Mining Conveyor Project | System Future Trends
In the realm of mining operations, conveyor systems stand as pivotal components, streamlining the movement of materials across various stages of the mining process. The initiation and execution of a mining conveyor project embody a strategic endeavor aimed at enhancing operational efficiency, reducing costs, and fostering innovation within the mining sector. These projects are not merely about installing conveyor belts; they are comprehensive solutions designed to address the multifaceted challenges faced by mining operations. From the drawing board to deployment, each mining conveyor project is a testament to the industry’s drive towards more sustainable and cost-effective material handling solutions. By integrating advanced technologies and adopting innovative practices, mining conveyor projects hold the promise of transforming the landscape of mining operations, making them safer, more efficient, and economically viable in the long run.
The Backbone of Mining Operations: The Role of Mining Conveyor Project
The integration of conveyor systems into mining operations marks a pivotal advancement in the industry, underscoring the essence of mining conveyor projects. These projects not only facilitate the seamless transport of materials but also underscore the critical role of efficient, reliable, and safe material handling solutions in the mining sector. By referencing comprehensive resources like conveyor belt systems mining pdf, one can gain a deeper understanding of how these systems are engineered to meet the rigorous demands of mining environments.
Mining conveyor projects employ a variety of conveyor systems, each tailored to specific operational needs and material characteristics. Among these, five notable types stand out for their widespread application and efficiency:
- Multi-ply Conveyors: Known for their versatility, multi-ply conveyor belts consist of multiple layers of fabric and rubber, making them suitable for transporting a wide range of materials over short to medium distances.
- Straight Warp Conveyors: These conveyors feature belts made from warp and weft yarns, offering higher resistance to tearing and impact, ideal for handling coarse and sharp materials.
- Steel Cord Conveyors: Utilizing steel cables as the belt’s tension element, these conveyors are preferred for their high strength and long-distance capabilities, perfect for deep mine operations.
- Pipe Conveyors: Offering an enclosed transport system, pipe conveyors protect the material and the environment by preventing spillage and dust emissions.
- Cable Belt Conveyors: These utilize a belt supported by steel cables, ideal for very long distance applications, providing high reliability and lower energy consumption.
The importance of these systems in enhancing productivity and safety within mines cannot be overstated. Here are five specific examples illustrating their impact:
- Reduced Operational Downtime: Mining conveyor project streamline the material handling process, significantly reducing the downtime associated with truck haulage and manual handling.
- Enhanced Safety: By automating the transport of materials, conveyors minimize human interaction with hazardous environments, reducing the risk of accidents.
- Increased Productivity: Conveyor systems enable continuous and efficient material flow, increasing the overall productivity of mining operations.
- Lowered Operational Costs: The efficiency and reliability of conveyor systems reduce the need for extensive maintenance and operational costs associated with alternative transport methods.
- Environmental Sustainability: Advanced conveyor systems, such as pipe conveyors, minimize environmental impact by reducing dust emissions and energy consumption.
Mining conveyor projects serve as the backbone of modern mining operations, embodying the industry’s move towards more sustainable, efficient, and safe material handling solutions.
Evaluating Mining Conveyor Project Costs
Understanding the financial aspects of mining conveyor projects is crucial for stakeholders aiming to maximize their investments while ensuring operational efficiency and sustainability. The cost of implementing a mining conveyor project is influenced by a myriad of factors, each contributing to the overall financial planning and decision-making process.
Factors Influencing the Cost of Mining Conveyor Projects
Several key factors play a pivotal role in determining the cost associated with mining conveyor projects:
- Length and Route of the Conveyor: The total length of the conveyor and the complexity of its route, including elevations and turns, significantly affect the cost. Longer conveyors with more complex routes require more materials, labor, and engineering, leading to higher costs.
- Type of Material Being Transported: The characteristics of the material, such as weight, abrasiveness, and corrosiveness, influence the type of conveyor belt needed, impacting the project’s cost.
- Conveyor Capacity and Speed: Higher capacity and speed requirements necessitate more robust and expensive components, including motors and control systems, to handle the increased load and throughput efficiently.
- Environmental and Regulatory Considerations: Projects in environmentally sensitive areas or those subject to stringent regulatory requirements may incur additional costs for compliance, including specialized equipment or mitigation measures.
- Innovations and Technology: Incorporating advanced technologies for automation, monitoring, and safety can increase initial costs but are critical for enhancing efficiency and reducing long-term operational costs.
Balancing Upfront Costs and Long-term Savings
The initial investment in a mining conveyor project often reflects a significant portion of the project’s total cost. However, selecting high-quality, durable components and incorporating advanced technologies can lead to substantial long-term savings. These savings manifest in reduced maintenance requirements, lower energy consumption, and minimized downtime, ultimately contributing to a more cost-effective and efficient mining operation.
