Gravity Rollers for Sale: New vs. Used – Making the Right Choice
Gravity rollers play a pivotal role in the seamless operation of material handling and logistics sectors, serving as the backbone for moving goods efficiently across warehouses, production lines, and distribution centers. These rollers, leveraging the fundamental force of gravity, offer a simple yet effective means to transport items from one point to another without the need for external power sources. Gravity roller conveyors, in particular, utilize this passive system to facilitate the movement of various loads, ranging from lightweight packages to heavy pallets, by allowing them to glide over rollers positioned in a slight decline. This operation principle not only maximizes operational efficiency but also significantly reduces energy consumption and operational costs, making gravity rollers an indispensable component in the design of modern material handling systems.
What Are Gravity Rollers
Gravity rollers are foundational elements in the realm of material handling, offering a simplistic yet highly effective means to transport goods across varying distances. These rollers harness the natural force of gravity, providing a seamless movement of items without necessitating external power sources. Below, we delve into the essence of gravity rollers, exploring their definition, operational mechanics, and the myriad benefits they bring to the table across diverse industrial landscapes.
Definition and Description of Gravity Rollers
Gravity rollers are the epitome of efficiency in the material handling sector, characterized by their cylindrical shape and ability to facilitate the smooth transit of goods. Here are eight key points that define and describe gravity rollers:
- Core Mechanism: At their core, gravity rollers are cylindrical tubes that pivot on bearings within a frame, creating a smooth pathway for items to traverse.
- Material Diversity: Manufactured from a range of materials like steel, plastic, and aluminum, they cater to varying operational demands and environmental conditions.
- Adaptability to Load: Engineered to accommodate a spectrum of load capacities, their diameter and wall thickness are tailored to specific requirements.
- Versatile Application: Their design makes them suitable for a wide array of goods, particularly those with flat bottoms, ensuring versatility across industries.
- Low Maintenance: The simplicity of their design translates to minimal maintenance needs, sidestepping the complexities associated with more intricate systems.
- Ease of Installation: Their installation is straightforward, allowing for configurations that include straight, curved, inclined, or declined sections to leverage gravity.
- Economic Efficiency: As passive systems, they represent a cost-effective solution for material transport, eschewing the need for electricity or fuel.
- Flexible Scalability: Their modular nature allows for easy expansion or reconfiguration, accommodating evolving business needs with ease.
How Gravity Rollers Work in Conveyor Systems
The operation of gravity rollers is a marvel of simplicity and efficiency, utilizing the gravitational pull to facilitate movement. Here are seven points that illuminate how gravity rollers function within conveyor systems:
- Operational Principle: They operate on the straightforward principle of gravity, allowing items to move downhill or across flat surfaces effortlessly.
- Initiation of Movement: Occasionally, a gentle push by operators is all that’s needed to get items moving on flat sections.
- Controlling Speed: The velocity of items can be moderated through the use of brakes or by tweaking the conveyor’s slope.
- Guided Paths: Items are steered along predetermined paths using guide rails or manual intervention at critical junctures.
- Uniform Load Distribution: The strategic placement of rollers ensures an even distribution of weight, safeguarding the transported items.
- System Integration: They seamlessly integrate with other conveyor types, creating a cohesive material handling ecosystem.
- Uninterrupted Efficiency: Their design allows for continuous operation, significantly boosting operational throughput.
The Benefits of Using Gravity Roller Conveyors in Various Industries
The adoption of roller gravity conveyors across industries heralds numerous advantages, from operational efficiencies to environmental stewardship. Here are eight benefits that underscore their value:
- Energy Conservation: They stand as beacons of energy efficiency, markedly reducing operational costs by operating without power.
- Enhanced Operational Flow: They streamline the movement of goods within facilities, bolstering overall productivity.
- Improved Safety: With fewer moving parts and no need for manual lifting, they significantly lower the risk of workplace injuries.
- Environmental Friendliness: Their operation minimizes the carbon footprint, offering a greener alternative to powered conveyors.
- User-Friendly: Their operation is straightforward, necessitating minimal training for personnel.
- Operational Flexibility: Their modular design allows for swift reconfigurations, adapting to changing business needs with minimal fuss.
- Robust Durability: Designed for longevity, they withstand regular use with minimal wear and tear.
- Cost-Effectiveness: The low initial investment and reduced operational expenses render gravity rollers an economically sound choice for businesses aiming for efficiency and sustainability.
In essence, gravity rollers embody the principles of simplicity, efficiency, and adaptability, making them indispensable in the optimization of material handling processes across a broad spectrum of industries.
Types of Gravity Rollers Conveyors
Gravity roller conveyors are versatile components in the material handling industry, offering solutions tailored to various operational needs. Each type of roller gravity conveyor serves a specific purpose, designed to optimize efficiency, handle different load capacities, and suit various environments. Here, we explore seven distinct types of gravity roller conveyors, including their unique characteristics and applications.
