Key Benefits of a Tail Drum Conveyor System
The tail drum conveyor is a crucial component in various industrial applications, ensuring the smooth operation of conveyor systems. This guide will explore the different aspects of tail drum conveyors, including their functions, types, and design considerations. Understanding the role of the tail drum conveyor is essential for optimizing performance and reliability in industries such as mining, quarrying, and manufacturing. By examining the unique features and benefits of the tail drum conveyor, this guide aims to provide a comprehensive overview that highlights its importance in maintaining tension and alignment, preventing slippage, and reducing wear and tear on conveyor belts.
Tail Drum Conveyor Overview
Definition and Function
A tail drum conveyor is a crucial component located at the end of the conveyor belt. Its primary function is to redirect the belt back towards the drive pulley, ensuring the maintenance of proper tension and alignment. This redirection is essential for the smooth operation of the conveyor system, preventing belt slippage and misalignment that can cause operational inefficiencies. By maintaining tension, the tail drum conveyor contributes to the overall stability and reliability of the conveyor system.
In practical terms, the tail drum conveyor works by providing a fixed point around which the conveyor belt loops. As the belt moves, it wraps around the tail drum, changing direction and heading back towards the head pulley. This looping action not only keeps the belt aligned but also helps distribute tension evenly across the belt, which is vital for preventing wear and tear. For instance, in a mining operation where heavy loads are common, the tail drum conveyor plays a critical role in ensuring that the belt remains taut and aligned, thereby enhancing the system’s efficiency and lifespan.
Materials and Construction
Tail drum conveyors are typically constructed from durable materials like steel or rubber to withstand harsh industrial environments. The choice of material often depends on the specific requirements of the application. Steel is commonly used due to its strength and durability, making it ideal for heavy-duty applications such as mining and quarrying. Rubber, on the other hand, offers flexibility and resistance to abrasion, which can be beneficial in certain manufacturing environments.
The construction of a tail drum conveyor involves several key components, including the cylindrical shell, end discs, and the shaft. The cylindrical shell is the main body of the drum, designed to provide a smooth surface for the conveyor belt to travel over. End discs are attached to either side of the shell to provide structural support and are often welded to ensure durability. The shaft, which runs through the center of the drum, is used to mount the drum onto the conveyor frame and is typically made from high-strength steel to handle the rotational forces involved.
For example, Martin Sprocket & Gear, Inc. manufactures tail drum conveyors with specific construction standards to meet the rigorous demands of industries like mining. Their drums are made from high-grade steel with precision welding to ensure maximum strength and durability. The use of advanced materials and construction techniques helps to extend the lifespan of the tail drum conveyor, reducing maintenance costs and downtime.
Applications
Tail drum conveyors are widely used in various industries due to their versatility and reliability. In the mining industry, they are essential for the efficient handling of bulk materials such as ore and coal. The robust construction of the tail drum conveyor ensures that it can handle the heavy loads and harsh conditions typically found in mining environments. By maintaining proper belt tension and alignment, the tail drum conveyor helps to minimize downtime and maximize productivity.
In the quarrying industry, tail drum conveyors are used to transport aggregates and other materials from one location to another. The ability to maintain belt tension and alignment is particularly important in this context, as it ensures the consistent and efficient movement of materials, reducing the risk of spillage and material loss.
Manufacturing industries also benefit from the use of tail drum conveyors. For example, in the automotive industry, tail drum conveyors are used in assembly lines to move parts and components between different stages of production. The ability to handle a variety of materials, coupled with the durability of the construction, makes tail drum conveyors an ideal choice for these environments.
A notable example of a company using tail drum conveyors is Caterpillar Inc., which employs these systems in their manufacturing plants to ensure the smooth and efficient movement of parts and materials. By using tail drum conveyors, Caterpillar is able to maintain high levels of productivity and reduce the likelihood of operational disruptions.
The tail drum conveyor is an indispensable component in numerous industrial applications, providing essential functions that enhance the efficiency and reliability of conveyor systems. Its robust construction and ability to maintain tension and alignment make it a valuable asset in industries ranging from mining to manufacturing.
