How to Select Coal Mining Conveyor Belt Systems
In the realm of coal mining, the conveyor belt stands as a pivotal component, streamlining the movement of coal from the depths of mines to the surface with unparalleled efficiency. This seamless transportation is crucial not only for the productivity of mining operations but also for maintaining the safety and well-being of the workforce. As we delve into the intricacies of coal mining conveyor belts, we will explore a variety of types, each with its unique specifications tailored to meet the rigorous demands of the mining environment. Furthermore, we will shed light on the esteemed manufacturers who engineer these belts, ensuring they withstand the harsh conditions of coal mining. Equally important is the consideration of costs, as the economic aspects of conveyor belts—ranging from initial investment to long-term maintenance—play a significant role in the operational budget of mining projects. Through this exploration, we aim to provide a comprehensive understanding of how these belts are integral to the coal mining industry, facilitating not just the transport of coal but also the efficiency and safety of the operations involved.
The Role of Conveyor Belts in Coal Mining
The coal mining conveyor belt stands as a pivotal component in the infrastructure of coal mining operations, serving as the lifeline that ensures the seamless flow of coal from the depths of mines to the surface for processing or storage. Coal mining conveyor belt are ideal for harsh coal mining environments, ensuring efficient, safe, and reliable coal transportation.This system not only streamlines the transportation of coal but also significantly enhances the efficiency and safety of mining operations.
Integral to Operations
At the heart of coal mining operations, the coal mining conveyor belt system is ingeniously designed to handle the rugged and demanding environment of the mining sites. These belts are tasked with the critical job of moving large quantities of coal over varying distances, from the mining faces where coal is extracted to the processing plants where it is prepared for sale, or to storage areas where it awaits shipment. The versatility and adaptability of conveyor belts to different mining environments make them indispensable in the coal mining industry.
Benefits of Using Conveyor Belts in Coal Mining
- Efficiency: Conveyor belts provide a continuous, high-capacity flow of coal, which significantly increases the overall efficiency of mining operations. They can move more coal out of mines than traditional haulage methods, such as trucks or railcars, which require loading and unloading.
- Safety: By reducing the need for heavy truck traffic and manual handling of coal, conveyor belts lower the risk of accidents and injuries among workers, making the mining environment safer.
- Cost-effectiveness: Although the initial investment in a conveyor belt system may be significant, the reduction in operational costs over time, such as labor, maintenance, and fuel, makes it a cost-effective solution for coal mining companies.
- Energy Efficiency: Conveyor belts are designed to be energy efficient, especially when compared to truck haulage, which can consume a vast amount of fuel. This efficiency contributes to lower operational costs and a reduced carbon footprint.
- Environmental Impact: With less dust and noise compared to trucks, conveyor belts have a smaller environmental footprint, helping to minimize the impact of mining operations on the surrounding environment.
- Reliability: Modern conveyor belt systems are highly reliable, with advanced technology to monitor the health of the belt and predict maintenance, reducing unexpected downtime.
- Flexibility: Conveyor systems can be designed to fit specific mining operations, taking into account the layout of the site and the distance coal needs to be transported. This flexibility allows for optimized coal flow and efficient use of space.
- Longevity: Built to withstand harsh mining conditions, conveyor belts are durable and have a long service life, which is crucial for continuous operations and minimizing replacement costs.
The coal mining conveyor belt is more than just a component in the coal mining industry; it is a critical asset that enhances the efficiency, safety, and sustainability of coal mining operations. Its benefits extend beyond mere transportation, contributing to the operational excellence and environmental stewardship of the mining sector.
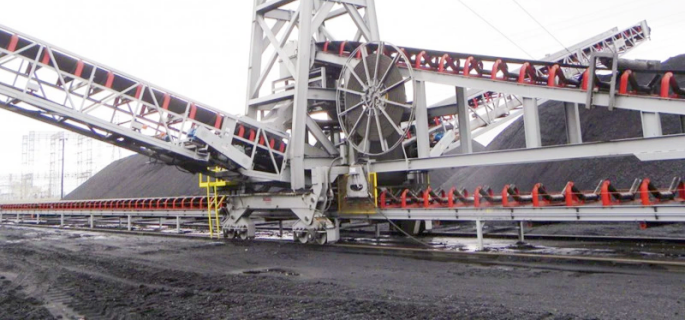
Types of Coal Mining Conveyor Belts
The diversity in the types of coal mining conveyor belts is a testament to the varied nature of coal mining operations and the unique challenges they present. From the depths of underground mines to the vast expanses of open-pit mines, the right type of conveyor belt is crucial for efficient and effective coal transport. Below is an overview of the different conveyor belt types used in coal mining, highlighting their specific applications and advantages.
