Trough Belt Conveyor Design Tips
Trough belt conveyor design is crucial for efficient bulk material handling in various industries. An effective design ensures that the conveyor system can handle large volumes of material with minimal spillage and maximum efficiency. Key considerations in trough belt conveyor design include selecting the appropriate trough angle, choosing the right belt width and speed, and ensuring proper alignment and support. The design should also account for the type of material being transported, its density, and flow characteristics. By focusing on these factors, you can optimize the performance and durability of your conveyor system, ensuring smooth operation and reduced maintenance costs.
Trough Belt Conveyor Design
A trough belt conveyor is a type of conveyor belt system designed to transport bulk materials in a continuous manner. It is widely used in various industries such as mining, agriculture, and manufacturing due to its efficiency and ability to handle large volumes of materials over long distances.
Key Components and Structure:
Belt:
- The conveyor belt is the main component and is typically made from a durable material such as rubber, PVC, or fabric. The belt is designed to be flexible yet strong enough to withstand the load of the materials being transported.
- The belt forms a “trough” shape, which helps to keep the materials centered on the belt and prevents spillage. This shape is achieved through the arrangement of the idlers.
Idlers:
- Carrying Idlers: These are sets of rollers that are positioned beneath the conveyor belt to support the weight of the materials. They are arranged in a triangular pattern, with two outer rollers inclined at an angle and one central roller, to create the trough shape.
- Return Idlers: These support the empty belt on its return journey after the materials have been discharged. They are typically flat since they do not need to maintain the trough shape.
Drive System:
- The drive system includes a motor, gearbox, and drive pulley. The motor powers the conveyor by rotating the drive pulley, which in turn moves the belt.
- The drive pulley is usually located at the discharge end of the conveyor to pull the belt, reducing the load on the motor and improving efficiency.
Tensioning System:
- A tensioning system is essential to maintain the correct belt tension, preventing slippage and ensuring smooth operation. This can be achieved through various mechanisms, such as screw-type tensioners, gravity take-ups, or hydraulic tensioners.
Belt Support and Tracking:
- Proper support is provided along the entire length of the belt to prevent sagging, particularly when transporting heavy materials. Additionally, tracking systems ensure that the belt stays aligned on the idlers and does not drift off-center, which could cause damage and reduce the system’s efficiency.
Load Zone:
- The load zone is the area where materials are loaded onto the conveyor belt. It is designed with features like impact idlers, which are reinforced to absorb the shock of falling materials, and side skirts, which prevent material spillage.
Discharge System:
- At the discharge end, the belt typically passes over a head pulley, where the materials are discharged. Discharge systems can include chutes, hoppers, or other mechanisms to guide the materials to their next destination.
Design Considerations:
Capacity and Speed:
- The design must take into account the volume of material to be transported and the speed at which it needs to move. This is influenced by the belt width, belt speed, and the nature of the material (e.g., density, particle size).
Material Properties:
- The design needs to consider the characteristics of the material being transported, such as abrasiveness, moisture content, and particle size. These factors influence the choice of belt material, idler spacing, and the need for features like cleaning systems.
Conveyor Length and Incline:
- The length of the conveyor and any inclines it must traverse will impact the design, particularly in terms of power requirements and belt tension. Longer conveyors or those with steep inclines may require multiple drive systems or special tensioning mechanisms.
Environmental Conditions:
- The operating environment (e.g., temperature, humidity, dust levels) plays a significant role in the design. For example, conveyors operating in extreme temperatures may require specialized belts, while those in dusty environments may need dust suppression systems.
Safety and Maintenance:
- Safety features such as emergency stop buttons, guards, and safety pull cords are essential. Additionally, the design should facilitate easy maintenance, with accessible components and features like belt cleaners to remove buildup that could cause wear or malfunction.
The design of a trough belt conveyor is a complex process that requires consideration of various factors to ensure efficiency, safety, and longevity. Proper design ensures that the conveyor meets the specific needs of the application while minimizing downtime and maintenance costs.
Key Principles of Trough Belt Conveyor Design
The design of trough belt conveyors is guided by several key principles that ensure their efficiency, reliability, and safety in transporting bulk materials. These principles are critical in achieving a design that meets operational requirements while minimizing maintenance and downtime. Here are the key design principles of trough belt conveyors:
Material Consideration
- Material Characteristics: Understanding the properties of the material being conveyed—such as bulk density, abrasiveness, moisture content, and particle size—is crucial. These characteristics influence the choice of belt material, idler spacing, and overall conveyor design.
- Flowability: The design must accommodate the flow characteristics of the material to prevent clogging or material buildup, especially at loading and discharge points.
Capacity and Speed Calculation
- Throughput Requirements: The conveyor must be designed to handle the maximum anticipated volume of material over a given time period. This involves calculating the belt speed and width required to achieve the desired capacity.
- Belt Width: The belt width is determined based on the size and volume of the material. Wider belts are used for higher capacities or larger materials, while narrower belts suffice for lower capacities or smaller materials.
- Belt Speed: The belt speed must be optimized to balance throughput with the potential for material spillage or excessive wear on the conveyor components.
