The Versatility of Carbon Steel Roller
Carbon steel roller stands as the backbone of numerous industrial processes, embodying a blend of durability, efficiency, and versatility that few materials can match. These rollers, crafted from high-grade carbon steel, are pivotal in manufacturing, agriculture, mining, and beyond, offering unparalleled support in conveyor systems and material handling operations. The significance of carbon steel roller extends beyond their functional utility; they represent a critical investment in the operational efficiency and longevity of industrial machinery. This blog post aims to delve into the myriad benefits and applications of carbon steel roller, shedding light on why they are a preferred choice in various sectors. We will also navigate through the essential considerations one must weigh before selecting these rollers, ensuring that readers are well-equipped with the knowledge to make informed decisions. By exploring the multifaceted advantages and diverse applications, this post seeks to underscore the pivotal role of carbon steel roller in enhancing industrial productivity and innovation.
What Is Carbon Steel Roller
Carbon steel rollers, integral to the functionality of conveyor systems and material handling equipment, are manufactured from carbon steel, a compound known for its robustness and versatility. The composition and construction of carbon steel roller encompass several critical attributes:
- High Carbon Content: The primary distinction of carbon steel is its high carbon content, which imparts the material with superior strength and hardness, making it ideal for the demanding environments of industrial applications.
- Manufacturing Techniques: These rollers are produced through either hot rolling or cold rolling processes. Hot rolling is performed at temperatures above the steel’s recrystallization level, while cold rolling is done at room temperature, affecting the steel’s strength and surface qualities.
- Surface Finishing: Carbon steel rollers may undergo various surface treatments, such as chrome plating or powder coating, to enhance corrosion resistance and extend their operational life.
- Customization Flexibility: They can be customized in terms of size, diameter, wall thickness, and length to meet the specific requirements of different conveyor systems.
- Enhanced Load-Bearing Capacity: The structural integrity of carbon steel allows these rollers to support heavier loads compared to rollers made from other materials, making them suitable for a wide range of industrial tasks.
- Low Maintenance: The durability of carbon steel minimizes the need for frequent maintenance, thereby reducing downtime and operational costs.
- Economic Efficiency: Carbon steel is readily available and easier to process, making rollers manufactured from this material more cost-effective than those made from alternative materials.
- Adaptability: With appropriate surface treatments, carbon steel rollers are capable of withstanding harsh environmental conditions, including exposure to chemicals, moisture, and extreme temperatures.
Comparison with Other Materials
The advantages of carbon steel roller become evident when directly compared with rollers made from rolled steel and cold rolled steel. Below is an expanded comparison to highlight these differences:
- Rolled Steel vs. Carbon Steel: While “rolled steel” is a general term that refers to steel processed through rolling to achieve various shapes and sizes, “carbon steel” specifies the steel’s composition that includes a significant amount of carbon, enhancing its mechanical properties. Carbon steel rollers, therefore, benefit from the inherent strength and durability provided by the higher carbon content, making them more resilient under heavy loads and wear conditions.
- Carbon Steel vs. Cold Rolled Steel: Cold rolled steel is distinguished by its manufacturing process, which involves rolling the steel at room temperature to achieve tighter tolerances and a smoother surface finish. Although cold rolled steel can be used to make rollers, carbon steel rollers manufactured through cold rolling benefit from the combined advantages of the material’s inherent strength and the enhanced surface finish and dimensional accuracy provided by the cold rolling process.
