Roller Conveyor Design Principles: Applications And Benenfits Guide
In the vast landscape of industrial operations and material handling, roller conveyors emerge as indispensable tools, their presence ubiquitous across a myriad of sectors including manufacturing, logistics, and packaging. These systems, through their simplicity and efficiency, revolutionize the way items are moved within facilities, significantly reducing labor costs and enhancing productivity. The essence of optimizing these benefits lies in the mastery of roller conveyor design, a complex yet fascinating process that encompasses a broad spectrum of considerations from load capacities and material selection to energy efficiency and operational safety. As we delve into the intricacies of conveyor roller design principles, calculations, and applications, our journey will unravel the layers of engineering marvels behind the seamless motion of goods, providing insights into the design choices that dictate their effectiveness and adaptability in various industrial scenarios. This exploration is not merely about understanding a mechanical system; it’s about appreciating the art and science that propel industries forward.
What is Roller Conveyors and Roller Conveyor Design
Definition and Functionality
Roller conveyors are mechanical systems designed to transport materials with ease across a defined path. Central to roller conveyor design is the utilization of cylindrical rollers, which are set in series to form a path. Materials, usually in the form of packaged goods or heavy items, are placed on these rollers. The design allows for movement either through manual force, gravity, or motor power, effectively reducing manual handling and increasing efficiency in material transport. In roller conveyor system design, the focus is on optimizing these systems to serve nine crucial roles in material handling: transporting, sorting, merging, accumulating, orienting, staging, and tracking of goods with precision and speed.
Historical Perspective
The history of roller conveyors dates back to the late 18th century, evolving from simple wooden rollers to sophisticated, powered systems. Initially designed to facilitate movement in mining and bakery operations, the design and application of roller conveyors have expanded significantly. Today, they are integral to numerous industries, symbolizing the advancements in mechanical engineering and efficiency in material handling. This evolution underscores the continuous improvements in roller conveyor design, adapting to the changing needs of industries and technology.
Types of Roller Conveyors
When delving into roller conveyor design, understanding the types available is essential. The design variations cater to different operational needs, including the weight of materials, the required speed of transport, and the level of automation needed. Below is an overview of the primary types:
Type | Description |
---|---|
Gravity Roller Conveyor | Utilizes the force of gravity for movement, ideal for low-power applications and short distances. |
Powered Roller Conveyor | Employs motors to move materials, suitable for heavy loads and long distances. |
Ball Tables | Designed for multi-directional movement, perfect for sorting and orienting processes. |
Chain-Driven Roller Conveyor | Uses chains to drive rollers, ideal for heavy-duty applications requiring robust support. |
24v Powered Conveyor | Features individual motorized rollers, allowing for precise control and flexibility in material handling. |
Each type represents a specific approach in roller conveyor design, tailored to solve distinct challenges in material transport and handling. From gravity conveyors that rely on the natural force of gravity to advanced 24v powered conveyors that offer unparalleled control and efficiency, the choice of system depends on a thorough understanding of the operational requirements and the inherent characteristics of the materials being transported. This diversity in design highlights the adaptability and versatility of roller conveyors, including industrial roller conveyor tables, in facilitating industrial processes, making them a cornerstone in the domain of material handling equipment.
What is Roller Conveyors Design
Roller conveyors are mechanical systems designed to transport materials across a fixed path using cylindrical rollers. The design of roller conveyors involves several key considerations:
Type of Rollers
The rollers can be gravity-powered or motor-driven, and they come in various sizes, materials, and coatings depending on the application and the type of material being handled.
Load Requirements: The design must accommodate the weight, size, and type of items the conveyor will carry. This influences the choice of roller material (such as steel, plastic, or coated rollers), roller diameter, and the spacing between rollers.
Conveyor Layout: This includes the length, width, and curvature of the conveyor system. Roller conveyors can be straight, curved, or flexible, allowing them to fit different spaces and route paths.
Speed and Efficiency: Motorized roller conveyors are designed for varying speeds and can be equipped with sensors and controls to manage the flow of goods, optimizing throughput and reducing bottlenecks.
Durability and Maintenance: The design considers the environment in which the conveyor will operate, such as exposure to chemicals, moisture, or extreme temperatures. Maintenance aspects, like ease of replacing rollers and cleaning the system, are also crucial.
Safety Features: Safety guards, emergency stop buttons, and other safety features are incorporated to protect workers and the materials being conveyed.
Designing an effective roller conveyor system requires a thorough understanding of the operational requirements and constraints to ensure reliability, efficiency, and safety in material handling.
Construction of Roller Conveyor
Constructing a roller conveyor involves several steps, from planning and designing to assembling the various components. This guide outlines the key stages and considerations in the construction of a roller conveyor, ensuring a durable and efficient system.
Key Components of Roller Conveyor Construction
Rollers
- Material: Typically made from steel, stainless steel, or high-density plastic.
- Diameter: Selected based on load requirements, common diameters range from 1 inch to 3 inches.
- Length: Customizable to the width of the conveyor.
- Bearings: Sealed or shielded to reduce maintenance and increase longevity.
Frame
- Material: Usually steel or aluminum for strength and durability.
- Design: Should be robust enough to support the rollers and the load they will carry.
Supports
- Height: Adjustable to ensure the conveyor is level.
- Material: Same as the frame to maintain consistency and strength.
Drive System (for powered conveyors)
- Motor: Adequate horsepower to move the expected load.
- Drive Type: Belt, chain, or direct drive, depending on the application.
