Conveyor Scrapers And Belt Scrapers:Conveyor Belt Cleaner
Conveyor scrapers are essential components in maintaining clean and efficient conveyor systems across various industries. These devices play a crucial role in removing residual material from conveyor belts, ensuring smooth operations and reducing downtime. The primary functions of conveyor scrapers include preventing material buildup, which can lead to belt damage and increased maintenance costs. By effectively cleaning the belts, conveyor scrapers enhance operational efficiency and extend the lifespan of the conveyor systems. Their importance is particularly notable in industries such as mining, manufacturing, and food processing, where maintaining clean belts is critical for both productivity and safety. Implementing conveyor scrapers can lead to significant cost savings and improved system performance, making them indispensable for modern conveyor operations.
What Are Conveyor Scrapers
A scraper bar conveyor is a specialized type of conveyor system equipped with conveyor scrapers to enhance its cleaning efficiency. These systems are designed to remove residual material from the surface of conveyor belts, ensuring smooth and uninterrupted operation. The design of a scraper bar conveyor typically includes a series of scraper bars positioned strategically along the conveyor belt. These bars are equipped with conveyor scrapers, which are blades made from durable materials such as polyurethane or carbide. The scrapers are tensioned against the belt, allowing them to effectively remove debris, fines, and other materials that may adhere to the belt surface.
Conveyor scrapers, also known as belt cleaners, are devices used in conveyor systems to remove residual material that adheres to the conveyor belt after the bulk material has been discharged. These devices are essential for maintaining the efficiency, safety, and longevity of conveyor systems.
For example, Flexco, a leading manufacturer of conveyor components, produces scraper bar conveyor systems that are designed to handle various materials in industries like mining and manufacturing. Their systems integrate high-performance conveyor scrapers that can be adjusted for different belt conditions and material types, ensuring optimal cleaning performance.
Conveyor scrapers are essential components in conveyor systems, crucial for maintaining operational efficiency, reducing maintenance costs, and ensuring safety. They play a significant role in cleaning the conveyor belt, preventing material buildup, and protecting the conveyor system from wear and damage. Investing in high-quality scrapers and ensuring their proper maintenance can lead to significant long-term benefits for any conveyor system.
Benefits of Conveyor Scrapers
Conveyor scrapers, also known as belt cleaners, offer several key benefits that enhance the overall performance and longevity of conveyor systems. Here are the primary benefits of using conveyor scrapers:
Enhanced Operational Efficiency
- Consistent Material Flow: By effectively removing residual materials from the conveyor belt, scrapers ensure a smooth and continuous flow of materials, reducing downtime and maintaining production efficiency.
- Optimal Belt Performance: Clean belts operate more efficiently, minimizing interruptions caused by material buildup and improving the overall performance of the conveyor system.
Reduced Maintenance Costs
- Lower Cleaning Requirements: With effective scrapers in place, there is less need for manual cleaning of the conveyor belt, leading to significant savings in labor costs and reducing the frequency of maintenance shutdowns.
- Prolonged Component Lifespan: Scrapers help prevent excessive wear on the conveyor belt and other components by removing abrasive materials, extending their service life and reducing the need for frequent replacements and repairs.
Increased Conveyor Belt Lifespan
- Minimized Wear and Tear: By protecting the belt from abrasive materials, scrapers significantly reduce wear and tear, prolonging the belt’s lifespan and maintaining its integrity.
- Preventing Damage: Scrapers remove sharp or heavy debris that could potentially damage the belt and other conveyor components, ensuring the system remains in good working condition.
Improved Safety
- Reduced Spillage: Scrapers help minimize material spillage, which can create hazardous working conditions. By keeping the belt clean, they contribute to a safer workplace.
- Less Dust Generation: Effective scrapers reduce dust generation, improving air quality and reducing health risks for workers.
Environmental Benefits
- Spillage Control: By minimizing material spillage, scrapers help facilities comply with environmental regulations and standards, contributing to better environmental stewardship.
- Reduced Waste: Cleaner conveyor belts result in less material waste, as more of the conveyed material reaches its intended destination without being lost due to spillage or buildup.
Cost Savings
- Lower Maintenance and Repair Costs: By reducing the frequency and severity of maintenance and repairs, scrapers provide significant cost savings over the lifespan of the conveyor system.
- Extended Equipment Lifespan: Prolonging the life of the conveyor belt and other components through effective cleaning reduces the need for expensive replacements, leading to long-term cost savings.
Optimized Performance
- Consistent Quality: Ensuring the conveyor belt is free from residual material helps maintain consistent quality in material handling processes, enhancing overall product quality and system performance.
- Increased Throughput: With a clean belt, the conveyor system can operate at optimal speeds, increasing throughput and productivity.