Conveyor Head and Tail Drum Conveyor
Comparison with Head Pulley
The tail drum conveyor is fundamentally different from the head pulley in both function and design, yet they work synergistically to ensure the smooth operation of conveyor systems. While the head pulley is responsible for driving the conveyor belt, providing the necessary power to move the belt and its load, the tail drum conveyor plays a critical role at the opposite end. It helps in redirecting the belt back towards the head pulley, maintaining proper tension and alignment throughout the system.
Understanding the distinction between the head pulley and the tail drum conveyor is essential for optimizing conveyor performance. The head pulley, often powered by a motor, pulls the conveyor belt forward, overcoming friction and the load’s weight. It is usually larger in diameter compared to the tail drum, providing the necessary traction to move the belt efficiently. On the other hand, the tail drum conveyor is typically smaller and works passively to guide the belt back, ensuring that it remains in the correct path and maintains the necessary tension.
For instance, in a large-scale manufacturing facility like those operated by General Motors, the head pulley might be equipped with a high-torque motor to handle the heavy automotive parts being transported. The tail drum conveyor at the end of this system ensures that the belt remains taut and correctly aligned, preventing any slippage that could disrupt the assembly line.
Interdependence
The tail drum conveyor and the head pulley must work in harmony to achieve optimal performance and efficiency. The interdependence of these components is crucial for preventing common issues such as belt slippage and misalignment, which can lead to significant operational disruptions and increased maintenance costs.
The head pulley, by driving the conveyor belt, sets the pace and direction of the belt’s movement. It must exert enough force to move the belt and its load, which requires precise control over speed and torque. Meanwhile, the tail drum conveyor maintains the belt’s tension, preventing it from sagging or slipping off track. This balance is essential, especially in environments where the conveyor system handles varying loads and speeds.
Consider a mining operation managed by BHP Billiton, where conveyor systems are used to transport vast quantities of ore. The head pulley must generate sufficient power to move the heavy loads, while the tail drum conveyor ensures that the belt remains correctly tensioned and aligned, even under fluctuating loads and harsh conditions. Any failure in this interdependence could lead to belt damage or operational downtime, significantly impacting productivity.
To maintain this delicate balance, regular maintenance and precise calibration of both the head pulley and the tail drum conveyor are necessary. This includes checking the alignment, tension, and wear of the belt, as well as ensuring that the pulleys are free from debris and functioning correctly. Advanced systems may use sensors and automated controls to continuously monitor and adjust the tension and alignment, further enhancing the reliability and efficiency of the conveyor system.
The head pulley and the tail drum conveyor are integral components of any conveyor system, each with distinct yet complementary roles. Their interdependence ensures that the conveyor belt operates smoothly and efficiently, handling the demands of various industrial applications. By understanding and optimizing the functions of both the head pulley and the tail drum conveyor, industries can achieve greater operational efficiency and reduce maintenance costs, ensuring continuous and reliable material handling.
Conveyor Drum Pulley in Tail Drum Conveyor Systems
Types of Drum Pulleys
In the context of a tail drum conveyor, understanding the various types of drum pulleys and their functions is essential for optimizing the conveyor system’s performance. The primary types of drum pulleys include head pulleys, tail pulleys, and snub pulleys, each serving a specific role within the system.
- Head Pulleys
Head pulleys are located at the discharge end of the conveyor. Their primary function is to drive the conveyor belt. These pulleys are usually larger in diameter and are often covered with a lagging material, such as rubber or ceramic, to increase traction and prevent belt slippage. For example, Flexco manufactures head pulleys with high-quality rubber lagging that enhances the grip on the belt, thereby improving efficiency and reducing wear. - Tail Pulleys
The tail pulley is a critical component of the tail drum conveyor system. Located at the opposite end of the head pulley, the tail pulley redirects the belt back towards the head pulley while maintaining proper tension and alignment. In a heavy-duty environment like a coal mine operated by Peabody Energy, the tail pulley’s role is crucial for ensuring that the belt remains taut and aligned, which is vital for continuous and efficient material transport. - Snub Pulleys
Snub pulleys are used to increase the angle of wrap on the drive pulley, thereby enhancing the belt’s traction on the drive pulley. This is particularly important in systems where high loads or steep inclines are present. By increasing the wrap angle, snub pulleys help maximize the drive pulley’s grip on the belt, ensuring smooth and reliable operation. For instance, in an Amazon fulfillment center, snub pulleys help maintain the efficiency of conveyor belts transporting packages at high speeds.