- Control System: To regulate the speed and operation of the conveyor.
Miscellaneous Components
- Brackets: To hold the rollers in place.
- Fasteners: Bolts, nuts, and washers for assembly.
- Safety Features: Guards, emergency stops, and safety rails.
How Roller Conveyors Work
Roller conveyors are a common type of industrial conveyor system used to transport materials efficiently and with minimal manual effort. They consist of a series of rollers mounted in a frame that allows items to move along a pathway. Understanding how roller conveyors work involves looking at their components, types, and operational principles.
Operational Principles
Load Placement
- Items are placed on the rollers, either manually or using automated equipment.
- Proper placement ensures even distribution of weight and smooth movement.
Movement
- Gravity or powered systems move items along the conveyor path.
- Rollers rotate, allowing items to glide smoothly from one point to another.
Speed Control
- Powered conveyors use motors and control systems to regulate speed.
- Ensures consistent flow and prevents bottlenecks in the process.
Direction and Path
- Conveyors can be straight, curved, or inclined based on layout requirements.
- Rollers and frames are designed to guide items along the desired path.
Stopping and Accumulating
- Sensors and control mechanisms manage the flow and accumulation of items.
- Accumulation conveyors ensure items are spaced correctly for downstream processes.
Benefits of Roller Conveyors
Efficiency
- Reduces manual handling and speeds up material transport.
- Ideal for high-throughput environments.
Versatility
- Suitable for a wide range of items, from small packages to heavy loads.
- Can be customized to fit various layouts and applications.
Cost-Effective
- Gravity conveyors have low operating costs.
- Powered systems increase productivity, justifying initial investment.
Safety
- Minimizes manual lifting and reduces the risk of injury.
- Can be equipped with safety features such as emergency stops and guards.
Roller conveyors are an essential component in many industrial settings, providing an efficient and reliable method for transporting materials. By understanding the components, types, and operational principles, businesses can select and implement the right conveyor system to enhance their material handling processes.
Design Principles of Roller Conveyors
Basic Design Considerations in Roller Conveyor Design
The foundation of efficient conveyor roller design lies in understanding and applying key design considerations. These factors ensure the conveyor not only meets operational requirements but also operates safely and efficiently. Here are nine critical factors influencing roller conveyor design:
- Load Capacity: The weight and type of materials the conveyor will carry. This determines the strength of the materials used in construction and the design of the rollers.
- Speed Requirements: The speed at which materials need to be moved affects the motor selection and the design of the control system.
- Material of Construction: Depending on the application, different materials such as steel, aluminum, or plastic are chosen for durability, weight, and cost considerations.
- Environmental Conditions: The presence of moisture, chemicals, or temperature extremes can influence material selection and design specifics to ensure longevity.
- Roller Diameter and Spacing: These are designed based on the size and weight of the items to be conveyed, ensuring stability and efficient movement.
- Type of Drive: Whether powered by gravity, a motor, or manually, the choice impacts the overall design, especially in terms of power supply and controls.
- Conveyor Length and Width: Determined by the space available and the size of the items to be transported, affecting the structural integrity and support needed.
- Modularity and Flexibility: Designs often incorporate modular components for easy expansion or reconfiguration to meet changing needs.
- Safety Features: Essential considerations include guards, emergency stops, and other safety features to protect operators and materials.
Roller Conveyor Diagrams
Roller conveyor diagrams serve as essential visual aids that detail the intricate components and layout of a conveyor system. These diagrams not only facilitate understanding of the roller conveyor design but also assist in planning maintenance, troubleshooting issues, and training staff. They typically illustrate the arrangement of rollers, frames, motors, and pathways, providing a blueprint that guides the assembly and integration of the conveyor into existing workflows.
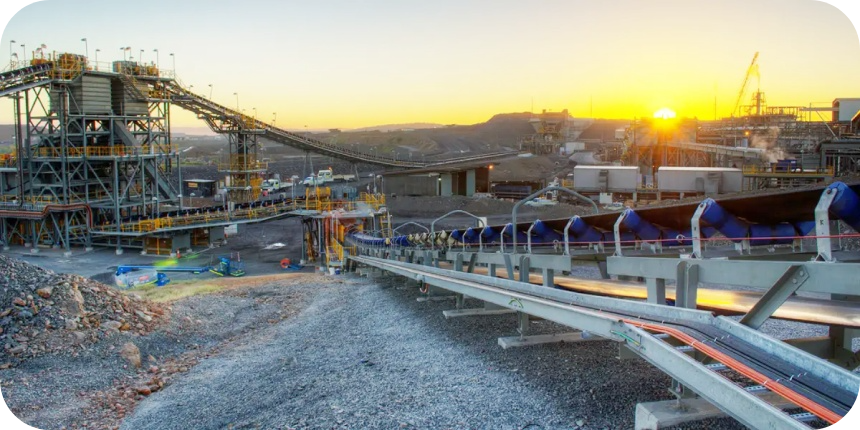
Parts of a Roller Conveyor
The complexity of roller conveyor design is reflected in the diversity of its components, each critical to the system’s overall functionality:
- Rollers: The cylindrical elements that convey materials along the conveyor. They can be made from various materials like steel, aluminum, or plastic, depending on the application.
- Frames: Support the rollers and provide the structure of the conveyor. The design of the frame affects the conveyor’s strength and rigidity.
- Motors: Power the conveyor, with choices ranging from external electric motors to internal 24V DC motors embedded within rollers for a more modular design.