Trough Angle and Idler Spacing
- Trough Angle: The angle formed by the idlers (typically 20°, 35°, or 45°) determines how the belt forms a trough shape, which helps contain the material. The trough angle must be selected based on the material’s characteristics and the desired capacity.
- Idler Spacing: The distance between idlers must be carefully calculated to provide adequate support to the belt and material load. Closer idler spacing may be required for heavier or more abrasive materials.
Belt Tension and Power Requirements
- Tensioning System: Proper belt tension is essential to prevent slippage and maintain smooth operation. The tensioning system, whether manual, gravity, or hydraulic, must be capable of maintaining consistent tension under varying loads.
- Drive Power: The power required to move the belt is calculated based on factors such as conveyor length, material load, belt speed, and incline. The motor and gearbox must be adequately sized to handle these requirements, ensuring efficient operation without overloading the system.
Loading and Discharge Considerations
- Loading Zones: The design of the loading zone is critical to avoid material spillage and belt damage. Features like impact idlers, side skirts, and load chutes help control the material flow onto the belt.
- Discharge Mechanisms: At the discharge end, the design should ensure that material is effectively transferred off the belt with minimal spillage or dust generation. This might involve the use of plows, scrapers, or hoppers.
Belt Tracking and Alignment
- Tracking Systems: Belt tracking mechanisms are necessary to ensure that the belt remains centered on the idlers throughout its operation. Misalignment can lead to belt damage, increased wear, and material spillage.
- Alignment Monitoring: Continuous monitoring and adjustments, either manually or through automated systems, help maintain proper belt alignment.
Environmental Adaptations
- Corrosive Environments: For conveyors operating in harsh environments (e.g., exposure to chemicals, salt, or moisture), materials and coatings that resist corrosion are essential.
- Dust and Spillage Control: Dust suppression systems, such as covers, enclosures, or water sprays, help manage dust generation, particularly in dry or windy conditions. Additionally, containment features like skirts and seals prevent material spillage.
Maintenance and Accessibility
- Ease of Maintenance: The conveyor design should allow easy access to components for routine maintenance. Features like removable covers, accessible idlers, and easy-to-replace belts reduce downtime and maintenance costs.
- Component Durability: Selecting high-quality, durable components can extend the life of the conveyor and reduce the frequency of maintenance.
Safety Considerations
- Safety Guards and Emergency Stops: The design must incorporate safety guards around moving parts and emergency stop mechanisms to protect workers.
- Risk Assessment: Conducting a thorough risk assessment during the design phase helps identify potential hazards and incorporate safety features to mitigate these risks.
Cost Efficiency
- Material and Component Selection: The design should strike a balance between cost and performance, ensuring that materials and components are chosen for their durability and suitability for the application without unnecessary overengineering.
- Energy Efficiency: Designing the system to minimize power consumption, such as through optimized belt speed and reduced friction, can lead to significant cost savings over the conveyor’s operational life.
Idler Spacing
The spacing of idlers along the conveyor belt is critical to providing adequate support. Closer idler spacing is used in areas with heavy loads or where the material being transported is particularly dense. Proper idler spacing ensures that the belt remains stable and prevents sagging, which can lead to belt misalignment and increased wear.
Drive and Tension Systems
The drive system, typically powered by electric motors, must be robust enough to handle the conveyor’s load. Proper tensioning mechanisms are essential to maintain belt alignment and prevent slippage. The drive and tension systems work together to ensure smooth and efficient operation, reducing the risk of downtime and maintenance issues.
By adhering to these key design principles, engineers can create trough belt conveyors that are efficient, reliable, and safe for their intended applications.
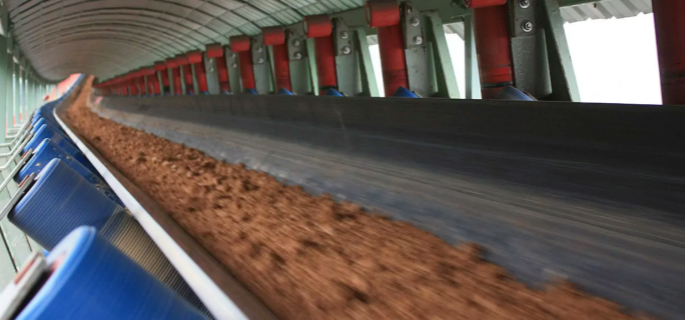
Features of Trough Belt Conveyor Design
Key Features of Roller Bed Belt Conveyors:
- Roller Configuration: The rollers can be configured in various ways to support the belt and the load it carries. Common configurations include straight rollers, tapered rollers, and crowned rollers, each serving a specific purpose in guiding and supporting the belt.
- Material Handling Capability: Roller bed belt conveyors are suitable for handling a wide range of materials, from light to heavy loads. The rolling surface reduces the friction between the belt and the conveyor, allowing for smoother movement and reduced wear.
- Flexibility: These conveyors can be designed to accommodate different belt widths and lengths, making them versatile for various industrial applications. They can also be customized to include additional features such as side guides and belt cleaners.
