Mining Conveyor Belt Maintenance Safety Checklist
In the vast and complex world of mining, conveyor belts stand as the lifelines of operations, seamlessly transporting materials across various stages of production. These belts not only expedite the movement of ores and minerals but also significantly reduce labor costs and enhance safety. However, the efficiency of these indispensable systems hinges on rigorous and consistent mining conveyor belt maintenance. Despite their robustness, conveyor belts are susceptible to a host of challenges, including wear and tear, misalignment, and blockages, which can disrupt mining operations and lead to substantial financial losses. Recognizing and addressing these maintenance challenges is crucial for sustaining the high productivity and safety standards essential in the mining industry.
The Essential Role of Mining Conveyor Belt Maintenance
In the realm of mining, conveyor belts stand as the lifeline of operations, transporting materials and ores over vast distances efficiently and continuously. Their critical role in mining operations cannot be overstated, as they contribute significantly to the overall productivity and safety of mining sites. This underscores the paramount importance of diligent mining conveyor belt maintenance.
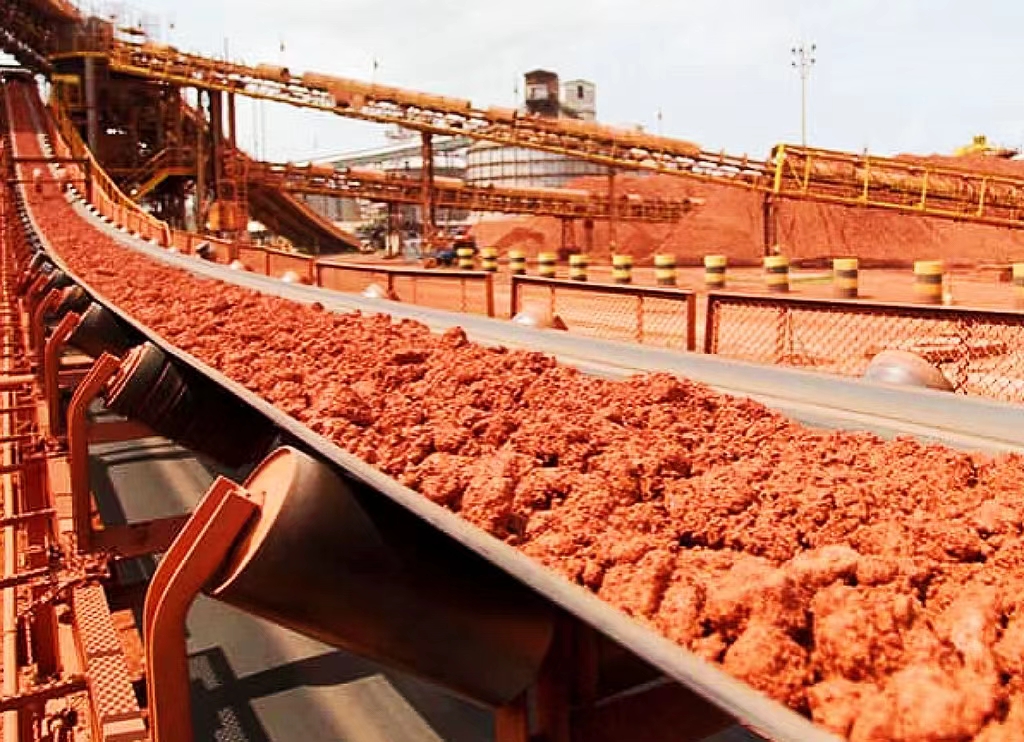
Mining conveyor belt maintenance plays a vital role in ensuring operational efficiency and safety in several ways:
- Preventing Unscheduled Downtime: Regular maintenance identifies potential issues before they lead to failures, minimizing unexpected interruptions that can significantly impact productivity and deadlines.
- Extending Equipment Lifespan: By addressing wear and tear proactively, maintenance routines extend the lifespan of conveyor belts and associated machinery, ensuring that investments yield the maximum possible return.
- Ensuring Operational Efficiency: Well-maintained conveyor belts run more smoothly and efficiently, reducing energy consumption and operational costs while maximizing throughput.
- Enhancing Safety: A well-maintained conveyor system is less likely to experience failures that could endanger workers, such as belt slippage, structural failures, or blockages that might lead to hazardous situations.
- Compliance with Regulations: Regular maintenance ensures that conveyor belt systems comply with safety standards and regulations, avoiding fines and legal issues.
- Optimizing Performance: Routine inspections and maintenance allow for adjustments that optimize the performance of the conveyor system, adapting to changing operational demands and conditions.
- Minimizing Repair Costs: Catching and addressing issues early through regular maintenance schedules can significantly reduce the cost and extent of repairs needed compared to addressing problems after a failure.
- Supporting Sustainability Efforts: Efficient and well-maintained conveyor belts contribute to sustainability by reducing energy consumption and minimizing waste, aligning with environmental goals and regulations.
The significance of mining conveyor belt maintenance cannot be overstated, as it is directly linked to the operational efficiency, safety, and profitability of mining operations. Investing in regular and thorough maintenance routines ensures that conveyor belts continue to perform their critical role reliably and efficiently, supporting the overarching goals of mining operations.