- Bearings: Facilitate smooth roller operations and are selected based on load requirements and environmental conditions. Options include precision and non-precision bearings.
- Controls: Include sensors, switches, and control panels that manage the operation of powered conveyors, allowing for automated or manual control.
Understanding these components and how they come together in roller conveyor design guide system is fundamental to creating efficient and effective material handling solutions. The design process must balance technical specifications with operational needs, ensuring that the final system enhances productivity, safety, and reliability.
HD Roller Conveyor Design
Heavy-duty (HD) roller conveyors are essential components in various industrial applications. They are designed to handle heavy loads and ensure smooth material handling. This guide provides an overview of HD roller conveyor design, highlighting key components, design considerations, and the benefits of using HD roller conveyors in industrial settings.
Key Components of HD Roller Conveyor Design
Rollers
- Material: Typically made from steel or stainless steel for durability and strength.
- Diameter: Larger diameters are used for heavier loads.
- Spacing: Spacing between rollers is crucial for supporting the load and ensuring smooth movement.
Frame
- Material: Constructed from robust materials such as steel or aluminum.
- Design: Must be sturdy to support the weight of the rollers and the load.
Bearings
- Type: Sealed or shielded bearings are preferred for reducing maintenance and prolonging lifespan.
- Load Capacity: Must match the expected load to ensure smooth operation.
Drive System
- Types: Can be gravity-driven, belt-driven, or chain-driven depending on the application.
- Motor: For powered conveyors, motors with adequate horsepower are necessary to handle the load.
Supports and Brackets
- Height Adjustability: Allows for flexibility in installation and alignment.
- Material: Should be robust to provide stability to the conveyor system.
Design Considerations
Load Capacity
- Determine the maximum load per roller and the overall load capacity of the conveyor.
- Consider the weight distribution of the load to ensure even support across rollers.
Conveyor Length and Width
- The length of the conveyor should match the application requirements.
- The width should be sufficient to accommodate the widest load.
Roller Spacing
- Spacing should be close enough to prevent the load from sagging between rollers.
- Typical spacing is around 1/3 to 1/2 the length of the shortest load.
Environmental Factors
- Consider the operating environment (e.g., temperature, humidity, exposure to chemicals) when selecting materials and designing the conveyor.
Safety Features
- Incorporate safety features such as guards, emergency stops, and safety rails to protect operators and equipment.
Benefits of HD Roller Conveyors
Durability and Strength
- Designed to handle heavy loads, ensuring long-term reliability and performance.
Efficiency
- Enhances productivity by enabling smooth and continuous material handling.
Versatility
- Can be customized to fit various industrial applications and load requirements.
Low Maintenance
- With proper design and material selection, HD roller conveyors require minimal maintenance, reducing downtime and operating costs.
HD roller conveyors are vital for efficient and reliable material handling in industrial settings. By understanding the key components and design considerations, manufacturers can create robust conveyor systems that meet their specific needs and enhance operational efficiency.
Roller Conveyor Design Method
Designing a roller conveyor involves a systematic approach to ensure that the conveyor performs efficiently, safely, and reliably under the expected operating conditions. Here’s a detailed method to design a roller conveyor:
Define the Application Requirements:
- Type of material to be conveyed (e.g., boxes, pallets, parts)
- Weight of these items
- Size and shape of the items
- Throughput required (items per hour or day)
- Environment in which the conveyor will operate (temperature, humidity, exposure to chemicals, etc.)
Select the Roller Type:
- Gravity rollers: Suitable for lighter loads and require a slight decline for movement.
- Powered rollers: Use motors to move heavier loads or for controlled speeds; can be chain-driven, belt-driven, or use individual motorized rollers.
Determine Roller Specifications:
- Material: Steel, plastic, or coated (such as rubber or polyurethane).
- Diameter: Larger rollers can carry heavier loads.
- Wall thickness of the roller tubes.
- Bearing type: Decide based on load and environmental conditions.
Layout Design:
- Straight sections, curves, and junctions according to the facility layout.
- Incline/decline sections if needed to utilize gravity rollers.
Calculate the Roller Spacing:
- Ensure that there are enough rollers under each item to distribute the weight evenly.
- The general rule is that the distance between the rollers should be less than the shortest dimension of the load.
Conveyor Frame Design:
- Material: Typically steel or aluminum.
- Strength and rigidity must be sufficient to support the load without significant deflection.
- Height and width to accommodate the load and integrate with other equipment.
Select Drive System (for powered rollers):
- Location of the motor (central or distributed along the conveyor).
- Type of drive mechanism: Direct drive, belt drive, or chain drive.
- Control system: Manual controls, automated sensors, or programmable logic controllers (PLCs).
Safety and Accessibility:
- Safety guards to protect pinch points and moving parts.
- Emergency stops along the length of the conveyor.
- Maintenance access for easy cleaning and repairs.
Testing and Adjustments:
- Test the conveyor with loads to ensure it operates smoothly and meets the design requirements.
- Make adjustments to roller spacing, motor settings, or track alignment as necessary.
Documentation and Training:
- Create detailed operation and maintenance manuals.
- Train staff on proper operation, safety procedures, and troubleshooting.
This methodical approach to roller conveyor design helps in creating a system that is optimized for specific operational needs, ensuring efficient, safe, and reliable material handling.