Standard Gravity Roller Conveyors: Standard gravity rollers are the backbone of many material handling systems, designed to transport items across short to moderate distances. These conveyors are ideal for moving products with a flat bottom, such as boxes, trays, and pallets. They rely purely on gravity and the manual effort of operators or the natural slope of the installation area to facilitate movement. Their simplicity, cost-effectiveness, and ease of maintenance make them a popular choice for warehouses, distribution centers, and assembly lines.
Heavy Duty Gravity Roller Conveyors: Built to withstand heavier loads, heavy-duty gravity roller conveyors feature rollers with larger diameters and thicker walls, often made from materials like steel. They are designed to handle items that are too heavy for standard conveyors, such as large pallets, heavy machinery parts, and bulky containers. These conveyors are typically used in manufacturing facilities, industrial plants, and anywhere that requires the movement of heavy goods. Their robust construction ensures durability and longevity, even under the stress of heavy loads and continuous operation.
Powered Roller Conveyors: While not a type of gravity roller conveyor, powered roller conveyors are worth mentioning for their role in material handling systems. They differ from gravity rollers by using motors to drive the rollers, moving items along the conveyor without manual effort or reliance on gravity. This makes them suitable for a wider range of applications, including inclined paths and long distances where gravity assistance is insufficient. Powered conveyors can handle various load sizes and types, offering speed control and directional changes that gravity conveyors cannot.
Flexible Gravity Roller Conveyors: Flexible gravity roller conveyors are designed for versatility and adaptability, with sections that can be expanded, curved, and bent to navigate around obstacles and through tight spaces. They are ideal for loading docks, packaging areas, and temporary setups where space constraints or layout flexibility is a priority. These conveyors can be easily stored when not in use, making them a practical solution for operations with changing needs.
Curved Gravity Roller Conveyors: Curved gravity roller conveyors allow for the directional change of goods within a conveyor system, facilitating turns and allowing for more complex conveyor layouts. They are essential in systems where space is limited or where the production line requires items to be redirected to different areas. Curved sections are designed to maintain product orientation and spacing without manual intervention.
Incline/Decline Gravity Roller Conveyors: These conveyors are specifically designed with a slope to utilize gravity for moving items either up or down between different elevations. Incline/decline conveyors are crucial in multi-level facilities, such as warehouses with mezzanine storage areas or production facilities requiring the movement of goods between floors. They are equipped with features to control speed and prevent items from sliding too quickly.
Ball Transfer Gravity Conveyors: Ball transfer tables or conveyors consist of a series of mounted ball casters, allowing for the multidirectional movement of goods. They are typically used at workstation interfaces, packaging areas, or within assembly processes where items need to be rotated or precisely positioned. Ball transfer units facilitate the easy handling of products without the need for lifting, significantly reducing manual effort and improving operational efficiency.
Accumulation Gravity Roller Conveyors: Accumulation roller gravity conveyors are designed to allow products to accumulate along the conveyor path without the need for manual intervention, making them ideal for staging products or buffering items between processes. These conveyors typically incorporate rollers that can be individually braked or sections that can be controlled to start or stop the flow of items, allowing products to accumulate without contact. This feature prevents damage to sensitive or fragile items and regulates the product flow for downstream processing. Accumulation gravity conveyors are commonly used in packaging and assembly lines where products need to be grouped or staged before the next phase of production.
Skate Wheel Gravity Conveyors: Skate wheel gravity conveyors consist of small wheels in a series, providing a lightweight and flexible solution for conveying items. These conveyors are particularly effective for lightweight packages and irregularly shaped items that might not travel well on standard roller conveyors. The skate wheels provide more contact points with the product, ensuring stability and smooth movement. Skate wheel conveyors are often used in shipping departments, assembly areas, and loading docks for their versatility and ease of reconfiguration. They can be easily curved and connected to create custom conveyor systems tailored to specific operational layouts.
Each of these types of gravity roller conveyors plays a crucial role in the design of efficient material handling systems. By understanding the specific characteristics and applications of these conveyors, businesses can select the most appropriate gravity rollers to meet their operational needs, enhancing productivity and streamlining processes across various industries.