Mining Conveyor Belt Maintenance: Addressing Common Conveyor Belt Problems in Mining
The effective maintenance of mining conveyor belts is crucial for the seamless operation of the mining industry. Addressing common conveyor belt problems not only ensures operational efficiency but also significantly reduces downtime and maintenance costs. Here, we delve into some prevalent issues associated with conveyor belts in mining and discuss how proper mining conveyor belt maintenance can mitigate these challenges.
Conveyor Belt Mistracking
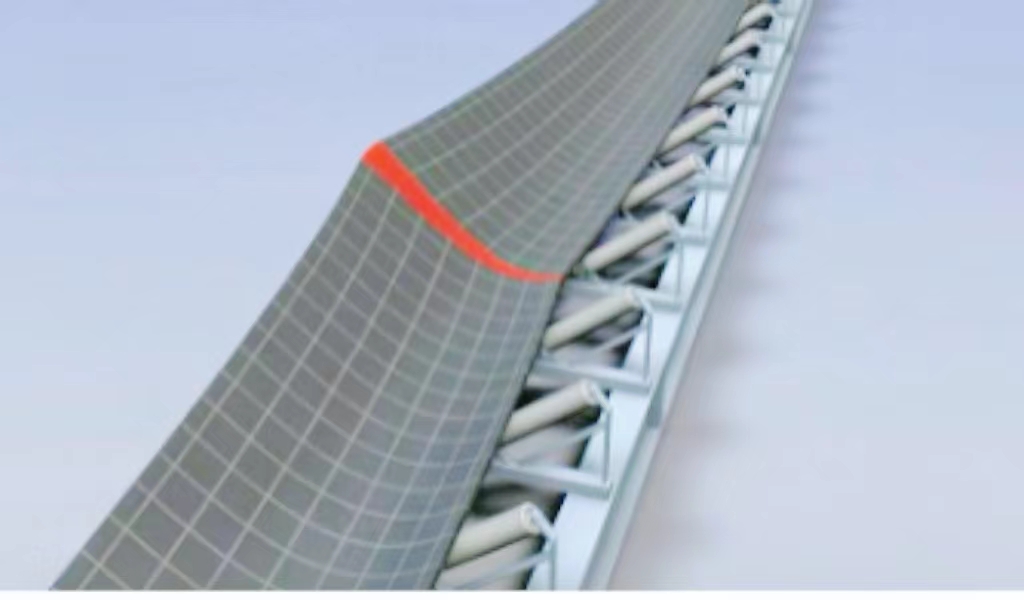
Conveyor belt mistracking is a frequent issue in mining operations. It occurs when the belt drifts off its intended path, leading to several operational problems. The causes of mistracking include misaligned rollers, uneven loading, worn-out tracking components, improper belt tension, structural damages, and buildup of conveyor materials on the rollers or pulley. These issues can lead to belt damage, increased wear and tear on the conveyor components, material spillage, decreased efficiency, and potentially hazardous working conditions. Implementing routine mining conveyor belt maintenance checks can identify and correct these issues early, preventing mistracking and its adverse effects.
Belt Slippage
Belt slippage happens when the belt loses grip on the drive pulley, significantly impacting productivity. Causes range from inadequate belt tension and worn pulley lagging to overloading and wet conditions. The effects include decreased throughput, increased wear on the belt and pulleys, and potential damage to the drive motor due to overexertion. Solutions involve adjusting belt tension, replacing or improving pulley lagging, ensuring proper loading, and maintaining optimal environmental conditions around the conveyor belt system.
Seized Rollers
Seized rollers, which no longer rotate freely, can create significant resistance on the conveyor belt, leading to increased power consumption and wear. They can be caused by material buildup, lack of lubrication, or bearing failure. Regular inspection and maintenance of rollers are essential to prevent seizing and its associated operational inefficiencies.
Blockages and Material Spillage
Material blockages and spillage are common issues that can lead to operational delays and increased maintenance work. Effective strategies for prevention and management include regular belt cleaning, installing adequate skirtboards, implementing proper chute designs, and ensuring the conveyor is correctly aligned and loaded. These measures not only minimize spillage and blockages but also enhance the overall safety and cleanliness of the mining site.
Material Carryback
Material carryback occurs when residues stick to the belt and are carried beyond the discharge point. This can lead to material loss, environmental concerns, and additional cleaning requirements, affecting the conveyor’s efficiency and lifespan. Addressing carryback involves installing primary and secondary rubber belt cleaners, proper chute design, and routine maintenance checks to ensure optimal cleaner performance.
Belt Tears and Seam Rips
Belt tears and seam rips can be catastrophic for mining conveyor operations, leading to significant downtime and repair costs. Common causes include sharp objects, impact load zone belt support, and material entrapment. Repair techniques involve hot or cold vulcanization, metal fasteners, or replacement of damaged sections, depending on the severity of the tear. Preventative measures include using impact beds, installing belt protection systems, and conducting regular belt inspections to identify and remove sharp objects and other hazards.
Effective mining conveyor belt maintenance is pivotal in addressing these common problems. By implementing a comprehensive maintenance program, mining operations can enhance their efficiency, reduce downtime, and extend the lifespan of their conveyor belt systems, thereby optimizing productivity and ensuring a safer working environment.
Mining Conveyor Belt Maintenance: Comprehensive Maintenance Strategies
Implementing comprehensive maintenance strategies for mining conveyor belts is not just a best practice; it’s a critical component of ensuring the longevity and efficiency of the conveyor system. A proactive approach to mining conveyor belt maintenance can significantly mitigate the risk of unexpected downtime, extend the lifespan of the belt, and optimize overall productivity.