The design of a trough belt conveyor incorporates several key features that ensure its effectiveness in transporting bulk materials. These features contribute to the conveyor’s reliability, efficiency, and safety. Below are the primary features of trough belt conveyor design:
1. Trough Shape
- Triangular Configuration: The belt is supported by three idlers arranged in a triangular configuration, creating a trough shape. This design helps to center the material on the belt, reducing the risk of spillage and ensuring a steady flow of materials.
- Adjustable Trough Angle: The trough angle, typically 20°, 35°, or 45°, can be adjusted depending on the nature of the material being conveyed. A steeper angle increases the conveyor’s capacity to handle larger volumes of material.
2. Belt
- Durable Materials: The belt is typically made from materials like rubber, PVC, or reinforced fabric, designed to withstand the wear and tear of handling bulk materials. The choice of material depends on the application, including factors such as material abrasiveness, temperature, and chemical exposure.
- Wide Belt Options: The width of the belt can vary to accommodate different capacities, from narrow belts for small-scale operations to wide belts for large-scale industrial applications.
3. Idlers
- Carrying Idlers: These are arranged in a trough configuration to support the belt and the material load. They reduce friction and wear on the belt, enhancing its lifespan and maintaining efficient operation.
- Return Idlers: Positioned on the return side of the conveyor, these idlers support the empty belt on its return journey. They are typically flat since there is no need to maintain the trough shape on the return path.
4. Drive System
- Powered Drive Pulley: The drive system includes a motor, gearbox, and drive pulley, which provides the necessary power to move the belt. The drive pulley is usually positioned at the discharge end of the conveyor to pull the belt, enhancing efficiency and reducing the load on the motor.
- Variable Speed Control: Some designs include a variable speed drive, allowing operators to adjust the belt speed to match the material flow rate or other operational requirements.
5. Tensioning Mechanism
- Automatic or Manual Tensioning: To ensure the belt operates without slipping and remains taut, the design includes a tensioning mechanism. This can be a gravity take-up system, hydraulic tensioner, or screw-type tensioner, depending on the specific application.
- Consistent Tensioning: The tensioning mechanism maintains consistent belt tension, which is crucial for preventing slippage and ensuring smooth operation.
6. Loading and Discharge Systems
- Impact Idlers: Positioned in the loading zone, these idlers are designed to absorb the impact of material as it is loaded onto the conveyor. They are typically reinforced to handle heavy loads without damaging the belt.
- Side Skirts and Seals: These features are included in the loading zone to prevent material from spilling off the sides of the belt. Side skirts keep the material contained, while seals help minimize dust generation.
- Discharge Chutes: At the discharge end, chutes guide the material off the belt and into the desired location, whether it’s a hopper, bin, or another conveyor. The design minimizes material drop height to reduce dust and wear on the conveyor.
7. Belt Tracking and Alignment
- Tracking Rollers: To prevent the belt from drifting off-center, tracking rollers or crowned pulleys are used. These components ensure that the belt remains aligned with the idlers throughout its operation.
- Alignment Adjustments: The system may include features that allow for easy adjustment of belt alignment, ensuring optimal performance and reducing wear on the belt edges.
8. Safety Features
- Guarding: Protective guards are installed around moving parts like pulleys and drive systems to prevent accidental contact by personnel, reducing the risk of injury.
- Emergency Stop Mechanisms: Safety pull cords and emergency stop buttons are positioned along the length of the conveyor, allowing operators to quickly stop the conveyor in case of an emergency.
- Belt Misalignment Detectors: These detectors monitor the belt’s position and can trigger an alarm or shut down the system if the belt deviates significantly from its path, preventing damage to the belt and conveyor structure.
9. Maintenance Accessibility
- Easy Access Points: The design often includes easy access points for maintenance activities, such as replacing idlers, cleaning the belt, or adjusting the tension. This minimizes downtime and ensures the conveyor remains in optimal working condition.
- Modular Components: Some designs use modular components that can be easily replaced without dismantling large sections of the conveyor, further reducing maintenance time.
10. Environmental Considerations
- Dust Control Systems: To manage dust generated by the material, especially during loading and discharge, dust control systems such as covers, enclosures, or water sprays are often integrated into the design.
- Corrosion Resistance: In environments where the conveyor may be exposed to corrosive materials or harsh weather, components are selected or treated to resist corrosion, ensuring longevity and reliability.
11. Energy Efficiency
- Optimized Power Usage: The design focuses on minimizing energy consumption by optimizing belt speed, reducing friction, and using energy-efficient motors and drive systems.
- Reduced Power Loss: Features like low-friction idlers and well-aligned components help reduce power loss, ensuring that the conveyor operates efficiently and cost-effectively.
These features collectively contribute to the robust design of trough belt conveyors, making them suitable for a wide range of industrial applications where efficient bulk material handling is required.
