What is the Coal Conveyor System: Key Insights
The coal conveyor system is a vital component in various industries, ensuring the efficient and safe transport of coal. These systems play a crucial role in thermal power plants, coal mines, and quarries, facilitating the movement of large quantities of coal with minimal manual labor. In thermal power plants, a coal conveyor system ensures a continuous supply of fuel to the boilers, enhancing energy production efficiency. In coal mines and quarries, these systems streamline the extraction and processing of coal, reducing operational costs and improving safety by minimizing the need for manual handling. The coal conveyor system’s significance in these applications underscores its importance in maintaining seamless industrial operations.
Coal Conveyor System Diagram
Description of a Typical Coal Conveyor System Diagram
A typical coal conveyor system diagram illustrates the various components and their interconnections designed to transport coal efficiently and safely from one location to another. The diagram serves as a blueprint for understanding the layout, operational flow, and integration of different parts within the coal conveyor system. The visual representation helps in identifying the placement of each component and their role in the overall functionality of the system.
Key Components Illustrated in the Diagram
Conveyor Belts
The conveyor belts are the primary component of any coal conveyor system. These belts are made from durable materials capable of withstanding the heavy load and abrasive nature of coal. The belts are designed to move continuously, carrying coal from the loading point to the discharge point. In the diagram, the belts are depicted as long, continuous loops that run over a series of rollers and pulleys.
Pulleys
Pulleys are crucial in guiding and controlling the movement of the conveyor belts. There are two main types of pulleys illustrated in the coal conveyor system diagram: drive pulleys and tail pulleys. The drive pulley is connected to a motor that powers the belt, ensuring it moves at the desired speed. The tail pulley, located at the opposite end of the conveyor, helps to maintain tension and alignment of the belt. Intermediate pulleys may also be present to support the belt and ensure smooth operation.
Motors
Motors are the driving force behind the movement of the conveyor belts. In the coal conveyor system diagram, motors are connected to the drive pulleys, providing the necessary power to move the belts and transport coal. These motors are often equipped with variable frequency drives (VFDs) to control the speed and torque, allowing for adjustments based on the operational needs.
Idlers
Idlers are rollers that support the conveyor belt and the load it carries. They are strategically placed along the length of the conveyor to ensure the belt remains in the correct position and to reduce friction. The diagram typically shows several sets of idlers, including carrying idlers, return idlers, and impact idlers, each serving a specific purpose in maintaining the belt’s integrity and performance.
Tensioning Systems
To ensure the conveyor belt operates smoothly and efficiently, a tensioning system is included in the coal conveyor system diagram. This system maintains the appropriate tension in the belt, preventing slippage and ensuring consistent movement. Tensioning devices can be manual or automatic, adjusting the belt tension as needed to accommodate load variations and operational conditions.
Loading and Unloading Points
The loading and unloading points are critical areas depicted in the coal conveyor system diagram. The loading point is where coal is introduced onto the conveyor belt, typically from a hopper or chute. The unloading point is where coal is discharged from the belt, usually into a storage facility, processing plant, or directly onto another conveyor system. These points are designed to minimize spillage and dust generation, ensuring efficient transfer of coal.
Importance of System Design for Efficiency and Safety
The design of a coal conveyor system is paramount to its efficiency and safety. A well-designed system ensures that coal is transported smoothly, with minimal interruptions and maximum throughput. The diagram highlights the importance of strategic placement of components, such as motors, pulleys, and idlers, to optimize the flow of coal and reduce wear and tear on the equipment.
Efficiency in a coal conveyor system is achieved through the proper selection of belt materials, motor power, and tensioning mechanisms. By choosing the right components, the system can handle the specific requirements of the coal being transported, whether it’s large chunks or fine particles. Additionally, the use of variable frequency drives (VFDs) allows for precise control of the belt speed, enhancing overall efficiency.