Case Studies of Cost-Effective Conveyor Projects
- The Australian Outback Mine: Implemented a high-capacity, long-distance conveyor system, reducing transportation costs by 40% compared to truck haulage.
- The Canadian Arctic Project: Utilized energy-efficient conveyor designs with advanced insulation, significantly lowering energy costs in extreme weather conditions.
- The South American Copper Mine: Integrated real-time monitoring systems to predict maintenance needs, reducing downtime by 25% and maintenance costs by 15%.
- The African Gold Mine: Adopted a modular belt conveyor system, allowing for rapid installation and reducing initial setup costs by 20%.
- The Asian Coal Mine: Implemented a conveyor belt with advanced abrasion-resistant materials, extending the belt’s lifespan and reducing replacement costs by 30%.
These examples highlight the importance of careful planning, innovative design, and strategic investment in mining conveyor project. By understanding and addressing the factors influencing costs, mining operations can achieve a balance between upfront expenditures and long-term operational efficiency, ensuring the financial viability and success of their conveyor projects.
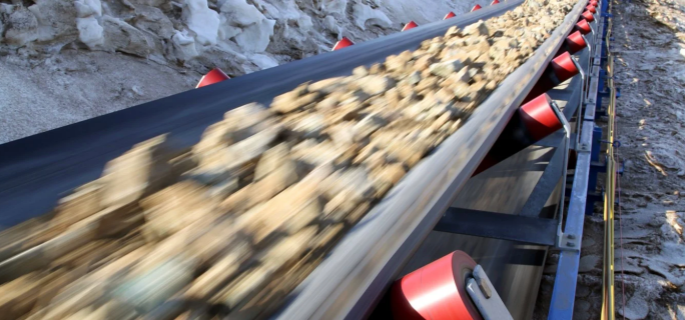
Application Mining Conveyor Project
Mining conveyor systems are vital for efficient material handling in the mining industry. These systems transport bulk materials like ore, coal, and overburden over long distances, improving productivity and safety. This guide outlines the essential aspects of implementing a mining conveyor project, including design considerations, key components, and benefits.
Project Overview
Objectives
- Efficiency: Improve material transport efficiency within the mining site.
- Safety: Enhance safety by reducing manual handling and truck traffic.
- Cost Reduction: Lower operational costs associated with material transport.
Scope
- Material Types: Ore, coal, overburden, and other bulk materials.
- Conveyor Types: Belt conveyors, pipe conveyors, and overland conveyors.
- Distance: Short to long distances, including inclines and declines.
Key Components of Mining Conveyor Systems
Conveyor Belt
- Material: High-tensile steel cords or fabric-reinforced for durability.
- Width: Varies based on material volume and conveyor capacity.
- Cover: Resistant to abrasion, impact, and harsh environmental conditions.
Drive System
- Motors: High-power electric motors to handle heavy loads.
- Gearboxes: Reduce motor speed and increase torque.
- Pulleys: Head and tail pulleys to drive and guide the belt.
Rollers and Idlers
- Troughing Idlers: Support the belt and form a trough shape for material stability.
- Return Idlers: Support the belt on the return path.
- Impact Idlers: Located at loading points to absorb impact.
Frame and Structure
- Material: Steel or aluminum for strength and durability.
- Design: Modular design for easy installation and maintenance.
Belt Cleaners
- Primary and Secondary Cleaners: Remove material adhering to the belt to prevent carryback.
- Plows and Scrapers: Installed at strategic points for effective cleaning.
Safety Features
- Emergency Stops: Easily accessible along the conveyor.
- Guards and Covers: Protect moving parts to prevent accidents.
- Belt Alignment Devices: Prevent belt misalignment and reduce wear.
Design Considerations
Material Characteristics
- Density and Size: Affects belt width, speed, and power requirements.
- Moisture Content: Impacts belt selection and material handling methods.
Capacity and Speed
- Throughput: Determine the volume of material to be transported per hour.
- Belt Speed: Balance speed with material stability and conveyor wear.
Environmental Conditions
- Temperature and Weather: Select materials and components that can withstand extreme conditions.
- Terrain: Design conveyors to navigate inclines, declines, and curves.
Safety and Regulations
- Compliance: Adhere to local and international safety standards.
- Inspection and Maintenance: Design for easy access and regular maintenance.
Benefits of Mining Conveyor Systems
Increased Efficiency
- Continuous and automated material transport reduces downtime.
- High-capacity conveyors handle large volumes of material quickly.
Enhanced Safety
- Reduces the need for manual handling and truck transport.
- Minimizes accidents and improves site safety.
Cost Savings
- Lower operational costs compared to truck haulage.
- Reduced fuel consumption and maintenance expenses.