Here’s a detailed comparison table:
Aspect | Carbon Steel Roller | Rolled Steel | Cold Rolled Steel |
---|---|---|---|
Strength and Durability | Exceptionally high due to enhanced carbon content, suitable for heavy-duty applications. | Moderate, depending on the alloy and heat treatment. | High, improved by the cold rolling process, but less than carbon steel in heavy-load applications. |
Surface Finish | Versatile; can be improved to high smoothness through finishing processes. | Typically rougher, requiring additional finishing for smooth applications. | Naturally smooth and polished, ideal for applications where surface finish is critical. |
Cost | Highly cost-effective due to the abundance and ease of processing carbon steel. | Generally lower initial cost but may require additional processing. | Higher due to the cold rolling process, but offers benefits in applications requiring precision. |
Application Suitability | Unmatched in heavy-load and high-wear environments. | Broad, but more suited to structural and less demanding mechanical applications. | Best for precise, high-finish applications, not subjected to extreme loads. |
Wear Resistance | Superior, especially when treated, making it ideal for long-term industrial use. | Variable, highly dependent on the specific steel grade and treatment. | Good for its smooth finish but may not withstand heavy wear as effectively as carbon steel. |
Carbon steel rollers, with their robust construction and adaptable design, stand out as the preferred choice for industrial applications requiring durability, efficiency, and cost-effectiveness. Their ability to be tailored for specific operational needs further enhances their appeal, solidifying their position as a cornerstone in the realm of material handling and conveyor systems.
Advantages of Carbon Steel Roller
The carbon steel roller is a cornerstone in the realm of industrial machinery and conveyor systems, offering a suite of benefits that underscore its indispensability. Here are nine key advantages that highlight the superiority of carbon steel roller:
Durability and Strength: The inherent durability and strength of carbon steel roller are significantly enhanced through carburizing and heat-treating processes. These treatments infuse the outer layer of the steel with additional carbon, creating a hard, wear-resistant surface while maintaining a tough, ductile core. This dual nature ensures that carbon steel rollers can withstand high stress and impact without deformation, extending their operational lifespan even in the most demanding environments.
Efficiency and Cost-Effectiveness: Carbon steel rollers are designed to minimize friction and maximize load-bearing capacity, which translates to lower energy consumption and reduced operational costs. The smooth surface and precise manufacturing of these rollers ensure efficient material handling, reducing the power required to move goods and thus lowering energy bills. Additionally, their long service life and minimal maintenance requirements make them a cost-effective solution over time.
Versatility in Applications: The versatility of carbon steel roller is unmatched, finding utility across a broad spectrum of industries such as manufacturing, agriculture, mining, and more. Their robust construction makes them suitable for heavy-duty applications, from moving raw materials in mining operations to processing goods in manufacturing plants. This adaptability ensures that businesses in various sectors can rely on carbon steel roller for their conveyor needs.
Corrosion Resistance: With appropriate coatings or treatments, such as galvanizing or chrome plating, carbon steel rollers can resist corrosion caused by exposure to moisture, chemicals, and other corrosive elements. This resistance is crucial for applications in harsh environments, ensuring longevity and reliability.
High Load Capacity: Carbon steel’s high strength-to-weight ratio allows rollers made from this material to support heavier loads than those made from other materials. This capability is essential for industries that move large volumes of goods or heavy materials, ensuring that the conveyor system can handle the required capacity without failure.
Low Maintenance: The durability and strength of carbon steel roller result in a product that requires less maintenance. Their ability to resist wear and deformation means that replacements and repairs are less frequent, saving time and money on maintenance operations.
Temperature Tolerance: Carbon steel rollers can operate effectively in a wide range of temperatures, making them suitable for industries with high-temperature processes or those located in extreme climates. This temperature tolerance ensures consistent performance regardless of environmental conditions.
Customization: Carbon steel roller can be customized to meet specific application requirements, including size, shape, and surface treatment. This flexibility allows for optimized conveyor systems that are tailored to the unique needs of each operation.
Environmental Sustainability: Finally, carbon steel is a recyclable material, making carbon steel rollers an environmentally sustainable choice for businesses looking to minimize their ecological footprint. The ability to recycle and repurpose these rollers at the end of their life cycle contributes to a more sustainable industrial practice.
The advantages of carbon steel roller extend from their physical and mechanical properties to their operational efficiency and environmental sustainability. These benefits make them an essential component in a wide array of industrial applications, offering reliability, versatility, and cost-effectiveness that are hard to match.