Type | Application in Coal Mining | Advantages |
---|---|---|
Belt Conveyor | The most common type of coal mining conveyor belt, used for horizontal and inclined transport of bulk materials. | High efficiency, large capacity, and ability to cover long distances with a single system. |
Screw Conveyor | Used for moving fine coal and other materials in a confined, tubular space. | Ideal for handling fine or crushed coal, providing a sealed and controlled environment. |
Flight Conveyor | Utilizes a series of scrapers or flights attached to a chain, moving within a trough, to push coal along. | Effective for handling sticky or wet coal that may adhere to other types of conveyors. |
Bucket Conveyor | Consists of a series of buckets attached to a belt or chain, used for vertical or steeply inclined transport. | Enables efficient vertical transport of coal, minimizing the footprint of the conveyor system. |
Grab Bucket Conveyor | Features a series of grab buckets that pick up coal and transport it over short distances. | Useful for loading and unloading coal in areas where space is limited or precise control over the placement of coal is required. |
Each type of coal mining conveyor belt is designed to meet specific operational needs, ensuring that coal is moved efficiently, safely, and economically from the mine to its destination. Whether it’s the high-capacity transport offered by belt conveyors, the precision handling of screw conveyors, the robustness of flight conveyors, the vertical capabilities of bucket conveyors, or the controlled movement provided by grab bucket conveyors, the right conveyor system can significantly enhance the productivity and safety of coal mining operations.
Mining Conveyor Belt Accessories
Mining conveyor belt accessories are essential for enhancing the efficiency, safety, and longevity of conveyor belt systems used in mining operations. Here are some key accessories commonly used:
1. Idlers and Rollers
- Impact Rollers: Absorb the impact of heavy loads falling onto the belt, protecting the belt from damage.
- Carrying Idlers: Support the belt and the load being transported.
- Return Idlers: Support the empty belt on its return journey.
- Self-aligning Idlers: Help to keep the belt aligned and prevent it from wandering.
2. Belt Cleaners and Scrapers
- Primary Belt Cleaners: Positioned at the head pulley to remove the bulk of the material adhering to the belt.
- Secondary Belt Cleaners: Installed further along the belt to remove any remaining material.
- V-Plows and Diagonal Plows: Prevent material from getting trapped between the belt and the pulleys, which can cause damage and misalignment.
3. Skirting and Sealing Systems
- Skirting Systems: Installed at transfer points to contain the material on the belt and reduce spillage.
- Dust Sealing: Prevents dust from escaping, improving air quality and safety in the mining environment.
4. Belt Tracking Systems
- Guiding Systems: Help to keep the belt centered and prevent misalignment, reducing wear and tear.
- Automatic Tracking Systems: Use sensors and actuators to continuously monitor and adjust the belt’s alignment.
5. Pulley Lagging
- Rubber Lagging: Increases the friction between the belt and the pulleys, reducing slippage.
- Ceramic Lagging: Provides superior wear resistance and increases the lifespan of the pulley.
6. Transfer Chutes and Hoppers
- Wear-resistant Liners: Protect the structure of the chutes and hoppers from abrasive materials.
- Flow Aids: Ensure smooth movement of material through the transfer points, reducing blockages and downtime.
7. Belt Covers and Hood Systems
- Weather Covers: Protect the belt and the transported material from the elements, such as rain, wind, and UV radiation.
- Safety Covers: Prevent accidents by covering moving parts of the conveyor system.
8. Belt Weighers and Monitoring Systems
- Belt Scales: Measure the weight of the material being transported, providing essential data for operational efficiency.
- Condition Monitoring Systems: Continuously monitor the health and performance of the conveyor belt, alerting operators to potential issues before they become critical.
9. Belt Clamps and Splicing Tools
- Belt Clamps: Secure the belt during maintenance and splicing operations.
- Splicing Kits: Include all the necessary tools and materials for on-site belt repairs and splicing.
10. Safety Accessories
- Emergency Stop Systems: Allow workers to quickly stop the conveyor in case of an emergency.
- Pull Cords: Positioned along the length of the conveyor, enabling workers to stop the belt from any point.
By integrating these accessories into a mining conveyor belt system, operators can significantly improve efficiency, safety, and overall operational effectiveness.