Importance of a Proactive Maintenance Approach
- Minimizes Unscheduled Downtime: Proactive maintenance identifies potential issues before they lead to significant problems, thereby reducing unexpected breakdowns.
- Increases Equipment Lifespan: Regular upkeep and timely repairs extend the life of the conveyor belt and its components.
- Enhances Safety: By maintaining equipment in optimal condition, the risk of accidents and injuries is significantly lowered.
- Optimizes Performance: Regularly serviced conveyor systems operate more efficiently, contributing to higher productivity.
- Reduces Repair Costs: Addressing minor issues promptly can prevent more severe and costly damage in the future.
- Improves Reliability: A well-maintained conveyor system is more reliable, ensuring consistent operation and material flow.
- Supports Budget Planning: Predictable maintenance schedules allow for better budgeting and allocation of resources.
- Ensures Compliance: Regular maintenance helps in complying with safety standards and regulations.
Implementing a Regular Preventive Maintenance Program
A well-structured preventive maintenance program is the cornerstone of effective mining conveyor belt maintenance. Key elements of such a program include:
- Scheduled Inspections: Regular, comprehensive inspections of the conveyor belt and its components (rollers, pulleys, bearings, etc.) to identify wear and tear, misalignments, and other potential issues.
- Routine Cleaning: Removing dirt, debris, and material buildup from the conveyor belt, rollers, and pulleys to prevent mistracking, slippage, and premature wear.
- Lubrication: Proper lubrication of moving parts to reduce friction, prevent seizing of rollers, and extend component life.
- Tension Adjustments: Regularly checking and adjusting belt tension to prevent slippage and ensure smooth operation.
- Wear and Tear Monitoring: Monitoring for signs of wear or damage on the belt and components, and performing necessary repairs or replacements.
- Training for Operators and Maintenance Staff: Educating personnel on the correct operation of conveyor systems and the signs of potential problems can aid in early detection and prevention of issues.
- Documentation and Record-Keeping: Maintaining detailed records of inspections, maintenance activities, and repairs to track the health of the conveyor system over time and plan future maintenance activities.
A proactive and comprehensive approach to mining conveyor belt maintenance is indispensable for ensuring operational efficiency, safety, and longevity of the conveyor system. By implementing a regular preventive maintenance program, mining operations can achieve higher productivity levels, minimize downtime, and significantly reduce long-term maintenance costs.
Mining Conveyor Belt Maintenance: Conveyor Belt Maintenance Checklist for Mining Operations
A comprehensive and systematic approach to mining conveyor belt maintenance is crucial for ensuring the efficiency and longevity of the conveyor system within mining operations. This section outlines a detailed guide on daily, weekly, and monthly maintenance tasks, emphasizing the importance of a systematic inspection routine.
Daily Maintenance Tasks
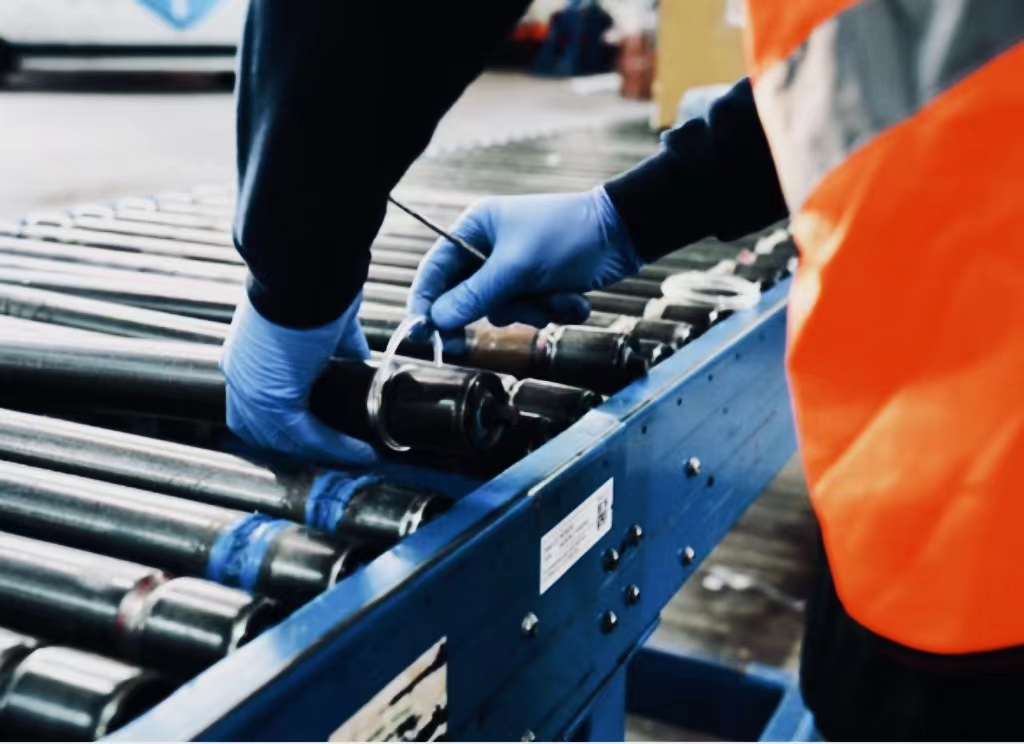
- Visual Inspection: Check for obvious issues like belt misalignment, visible wear and tear on the belt, and damage to the structure.