Safety is another critical aspect of coal conveyor system design. The diagram illustrates various safety features, such as emergency stop buttons, belt misalignment detectors, and guardrails, which are essential for protecting workers and equipment. Properly designed loading and unloading points also contribute to safety by minimizing the risk of spillage and dust, which can create hazardous working conditions.
Coal Conveyor System Specifications
Detailed Specifications of Coal Conveyor Belts
When it comes to designing and implementing a coal conveyor system, understanding the detailed specifications of the conveyor belts used is crucial. These specifications ensure that the system operates efficiently, safely, and with minimal downtime. Below are the key aspects and specifications of coal conveyor belts.
Materials Used
Rubber
Rubber is one of the most common materials used in coal conveyor belts due to its flexibility, durability, and resistance to wear. Rubber belts are suitable for various coal handling environments, providing a balance between strength and flexibility. They can absorb impacts from the loading of heavy coal chunks and maintain their integrity over long periods of use.
Fabric
Fabric-reinforced conveyor belts are designed to handle high tension and stress. These belts are made by layering multiple fabric materials, such as polyester or nylon, to provide additional strength and flexibility. Fabric belts are particularly useful in applications where the belt needs to navigate complex paths with multiple curves and angles.
Steel Cord
Steel cord conveyor belts offer superior tensile strength and durability. These belts are reinforced with steel cables, making them ideal for heavy-duty applications where high load capacities and long-distance coal transportation are required. Steel cord belts are less prone to elongation and provide a more stable and robust solution for coal conveyor systems.
Key Properties
Tensile Strength
Tensile strength is a critical property of coal conveyor belts, determining their ability to withstand the forces exerted by heavy loads of coal. Belts with higher tensile strength can handle more significant amounts of coal without stretching or breaking, ensuring reliable performance and reducing the risk of mechanical failure.
Abrasion Resistance
Coal conveyor belts must have excellent abrasion resistance to withstand the constant friction and wear caused by the movement of coal. Abrasion-resistant belts last longer and require less frequent maintenance, minimizing operational costs and downtime. This property is particularly important in applications where the belt is exposed to sharp or abrasive coal particles.
Flame Retardancy
Safety is paramount in coal handling operations, and flame retardancy is a crucial property of conveyor belts used in these environments. Flame-retardant belts are designed to resist ignition and prevent the spread of fire, protecting both the equipment and personnel. These belts are typically required in underground coal mines and other high-risk areas.
Examples of Standard and Custom Specifications
Standard Specifications
Standard specifications for coal conveyor belts are designed to meet the general needs of most coal handling applications. These specifications include typical belt widths, tensile strengths, and material compositions that are widely used across the industry. For example, a standard coal conveyor belt might have a width of 800 mm, a tensile strength of 2000 N/mm, and be made of a rubber and fabric composite.
Standard specifications also cover the operating temperature range, ensuring that the belt can perform effectively in both hot and cold environments. These belts are readily available and can be quickly implemented in most coal conveyor systems.
Custom Specifications
Custom specifications are tailored to meet the unique requirements of specific coal handling operations. These specifications might involve variations in belt width, length, material composition, and special properties such as enhanced abrasion resistance or increased flame retardancy. Custom belts are designed to handle unique challenges, such as transporting coal over longer distances, navigating complex conveyor paths, or operating in extreme conditions.
For example, a custom coal conveyor belt might be designed with a width of 1200 mm, a tensile strength of 3000 N/mm, and reinforced with steel cords to handle particularly heavy loads. Additionally, the belt could be treated with a special coating to improve its resistance to chemical exposure or to provide additional flame retardant properties.
Custom specifications also allow for the inclusion of special features such as rip detection sensors, which help prevent catastrophic failures by detecting and alerting operators to any damage or tears in the belt. This level of customization ensures that the coal conveyor system can meet the specific demands of any operation, enhancing efficiency, safety, and reliability.
In conclusion, understanding the detailed specifications of coal conveyor belts is essential for designing a coal conveyor system that is efficient, safe, and reliable. By choosing the right materials and properties, and by considering both standard and custom specifications, operators can ensure their system meets the unique needs of their coal handling operations.