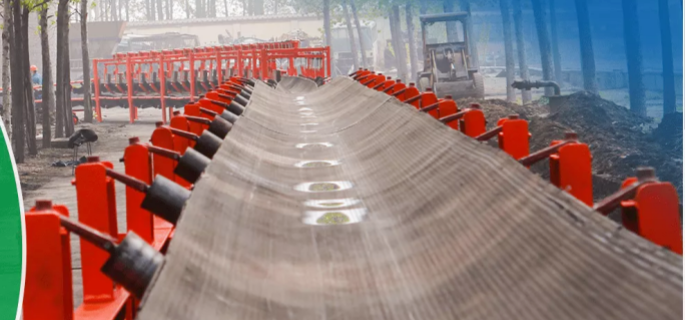
Trough Belt Conveyor Design Applications
Roller bed belt conveyors are designed to provide enhanced support and guidance to the conveyor belt. These conveyors consist of a series of rollers over which the belt travels. The rollers are spaced at regular intervals and are mounted on a solid frame, creating a rolling surface for the belt. This design reduces friction and provides a smooth, stable surface for the belt to move over, which is particularly beneficial in heavy-duty applications.
Heavy-Duty Applications
Enhanced Belt Support
One of the primary advantages of roller bed belt conveyors is the enhanced support they provide to the belt. The rollers create a continuous support surface, reducing the stress on the belt and preventing sagging. This is particularly important in heavy-duty applications where the belt carries substantial loads.
Reduced Friction
The rolling action of the rollers significantly reduces the friction between the belt and the conveyor frame. This reduction in friction leads to lower energy consumption, as less force is required to move the belt. It also minimizes wear on the belt, extending its lifespan and reducing maintenance costs.
Improved Belt Tracking
Roller bed belt conveyors improve belt tracking, which is the ability of the belt to stay aligned with the conveyor. Proper belt tracking is essential to prevent misalignment, which can cause spillage, increased wear, and potential damage to the conveyor system. The rollers guide the belt along the correct path, ensuring smooth and efficient operation.
High Load Capacity
The robust design of roller bed belt conveyors allows them to handle high load capacities effectively. The evenly distributed support provided by the rollers prevents the belt from deforming under heavy loads, ensuring consistent performance and reliability in demanding applications.
Versatility and Customization
Roller bed belt conveyors can be customized to meet the specific needs of different industries. They can be designed with various roller configurations, belt materials, and additional features to optimize performance for specific applications. This versatility makes them suitable for a wide range of uses, from manufacturing and distribution to mining and heavy industry.
Durability and Longevity
The use of high-quality materials and robust construction techniques in roller bed belt conveyors ensures their durability and longevity. These conveyors are built to withstand the rigors of continuous operation in challenging environments, providing reliable service over extended periods.
PDF Resources for Planning and Implementation
Utilizing trough belt conveyor design PDF resources offers several advantages for the planning and implementation of conveyor systems:
Comprehensive Information
Design PDFs provide detailed information on all aspects of trough belt conveyor design, including component specifications, installation guidelines, and maintenance procedures. This comprehensive documentation helps ensure that all design considerations are thoroughly addressed.
Standardization
Design PDFs often adhere to industry standards and best practices, ensuring that the conveyor systems meet regulatory requirements and perform reliably. This standardization helps avoid design flaws and operational issues.
Ease of Access and Sharing
PDF resources are easily accessible and can be shared among team members, contractors, and stakeholders. This facilitates collaboration and ensures that everyone involved in the project has access to the same information.
Customization and Scalability
Many design PDFs offer templates and customizable options that can be tailored to specific project needs. This flexibility allows engineers to adapt the designs to different applications and scale them according to the project’s requirements.
Visualization and Planning
Design PDFs often include diagrams, charts, and illustrations that help visualize the conveyor system. These visual aids are invaluable for planning, enabling engineers to identify potential issues and optimize the design before construction begins.
Training and Reference
Detailed design PDFs serve as valuable reference materials for training personnel on the operation and maintenance of the conveyor system. This ensures that staff are well-equipped to manage the system effectively, reducing the likelihood of operational disruptions.
The Way of Trough Belt Conveyor Design
Designing a trough belt conveyor involves a systematic approach that considers various engineering principles, operational requirements, and environmental factors. The goal is to create a conveyor system that efficiently transports bulk materials while minimizing operational costs, maintenance, and downtime. Below is a comprehensive guide to the way of designing a trough belt conveyor:
Define the Application Requirements
- Material Characteristics: Begin by thoroughly understanding the material to be conveyed. Key factors include bulk density, moisture content, abrasiveness, and particle size. This information will influence decisions regarding the belt material, trough angle, idler spacing, and more.
- Capacity Needs: Determine the required throughput, which is the amount of material to be transported per unit of time. This will dictate the belt width and speed.
- Conveyor Length and Routing: Identify the conveyor length, elevation changes, and routing through the facility. This includes considering any inclines, declines, or horizontal sections.
Select the Belt and Trough Configuration
- Belt Type and Material: Choose a belt material that suits the properties of the conveyed material (e.g., rubber, PVC, steel-reinforced). Consider factors like wear resistance, flexibility, and the environment in which the conveyor will operate.
- Trough Angle: Select an appropriate trough angle (commonly 20°, 35°, or 45°) based on the material’s characteristics and the desired capacity. A larger angle generally allows for higher capacity but may require more robust idlers.
- Belt Width and Speed: Calculate the optimal belt width and speed based on the desired capacity and the material’s bulk density. Wider belts or higher speeds can increase capacity but may also increase costs and power requirements.