Conveyor scrapers are essential for maintaining the efficiency, safety, and longevity of conveyor systems. They provide numerous benefits, including enhanced operational efficiency, reduced maintenance costs, increased belt lifespan, improved safety, environmental compliance, cost savings, and optimized performance. Investing in high-quality scrapers and maintaining them properly can lead to significant long-term benefits for any material handling operation.
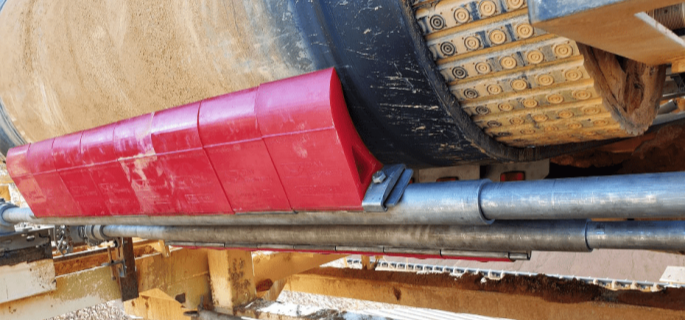
Applications of Conveyor Scrapers
Conveyor scrapers are vital components in various industries where conveyor belts are used to transport materials. Their primary function is to clean the conveyor belt and prevent material buildup, which can lead to inefficiencies, maintenance issues, and safety hazards. Here are some key applications of conveyor scrapers:
Mining Industry
- Coal and Ore Handling: Conveyor scrapers are used to remove coal, ores, and other mined materials from conveyor belts, ensuring smooth operation and preventing blockages.
- Abrasive Materials: Scrapers handle abrasive materials like gravel, sand, and rock, reducing wear and tear on the conveyor belt.
Aggregate and Quarrying
- Sand and Gravel Processing: Scrapers help in removing residual sand, gravel, and other aggregates from the belt, maintaining efficient material flow.
- Crushed Stone: Effective in handling the buildup of crushed stone and ensuring continuous operation.
Cement and Concrete Plants
- Raw Materials Handling: Used to clean conveyor belts that transport raw materials such as limestone, clay, and gypsum.
- Finished Products: Ensure cleanliness of belts transporting finished cement and concrete products.
Power Generation
- Coal-Fired Power Plants: Scrapers are crucial in cleaning belts that transport coal to boilers, preventing material buildup and ensuring consistent fuel supply.
- Ash Handling: Used in the removal of ash from the conveyor systems post-combustion.
Food Processing
- Hygienic Requirements: In food processing, conveyor scrapers are essential for maintaining hygiene by removing food residues and preventing cross-contamination.
- Conveying Packaged Goods: Scrapers help in the transport of packaged goods, ensuring the belts remain clean and operational.
Recycling Plants
- Waste Material Handling: Scrapers are used to clean belts that transport various waste materials, including plastics, metals, and paper, ensuring efficient recycling processes.
- Sorting Lines: Help in maintaining the cleanliness of conveyor belts in sorting lines, improving the accuracy and speed of material separation.
Manufacturing and Assembly Lines
- Automotive: In automotive manufacturing, scrapers keep conveyor belts clean, preventing interruptions in the assembly line.
- Electronics: Used to clean belts that transport electronic components, ensuring precision and preventing damage.
Chemical and Pharmaceutical
- Material Handling: Scrapers are used to clean belts transporting chemicals, powders, and other materials, preventing contamination and ensuring accurate mixing and processing.
- Strict Hygiene Standards: In pharmaceutical applications, scrapers maintain strict hygiene standards by removing residual products from belts.
Agriculture
- Grain and Feed Handling: Scrapers clean belts transporting grains, seeds, and animal feed, preventing contamination and spoilage.
- Fertilizer Distribution: Ensure cleanliness of belts used in the transportation and distribution of fertilizers.
Paper and Pulp Industry
- Pulp Transport: Scrapers are used to clean conveyor belts transporting wet pulp, preventing buildup and ensuring smooth operation.
- Finished Paper Products: Maintain cleanliness of belts used for transporting finished paper products, ensuring quality and efficiency.
Conveyor scrapers are essential across various industries for maintaining the efficiency, safety, and longevity of conveyor systems. They prevent material buildup, reduce wear and tear, improve safety, and ensure smooth operation. By selecting the appropriate type and material of scraper for specific applications, industries can achieve significant operational benefits and cost savings.