Environmental Impact
- Lower carbon emissions compared to truck transport.
- Reduced environmental footprint with minimal ground disturbance.
Implementation Steps
Project Planning
- Conduct feasibility studies and site assessments.
- Define project scope, objectives, and timeline.
Design and Engineering
- Create detailed design plans and engineering specifications.
- Select appropriate materials and components.
Procurement
- Source high-quality materials and components from reliable suppliers.
- Ensure timely delivery to meet project timelines.
Installation
- Prepare the site and install conveyor structures.
- Assemble and install conveyor components, ensuring proper alignment and tension.
Testing and Commissioning
- Conduct thorough testing to ensure system functionality.
- Address any issues and optimize performance.
Maintenance and Monitoring
- Implement a regular maintenance schedule.
- Monitor system performance and address wear and tear promptly.
Implementing a mining conveyor system significantly enhances material handling efficiency, safety, and cost-effectiveness in mining operations. By carefully considering design aspects, selecting the right components, and following a structured implementation plan, mining companies can achieve optimal performance and long-term benefits from their conveyor systems.
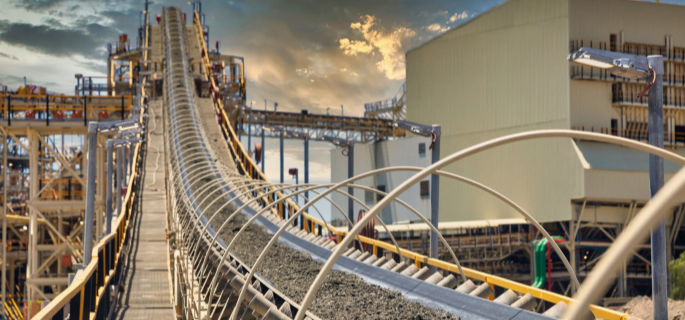
Selecting a Mining Conveyor Project
Selecting the right mining conveyor system is crucial for efficient and cost-effective material handling in mining operations. This guide outlines key considerations and steps to help you choose the best conveyor system for your mining project.
Key Considerations
1. Material Characteristics
- Type of Material: Determine the type of material to be transported (e.g., ore, coal, overburden).
- Density and Size: Assess the bulk density and size of the material, which impact conveyor design and capacity.
- Moisture Content: Consider the moisture content, as it affects material flow and belt selection.
2. Capacity Requirements
- Throughput: Calculate the volume of material to be transported per hour.
- Peak Load: Consider the peak load requirements to ensure the system can handle maximum capacity without issues.
3. Conveyor Length and Path
- Distance: Determine the length of the conveyor, considering both horizontal and vertical distances.
- Terrain: Evaluate the terrain, including inclines, declines, and curves, to design an efficient path.
- Elevation Changes: Account for any elevation changes that may require special conveyor designs.
4. Conveyor Type
- Belt Conveyors: Suitable for long distances and continuous material transport.
- Pipe Conveyors: Enclosed design prevents material spillage and protects against environmental factors.
- Overland Conveyors: Ideal for transporting materials over long distances with minimal environmental impact.
5. Environmental Conditions
- Temperature: Select materials and components that can withstand temperature extremes.
- Weather Conditions: Consider exposure to rain, snow, and wind, which may affect conveyor operation.
- Corrosive Environments: Choose corrosion-resistant materials for operations in harsh environments.
6. Drive System
- Motor Power: Ensure motors have sufficient power to handle the expected load.
- Efficiency: Opt for energy-efficient motors and drive systems to reduce operating costs.
- Control Systems: Incorporate advanced control systems for precise operation and monitoring.
7. Maintenance and Reliability
- Ease of Maintenance: Design the system for easy access to components for routine maintenance.
- Reliability: Choose high-quality components to minimize downtime and ensure long-term reliability.
- Spare Parts Availability: Ensure that spare parts are readily available to reduce maintenance delays.
8. Safety and Compliance
- Safety Standards: Adhere to local and international safety standards and regulations.
- Emergency Systems: Install emergency stop buttons and safety guards to protect workers.
- Training: Provide proper training for operators and maintenance personnel.
Steps to Selecting a Mining Conveyor Project
1. Conduct a Feasibility Study
- Site Assessment: Evaluate the mining site and material handling needs.
- Cost Analysis: Estimate the total cost of the conveyor system, including installation, operation, and maintenance.
- Benefits Analysis: Assess the potential benefits, such as increased efficiency and reduced operating costs.
2. Define Project Requirements
- Scope: Clearly define the scope of the project, including the type and volume of material to be transported.
- Objectives: Establish project objectives, such as improving efficiency, reducing costs, and enhancing safety.
- Timeline: Develop a realistic timeline for project implementation.