Find the perfect conveyor roller for your needs. Inquire here!
To Select the Best Carbon Steel Roller
Choosing the right carbon steel roller for your conveyor system is crucial for ensuring efficiency, durability, and cost-effectiveness. Here are key factors and considerations to guide you in selecting the best carbon steel roller for your needs.
Factors to Consider
When embarking on the selection process for the ideal carbon steel roller for your conveyor system, it’s imperative to approach the decision with a comprehensive understanding of the various factors that will influence both performance and longevity. The choice of a carbon steel roller is not merely about finding a component that fits; it’s about ensuring that every aspect of the roller aligns with the specific demands and operational conditions of your system. Here are several critical factors to consider that will guide you in making an informed selection, ensuring that the carbon steel roller you choose not only meets but exceeds your expectations:
- Material Quality: High-quality carbon steel ensures strength and durability. Look for rollers made from certified steel grades known for their performance in industrial applications.
- Bearing Options: Bearings are critical for smooth operation. Consider sealed and lubricated bearings for reduced maintenance, and choose between ball bearings and roller bearings based on load requirements.
- Surface Finish: A smooth finish reduces material wear and noise. Options like galvanizing or coating with polymers can also enhance corrosion resistance.
- Load Capacity: Ensure the roller can handle the maximum load of your application. This depends on both the material quality and the roller design.
- Environmental Resistance: For operations exposed to harsh conditions, consider rollers with additional corrosion protection or temperature resistance.
- Maintenance Requirements: Look for rollers designed for easy maintenance or those that offer low-maintenance solutions through their construction and material choice.
- Operational Speed: The roller’s design should accommodate the operational speed of your conveyor system without compromising efficiency or lifespan.
- Compatibility: Ensure the rollers are compatible with your conveyor system’s design, including frame and track alignment.
- Cost vs. Value: While initial cost is a consideration, focus on the total value offered by the roller, including lifespan, maintenance savings, and operational efficiency.
Customization and Specifications
Selecting the right specifications for carbon steel roller is essential for optimizing your conveyor system’s performance:
- Diameter: Match the roller diameter to the size and weight of the materials being conveyed.
- Wall Thickness: Thicker walls increase strength and load capacity but may require more power to move.
- Shaft Options: Choose the right shaft size and material to ensure durability and compatibility with the conveyor system.
- Length: The roller length should be appropriate for the width of the materials to prevent overhang and ensure balanced support.
- Bearing Type: Select bearings that suit the load and speed requirements of your application.
- Surface Treatment: Consider treatments that enhance wear resistance and reduce maintenance needs.
- Custom Features: Features like grooves or coatings can be customized to suit specific operational needs.
- Quality Assurance: Opt for rollers from manufacturers that offer warranties and quality certifications.
Is Carbon Roller Good?
Evaluating the suitability of carbon steel roller for your conveyor system involves a nuanced understanding of their capabilities and how they align with your operational demands. Carbon steel rollers are not just a component; they are a critical investment in the efficiency and longevity of your material handling processes. Let’s explore their merits and applicability in greater detail, focusing on aspects that distinguish them from other materials without reiterating previously mentioned points.
Enhanced Performance in Diverse Environments
Carbon steel rollers are engineered to excel across a broad spectrum of environments. Their robust construction enables them to operate seamlessly under substantial load capacities, which is crucial for industries that deal with heavy or bulky materials. The resilience of carbon steel to environmental stressors such as impact, abrasion, and fluctuating temperatures ensures that these rollers maintain optimal performance levels, minimizing downtime and enhancing productivity.
Longevity and Maintenance
The longevity of carbon steel rollers is a testament to their construction and material properties. Unlike other materials that may require frequent replacements or are prone to rapid wear, carbon steel offers a durable solution that stands the test of time. This durability translates into lower lifecycle costs, as the need for replacements and the associated downtime are significantly reduced. Moreover, advancements in manufacturing techniques have led to carbon steel rollers that are easier to maintain, further reducing the total cost of ownership.