Design Specifications
The design specifications of drum pulleys are crucial for the efficient performance of a tail drum conveyor. Key factors such as diameter, material, and lagging options must be carefully considered to meet the specific needs of the application.
Diameter
The diameter of the drum pulley is a significant factor in its performance. Larger diameters are typically used for head pulleys to provide greater traction and to handle higher loads. Conversely, tail pulleys may have smaller diameters but must be robust enough to maintain belt tension and alignment. For example, a mining operation might use head pulleys with diameters of up to 48 inches to handle the heavy loads and harsh conditions.
Material
The material used for drum pulleys affects their durability and performance. Steel is commonly used for its strength and resistance to wear, making it suitable for heavy-duty applications. In environments where corrosion is a concern, such as in chemical plants operated by Dow Chemical, stainless steel or coated pulleys may be used to resist rust and chemical damage.
Lagging Options
Lagging, the material covering the drum pulley’s surface, plays a vital role in enhancing the friction between the pulley and the conveyor belt. Rubber lagging is common and provides a good balance of grip and durability. Ceramic lagging, on the other hand, offers superior wear resistance and is used in applications where high abrasion is a concern. For example, Continental AG produces drum pulleys with ceramic lagging for use in mining operations, where the abrasive nature of materials can quickly wear down other types of lagging.
Other Design Considerations
Other important design considerations include the type of bearings used, the method of conveyor roller shaft attachment, and the overall structural integrity of the drum pulley. Bearings must be selected to handle the specific load and rotational speed requirements of the conveyor system. The shaft attachment method, whether it be through a keyed or keyless design, must ensure secure and reliable operation under varying loads and conditions.
For instance, Martin Sprocket & Gear, Inc. uses advanced welding techniques and high-precision machining to ensure that their drum pulleys meet stringent quality standards. This attention to detail helps ensure that the pulleys perform reliably over long periods, even in demanding applications.
The design and selection of drum pulleys for a tail drum conveyor require careful consideration of various factors to ensure optimal performance and longevity. By understanding the specific needs of the application and selecting appropriately designed pulleys, industries can enhance the efficiency and reliability of their conveyor systems, thereby improving overall productivity and reducing maintenance costs.
Drum Pulley Drawing in Tail Drum Conveyor Systems
Technical Drawings
Technical drawings are essential for understanding the detailed specifications and technical aspects of a tail drum conveyor. These drawings provide a comprehensive view of the design, construction, and operational parameters, ensuring that every component is manufactured and assembled to meet precise standards. For instance, companies like CEMA (Conveyor Equipment Manufacturers Association) provide detailed technical guidelines and drawings to ensure consistency and reliability in conveyor system components.
In a tail drum conveyor, the technical drawings typically include the dimensions and geometry of the drum pulley, detailing the cylindrical shell, end discs, shaft, and any additional features such as lagging. These drawings are crucial for engineers and technicians as they provide a visual representation of the pulley, highlighting critical measurements and tolerances that must be adhered to during manufacturing and assembly.
For example, in the mining industry, technical drawings of a tail drum conveyor used by Rio Tinto would detail the drum’s diameter, length, wall thickness, and the materials used. These specifications are critical for ensuring that the drum can withstand the heavy loads and abrasive materials typical in mining operations. By following these detailed drawings, manufacturers can produce drum pulleys that meet the stringent demands of such high-stress environments.
Key Components
Understanding the key components of a tail drum conveyor is vital for grasping how these systems function and ensuring their reliable operation. The main structural elements of a drum pulley include the cylindrical shell, end discs, and shaft attachment methods, each playing a critical role in the system’s performance.
Cylindrical Shell
The cylindrical shell is the main body of the drum pulley, providing the surface over which the conveyor belt runs. The shell must be robust and smooth to ensure minimal friction and wear on the belt. It is typically made from high-strength materials such as carbon steel or stainless steel, depending on the application’s requirements. For example, a tail drum conveyor used in a cement plant operated by LafargeHolcim would likely have a shell made from abrasion-resistant steel to handle the rough, abrasive materials.