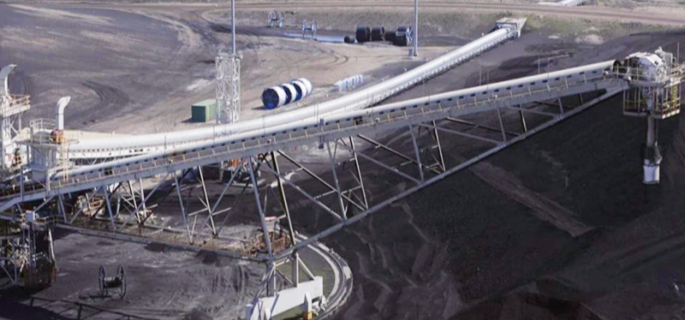
Above or Underground Coal Mining Conveyor Belt
For both above and underground coal mining, the conveyor belt system plays a crucial role in efficiently transporting coal from the mining site to the processing plant or storage area. Here are key aspects to consider for conveyor belts used in these environments:
Above Ground Coal Mining Conveyor Belts
- Durability: Must withstand harsh environmental conditions, including exposure to UV radiation, rain, and wind.
- Material Handling: Capable of transporting large quantities of coal over long distances.
- Belt Construction: Typically made from high-strength materials such as rubber or PVC with steel reinforcement to handle heavy loads.
- Maintenance: Designed for easy maintenance and quick replacement to minimize downtime.
- Safety Features: Include fire-resistant and anti-static properties to prevent accidents.
Underground Coal Mining Conveyor Belts
- Flame Resistance: Essential to meet strict fire safety standards due to the high risk of fires in underground environments.
- Low Smoke Emission: Materials that emit minimal smoke in case of a fire to ensure the safety of miners.
- Durability: Robust construction to handle the abrasive nature of coal and the harsh conditions of underground mining.
- Flexibility: Able to navigate through the complex and often restricted underground tunnels.
- Maintenance and Accessibility: Designed for ease of access and maintenance in confined spaces.
Key Considerations for Both Environments
- Belt Speed: Optimized for the efficient transportation of coal while maintaining safety standards.
- Load Capacity: Engineered to handle the expected volume and weight of coal.
- Energy Efficiency: Designed to reduce energy consumption and operational costs.
- Automation and Monitoring: Integration with automated systems for monitoring belt health, speed, and load, enhancing overall efficiency and safety.
Example Products
- GRAM Conveyor Belts: These belts could be tailored to meet the specific needs of coal mining, whether above or underground, focusing on durability, safety, and efficiency.
When selecting a conveyor belt for coal mining, it is critical to consider the specific requirements of the mining environment, whether it is above or underground. The right choice will enhance safety, efficiency, and longevity, contributing to the overall success of the mining operation.
Key Specifications of Coal Mining Conveyor Belts
When selecting a coal mining conveyor belt, understanding the key specifications is crucial to ensure optimal performance and durability under the harsh conditions of mining operations. These specifications not only determine the conveyor belt’s ability to transport coal efficiently but also its resistance to wear, tear, and environmental challenges. Below are eight important specifications to consider:
- Material: The composition of the coal mining conveyor belt is fundamental, as it affects its durability, flexibility, and resistance to abrasion and tearing. Common materials include rubber, PVC, and synthetic fabrics, each offering different levels of strength and resilience.
- Tensile Strength: This indicates the maximum load that the conveyor belt can handle without breaking. High tensile strength is essential for belts carrying heavy loads of coal, ensuring they can withstand the weight and stress of continuous operation.
- Width: The width of the conveyor belt must be suitable for the size and volume of coal to be transported. Wider belts can carry more coal, improving the efficiency of coal transportation from the mine to processing facilities.
- Length: The length of the conveyor belt is determined by the distance between the coal extraction site and the processing or storage area. Longer belts are required for extensive mining operations, where coal needs to be transported over significant distances.
- Thickness: The thickness of the conveyor belt contributes to its durability and impact resistance. Thicker belts are more resistant to punctures, tears, and wear, making them suitable for rough mining conditions.
- Temperature Resistance: Coal mining operations can expose conveyor belts to extreme temperatures, from the cold of underground mines to the heat of processing areas. Temperature-resistant materials ensure the belt’s performance is not compromised by these conditions.
- Speed: The speed at which the conveyor belt moves impacts the overall efficiency of coal transportation. The optimal speed depends on the operation’s scale, the type of coal being transported, and the belt’s design.
- Flexibility: The ability of the conveyor belt to navigate curves, inclines, and declines without compromising its integrity or the coal’s stability is crucial. Flexibility is especially important in complex mine layouts where the conveyor path may not be straight.