- Cleanup: Remove any debris, material spillage, and accumulation around the conveyor area to prevent blockages and reduce wear.
- Check Belt Tension: Ensure the belt is adequately tensioned to prevent slippage.
- Monitor Belt Operation: Listen for unusual noises and observe the belt’s operation to detect issues like mistracking or slippage early.
Weekly Maintenance Tasks
- Inspect Rollers and Idlers: Check for smooth operation, and replace any that are seized or spinning poorly.
- Check Conveyor Belt Seams and Edges: Look for fraying, tears, or wear that might indicate a need for repair or adjustment.
- Lubricate Bearings and Rollers: As needed, based on manufacturer recommendations and previous maintenance records.
Monthly Maintenance Tasks
- Thorough Cleaning: Conduct a more detailed cleaning of the conveyor system, including hard-to-reach areas.
- Belt Splice Inspection: Check belt splices for wear or damage, and repair as necessary.
- Test Emergency Stops: Ensure all emergency stop mechanisms are functioning correctly.
- Record Keeping: Update maintenance logs with the findings, actions taken, and parts replaced during the inspections.
Importance of a Systematic Inspection Routine
- Predictability: A systematic routine allows for predictable maintenance windows, minimizing unexpected downtimes.
- Cost Efficiency: Early detection of potential issues can lead to cost savings by avoiding major repairs or replacements.
- Safety: Regular inspections help identify and mitigate safety hazards, protecting workers and equipment.
- Operational Efficiency: Ensures that the conveyor system operates at optimal efficiency, contributing to overall productivity.
- Longevity: Regular maintenance extends the life of the conveyor belt and system components.
- Compliance: Helps in complying with industry standards and safety regulations.
- Reliability: A well-maintained conveyor system is more reliable, reducing the risk of operational disruptions.
- Performance Tracking: Systematic inspections provide data that can be used to track the performance and health of the conveyor system over time.
- Continuous Improvement: Regular maintenance and inspections allow for the identification of opportunities for improvements in the conveyor system’s design and operation.
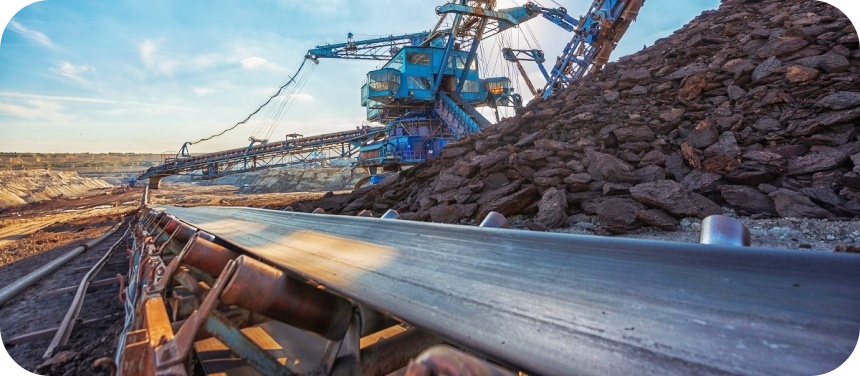
A detailed and systematic approach to mining conveyor belt maintenance is essential for the effective and safe operation of conveyor systems in mining environments. Adhering to a structured maintenance checklist ensures the conveyor belt’s reliability, efficiency, and longevity, significantly contributing to the overall productivity of mining operations.
As-Needed Maintenance in Mining Conveyor Belt Maintenance
Maintaining the efficiency and longevity of mining conveyor belts is crucial to ensure smooth operations in mining facilities. As-needed maintenance is a key component of the overall maintenance strategy for mining conveyor belts. It involves addressing issues as they arise, preventing minor problems from escalating into major failures that could halt production. This approach requires a thorough understanding of the various components of the conveyor system and a proactive stance in identifying and resolving potential issues.