Design the Conveyor Structure
- Frame and Support Structure: Design a sturdy frame that can support the conveyor, taking into account the total weight of the material, belt, and idlers. The structure should be designed to minimize deflection and vibration.
- Idler Spacing and Support: Determine the spacing of carrying and return idlers to provide adequate support for the belt and material load. Heavier materials or longer conveyors may require closer idler spacing to prevent sagging.
- Drive and Tensioning System: Select a drive system (motor and gearbox) with sufficient power to move the belt under full load, considering factors like friction, incline, and the length of the conveyor. Implement a tensioning system to maintain proper belt tension, which is critical for preventing slippage and ensuring smooth operation.
Incorporate Loading and Discharge Features
- Loading Zone Design: Design the loading area to minimize impact on the belt and reduce material spillage. This may include impact idlers, side skirts, and loading chutes to control the flow of material onto the belt.
- Discharge Mechanism: Ensure the discharge system efficiently transfers material off the belt, whether through a simple head pulley discharge or more complex systems like plows or trippers for distributing material along the conveyor’s length.
Implement Belt Tracking and Alignment Systems
- Tracking Devices: Incorporate belt tracking systems, such as crowned pulleys or guide rollers, to keep the belt centered on the idlers. Proper tracking is crucial to prevent belt misalignment, which can lead to wear and damage.
- Alignment Monitoring: Design the conveyor with provisions for monitoring and adjusting belt alignment. Automated tracking systems can be particularly beneficial in reducing maintenance needs and prolonging belt life.
Consider Environmental and Operational Factors
- Environmental Conditions: Account for the operating environment, including temperature extremes, moisture, dust, and corrosive elements. This may necessitate the use of specialized materials, coatings, or enclosures to protect the conveyor and maintain efficient operation.
- Energy Efficiency: Design the conveyor to minimize energy consumption, which may involve optimizing belt speed, reducing friction through proper idler and pulley design, and selecting energy-efficient motors.
Ensure Safety and Accessibility
- Safety Features: Integrate safety guards around moving parts, emergency stop devices, and safety pull cords along the length of the conveyor. Conduct a thorough risk assessment to identify potential hazards and incorporate necessary safety measures.
- Maintenance Access: Design the conveyor with maintenance in mind, ensuring that key components like idlers, pulleys, and belts are easily accessible. This can significantly reduce downtime and maintenance costs.
Finalizing Design and Validation
- Detailed Engineering Drawings: Develop comprehensive engineering drawings that detail the conveyor’s dimensions, component specifications, and installation requirements. These drawings should be reviewed and validated for accuracy.
- Simulations and Testing: Use simulations to model the conveyor’s performance under various conditions, ensuring it meets the desired capacity and operates smoothly. If possible, conduct physical testing of a prototype or key components to validate the design.
Installation and Commissioning
- Installation Planning: Plan the installation process carefully, including the layout, assembly sequence, and necessary tools and equipment. Ensure that all components are delivered on-site and that the installation crew is adequately trained.
- Commissioning: Once installed, thoroughly test the conveyor system to ensure it operates according to the design specifications. Address any issues that arise during testing before the system is put into full operation.
Ongoing Maintenance and Optimization
- Maintenance Schedule: Establish a regular maintenance schedule that includes inspection, lubrication, and replacement of worn parts. Regular maintenance is critical to ensuring the longevity and reliability of the conveyor.
- Performance Monitoring: Continuously monitor the conveyor’s performance, looking for signs of wear, misalignment, or inefficiency. Use the data collected to make ongoing adjustments and improvements to the system.
By following these steps, engineers can design a trough belt conveyor that is tailored to the specific needs of their application, ensuring it operates efficiently, safely, and reliably over its intended lifespan.
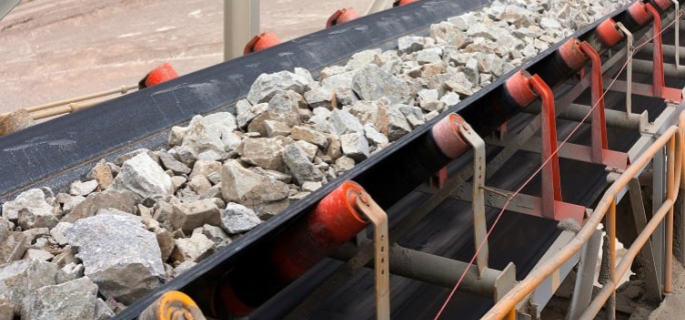
The Types of Trough Belt Conveyor Design
A troughed belt conveyor design is essential for the efficient transport of bulk materials, offering increased capacity and minimized spillage. This type of conveyor forms the belt into a trough shape using idlers or rollers, which helps contain the material and ensures smooth and reliable transportation. Enhancing this design with closed belt conveyor systems can further improve material handling by providing complete containment and protection.
Closed Belt Conveyor Systems
Closed belt conveyor systems are an advanced adaptation of traditional conveyor designs. They are engineered to fully enclose the conveyor belt and the materials being transported, offering several key benefits and specific applications that enhance the overall efficiency and cleanliness of material handling processes.