These specifications directly impact the performance and longevity of coal mining conveyor belts. A well-chosen conveyor belt that meets these specifications can handle the demanding conditions of coal mining, ensuring efficient coal transport, minimizing downtime, and reducing maintenance costs. It’s a balance of selecting a belt that is strong enough to withstand the rigors of coal mining while being efficient and cost-effective for the operation.
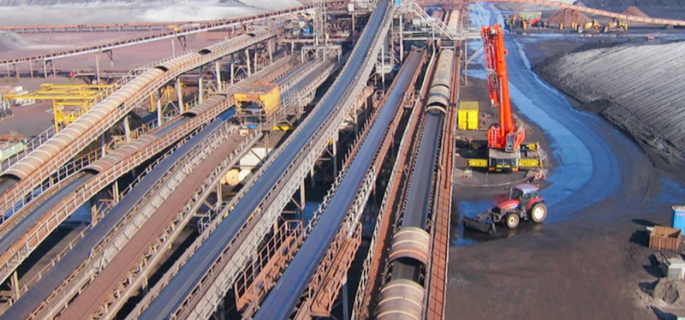
Cost Considerations for Coal Mining Conveyor Belts
Investing in a coal mining conveyor belt system involves a variety of cost considerations that extend beyond the initial purchase price. Understanding these factors is crucial for budgeting and ensuring that the chosen system offers the best value and performance over its lifespan. Below, we discuss eight key factors that influence the cost of coal mining conveyor belts and provide insights into budgeting for these systems.
Factors Affecting Conveyor Belt Price
- Material: The type of material used in the conveyor belt (e.g., rubber, PVC, fabric) significantly impacts its price. High-quality, durable materials that offer enhanced resistance to wear and tear are generally more expensive.
- Size: The length and width of the conveyor belt directly affect its cost. Larger conveyor systems, designed to cover longer distances and carry more coal, require more material and are consequently more expensive.
- Tensile Strength: Belts with higher tensile strength, capable of handling heavier loads without breaking, are typically more costly due to the quality and durability of the materials used.
- Custom Features: Customizations such as special coatings, reinforced edges, or custom cleats to improve load carrying and prevent slippage add to the cost.
- Complexity of the Conveyor System: Advanced systems with integrated sensors, monitoring equipment, and automated controls are more expensive due to the added technology and complexity.
- Brand and Manufacturer: Premium brands and manufacturers known for their quality and innovation may charge more for their conveyor belts, reflecting their reputation and the reliability of their products.
- Installation Requirements: The complexity of installing the conveyor belt, including the terrain, length of the system, and integration with existing operations, can significantly impact the overall cost.
- Operating Environment: Conveyor belts designed for harsh mining conditions, with resistance to abrasion, extreme temperatures, and chemicals, may come at a premium due to the specialized materials and technologies used.
Budgeting Insights for Conveyor Belt Systems
- Initial Purchase: Consider not only the cost of the conveyor belt itself but also any custom features and the reputation of the manufacturer.
- Installation Costs: Factor in the expenses associated with installing the conveyor system, including labor, equipment, and any necessary modifications to the site.
- Maintenance and Repairs: Regular maintenance is essential for the longevity of the conveyor belt. Budget for routine inspections, repairs, and replacements of worn parts.
- Energy Consumption: Evaluate the energy efficiency of the conveyor system, as this will impact operational costs over time.
- Downtime Costs: Consider the potential costs associated with unexpected downtime due to conveyor belt failures, including lost production and emergency repair expenses.
- Lifecycle Costs: Look beyond the initial purchase and installation costs to consider the total cost of ownership, including maintenance, energy use, and expected lifespan.
- Safety and Compliance: Ensure that the conveyor belt meets all safety standards and regulations, as non-compliance can result in fines and increased costs.
- Financing Options: Explore financing options that may be available to spread out the cost of the conveyor system, making it more manageable for your budget.
By carefully considering these factors and insights, coal mining operations can make informed decisions when investing in conveyor belt systems, ensuring they select a system that provides the best balance of performance, durability, and cost-effectiveness.
Coal Conveyor Systems in Thermal Power Plants
In the realm of thermal power plants, the coal mining conveyor belt system plays a crucial role in the continuous and efficient transport of coal, which is the backbone of electricity generation. These systems are engineered to meet the high-volume and constant demand for coal, ensuring that power plants operate smoothly and reliably. Below, we delve into seven key roles of coal conveyor systems in thermal power plants and highlight specific requirements and challenges these systems face in such settings.
Roles of Coal Conveyor Systems in Thermal Power Plants
- Continuous Coal Supply: Conveyor belts provide a continuous flow of coal to the boilers, ensuring that there is always enough fuel to generate electricity.