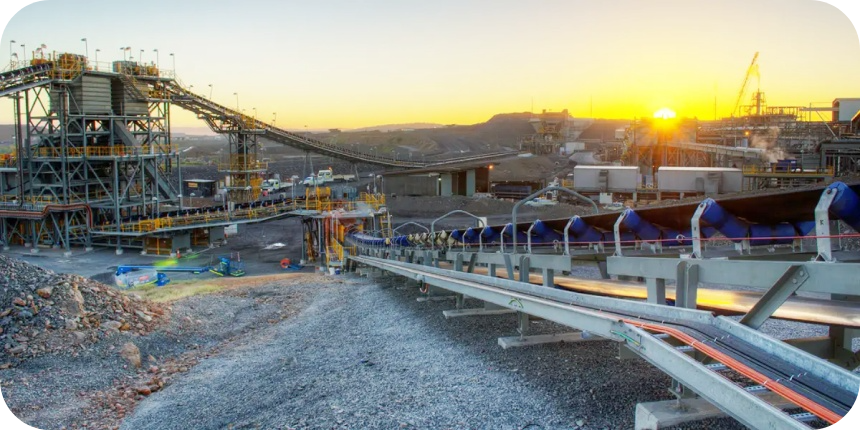
Key Features of Gravity Rollers Conveyors
Gravity roller conveyors are indispensable in the material handling sector, celebrated for their simplicity and efficiency. Here are eight key features that highlight the versatility and functionality of gravity rollers conveyors:
- Roller Diameters and Materials: The diameter and material of the rollers are crucial for accommodating different types of loads. Options range from steel for heavy-duty applications to plastic and aluminum for lighter loads, each offering unique benefits in terms of strength, weight, and corrosion resistance.
- Frame Styles and Materials: Frames provide the structural support for the conveyor and are available in various materials like steel, aluminum, and sometimes plastic. The choice of material and style, including straight, curved, and flexible options, depends on the specific application and load requirements.
- Load Capacity: Gravity roller conveyors are designed to handle a wide range of load capacities. The capacity is influenced by factors such as roller diameter, material, spacing, and frame construction, making it essential to select a system that matches the operational demands.
- Roller Spacing Considerations: The spacing between rollers is a critical design aspect that affects the conveyor’s ability to transport items smoothly. Optimal spacing ensures that items move efficiently without the risk of falling through or becoming stuck.
- Ease of Installation and Integration: These conveyors are favored for their modular design and ease of installation, allowing for quick setup and integration into existing workflows. Adjustable stands and sections enable customization and flexibility in layout planning.
- Maintenance Requirements: With fewer moving parts compared to powered systems, gravity roller conveyors require minimal maintenance. Regular inspections and basic upkeep, such as cleaning and lubrication, help maintain performance and extend the conveyor’s lifespan.
- Cost-Effectiveness: The simplicity of gravity roller conveyors makes them a cost-effective solution for material handling. Lower initial investment and minimal operational costs, due to the absence of electrical components, make them an economical choice for many businesses.
- Energy Efficiency: Operating solely on the force of gravity, these conveyors are an energy-efficient method of transporting goods. This not only reduces operational costs but also supports sustainability efforts by minimizing the environmental impact of material handling operations.
Understanding these key features of gravity rollers conveyors allows businesses to make informed decisions when selecting a conveyor system, ensuring that it meets their specific needs for efficient and effective material handling.
How to Select the Right Gravity Rollers Conveyor
Choosing the appropriate gravity roller conveyor for your operations is a critical decision that impacts efficiency, safety, and productivity. This selection process involves evaluating various factors to match the conveyor system with your specific material handling requirements. Below, we delve into eight essential factors to consider, followed by key design considerations that ensure the chosen gravity rollers conveyors optimize both efficiency and safety.
Essential Factors to Consider
When selecting a gravity roller conveyor, it’s important to thoroughly assess your needs and the capabilities of different conveyor systems. Here are the crucial factors to guide your choice:
- Load Type: The nature of the items being transported—considering their size, shape, and material—is fundamental in choosing the right conveyor. Different types of goods may require specific roller materials or configurations to ensure smooth transit.
- Load Weight: The weight of your products directly influences the required strength and durability of the conveyor. It’s vital to choose a system that can reliably support your heaviest loads without compromise.
- Conveyor Length and Width: The dimensions of the conveyor must be sufficient to handle your largest items with ease, providing enough space to prevent any overhang and maintain stability during transport.
- Environment: The working environment can significantly affect the choice of conveyor materials and design, especially in terms of hygiene requirements or exposure to corrosive substances.
- Incline or Decline: The presence of slopes in your material handling path necessitates conveyors designed to manage inclines or declines effectively, possibly requiring additional features for control and safety.
- Flexibility and Scalability: Anticipating future changes in your operations can save time and money. Opting for a modular conveyor system allows for easy reconfiguration or expansion as your business evolves.
- Integration with Existing Systems: Compatibility with your existing material handling setup is crucial for a seamless operation, ensuring that the new conveyor works harmoniously with other equipment.
- Budget: While initial costs are an important consideration, it’s also wise to think about long-term expenses related to maintenance, energy use, and potential modifications.
Design Considerations for Efficiency and Safety
Designing a roller gravity conveyor system that meets your operational needs while ensuring safety and efficiency involves several key considerations:
- Roller Material and Diameter: Selecting the appropriate roller material and size is crucial for durability and the smooth movement of goods, particularly in relation to the types of items being handled and the specific demands of the operational environment.
