Common Materials in Harga Belt Conveyor 4 Ply
Understanding the significance of harga belt conveyor 4 ply is essential for various industries that rely on efficient material handling systems. The harga belt conveyor 4 ply offers robust performance, durability, and cost-effectiveness, making it a popular choice in sectors such as mining, agriculture, and manufacturing. The 4 ply construction ensures added strength and flexibility, catering to heavy-duty applications and harsh working conditions. By investing in harga belt conveyor 4 ply, businesses can enhance their operational efficiency, reduce downtime, and ensure a smoother workflow, ultimately leading to improved productivity and profitability.
Factors Influencing Harga Belt Conveyor 4 Ply
The term harga belt conveyor 4 ply refers to the price of a conveyor belt that is constructed with four layers of synthetic fabric, providing increased strength and durability. Understanding the factors that influence the harga (price) of belt conveyor 4 ply is crucial for businesses looking to invest in high-quality conveyor systems. Several key factors determine the harga of these belts, including material costs, manufacturing processes, specifications, and market demand.
Material Costs
One of the primary factors influencing the harga belt conveyor 4 ply is the cost of raw materials used in its construction. The materials commonly used include high-strength synthetic fabrics such as polyester or nylon, and durable rubber or synthetic compounds for the covers. The quality and grade of these materials significantly impact the overall cost. For instance, higher-quality materials that offer better resistance to wear and tear, higher tensile strength, and improved durability tend to be more expensive.
Manufacturing Processes
The manufacturing processes involved in producing a 4 ply conveyor belt also play a significant role in determining its harga. Advanced manufacturing techniques that ensure precise construction, superior bonding of layers, and consistent quality control can increase production costs. Additionally, processes that involve specialized treatments, such as heat-resistant or chemical-resistant coatings, add to the overall cost of the belt.
Specifications and Customization
The specific technical specifications and customization options for a 4 ply conveyor belt also affect its harga. Factors such as belt width, length, thickness, and the type of cover materials used are all considered in the pricing. Customization options, such as reinforced edges, specific surface textures (smooth, rough top, cleated), and special features like anti-static or flame-resistant properties, further influence the price. The more tailored the belt is to meet specific operational requirements, the higher the harga is likely to be.
Market Demand and Supply
Market demand and supply dynamics significantly impact the harga belt conveyor 4 ply. When there is high demand for conveyor belts in industries such as mining, construction, and material handling, prices tend to rise due to increased competition for available products. Conversely, when supply exceeds demand, prices may decrease. Additionally, global market trends, economic conditions, and trade policies can influence material costs and, consequently, the price of conveyor belts.
Brand and Manufacturer
The brand and reputation of the manufacturer also play a crucial role in determining the harga belt conveyor 4 ply. Established brands with a history of producing high-quality conveyor belts may charge a premium for their products. These manufacturers often invest in research and development, ensuring their belts meet industry standards and offer superior performance. On the other hand, lesser-known brands or new entrants to the market may offer lower prices to attract customers, although the quality may vary.
Additional Costs
Other factors that can influence the harga belt conveyor 4 ply include shipping and handling costs, import/export duties, and installation and maintenance services. For businesses purchasing belts from international manufacturers, transportation costs and customs duties can significantly add to the overall price. Additionally, some suppliers may offer installation and maintenance services, which, while providing added convenience, also contribute to the total cost.
Understanding the various factors that influence the harga belt conveyor 4 ply is essential for businesses looking to make informed purchasing decisions. By considering material costs, manufacturing processes, technical specifications, market dynamics, brand reputation, and additional costs, businesses can select the best conveyor belt that meets their operational needs and budget constraints. Investing in a high-quality 4 ply conveyor belt can lead to improved efficiency, reduced downtime, and long-term cost savings.
Materials Used in Harga Belt Conveyor 4 Ply
The materials used in the construction of a harga belt conveyor 4 ply are crucial in determining its performance, durability, and cost. These materials are selected based on their ability to withstand the operational demands of various industries, including mining, construction, and bulk material handling. Understanding the materials commonly used in manufacturing a 4 ply conveyor belt can help businesses make informed decisions when selecting a belt for their specific needs.
Synthetic Fabrics for Ply Layers
The ply layers in a 4 ply conveyor belt are typically made from high-strength synthetic fabrics such as polyester or nylon. These fabrics provide the necessary tensile strength and flexibility required for heavy-duty applications.