Coal Conveyor System in Thermal Power Plant
Role of Coal Conveyor Systems in Thermal Power Plants
In thermal power plants, the coal conveyor system plays a pivotal role in ensuring the continuous and efficient supply of coal to the boilers. These systems are essential for maintaining the steady flow of fuel necessary for electricity generation. By automating the transportation of coal, conveyor systems significantly enhance the operational efficiency, reliability, and safety of power plant operations.
Detailed Description of the Process from Coal Delivery to Combustion
Coal Delivery
The process begins with the delivery of coal to the thermal power plant. Coal is typically transported to the plant via rail or ship. Upon arrival, the coal is unloaded onto a receiving conveyor belt using heavy machinery like bulldozers or front-end loaders. The receiving belt directs the coal to a storage area or directly to the initial stages of the conveyor system.
Primary Crushing
Before coal is transported further, it must be crushed into smaller, manageable sizes. The primary crusher, located at the beginning of the coal conveyor system, reduces large chunks of coal to a size suitable for the subsequent stages of the process. This crushing step is crucial for ensuring that the coal can be handled efficiently by the conveyor system and the boilers.
Intermediate Conveying
After primary crushing, the coal is transported by intermediate conveyor belts to storage silos or directly to the power plant’s boiler house. These conveyor belts are equipped with numerous safety and monitoring devices, such as belt misalignment detectors, to ensure smooth operation. The intermediate conveyors might also include stages for further crushing and screening to refine the coal size.
Storage and Reclaiming
Once the coal reaches the storage silos, it is temporarily stored until it is needed for combustion. The storage system allows for the management of supply and demand, ensuring that there is always a sufficient reserve of coal available. When coal is needed, reclaimers extract it from the silos and transfer it onto reclaim conveyor belts, which then transport it to the final stage of the process.
Final Conveying and Feeding
The final conveyor belts transport the coal from the storage silos to the boiler feed system. These belts are designed to handle the coal at a controlled rate, ensuring a consistent feed to the boilers. The feed system often includes pulverizers that grind the coal into a fine powder, optimizing it for combustion. The finely ground coal is then blown into the boilers, where it ignites and generates heat for producing steam.
Combustion
In the combustion phase, the finely pulverized coal is burned in the boiler’s combustion chamber. The heat generated from this process converts water into steam, which drives the turbines connected to electricity generators. The efficiency of this entire process heavily relies on the coal conveyor system’s ability to provide a consistent and reliable supply of coal.
Advantages of Using Conveyor Systems in Power Plants
Efficiency
One of the primary advantages of using a coal conveyor system in thermal power plants is the increased efficiency. Conveyor systems automate the transportation of coal, reducing the need for manual handling and thus minimizing delays and labor costs. The continuous movement of coal ensures that the boilers are consistently fed with fuel, optimizing the combustion process and enhancing overall plant efficiency.
Reliability
Coal conveyor systems are designed to be highly reliable, with robust construction and advanced monitoring systems. This reliability ensures minimal downtime, which is critical for power plants that need to operate continuously to meet electricity demands. Features like automated control systems, real-time monitoring, and preventive maintenance programs contribute to the system’s reliability.
Safety
Safety is another significant advantage of coal conveyor systems. By automating the coal transportation process, the systems reduce the risk of accidents associated with manual handling of heavy and potentially hazardous coal. Conveyor systems are equipped with safety devices such as emergency stop buttons, belt alignment sensors, and fire suppression systems, ensuring a safer working environment.
Environmental Benefits
Modern coal conveyor systems are also designed with environmental considerations in mind. Enclosed conveyor belts minimize dust generation and spillage, reducing the environmental impact of coal handling. Additionally, the efficient and controlled transportation of coal helps in reducing the overall carbon footprint of the power plant.
