Belt Conveyor System Details: Components and Functionality
Belt conveyor system details reveal how these mechanisms are integral to modern industry, facilitating the swift and efficient transportation of goods across various sectors. This overview introduces the foundational elements of belt conveyor systems, highlighting their importance in automating processes and reducing labor costs in industrial applications. By understanding the essential belt conveyor system details, businesses can enhance operational efficiency and adapt to the high demands of production and distribution. This post will delve into the critical components, working mechanisms, and strategic considerations involved in choosing and implementing the right conveyor system for specific industrial needs.
Exploring Belt Conveyor System Details: An In-depth Overview
Definition and Functionality
Belt conveyor systems are a cornerstone of the modern industry, designed for the continuous transportation of goods and materials across varying distances. These systems consist of two or more pulleys, with a continuous loop of carrying medium—the conveyor belt—that rotates around them. One or more of the pulleys are powered, moving the belt and the material on the belt forward. The powered pulleys are known as drive pulleys while the unpowered ones are called idlers.
The essential function of belt conveyor system details lies in their ability to move products efficiently and reliably across production lines, warehouses, and even from one facility to another. This seamless transportation is crucial not only for industries such as mining, agriculture, and manufacturing but also in retail and airport baggage handling. The versatility of conveyor systems allows them to be customized with various belt materials tailored to different environmental conditions and material handling needs, making them indispensable in sectors where quick and effective movement of goods is critical.
Historical Background
The history of conveyor belts is a fascinating journey that mirrors the evolution of industrial technology. The first primitive conveyor belts appeared in the late 18th century, with the basic concepts used primarily in the agricultural and mining industries to move bulk materials. These early belts were typically made of leather or canvas driven by pulleys and were manually operated.
However, the industrial revolution catalyzed significant advancements in conveyor technology. The introduction of steam power in the 19th century, and later, electrical power, transformed conveyor belts from simple manual systems to complex mechanized systems. In 1901, the Swedish engineering company Sandvik invented the first steel conveyor belt, which was more durable and capable of handling heavier loads than its predecessors.
Further innovation occurred in the 20th century with the development of synthetic materials, such as rubbers and polymers, which provided more strength, flexibility, and resistance to environmental factors. These materials revolutionized belt conveyor system details by enabling the design of belts that could be used in diverse environments and for a broader range of applications. Today, modern conveyor belts are highly engineered systems designed with sophisticated materials and capabilities, including sensors and automated controls, that optimize efficiency and safety.
The journey from those early designs to today’s advanced systems highlights the ingenuity and continual progress within the engineering and manufacturing fields. Belt conveyor systems have evolved from basic mechanical components to intricate systems that are integral in various industries around the world. This evolution reflects broader industrial innovations and challenges, emphasizing the continuous need for efficiency and productivity improvements in all sectors of the economy.
As industries continue to demand faster, more efficient, and safer transportation methods for goods and materials, the role of belt conveyor systems is likely to grow. Innovations in materials science and automation technology may lead to the next generation of conveyor systems, which will be even more reliable, efficient, and tailored to specific industrial needs. Understanding these belt conveyor plant details is crucial for anyone involved in the design, operation, or maintenance of these systems, as they provide the critical link in a chain of operations that must run smoothly for optimal production and distribution efficiency.
Detailed Examination of Belt Conveyor System Details: Components and Functions
Components of Belt Conveyor Systems
The intricate workings of belt conveyor systems are made possible by a symphony of various components, each playing a pivotal role in the system’s operation and efficiency. Understanding these components is essential for optimizing the system’s performance and durability. Here, we delve deeper into the main elements that make up belt conveyor system details.
Detailed Parts Overview
- Belts: The belt itself is the most visible part of a conveyor system and is designed to carry the load continuously between two points. The choice of belt material is crucial and can include fabric, rubber, or synthetic materials, depending on the application’s specific needs regarding durability, friction, and resistance to elements such as heat or chemicals.
- Pulleys: These are the wheels over which the belt moves. The main pulleys in a conveyor belt system include the drive pulley, which is powered and moves the belt, and the idler pulleys, which are not powered but support the belt and guide it as necessary. Pulleys are often lined with rubber or other materials to increase friction and grip on the belt.
- Motors: Motors are the driving force behind the conveyor, converting electrical energy into mechanical energy to move the belt. The type of motor can vary based on the required power, speed, and torque, and it is typically connected to a gearbox that moderates the speed of the belt.
- Rollers: Rollers support the belt and contents being transported from the loading point to the discharge point. They reduce the amount of friction that the belt experiences, which can extend the belt’s life and reduce energy consumption.
- Frames: These structures support the rollers, motors, and the conveyor belt itself. Frames need to be robust and are typically constructed from materials like steel or aluminum, which provide the necessary support and alignment to ensure smooth operations.
Functionality of Each Part
- Belts: The primary function of the conveyor belt is to transport material from one point to another. It needs to be sufficiently strong, durable, and flexible to handle various loads and withstand operational stresses without stretching excessively or breaking.