- Polyester: Polyester is a popular choice for conveyor belt ply layers due to its excellent strength-to-weight ratio, resistance to stretching, and durability. Polyester fabrics are also resistant to moisture and chemicals, making them suitable for a wide range of environments.
- Nylon: Nylon is another commonly used material for ply layers. It offers high tensile strength, excellent elasticity, and good abrasion resistance. Nylon fabrics are particularly suitable for applications where the belt needs to navigate tight turns and inclines, as they provide superior flexibility.
Rubber and Synthetic Covers
The top and bottom covers of a 4 ply conveyor belt are made from durable rubber or synthetic compounds. These covers protect the ply layers from external damage and wear, ensuring the belt’s longevity and performance.
- Natural Rubber: Natural rubber is known for its excellent abrasion resistance, flexibility, and durability. It is commonly used in conveyor belts that handle abrasive materials such as rocks and minerals. Natural rubber covers also provide good resistance to impact and mechanical damage.
- Synthetic Rubber: Synthetic rubber compounds, such as nitrile or neoprene, are used for applications that require specific properties like chemical resistance, heat resistance, or oil resistance. These compounds offer similar durability and flexibility to natural rubber but with added benefits tailored to specific operational needs.
- Polyurethane: Polyurethane covers are used for applications requiring superior resistance to abrasion, cuts, and chemicals. Polyurethane is also known for its high load-bearing capacity and excellent flexibility, making it ideal for heavy-duty conveyor belts.
Adhesives and Bonding Agents
The bonding of the ply layers and covers in a 4 ply conveyor belt is achieved using high-quality adhesives and bonding agents. These materials ensure that the layers remain securely bonded, preventing delamination and ensuring the belt’s structural integrity.
- Cold Bonding Adhesives: Cold bonding adhesives are used for splicing and repairing conveyor belts. They provide strong, durable bonds without the need for heat or pressure, making them suitable for on-site repairs.
- Hot Vulcanizing Agents: Hot vulcanizing agents are used in the manufacturing process to bond the ply layers and covers. This method involves applying heat and pressure to create a seamless, strong bond that enhances the belt’s durability and performance.
Special Coatings and Treatments
To meet specific operational requirements, 4 ply conveyor belts may be treated with special coatings and treatments that enhance their properties.
- Heat-Resistant Coatings: Heat-resistant coatings are applied to conveyor belts used in high-temperature environments, such as foundries and steel mills. These coatings protect the belt from thermal degradation and maintain its performance under extreme temperatures.
- Chemical-Resistant Coatings: Chemical-resistant coatings are used for belts that transport materials exposed to corrosive substances. These coatings prevent chemical damage and extend the belt’s lifespan in harsh environments.
- Anti-Static Treatments: Anti-static treatments are applied to conveyor belts used in environments where static electricity could pose a hazard. These treatments reduce the buildup of static electricity, ensuring safe operation.
Environmental Considerations
The selection of materials for a harga belt conveyor 4 ply also considers environmental factors such as sustainability and recyclability. Some manufacturers offer eco-friendly options, such as belts made from recycled materials or those designed to minimize environmental impact.
The materials used in the construction of a harga belt conveyor 4 ply play a critical role in determining its performance, durability, and cost. By understanding the properties and benefits of synthetic fabrics, rubber and synthetic covers, adhesives, and special coatings, businesses can select the best conveyor belt for their specific operational needs. Investing in high-quality materials ensures the belt can withstand the demands of heavy-duty applications, providing long-term reliability and cost savings.
Technical Specifications of Harga Belt Conveyor 4 Ply
The technical specifications of a harga belt conveyor 4 ply provide detailed information on the belt’s construction, performance characteristics, and operational capabilities. Understanding these specifications is essential for selecting the right conveyor belt for specific applications, ensuring it meets the required standards for durability, load capacity, and resistance to environmental factors.
Ply Construction and Thickness
The 4 ply conveyor belt is constructed with four layers of synthetic fabric, providing enhanced strength and durability for heavy-duty applications. The overall thickness of the belt typically ranges from 5/16 inch to 3/4 inch, depending on the manufacturer and specific application requirements.
- Top Cover: The top cover thickness can vary from 1/8 inch to 1/4 inch, designed to withstand abrasion and impact from transported materials.
- Intermediate Ply Layers: Each intermediate layer typically adds around 1/16 inch to 1/8 inch to the total thickness, providing additional strength and durability.
- Bottom Cover: The bottom cover thickness is generally similar to the top cover, ranging from 1/8 inch to 1/4 inch, providing support and reducing wear on the conveyor system components.