Replacing Worn or Malfunctioning Equipment
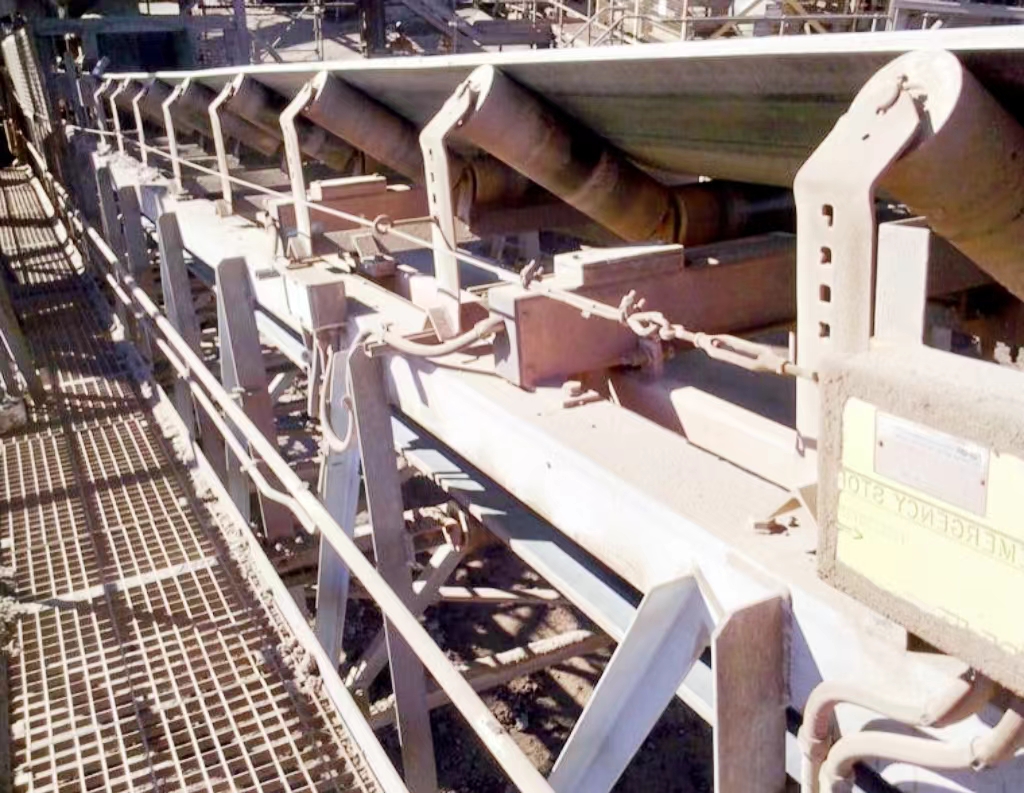
One of the primary aspects of as-needed maintenance in mining conveyor belt maintenance is replacing worn or malfunctioning equipment. Conveyor belts are subjected to constant use and wear, making it essential to regularly inspect and replace components that show signs of wear. This includes everything from the belt itself to the various mechanical and electrical components that keep the system running smoothly.
Identifying Worn Equipment
The first step in replacing worn or malfunctioning equipment is to identify the components that need attention. Regular inspections are vital to this process. Signs of wear can include visible damage, unusual noises, or a decrease in performance. Technicians should be trained to recognize these signs and understand the potential implications of ignoring them.
Commonly Replaced Components
Several components of a mining conveyor belt system are prone to wear and may need replacement as part of as-needed maintenance. These include:
- Belts: The belts themselves are the most obvious components that can wear out. Look for fraying, cracks, or any signs of tearing.
- Bearings: Bearings can wear out over time, leading to increased friction and potential system failures.
- Motors and Drives: The motors and drives that power the conveyor belt can also wear out or malfunction, requiring replacement.
- Pulleys and Shafts: These components can become worn or damaged and need to be inspected regularly.
Replacement Process
Replacing worn or malfunctioning equipment involves several steps:
- Shut Down the System: Ensure that the conveyor belt system is shut down and locked out to prevent accidental startup during maintenance.
- Remove the Worn Component: Carefully remove the worn or malfunctioning component. This may require specialized tools and expertise.
- Install the New Component: Install the new component, ensuring it is properly aligned and secured.
- Test the System: Once the new component is installed, test the system to ensure it is functioning correctly.
Repairing or Replacing Damaged Idlers, Rollers, and Lagging
Idlers, rollers, and lagging are critical components of a mining conveyor belt system. They support the belt and help to maintain its alignment and tension. Damage to these components can lead to significant issues, including belt misalignment, increased wear, and even belt failure.
Identifying Damage
Regular inspections are essential to identify damaged idlers, rollers, and lagging. Signs of damage can include:
- Visible Wear or Damage: Cracks, chips, or other visible damage to the idlers, rollers, or lagging.
- Unusual Noises: Squeaking, grinding, or other unusual noises coming from the conveyor system.
- Belt Misalignment: If the belt is not running straight, it could be a sign of damaged idlers or rollers.
Repairing Damaged Components
In some cases, it may be possible to repair damaged idlers, rollers, and lagging rather than replacing them. This can involve:
- Realigning Idlers and Rollers: If the idlers or rollers have shifted out of alignment, they can be realigned to correct the issue.
- Replacing Lagging: Lagging that has worn out or become damaged can often be replaced without the need to replace the entire pulley.
Replacing Components
When repair is not possible, replacing the damaged components is necessary. This process involves:
- Shut Down the System: Ensure the conveyor system is shut down and locked out.
- Remove the Damaged Component: Carefully remove the damaged idler, roller, or lagging.
- Install the New Component: Install the new component, ensuring it is properly aligned and secured.
- Test the System: Test the system to ensure it is functioning correctly and that the belt is properly aligned.
Maintaining Dust Containment Systems
Dust is a significant issue in mining operations, and conveyor belt systems are no exception. Dust can cause a variety of problems, including health hazards for workers, increased wear on equipment, and potential fire hazards. Maintaining dust containment systems is a critical aspect of as-needed maintenance in mining conveyor belt maintenance.
Importance of Dust Containment
Effective dust containment is essential for several reasons:
- Health and Safety: Dust can pose serious health risks to workers, including respiratory issues and other health problems.
- Equipment Longevity: Dust can accelerate wear on conveyor belt components, leading to more frequent maintenance and replacements.
- Fire Prevention: Accumulated dust can be a fire hazard, particularly in environments where there are sparks or high temperatures.
Dust Containment Systems
Several types of dust containment systems can be used in mining conveyor belt maintenance:
- Dust Collectors: These systems capture dust at the source, preventing it from becoming airborne.