- Efficient Handling of Bulk Coal: These systems are designed to handle large volumes of coal efficiently, minimizing the time and labor required to move coal from storage to the boilers.
- Cost-Effective Transportation: Conveyor belts offer a cost-effective solution for transporting coal over short to medium distances within the power plant, compared to other modes of transport.
- Minimizing Environmental Impact: Enclosed conveyor systems reduce coal dust emissions and minimize the environmental impact of coal transportation within the plant.
- Flexibility in Operation: Conveyor systems can be designed to accommodate the specific layout of a power plant, including changes in elevation and direction, ensuring efficient coal delivery.
- Integration with Coal Processing: Conveyor belts can be integrated with coal processing equipment, such as crushers and screens, to prepare coal for combustion.
- Emergency Fuel Supply: In case of disruptions in coal delivery, conveyor systems can transport coal from emergency storage areas to ensure continuous power generation.
Requirements and Challenges in Thermal Power Plant Settings
- High Reliability: Given the critical role of coal in power generation, conveyor systems must be highly reliable to avoid disruptions in electricity production.
- Large Capacity: Conveyor belts in thermal power plants need to have a large capacity to transport significant amounts of coal to meet the constant demand.
- Resistance to Harsh Conditions: These systems must withstand high temperatures, abrasive coal dust, and other harsh conditions prevalent in power plants.
- Energy Efficiency: Given the large volumes of coal transported daily, conveyor systems must be energy-efficient to minimize operational costs.
- Safety Standards: Conveyor belts must adhere to strict safety standards to prevent accidents, including fire resistance and emergency stop mechanisms.
- Maintenance Accessibility: Easy access for maintenance is crucial to ensure that conveyor systems can be quickly repaired or serviced without significant downtime.
- Environmental Compliance: Conveyor systems must comply with environmental regulations, including dust control measures and noise reduction, to minimize their impact on the surrounding environment.
Coal mining conveyor belt systems in thermal power plants are indispensable for the efficient and continuous supply of coal for electricity generation. These systems are tailored to meet the specific demands and challenges of the power generation industry, ensuring reliability, efficiency, and compliance with safety and environmental standards.
Port Coal Ship Loading Conveyor Belt
Port coal ship loading conveyor belts are specialized systems designed to efficiently and safely transfer coal from storage facilities onto ships for transport. These systems are critical in ensuring the smooth and effective handling of coal at ports. Here are the key components and considerations for such conveyor belt systems:
Key Components of Port Coal Ship Loading Conveyor Belt Systems
Conveyor Belts
- High Tensile Strength Belts: Designed to handle heavy loads and resist wear and tear from abrasive coal.
- Fire-Resistant Belts: Necessary for safety, as coal can be highly flammable.
- Anti-Static Belts: To prevent static electricity buildup, reducing the risk of ignition.
Loaders and Unloaders
- Ship Loaders: Large machines that load coal onto ships. They often have extendable arms and are capable of swiveling to reach different parts of the ship’s hold.
- Hoppers and Feeders: Facilitate the smooth transfer of coal from storage to the conveyor belt.
Transfer Points
- Chutes: Direct coal onto the conveyor belt with minimal spillage and dust generation.
- Skirting and Sealing Systems: Prevent spillage and dust emission at transfer points.
Dust Control Systems
- Dust Suppression Sprays: Reduce dust during the transfer and loading processes.
- Enclosed Conveyor Systems: Prevent coal dust from escaping into the environment.
Belt Cleaners and Scrapers
- Primary and Secondary Belt Cleaners: Ensure the belt is free from coal residue, preventing build-up and reducing maintenance needs.
Idlers and Pulleys
- Carrying and Return Idlers: Support the belt and coal load, ensuring smooth operation.
- Impact Idlers: Absorb the impact at loading points, protecting the belt from damage.
- Drive Pulleys: Provide the necessary traction to move the belt.
- Take-Up Pulleys: Maintain proper tension in the belt.
Safety Systems
- Emergency Stop Mechanisms: Allow for immediate halting of operations in case of an emergency.
- Conveyor Guards: Protect workers from moving parts.
Automation and Monitoring
- Automated Control Systems: Optimize loading efficiency and ensure consistent operations.
- Condition Monitoring: Tracks belt health and performance, alerting operators to potential issues before they cause downtime.
Key Considerations for Designing and Implementing Port Coal Ship Loading Conveyor Belt Systems
- Efficiency: The system must be capable of handling large volumes of coal quickly to keep up with shipping schedules.