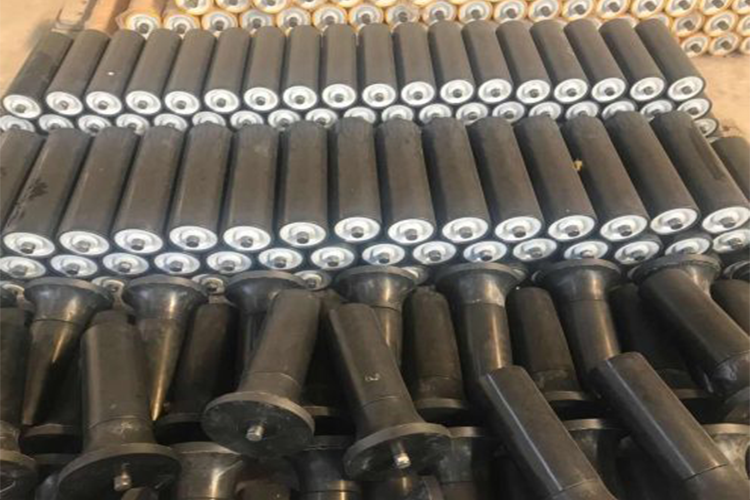
Roller Conveyor Design Calculations
Calculations in Roller Conveyor Design
The cornerstone of effective roller conveyor design is the execution of precise calculations. These calculations ensure the conveyor operates not only efficiently but also safely under varying conditions. Given the diversity in application requirements and operational environments, accurately determining parameters such as load capacity, speed, and power requirements is essential. These calculations are crucial for the customization of the conveyor system to meet specific operational needs, thereby optimizing performance and minimizing potential risks.
Calculations are crucial in roller conveyor design to ensure the system is efficient, effective, and safe. Here are the key calculations involved:
1. Load Calculations
- Maximum Load Capacity: This is calculated based on the strength of the rollers, the roller spacing, and the frame. The load each roller can carry is determined by the roller material and diameter.

- Total Load Capacity: The total load the conveyor can carry is also dependent on the drive system’s power and the structural strength of the frame.
2. Roller Spacing
- Roller Spacing: Ensures that the load is supported by multiple rollers at any given time. Typically, the roller spacing is calculated so that the smallest item on the conveyor is supported by at least three rollers at all times.

3. Speed Calculations
- Conveyor Speed: Important for determining throughput. It is calculated based on the desired rate of movement of items and the available motor speed.

4. Power Requirements
- Motor Power Requirement: Calculated based on the total load, conveyor speed, and friction factors. The required power is higher with increased load and speed, and must overcome friction in the bearings and drive system.

5. Torque Calculations
- Torque Requirement: This calculation is crucial for selecting the motor and drive system. It is the product of the load and the radius of the rollers, adjusted for friction and efficiency.

6. Deflection and Stress
- Beam Deflection: Ensures that the frame and rollers do not flex excessively under load, which could cause misalignment or damage.

- Stress in Rollers: Calculated to ensure that the materials used for rollers and frame can withstand the forces without permanent deformation or failure.

7. Factor of Safety
- Factor of Safety (FOS): Applied to all structural calculations to ensure a margin of safety in design under unexpected loads or conditions.

These calculations are critical for designing a roller conveyor that is both reliable and efficient. Proper application of these principles ensures that the conveyor system will operate smoothly, maintain alignment, and handle the intended loads safely.
Step-by-Step Guide to Design Calculations
Understanding the fundamentals of roller conveyor design calculations is key to engineering a system tailored to application requirements. Here is a step-by-step guide to some of the critical calculations:
- Load Calculation: Determining the maximum load the conveyor will need to handle. This involves considering the weight of individual items and the total load over a section of the conveyor.
- Speed Requirements: Calculating the necessary conveyor speed to meet production demands. This is typically measured in feet per minute (FPM).
- Roller Spacing: Deciding on the appropriate spacing between rollers, which is influenced by the size and shape of the items being conveyed. Proper spacing ensures stability and prevents items from sagging or catching.
- Motor Requirements: Identifying the power needed to drive the conveyor, considering factors such as total load, conveyor length, and operational speed. This also includes selecting the right type of motor and considering energy efficiency.
To aid in these calculations, many resources and calculation tools are available for download. These tools often come in the form of spreadsheets or software applications designed to input operational parameters and receive precise calculations, significantly simplifying the design process.
Gravity Roller Conveyor Design
Designing gravity roller conveyors requires a unique set of considerations, distinct from powered systems. Here are eight specific considerations vital for gravity roller conveyor design:
- Slope: Determining the appropriate slope to ensure items move at the desired speed purely under the influence of gravity.
- Roller Diameter: Selecting a roller diameter that can support the load while minimizing friction and resistance.
- Product Weight: Understanding the weight distribution of products to prevent overloading and ensure smooth movement.
- Friction: Calculating the coefficient of friction between the product and the rollers to ensure efficient movement without manual intervention.
- Stop Points: Integrating manual or automated stop points to control the flow of goods along the conveyor.
- Load Type: Considering the type and variability of loads to design a versatile system.
- Material Handling: Ensuring that the materials of construction can withstand the wear and environmental conditions of the application.
- Safety Measures: Implementing necessary safety features to protect operators and products during operation.
Gravity roller conveyor design emphasizes the physical properties and dynamics of the materials being handled. By meticulously considering these factors, designers can create efficient, low-maintenance systems that leverage gravity to minimize energy use and operational costs. This approach to roller conveyor system design calculations exemplifies the blend of theoretical principles and practical application that defines successful conveyor system design.