- Enclosures and Covers: Enclosing conveyor belts and other equipment can help to contain dust and prevent it from spreading.
- Water Sprays: Spraying water can help to suppress dust and keep it from becoming airborne.
Maintaining Dust Containment Systems
Regular maintenance of dust containment systems is essential to ensure they remain effective. This can involve:
- Inspecting Dust Collectors: Regularly inspect dust collectors to ensure they are functioning correctly and that filters are not clogged.
- Checking Enclosures and Covers: Ensure that enclosures and covers are intact and that there are no gaps where dust can escape.
- Maintaining Water Sprays: Ensure that water sprays are functioning correctly and that nozzles are not clogged.
Addressing Issues
If issues are identified with the dust containment systems, they should be addressed promptly to prevent dust from becoming a problem. This can involve:
- Replacing Filters: If dust collector filters are clogged or damaged, they should be replaced.
- Repairing Enclosures: Any gaps or damage to enclosures and covers should be repaired to ensure they are effective.
- Cleaning Nozzles: Water spray nozzles should be cleaned regularly to ensure they are not clogged and are functioning correctly.
Integrating As-Needed Maintenance with Overall Maintenance Strategy
As-needed maintenance is just one part of an effective mining conveyor belt maintenance strategy. It should be integrated with other maintenance approaches, including preventive and predictive maintenance, to ensure comprehensive coverage and optimal performance.
Preventive Maintenance
Preventive maintenance involves regularly scheduled inspections and maintenance tasks designed to prevent issues before they occur. This can include tasks such as lubricating moving parts, tightening loose components, and replacing worn parts before they fail.
Predictive Maintenance
Predictive maintenance uses data and analytics to predict when components are likely to fail and schedule maintenance accordingly. This can involve monitoring vibration levels, temperature, and other indicators of wear and tear.
Combining Approaches
Combining as-needed, preventive, and predictive maintenance can provide a comprehensive approach to mining conveyor belt maintenance. This can help to ensure that issues are identified and addressed promptly, reducing the risk of unexpected failures and improving the overall efficiency and longevity of the conveyor system.
Mining Conveyor Belt Maintenance: Advanced Solutions and Innovations
In the realm of mining conveyor belt maintenance, the integration of advanced solutions and innovations plays a pivotal role in enhancing safety, efficiency, and effectiveness. Among such innovations, protective gear like HexArmor® chaps stands out for offering superior safety during maintenance tasks. This section delves into the transformative impact of modern technology on simplifying conveyor belt maintenance in the mining industry.
Introduction to Innovative Solutions
HexArmor® Chaps for Safer Maintenance Tasks: Maintenance personnel often face risks from sharp objects, heavy machinery, and the conveyor belt itself. HexArmor® chaps provide a high level of protection against cuts, abrasions, and impacts, ensuring that workers can perform maintenance tasks with an added layer of safety. These chaps are designed with durable materials that resist tearing and puncturing, making them an essential part of the maintenance toolkit.
Roles of Modern Technology in Simplifying Conveyor Belt Maintenance
Condition Monitoring Systems: Advanced sensors and IoT devices continuously monitor the health of conveyor belts and components, detecting issues like misalignment, abnormal vibrations, and wear patterns early on.
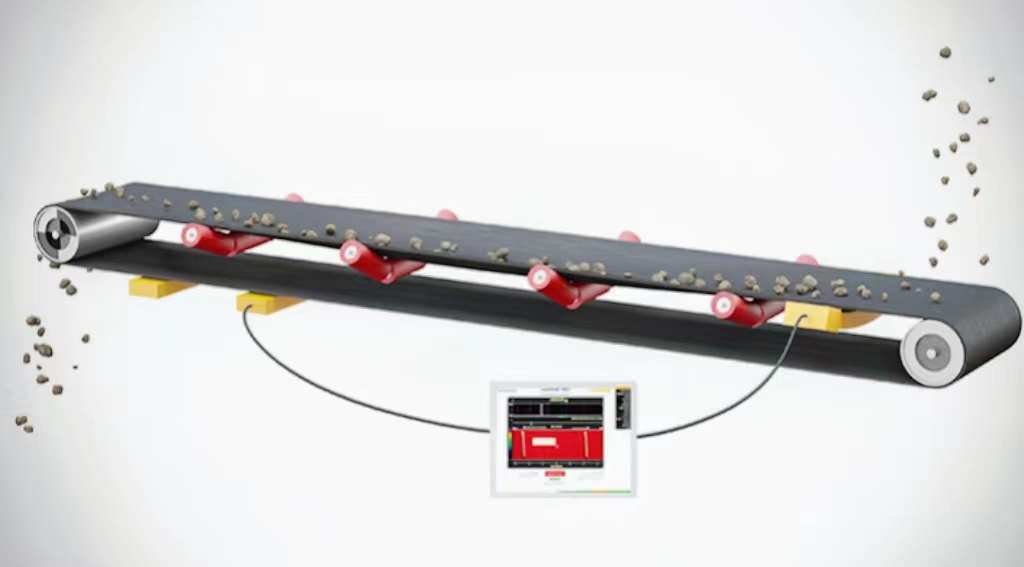
Automated Inspections: Drones and robotic devices can conduct regular inspections of hard-to-reach areas, providing high-resolution images and data for analysis, thus reducing the need for manual inspections in potentially hazardous conditions.