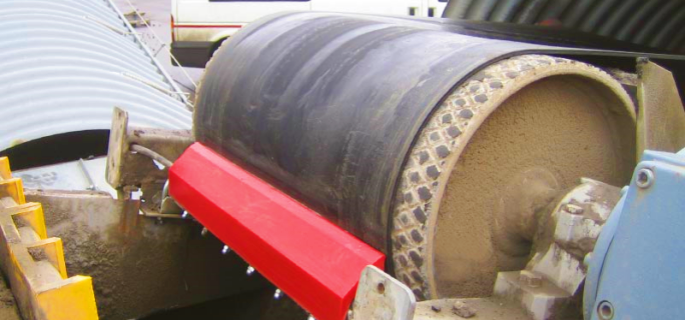
Conveyor Belt Scraper Types in Conveyor Scrapers
Primary Conveyor Belt Scraper
The primary conveyor belt scraper is a critical component of conveyor scrapers, designed for aggressive cleaning action right at the point where material is discharged from the conveyor belt. Positioned at the head pulley, the primary scraper is the first line of defense against material carryback. Its main function is to remove the bulk of the material that sticks to the belt, ensuring that the conveyor system operates efficiently and without interruption.
The design of primary conveyor belt scrapers typically involves durable blades made from materials like polyurethane or carbide. These blades are engineered to withstand the abrasive nature of bulk materials commonly transported in industries such as mining, cement, and aggregate. For example, the Martin Engineering Primary Belt Cleaner is known for its robust construction and high efficiency in removing carryback. It features a heavy-duty blade that can endure the harsh conditions of industrial applications, thereby reducing maintenance needs and prolonging the lifespan of the conveyor belt.
Primary scrapers are also adjustable to maintain optimal tension against the belt, ensuring consistent cleaning performance. This adjustability is crucial for accommodating wear on the scraper blade over time, maintaining effective cleaning without damaging the belt. Companies like Flexco provide primary scrapers with easy-to-adjust tensioning systems that enhance their operational efficiency and longevity.
Secondary Belt Scraper
Secondary belt scrapers are an essential part of conveyor scrapers, positioned further down the conveyor system, typically after the head pulley. Their primary role is to remove any remaining material that was not cleared by the primary scraper. Secondary scrapers are generally designed to be less aggressive than primary scrapers, using lighter blades to ensure thorough cleaning without causing excessive wear to the conveyor belt.
The function of secondary belt scrapers is to provide a finishing touch to the cleaning process, ensuring that the conveyor belt is as clean as possible before it returns to the loading point. For instance, the Flexco Secondary Belt Cleaner is renowned for its precision cleaning capabilities. It employs a variety of blade materials, including polyurethane and carbide, to suit different applications and material types. The use of secondary scrapers is particularly important in environments where even small amounts of carryback can cause significant problems, such as in food processing or chemical manufacturing.
One of the key features of secondary scrapers is their ability to self-adjust to the belt’s surface, ensuring consistent contact and cleaning performance. This self-adjusting mechanism helps maintain effective cleaning throughout the scraper’s lifespan, reducing the need for frequent manual adjustments and maintenance.
Specialty Scrapers
In addition to primary and secondary scrapers, there are various specialty scrapers designed to address specific cleaning challenges and environments. These specialty conveyor scrapers are tailored to meet the unique requirements of particular industries or materials, ensuring optimal cleaning performance in even the most challenging conditions.
For example, the Excalibur Food Grade Scraper by Argonics is specifically designed for the food processing industry. It features a unique blade made from FDA-approved materials, ensuring that it meets stringent hygiene standards while effectively removing residual material from the conveyor belt. This scraper is ideal for applications where contamination must be avoided at all costs, providing a high level of cleanliness and safety.
Another example is the Chevron Belt Cleaner, designed to clean belts with a chevron or ribbed surface. Traditional flat scrapers are often ineffective on these types of belts due to their textured surface. The Chevron Belt Cleaner uses a finger system that conforms to the belt’s contours, providing effective cleaning without damaging the belt. Companies like Flexco offer chevron belt cleaners that can be customized to fit various belt widths and patterns, ensuring versatility and efficiency.
Specialty scrapers also include models designed for high-temperature applications, where standard scrapers may fail due to heat degradation. These high-temperature scrapers are made from materials that can withstand extreme temperatures, ensuring continuous and effective cleaning in environments such as steel mills or foundries.
Conveyor scrapers, including primary, secondary, and specialty scrapers, play an indispensable role in maintaining the cleanliness and efficiency of conveyor systems. By effectively removing residual material from conveyor belts, they help prevent buildup, reduce maintenance costs, and extend the lifespan of the conveyor system. Companies like Martin Engineering, Flexco, and Argonics continue to innovate and provide high-quality scrapers tailored to meet the diverse needs of industries worldwide.
What is the Best Conveyor Scraper Type for Your Conveyor System
Choosing the best conveyor scraper type for your conveyor system depends on several factors, including the material being conveyed, the conveyor system’s operating conditions, and specific requirements for cleaning efficiency and maintenance. Here are the main types of conveyor scrapers and guidance on selecting the best type for your system:
Primary Scrapers
- Best For: Systems where the primary concern is to remove the majority of the conveyed material immediately after discharge.
Secondary Scrapers
- Best For: Systems requiring a higher degree of belt cleanliness, especially where residual material could cause issues downstream.