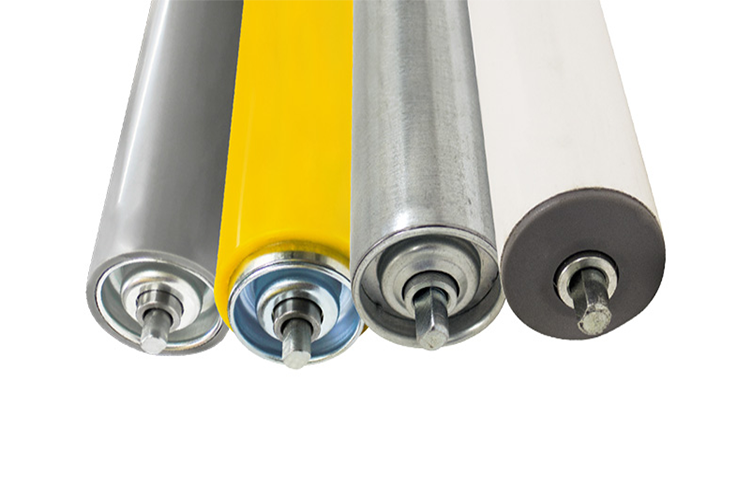
Advanced Design Topics in Roller Conveyor Design
Exploring the depth of roller conveyor design, this chapter delves into the advanced considerations that elevate a conveyor system from functional to exceptional. These considerations encompass material selection, energy efficiency, and adherence to safety standards, each critical for designing a system that not only meets but exceeds operational and environmental expectations.
Material and Roller Selection
Material and roller selection lies at the heart of advanced roller conveyor design, where the right choices can significantly enhance performance, durability, and cost-effectiveness. Here are nine criteria for choosing the appropriate roller materials:
- Load Capacity: The material’s ability to withstand the weight of items without deforming or failing.
- Environmental Resistance: Suitability of the material against conditions like moisture, chemicals, and temperature extremes.
- Friction Requirements: Selection based on the desired level of friction between the rollers and the conveyed items.
- Wear Resistance: The material’s ability to resist abrasion and maintain integrity over time.
- Impact Resistance: Capability to absorb shocks and impacts without damage.
- Cost-Effectiveness: Balancing material benefits with cost to ensure a viable economic solution.
- Maintenance Needs: Materials that require less maintenance offer long-term savings and reliability.
- Compliance with Regulations: Ensuring materials meet applicable standards and regulations.
- Sustainability: Preference for materials that are recyclable or from sustainable sources, reflecting environmental responsibility.
Steel, plastic, nylon, and rubber-coated rollers each offer unique benefits tailored to specific applications, from heavy-duty load bearing to noise reduction and shock absorption.
Energy Efficiency and Sustainability
In contemporary roller conveyor design, energy efficiency and sustainability are paramount. Designers aim to minimize power consumption while maximizing operational efficiency, reducing the environmental footprint of material handling operations. Key strategies include:
- Utilizing Low-Energy Motors: Opting for motors that consume less power without compromising performance.
- Implementing Smart Systems: Advanced control systems that optimize energy use by adjusting speeds and operational modes based on real-time demand.
- Material Recycling: Choosing materials that are recyclable at the end of their lifecycle to minimize waste.
- Lifecycle Analysis: Considering the entire lifecycle of the conveyor system to assess and minimize its environmental impact from manufacturing through disposal.
Safety and Compliance
Ensuring roller conveyor designs meet industry standards and safety regulations is not just a legal obligation but a moral one, safeguarding the well-being of operators and maintenance personnel. Advanced design topics in safety and compliance include:
- Incorporating Safety Guards: Protecting users from moving parts and reducing the risk of accidents.
- Emergency Stop Mechanisms: Easily accessible emergency stops to quickly halt the conveyor in case of danger.
- Regular Compliance Reviews: Staying updated with changes in regulations and standards to ensure ongoing compliance.
- Ergonomic Design: Considering operator interaction with the conveyor system to minimize strain and enhance usability.
By addressing these advanced topics in roller conveyor design, engineers and designers can create systems that are not only efficient and reliable but also sustainable and safe, reflecting the evolving demands of the modern industrial landscape.
Construction Steps of Roller Conveyor
1. Planning and Design
Requirements Assessment
- Load Capacity: Determine the maximum weight the conveyor needs to handle.
- Dimensions: Specify the length, width, and height of the conveyor.
- Path: Plan the conveyor path, including straight sections, curves, and inclines if needed.
- Environment: Consider environmental factors such as temperature, humidity, and exposure to chemicals.
Layout Design
- Frame Design: Design the frame structure to support the rollers and load.
- Roller Spacing: Calculate the appropriate spacing between rollers to support the load effectively.
- Support Placement: Determine the placement and height of supports to ensure stability.
Material Selection
- Rollers: Choose materials (e.g., steel, stainless steel, or high-density plastic) and dimensions based on the load.
- Frame and Supports: Select robust materials such as steel or aluminum.
- Bearings: Opt for sealed or shielded bearings to reduce maintenance.
2. Frame Construction
Cutting
- Cut the frame components to the required dimensions using appropriate tools.
Assembly
- Assemble the frame using brackets and fasteners.
- Ensure the frame is level and stable.
3. Roller Installation
Preparation
- Insert bearings into rollers if not pre-installed.
Mounting
- Place rollers onto the frame, securing them with brackets or axles.
- Ensure proper spacing between rollers to support the load effectively.
4. Drive System Installation (if applicable)
Motor Mounting
- Secure the motor to the frame.
Drive Connection
- Connect the drive system (belt, chain, or direct drive) to the rollers.
