system where material handling is achieved using a series of rollers mounted in a fixed frame. In such systems, goods and materials are placed directly onto rollers, where they’re then transported from one point of the operation to the next.
Roller conveyors can be either gravity-driven, where objects are moved by the force of gravity or manually pushed, or powered, where the rollers are motor-driven to propel the goods forward. This type of conveyor is commonly used in warehouses, manufacturing centers, and packaging facilities for applications like assembly lines, order picking, and sorting systems.
Powered roller conveyors can also feature components like sensors and controllers to manage the pace and direction of goods, while gravity-based roller conveyors often leverage the work environment’s natural gradient for product-flow. Their efficient, scalable design and easy integration into complex operations make roller conveyors a popular choice across numerous industries.
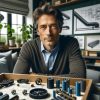
Jordan Smith, a seasoned professional with over 20 years of experience in the conveyor system industry. Jordan’s expertise lies in providing comprehensive solutions for conveyor rollers, belts, and accessories, catering to a wide range of industrial needs. From initial design and configuration to installation and meticulous troubleshooting, Jordan is adept at handling all aspects of conveyor system management. Whether you’re looking to upgrade your production line with efficient conveyor belts, require custom conveyor rollers for specific operations, or need expert advice on selecting the right conveyor accessories for your facility, Jordan is your reliable consultant. For any inquiries or assistance with conveyor system optimization, Jordan is available to share his wealth of knowledge and experience. Feel free to reach out at any time for professional guidance on all matters related to conveyor rollers, belts, and accessories.