Tertiary Scrapers
- Best For: Applications demanding extremely clean conveyor belts, such as in food processing or where cross-contamination must be avoided.
V-Plow Scrapers
- Best For: Preventing material buildup on the return side of the belt and protecting the tail pulley.
Rotary Scrapers
- Best For: Applications where continuous or rotating action is beneficial for cleaning, often used in high-volume or abrasive material handling.
Factors to Consider When Choosing a Conveyor Scraper
Material Type:
- Abrasiveness: For abrasive materials, choose scrapers with harder materials like carbide or hardened steel.
- Sticky or Wet Materials: For sticky or wet materials, polyurethane or specialized blade designs that prevent clogging may be more effective.
Belt Speed and Width:
- High-Speed Belts: Require scrapers with robust construction and durable materials to withstand the increased wear and tear.
- Wide Belts: Ensure the scraper can cover the entire width of the belt effectively.
Operating Conditions:
- Temperature: High-temperature applications may require scrapers made of heat-resistant materials.
- Environment: Consider scrapers that are resistant to corrosion if operating in harsh environments.
Cleaning Efficiency:
- Primary vs. Secondary: Determine if a single scraper type will suffice or if a combination of primary and secondary scrapers is needed for thorough cleaning.
Maintenance and Durability:
- Ease of Replacement: Choose scrapers that are easy to maintain and replace to minimize downtime.
- Durability: Ensure the scraper material is durable enough to handle the specific conditions of your conveyor system.
Selecting the best conveyor scraper type involves evaluating the material being conveyed, the operating conditions, and the specific cleaning requirements of your conveyor system. Primary scrapers are suitable for initial cleaning, while secondary and tertiary scrapers provide additional levels of cleanliness. V-plow scrapers are essential for the return side, and rotary scrapers offer continuous cleaning action. By considering these factors and the types of scrapers available, you can choose the most effective scraper type to optimize the performance and longevity of your conveyor system.
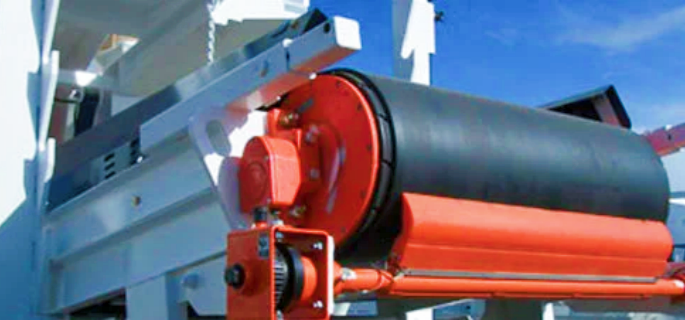
Primary Conveyor Belt Scraper: The First Line of Defense in Conveyor Scrapers
Functionality
Primary conveyor belt scrapers are essential components of conveyor scrapers, serving as the first line of defense in removing bulk material carryback. Positioned at the head pulley of the conveyor system, these scrapers are designed to remove the majority of the material that adheres to the belt after the discharge point. The primary scraper’s aggressive cleaning action ensures that large amounts of carryback are effectively scraped off, preventing material buildup and reducing the risk of belt damage and operational inefficiencies.
The primary function of these scrapers is to tackle the bulk of the material removal. By doing so, they prevent the accumulation of debris on the belt that can lead to various issues such as belt misalignment, increased wear and tear, and potential system failures. For instance, Flexco’s EZP1 Precleaner is specifically engineered to handle heavy-duty cleaning tasks, providing effective removal of large particles and debris that could otherwise compromise the conveyor system’s performance.
Design and Benefits
The design of primary conveyor belt scrapers in conveyor scrapers is characterized by robust construction and high efficiency in initial cleaning. These scrapers typically feature heavy-duty blades made from durable materials such as polyurethane or carbide, chosen for their ability to withstand the abrasive nature of bulk materials. The blades are designed to maintain a precise angle against the conveyor belt, ensuring maximum contact and efficient material removal.
One of the key design aspects of primary scrapers is their adjustable tensioning system. This system allows for consistent pressure to be applied to the scraper blade, maintaining optimal cleaning performance even as the blade wears down over time. Companies like Martin Engineering incorporate advanced tensioning mechanisms in their primary scrapers, ensuring that the blades maintain effective contact with the belt surface throughout their lifespan.
Another significant benefit of primary conveyor belt scrapers is their ability to extend the lifespan of the conveyor belt itself. By removing bulk material carryback, these scrapers reduce the amount of abrasive material that can cause wear and damage to the belt. This leads to fewer repairs and replacements, ultimately lowering maintenance costs and improving the overall durability of the conveyor system. Martin Engineering’s SHD Heavy-Duty Cleaner, for example, is designed to provide maximum cleaning efficiency while minimizing wear on the belt, contributing to longer operational periods and reduced maintenance requirements.