End Discs
End discs are attached to either side of the cylindrical shell, providing structural support and helping to maintain the shell’s shape under load. These discs are usually welded to the shell to form a solid, integral unit. The design and material of the end discs are critical for the overall durability and performance of the drum pulley. For instance, in a tail drum conveyor used by Caterpillar Inc., the end discs would be precision-machined and welded to ensure maximum strength and stability.
Shaft Attachment Methods
The shaft is another critical component, running through the center of the drum pulley and providing the means to mount the drum onto the conveyor frame. The attachment method of the shaft to the drum is crucial for ensuring that the drum rotates smoothly and reliably. Common attachment methods include keyways, set screws, and locking assemblies. In heavy-duty applications, such as those handled by BHP Group, keyless locking assemblies might be used to provide a secure and maintenance-friendly attachment.
Detailed technical drawings of these components will show the precise measurements and specifications required to manufacture them. For example, a technical drawing of a tail drum conveyor might specify the exact dimensions of the cylindrical shell, including its diameter, wall thickness, and length. It would also detail the design of the end discs, including their thickness and how they are welded to the shell. Finally, the drawing would show the shaft and its attachment method, ensuring that the drum pulley can be securely mounted and operated.
For instance, Martin Sprocket & Gear, Inc. uses advanced CAD (Computer-Aided Design) software to create detailed technical drawings for their tail drum conveyors. These drawings are essential for ensuring that each component is manufactured to the highest standards, providing reliability and performance in demanding industrial applications.
The technical drawings and key components of a tail drum conveyor are essential for understanding its design and ensuring its reliable operation. By providing detailed specifications and visual representations of the drum pulley, these drawings help manufacturers produce high-quality components that meet the rigorous demands of various industrial applications. This detailed understanding of the drum pulley’s construction and design is crucial for maintaining efficient and reliable conveyor systems.
Conveyor Tail Drum Overview
Definition and Function
A conveyor tail drum, also known as a tail pulley, is a critical component located at the end of the conveyor belt system. Its primary function is to redirect the belt back towards the drive pulley, ensuring the maintenance of proper tension and alignment. This redirection is essential for the smooth operation of the conveyor system, preventing belt slippage and misalignment that can cause operational inefficiencies. By maintaining tension, the conveyor tail drum contributes to the overall stability and reliability of the conveyor system.
In practical terms, the conveyor tail drum works by providing a fixed point around which the conveyor belt loops. As the belt moves, it wraps around the tail drum, changing direction and heading back towards the head pulley. This looping action not only keeps the belt aligned but also helps distribute tension evenly across the belt, which is vital for preventing wear and tear. For instance, in a mining operation where heavy loads are common, the conveyor tail drum plays a critical role in ensuring that the belt remains taut and aligned, thereby enhancing the system’s efficiency and lifespan.
Materials and Construction
Conveyor tail drums are typically constructed from durable materials like steel or rubber to withstand harsh industrial environments. The choice of material often depends on the specific requirements of the application. Steel is commonly used due to its strength and durability, making it ideal for heavy-duty applications such as mining and quarrying. Rubber, on the other hand, offers flexibility and resistance to abrasion, which can be beneficial in certain manufacturing environments.
The construction of a conveyor tail drum involves several key components, including the cylindrical shell, end discs, and the shaft. The cylindrical shell is the main body of the drum, designed to provide a smooth surface for the conveyor belt to travel over. End discs are attached to either side of the shell to provide structural support and are often welded to ensure durability. The shaft, which runs through the center of the drum, is used to mount the drum onto the conveyor frame and is typically made from high-strength steel to handle the rotational forces involved.
For example, Martin Sprocket & Gear, Inc. manufactures conveyor tail drums with specific construction standards to meet the rigorous demands of industries like mining. Their drums are made from high-grade steel with precision welding to ensure maximum strength and durability. The use of advanced materials and construction techniques helps to extend the lifespan of the conveyor tail drum, reducing maintenance costs and downtime.