- Pulleys: Drive pulleys are critical for initiating the movement of the belt, transferring the rotational motion from the motor to the belt. Understanding the conveyor belt rubber weight is essential for ensuring that the drive pulleys can handle the load efficiently. Idler pulleys, on the other hand, support the belt’s weight and its load, helping to stabilize and guide the belt as it travels, with the accurate calculation of conveyor belt rubber weight being crucial for optimal performance.
- Motors: The motor’s role is to provide the necessary power to drive the conveyor. The efficiency, speed, and load capacity of the conveyor are directly impacted by the motor’s specifications and performance.
- Rollers: Rollers primarily support the belt and facilitate smooth and efficient movement of goods. They are strategically placed along the path of the conveyor to prevent the belt from sagging and to minimize the contact friction, allowing the belt to move smoothly with less resistance and wear.
- Frames: The frame provides the structural support necessary to hold all the components of the conveyor in the correct alignment and position. It ensures that the system remains stable during operation and is capable of handling the expected loads.
Understanding these belt conveyor system details is crucial for anyone involved in the design, maintenance, or operation of conveyor systems. Each component must be carefully selected and maintained to ensure that the conveyor system functions efficiently and continues to meet the operational demands of modern industries. These details not only highlight the complexity and precision required in designing and operating conveyor systems but also underscore the importance of regular maintenance to avoid breakdowns and extend the lifespan of the conveyor system.
In-depth Analysis of Belt Conveyor System Details: Working Mechanism
Working Mechanism
Understanding the working mechanism of belt conveyor systems is crucial for optimizing their efficiency and functionality. This section breaks down the basic working principle and the various energy sources that can power these systems, providing a comprehensive look into how these complex assemblies operate seamlessly in countless industrial applications.
Basic Working Principle
Belt conveyors operate on a relatively simple principle: a belt made from various materials is set in motion by pulleys that rotate. The process begins with the belt being looped around the drive pulley (or pulleys) that are connected to a motor. As the motor activates, the rotational movement is transferred from the motor to the drive pulley. The friction between the pulley and the belt propels the belt forward, carrying any material placed upon it from the loading point to the unloading point.
The system typically includes at least one or more idler pulleys which are not powered but serve to guide and support the belt as it travels. These pulleys help maintain the belt’s tension and alignment. The entire system is supported by a frame that holds all the components in their proper positions, ensuring that the belt has a smooth path to follow.
For the conveyor to operate efficiently, the belt’s surface, material, and tension must be correctly selected and maintained. The belt’s movement can be controlled in terms of speed and direction, depending on the needs of the application. This controlled movement is what allows conveyor belts to be such an integral part of production lines and material handling systems.
Energy Sources
The operation of belt conveyor systems can be powered by various energy sources, which influence their application and efficiency. The most common sources include:
- Motor-driven: This is the most prevalent source of power for conveyor belts, especially in industrial applications. Electric motors are used to drive the drive pulley, effectively moving the conveyor belt. Depending on the system, the motor might be connected directly to the pulley or through a gearbox that reduces speed and increases torque.
- Gravity: Some conveyor systems are designed to utilize gravity, especially for downward transportation. These systems are usually positioned at a slight decline, and the weight of the materials being transported is enough to move the belt as it goes over the rollers. Gravity conveyors are simple and cost-effective but are limited by the necessity of having a downward path.
- Manual: In smaller or less automated settings, some conveyor belts can be manually operated. These are less common and are typically found in applications where motorized belts are not feasible or necessary. Manual belts require human effort to move goods along the conveyor, which can be labor-intensive and inefficient for larger operations.
Each of these energy sources has its advantages and constraints, and the choice of which to use depends largely on the specific needs of the application, including the desired speed, load capacity, and operational environment. Motor-driven systems offer the greatest flexibility and control, making them suitable for most industrial applications. Gravity systems, while limited, provide a cost-effective solution for certain logistical operations. Manual systems are less common but may be used in specialty applications where simplicity and cost are more critical than efficiency.
Understanding these belt conveyor system details not only aids in selecting the right system for an application but also enhances the ability to troubleshoot, maintain, and optimize the conveyor for prolonged service life and better reliability. This detailed examination of the working mechanism and energy sources of conveyor systems underscores the importance of thoughtful design and configuration in meeting the demanding conditions of modern industrial environments.
Essential Belt Conveyor System Details: Choosing the Right Conveyor System
Selecting the right conveyor system is pivotal for ensuring efficiency, reducing downtime, and optimizing the workflow within various industrial environments. This section discusses the critical considerations needed when choosing the ideal conveyor system, focusing on the materials and products being handled, as well as the specific environmental and spatial challenges that might influence system design and functionality.
Material and Product Considerations
When selecting a conveyor belt system, the characteristics of the materials and products that will be transported are among the most crucial factors to consider. These characteristics can significantly affect the choice of conveyor type, belt material, and system design:
- Type of Material: The nature of the materials—whether they are bulky, heavy, fine-grained, sticky, or hot—affects the type of conveyor belt needed. For example, materials that are hot or have high abrasiveness might require specialized conveyor belts that are heat-resistant and designed to reduce wear and tear.
- Weight of Material: The weight of the products being transported directly influences the design of the conveyor system. Heavier loads require stronger belts with higher load capacities and more robust construction to prevent breakdowns and maintain efficiency.
