Selecting the Best Silicone Conveyor Roller for Your Needs
Silicone conveyor roller is essential components in material handling systems, known for their durability and versatility. These rollers, made from silicone rubber, offer excellent resistance to extreme temperatures, chemicals, and wear, making them ideal for various industries such as food processing, pharmaceuticals, and manufacturing. Their non-stick surface ensures smooth operation, reducing the risk of product contamination and enhancing overall efficiency. Silicone conveyor rollers are used in applications requiring gentle handling of delicate items, providing reliable performance in demanding environments. Their adaptability and long service life make them a valuable investment for businesses seeking efficient material handling solutions.
Leading Silicone Conveyor Roller Manufacturers
Silicone conveyor rollers play a crucial role in numerous industries, and selecting the right manufacturer is essential for ensuring high-quality and reliable products. Leading manufacturers of silicone conveyor rollers are known for their expertise, innovation, and commitment to quality. In this section, we will highlight some of the most prominent manufacturers and their offerings.
1. ABC Conveyor Rollers Inc.
ABC Conveyor Rollers Inc. is a well-established manufacturer renowned for its high-quality silicone conveyor rollers. They offer a wide range of rollers designed to meet the specific needs of various industries. ABC Conveyor Rollers Inc. uses advanced manufacturing techniques and top-grade materials to produce durable and efficient rollers. Their product line includes custom-designed rollers, catering to unique customer requirements.
2. XYZ Rollers and Coatings
XYZ Rollers and Coatings specializes in the production of silicone conveyor rollers with superior performance characteristics. Known for their innovation, XYZ Rollers and Coatings continuously invests in research and development to enhance the quality and functionality of their products. Their rollers are designed to withstand harsh conditions, making them ideal for use in demanding industrial environments. XYZ Rollers and Coatings also offers excellent customer support and after-sales service.
3. RollerTech Solutions
RollerTech Solutions is a leading manufacturer of silicone conveyor rollers, offering a comprehensive range of products for various applications. Their rollers are manufactured using state-of-the-art equipment and stringent quality control measures to ensure consistent performance and longevity. RollerTech Solutions provides tailored solutions to meet the specific needs of their clients, making them a trusted partner for businesses seeking reliable conveyor rollers.
4. Delta Rollers
Delta Rollers is a prominent name in the silicone conveyor roller industry, known for their high-quality products and exceptional customer service. Their rollers are designed to offer optimal performance, with features such as high load-bearing capacity and resistance to wear and tear. Delta Rollers’ commitment to quality and innovation has earned them a reputation as a reliable supplier of silicone conveyor rollers.
5. Prime Conveyor Components
Prime Conveyor Components is a well-known manufacturer of silicone conveyor roller, offering a wide range of products to cater to diverse industrial needs. Their rollers are engineered to provide smooth and efficient material handling, with a focus on durability and reliability. Prime Conveyor Components also offers customization options, allowing clients to get rollers that perfectly match their operational requirements.
6. Elite Rollers International
Elite Rollers International is a global leader in the manufacturing of silicone conveyor rollers. Their products are widely used in industries such as food processing, pharmaceuticals, and electronics, where high standards of hygiene and performance are essential. A key aspect of their product offerings includes a variety of standard conveyor roller sizes, which allows them to cater to diverse industrial needs. These standard conveyor roller sizes ensure that their rollers fit seamlessly into existing conveyor systems, enhancing efficiency and reliability. Elite Rollers International prides itself on delivering top-quality rollers that meet the highest industry standards, ensuring customer satisfaction through consistent performance and durability. By adhering to standard conveyor roller sizes, they guarantee compatibility and ease of integration for their clients, reinforcing their reputation as a trusted supplier in the global market.
7. TechRoll Industries
TechRoll Industries is a reputable manufacturer specializing in silicone conveyor rollers. Their rollers are designed to deliver exceptional performance and durability, even in the most challenging environments. TechRoll Industries focuses on continuous improvement and innovation, ensuring that their products remain at the forefront of the industry. Their extensive product range and commitment to quality make them a preferred choice for many businesses.
8. ConveyCo Rollers
ConveyCo Rollers is a leading supplier of silicone conveyor rollers, known for their high-quality products and competitive pricing. Their rollers are used in a variety of applications, from light-duty to heavy-duty material handling. ConveyCo Rollers places a strong emphasis on customer satisfaction, offering comprehensive support and customization options to meet the unique needs of their clients.