Coal Conveyor System Crossword Clue
Introduction to Common Terminology Related to Coal Conveyors
Understanding the terminology associated with coal conveyor systems is essential for both industry professionals and enthusiasts. These terms not only describe the components and processes involved in coal transportation but also frequently appear in crossword puzzles. Crossword clues often leverage industry-specific jargon to challenge and educate solvers. By familiarizing oneself with common terms related to coal conveyor systems, one can gain a better understanding of the industry and enhance their crossword-solving skills.
Explanation of Popular Crossword Clues and Their Meanings
Crossword puzzles often include clues related to coal conveyor systems, requiring solvers to have knowledge of specific terms. Below are some popular crossword clues along with their meanings:
Term | Letters | Description |
---|---|---|
Belt | 4 | This clue typically refers to the conveyor belt, a continuous loop that transports coal within the system. Conveyor belts are made from durable materials such as rubber, fabric, or steel cord, designed to withstand the heavy load and abrasive nature of coal. |
Pulley | 6 | A pulley is a wheel with a grooved rim that guides and supports the conveyor belt. In coal conveyor systems, there are different types of pulleys, including drive pulleys that move the belt and tail pulleys that maintain tension. |
Idler | 5 | Idlers are rollers that support the conveyor belt and the load it carries. They reduce friction and ensure smooth belt movement. Idlers are strategically placed along the conveyor to maintain the belt's alignment and integrity. |
Motor | 5 | The motor is the power source that drives the conveyor belt. It converts electrical energy into mechanical motion, moving the belt and the coal it carries. Motors are often equipped with variable frequency drives (VFDs) to control speed and torque. |
Chute | 5 | A chute is a channel or slide used for conveying coal from one point to another, often directing coal onto the conveyor belt or from the belt to a storage area or processing unit. Chutes are designed to minimize spillage and dust. |
Silo | 4 | A silo is a tall, cylindrical storage structure used to hold bulk materials like coal. In coal conveyor systems, silos temporarily store coal before it is transported to the next stage of the process. |
Examples of How These Terms Are Used in Industry Contexts
Belt in Industry Context
In a coal conveyor system, the belt is the backbone that supports the entire process. It moves coal from the unloading area to various stages of processing and eventually to the combustion site in thermal power plants. For instance, in a power plant, the belt ensures a continuous supply of coal to the pulverizers, maintaining the steady flow needed for electricity generation.
Pulley in Industry Context
Pulleys play a crucial role in guiding and driving the conveyor belt. The drive pulley, powered by a motor, initiates the movement of the belt, while the tail pulley helps maintain tension, preventing slippage. In mining operations, pulleys ensure that coal is efficiently transported from the extraction site to the processing plant.
Idler in Industry Context
Idlers are essential for reducing friction and supporting the belt. In a coal handling facility, carrying idlers support the loaded side of the belt, while return idlers support the empty side. Impact idlers are placed at loading points to absorb the impact of falling coal, preventing damage to the belt.
Motor in Industry Context
The motor’s role is to provide the mechanical force necessary to move the belt. In large coal conveyor systems, motors with high horsepower and torque are used to handle the substantial load. These motors are often paired with VFDs to allow for precise control of the belt speed, optimizing the coal transportation process.
Chute in Industry Context
Chutes ensure that coal is efficiently transferred from one conveyor belt to another or from the belt to a storage facility. In an industrial setting, chutes are designed to handle large volumes of coal, directing it smoothly to minimize blockages and reduce dust emissions.
Silo in Industry Context
Silos are integral to managing coal supply in large operations. They provide a buffer storage that ensures a steady supply of coal to the processing units, even if there are interruptions in the initial supply chain. In a thermal power plant, silos help maintain the continuous flow of coal to the boilers, ensuring uninterrupted power generation.
Coal Conveyor System Belt Drawing
Importance of Accurate Drawings in the Design and Installation of Coal Conveyor Systems
Accurate drawings are crucial in the design and installation of coal conveyor systems. These detailed representations ensure that all components are correctly sized, positioned, and integrated into the system. Precise drawings help in visualizing the entire conveyor layout, identifying potential issues, and ensuring that the system meets the required specifications for efficiency and safety. For companies like those in the SEO and manufacturing sectors, where precision and efficiency are paramount, having meticulous and well-drafted conveyor belt drawings can significantly reduce installation errors, minimize downtime, and optimize operational performance.