Operational Impact
The impact of primary conveyor belt scrapers on conveyor system efficiency, maintenance, and overall performance is profound. By effectively removing bulk material carryback, these scrapers help maintain a clean belt surface, which is crucial for the smooth operation of the conveyor system. Clean belts run more efficiently, reducing the amount of energy required to move materials and minimizing the risk of belt slippage and misalignment.
In terms of maintenance, primary scrapers significantly reduce the frequency and cost of maintenance activities. By preventing material buildup, they help avoid the common issues associated with carryback, such as increased wear on conveyor components and the need for frequent cleaning and repairs. A study conducted by West River Conveyors demonstrated that the use of high-quality primary scrapers reduced maintenance costs by up to 20%, highlighting their effectiveness in maintaining system reliability and reducing operational expenses.
Furthermore, the presence of primary conveyor belt scrapers enhances the overall performance of the conveyor system. With reduced material carryback, there is less downtime due to cleaning and repairs, allowing for more consistent and efficient operation. This improvement in system performance can lead to increased productivity and throughput, as the conveyor system is able to operate at optimal efficiency with minimal interruptions.
Real-world examples of the benefits of primary conveyor belt scrapers can be seen in various industries. In the mining sector, where conveyors are used to transport heavy and abrasive materials, primary scrapers are essential for maintaining the cleanliness and efficiency of the belts. Flexco’s heavy-duty primary scrapers have been successfully implemented in numerous mining operations, resulting in improved conveyor performance and reduced maintenance costs.
Similarly, in the cement industry, where conveyors are exposed to harsh conditions and abrasive materials, the use of robust primary scrapers is crucial. Martin Engineering’s primary belt cleaners have been deployed in cement plants worldwide, providing reliable and efficient cleaning solutions that enhance system performance and reduce downtime.
Primary conveyor belt scrapers are indispensable components of conveyor scrapers, offering robust design, efficient cleaning, and significant operational benefits. Their role as the first line of defense against material carryback ensures that conveyor systems operate smoothly and efficiently, with reduced maintenance costs and enhanced performance. Companies like Flexco and Martin Engineering continue to innovate and provide high-quality primary scrapers, helping industries maintain clean and efficient conveyor operations.
Secondary Belt Scraper: The Finishing Touch in Conveyor Scrapers
Functionality
Secondary belt scrapers, integral components of conveyor scrapers, play a pivotal role in ensuring the thorough cleaning of conveyor belts. Positioned further down the conveyor line, typically after the head pulley, secondary scrapers are designed to remove any residual material left behind by the primary scraper. This additional cleaning step is crucial for maintaining the efficiency and longevity of conveyor systems, especially in operations where material carryback can cause significant issues.
The primary function of secondary belt scrapers is to provide a finishing touch to the cleaning process. While primary scrapers are designed to handle the bulk of the material removal, they may not always capture all the residuals. Secondary scrapers ensure that even the smallest particles are removed, leaving the conveyor belt as clean as possible. This thorough cleaning process prevents material buildup, which can lead to belt misalignment, increased wear and tear, and potential system failures. For instance, the Flexco R-Type Secondary Belt Cleaner is known for its effectiveness in removing fine materials, ensuring that the belt is free from any remnants that could affect its performance.
Design and Benefits
The design of secondary belt scrapers in conveyor scrapers is specifically tailored to achieve precision cleaning and minimize belt wear. These scrapers typically feature lighter blades compared to primary scrapers, which allows them to gently remove residual materials without causing damage to the conveyor belt. The blades are often made from high-quality materials such as polyurethane or carbide, chosen for their durability and ability to withstand harsh conditions.
One of the key design features of secondary scrapers is their self-adjusting mechanism. This feature ensures that the scraper maintains constant contact with the belt, adapting to changes in belt wear and tension. The self-adjusting mechanism enhances the scraper’s cleaning efficiency and reduces the need for manual adjustments, saving time and maintenance costs. Martin Engineering’s QC1+ Secondary Belt Cleaner is a prime example, offering a robust self-adjusting system that ensures optimal cleaning performance with minimal maintenance.
Another significant benefit of secondary belt scrapers is their contribution to reducing overall maintenance costs. By effectively removing residual material, these scrapers help prevent material buildup that can cause excessive wear on the conveyor belt and other system components. This reduction in wear translates to fewer repairs and replacements, ultimately lowering operational expenses. A case study by West River Conveyors demonstrated that using high-quality secondary scrapers reduced maintenance costs by 15%, highlighting their cost-effectiveness.
Applications
Secondary belt scrapers in conveyor scrapers are particularly effective in a variety of operations and material types. They are essential in industries where even minimal carryback can lead to significant problems, such as mining, food processing, and chemical manufacturing.