Customization for Precision Applications
One of the standout features of carbon steel roller is their adaptability to customization. This allows for precision engineering to meet the exact requirements of your conveyor system, ensuring that each roller contributes to the overall efficiency and effectiveness of material handling. Whether it’s specific dimensions, surface treatments, or bearing configurations, carbon steel rollers can be tailored to provide the best fit for your operations, enhancing system performance and reliability.
Economic and Environmental Sustainability
In addition to their operational advantages, carbon steel rollers are also an economically and environmentally sustainable choice. The material’s abundance and recyclability mean that it supports a circular economy, reducing waste and promoting the reuse of resources. This aspect is increasingly important in a global context that prioritizes sustainable practices and environmental stewardship.
Assessing Suitability for Your Operations
The decision to choose carbon steel rollers should be based on a comprehensive assessment of your operational needs, including load requirements, environmental conditions, and maintenance practices. While carbon steel rollers offer numerous advantages, ensuring that they align with the specific demands of your application is crucial for maximizing their benefits.
Carbon steel rollers represent a versatile, durable, and cost-effective solution for a wide range of conveyor system applications. Their ability to perform reliably in diverse conditions, combined with the potential for customization and their contribution to sustainability, makes them a compelling choice for businesses looking to optimize their material handling processes. When evaluating whether carbon steel rollers are a good fit for your operations, consider these unique attributes and how they can enhance the efficiency and longevity of your conveyor system.
Maintenance and Longevity of Carbon Steel Roller
The maintenance and longevity of carbon steel roller are critical aspects that significantly influence the efficiency and cost-effectiveness of conveyor systems. Proper care, routine maintenance, and understanding the lifecycle costs associated with these rollers can greatly extend their service life while ensuring they continue to operate at peak performance. This section delves into essential maintenance tips and a comprehensive analysis of the lifecycle costs, providing a blueprint for maximizing the value of carbon steel roller in industrial applications.
Care and Maintenance Tips
Ensuring the durability and operational efficiency of carbon steel roller requires a proactive approach to maintenance. Here are detailed strategies designed to extend the life of these vital components:
- Regular Inspection: Implement a schedule for periodic inspections to identify and address wear, corrosion, or damage before they escalate.
- Lubrication: Adequate lubrication of bearings and moving parts is essential to minimize friction, one of the primary causes of wear.
- Cleaning: Keeping the rollers clean prevents the accumulation of debris that can lead to imbalance or increased wear over time.
- Alignment Checks: Regularly checking and correcting the alignment of rollers within the conveyor system ensures even distribution of loads and reduces wear.
- Load Monitoring: Adhering to the recommended load capacities prevents overloading, which can lead to premature roller failure.
- Environmental Protection: Use protective coatings and covers to shield the rollers from harmful substances and extreme weather conditions.
- Replacement of Worn Parts: Replacing worn components, such as bearings or seals, in a timely manner maintains the roller’s efficiency and prevents further damage.
- Use of Compatible Materials: Ensure compatibility of all parts and components with the carbon steel rollers to avoid adverse reactions or increased wear.
- Professional Servicing: Engaging professionals for maintenance checks and services guarantees that the rollers are maintained at industry standards.
Lifecycle Costs
Understanding the lifecycle costs of carbon steel rollers is crucial for effective budgeting and operational planning. Here’s an in-depth look at the financial considerations over the lifespan of these rollers:
- Initial Investment: The upfront cost is a consideration, but the long-term benefits of durability and efficiency often outweigh initial expenses.
- Reduced Downtime: Minimizing downtime through regular maintenance not only saves on direct repair costs but also avoids production losses.
- Maintenance Expenses: While ongoing maintenance incurs costs, a well-planned approach can significantly reduce unexpected repair expenses and extend the roller’s service life.