Explanation of Closed Belt Conveyor Systems
Closed belt conveyor systems, often referred to as tubular or pipe conveyors, feature a belt that is formed into a closed tube or pipe shape. This is achieved by using a series of idlers that wrap the belt into a circular cross-section, creating a fully enclosed environment. The closed design can also be implemented with a protective cover over a flat or troughed belt, ensuring that the material is contained and protected from external elements.
Key Components of Closed Belt Conveyor Systems:
- Enclosed Belt: The belt is either formed into a tubular shape or covered to enclose the material, preventing any spillage and protecting it from contamination.
- Idlers and Rollers: Specially designed idlers and rollers are used to form and support the enclosed belt, ensuring that it maintains its shape and integrity throughout the transport process.
- Sealing Mechanisms: Seals and gaskets are used at the loading and unloading points to maintain the enclosure and prevent material leakage.
- Drive Systems: Efficient drive systems ensure smooth operation, with controls to adjust the speed and tension of the belt as required.
Applications and Advantages of Using Closed Belt Conveyors for Material Containment
Closed belt conveyor systems are particularly beneficial in applications where material containment is critical. They offer several advantages over open conveyor systems, making them ideal for specific industries and uses.
Applications of Closed Belt Conveyors:
Mining and Bulk Material Handling:
- Closed belt conveyors are extensively used in mining operations to transport materials such as coal, ore, and aggregate. The enclosed design prevents material spillage, reduces dust generation, and protects the environment from contamination.
Chemical and Pharmaceutical Industries:
- In the chemical and pharmaceutical industries, closed belt conveyors are used to handle sensitive and hazardous materials. The enclosed environment prevents contamination and ensures the safe transport of chemicals and pharmaceuticals, maintaining their purity and integrity.
Food Processing:
- Closed belt conveyors are ideal for food processing applications where hygiene and cleanliness are paramount. They prevent contamination from external sources and ensure that food products are transported in a clean and controlled environment.
Agriculture:
- In agricultural operations, closed belt conveyors transport grains, seeds, and fertilizers. The enclosed design protects the materials from moisture, pests, and contamination, ensuring quality and reducing waste.
Recycling and Waste Management:
- Closed belt conveyors are used in recycling and waste management to transport recyclables and waste materials. They help contain dust and odors, improving the working environment and efficiency of the recycling process.
Advantages of Using Closed Belt Conveyors:
Material Containment:
- The primary advantage of closed belt conveyors is their ability to completely contain the material being transported. This containment prevents spillage, reduces waste, and maintains a clean working environment.
Environmental Protection:
- Closed belt conveyors protect the environment by preventing dust, debris, and hazardous materials from escaping into the air and surrounding areas. This is particularly important in industries dealing with toxic or harmful substances.
Reduced Maintenance Costs:
- By preventing material spillage and protecting the belt from external contaminants, closed belt conveyors reduce the need for frequent cleaning and maintenance. This leads to lower operational costs and less downtime.
Improved Safety:
- The enclosed design enhances safety by minimizing the risk of material spills and exposure to hazardous substances. This protects workers and reduces the likelihood of accidents and injuries.
Enhanced Efficiency:
- Closed belt conveyors maintain a consistent flow of materials without interruptions caused by spillage or contamination. This improves the overall efficiency of the material handling process and increases productivity.
Protection from External Elements:
- The enclosed design shields the material from weather conditions such as rain, wind, and extreme temperatures. This protection ensures that the material remains in optimal condition throughout its transport.
Versatility:
- Closed belt conveyors are versatile and can be used in various configurations and environments. They can handle a wide range of materials, from fine powders to large aggregates, making them suitable for numerous industrial applications.
The Keys Trough Belt Conveyor Design
The trough belt conveyor design pdf is a fundamental aspect of material handling in various industries. This design is characterized by its ability to form a trough shape, which helps contain and transport bulk materials efficiently. This comprehensive exploration will delve into the applications of trough belt conveyors, highlighting the industries that utilize them and the benefits they offer.
Trough Conveyor Applications
Trough belt conveyors are utilized in a wide range of industries due to their versatility and efficiency in handling bulk materials. Some of the typical industries that benefit from trough belt conveyors include:
Mining and Quarrying
In the mining and quarrying industry, trough belt conveyors are essential for transporting raw materials such as ores, coal, and aggregates. The trough design helps contain these materials, preventing spillage and ensuring smooth transportation from extraction sites to processing facilities.
Agriculture
The agricultural sector relies heavily on trough belt conveyors for handling grains, seeds, and fertilizers. These conveyors facilitate the efficient movement of bulk agricultural products, from storage facilities to processing plants, and are crucial for maintaining the flow of materials during harvesting and post-harvest processing.
Cement and Construction
In the cement and construction industry, trough belt conveyors are used to transport materials like cement, sand, gravel, and other aggregates. The ability to handle heavy and abrasive materials makes these conveyors ideal for this sector, ensuring that materials are moved efficiently to and from production sites.
Food Processing
The food processing industry utilizes trough belt conveyors to handle bulk food products, such as grains, sugar, flour, and other raw materials. These conveyors help maintain the integrity of food products by providing a contained and clean transportation environment, reducing the risk of contamination and spillage.