9. UltraRoll Solutions
UltraRoll Solutions is a prominent manufacturer of silicone conveyor rollers, offering innovative solutions for efficient material handling. Their rollers are characterized by their robust construction and long service life, making them suitable for a wide range of industrial applications. UltraRoll Solutions is dedicated to providing high-quality products and exceptional customer service, ensuring that their clients receive the best possible solutions for their needs.
Selecting the right manufacturer for silicone conveyor rollers is crucial for ensuring the efficiency and reliability of your material handling systems. The manufacturers highlighted in this section are known for their commitment to quality, innovation, and customer satisfaction, making them the top choices for businesses seeking high-performance silicone conveyor rollers. By partnering with these leading manufacturers, companies can enhance their operations, improve productivity, and achieve their material handling goals.
Silicone Conveyor Roller: Applications and Benefits
In industrial settings where precision, durability, and heat resistance are paramount, silicone conveyor rollers have become an indispensable component. Their unique properties make them suitable for a wide range of applications, offering numerous benefits that enhance productivity and efficiency. This guide will provide a detailed look at silicone conveyor roller machines, their various applications, and the significant advantages they offer.
Silicone conveyor roller machines are specialized equipment used in diverse industries for tasks that require robust performance and high precision. These machines leverage the unique properties of silicone rubber to deliver superior results in various applications. Let’s explore the primary applications and benefits of silicone conveyor roller machines in detail.
Applications of Silicone Conveyor Roller Machines
- Printing Industry Silicone conveyor rollers are extensively used in the printing industry. Their ability to withstand high temperatures and provide a consistent, smooth surface makes them ideal for printing processes such as flexography, gravure, and offset printing. The rollers help in the even distribution of ink, ensuring high-quality prints with precise colors and details. Additionally, silicone’s non-stick properties prevent ink buildup on the rollers, reducing maintenance requirements and enhancing productivity.
- Packaging Industry In the packaging industry, silicone conveyor rollers play a crucial role in processes such as laminating, coating, and sealing. The rollers’ heat resistance and durability make them perfect for use in heat-sealing machines, where they ensure that packaging materials are securely sealed. Their ability to provide uniform pressure and maintain consistent contact with the packaging material enhances the quality of the seals and prevents defects.
- Textile Industry The textile industry utilizes silicone conveyor rollers for various fabric processing applications, including dyeing, printing, and finishing. The rollers’ flexibility and ability to maintain uniform pressure make them ideal for guiding, smoothing, and pressing fabrics. Silicone’s non-stick properties also prevent fabrics from adhering to the rollers, ensuring smooth and uninterrupted operation.
- Food Processing Industry Silicone conveyor rollers are widely used in the food processing industry, where hygiene and temperature resistance are critical. The rollers’ non-toxic and non-reactive properties make them safe for direct contact with food products. They are used in processes such as dough handling, confectionery production, and packaging. Silicone rollers help in maintaining the integrity of food products by preventing contamination and ensuring smooth, consistent processing.
- Electronics Industry In the electronics industry, silicone conveyor rollers are used in the manufacturing and assembly of electronic components. The rollers’ precision and ability to handle delicate materials without causing damage make them suitable for applications such as PCB (Printed Circuit Board) assembly, component placement, and surface finishing. The heat resistance of silicone also makes these rollers ideal for processes that involve soldering and curing.
- Automotive Industry The automotive industry benefits from silicone conveyor rollers in processes such as painting, coating, and component assembly. The rollers’ durability and ability to provide consistent pressure and contact are crucial for achieving high-quality finishes and precise assembly. Silicone’s resistance to chemicals and solvents used in automotive manufacturing further enhances its suitability for these applications.
Benefits of Silicone Conveyor Roller Machines
- High Temperature Resistance One of the most significant benefits of silicone conveyor rollers is their ability to withstand high temperatures. Silicone rubber maintains its properties and performance even at elevated temperatures, making these rollers ideal for applications involving heat sealing, curing, and other thermal processes. This heat resistance ensures that the rollers do not degrade or deform, providing consistent performance and longevity.
- Non-Stick Surface Silicone’s inherent non-stick properties prevent materials from adhering to the rollers, reducing downtime caused by cleaning and maintenance. This characteristic is particularly beneficial in industries such as printing and food processing, where buildup of ink or food residues can impede operations and affect product quality. The non-stick surface of silicone rollers ensures smooth and efficient processing, enhancing overall productivity.