- Roller Spacing: Adequate roller spacing is essential to support the smallest items without risk of them falling through or becoming lodged, ensuring a smooth and uninterrupted flow of goods.
- Frame Construction: A robust frame construction is necessary to support anticipated loads reliably, with considerations for environmental suitability, such as resistance to moisture or chemicals.
- Safety Features: Incorporating comprehensive safety features, including guardrails and emergency stops, is vital, especially in designs that include inclined or declined sections, to protect both the products and personnel.
- Ease of Maintenance: Choosing a design that facilitates easy maintenance access to rollers and other critical components can significantly reduce downtime and extend the lifespan of the conveyor.
- Ergonomics: The ergonomic design of the conveyor, particularly regarding manual loading and unloading tasks, is important for worker comfort and safety, helping to prevent strain injuries and improve overall productivity.
By carefully considering these factors and design elements, you can ensure the selection of a gravity roller conveyor that not only meets your current needs but is also adaptable, safe, and efficient for future demands.
Improve efficiency with our conveyor rollers. Contact us today!
Gravity Rollers for Sale: New vs. Used
In the quest to enhance material handling processes, businesses face the critical decision of choosing between new and used gravity rollers. This choice not only impacts the immediate financial outlay but also affects operational efficiency and long-term investment value. Let’s delve into the nuances of purchasing new versus used gravity rollers, examining the advantages and disadvantages of each option, offering guidance for acquiring used conveyors, and detailing strategies to ensure the quality of used equipment.
Advantages and Disadvantages of Buying New Gravity Rollers
Opting for new gravity rollers presents a myriad of benefits, from cutting-edge technology to long-term reliability, yet it’s not without its drawbacks, primarily cost-related.
Advantages:
- Latest Innovations: New gravity rollers incorporate the latest design improvements and materials, enhancing efficiency and durability.
- Customization Options: Tailoring new conveyors to specific operational requirements ensures optimal integration and performance.
- Warranty and Support: Manufacturer warranties and comprehensive customer support offer protection and assistance.
- Longevity and Reliability: The expected lifespan of new equipment is generally longer, providing better value over time.
- Compliance and Safety: New models are more likely to adhere to the latest safety standards, reducing the risk of workplace incidents.
- Reduced Maintenance: Starting fresh with new equipment minimizes early maintenance issues, saving time and resources.
- Immediate Availability: Manufacturers often have stock ready for shipment, minimizing delays in setup or expansion projects.
- Energy Efficiency: Modern designs may include features that lower operational costs through improved energy efficiency.
- Enhanced Reputation: Investing in new equipment can bolster your company’s image by showcasing a commitment to quality and modernity.
Disadvantages:
- Cost: The primary downside is the higher initial investment required, which may be prohibitive for some businesses.
- Higher Initial Investment: The most significant barrier to purchasing new gravity rollers is the upfront cost, which can be substantially higher than that of used equipment. This can strain budgets, especially for startups or businesses looking to expand rapidly.
- Longer Lead Times: Customization options, while beneficial, can result in longer lead times. Manufacturing and delivery of new, tailored gravity roller conveyors might delay project timelines, affecting operational efficiency.
- Depreciation: Like all new equipment, gravity rollers depreciate the moment they are put into use. This rapid depreciation can affect the overall return on investment, especially if the equipment is not utilized to its full potential.
- Over-Specification: There’s a risk of over-specifying when buying new, leading to unnecessary features that inflate costs without providing proportional benefits. Businesses may end up paying for capabilities they do not need.
- Environmental Impact: The production of new gravity rollers involves the consumption of raw materials and energy, contributing to a larger environmental footprint compared to reusing or refurbishing existing equipment.
- Market Availability: While immediate availability is often cited as an advantage, the reality can be different. Popular models or specific customizations might not be readily available, leading to unexpected delays.
Tips for Purchasing Used Gravity Roller Conveyors
Navigating the market for used gravity rollers requires diligence and strategic thinking to uncover the best deals without compromising on quality or suitability.
- Research Sellers: Evaluate the reputation and reliability of vendors to avoid potential pitfalls.
- Conduct Thorough Inspections: Physical or virtual inspections can reveal wear and tear that might not be evident from descriptions alone.
- Inquire About History: Understanding the conveyor’s usage history and maintenance practices can provide insights into its condition and longevity.
- Assess Compatibility: Ensure the used equipment will seamlessly integrate with your existing setup.
- Understand Return Policies: Knowing your options in case the equipment fails to meet expectations is crucial.
- Factor in Shipping Costs: Consider how shipping fees impact the overall value of the purchase.
- Check for Compliance: Verify that the equipment meets current safety and operational standards.