Control System
- Install and configure the control system for operation.
5. Supports Installation
Placement
- Position the supports along the length of the conveyor.
Height Adjustment
- Adjust the height of the supports to ensure the conveyor is level.
Securing
- Fasten the supports to the frame.
6. Safety Features Installation
Guards
- Install guards around moving parts to prevent accidents.
Emergency Stops
- Position emergency stop buttons along the conveyor.
Safety Rails
- Add safety rails where necessary to protect operators.
7. Testing and Adjustment
Initial Testing
- Run the conveyor empty to check for smooth operation and identify any alignment issues.
- Test with a light load to ensure rollers and drive systems function correctly.
Adjustments
- Make necessary adjustments to roller spacing, support height, and drive system tension.
- Ensure all fasteners are tightened securely.
Load Testing
- Gradually increase the load to the maximum expected capacity to test the conveyor’s performance.
- Monitor for any signs of strain or failure in the components.
8. Maintenance and Inspection
Regular Inspection
- Check rollers, bearings, and drive systems for wear and tear.
- Ensure the frame and supports remain secure and stable.
Maintenance
- Lubricate bearings and drive components as needed.
- Replace any worn or damaged parts promptly to prevent breakdowns.
Constructing a roller conveyor involves detailed planning, precise assembly, and thorough testing. By following these steps and considering key components and design factors, you can build a reliable roller conveyor that meets industrial needs and enhances operational efficiency.
Applications and Case Studies in Roller Conveyor Design
The versatility of roller conveyors allows them to be a pivotal part of various industrial operations, enhancing efficiency and productivity. This chapter explores the broad range of applications for roller conveyors across different sectors and delves into real-world case studies that highlight the innovative solutions roller conveyor design can provide.
Industrial Applications
Roller conveyors are instrumental in the smooth operation of numerous sectors, each with unique demands and challenges. Here are ten industries that significantly benefit from the integration of roller conveyor systems:
- Manufacturing: Streamlining the assembly line process, from raw material handling to finished product packaging.
- Automotive: Facilitating the movement of parts and assemblies across different stages of vehicle construction.
- Pharmaceuticals: Ensuring precise and gentle handling of sensitive medical products and supplies.
- Food and Beverage: From processing ingredients to packaging finished goods under stringent hygiene standards.
- E-commerce and Retail: Efficiently sorting and dispatching a vast array of products for rapid delivery.
- Warehousing and Distribution: Optimizing storage and retrieval processes to enhance order fulfillment speed.
- Airports: Handling luggage with care while ensuring timely sorting and delivery to the correct flights.
- Agriculture: Moving bulk materials like grains and produce for processing and packaging.
- Recycling Plants: Sorting recyclables efficiently to streamline the recycling process.
- Postal Services: Sorting parcels and letters to expedite shipping and delivery.
Case Studies
Examining real-world examples provides insight into the practical challenges and solutions in roller conveyor design:
- Automotive Parts Manufacturer: Faced with the challenge of safely transporting delicate parts across a sprawling manufacturing facility, a custom roller conveyor system was designed with specialized padding and guardrails, significantly reducing damage during transit.
- E-commerce Giant: To handle the surge in online shopping, an e-commerce warehouse implemented an advanced roller conveyor system. The design incorporated smart sensors and automated sorting mechanisms, doubling the capacity for order processing and reducing errors.
- Pharmaceutical Packaging: A pharmaceutical company needed a solution for handling fragile vials. The roller conveyor design included soft-touch rollers and precise speed control, ensuring the safe transport of vials through the packaging line without compromising efficiency.
- Airport Luggage Handling System: An airport faced frequent breakdowns with its old conveyor system, leading to luggage delays. The new design utilized heavy-duty steel rollers and a more reliable motor system, improving durability and reducing maintenance downtime, thereby enhancing traveler satisfaction.
These case studies underscore the importance of custom roller conveyor design in addressing specific operational challenges. Through innovative design and engineering, roller conveyors can significantly improve productivity, safety, and efficiency across a wide range of industries, showcasing their adaptability and essential role in modern industrial operations.
Selecting a Conveyor Roller Manufacturer for Optimal Roller Conveyor Design
When it comes to implementing a roller design for conveyor, selecting the right manufacturer is as crucial as the design itself. The manufacturer’s capability to produce high-quality components that meet specific requirements can greatly influence the efficiency, durability, and overall success of the conveyor system. Here are seven key criteria to consider when choosing a conveyor roller manufacturer:
What to Look For
- Quality of Materials and Construction: High-quality materials are essential for the longevity and reliability of roller conveyors. Look for manufacturers with a reputation for using premium-grade materials and robust construction practices.
- Customization Capabilities: Every industrial application has its unique challenges and requirements. A manufacturer that can offer customized solutions will be able to meet specific operational needs more effectively.
- Technical Support and Service: Post-installation support is critical for maintaining the performance of your conveyor system. Choose a manufacturer that provides comprehensive technical support and service.
- Innovative Design Solutions: Manufacturers at the forefront of roller design for conveyor are more likely to offer innovative solutions that can enhance efficiency and productivity.
- Compliance with Standards: Ensure the manufacturer adheres to industry standards and regulations, which is indicative of their commitment to safety and quality.
- Proven Track Record: Look for manufacturers with a proven track record of delivering successful projects, particularly in your industry or for applications similar to yours.
- Cost-Effectiveness: While quality should not be compromised for cost, it’s important to select a manufacturer who offers competitive pricing without sacrificing the integrity of the roller conveyor design.