- Durability: Materials and components must withstand harsh marine environments, including exposure to saltwater and high humidity.
- Environmental Compliance: Systems must adhere to environmental regulations, particularly regarding dust and spillage control.
- Safety: Comprehensive safety features are essential to protect workers and prevent accidents.
- Maintenance: Easy access for maintenance to minimize downtime and ensure continuous operation.
Port coal ship loading conveyor belts are complex systems that require careful design and robust components to handle the unique challenges of loading coal onto ships. By focusing on efficiency, durability, safety, and environmental compliance, these systems can ensure smooth and effective coal handling operations at ports.
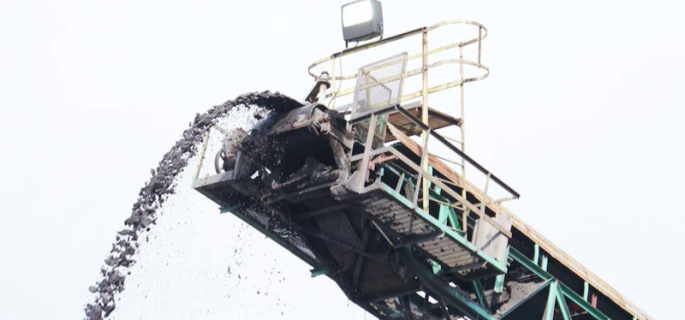
Choosing the Right Conveyor Belt for the Coal Mining Industry
Selecting the appropriate coal mining conveyor belt is pivotal for ensuring operational efficiency, safety, and longevity in the harsh conditions of the mining industry. The right conveyor belt not only enhances productivity but also minimizes downtime and maintenance costs. Below are eight essential guidelines for choosing the most suitable conveyor belt for coal mining applications, followed by the importance of custom conveyor solutions and accessories.
Guidelines for Selecting the Right Conveyor Belt
- Assess Material Characteristics: Consider the type of coal and any other materials the conveyor will transport, including their size, weight, and abrasiveness. This will influence the choice of belt material and design.
- Understand the Operational Environment: Evaluate the mining environment, including the presence of moisture, extreme temperatures, and potentially corrosive conditions, to select a belt that can withstand these challenges.
- Determine Load Capacity Requirements: The conveyor belt must have the appropriate tensile strength to handle the expected load without risk of elongation or breakage.
- Consider Belt Speed: The speed of the conveyor belt should match the operational requirements of the coal mine, ensuring efficient coal transport without causing spillage or accumulation.
- Evaluate Safety Requirements: Safety is paramount in coal mining. Choose conveyor belts with fire-resistant or anti-static properties to reduce the risk of fire or explosions in the mine.
- Account for Maintenance and Durability: Opt for conveyor belts that are durable and easy to maintain, with high-quality materials and construction that minimize the need for frequent repairs or replacements.
- Check for Flexibility and Adaptability: The conveyor belt should be flexible enough to accommodate the mine’s layout, including curves, inclines, and declines, without compromising performance.
- Compliance with Industry Standards: Ensure the conveyor belt meets or exceeds industry standards and regulations, guaranteeing its quality and reliability in coal mining operations.
Importance of Custom Conveyor Solutions and Accessories
- Tailored Efficiency: Custom conveyor solutions are designed to meet the specific needs of a coal mine, optimizing the coal handling process for maximum efficiency.
- Enhanced Safety: Customized features can include safety enhancements like emergency stop systems, guards, and monitoring devices to improve overall mine safety.
- Reduced Downtime: Conveyor systems tailored to the specific conditions of a coal mine are less likely to suffer from unexpected breakdowns, reducing downtime.
- Improved Durability: Custom solutions can be engineered with materials and components that are best suited to the mine’s environment, enhancing the conveyor’s longevity.
- Optimal Material Handling: Accessories like custom chutes, skirts, and scrapers can be added to improve material handling, reduce spillage, and increase the cleanliness of the operation.
- Energy Efficiency: Customized conveyor systems can be designed for energy efficiency, reducing operational costs and the environmental footprint of the mine.
- Scalability: Custom conveyor solutions can be designed with future expansion in mind, allowing for easy modifications and upgrades as the mine’s needs change.
- Integration with Other Systems: Custom conveyors can be seamlessly integrated with other mining equipment and systems, enhancing overall operation efficiency and productivity.
Choosing the right coal mining conveyor belt and investing in custom solutions and accessories are crucial steps in optimizing the coal handling process, ensuring safety, efficiency, and reliability in the demanding environment of the mining industry.