Tensile Strength
The tensile strength of a 4 ply conveyor belt indicates its ability to withstand pulling forces without breaking. This specification is typically measured in pounds per inch width (PIW) or newtons per millimeter (N/mm). A 4 ply conveyor belt generally has a tensile strength of 440-660 PIW, ensuring it can handle substantial loads without stretching or deforming. This high tensile strength makes it ideal for heavy-duty applications where robust performance is required.
Elongation at Break
Elongation at break measures the belt’s ability to stretch under stress before breaking. This specification is important for applications where the belt may be subjected to varying loads. Manufacturers typically provide elongation ratings as a percentage of the belt’s original length. A 4 ply conveyor belt usually has an elongation at break rating of around 10
-15%, indicating that it can stretch to accommodate sudden increases in load without breaking.
Adhesion Strength
Adhesion strength measures the bond between the fabric layers and the rubber covers. This specification ensures the belt’s integrity under heavy loads and abrasive conditions. Adhesion strength is usually measured in pounds per inch width (PIW) or newtons per millimeter (N/mm). A high adhesion strength ensures that the layers remain bonded, preventing delamination and ensuring the belt’s durability. A typical 4 ply conveyor belt has an adhesion strength of 35-50 PIW.
Abrasion Resistance
Abrasion resistance is a crucial specification for conveyor belts used in harsh environments. It measures the belt’s ability to withstand wear and tear caused by friction and abrasive materials. Abrasion resistance is typically measured using the DIN (Deutsches Institut für Normung) standard, with lower values indicating better resistance. A 4 ply conveyor belt typically has an abrasion resistance value of less than 150 mm³, ensuring long-lasting performance even in abrasive conditions.
Impact Resistance
Impact resistance measures the belt’s ability to absorb and withstand sudden shocks or impacts. This specification is particularly important for applications involving heavy or sharp materials. Impact resistance is typically measured in joules or foot-pounds. A 4 ply conveyor belt generally has a high impact resistance, ensuring it can handle the rigors of demanding industrial environments without suffering damage.
Flexibility
Flexibility is a measure of the belt’s ability to bend and flex without cracking or breaking. This specification is crucial for conveyor systems with tight turns or inclines. Flexibility is usually measured in terms of the minimum pulley diameter the belt can navigate. A 4 ply conveyor belt typically has a minimum pulley diameter of 8-12 inches, ensuring it can handle various conveyor system designs without cracking or breaking.
Temperature Range
The temperature range specification indicates the operating temperatures within which the belt can function effectively. This is particularly important for applications involving extreme temperatures. A 4 ply conveyor belt usually has a temperature range of -20°F to 200°F (-29°C to 93°C), making it suitable for a wide range of industrial environments.
Chemical Resistance
Chemical resistance measures the belt’s ability to withstand exposure to chemicals without degrading. This specification is important for applications in chemical processing or waste management. A 4 ply conveyor belt typically has good resistance to a variety of chemicals, including oils, acids, and alkalis. This ensures long-term performance and prevents damage from chemical exposure.
Certification and Compliance
Certification and compliance specifications indicate that the belt meets specific industry standards and regulations. These can include ISO standards, MSHA (Mine Safety and Health Administration) approval for mining applications, and FDA (Food and Drug Administration) compliance for food-grade belts. Choosing a certified and compliant 4 ply conveyor belt ensures that it meets the necessary safety, quality, and performance standards.
Understanding the detailed technical specifications of a harga belt conveyor 4 ply is crucial for selecting the right belt for heavy-duty applications. Accurate specifications ensure the belt can handle the required loads, provide the necessary durability, and maintain the flexibility needed for efficient operation. By choosing the correct specifications, businesses can optimize their conveyor systems, improving productivity and reducing maintenance costs.
Applications of Harga Belt Conveyor 4 Ply
The harga belt conveyor 4 ply is a critical component in various industries, renowned for its durability, flexibility, and efficiency in handling heavy loads. Its multi-ply structure, typically comprising four layers of fabric, provides enhanced strength and resistance to wear and tear, making it suitable for a wide range of applications. This section delves into the diverse industrial sectors where harga belt conveyor 4 ply finds its applications, highlighting its indispensability and the specific benefits it brings to each sector.