List of Leading Manufacturers
Several manufacturers have established themselves as leaders in the field of conveyor roller manufacturing, renowned for their innovation, quality, and service. While this is not an exhaustive list, it highlights some of the most reputable names in the industry:
Gram Conveyor
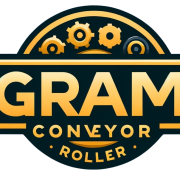
As one of China’s leading conveyor producers and distributors, here at Gram, we pride ourselves on delivering superior quality. We understand the challenges and risks associated with manual lifting, carrying, and storage, which is why we’ve developed industrial conveyor systems designed to eliminate these issues. Our systems not only prevent workplace injuries but also significantly boost productivity. They enhance the efficiency of loading and unloading processes, reducing the risks of accidental damage. Our range of offerings is vast, designed to meet both large-scale and small-scale needs. We offer a wide variety of roller sizes compatible with most popular conveyor brands, and we’re more than willing to customize rollers to meet your specific requirements. At our core, we’re dedicated to the manufacturing and supply of high-quality components for belt conveyor systems, always aiming to align with our customers’ diverse needs.
Products we offer:
- Heavy Duty Roller Conveyor
- Nylon Conveyor Rollers
- Impact Roller
- Ceramic Conveyor Rollers
- Carrying Garland
- Polymer Rollers
- Silent Roller Conveyor
- Guide Rollers
- Steel Roller
- Conveyor Roller Cleaner
Interroll
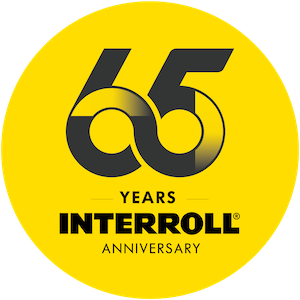
Known for their wide range of rollers and innovative drive solutions, Interroll caters to various industries with high-quality products and systems.
Hytrol
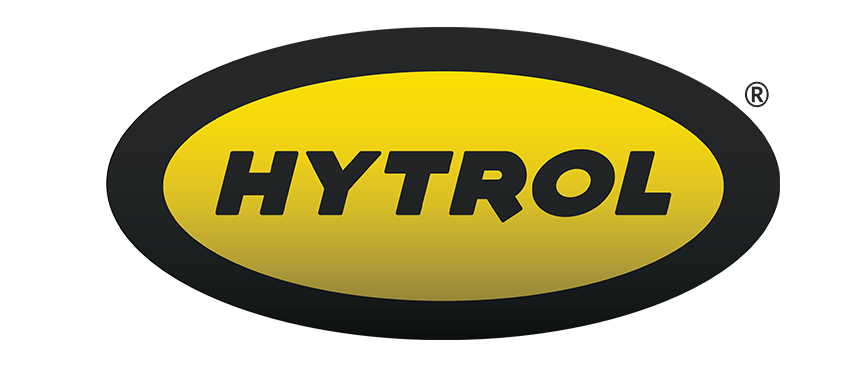
A leading manufacturer of advanced conveyor systems, Hytrol offers a comprehensive line of conveyor solutions, including custom-designed roller conveyors.
Conveyors & Drives, Inc.
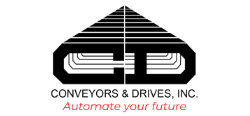
Specializes in conveyor rollers, offering a broad spectrum of solutions tailored to meet specific application requirements.
Rexnord

With a focus on durability and reliability, Rexnord provides a variety of conveyor components, including roller conveyors designed for heavy-duty applications.
Precision Pulley & Idler (PPI)
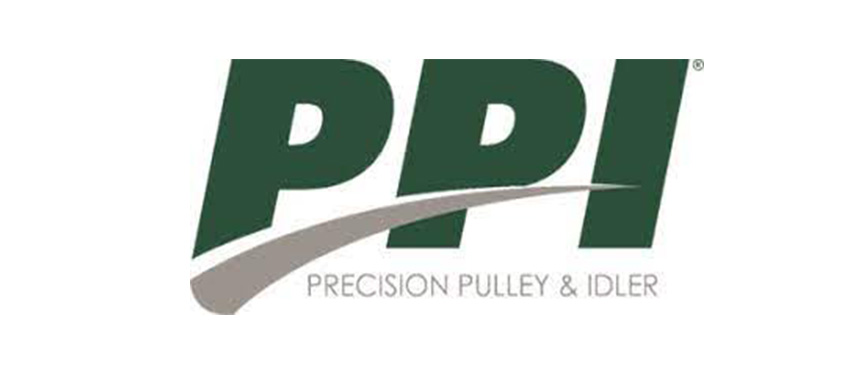
PPI is known for their high-quality conveyor components, including PPI conveyor idlers and rollers that meet rigorous performance standards.
Selecting the right conveyor roller manufacturer is a critical step in the successful implementation of a roller conveyor design. By focusing on these criteria and considering the leading manufacturers in the industry, businesses can ensure they choose a partner capable of delivering a conveyor system that meets their specific needs and operational challenges.
Choose our conveyor rollers for superior strength and longevity. Contact us now!