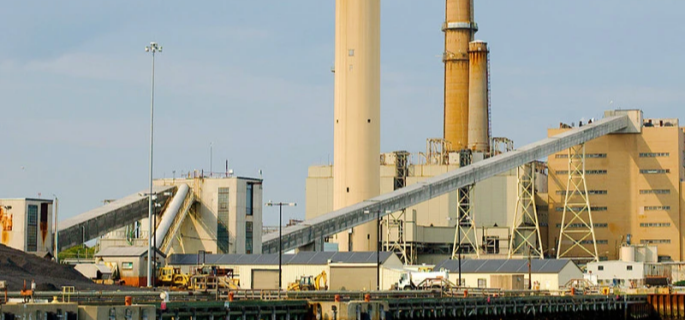
Innovations and Trends in Coal Mining Conveyor Belt Technology
The coal mining industry is witnessing a wave of innovations and trends in conveyor belt technology, driven by the need for safer, more sustainable, and cost-effective operations. These advancements are revolutionizing the way coal is transported within mines, enhancing efficiency and environmental compliance while ensuring the safety of the workforce. Below, we explore recent innovations in coal mining conveyor belt technology and their impact on the industry.
Recent Advancements in Conveyor Belt Technology
- Improved Materials: The development of new, high-performance materials for conveyor belts offers enhanced durability, resistance to abrasion, and reduced maintenance needs. Materials such as ultra-strong fabrics and reinforced rubber compounds are being used to extend the life of conveyor belts in the harsh conditions of coal mining.
- Smart Monitoring Systems: The integration of IoT (Internet of Things) sensors and monitoring devices into conveyor systems allows for real-time tracking of belt health, performance, and operational efficiency. These smart systems can predict maintenance needs, reducing downtime and preventing catastrophic failures.
- Energy-Efficient Designs: Advances in conveyor belt design, including low-resistance belt covers and energy-optimized conveyor rollers, are contributing to significant energy savings. These designs reduce the power consumption of conveyor systems, lowering operational costs and environmental impact.
- Self-Healing Materials: Innovations in self-healing materials for conveyor belts are emerging, where minor cuts and abrasions can be automatically repaired, maintaining the integrity of the belt and extending its service life.
- Advanced Splicing Techniques: New splicing methods and materials are enhancing the strength and durability of conveyor belt joints, a critical aspect for long-distance coal transport. These techniques ensure seamless operation and reduce the risk of belt failure.
- Eco-Friendly Solutions: The trend towards environmentally friendly materials and processes in manufacturing conveyor belts is growing. This includes the use of sustainable materials and the reduction of harmful chemicals in the production process.
- Automated Inspection Systems: The use of drones and robotic systems for the regular inspection of conveyor belts and infrastructure is becoming more common. These automated systems can safely and efficiently identify potential issues before they lead to failures.
- Wear Detection Technology: Advanced wear detection technology enables operators to monitor the wear and tear of conveyor belts in real-time, facilitating proactive maintenance and replacement strategies.
Impact on Coal Mining Operations
These innovations in coal mining conveyor belt technology are making significant contributions to the industry:
- Enhanced Safety: Smart monitoring and automated inspection systems reduce the risk of accidents and injuries by providing early warnings of potential issues.
- Sustainability: Energy-efficient designs and eco-friendly materials minimize the environmental footprint of coal mining operations, aligning with global sustainability goals.
- Cost-Effectiveness: Improved materials and self-healing technologies extend the lifespan of conveyor belts, reducing the frequency and cost of replacements. Smart monitoring also minimizes downtime, enhancing overall operational efficiency.
- Operational Efficiency: Advanced materials and designs ensure that conveyor belts can handle higher loads and operate at optimal speeds, improving the efficiency of coal transportation.
The ongoing innovations and trends in coal mining conveyor belt technology are pivotal in addressing the operational, environmental, and safety challenges faced by the coal mining industry. These advancements are setting new standards for conveyor belt performance, reliability, and sustainability, driving the industry towards more efficient and responsible coal mining practices.
FAQs about Coal Mining Conveyor Belt
In coal mining, several types of conveyors are used, each serving a specific function in the transportation of coal from the mining site to processing facilities or storage areas. The most common type is the belt conveyor, which consists of a continuous belt made from durable materials like rubber, PVC, or synthetic fabrics, moving over a series of rollers. Belt conveyors are favored for their ability to transport large volumes of coal over significant distances, both horizontally and inclined, with high efficiency and speed.