1. Mining Industry
In the mining sector, the harga belt conveyor 4 ply is extensively used for transporting extracted minerals and ores from the mining site to processing facilities. The conveyor belts must withstand harsh conditions, including abrasive materials, sharp edges, and heavy loads. The four-ply construction offers superior resistance to punctures and tears, ensuring uninterrupted operations. Additionally, the conveyor belts are often equipped with special coatings to resist oil, chemicals, and extreme temperatures, making them ideal for the demanding environment of the mining industry.
2. Manufacturing and Production
Manufacturing plants rely on harga belt conveyor 4 ply for efficient movement of raw materials, semi-finished goods, and finished products along the production line. These conveyor belts are crucial in automating processes, reducing manual handling, and increasing overall productivity. Their robust construction ensures they can handle the constant movement and heavy loads typical in manufacturing environments. Whether it’s the automotive industry, electronics, or consumer goods production, harga belt conveyor 4 ply plays a pivotal role in streamlining operations and maintaining a smooth workflow.
3. Agriculture
In agriculture, the harga belt conveyor 4 ply is used for transporting bulk materials such as grains, seeds, and fertilizers. These conveyor belts help in moving products from storage facilities to processing areas or for loading and unloading trucks. The agricultural sector benefits from the conveyor belts’ ability to handle large volumes efficiently while minimizing product damage. The durability of the four-ply structure ensures that the belts can endure the rough handling and variable environmental conditions typically found in agricultural settings.
4. Food Processing
Food processing industries utilize harga belt conveyor 4 ply to handle a variety of products, from raw ingredients to packaged goods. The conveyor belts must meet stringent hygiene standards and are often made with food-grade materials to prevent contamination. They are designed to be easy to clean and maintain, ensuring compliance with health and safety regulations. In addition to their robustness, these belts are engineered to resist oils, fats, and other substances commonly encountered in food processing, ensuring long-term reliability and efficiency.
5. Logistics and Distribution
The logistics and distribution sector heavily relies on harga belt conveyor 4 ply for sorting, transporting, and distributing packages and goods. Conveyor belts facilitate the movement of items through warehouses and distribution centers, significantly speeding up the sorting and delivery process. The durability and strength of the four-ply belts ensure they can handle the continuous operation and heavy loads typical in logistics environments. Additionally, these belts are designed to operate smoothly and quietly, reducing noise levels in busy distribution centers.
6. Construction
In the construction industry, harga belt conveyor 4 ply is used to transport construction materials such as sand, gravel, cement, and bricks. These conveyor belts need to withstand the rough and abrasive nature of construction materials, and the four-ply construction provides the necessary strength and durability. They are often used in conjunction with other machinery, such as crushers and screens, to ensure a continuous flow of materials on construction sites, enhancing efficiency and reducing manual labor.
7. Recycling
Recycling facilities use harga belt conveyor 4 ply to sort and transport recyclable materials such as plastics, metals, paper, and glass. The conveyor belts help in automating the sorting process, improving efficiency and throughput. The durability of the four-ply structure ensures that the belts can handle the sharp edges and abrasive nature of many recyclable materials. Additionally, these belts can be customized with specific coatings to resist chemicals and other substances encountered in recycling operations.
Installation Process of Harga Belt Conveyor 4 Ply
Installing a harga belt conveyor 4 ply involves several critical steps to ensure it operates efficiently and safely. Proper installation is essential to maximize the conveyor belt’s lifespan and performance. This section provides a detailed step-by-step guide to the installation process, highlighting key considerations and best practices.
Step 1: Preparation and Planning
Before beginning the installation, it is crucial to prepare and plan thoroughly. This includes:
- Site Assessment: Evaluate the installation site to ensure it is suitable for the conveyor system. Consider factors such as space availability, floor conditions, and accessibility.
- Material and Tools: Gather all necessary materials and tools, including the harga belt conveyor 4 ply, mounting brackets, fasteners, rollers, and power tools.
- Safety Precautions: Implement safety measures to protect workers during the installation process. This includes wearing appropriate personal protective equipment (PPE) and ensuring the work area is free from hazards.
Step 2: Setting Up the Frame
The next step is to set up the conveyor frame, which provides the foundation for the entire system.
- Frame Assembly: Assemble the conveyor frame according to the manufacturer’s instructions. Ensure all parts are securely fastened and aligned correctly.
- Leveling: Use a level to ensure the frame is perfectly horizontal. This is crucial for the smooth operation of the conveyor belt.
- Anchoring: Secure the frame to the floor or mounting surface using appropriate anchors or fasteners. This prevents movement or vibration during operation.
Step 3: Installing Rollers and Supports
With the frame in place, the next step is to install the rollers and supports that will guide the conveyor belt.