FAQs about Roller Conveyor Design
The formula for designing a conveyor roller system varies depending on the specific requirements of the material handling process, but it generally involves calculations related to the load capacity, speed of the conveyor, roller diameter, and spacing between rollers. One basic formula used in the design of a conveyor system is the calculation of the conveyor’s speed, which can be represented as: (Speed (m/s) = \frac{Roller diameter (m) \times RPM}{60}). Another important calculation is determining the load capacity of a roller, which depends on the roller material, diameter, wall thickness, and bearing type. Calculating the center-to-center spacing of rollers is also crucial to prevent sagging of materials between rollers. This spacing is often determined based on the length of the material being conveyed and the type of material. For precise design and calculations, it’s recommended to consult with a conveyor roller manufacturer or use specialized software tools that take into account the myriad factors influencing conveyor roller design.
Roller conveyors work by utilizing a series of cylindrical rollers mounted parallel to each other to form a conveyor belt or track. These rollers can rotate freely, allowing objects placed on them to glide over the surface with minimal friction. The movement of items can be powered by gravity (in the case of slightly inclined conveyors), manual effort, or motorized rollers. In gravity roller conveyors, items move due to the force of gravity acting upon them, which necessitates a slight decline along the conveyor’s path. For powered roller conveyors, either individual rollers are motorized or a motor drives the conveyor belt that moves the rollers, thus propelling objects along the conveyor’s length. This design is highly efficient for moving goods across a facility, sorting items, and assembling products, offering flexibility and adaptability to various operational needs.
There are several types of conveyor rollers, designed to cater to various applications and operational requirements:
Gravity Rollers: These rely on gravity to move items and are best suited for lightweight applications or when items are manually pushed along the conveyor.
Powered Rollers: These rollers are motorized and can move items along the conveyor without manual effort or gravity, ideal for heavy loads and automated systems.
Grooved Rollers: Specifically designed to handle belts within the conveyor setup, grooved rollers are used in belt conveyor systems.
Tapered Rollers: Used primarily on curves or bends in the conveyor system to maintain the orientation and alignment of the items being transported.
Impact Rollers: Installed at loading points, impact rollers are designed to absorb the shock and impact of heavy materials being dropped onto the conveyor belt.
Plastic Rollers: Made from durable plastics, these rollers are suitable for lightweight applications and environments where corrosion resistance is necessary.
Each type has its unique advantages and is selected based on the specific needs of the material handling process, including load weight, environmental conditions, and conveyor design.
The structure of a roller conveyor typically includes several key components:
Rollers: The cylindrical elements that actually convey items along the conveyor. They can be made from various materials such as metal, plastic, or rubber.
Frame: Supports the rollers and provides the overall structure of the conveyor. Frames are typically made of steel or aluminum for durability.
Drive Mechanism: In powered roller conveyors, a motor and gearbox are used to drive the rollers, either directly or via belts, chains, or sprockets.
Bearings: Installed at the ends of each roller, allowing them to rotate freely with minimal friction.
Support Legs: These provide stability and height adjustment to the conveyor, ensuring it operates at the optimal level for loading and unloading.
Control System: For automated or motorized systems, a control system is used to regulate the speed and direction of the conveyor.
This structure can be customized with additional components such as side guards, end stops, and transfer plates, depending on the specific application and operational needs. The design and complexity of a roller conveyor’s structure will vary based on its intended use, from simple manual conveyors to complex automated material handling systems.
To make a conveyor roller, start by selecting the appropriate materials, typically steel, stainless steel, or plastic, depending on the application. Measure and cut the roller tube to the desired length, ensuring precision for proper alignment. Next, fabricate the shaft that fits inside the tube, slightly shorter to accommodate end caps and bearings. Install suitable bearings, such as ball bearings, which are robust enough for the expected load. Attach end caps to the roller tube, either by press-fitting, welding, or using fasteners, ensuring the bearings are properly seated. Finally, assemble the roller by inserting the shaft through the bearings in the end caps. Make sure the roller spins freely and has minimal lateral movement. Apply any necessary finishes, like paint or coatings, for protection against wear and environmental factors, and conduct a final inspection to ensure everything is balanced and operates smoothly.
Designing a conveyor involves several key steps. Begin by thoroughly understanding the application, including the type of material to be conveyed, the volume, required speed, and environmental conditions. Choose the type of conveyor best suited for the material, such as belt, roller, chain, or slat. Calculate essential specifications like load capacity, speed, and power requirements. Plan the layout of the conveyor system, considering the necessary paths (straight, curved, inclines, declines) and how it fits within the existing operations. Select materials and components that ensure durability and meet operational demands; this includes choosing the right motor, belts, and rollers. Design the supporting structure to handle the load without significant deflection, and ensure that all components are easily accessible for maintenance. Incorporate safety features like guards, emergency stops, and clear signage. Prototype a section of the conveyor, test it under expected conditions, and adjust as necessary. Finally, provide comprehensive documentation and training for operators and maintenance personnel, covering all aspects of operation and safety.
Last Updated on June 21, 2024 by Jordan Smith
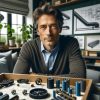
Jordan Smith, a seasoned professional with over 20 years of experience in the conveyor system industry. Jordan’s expertise lies in providing comprehensive solutions for conveyor rollers, belts, and accessories, catering to a wide range of industrial needs. From initial design and configuration to installation and meticulous troubleshooting, Jordan is adept at handling all aspects of conveyor system management. Whether you’re looking to upgrade your production line with efficient conveyor belts, require custom conveyor rollers for specific operations, or need expert advice on selecting the right conveyor accessories for your facility, Jordan is your reliable consultant. For any inquiries or assistance with conveyor system optimization, Jordan is available to share his wealth of knowledge and experience. Feel free to reach out at any time for professional guidance on all matters related to conveyor rollers, belts, and accessories.