Steps Involved in Creating Detailed Conveyor Belt Drawings
Initial Concept and Requirements Gathering
The process begins with gathering all necessary information and requirements. This includes understanding the specific needs of the coal conveyor system, such as the type of coal being transported, the distance, the elevation changes, and the desired throughput. This step involves close collaboration with engineers, project managers, and stakeholders to ensure all critical factors are considered.
Preliminary Sketches
Once the requirements are clear, preliminary sketches are created. These sketches provide a basic layout of the conveyor system, illustrating the general path the conveyor belt will take. This stage is essential for visualizing the overall design and making any necessary adjustments before moving on to more detailed drawings.
Detailed Design and Component Specification
The next step involves creating detailed drawings of the conveyor belt and its components. This includes specifying the dimensions, materials, and precise locations of each part, such as the belts, pulleys, motors, idlers, and support structures. Each component is meticulously detailed to ensure it fits perfectly within the overall design. For instance, if the coal conveyor system requires a specific type of belt with high abrasion resistance or flame retardancy, these specifications are clearly outlined in the drawings.
Review and Validation
After the detailed drawings are complete, they are reviewed and validated by engineering teams and stakeholders. This review process is critical for ensuring that all design elements are accurate and meet the project requirements. Any discrepancies or potential issues are addressed at this stage to prevent costly changes during installation.
Finalization and Documentation
Once the drawings have been reviewed and validated, the final versions are created. These drawings are then documented and shared with the installation team. Comprehensive documentation ensures that everyone involved in the project has access to the correct and most up-to-date information, facilitating a smooth installation process.
Tools and Software Commonly Used for Drafting Conveyor Belt Designs
Computer-Aided Design (CAD) Software
CAD software is the cornerstone of modern conveyor belt design. Programs like AutoCAD, SolidWorks, and CATIA are commonly used to create detailed and precise drawings. These tools allow designers to create 2D and 3D models of the coal conveyor system, enabling a comprehensive view of the entire design. CAD software provides a range of functionalities, including dimensioning, tolerance analysis, and simulation, which are essential for creating accurate and reliable drawings.
Simulation Software
In addition to CAD tools, simulation software like ANSYS or EDEM is often used to model the behavior of coal within the conveyor system. These simulations help in understanding how coal will flow, identifying potential bottlenecks, and optimizing the design for efficient material handling. Simulation software can also predict wear and tear on components, allowing for better maintenance planning and extending the lifespan of the conveyor system.
Project Management Tools
Project management tools such as Microsoft Project or Primavera are used to coordinate the design and installation phases. These tools help in scheduling, resource allocation, and tracking progress, ensuring that the project stays on time and within budget. Effective project management is crucial for ensuring that all aspects of the conveyor system design are executed flawlessly.
Quarry Conveyor Systems
Specific Requirements and Challenges of Quarry Conveyor Systems
Quarry conveyor systems are essential for the efficient and continuous transportation of extracted materials, such as rocks, sand, gravel, and aggregates. These systems must be robust and durable to withstand the harsh and abrasive conditions of quarry operations. Below are some specific requirements and challenges associated with quarry conveyor systems:
Durability and Wear Resistance
Quarry conveyor systems must be constructed from materials that can endure constant wear and tear from abrasive materials. Conveyor belts often need to be made from heavy-duty rubber with reinforced layers to resist cuts, tears, and impacts from sharp rocks and heavy loads.
Load Capacity
The conveyor system must handle large quantities of materials efficiently. This requires designing belts and support structures that can manage the weight and volume of materials transported daily. The system must also be scalable to accommodate changes in production levels.