- Roller Placement: Position the rollers along the length of the conveyor frame. Ensure they are evenly spaced and aligned properly.
- Support Installation: Install additional supports and brackets as needed to provide stability to the rollers. This may include side rails, guides, and tensioning devices.
- Roller Alignment: Verify that all rollers are aligned and level. Misaligned rollers can cause the belt to track improperly and lead to premature wear.
Step 4: Installing the Conveyor Belt
The most critical step in the installation process is fitting the harga belt conveyor 4 ply onto the frame.
- Unrolling the Belt: Carefully unroll the conveyor belt and lay it out along the length of the frame. Ensure there are no twists or folds.
- Belt Positioning: Position the belt so that it is centered on the rollers. This helps prevent tracking issues during operation.
- Joining the Ends: If the belt is supplied in sections, join the ends using appropriate splicing methods. This may include mechanical fasteners, vulcanization, or other techniques specified by the manufacturer.
- Tensioning: Apply tension to the conveyor belt according to the manufacturer’s guidelines. Proper tensioning is crucial for smooth operation and to prevent slippage.
Step 5: Testing and Adjustments
Once the belt is installed, it is essential to test the system and make any necessary adjustments.
- Initial Testing: Run the conveyor belt at a slow speed to check for proper alignment and tension. Look for any signs of tracking issues or abnormal noises.
- Adjustments: Make any necessary adjustments to the rollers, supports, or tensioning devices to ensure the belt runs smoothly and stays centered.
- Full-Speed Testing: Gradually increase the speed of the conveyor belt and continue monitoring its performance. Ensure that the system operates smoothly at full speed.
Step 6: Final Inspection and Safety Checks
Before commissioning the conveyor belt system, conduct a final inspection and safety checks.
- Visual Inspection: Inspect the entire system for any loose fasteners, misaligned components, or other issues.
- Safety Devices: Ensure all safety devices, such as emergency stop buttons and guards, are in place and functioning correctly.
- Documentation: Document the installation process, including any adjustments made and the results of the testing. This information is valuable for future maintenance and troubleshooting.
Maintenance Tips for Harga Belt Conveyor 4 Ply
Maintaining a harga belt conveyor 4 ply is crucial to ensure its longevity and efficiency. Regular maintenance not only prolongs the life of the conveyor belt but also enhances its performance, reducing downtime and operational costs. Below are detailed maintenance tips for harga belt conveyor 4 ply systems.
1. Regular Inspection and Monitoring
One of the fundamental maintenance practices is regular inspection and monitoring. This involves visually inspecting the conveyor belt and its components for signs of wear, damage, or misalignment. Regular monitoring helps in early detection of issues, allowing for timely intervention before minor problems escalate into major failures.
- Visual Checks: Conduct daily visual inspections of the belt surface for signs of wear and tear, such as fraying, cracking, or gouging. Pay special attention to the edges and splices of the belt.
- Component Inspections: Check other components such as rollers, pulleys, and idlers for signs of damage or unusual wear. Ensure that they are free of debris and are functioning smoothly.
- Alignment: Ensure that the belt is properly aligned and that the tracking is correct. Misalignment can cause the belt to drift off course, leading to uneven wear and potential damage.
2. Regular Cleaning
Keeping the harga belt conveyor 4 ply clean is essential for its efficient operation. Accumulation of dirt, debris, and material spillage can cause undue stress on the belt and its components, leading to premature wear.
- Cleaning Schedule: Establish a regular cleaning schedule based on the operating environment. In dusty or dirty environments, more frequent cleaning may be necessary.
- Cleaning Methods: Use appropriate cleaning methods such as brushes, air jets, or water jets to remove dirt and debris. Ensure that the cleaning process does not damage the belt surface or other components.
- Spillage Management: Implement measures to minimize material spillage onto the belt. This may involve using skirting, plows, or other containment systems.
3. Proper Lubrication
Lubrication of moving parts is crucial to reduce friction and wear. Ensure that all bearings, rollers, and other moving parts are properly lubricated according to the manufacturer’s recommendations.
- Lubrication Schedule: Follow a regular lubrication schedule to ensure that all moving parts are adequately lubricated. Over-lubrication or under-lubrication can both cause issues.
- Lubricant Type: Use the correct type of lubricant as specified by the manufacturer. The wrong lubricant can cause damage or reduce the effectiveness of the lubrication.