- Moisture Content: Materials with high moisture content can affect the integrity of certain conveyor belt materials and may require the use of stainless steel components and water-resistant belts to prevent corrosion and slippage.
- Abrasive Characteristics: Materials that are highly abrasive can wear down belt materials quickly. For these types of materials, belts with reinforced fabrics or top-coatings that resist cuts and gouges are preferable to extend the lifespan of the conveyor system.
Understanding these material and product considerations is critical in the selection process, as they ensure the chosen belt conveyor system details are tailored to handle the specific demands of the materials, thereby optimizing both operational efficiency and longevity.
Environmental and Spatial Considerations
The environmental conditions and physical space of the facility where the conveyor system will be installed play a significant role in determining the most suitable conveyor design:
- Environmental Factors: Temperature, humidity, and exposure to chemicals are all environmental factors that can affect conveyor operation. Systems used in cold environments may require materials that maintain flexibility at low temperatures, while those used in wet or corrosive environments might need corrosion-resistant materials like stainless steel or specially coated components.
- Spatial Limitations: The available space within a facility can greatly influence the type and configuration of conveyor systems that can be installed. In facilities with limited space, curved conveyors, vertical conveyors, or even overhead systems may be necessary to maximize the use of available space. Each option comes with its own set of belt conveyor system details that must be considered, such as turning radius for curved conveyors or load capacity for vertical systems.
- Facility Layout: The layout of the plant will determine the path that the conveyor system will follow. Complex layouts may require conveyors with flexible pathing options, such as modular belt conveyors that can easily be configured to navigate around obstacles and through tight spaces.
Considering these environmental and spatial aspects during the conveyor selection process is crucial to ensure that the system not only fits within the operational parameters but also operates efficiently under the specific conditions of the site. By thoroughly evaluating these belt conveyor system or belt conveyor details, businesses can make informed decisions that result in optimal conveyor solutions tailored to their unique industrial needs, ensuring both high performance and cost-effectiveness in their material handling operations.
FAQs about Belt Conveyor System Details
Conveyor belts are engineered systems designed to move materials or objects from one location to another efficiently. The technical specifications of conveyor belts can vary widely depending on their intended use, but common parameters include material, width, thickness, tensile strength, and operating speed. Materials used for conveyor belts might range from rubber and PVC (polyvinyl chloride) to more specialized materials like Kevlar or stainless steel, depending on the demands of the application such as heat resistance or load capacity. Additionally, conveyor belts can be either flat or textured, with the latter helping to increase grip on transported items. Belt length and width are determined based on the load and the distance that needs to be covered by the conveyor system.
A conveyor belt system operates on the principle of two or more pulleys, with a continuous loop of material – the conveyor belt – that rotates around them. One of the pulleys is usually powered, moving the belt and the material on the belt forward. The powered pulley is called the drive pulley while the unpowered one is known as the idler pulley. This system is commonly used in various industries including manufacturing, agriculture, and packaging, for transporting goods over short or long distances. Additional components like motors, belts, and control systems are configured to meet specific handling requirements, ensuring that materials are moved efficiently from one stage of production or processing to another.
The conveyor belt system comprises several key components that work together to transport materials efficiently. These include:
Belt: This is the flexible element of the conveyor that moves the materials.
Pulleys: Typically, there are at least two pulleys in a conveyor belt system – a drive pulley, which is powered and moves the belt, and an idler pulley, which is unpowered.
Motors: These provide the necessary power to the drive pulley.
Rollers: These support the conveyor belt and are spaced throughout the length of the system to ensure that the belt remains in alignment and doesn’t sag.
Frame: This provides the structure that supports the pulleys, rollers, belt, and the material being conveyed. Each component must be precisely engineered and maintained to ensure efficient and reliable operation of the conveyor belt system.
The basic working principle of a belt conveyor system is relatively straightforward and involves the movement of a looped belt along a predefined path. The system typically consists of a belt that is wrapped around two or more pulleys. When at least one pulley is powered, usually by an electric motor, the friction between the belt and the pulley causes the belt to move. This movement transports the material placed on the belt from one point to another. The belt’s motion can be controlled in terms of speed and direction to suit specific tasks within a production process. Additionally, the efficiency and effectiveness of a conveyor belt system depend on proper loading, regular maintenance, and the suitability of the belt material for the specific task.
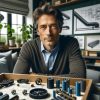
Jordan Smith, a seasoned professional with over 20 years of experience in the conveyor system industry. Jordan’s expertise lies in providing comprehensive solutions for conveyor rollers, belts, and accessories, catering to a wide range of industrial needs. From initial design and configuration to installation and meticulous troubleshooting, Jordan is adept at handling all aspects of conveyor system management. Whether you’re looking to upgrade your production line with efficient conveyor belts, require custom conveyor rollers for specific operations, or need expert advice on selecting the right conveyor accessories for your facility, Jordan is your reliable consultant. For any inquiries or assistance with conveyor system optimization, Jordan is available to share his wealth of knowledge and experience. Feel free to reach out at any time for professional guidance on all matters related to conveyor rollers, belts, and accessories.