- Evaluate Overall Value: Weigh the initial savings against potential future costs for repairs or upgrades.
Ensuring Quality When Selecting Used Equipment
Securing high-quality used gravity rollers is paramount to avoid unforeseen costs and operational disruptions. Here’s how to ensure you’re making a wise investment.
- Seek Demonstrations: Observing the equipment in action can highlight issues that are not apparent when stationary.
- Look for Signs of Wear: Detailed inspections can uncover damage or wear that may affect functionality.
- Verify Specifications: Double-check that the equipment’s specs align with your needs to avoid mismatches.
- Ask About Past Modifications: Modifications by previous owners could influence the conveyor’s performance or compatibility.
- Consult Experts: When possible, have a technician or engineer assess the equipment’s condition.
- Consider Refurbished Options: Refurbished conveyors might offer a good balance between cost and reliability.
- Inquire About Warranties: Although rare, some used equipment may come with a warranty or guarantee.
- Check Spare Parts Availability: Ensure you can obtain necessary spare parts to avoid downtime.
- Perform a Cost-Benefit Analysis: Balance the upfront savings against the likelihood of additional expenses down the line.
By carefully weighing these considerations, businesses can make informed decisions that align with their operational needs and budget constraints, whether opting for new or used gravity rollers.
Leading Manufacturers of Gravity Rollers
The market for gravity rollers is diverse, with several key players leading the industry through innovation, extensive product ranges, and exceptional customer service. These manufacturers have established themselves as trusted sources for high-quality gravity rollers, catering to a wide array of material handling needs across various sectors. Here’s an overview of the top gravity roller manufacturers and what sets them apart in the competitive landscape.
- Hytrol Conveyor Company, Inc.: Renowned for its comprehensive range of conveyor solutions, Hytrol offers gravity rollers that are known for durability and reliability. Innovation in design and a commitment to quality make Hytrol a go-to for businesses seeking efficient material handling solutions.
- Interroll Group: Interroll is celebrated for its modular conveyor platforms and vast array of roller options. Their focus on energy efficiency and sustainability in product design sets them apart, catering to environmentally conscious businesses.
- Daifuku Co., Ltd.: As a global leader in material handling systems, Daifuku brings innovative automation solutions to the table. Their gravity rollers are part of a broader portfolio that emphasizes customization and integration for complex systems.
- Vanderlande Industries: Vanderlande’s strength lies in its tailored solutions for airport logistics and parcel delivery services. Their gravity rollers are designed for high performance and low maintenance, ensuring smooth operations in critical logistics hubs.
- Dematic Group: Dematic’s extensive research and development efforts have positioned them as pioneers in automated guided vehicle (AGV) technology and smart conveyor systems, including gravity rollers. Their focus on smart logistics and data-driven optimization is their hallmark.
- LEWCO, Inc.: Specializing in industrial ovens and conveyor systems, LEWCO offers a robust selection of gravity rollers that stand out for their heavy-duty performance and customizability, catering to specific industrial applications.
- Titan Conveyors: Titan’s approach to manufacturing gravity rollers involves heavy-duty materials and designs intended for challenging environments. Their products are favored in industries where durability and longevity are paramount.
- Ashland Conveyor Products: Ashland Conveyor stands out for its customer-centric approach, offering an extensive catalog of gravity rollers and accessories. Their focus on affordability and support makes them a preferred choice for small to medium-sized businesses.
What sets these manufacturers apart is not just their ability to produce high-quality gravity rollers but also their commitment to innovation, customer service, and the development of solutions that meet the evolving needs of industries. Whether it’s through offering energy-efficient designs, customizable systems, or comprehensive support and maintenance services, these companies lead the way in facilitating efficient and effective material handling solutions. Their dedication to advancing conveyor technology ensures that businesses have access to the best gravity rollers available, tailored to their specific operational requirements.
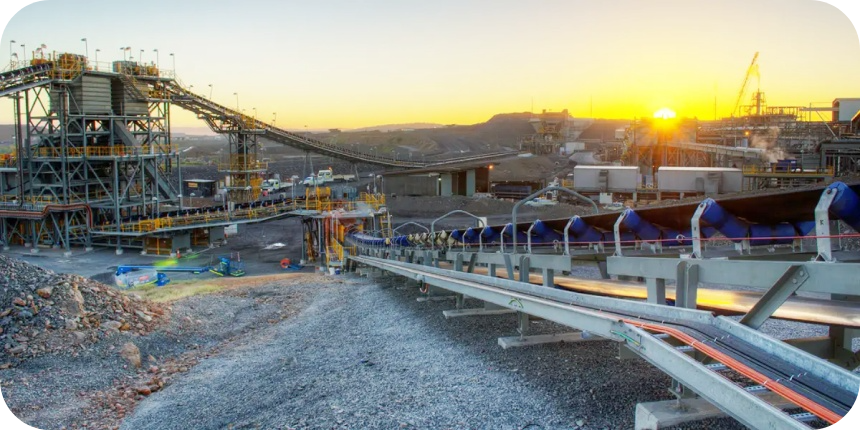
Gravity Rollers Conveyor Price Factors
Investing in gravity roller conveyors is a significant decision for any business, impacting both operational efficiency and financial health. The cost of these systems can vary widely, influenced by a multitude of factors. Understanding these variables is crucial for making an informed purchase that aligns with both your logistical needs and budgetary constraints. Below, we explore the key components that influence the cost of gravity roller conveyors, providing insights into what drives price variations. This knowledge is instrumental in planning and budgeting for your gravity roller conveyor investment effectively.