3. Select Conveyor Type and Design
- Conveyor Type: Choose the appropriate conveyor type based on material characteristics, distance, and terrain.
- Custom Design: Work with engineers to design a custom conveyor system that meets your specific requirements.
- Component Selection: Select high-quality components, including belts, rollers, motors, and control systems.
4. Procure Materials and Components
- Suppliers: Identify reliable suppliers for conveyor materials and components.
- Quality Control: Ensure that all materials and components meet quality standards and specifications.
- Logistics: Plan for the timely delivery of materials and components to the project site.
5. Installation and Commissioning
- Site Preparation: Prepare the site for installation, including grading and foundation work.
- Installation: Assemble and install the conveyor system according to design specifications.
- Testing: Conduct thorough testing to ensure the system operates correctly and meets performance requirements.
- Commissioning: Officially commission the conveyor system for operation, ensuring all safety protocols are in place.
6. Training and Maintenance
- Operator Training: Provide training for operators on the safe and efficient use of the conveyor system.
- Maintenance Training: Train maintenance personnel on routine maintenance and troubleshooting.
- Maintenance Schedule: Develop and implement a regular maintenance schedule to ensure long-term reliability.
Selecting the right mining conveyor project involves careful consideration of material characteristics, capacity requirements, environmental conditions, and safety standards. By following these steps and focusing on key considerations, you can choose a conveyor system that enhances efficiency, reduces costs, and ensures safe and reliable material handling in your mining operations.
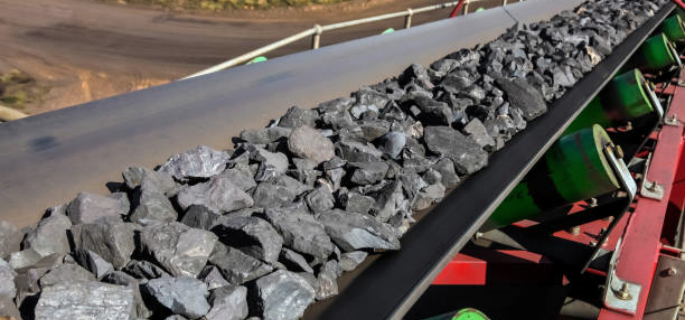
Advancements in Mining Conveyor Project Technologies and Manufacturers
The evolution of mining conveyor project is significantly driven by technological innovations and the contributions of leading manufacturers. These advancements not only enhance the efficiency and sustainability of mining operations but also set new standards for safety and reliability in the industry.
Leading Mining Conveyor Belt Manufacturersc
Several manufacturers stand out for their innovative contributions to mining conveyor project:
- GRAM Conveyor:GRAM Conveyor is known for its high-quality conveyor belt systems used in various mining operations globally.They specialize in designing and manufacturing heavy-duty conveyor belts tailored for mining applications.Their product range includes standard and custom-designed conveyor belts, modular conveyor systems, and related accessories.
- ContiTech: Offers high-end conveyor belting solutions, known for their durability and high performance in extreme mining conditions.
- Bridgestone: Specializes in high-strength, low-stretch conveyor belts that reduce energy consumption and increase long-term savings for mining operations.
- Fenner Dunlop: Pioneers in the development of fire-resistant conveyor belts, enhancing safety in mines prone to fire hazards.
- Phoenix Conveyor Belt Systems: Delivers conveyor belt systems that withstand the test of time in harsh mining environments, focusing on longevity and reliability.
- Sempertrans: Known for their environmentally friendly and energy-efficient conveyor solutions, contributing to sustainable mining practices.
The Role of ABB and Metso in Advancing Mining Conveyor Technology
ABB and Metso have been instrumental in pushing the boundaries of mining conveyor technology:
- ABB Ability™ Conveyor Roller Inspection Services: Utilizes digital solutions to monitor the health of conveyor rollers, predicting failures before they occur and reducing downtime.
- Metso’s Energy-Saving Idlers (ESI): Introduces a unique design that significantly reduces the energy consumption of Metso conveyor Idlers.
- ABB’s Gearless Conveyor Drives: Offer increased efficiency and reliability, with lower maintenance requirements, suitable for long-distance conveyors.
- Metso’s Conveyor Sensors and Analytics: Implement advanced sensors and analytics to optimize conveyor performance and material flow.
- ABB’s Integrated Control and Monitoring Systems: Provide comprehensive control and monitoring capabilities, enhancing operational efficiency and safety.
Innovations in Conveyor Belt Systems
Recent innovations in conveyor belt systems have revolutionized the way materials are transported in mining operations:
- Shuttle Conveyors: Offer flexible material handling by moving along a track, allowing for material discharge at multiple points along the conveyor path.
- Trunk Conveyors: Designed for deep mine applications, these conveyors are built to transport materials from the mining face to the surface efficiently.