Flexibility and Adaptability
Quarries often have complex layouts with varying terrains and elevation changes. Conveyor systems must be flexible and adaptable to these conditions, incorporating features such as incline belts, curved sections, and mobile units to transport materials across different site areas effectively.
Maintenance and Downtime Minimization
Given the continuous nature of quarry operations, minimizing downtime is crucial. Conveyor systems must be designed for easy maintenance and quick repairs. Features such as modular components, easy-access maintenance points, and reliable monitoring systems are essential to ensure minimal operational disruptions.
Comparison of Quarry Conveyor Systems with Coal Conveyor Systems
While both quarry and coal conveyor systems serve the purpose of transporting bulk materials, there are notable differences in their design and operational requirements:
Material Characteristics
Coal conveyor systems are designed to handle coal, which is generally less abrasive than the materials transported in quarries. Consequently, the wear resistance and durability requirements for quarry conveyor belts are typically higher.
Environmental Conditions
Quarry conveyor systems operate in more exposed and rugged environments compared to the relatively controlled conditions of coal conveyor systems in mines and power plants. This exposure necessitates more robust design features to withstand weather extremes, dust, and varying terrain.
System Complexity
Coal conveyor systems often have more complex configurations involving multiple transfer points, screening processes, and storage facilities. In contrast, quarry conveyor systems may focus more on direct transportation from extraction points to processing or stockpile areas, albeit over diverse and challenging terrains.
Examples of Efficient Quarry Conveyor System Designs and Their Benefits
Overland Conveyor Systems
Overland conveyor systems are an efficient solution for transporting materials over long distances in quarries. These systems consist of a series of conveyors that move materials across varied terrains, reducing the need for truck transport. Overland conveyors offer significant cost savings in terms of fuel, labor, and maintenance while minimizing environmental impact by reducing emissions.
Mobile Conveyor Systems
Mobile conveyor systems provide flexibility and adaptability in quarry operations. These systems can be moved and reconfigured as the quarry expands or changes. Mobile conveyors are particularly beneficial for short-term projects or in quarries with multiple extraction sites. They enhance operational efficiency by reducing material handling times and allowing for rapid deployment.
Incline and Decline Conveyors
Incline and decline conveyor systems are designed to transport materials up and down slopes within the quarry. These systems incorporate features such as cleated belts or high-tension rollers to ensure materials are securely moved without spillage. Incline conveyors enable efficient material transfer from deep pits to surface processing plants, optimizing resource extraction.
Conveyor System Automation
Integrating automation into quarry conveyor systems enhances efficiency and reduces labor costs. Automated systems use sensors and control software to monitor and adjust conveyor operations in real-time. Automation can optimize material flow, detect and resolve issues promptly, and provide valuable data for predictive maintenance, further minimizing downtime.
Benefits of Efficient Quarry Conveyor System Designs
Efficient quarry conveyor systems offer several benefits:
- Cost Reduction: Efficient conveyor systems reduce the need for manual labor and heavy machinery, leading to significant cost savings in fuel, maintenance, and labor.
- Increased Productivity: By ensuring continuous and reliable material transport, conveyor systems boost overall productivity and operational efficiency.
- Environmental Benefits: Conveyor systems reduce the reliance on trucks, lowering greenhouse gas emissions and minimizing environmental impact.
- Enhanced Safety: Automated and well-designed conveyor systems reduce the risk of accidents and injuries associated with manual material handling and truck operations.
Iron Ore Conveyor Systems
Role of Conveyor Systems in Iron Ore Mining and Processing
Conveyor systems play an integral role in iron ore mining and processing, facilitating the efficient and continuous movement of ore from the extraction site to processing facilities and storage areas. In iron ore mining, conveyor systems are used to transport ore from the mine to the processing plant, where it undergoes crushing, screening, and beneficiation to produce market-ready iron ore. These systems are essential for minimizing manual handling, reducing transportation costs, and ensuring the smooth flow of materials through various stages of production.