Components Influencing Cost
The price of gravity roller conveyors is not a fixed figure; it fluctuates based on several critical components. Each of these factors plays a role in determining the final cost:
- Material of Rollers: The construction material of the rollers (steel, aluminum, or plastic) significantly affects the conveyor’s price, with steel typically being the most expensive option due to its durability and load capacity.
- Roller Diameter and Wall Thickness: The size and robustness of the rollers determine their ability to handle various loads, directly impacting the cost. Larger and thicker rollers, capable of supporting heavier weights, command higher prices.
- Frame Material and Construction: The material and design complexity of the conveyor frame also contribute to the cost. Durable, heavy-duty frames are essential for longevity but increase the overall investment.
- Length and Width of the Conveyor: The dimensions of the conveyor directly correlate with the amount of material used in its construction, influencing the price. Larger conveyors require more resources, hence are more costly.
- Customization and Accessories: Any custom features or additional accessories designed to meet specific operational requirements can elevate the price significantly.
- Brand and Quality: Premium brands with a reputation for quality and reliability may offer their products at a higher price point, reflecting the advanced technology and materials used.
- Installation and Delivery: The logistics of delivering and installing the conveyor system can add a considerable amount to the total cost, especially for extensive or complex setups.
Budgeting for Your Gravity Roller Conveyor Investment
Budgeting for a gravity roller conveyor system requires a strategic approach to ensure that the investment is justified and aligns with your business’s operational and financial goals. Here are essential steps to consider:
- Assess Operational Needs: Start by clearly defining the operational requirements of your conveyor system to avoid overspending on unnecessary features.
- Get Multiple Quotes: Soliciting quotes from various suppliers allows you to compare prices and negotiate better deals, ensuring you get the best value for your investment.
- Consider Total Cost of Ownership: Look beyond the initial purchase price to include maintenance, repair costs, and potential operational downtime in your budgeting.
- Allocate a Contingency Fund: Unexpected expenses can arise during the installation or customization process. Having a financial buffer can help manage these costs without derailing the project.
- Explore Financing Options: If the upfront cost is a concern, consider financing options that can spread the expense over a more manageable period.
- Evaluate Used or Refurbished Options: For tighter budgets, consider high-quality used or refurbished conveyors, which can offer significant savings without compromising on functionality.
- Factor in Energy Efficiency: While generally less of a concern for non-powered systems, any powered components or accessories should be evaluated for their energy consumption and impact on operational costs.
- Plan for Future Expansion: Anticipate future growth and choose a system that can be easily expanded or modified to accommodate changing needs, protecting your investment in the long term.
By carefully navigating these price factors and budgeting considerations, businesses can make well-informed decisions when investing in gravity rollers conveyors, ensuring that the chosen system meets their needs efficiently and cost-effectively.
Innovative Uses of Gravity Rollers
Gravity rollers, traditionally seen in the backdrop of manufacturing plants and distribution centers, have transcended their conventional roles to emerge as pivotal elements in a variety of innovative applications. This versatility not only showcases their fundamental utility but also sparks creativity across different sectors. Below, we explore unique applications and systems that leverage gravity rollers, followed by real-world case studies that highlight their adaptability and efficiency in action.
Unique Applications and Systems
The adaptability of gravity rollers has led to their application in unexpected and creative ways, far beyond the confines of industrial environments. These applications demonstrate the ingenuity with which gravity rollers can be integrated into various fields:
- Gravity Roller Toys: Transforming play and learning, gravity roller toys and marble runs offer a hands-on experience with physics principles, captivating the minds of young learners.
- Art Installations: Artists have harnessed the dynamic potential of gravity rollers to create moving sculptures, engaging the public in a dialogue with motion and mechanics.
- Agricultural Sorting Systems: Leveraging gravity rollers for the sorting of agricultural produce has streamlined operations, enhancing efficiency and precision in the packaging process.
- Retail Stock Rooms: The retail sector has seen significant improvements in stock management and accessibility, thanks to gravity rollers facilitating swift movement from storage to storefront.