- Underground Systems: Utilize advanced materials and engineering to withstand the harsh conditions of underground mining while ensuring safety and reliability.
- Self-Healing Conveyor Belts: Feature materials that automatically repair minor cuts and punctures, reducing maintenance downtime.
- Smart Conveyor Technology: Incorporates IoT and AI to monitor system performance in real-time, predict maintenance needs, and optimize operations.
These technological advancements and the contributions of leading manufacturers are pivotal in the development of mining conveyor project. By embracing innovation, the mining industry can achieve unprecedented levels of efficiency, safety, and environmental sustainability.
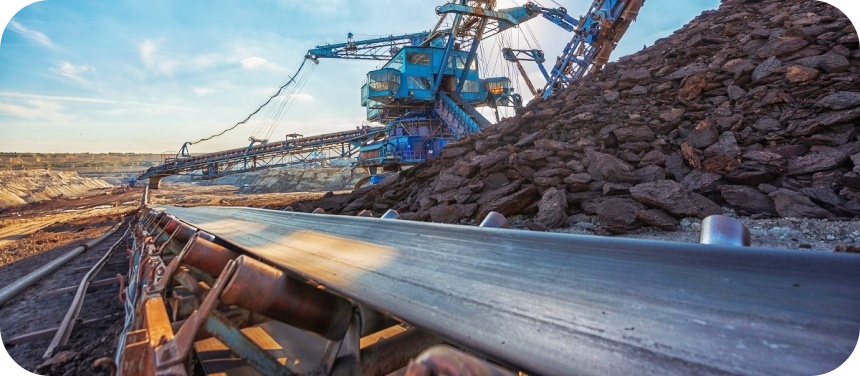
Design and Safety Considerations in Mining Conveyor Project
The design and safety considerations of a mining conveyor project are paramount, directly impacting the system’s durability, efficiency, and safety. These factors are critical in ensuring that the conveyor system not only meets the operational demands of mining activities but also adheres to stringent safety standards to protect workers and the environment.
Significance of Design Concepts
- Material Selection: Choosing the right materials for belts and components can significantly enhance the conveyor’s durability and resistance to harsh mining environments, reducing wear and tear.
- System Redundancy: Incorporating redundancy in critical components of the conveyor system ensures operations can continue smoothly even if one part fails, enhancing overall efficiency and safety.
- Energy Efficiency: Designing conveyors with energy-efficient motors and drives can significantly reduce the operation’s carbon footprint and operational costs.
- Ergonomic Design: Ensuring that the conveyor design considers human interaction, with easy access for maintenance and emergency stops, can greatly enhance safety and operational efficiency.
- Advanced Monitoring Systems: Integrating sensors and monitoring systems to track the health and performance of the conveyor in real-time allows for predictive maintenance, reducing downtime and enhancing safety.
Safety Regulations and Practices
- Conveyor Guarding: Implementing robust guarding around moving parts prevents access to hazardous areas, significantly reducing the risk of injuries.
- Regular Maintenance and Inspections: Scheduled maintenance and inspections ensure that the system operates safely and efficiently, identifying potential issues before they lead to accidents.
- Training Programs: Comprehensive training for all personnel involved in the operation and maintenance of the conveyor system ensures that workers are aware of safety practices and operational procedures.
- Emergency Stop Systems: Installing easily accessible emergency stop mechanisms along the conveyor allows for the quick shutdown of the system in case of an emergency, enhancing worker safety.
- Dust and Spillage Control: Implementing dust suppression systems and spillage controls reduces the risk of respiratory issues and slip hazards, contributing to a safer working environment.
Customizations and Additional Equipment
- Adaptive Belt Cleaners: Custom belt cleaners tailored to the specific type of material being transported can significantly reduce carryback and spillage, improving efficiency and reducing cleanup costs.
- Impact Beds and Skirting: Installing impact beds at loading zones and effective skirting along the belt edges minimizes material spillage and dust, enhancing operational cleanliness and safety.
- Variable Speed Drives: Incorporating variable speed drives allows for the adjustment of belt speed based on the load, improving energy efficiency and reducing wear on the belt.
- Weather Protection: Custom covers and enclosures protect the conveyor from extreme weather conditions, ensuring reliable operation in all climates and reducing weather-related wear.
- Custom Conveyor Configurations: Designing the conveyor layout and configuration to fit the unique topography and spatial constraints of the mining site ensures optimal performance and safety.
Incorporating these design and safety considerations into mining conveyor project not only enhances the system’s performance and longevity but also ensures the safety of personnel and compliance with regulatory standards. Through careful planning and adherence to best practices, mining operations can achieve a balance between operational efficiency and safety.