Power Generation
In power generation plants, trough belt conveyors are used to transport coal and other fuels to boilers and other processing units. The design ensures that these materials are moved efficiently and safely, reducing the risk of spillage and maintaining a steady supply to the plant.
Recycling and Waste Management
Trough belt conveyors play a critical role in recycling and waste management operations. They are used to move recyclable materials, waste products, and other bulk items through various stages of processing and sorting. The containment provided by the trough design helps manage these materials effectively, ensuring efficient processing and reducing environmental impact.
Benefits of Using Trough Conveyors in Various Industrial Settings
The use of trough belt conveyors in various industrial settings offers numerous benefits, including enhanced efficiency, reduced operational costs, and improved material handling. Some of the key benefits include:
Efficient Material Containment
The trough design of these conveyors ensures that bulk materials are contained within the belt, minimizing spillage and loss. This containment is crucial for maintaining a clean and efficient operation, reducing the need for manual cleanup and minimizing material waste.
Versatility in Handling Different Materials
Trough belt conveyors are highly versatile and can handle a wide range of materials, from fine powders to large aggregates. This versatility makes them suitable for various industries, allowing them to transport different types of bulk materials efficiently.
Enhanced Load Capacity
The design of trough belt conveyors allows them to handle heavy loads and large volumes of materials. This increased load capacity ensures that these conveyors can meet the demands of high-volume industrial operations, improving overall productivity and efficiency.
Improved Safety and Reliability
The containment and support provided by the trough design enhance the safety and reliability of these conveyors. By preventing spillage and maintaining the stability of transported materials, trough belt conveyors reduce the risk of accidents and operational disruptions, ensuring a safer working environment.
Cost-Effective Operation
Trough belt conveyors offer a cost-effective solution for bulk material handling. Their ability to transport large volumes of materials with minimal spillage and maintenance reduces operational costs. Additionally, their durability and longevity result in lower replacement and repair costs over time.
Environmental Benefits
By reducing spillage and containing materials within the belt, trough belt conveyors contribute to a cleaner and more environmentally friendly operation. This containment helps minimize the environmental impact of industrial activities, promoting sustainable practices in various industries.
How about Trough Belt Conveyor Design
The trough belt conveyor design is a pivotal innovation in material handling systems, providing efficient transportation of bulk materials by forming the belt into a trough shape. This design increases the carrying capacity and prevents material spillage, making it suitable for transporting loose or granular materials such as grains, coal, ore, and sand. To better understand its advantages, it’s essential to compare trough belt conveyors with flat belt conveyors, highlighting the situations where each type is most effective.
Flat Belt Conveyor vs. Trough Belt Conveyor
Both flat belt conveyors and trough belt conveyors are widely used in various industries, each offering unique benefits and applications. Understanding their differences helps in selecting the right conveyor system for specific needs.
Comparison Between Flat Belt Conveyors and Trough Belt Conveyors
Aspect | Flat Belt Conveyors | Trough Belt Conveyors |
---|---|---|
Design | Flat surface for carrying items. | Belt forms a trough shape, with sides angled upwards. |
Material Handling | Suitable for light to medium loads. | Suitable for handling bulk materials and heavy loads. |
Applications | Ideal for small items, packaged goods, and uniform objects. | Ideal for loose, bulk materials like grains, coal, and minerals. |
Construction | Simpler design, typically with a single flat belt. | More complex, with rollers forming the trough shape. |
Load Capacity | Lower load capacity, typically for lighter materials. | Higher load capacity, can handle larger volumes of material. |
Speed | Generally higher speeds, as it carries lighter loads. | Generally lower speeds due to the heavier and bulkier materials. |
Flexibility | High flexibility, can be used in various configurations. | Less flexible, primarily used for specific bulk material applications. |
Situations Where Each Type is Most Effective and Their Specific Uses
Flat Belt Conveyors
Flat belt conveyors are most effective in situations where the materials being transported are uniform in size, packaged, or need to be handled with care. Here are some specific applications:
- Manufacturing and Assembly Lines: In manufacturing plants, flat belt conveyors are used to transport products between different stages of assembly. Their flat surface ensures that delicate items are handled gently, reducing the risk of damage.
- Packaging and Distribution: Flat belt conveyors are commonly used in packaging and distribution centers to move boxes, packages, and other items along the processing line. Their simplicity and efficiency make them ideal for high-throughput environments.
- Food Processing: In the food industry, flat belt conveyors are used to transport food products through various stages of production. They are designed with food-grade materials and are easy to clean, ensuring hygiene standards are met.
- Airport Baggage Handling: Flat belt conveyors are extensively used in airports for baggage handling systems. They efficiently move luggage from check-in counters to sorting areas and onto the aircraft.
Trough Belt Conveyors
Trough belt conveyors are best suited for transporting bulk materials, especially in industries where material containment and capacity are critical. Here are some specific applications:
- Mining and Quarrying: In mining operations, trough belt conveyors are used to transport bulk materials like coal, ore, and aggregate. The trough design prevents material spillage and ensures efficient transport over long distances.
- Agriculture: In agricultural settings, trough belt conveyors transport grains, seeds, and fertilizers. Their design ensures minimal spillage and protects the materials from contamination, which is crucial for maintaining quality.