- Energy Efficiency: Efficient operation of well-maintained rollers leads to lower energy consumption, contributing to operational cost savings.
- Replacement Frequency: The extended lifespan of carbon steel roller, thanks to their robust construction, reduces the need for frequent replacements.
- Resale Value: High-quality materials and construction mean carbon steel rollers can retain value, offering potential resale opportunities.
- Recyclability: The ability to recycle carbon steel roller at the end of their life cycle offers an environmentally friendly disposal option and potential cost recovery.
- Total Cost of Ownership: Considering all factors, including maintenance, energy efficiency, and replacement intervals, carbon steel rollers often present a favorable total cost of ownership.
By adhering to the outlined maintenance strategies and understanding the comprehensive lifecycle costs, businesses can ensure their carbon steel rollers remain a valuable and efficient part of their conveyor systems for years to come. This proactive approach not only enhances operational efficiency but also contributes to the overall sustainability of industrial operations.
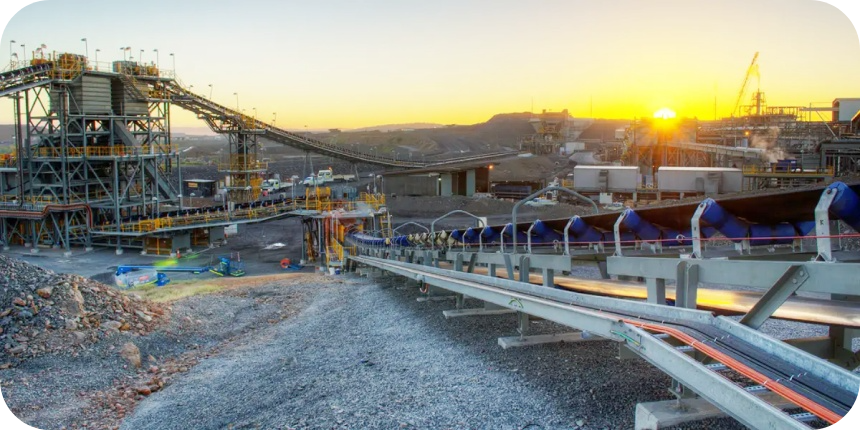
Where to Find the Best Carbon Steel Rollers for Sale
Identifying the right supplier for carbon steel rollers is crucial for ensuring that you receive high-quality components that meet your specific needs. This section provides guidance on choosing a reputable supplier and highlights some of the top-rated carbon steel rollers available in the market.
Choosing a Supplier
When it comes to selecting a supplier for carbon steel rollers, several key factors should be considered to ensure you partner with a company that can meet your requirements effectively:
- Industry Reputation: Look for suppliers with a strong reputation in the industry, evidenced by positive reviews and testimonials from other businesses.
- Quality Assurance: Ensure the supplier adheres to strict quality control standards and offers products that meet or exceed industry specifications.
- Customization Capabilities: Choose a supplier that can provide customized solutions tailored to your specific operational needs.
- Material Sourcing: Investigate the source of their materials to ensure the carbon steel used is of high quality and durability.
- Technical Support: A reputable supplier should offer comprehensive technical support, including assistance with selection, installation, and maintenance.
- Delivery and Lead Times: Consider the supplier’s ability to meet your timeline requirements, including their policies on delivery times and expedited orders.
- After-Sales Service: Look for suppliers that provide excellent after-sales service, including warranty coverage and easy access to replacement parts.
- Cost-Effectiveness: While quality should not be compromised for cost, it’s important to evaluate the overall value offered by the supplier, considering both price and service.
- Sustainability Practices: Prefer suppliers committed to sustainable practices, including the use of recyclable materials and eco-friendly manufacturing processes.
Product Highlights
Several carbon steel rollers stand out in the market for their exceptional quality, durability, and performance. Here are a few top-rated options, along with their key features and benefits:
- High-Load Capacity Rollers: Designed for heavy-duty applications, these rollers can support substantial loads without deformation, ensuring smooth operations in demanding environments.