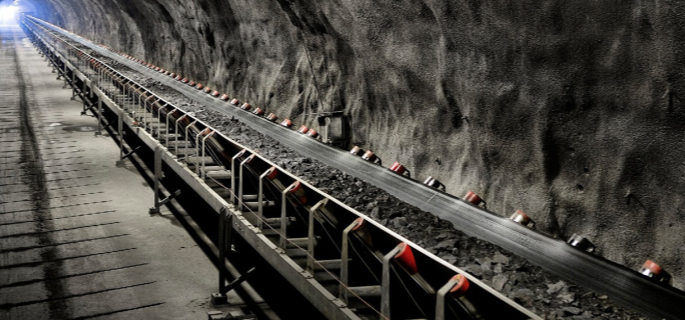
Maintaining the Mining Conveyor Project
Proper maintenance of a mining conveyor system is crucial for ensuring its longevity, efficiency, and safety. This guide provides detailed steps and best practices for maintaining your mining conveyor project to minimize downtime, prevent breakdowns, and optimize performance.
Key Maintenance Areas
Conveyor Belt Maintenance
- Inspection: Regularly inspect the belt for signs of wear, damage, or misalignment.
- Cleaning: Keep the belt clean to prevent material buildup that can cause slippage or tracking issues.
- Tensioning: Ensure the belt is properly tensioned to avoid slippage and premature wear.
- Splicing: Regularly check splices and repair any weak or damaged sections immediately.
Rollers and Idlers Maintenance
- Inspection: Inspect rollers and idlers for wear, misalignment, and proper rotation.
- Lubrication: Lubricate bearings as required to ensure smooth operation and prevent overheating.
- Replacement: Replace any damaged or worn rollers and idlers to maintain smooth conveyor operation.
Drive System Maintenance
- Motor Inspection: Regularly check motors for signs of wear, overheating, and proper operation.
- Gearbox Maintenance: Inspect gearboxes for proper lubrication levels and check for leaks or abnormal noises.
- Belt and Chain Drives: Inspect and maintain belt and chain drives for proper tension and alignment.
Frame and Structure Maintenance
- Structural Integrity: Inspect the frame and supports for signs of wear, corrosion, or damage.
- Alignment: Ensure the frame remains properly aligned to prevent belt tracking issues.
- Bolts and Fasteners: Regularly check and tighten all bolts and fasteners to maintain structural integrity.
Safety Features Maintenance
- Emergency Stops: Test emergency stop buttons and safety switches to ensure they are functioning correctly.
- Guards and Covers: Inspect and maintain all guards and covers to ensure they are secure and in good condition.
- Safety Rails: Ensure safety rails are properly installed and free from damage.
Maintenance Schedule
Daily Maintenance
- Visual Inspection: Conduct a visual inspection of the entire conveyor system.
- Belt Check: Inspect the belt for any signs of wear or damage.
- Roller and Idler Check: Ensure all rollers and idlers are rotating freely and are not damaged.
- Cleaning: Clean any material buildup from the belt and other components.
Weekly Maintenance
- Detailed Inspection: Perform a more detailed inspection of the belt, rollers, idlers, and drive system.
- Lubrication: Lubricate bearings and other moving parts as required.
- Tension Adjustment: Check and adjust belt tension if necessary.
Monthly Maintenance
- Motor and Gearbox Inspection: Inspect motors and gearboxes for proper operation and lubrication levels.
- Structural Check: Inspect the frame and supports for any signs of wear or damage.
- Safety Systems: Test all safety systems, including emergency stops and guards.
Quarterly Maintenance
- Alignment Check: Ensure the conveyor belt and frame are properly aligned.
- Component Replacement: Replace any worn or damaged components, such as rollers, idlers, or belts.
- Performance Testing: Conduct performance tests to ensure the conveyor is operating efficiently.
Annual Maintenance
- Comprehensive Inspection: Perform a comprehensive inspection of the entire conveyor system.
- System Overhaul: Conduct a thorough overhaul, replacing any major components as necessary.
- Safety Audit: Perform a safety audit to ensure compliance with all safety standards and regulations.
Best Practices for Maintenance
Preventive Maintenance
- Implement a preventive maintenance schedule to address potential issues before they cause downtime.
- Keep detailed records of all maintenance activities to track the condition of the conveyor system.
Training and Education
- Provide regular training for maintenance personnel on proper inspection, lubrication, and repair techniques.
- Educate operators on identifying and reporting potential issues.
Use of High-Quality Components
- Invest in high-quality components and spare parts to ensure durability and reliability.
- Source components from reputable suppliers to ensure compatibility and performance.
Regular Upgrades
- Keep up with technological advancements and upgrade components as necessary to improve efficiency and safety.
- Implement software and control system updates to enhance performance and monitoring capabilities.