Another type used is the chain conveyor, which utilizes a series of interconnected metal links or plates to move coal, particularly useful in situations where the conveyor path includes sharp angles or requires a heavy-duty solution. Screw conveyors, which use a rotating helical screw blade to move coal, are employed for shorter distances, especially when the material needs to be moved vertically or through tight spaces.
Each type of conveyor is chosen based on the specific requirements of the mining operation, including the distance coal needs to be transported, the terrain, and the volume of coal that needs to be moved.
A coal conveyor belt is a specialized type of conveyor belt designed specifically for transporting coal in mining operations. It is a critical component of the coal handling system, which includes the transfer of coal from the mine to processing plants or storage areas. Coal conveyor belts are engineered to withstand the harsh conditions of mining environments, including exposure to abrasive coal dust, moisture, and varying temperatures.
These belts are made from durable materials that offer high tensile strength and resistance to wear and tear, ensuring they can handle the heavy loads and continuous operation required in coal mining. The design of coal conveyor belts often includes features such as rip and tear resistance, fire resistance to minimize the risk of fire in the mine, and anti-static properties to prevent electrical discharges that could ignite coal dust.
In the context of mining, a conveyor belt is an essential piece of equipment used for the continuous transport of materials, such as coal, ore, and other mined resources, from the mining site to processing facilities or storage areas. Conveyor belts in mining are designed to handle heavy loads, resist abrasive materials, and operate in challenging conditions, including extreme temperatures and environments with high levels of dust and moisture.
Mining conveyor belts are made from durable materials like rubber, reinforced with metal or fabric to provide the necessary strength and wear resistance. They can be customized with various features to suit specific mining operations, including specialized coatings for additional durability, cleats for inclined transport, and sidewalls to prevent spillage. The use of conveyor belts in mining significantly improves efficiency, safety, and productivity by providing a cost-effective and reliable method of material transport.
The belt conveyor is the most widely used type of conveyor for moving coal in mining operations. Its popularity stems from its ability to efficiently transport large volumes of coal over significant distances, both horizontally and inclined. Belt conveyors consist of a continuous loop of a durable material, typically rubber, PVC, or a synthetic fabric, stretched between two or more pulleys.
Belt conveyors are favored in coal mining due to their versatility, high capacity, and ability to cover long distances with minimal energy consumption compared to other transportation methods. They can be designed to fit the specific layout of a mining operation, accommodating changes in direction and elevation, and can be equipped with features like variable speed controls to optimize the flow of coal.
Mining conveyor belts can be purchased from manufacturers and suppliers specializing in bulk material handling equipment for the mining industry. These companies offer a wide range of conveyor belts designed to meet the specific needs of mining operations, including coal mining. When looking to purchase a mining conveyor belt, it’s important to consider factors such as the belt’s material, tensile strength, width, and features like fire resistance and durability.
Reputable manufacturers and suppliers can be found through industry directories, trade shows, and mining equipment exhibitions. Many also have an online presence, allowing potential buyers to view product catalogs, technical specifications, and contact information on their websites. It’s advisable to consult with a supplier’s technical team to ensure the chosen conveyor belt meets the specific requirements of your mining operation, including the type of material to be transported, the conveyor’s length and capacity, and the environmental conditions it will operate in.
The Belt Conveyor for Coal in the mining industry is essential for efficient material handling. It facilitates the continuous transportation of coal from the mining site to processing areas, storage facilities, or directly to the power plants. This system enhances operational efficiency by reducing manual labor, minimizing transportation time, and lowering operational costs. Additionally, belt conveyors improve safety by reducing the need for traditional haulage methods, which often pose higher risks of accidents. They are designed to handle large volumes of coal, providing a consistent and reliable means of transport. The use of belt conveyors also supports environmental sustainability by reducing the carbon footprint associated with the transportation process. Overall, belt conveyors are a critical component in the mining industry, ensuring the smooth and efficient movement of coal from extraction to end-use.
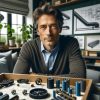
Jordan Smith, a seasoned professional with over 20 years of experience in the conveyor system industry. Jordan’s expertise lies in providing comprehensive solutions for conveyor rollers, belts, and accessories, catering to a wide range of industrial needs. From initial design and configuration to installation and meticulous troubleshooting, Jordan is adept at handling all aspects of conveyor system management. Whether you’re looking to upgrade your production line with efficient conveyor belts, require custom conveyor rollers for specific operations, or need expert advice on selecting the right conveyor accessories for your facility, Jordan is your reliable consultant. For any inquiries or assistance with conveyor system optimization, Jordan is available to share his wealth of knowledge and experience. Feel free to reach out at any time for professional guidance on all matters related to conveyor rollers, belts, and accessories.