Applications
Conveyor tail drums are widely used in various industries due to their versatility and reliability. In the mining industry, they are essential for the efficient handling of bulk materials such as ore and coal. The robust construction of the conveyor tail drum ensures that it can handle the heavy loads and harsh conditions typically found in mining environments. By maintaining proper belt tension and alignment, the conveyor tail drum helps to minimize downtime and maximize productivity.
In the quarrying industry, conveyor tail drums are used to transport aggregates and other materials from one location to another. The ability to maintain belt tension and alignment is particularly important in this context, as it ensures the consistent and efficient movement of materials, reducing the risk of spillage and material loss.
Manufacturing industries also benefit from the use of conveyor tail drums. For example, in the automotive industry, conveyor tail drums are used in assembly lines to move parts and components between different stages of production. The ability to handle a variety of materials, coupled with the durability of the construction, makes conveyor tail drums an ideal choice for these environments.
A notable example of a company using conveyor tail drums is Caterpillar Inc., which employs these systems in their manufacturing plants to ensure the smooth and efficient movement of parts and materials. By using conveyor tail drums, Caterpillar is able to maintain high levels of productivity and reduce the likelihood of operational disruptions.
The conveyor tail drum is an indispensable component in numerous industrial applications, providing essential functions that enhance the efficiency and reliability of conveyor systems. Its robust construction and ability to maintain tension and alignment make it a valuable asset in industries ranging from mining to manufacturing.
Conveyor Belt Pulley Types in Tail Drum Conveyor Systems
Overview of Pulley Types
Understanding the various pulley types used in conveyor systems, including the tail drum conveyor, is essential for optimizing their performance and ensuring reliability. Conveyor systems employ several types of pulleys, each serving a distinct function. These include head pulleys, tail pulleys, snub pulleys, bend pulleys, and take-up pulleys. Each type of pulley contributes to the overall efficiency and functionality of the conveyor system.
- Head Pulleys
The head pulley is located at the discharge end of the conveyor. It drives the conveyor belt and is typically larger in diameter than other pulleys. The head pulley is often lagged with rubber or ceramic to increase traction and prevent slippage. For example, the head pulleys used by mining companies like Anglo American are designed to handle heavy loads and harsh conditions, ensuring continuous operation. - Tail Pulleys
Tail pulleys are critical components of the tail drum conveyor. Positioned at the opposite end of the head pulley, the tail pulley redirects the conveyor belt back towards the head pulley while maintaining tension and alignment. Companies such as Martin Engineering provide tail pulleys that are robustly constructed to withstand the demands of industries like mining and quarrying. These pulleys are essential for maintaining the belt’s proper tension and preventing misalignment. - Snub Pulleys
Snub pulleys are used to increase the wrap angle of the belt around the drive pulley. This additional wrap enhances the traction of the belt on the drive pulley, which is particularly useful in applications where there is a high load or steep incline. In industrial applications, such as those managed by Thyssenkrupp, snub pulleys play a vital role in ensuring the efficient transmission of power and preventing belt slippage. - Bend Pulleys
Bend pulleys are used to change the direction of the conveyor belt. These pulleys are typically installed to redirect the belt and provide the necessary tension for smooth operation. Bend pulleys are critical in complex conveyor systems where the belt needs to navigate multiple changes in direction. For instance, in large manufacturing plants operated by companies like Procter & Gamble, bend pulleys help to efficiently route the conveyor belt through various stages of the production process. - Take-up Pulleys
Take-up pulleys are adjustable pulleys used to maintain the proper tension on the conveyor belt. These pulleys ensure that the belt remains taut and aligned, accommodating changes in belt length due to stretching or environmental conditions. For example, in an agricultural processing facility run by Archer Daniels Midland, take-up pulleys are essential for adjusting the tension of long conveyor belts that transport grains and other materials.
Material and Design Variations
The materials and design features of conveyor pulleys, including those used in tail drum conveyor systems, are critical for their performance and durability. Different industrial applications require specific material properties and design characteristics to handle various operational demands.
Material Selection
The material selection for conveyor pulleys depends on the specific requirements of the application. Common materials include carbon steel, stainless steel, and aluminum. Carbon steel is widely used for its strength and durability, making it suitable for heavy-duty applications such as mining and quarrying. Stainless steel offers excellent corrosion resistance, making it ideal for use in food processing and chemical industries. Aluminum, being lightweight and corrosion-resistant, is often used in applications where weight reduction is essential.