In the mining industry, conveyor belts are used to transport large quantities of abrasive materials. The harsh conditions and the nature of the materials make it imperative to have a thorough cleaning process. Secondary scrapers ensure that the belts remain clean, preventing material buildup that could lead to system failures and costly downtime. Companies like Flexco provide robust secondary scrapers designed to handle the demanding conditions of mining operations, ensuring continuous and efficient performance.
In food processing, maintaining hygiene and cleanliness is critical. Conveyor scrapers equipped with secondary scrapers help prevent cross-contamination between different production batches, ensuring that the products meet strict hygiene standards. For example, UniFlex’s food-grade conveyor systems incorporate advanced secondary scrapers made from FDA-approved materials, providing a high level of cleanliness and safety in food processing environments.
The chemical manufacturing industry also benefits from the use of secondary belt scrapers. The precise removal of residual materials is crucial in preventing contamination and ensuring the purity of chemical products. Martin Engineering’s secondary scrapers are widely used in this industry, offering reliable and efficient cleaning solutions that meet the stringent requirements of chemical manufacturing processes.
Secondary belt scrapers, as vital components of conveyor scrapers, provide essential cleaning that enhances the efficiency, safety, and longevity of conveyor systems. Their precise design, self-adjusting mechanisms, and ability to handle various materials make them indispensable in numerous industries. Companies across the globe continue to rely on these scrapers to maintain clean and efficient conveyor operations, underscoring their critical role in modern material handling systems.
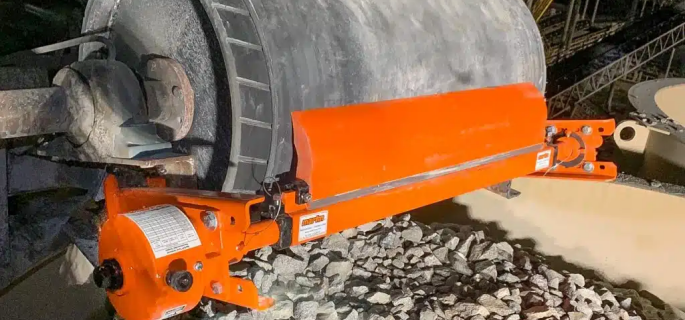
Belt Cleaners: Essential Components of Conveyor Scrapers
Role of Belt Cleaners
Belt cleaners, an integral part of conveyor scrapers, play a crucial role in maintaining the cleanliness and efficiency of conveyor systems. They are designed to remove residual material from conveyor belts, preventing buildup that can lead to operational inefficiencies and increased maintenance costs. Conveyor scrapers, including belt cleaners, are vital in ensuring that conveyor belts operate smoothly and effectively, reducing downtime and prolonging the life of the conveyor system.
For instance, in industries like mining and manufacturing, conveyor belts are subjected to heavy loads and abrasive materials. The presence of residual materials on the belt can cause significant wear and tear, leading to frequent maintenance and replacement. Belt cleaners mitigate this issue by scraping off the residual materials, thereby keeping the belts clean and functional. Companies such as Flexco and Martin Engineering specialize in producing high-quality belt cleaners that are designed to handle the rigorous demands of these industries.
Types of Belt Cleaners
There are various types of belt cleaners used in conveyor scrapers, each designed for specific functions and cleaning needs. The two main categories are primary and secondary belt cleaners.
Primary Belt Cleaners
Primary belt cleaners are positioned at the head pulley of the conveyor system. Their main function is to remove the bulk of the material that adheres to the belt after the discharge point. These cleaners are typically more aggressive, using sturdy blades made from materials like polyurethane or carbide to effectively scrape off the material. For example, Flexco’s EZP1 Precleaner is designed for primary cleaning and is known for its robust construction and high efficiency in removing large amounts of carryback material.
Secondary Belt Cleaners
Secondary belt cleaners are installed further down the conveyor line, typically beyond the head pulley. Their role is to remove any remaining material that was not cleared by the primary cleaner. Secondary cleaners are generally less aggressive and use lighter blades to ensure thorough cleaning without damaging the belt. Martin Engineering’s SQC2 Secondary Cleaner is a popular choice for secondary cleaning, offering precision cleaning and easy maintenance, which enhances the overall efficiency of the conveyor system.
Benefits of Belt Cleaners
The use of belt cleaners in conveyor scrapers provides numerous benefits that significantly enhance the performance and longevity of conveyor systems.
Reduced Material Carryback
One of the primary benefits of using belt cleaners is the substantial reduction in material carryback. Carryback refers to the residual material that remains on the conveyor belt after it has discharged its load. This material can accumulate over time, leading to belt misalignment, increased wear, and potential damage to the conveyor system. By effectively removing carryback, belt cleaners help maintain a clean belt surface, ensuring smooth and efficient operation.