- Construction: Trough belt conveyors are used to move construction materials such as sand, gravel, and cement. Their robust construction and ability to handle heavy loads make them ideal for this industry.
- Power Plants: In power plants, trough belt conveyors are used to transport coal to the boilers and to move ash and other by-products away from the combustion area. The containment of materials helps maintain a clean and efficient operation.
- Chemical Processing: In the chemical industry, trough belt conveyors handle various raw materials and finished products. Their enclosed design prevents contamination and ensures the safe transport of potentially hazardous materials.
- Recycling Facilities: Trough belt conveyors are used in recycling facilities to transport materials such as paper, plastic, and metals. The design helps in sorting and processing recyclable materials efficiently.
FAQS about Trough Belt Conveyor Design.
A trough belt conveyor is a type of conveyor system specifically designed to handle bulk materials. It features a belt that is supported by rollers or idlers arranged in a way that creates a concave, trough-like shape. This design helps to keep the materials centered on the belt, preventing spillage and allowing for efficient transport over long distances. Trough belt conveyors are commonly used in industries such as mining, agriculture, construction, and waste management. They are ideal for transporting loose or bulk materials like grain, coal, sand, and waste products. The trough shape can vary in depth depending on the type of material being transported and the specific application requirements.
The capacity of a trough belt conveyor depends on several factors, including the width of the belt, the speed at which the belt travels, the angle of the trough, and the type of material being conveyed. Typically, trough belt conveyors can handle capacities ranging from a few tons per hour to several hundred tons per hour. For example, a conveyor with a belt width of 800 mm and a belt speed of 1.5 meters per second might handle around 300 tons per hour of loose bulk materials. The actual capacity will vary based on the specific design and operational parameters. Understanding these factors and selecting the appropriate specifications is crucial for optimizing the conveyor’s performance and ensuring it meets the operational demands of the application.
The angle of a troughing belt conveyor refers to the angle at which the idlers or rollers are set to form the trough shape. This angle is crucial because it determines how well the belt can contain and transport the bulk materials. Common troughing angles are 20 degrees, 35 degrees, and 45 degrees. A 20-degree angle is typically used for lighter materials or when the conveyor is flat. A 35-degree angle is more standard for most bulk material applications, providing a good balance between material containment and conveyor stability. A 45-degree angle is used for very heavy or abrasive materials, where maximum containment is necessary to prevent spillage. The choice of angle depends on the type of material being transported and the specific requirements of the conveying system.
Designing a belt conveyor involves several key steps to ensure it meets the specific requirements of the application:
Determine the Material and Capacity: Identify the type and amount of material to be conveyed. This will influence the belt width, speed, and capacity.
Select the Belt Width and Speed: Based on the material characteristics and required capacity, choose the appropriate belt width and speed. Wider belts and higher speeds are needed for higher capacities.
Choose the Troughing Angle: Select the appropriate troughing angle (20, 35, or 45 degrees) to ensure proper containment of the material.
Design the Conveyor Structure: Plan the length, height, and incline of the conveyor. Consider the overall layout and how the conveyor integrates with other equipment.
Specify the Drive System: Select the motor and drive system to ensure it can handle the required load and speed.
Include Safety and Maintenance Features: Design features like emergency stops, safety guards, and easy access for maintenance to ensure safe and efficient operation.
Calculate Power Requirements: Determine the power needed to move the belt and the load it carries, taking into account factors like friction, belt tension, and incline.
Plan for Environmental Conditions: Consider factors like temperature, humidity, and exposure to the elements, which can affect the choice of materials and components.
In the mining and heavy industrial sectors, three primary types of conveyor belts are commonly used:
Steel Cord Conveyor Belts: These belts are reinforced with steel cords, making them exceptionally strong and durable. They are ideal for transporting heavy materials over long distances, such as in mining operations where the belt must withstand high stress and harsh environmental conditions.
Textile Reinforced Conveyor Belts: Typically reinforced with layers of synthetic fabrics like polyester or nylon, these belts are used in medium to heavy-duty applications. They offer good flexibility and strength, making them suitable for carrying bulk materials in mining, quarrying, and similar industries.
Chevron Conveyor Belts: Featuring a chevron-shaped pattern on the surface, these belts are designed to handle steep inclines. The pattern helps to prevent material from slipping back, making them effective in transporting loose materials like gravel or sand in mining and construction environments.
Last Updated on August 23, 2024 by Jordan Smith
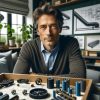
Jordan Smith, a seasoned professional with over 20 years of experience in the conveyor system industry. Jordan’s expertise lies in providing comprehensive solutions for conveyor rollers, belts, and accessories, catering to a wide range of industrial needs. From initial design and configuration to installation and meticulous troubleshooting, Jordan is adept at handling all aspects of conveyor system management. Whether you’re looking to upgrade your production line with efficient conveyor belts, require custom conveyor rollers for specific operations, or need expert advice on selecting the right conveyor accessories for your facility, Jordan is your reliable consultant. For any inquiries or assistance with conveyor system optimization, Jordan is available to share his wealth of knowledge and experience. Feel free to reach out at any time for professional guidance on all matters related to conveyor rollers, belts, and accessories.