- Airport Baggage Handling: Gravity rollers play a crucial role in the seamless transport of luggage in airports, ensuring that travelers’ belongings reach their destinations efficiently.
- Theater Stage Sets: The theatrical world benefits from the seamless and quiet operation of gravity rollers, allowing for dynamic set changes that captivate audiences.
- Emergency Evacuation Slides: In safety applications, gravity rollers are employed in innovative evacuation systems, offering a rapid and secure means of exit during emergencies.
- Automated Parking Systems: Addressing urban space constraints, gravity rollers have been integrated into automated parking solutions, optimizing space and reducing vehicle retrieval times.
Case Studies of Gravity Rollers in Action
The following case studies provide a glimpse into the practical and impactful uses of gravity rollers across various domains, showcasing their effectiveness and the innovative spirit of their applications:
- Educational Marble Runs: Schools have adopted gravity roller-based marble runs as educational tools, facilitating an engaging learning experience that introduces students to basic physics and engineering concepts.
- Kinetic Art Exhibitions: An exhibition featuring kinetic sculptures powered by gravity rollers captivated visitors, illustrating the potential of integrating mechanical elements into art for dynamic expressions.
- Fruit Sorting Conveyor: A case study from a fruit farm revealed how the introduction of a gravity roller sorting system significantly boosted productivity and accuracy in fruit sorting, marking a leap in agricultural efficiency.
- Efficient Retail Restocking: A leading retail chain’s implementation of gravity roller aisles in stock rooms exemplifies how these systems can revolutionize inventory management and operational efficiency.
- Airport Luggage System Upgrade: The upgrade of an international airport’s baggage handling system with gravity rollers stands as a testament to their role in enhancing the reliability and flow of luggage handling operations.
- Dynamic Theater Productions: The use of gravity rollers in theater productions for quick and seamless set changes demonstrates their utility in enhancing the visual and narrative flow of performances.
- High-Rise Fire Evacuation: The integration of gravity rollers into a skyscraper’s emergency evacuation system highlights their importance in safety and emergency preparedness, offering a novel solution to high-rise evacuation challenges.
- Space-Saving Automated Parking: An urban development project showcases how gravity rollers can be ingeniously used in automated parking systems to address the challenge of limited parking space, providing a model for future urban infrastructure.
These applications and case studies underscore the broad spectrum of possibilities that gravity rollers offer, from enhancing educational experiences and artistic expressions to solving practical challenges in agriculture, retail, safety, and urban planning. Their simplicity, combined with innovative thinking, continues to open new avenues for their use, proving that even the most straightforward tools can have far-reaching impacts when applied creatively.
Designing a Gravity Roller Conveyor System: Integrating Gravity Rollers for Efficient Material Handling
When planning and designing a gravity roller conveyor system, it’s crucial to follow a systematic approach to ensure optimal functionality and efficiency. Here are seven fundamental steps to consider:
- Assessing Material Requirements: Begin by analyzing the type, size, and weight of materials to be conveyed. Gravity rollers are versatile and can handle various loads, but understanding specific material characteristics is essential for proper design.
- Determining Conveyor Layout: Plan the layout of the conveyor system, considering factors such as available space, workflow, and material flow direction. Gravity rollers allow for flexible configurations, including straight sections, curves, and inclines, to adapt to different facility layouts.
- Selecting Roller Diameter and Spacing: Choose the appropriate roller diameter and spacing based on the size and weight of the materials being transported. Optimal roller spacing ensures smooth movement and prevents jams, maximizing operational efficiency.
- Calculating Conveyor Slope: Calculate the necessary slope for gravity-fed sections of the conveyor to ensure proper material flow without excessive speed or congestion. Balancing slope and roller resistance is critical for controlled transportation of goods.
- Designing Support Structures: Develop robust support structures to maintain stability and alignment along the conveyor route. Gravity roller conveyors typically require minimal support compared to powered systems, but ensuring adequate support at curves and transition points is essential.
- Incorporating Safety Features: Integrate safety features such as guards, emergency stops, and safety sensors to protect workers and prevent accidents. Gravity roller conveyors should comply with relevant safety standards to ensure a secure working environment.
- Testing and Optimization: Conduct thorough testing of the conveyor system to identify any issues and fine-tune performance. Adjust roller spacing, slope angles, and other parameters as needed to optimize efficiency and reliability.
Importance of customization and scalability in conveyor design:
- Adaptability to Diverse Applications: Customization allows conveyor systems to meet specific requirements of different industries and applications. Gravity rollers conveyors can be tailored to handle a wide range of products, from small packages to heavy pallets, enhancing versatility.
- Efficient Space Utilization: Customized conveyor designs optimize space utilization within facilities, maximizing storage capacity and operational efficiency. By tailoring conveyor layouts to fit available space, businesses can streamline material handling processes and minimize wasted floor space.