For instance, a tail drum conveyor in a salt processing plant operated by Morton Salt would likely use stainless steel pulleys to resist the corrosive effects of salt. In contrast, a conveyor system in a coal mine might use carbon steel pulleys for their robustness and ability to handle heavy loads.
Design Features
The design features of conveyor pulleys can significantly impact their performance. Key design aspects include the pulley’s diameter, width, and the type of lagging used. The diameter of the pulley affects the amount of belt wrap and the tension distribution across the belt. Larger diameters are typically used for head pulleys to provide better traction and reduce belt wear.
Lagging, the material covering the pulley’s surface, enhances the friction between the belt and the pulley. Rubber lagging is common and provides a good balance of grip and durability. Ceramic lagging offers superior wear resistance and is used in applications where high abrasion is a concern. For example, Fenner Dunlop produces conveyor pulleys with ceramic lagging that are used in mining operations to extend the service life of the pulleys and reduce maintenance costs.
Another important design feature is the construction of the pulley’s shell and end discs. Precision welding and machining are essential to ensure that the pulley maintains its structural integrity and operates smoothly. Companies like Continental AG use advanced manufacturing techniques to produce conveyor pulleys with high concentricity and balance, which are crucial for reducing vibration and wear.
By selecting the appropriate materials and design features, industries can ensure that their tail drum conveyor systems operate efficiently and reliably. Understanding the various types of conveyor pulleys and their specific applications helps in making informed decisions that enhance the overall performance and longevity of the conveyor system.
Conveyor Head Pulley in Tail Drum Conveyor Systems
Role in the System
The head pulley is a pivotal component in the tail drum conveyor system, playing a crucial role in driving the conveyor belt and ensuring smooth material handling. Positioned at the discharge end of the conveyor, the head pulley is responsible for imparting motion to the belt, which is essential for the transportation of materials. The head pulley works in tandem with the tail drum conveyor to maintain proper belt tension and alignment, thereby enhancing the system’s efficiency and reliability.
In a tail drum conveyor, the head pulley’s primary function is to provide the driving force that propels the conveyor belt. This is typically achieved through a motor connected to the head pulley via a gearbox. The rotational motion of the head pulley is transferred to the conveyor belt, moving it forward along the conveyor path. This motion is critical for transporting materials from one point to another within industrial settings. For example, in an automotive assembly line at Ford Motor Company, the head pulley drives the conveyor belt that moves car parts through various stages of assembly, ensuring a seamless production process.
Moreover, the head pulley’s interaction with the tail drum conveyor is crucial for maintaining belt tension. Proper tension is essential to prevent belt slippage and ensure that the belt remains aligned with the pulleys. If the tension is too low, the belt may slip, leading to inefficiencies and potential damage to the conveyor system. Conversely, excessive tension can cause undue stress on the belt and pulleys, leading to premature wear and tear. By working together, the head pulley and the tail drum conveyor maintain the optimal tension, promoting smooth and reliable operation.
Additionally, the head pulley contributes to the overall stability and direction of the conveyor belt. As the belt moves over the head pulley, it experiences a change in direction, which is essential for discharging materials at the desired location. This directional change is facilitated by the head pulley’s design, which ensures that the belt moves smoothly without causing material spillage or misalignment. For instance, in a large-scale mining operation by Rio Tinto, the head pulley’s role in directing the conveyor belt is critical for efficiently transporting ore from the extraction site to the processing facility.
Performance Enhancements
The design and performance of the head pulley can significantly impact the overall efficiency and longevity of the tail drum conveyor system. Several design features and enhancements can be incorporated into the head pulley to improve its performance and extend its service life.
One key design feature is the use of lagging on the head pulley. Lagging refers to the material covering the surface of the pulley, which enhances the friction between the pulley and the conveyor belt. Common lagging materials include rubber and ceramic, each offering distinct advantages. Rubber lagging provides a good balance of grip and durability, making it suitable for a wide range of applications. Ceramic lagging, on the other hand, offers superior wear resistance and is ideal for high-abrasion environments. For example, Flexco manufactures head pulleys with ceramic lagging for use in the mining industry, where the abrasive nature of the transported materials can quickly wear down other types of lagging.