4. Tension and Tracking Adjustments
Maintaining the correct tension and tracking of the belt is vital for its proper functioning. Incorrect tension can cause slippage, excessive wear, and potential damage to the belt and components.
- Tension Checks: Regularly check and adjust the tension of the belt to ensure it is within the recommended range. Use a tension gauge to measure the tension accurately.
- Tracking Adjustments: Ensure that the belt is tracking correctly. Misalignment can cause the belt to drift and wear unevenly. Adjust the tracking devices to keep the belt centered on the conveyor.
5. Splice Maintenance
Splices are critical points on a conveyor belt where two ends are joined together. Proper maintenance of splices is essential to ensure the integrity and longevity of the belt.
- Regular Inspection: Inspect splices regularly for signs of wear, separation, or damage. Pay close attention to the condition of the splice material and the adhesive used.
- Repairs: Promptly repair any damaged or worn splices. Use the correct splicing techniques and materials as recommended by the manufacturer.
6. Belt Replacement and Repair
Despite regular maintenance, there will come a time when the belt will need to be repaired or replaced. Knowing when and how to replace or repair the belt is crucial to maintaining efficient operations.
- Wear Indicators: Monitor the wear indicators on the belt to determine when it needs to be replaced. Excessive wear can compromise the integrity and performance of the belt.
- Repair Techniques: For minor damages, use appropriate repair techniques such as patching or vulcanizing to extend the life of the belt. Ensure that repairs are done correctly to avoid further damage.
7. Staff Training
Properly trained staff are essential for effective maintenance of harga belt conveyor 4 ply systems. Ensure that all personnel involved in the operation and maintenance of the conveyor are adequately trained.
- Training Programs: Implement regular training programs to keep staff updated on the latest maintenance techniques and safety procedures.
- Documentation: Provide detailed documentation and manuals for reference. Ensure that staff understand and follow the maintenance guidelines provided by the manufacturer.
8. Scheduled Maintenance
In addition to regular inspections and monitoring, scheduled maintenance is crucial to the long-term health of the conveyor system.
- Maintenance Schedule: Develop a comprehensive maintenance schedule that includes periodic checks and servicing of all components. Follow the manufacturer’s recommendations for maintenance intervals.
- Professional Servicing: Consider professional servicing for more complex maintenance tasks. Professional technicians can provide expert insights and ensure that maintenance is carried out to the highest standards.
9. Safety Considerations
Safety should always be a priority during maintenance activities. Ensure that all safety protocols are followed to prevent accidents and injuries.
- Safety Training: Provide regular safety training for all personnel involved in maintenance activities. Ensure that they are aware of the potential hazards and how to mitigate them.
- Personal Protective Equipment (PPE): Ensure that all maintenance staff wear the appropriate PPE, such as gloves, safety glasses, and hard hats.
- Lockout/Tagout Procedures: Implement lockout/tagout procedures to ensure that the conveyor is safely de-energized during maintenance activities.
10. Record Keeping
Maintaining detailed records of all maintenance activities is essential for tracking the condition of the harga belt conveyor 4 ply and planning future maintenance.
- Maintenance Logs: Keep detailed maintenance logs that document all inspections, repairs, and replacements. Include information on the condition of the belt and components, as well as any actions taken.
- Trend Analysis: Use the maintenance records to analyze trends and identify recurring issues. This can help in planning proactive maintenance and preventing future problems.
By following these comprehensive maintenance tips, you can ensure the longevity and efficiency of your harga belt conveyor 4 ply. Regular maintenance not only reduces downtime and operational costs but also enhances the overall performance and reliability of the conveyor system. Remember that proper maintenance is an ongoing process that requires attention to detail, regular inspections, and timely interventions.
Last Updated on August 16, 2024 by Jordan Smith
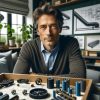
Jordan Smith, a seasoned professional with over 20 years of experience in the conveyor system industry. Jordan’s expertise lies in providing comprehensive solutions for conveyor rollers, belts, and accessories, catering to a wide range of industrial needs. From initial design and configuration to installation and meticulous troubleshooting, Jordan is adept at handling all aspects of conveyor system management. Whether you’re looking to upgrade your production line with efficient conveyor belts, require custom conveyor rollers for specific operations, or need expert advice on selecting the right conveyor accessories for your facility, Jordan is your reliable consultant. For any inquiries or assistance with conveyor system optimization, Jordan is available to share his wealth of knowledge and experience. Feel free to reach out at any time for professional guidance on all matters related to conveyor rollers, belts, and accessories.