Predictive Maintenance Software: Leveraging AI and machine learning, these systems analyze data from condition monitoring to predict potential failures, allowing for maintenance to be scheduled before issues become critical.
Wearable Safety Devices: Beyond HexArmor® chaps, other wearable technologies, such as smart helmets and vests, enhance worker safety by monitoring vital signs and environmental conditions, and providing real-time alerts in case of emergencies.
Digital Maintenance Logs: Cloud-based platforms enable the digital recording and tracking of maintenance activities, inspections, and repairs, improving accountability and providing a comprehensive history of conveyor belt maintenance.
Advanced Repair Solutions: Techniques like cold bonding and laser cladding offer quicker, more durable repairs to conveyor belts and components, minimizing downtime and extending service life.
Training Simulators: Virtual reality (VR) and augmented reality (AR) provide immersive training experiences for maintenance personnel, improving their skills in a safe, controlled environment without the need to halt conveyor operations.
Energy-Efficient Technologies: Innovations in motor and drive systems, along with energy-efficient belt materials, reduce the energy consumption of conveyor systems, contributing to sustainability goals while lowering operational costs.
Incorporating these advanced solutions and innovations into mining conveyor belt maintenance protocols not only simplifies the maintenance process but also significantly enhances safety, efficiency, and reliability. As technology continues to evolve, the mining industry stands to benefit from these developments, ensuring that conveyor belt systems remain a vital and efficient component of mining operations worldwide.
Mining Conveyor Belt Maintenance: Safety First – Prioritizing Worker Safety in Maintenance Operations
In the context of mining conveyor belt maintenance, prioritizing worker safety is paramount. The inherent risks associated with maintenance operations in mining environments necessitate stringent safety protocols and equipment for maintenance crews. Moreover, the importance of comprehensive training and strict adherence to safety guidelines cannot be overstated. This section outlines key safety protocols, essential equipment, and the critical role of training in ensuring a safe working environment during conveyor belt maintenance tasks.
Safety Protocols and Equipment for Maintenance Crews
- Personal Protective Equipment (PPE): Standard PPE for maintenance crews includes safety helmets, gloves, eye protection, high-visibility clothing, and steel-toed boots. For specific tasks, additional protective gear like HexArmor® chaps may be required to guard against particular hazards.
- Lockout-Tagout (LOTO) Procedures: Before any maintenance work begins, it’s crucial to implement LOTO procedures to ensure that conveyor systems are de-energized and cannot be started accidentally.
- Fall Protection Systems: When maintenance work involves heights, fall protection measures such as safety harnesses, lanyards, and guardrails are essential to prevent fall-related injuries.
- Fire Safety Equipment: Ready access to fire extinguishers and fire blankets is necessary, especially when maintenance tasks involve welding or the use of flammable materials.
- Emergency Stop Systems: Maintenance crews must be familiar with the locations and operation of emergency stop controls along the conveyor system.
- Ventilation and Respiratory Protection: Adequate ventilation is critical in enclosed spaces, and respiratory protection may be required when working in dusty conditions or with potentially harmful chemicals.
- Communication Devices: Two-way radios or other communication devices ensure that maintenance personnel can quickly communicate, especially in large or noisy operations.
- First Aid Kits and Training: Accessible, well-stocked first aid kits and trained first responders are crucial for addressing any injuries immediately.
Experience unparalleled strength and reliability—order our conveyor belts today!
Importance of Training and Adherence to Safety Guidelines
- Comprehensive Training Programs: Regular, detailed training sessions equip maintenance personnel with the knowledge and skills to safely perform their tasks, recognize potential hazards, and respond effectively to emergencies.
- Safety Guidelines and Procedures: Clearly documented and easily accessible safety guidelines and procedures help ensure that all maintenance activities are conducted consistently and safely.
- Continuous Learning: Ongoing education on the latest safety practices, technologies, and regulations keeps maintenance crews informed and prepared to work safely.
- Safety Culture: Fostering a strong safety culture within the organization encourages workers to prioritize safety in every task and to look out for one another.
- Incident Reporting and Analysis: Encouraging the reporting and analysis of all incidents, no matter how minor, can provide valuable insights into potential safety improvements.
- Regulatory Compliance: Adhering to local, national, and industry-specific safety regulations is not only a legal requirement but also a cornerstone of safe maintenance practices.
Prioritizing worker safety in mining conveyor belt maintenance operations involves a comprehensive approach that includes the right safety protocols, equipment, and rigorous training. By fostering a culture of safety, adhering to strict safety guidelines, and continuously updating training programs, mining operations can significantly reduce the risk of accidents and injuries, ensuring the well-being of their maintenance crews.
FAQs about Mining Conveyor Belt Maintenance
How do you maintain a conveyor belt?
Maintaining a conveyor belt requires a comprehensive approach that encompasses regular inspections, cleaning, adjustments, and replacements when necessary. The key to effective maintenance is consistency and thoroughness.
First, you should conduct daily visual checks to look for signs of wear or damage to the belt. During these checks, remove any debris or residue that could hinder the belt’s operation. Ensure that the belt is properly aligned and tensioned to prevent mistracking and slippage, which are common issues that can lead to larger problems if left unaddressed.
Weekly tasks should include a more in-depth inspection of all the conveyor components, such as rollers, bearings, and drive motors. This is also a good time to lubricate any moving parts if required.