Another important aspect of head pulley design is the pulley’s diameter. A larger diameter head pulley can provide better traction and reduce the stress on the conveyor belt, thereby extending its lifespan. Additionally, larger diameters can accommodate higher loads and increase the wrap angle of the belt, improving the overall grip and reducing slippage. For instance, a head pulley with a diameter of 48 inches might be used in a heavy-duty conveyor system at Caterpillar Inc., where it needs to handle large and heavy materials with minimal slippage.
The material selection for the head pulley is also crucial for its performance. High-strength materials such as carbon steel and stainless steel are commonly used to ensure the pulley can withstand the stresses of continuous operation. In environments where corrosion is a concern, such as in chemical processing plants operated by Dow Chemical, stainless steel pulleys are preferred for their resistance to rust and chemical damage.
Furthermore, advanced manufacturing techniques can enhance the precision and balance of the head pulley. Precision machining and dynamic balancing ensure that the pulley rotates smoothly, minimizing vibrations and reducing wear on the belt and bearings. Companies like Martin Sprocket & Gear, Inc. utilize state-of-the-art machining processes to produce head pulleys with high concentricity and balance, which are critical for high-speed conveyor systems.
By incorporating these design features and performance enhancements, the head pulley can significantly improve the efficiency and longevity of the tail drum conveyor system. Properly designed and maintained head pulleys ensure smooth operation, reduce maintenance costs, and enhance the overall productivity of industrial processes. This detailed understanding of the head pulley’s role and its performance enhancements is crucial for optimizing conveyor systems across various industries.
Tail Pulley Function in Tail Drum Conveyor Systems
Maintaining Belt Tension
The role of the tail drum conveyor in maintaining proper belt tension is critical to the overall efficiency and functionality of the conveyor system. The tail pulley, positioned at the end of the conveyor, helps ensure that the belt remains taut and aligned, which is essential for smooth and reliable operation.
Maintaining the correct tension in a tail drum conveyor system involves several key factors. The tension must be sufficient to prevent the belt from slipping off the pulleys, which can cause significant operational disruptions. At the same time, it should not be so tight that it causes excessive wear on the belt and other components. The tail pulley achieves this balance by acting as a counterbalance to the head pulley, creating a stable and controlled tension throughout the conveyor belt.
In large-scale industrial operations, such as those conducted by Caterpillar Inc., maintaining proper belt tension is crucial for handling heavy loads and preventing downtime. For example, in a mining operation where the conveyor system is used to transport ore, the tail drum conveyor ensures that the belt tension is consistently maintained, allowing for the continuous and efficient movement of materials. This consistent tension helps prevent the belt from sagging or becoming misaligned, which can lead to operational inefficiencies and increased maintenance requirements.
To achieve and maintain the proper tension, many modern tail drum conveyor systems are equipped with automated tensioning devices. These devices continuously monitor the tension and make real-time adjustments to ensure optimal performance. Companies like Siemens offer advanced tensioning systems that use sensors and actuators to maintain the correct belt tension automatically, reducing the need for manual adjustments and increasing the overall reliability of the conveyor system.
Preventing Wear and Tear
Proper functioning of the tail pulley in a tail drum conveyor is essential for reducing wear and tear on the conveyor belt and extending its operational life. The tail pulley ensures that the belt is properly aligned and tensioned, which minimizes friction and prevents damage to both the belt and the pulleys.
One of the primary ways the tail drum conveyor prevents wear and tear is by maintaining a smooth and consistent motion of the conveyor belt. When the belt is properly tensioned, it moves over the pulleys without excessive friction, which reduces the wear on the belt’s surface. This is particularly important in industries where the conveyor system is in constant use, such as in the manufacturing plants operated by General Motors. In these environments, minimizing wear and tear on the conveyor belt can lead to significant cost savings by reducing the frequency of belt replacements and maintenance.