The use of conveyor systems in iron ore mining helps to streamline operations by automating the movement of ore, reducing the need for heavy trucks and the associated fuel and maintenance costs. Additionally, conveyor systems contribute to safer working conditions by minimizing the risk of accidents related to manual material handling and vehicle traffic. Overall, conveyor systems enhance productivity and operational efficiency, making them a critical component in the iron ore industry.
Differences Between Iron Ore and Coal Conveyor Systems
While both iron ore and coal conveyor systems are designed to transport bulk materials, there are significant differences in their design and operational requirements due to the distinct characteristics of the materials they handle.
Aspect | Iron Ore Conveyor Systems | Coal Conveyor Systems |
---|---|---|
Material Characteristics | Iron ore is denser and more abrasive than coal, necessitating stronger and more durable conveyor belts. These belts must withstand high tensile stress and resist wear and tear caused by sharp, heavy ore particles. | Coal is lighter and less abrasive, so the conveyor belts do not require as high a degree of reinforcement. |
Environmental Conditions | Iron ore mining environments are harsher, with greater exposure to extreme weather conditions, moisture, and corrosive elements. Conveyor systems must incorporate materials and coatings that prevent corrosion and degradation. | While exposed to harsh conditions, coal conveyor systems may not face the same level of environmental stress as iron ore conveyor systems. |
System Complexity | Iron ore conveyor systems are more complex due to the extensive processing iron ore undergoes before becoming a finished product. These systems often include multiple stages of crushing, screening, and separation, requiring a more intricate arrangement of conveyors and related equipment. | Coal conveyor systems may involve fewer processing stages, resulting in a simpler system design. |
Key Features and Specifications of Iron Ore Conveyor Belts
High Tensile Strength
Iron ore conveyor belts must possess high tensile strength to support the heavy weight of the ore and the long distances over which it is transported. These belts are typically reinforced with steel cords or multiple layers of high-strength fabric to ensure they can handle the substantial loads without stretching or breaking.
Abrasion and Impact Resistance
Given the abrasive nature of iron ore, conveyor belts must be designed to resist wear and impact. Belts made from durable rubber compounds enhanced with abrasion-resistant additives are commonly used. This design ensures that the belts can endure the constant friction and impact from the ore without suffering significant damage.
Corrosion Resistance
Iron ore conveyor systems often operate in environments where moisture and other corrosive elements are present. To prevent corrosion and extend the lifespan of the conveyor components, belts and other parts are treated with special coatings or made from corrosion-resistant materials such as galvanized steel or stainless steel.
Heat Resistance
In some iron ore processing operations, high temperatures can be encountered, particularly near furnaces and other heat-generating equipment. Conveyor belts used in these areas must be heat-resistant to prevent degradation and maintain their performance under thermal stress.
Custom Design Features
Iron ore conveyor systems are often custom-designed to meet the specific requirements of a mining operation. This includes tailored belt widths, lengths, and inclines to accommodate the unique layout and material handling needs of the site. Additionally, features such as dust suppression systems, belt cleaners, and automatic tensioning devices are integrated to enhance the efficiency and reliability of the system.
FAQs about Coal Conveyor System
What is a coal conveyor?
What are the three types of conveyor?
What is the angle of a coal conveyor belt?
What is the speed of a coal conveyor belt?
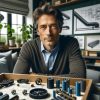
Jordan Smith, a seasoned professional with over 20 years of experience in the conveyor system industry. Jordan’s expertise lies in providing comprehensive solutions for conveyor rollers, belts, and accessories, catering to a wide range of industrial needs. From initial design and configuration to installation and meticulous troubleshooting, Jordan is adept at handling all aspects of conveyor system management. Whether you’re looking to upgrade your production line with efficient conveyor belts, require custom conveyor rollers for specific operations, or need expert advice on selecting the right conveyor accessories for your facility, Jordan is your reliable consultant. For any inquiries or assistance with conveyor system optimization, Jordan is available to share his wealth of knowledge and experience. Feel free to reach out at any time for professional guidance on all matters related to conveyor rollers, belts, and accessories.