Maintaining a mining conveyor project involves regular inspections, timely repairs, and adherence to a structured maintenance schedule. By focusing on key maintenance areas and following best practices, you can ensure the longevity, efficiency, and safety of your conveyor system, ultimately enhancing productivity and reducing operational costs in your mining operations.
The Future of Mining Conveyor Project
The landscape of mining conveyor project is rapidly evolving, driven by technological advancements and a growing emphasis on sustainability and efficiency. The future of these systems is marked by several emerging trends that promise to redefine how materials are transported within mining operations.
Emerging Trends in Mining Conveyor Projects
- Automation: The integration of automated systems into mining conveyor parts, such as autonomous operation and self-adjusting belt systems, reduces the need for manual oversight, enhancing efficiency and safety.
- Digital Monitoring (e.g., ABB Ability™): Advanced digital monitoring platforms offer real-time insights into conveyor performance, predicting maintenance needs and optimizing operations for unparalleled efficiency.
- Internet of Things (IoT): IoT sensors embedded in conveyor systems enable precise tracking of material flow, system health, and operational anomalies, facilitating proactive maintenance and operational adjustments.
- Artificial Intelligence (AI) and Machine Learning: AI and machine learning algorithms analyze data from conveyor systems to predict failures, optimize loading and unloading procedures, and improve overall system performance.
- Energy-Efficient Technologies: Innovations such as regenerative braking systems and energy-efficient motors reduce the environmental footprint of mining conveyor project, aligning with global sustainability goals.
Environmental Impact and Sustainability Efforts
The environmental impact of mining conveyors is a critical consideration, with efforts underway to minimize energy consumption and reduce emissions. Sustainable practices include the use of solar power to operate conveyor systems, the development of low-impact materials for belts and components, and the implementation of closed-loop water cooling systems for drive units. These initiatives not only reduce the environmental impact of mining operations but also contribute to cost savings over the long term.
Predictions for Future Developments
The future of mining conveyor technology is poised for significant developments:
- Modular and Flexible Systems: The development of modular conveyor components that can be easily configured and reconfigured to meet changing mining layouts and production needs.
- Advanced Material Technologies: The introduction of new materials for conveyor belts and components that offer increased durability, reduced weight, and lower maintenance requirements.
- Enhanced Integration with Mining Operations: Closer integration of conveyor systems with overall mining operations through advanced software platforms, improving coordination and efficiency.
- Sustainability Innovations: Continued focus on reducing the environmental impact of conveyors, including further advancements in energy efficiency and the use of recycled or sustainable materials.
- Global Standardization of Safety and Performance: The development of global standards for the design, operation, and maintenance of mining conveyors to ensure safety, reliability, and efficiency across the industry.
As mining conveyor project continue to evolve, these trends and predictions highlight a future where efficiency, safety, and sustainability are paramount. The adoption of advanced technologies and practices will not only enhance the operational capabilities of mining conveyors but also ensure they play a pivotal role in the sustainable development of the mining industry.
Your ideal conveyor await. Contact us for details!
Choosing the Right Partner for Your Mining Conveyor Project
Selecting the ideal partner for a mining conveyor project is a critical decision that can significantly influence the project’s success, operational efficiency, and safety. The right partnership ensures that the mining conveyor system is not only designed and installed according to the highest standards but also supported throughout its lifecycle.
Criteria for Selecting Mining Conveyor Belt Manufacturers and Technology Providers
- Experience and Reputation: Look for partners with a proven track record in delivering successful mining conveyor project. Their experience in navigating the complexities of mining operations is invaluable.
- Technological Expertise: Choose providers that lead in technological innovation, offering advanced solutions like digital monitoring systems, energy-efficient drives, and durable materials.
- Customization Capabilities: The ability to customize conveyor systems to meet specific mining conditions and requirements is crucial. Partners should offer tailored solutions that address unique challenges.
- Comprehensive Support Services: Post-installation support, including maintenance, training, and emergency services, is essential. A partner that offers comprehensive after-sales support ensures the long-term success of the project.
- Safety and Environmental Compliance: Partners should demonstrate a strong commitment to safety and environmental standards, ensuring that the conveyor system adheres to regulatory requirements and industry best practices.
The Importance of Reliability, Safety, and Innovation in Vendor Selection
- Reliability: A reliable partner guarantees the delivery of a conveyor system that operates efficiently under the demanding conditions of mining operations, minimizing downtime and maintenance requirements.
- Safety: Safety is paramount in mining operations. Selecting a partner that prioritizes safety features and complies with international safety standards can significantly reduce the risk of accidents and injuries.
- Innovation: A partner that invests in research and development can offer innovative solutions that enhance the efficiency, sustainability, and cost-effectiveness of the conveyor system.