Another important factor in preventing wear and tear is the design and construction of the tail pulley itself. High-quality materials and precise manufacturing processes ensure that the tail pulley can withstand the demands of continuous operation. For instance, Fenner Dunlop manufactures tail pulleys with high-strength steel and advanced welding techniques to ensure durability and longevity. These robust pulleys are designed to handle the stresses of heavy-duty applications, reducing the risk of failure and extending the life of the conveyor system.
The tail drum conveyor also plays a crucial role in preventing belt misalignment, which can cause significant wear and tear on the belt edges. When the belt is not properly aligned, it can rub against the conveyor structure, leading to fraying and damage. By maintaining proper alignment, the tail pulley ensures that the belt runs smoothly and reduces the risk of edge wear. This is particularly important in high-precision environments, such as in the aerospace manufacturing facilities of Boeing, where maintaining the integrity of the conveyor belt is critical for operational efficiency.
Furthermore, regular maintenance and inspection of the tail drum conveyor can help prevent wear and tear. This includes checking the alignment and tension of the belt, inspecting the condition of the pulleys, and ensuring that all components are free from debris and functioning correctly. By conducting routine maintenance, companies can identify and address potential issues before they lead to significant wear and tear, thereby extending the life of the conveyor system.
The tail drum conveyor is essential for maintaining proper belt tension and alignment, which is crucial for preventing wear and tear on the conveyor belt. By ensuring smooth and consistent operation, the tail pulley helps extend the operational life of the conveyor system, reducing maintenance costs and enhancing overall productivity in various industrial applications.
FAQs about Tail Drum Conveyor
A tail drum conveyor, also known as a tail pulley, is a crucial component in the conveyor belt system. It is typically located at the end of the conveyor belt system and serves as the point where the belt changes direction and starts its return journey. The tail drum helps in maintaining the tension and alignment of the conveyor belt, ensuring smooth and efficient operation. Made from durable materials like steel, it is designed to withstand the harsh conditions of industrial environments. The tail drum is essential for preventing slippage and maintaining the belt’s tension, thereby enhancing the overall efficiency and lifespan of the conveyor system.
The tail of a conveyor refers to the end part of the conveyor system where the tail drum conveyor is situated. This section is critical for the smooth operation of the conveyor belt. The tail drum, located at this end, ensures that the belt runs smoothly and maintains the necessary tension. It plays a pivotal role in the return path of the conveyor belt, helping in aligning and guiding the belt back to the drive drum. Proper maintenance of the tail section is essential for preventing operational issues like belt misalignment, excessive wear, and tear, and potential downtime in industrial processes.
A conveyor drum, often referred to as a pulley, is a cylindrical component that drives and guides the conveyor belt. There are two primary types of conveyor drums: the drive drum, which provides the motive power for the belt’s movement, and the tail drum conveyor, which guides the belt at the return end. The conveyor drum’s primary function is to maintain tension, provide traction, and guide the belt along the conveyor system. Made from materials like steel or aluminum, conveyor drums are designed to handle heavy loads and harsh working conditions, ensuring the efficiency and reliability of the conveyor system.
In a conveyor system, the head and tail refer to two different ends where the main pulleys are located. The head drum is situated at the discharge end of the conveyor belt and is responsible for driving the belt. It provides the necessary power to move the belt and the materials on it. On the other hand, the tail drum conveyor is located at the feed end, where the belt changes direction to start its return journey. While the head drum drives the belt, the tail drum primarily guides and maintains tension. Both components are crucial for the conveyor system’s efficient and smooth operation, ensuring optimal performance and longevity of the belt.
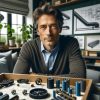
Jordan Smith, a seasoned professional with over 20 years of experience in the conveyor system industry. Jordan’s expertise lies in providing comprehensive solutions for conveyor rollers, belts, and accessories, catering to a wide range of industrial needs. From initial design and configuration to installation and meticulous troubleshooting, Jordan is adept at handling all aspects of conveyor system management. Whether you’re looking to upgrade your production line with efficient conveyor belts, require custom conveyor rollers for specific operations, or need expert advice on selecting the right conveyor accessories for your facility, Jordan is your reliable consultant. For any inquiries or assistance with conveyor system optimization, Jordan is available to share his wealth of knowledge and experience. Feel free to reach out at any time for professional guidance on all matters related to conveyor rollers, belts, and accessories.