Lower Maintenance Costs
Another significant advantage of using belt cleaners is the reduction in maintenance costs. Clean conveyor belts experience less wear and tear, which translates to fewer repairs and replacements. For example, a study conducted by West River Conveyors showed that the implementation of high-quality belt cleaners reduced maintenance costs by up to 20%, as the belts required less frequent servicing and had a longer operational lifespan.
Improved Conveyor Belt Lifespan
The lifespan of a conveyor belt is directly impacted by the presence of residual material. Accumulated material can cause abrasive wear on the belt surface, leading to premature aging and frequent replacements. Belt cleaners, as part of conveyor scrapers, help extend the lifespan of the belt by maintaining a clean surface, reducing friction, and minimizing wear. This not only enhances the durability of the belt but also ensures consistent performance over time.
Real-World Applications and Examples
The benefits of belt cleaners in conveyor scrapers are evident in various real-world applications. In the mining industry, for example, conveyor belts are used to transport large quantities of ore and other materials. The harsh conditions and abrasive nature of these materials make belt cleaners essential for maintaining the efficiency and reliability of the conveyor systems. Companies like Flexco and Martin Engineering have developed specialized belt cleaners that can withstand the demanding conditions of mining operations, providing effective cleaning and reducing downtime.
Similarly, in the food processing industry, hygiene and cleanliness are of utmost importance. Conveyor scrapers equipped with belt cleaners ensure that food products are not contaminated by residual materials from previous batches. UniFlex, a manufacturer of food-grade conveyor systems, integrates advanced belt cleaners into their designs to meet stringent hygiene standards and ensure product safety.
The role of belt cleaners in conveyor scrapers is indispensable in maintaining the cleanliness, efficiency, and longevity of conveyor systems across various industries. Their ability to effectively remove residual material, reduce maintenance costs, and extend the lifespan of conveyor belts makes them a critical component in modern conveyor operations.
Conveyor Belt Scraper Blades in Conveyor Scrapers
Types of Blades
Conveyor belt scraper blades are critical components of conveyor scrapers, designed to efficiently clean conveyor belts by removing residual material. The types of scraper blades vary based on their material composition, design, and specific applications. The primary materials used for these blades include polyurethane, carbide, and stainless steel, each offering distinct advantages depending on the operating environment.
Polyurethane Blades
Polyurethane blades are widely used in conveyor scrapers due to their flexibility and durability. They are particularly effective in environments where belts need to be protected from excessive wear. Polyurethane blades are resistant to abrasion and chemicals, making them suitable for a variety of industrial applications. For example, Flexco’s U-Type Polyurethane Blade is known for its resilience and long service life, providing effective cleaning without damaging the conveyor belt.
Carbide Blades
Carbide blades are another common type of scraper blade, known for their hardness and abrasion resistance. These blades are ideal for harsh environments where belts are exposed to abrasive materials such as minerals and ores. The robust nature of carbide blades ensures efficient cleaning and a longer lifespan compared to other materials. Martin Engineering’s SHD Heavy-Duty Cleaner utilizes carbide blades to handle the toughest materials, ensuring minimal carryback and extended operational periods.
Stainless Steel Blades
Stainless steel blades are used in conveyor scrapers where hygiene is paramount, such as in the food processing and pharmaceutical industries. These blades offer excellent corrosion resistance and can be easily sanitized, making them ideal for environments that require stringent cleanliness standards. The Excalibur Food Grade Scraper by Argonics features stainless steel blades that comply with FDA regulations, ensuring both effective cleaning and adherence to health standards.
Blade Maintenance
Proper maintenance of conveyor belt scraper blades is essential to ensure optimal performance and longevity. Regular inspection and maintenance routines help identify wear and tear early, preventing more significant issues and maintaining the efficiency of conveyor scrapers.
Inspection and Cleaning
Routine inspection of scraper blades involves checking for wear, damage, and proper alignment. Blades should be cleaned regularly to remove any accumulated material that could hinder their effectiveness. For instance, in heavy industrial applications, it is advisable to inspect the blades at least once a week. Companies like Flexco provide maintenance kits that include tools and guidelines for thorough blade inspection and cleaning.
Replacement Procedures
Replacing worn or damaged scraper blades is a critical aspect of maintenance. Blades should be replaced when they show significant signs of wear, such as reduced cleaning efficiency or visible damage. The replacement process typically involves loosening the tensioning system, removing the old blades, and installing new ones. Martin Engineering’s replacement kits are designed to make this process quick and easy, minimizing downtime and ensuring that the conveyor scrapers remain effective.
Adjustments
Adjustments to the tensioning system are necessary to maintain optimal contact between the scraper blades and the conveyor belt. Over time, as blades wear down, the tension needs to be readjusted to ensure continued effectiveness. Self-adjusting systems, like those found in some of Flexco’s scrapers, can reduce the frequency of manual adjustments, enhancing operational efficiency.