- Precision Engineered Rollers: Offering tight tolerances and smooth surfaces, these rollers are ideal for applications requiring high precision and minimal vibration.
- Corrosion-Resistant Rollers: With special coatings or treatments, these rollers are protected against corrosion, making them suitable for use in harsh or wet environments.
- Temperature-Resistant Rollers: Capable of operating efficiently in extreme temperatures, these rollers are perfect for industries with high-heat processes.
- Low-Maintenance Rollers: Featuring sealed bearings and durable construction, these rollers require minimal maintenance, reducing operational costs.
- Eco-Friendly Rollers: Made from recyclable materials and manufactured through environmentally friendly processes, these rollers appeal to sustainability-conscious businesses.
- Customizable Rollers: Suppliers offer rollers that can be customized in terms of size, material, and surface treatment to meet specific application requirements.
- High-Speed Rollers: Engineered for high-speed conveyor systems, these rollers ensure efficient material handling with minimal noise and wear.
Finding the best carbon steel roller for sale involves careful consideration of both the supplier’s capabilities and the specific features of the rollers themselves. By focusing on quality, customization options, and customer service, you can select a supplier that will provide rollers to enhance the efficiency and reliability of your conveyor system. Highlighting top-rated products further assists in identifying rollers that offer the best performance and value for your operations.
FAQs about Carbon Steel Roller
Rollers are typically manufactured from two main types of steel: carbon steel and stainless steel. Carbon steel rollers are known for their strength and durability, making them suitable for heavy-duty applications. This type of steel is an alloy that contains varying amounts of carbon, which enhances its hardness and wear resistance. Carbon steel rollers can handle high load capacities and are often used in industries requiring robust material handling solutions.
Stainless steel rollers, on the other hand, are valued for their exceptional corrosion resistance. Made from an alloy that includes iron, carbon, and a minimum of 10.5% chromium, stainless steel forms a protective layer of chromium oxide on the surface that prevents rust and corrosion. This makes stainless steel rollers ideal for use in environments that are moist or where exposure to chemicals is common, such as in the food processing or chemical manufacturing industries. Stainless steel is also chosen for applications where sanitation is crucial, thanks to its easy-to-clean surface that resists bacterial growth.
A stainless steel roller is a component used in conveyor systems and machinery, crafted from stainless steel alloy for its notable corrosion resistance and durability. These rollers are especially beneficial in environments where exposure to moisture, chemicals, or other corrosive elements is frequent. Stainless steel’s resistance to rust and corrosion ensures the longevity and reliability of the rollers, making them a preferred choice for many industrial applications.
Stainless steel rollers are not only durable but also hygienic, with a smooth surface that’s easy to clean and disinfect. This makes them particularly suitable for industries where cleanliness is paramount, such as food and beverage processing, pharmaceuticals, and healthcare. The choice of stainless steel grade (e.g., 304 or 316) can be tailored to the specific needs of the application, with higher grades offering enhanced corrosion resistance. Overall, stainless steel rollers offer a combination of durability, hygiene, and performance, making them an excellent choice for a wide range of conveyor system applications.
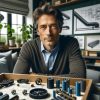
Jordan Smith, a seasoned professional with over 20 years of experience in the conveyor system industry. Jordan’s expertise lies in providing comprehensive solutions for conveyor rollers, belts, and accessories, catering to a wide range of industrial needs. From initial design and configuration to installation and meticulous troubleshooting, Jordan is adept at handling all aspects of conveyor system management. Whether you’re looking to upgrade your production line with efficient conveyor belts, require custom conveyor rollers for specific operations, or need expert advice on selecting the right conveyor accessories for your facility, Jordan is your reliable consultant. For any inquiries or assistance with conveyor system optimization, Jordan is available to share his wealth of knowledge and experience. Feel free to reach out at any time for professional guidance on all matters related to conveyor rollers, belts, and accessories.