- Adaptability: The mining industry is constantly evolving. A partner that is adaptable and responsive to changes in the industry can help ensure that the conveyor system remains relevant and efficient.
- Global Support Network: A partner with a global support network can provide timely assistance and resources, regardless of the project’s location, ensuring smooth operations and quick resolution of issues.
Enhancing Project Success with Experienced Manufacturers like ABB and Metso
Partnerships with industry leaders such as ABB and Metso can significantly enhance the success of a mining conveyor project. These manufacturers bring a wealth of experience, cutting-edge technology, and a commitment to quality and sustainability. ABB’s advanced digital and automation solutions, combined with Metso’s expertise in durable and efficient conveyor designs, offer mining operations a competitive edge. By leveraging their global presence and comprehensive support services, mining operations can benefit from reduced operational costs, improved safety, and enhanced efficiency.
Choosing the right partner for a mining conveyor project involves careful consideration of the manufacturer’s experience, technological expertise, customization capabilities, support services, and commitment to safety and environmental standards. Partnerships with reputable manufacturers like ABB and Metso can provide valuable benefits, ensuring the project’s success and the long-term sustainability of the mining operation.
FAQs About Mining Conveyor Project
Conveyors in mining are essential pieces of equipment that facilitate the movement of materials from one location to another within mine operations. These systems are designed to transport large volumes of raw materials, processed ores, and waste, efficiently and safely over long distances, including from deep underground to surface levels. The use of conveyors in mining not only increases productivity by automating the transportation process but also reduces the reliance on heavy truck haulage, which can be more expensive and environmentally damaging. Conveyors can be customized to handle a wide range of materials in various environmental conditions, making them a versatile solution for the mining industry. Their implementation can significantly impact the operational efficiency, cost reduction, and environmental sustainability of mining operations.
The three primary types of conveyors used in various industries, including mining, are:
Belt Conveyors: The most common type, belt conveyors consist of continuous belts that loop over a series of rollers or pulleys. They are used for transporting materials over a flat or inclined path and are particularly effective for moving bulk materials over long distances.
Roller Conveyors: These conveyors use a series of rollers mounted on a frame to move items. They are ideal for transporting items with a rigid bottom surface and are commonly used for handling packages or pallets in warehouses but can also be adapted for mining applications, especially for handling mined materials at the surface level.
Chain Conveyors: Chain conveyors use a chain or multiple chains to move pallets or other large, heavy items. They are especially useful in situations where the load needs to be supported from below and are used in mining for moving large pieces of equipment or mined materials that are too heavy for belt conveyors.
Each type of conveyor has its specific advantages and is chosen based on the material to be transported, the transportation distance, and the operational environment.
The thickness of a mining conveyor belt can vary significantly depending on the application, material being transported, and specific operational requirements. Typically, the overall thickness of a mining conveyor belt can range from about 10 mm to 30 mm. This includes the top cover, carcass (which provides the belt’s structural integrity), and the bottom cover. The top and bottom covers protect the carcass from wear and environmental conditions and can vary in thickness based on the conveyor belt’s intended use. For example, belts used for conveying sharp or highly abrasive materials may have thicker covers for added durability and lifespan. The choice of thickness is crucial for ensuring the belt’s performance, longevity, and safety in the demanding conditions of mining operations.
A Z conveyor is a specialized type of conveyor designed to transport materials vertically or at steep inclines in a Z-shaped configuration. This design incorporates horizontal sections at the top and bottom connected by a steep incline or decline section. Z conveyors are particularly useful in facilities where space is limited, as they can efficiently elevate materials without requiring the long horizontal space that would be needed for a standard incline conveyor. In mining, Z conveyors can be used to move materials from underground to the surface or between different levels within a processing plant. They are ideal for handling a wide range of materials, including ores, concentrates, and tailings. The Z configuration helps to maintain the stability of the material being transported, reducing spillage and ensuring a continuous flow of material.
Last Updated on June 21, 2024 by Jordan Smith
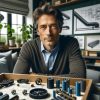
Jordan Smith, a seasoned professional with over 20 years of experience in the conveyor system industry. Jordan’s expertise lies in providing comprehensive solutions for conveyor rollers, belts, and accessories, catering to a wide range of industrial needs. From initial design and configuration to installation and meticulous troubleshooting, Jordan is adept at handling all aspects of conveyor system management. Whether you’re looking to upgrade your production line with efficient conveyor belts, require custom conveyor rollers for specific operations, or need expert advice on selecting the right conveyor accessories for your facility, Jordan is your reliable consultant. For any inquiries or assistance with conveyor system optimization, Jordan is available to share his wealth of knowledge and experience. Feel free to reach out at any time for professional guidance on all matters related to conveyor rollers, belts, and accessories.