On a monthly basis, more extensive evaluations should take place. This might involve checking the integrity of the belt splices, confirming that all emergency stops and controls are fully operational, and updating maintenance records. These records are vital for tracking the longevity and performance of your conveyor belt over time.
Lastly, ensure that all maintenance personnel are properly trained in both the operation and the maintenance procedures for your conveyor system to maintain its longevity and functionality.
Conveyor maintenance tasks can be categorized as daily, weekly, and monthly activities that are designed to keep the conveyor system running smoothly and prevent downtime.
Daily tasks include cleaning the conveyor to remove dirt and debris, checking for any signs of wear or damage, and ensuring that the belt is running correctly. It’s also important to listen for unusual noises that could indicate a problem with the conveyor.
Weekly maintenance should involve inspecting key mechanical components, including rollers, bearings, and the motor, to ensure optimal performance. Checking for proper belt tension and alignment is also crucial to prevent mistracking.
Monthly maintenance often involves a thorough check of the entire system. This is when you would perform any necessary repairs, replace parts that are showing excessive wear, and carry out detailed cleaning tasks. It is also essential to test safety mechanisms and emergency stops to ensure they are functioning properly.
Regular maintenance ensures that the conveyor operates efficiently and can greatly extend the life of the system.
Preventive maintenance of a conveyor system involves a series of planned activities that aim to prevent unexpected breakdowns and extend the lifespan of the conveyor. The goal is to identify and address issues before they lead to significant problems.
A typical preventive maintenance program will include the following:
Regular inspections to identify wear and potential failures.
Scheduled lubrication of moving parts to reduce friction and wear.
Calibration and adjustment of sensors and controls.
Belt tensioning and tracking adjustments to prevent slippage and ensure the belt runs smoothly.
Checking and tightening of all bolts and fasteners to prevent structural issues.
Timely replacement of worn or damaged parts before they can cause a breakdown.
Preventive maintenance is crucial because it helps to maintain the reliability of the conveyor system, ensures safety, improves performance, and ultimately saves money by reducing the need for emergency repairs and downtime.
One of the most common problems of belt conveyors is mistracking, where the belt drifts off its intended path. This can lead to several issues such as premature belt wear, damage to the belt edges, spillage of conveyed materials, or even complete belt failure. Other frequent problems include belt slippage, seized rollers, blockages, material spillage, wear and tear on conveyor components, and motor or gearbox failures. Regular maintenance and inspections can identify these problems early on, preventing them from escalating into major issues.
Mining conveyor belts can be purchased from suppliers that specialize in mining equipment and industrial hardware. To find a supplier, you can conduct an online search for “mining conveyor belt suppliers” or visit industrial trade shows where manufacturers display their products. It’s important to choose a reputable supplier that offers high-quality conveyor belts designed for the specific demands of the mining industry. Consider the belt’s durability, resistance to wear and abrasion, load capacity, and suitability for the type of materials it will carry. Additionally, it’s advisable to seek out suppliers that provide after-sales support and can supply replacement parts as needed.
General maintenance of a conveyor belt involves regular inspection and servicing to ensure optimal performance and longevity. Key tasks include checking for wear and tear on the belt itself, inspecting and lubricating rollers and bearings, and ensuring the motor and other mechanical components are functioning correctly. Regular cleaning to remove any debris that could cause damage or reduce efficiency is also essential. Additionally, it’s important to check the alignment and tension of the belt to prevent slippage and excessive wear. Keeping a detailed maintenance log can help track the condition of the conveyor belt and schedule timely repairs or replacements.
The frequency of conveyor belt servicing depends on several factors, including the operating environment, load capacity, and usage intensity. For most industrial applications, a general recommendation is to perform a thorough inspection and servicing every three months. However, in high-use or harsh environments, more frequent checks, such as monthly or even weekly, might be necessary. Regular maintenance helps to identify and address issues early, reducing the risk of unexpected breakdowns and extending the lifespan of the conveyor system. Always refer to the manufacturer’s guidelines for specific maintenance intervals.
Maintaining a conveyor belt involves several key steps. First, regularly inspect the belt for any signs of wear, damage, or misalignment. Ensure that the belt is properly tensioned and aligned to prevent slippage and uneven wear. Clean the belt and surrounding components to remove any debris that could cause damage. Lubricate moving parts such as rollers and bearings to reduce friction and wear. Check the motor and other mechanical components for proper operation and address any issues promptly. Additionally, keep a maintenance log to track inspections, servicing, and any repairs made. Following these steps can help maintain the efficiency and longevity of the conveyor belt.
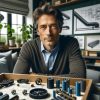
Jordan Smith, a seasoned professional with over 20 years of experience in the conveyor system industry. Jordan’s expertise lies in providing comprehensive solutions for conveyor rollers, belts, and accessories, catering to a wide range of industrial needs. From initial design and configuration to installation and meticulous troubleshooting, Jordan is adept at handling all aspects of conveyor system management. Whether you’re looking to upgrade your production line with efficient conveyor belts, require custom conveyor rollers for specific operations, or need expert advice on selecting the right conveyor accessories for your facility, Jordan is your reliable consultant. For any inquiries or assistance with conveyor system optimization, Jordan is available to share his wealth of knowledge and experience. Feel free to reach out at any time for professional guidance on all matters related to conveyor rollers, belts, and accessories.