- Enhanced Ergonomics and Worker Safety: Customized conveyor systems can be designed with ergonomic features to reduce strain on workers and minimize the risk of injuries. Adjustable heights, ergonomic loading stations, and automated controls contribute to a safer and more comfortable working environment.
- Scalability for Future Growth: Scalable conveyor designs accommodate future expansion and changes in production demands. Whether scaling up operations or reconfiguring workflows, modular conveyor systems can be easily modified or extended to meet evolving needs, minimizing downtime and investment costs.
- Optimized Throughput and Productivity: Tailored conveyor solutions optimize throughput and productivity by minimizing bottlenecks, reducing cycle times, and streamlining material flow. By customizing conveyor speed, capacity, and layout, businesses can achieve higher efficiency and meet production targets.
- Integration with Automation Technologies: Customized conveyor systems can be seamlessly integrated with automation technologies such as robotics, sensors, and software controls. This integration enhances efficiency, accuracy, and traceability in material handling processes, driving overall productivity gains.
- Compliance with Industry Standards and Regulations: Customized conveyor designs can be engineered to comply with industry-specific standards and regulations, ensuring regulatory compliance and minimizing risk. By incorporating safety features and design elements tailored to industry requirements, businesses can mitigate compliance-related challenges.
- Improved Customer Satisfaction: Customized conveyor systems enable businesses to meet unique customer requirements with greater precision and reliability. Whether it’s optimizing order fulfillment processes or enhancing product packaging and presentation, customized conveyors contribute to improved customer satisfaction and loyalty.
By prioritizing customization and scalability in conveyor design, businesses can create efficient, adaptable, and future-proof material handling solutions that drive operational excellence and competitive advantage.
FAQs about Gravity Rollers
A gravity roller operates on a simple yet effective principle: gravity. As objects are placed on the rollers of the conveyor, their weight causes them to move along the inclined surface of the conveyor. The rollers are set at a slight decline, allowing items to roll freely from one end to the other without the need for external power sources. When items are loaded onto the conveyor, gravity pulls them downward, initiating their movement along the rollers until they reach the end of the line or are transferred to another conveyor.
Gravity rollers are typically constructed from robust materials such as steel or aluminum. These materials offer the necessary strength and durability to withstand the rigors of various industrial applications. Additionally, some gravity rollers may feature coatings or coverings, such as polyurethane or rubber, to enhance grip and reduce friction. These enhancements ensure smooth and efficient material transport while minimizing wear and tear on both the rollers and the conveyed items.
The angle of a gravity roller conveyor typically falls within the range of 1 to 5 degrees, although this can vary depending on the specific application and requirements. The slight incline of the conveyor facilitates the movement of objects along the conveyor by harnessing the force of gravity. Careful calibration of the angle is essential to ensure optimal material flow while preventing items from rolling too quickly or causing congestion. Adjustments to the angle may be made based on factors such as the weight and size of the conveyed items, as well as the desired speed of transport.
Conveyor rollers come in a variety of types, each designed to suit different applications and environments:
Gravity Rollers: These rollers rely on gravity for movement and are commonly used in manual material handling operations where powered conveyors are not necessary.
Powered Rollers: Powered rollers are driven by motors or other mechanical means to facilitate automated material transport, offering increased efficiency and throughput.
Steel Rollers: Steel rollers are known for their durability and strength, making them suitable for heavy-duty applications and harsh operating conditions.
Plastic Rollers: Plastic rollers are lightweight and corrosion-resistant, making them ideal for applications requiring non-metallic materials or environments where corrosion is a concern.
Tapered Rollers: Tapered rollers feature a conical shape, allowing for smooth transitions between conveyors or different roller sizes, reducing the risk of jams or obstructions.
Grooved Rollers: Grooved rollers have ridges or grooves along their surface, providing enhanced traction and stability for conveyed items, particularly useful in applications where slippage is a concern.
Each type of conveyor roller offers unique features and advantages, allowing businesses to select the most suitable option based on their specific material handling needs and operating conditions.
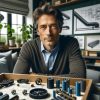
Jordan Smith, a seasoned professional with over 20 years of experience in the conveyor system industry. Jordan’s expertise lies in providing comprehensive solutions for conveyor rollers, belts, and accessories, catering to a wide range of industrial needs. From initial design and configuration to installation and meticulous troubleshooting, Jordan is adept at handling all aspects of conveyor system management. Whether you’re looking to upgrade your production line with efficient conveyor belts, require custom conveyor rollers for specific operations, or need expert advice on selecting the right conveyor accessories for your facility, Jordan is your reliable consultant. For any inquiries or assistance with conveyor system optimization, Jordan is available to share his wealth of knowledge and experience. Feel free to reach out at any time for professional guidance on all matters related to conveyor rollers, belts, and accessories.