Selection Criteria
Selecting the right scraper blades for conveyor scrapers depends on several factors, including the type of material being transported, the operating environment, and the specific requirements of the conveyor system.
Material Compatibility
The material being transported plays a crucial role in blade selection. For abrasive materials, carbide blades are often preferred due to their durability and resistance to wear. In contrast, for applications where belt protection is a priority, polyurethane blades are a better choice due to their flexibility and gentler impact on the belt.
Environmental Considerations
The operating environment also influences blade selection. In environments with high chemical exposure, such as chemical processing plants, blades made from corrosion-resistant materials like stainless steel or specially formulated polyurethanes are ideal. In food processing industries, where hygiene is critical, FDA-compliant stainless steel blades are necessary to ensure both cleanliness and safety.
Operational Requirements
The specific requirements of the conveyor system, such as belt speed, load, and cleaning efficiency, must also be considered. High-speed conveyors may require blades with greater abrasion resistance, while systems handling sticky or wet materials may benefit from blades designed to prevent clogging and material buildup. For example, Flexco offers a range of blade options tailored to different conveyor speeds and material types, ensuring that each system operates at peak efficiency.
Conveyor belt scraper blades are essential for the effective operation of conveyor scrapers, ensuring clean and efficient conveyor systems. By understanding the types of blades available, maintaining them properly, and selecting the appropriate blades for specific applications, industries can maximize the performance and lifespan of their conveyor systems. Companies like Flexco, Martin Engineering, and Argonics provide a variety of high-quality scraper blades designed to meet the diverse needs of modern conveyor operations.
FAQs about Conveyor Scrapers
A scraper in a conveyor, specifically known as a conveyor scraper, is a device used to clean the conveyor belt and remove any residue or material build-up. Conveyor scrapers are essential components in maintaining the efficiency and longevity of conveyor systems. They are typically positioned at strategic points along the belt to ensure that any debris, dirt, or leftover material is effectively removed, preventing potential damage and ensuring smooth operation. By keeping the belt clean, conveyor scrapers help in reducing wear and tear, minimizing downtime, and enhancing overall productivity.
Belt scrapers are made from a variety of materials, each selected based on the specific needs and conditions of the conveyor system. Common materials used for conveyor scrapers include polyurethane, rubber, and various metals like stainless steel. Polyurethane and rubber are often chosen for their flexibility, durability, and resistance to abrasion, making them ideal for applications where the scraper needs to maintain close contact with the belt without causing damage. Metal scrapers, on the other hand, are used in more demanding environments where higher levels of toughness and heat resistance are required. The choice of material for belt scrapers depends on factors such as the type of material being conveyed, the operating environment, and the desired level of cleaning efficiency.
A primary scraper and a secondary scraper are two types of conveyor scrapers used to clean the conveyor belt at different stages. The primary scraper is installed at the head pulley, where it removes the majority of the material that adheres to the belt. It is the first line of defense against carryback and is designed to tackle larger, more stubborn debris. The secondary scraper is placed further along the return path of the belt and is used to remove any remaining fine particles and residue that the primary scraper might have missed. By working together, the primary and secondary scrapers ensure that the conveyor belt is thoroughly cleaned, reducing the risk of contamination and enhancing the overall efficiency of the conveyor system.
Cleaning a conveyor belt effectively involves several steps to ensure that all debris and residue are removed, maintaining optimal performance and longevity of the system. The use of conveyor scrapers is one of the primary methods. Initially, a primary scraper is positioned at the head pulley to remove large chunks of material. Following this, a secondary scraper is used to clean up finer particles left behind. Regular inspections and maintenance are crucial to ensure that scrapers are in good working condition and properly aligned. Additionally, manual cleaning might be required for thorough cleaning, especially in areas that scrapers cannot reach. This involves using brushes, water, and cleaning agents to remove any remaining residue. By maintaining a clean conveyor belt, you can prevent potential damage, reduce maintenance costs, and ensure a smooth, efficient operation.
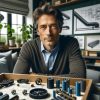
Jordan Smith, a seasoned professional with over 20 years of experience in the conveyor system industry. Jordan’s expertise lies in providing comprehensive solutions for conveyor rollers, belts, and accessories, catering to a wide range of industrial needs. From initial design and configuration to installation and meticulous troubleshooting, Jordan is adept at handling all aspects of conveyor system management. Whether you’re looking to upgrade your production line with efficient conveyor belts, require custom conveyor rollers for specific operations, or need expert advice on selecting the right conveyor accessories for your facility, Jordan is your reliable consultant. For any inquiries or assistance with conveyor system optimization, Jordan is available to share his wealth of knowledge and experience. Feel free to reach out at any time for professional guidance on all matters related to conveyor rollers, belts, and accessories.