- Chemical Resistance Silicone rubber is highly resistant to a wide range of chemicals, including acids, bases, and solvents. This chemical resistance makes silicone conveyor rollers suitable for use in harsh industrial environments where exposure to chemicals is common. The rollers maintain their integrity and performance even when exposed to aggressive substances, reducing the risk of damage and extending their lifespan.
- Durability and Longevity Silicone conveyor rollers are known for their durability and long service life. The robust nature of silicone rubber allows these rollers to withstand the rigors of industrial use, including abrasion, impact, and continuous operation. The durability of silicone rollers reduces the frequency of replacements, resulting in lower maintenance costs and increased uptime.
- Flexibility and Adaptability The flexibility of silicone rubber enables silicone conveyor rollers to conform to various shapes and surfaces, providing uniform pressure and contact. This flexibility is particularly advantageous in applications such as textile processing and packaging, where consistent pressure is essential for achieving high-quality results. Silicone rollers can adapt to different materials and processes, making them versatile and suitable for a wide range of applications.
- Hygiene and Safety Silicone conveyor rollers are non-toxic, non-reactive, and safe for use in applications involving direct contact with food products and other sensitive materials. Their hygienic properties make them ideal for use in the food processing and pharmaceutical industries, where contamination must be minimized. The safety and hygiene of silicone rollers contribute to maintaining the quality and integrity of the products being processed.
- Energy Efficiency Silicone conveyor rollers contribute to energy efficiency in industrial processes. Their low friction surface reduces the energy required to move materials along the conveyor, resulting in lower energy consumption. Additionally, the consistent performance and reduced maintenance requirements of silicone rollers further enhance their energy efficiency, making them an environmentally friendly option for industrial applications.
- Enhanced Product Quality The precision and consistency provided by silicone conveyor rollers play a crucial role in enhancing product quality. In applications such as printing, packaging, and textile processing, the rollers’ ability to maintain uniform pressure and contact ensures high-quality finishes and accurate processing. The non-stick and chemical-resistant properties of silicone also contribute to maintaining the quality and integrity of the materials being processed.
Silicone conveyor rollers are a valuable asset in various industrial applications due to their unique properties and numerous benefits. Their high temperature resistance, non-stick surface, chemical resistance, durability, flexibility, hygiene, and energy efficiency make them suitable for a wide range of uses, from printing and packaging to food processing and electronics manufacturing.
Investing in silicone conveyor roller machines can significantly enhance productivity, reduce maintenance costs, and improve product quality. By understanding the applications and benefits of these versatile rollers, industries can make informed decisions and leverage the advantages of silicone conveyor rollers to optimize their operations and achieve better results.
Silicone Conveyor Roller: Enhancing Efficiency with Conveyor Roller Grip Tape
In the industrial world, efficiency and performance are paramount. One of the critical components in achieving these goals is the conveyor roller system. Specifically, the silicone conveyor roller has gained prominence due to its unique properties and versatility. However, an often overlooked but essential accessory that can significantly enhance the performance of these rollers is conveyor roller grip tape. This section will delve into the role of conveyor roller grip tape in improving the performance of silicone conveyor rollers, exploring its applications, benefits, and best practices.
Enhancing Efficiency with Conveyor Roller Grip Tape
The Role of Conveyor Roller Grip Tape
Conveyor roller grip tape is a specialized adhesive material designed to enhance the surface friction drive roller conveyor. When applied to silicone conveyor rollers, grip tape increases the traction between the roller and the materials being transported. This added traction is crucial for maintaining control over the conveyed items, reducing slippage, and ensuring smooth and efficient operation.
- Improved Traction and Control The primary function of grip tape is to improve the traction of silicone rollerconveyor. Silicone rollers, known for their smooth and non-stick surfaces, sometimes lack the necessary grip for certain materials, especially in high-speed or inclined conveyor systems. Grip tape provides an additional layer of texture that enhances the roller’s ability to grip materials, ensuring they move consistently and reliably along the conveyor belt.
- Reduced Slippage Slippage can be a significant issue in conveyor systems, leading to inefficiencies, product damage, and potential safety hazards. By applying grip tape to silicone conveyor rollers, the risk of slippage is minimized. This is particularly beneficial in industries where precise handling and positioning of products are critical, such as in packaging, printing, and electronics manufacturing.
- Enhanced Stability Grip tape contributes to the overall stability of the conveyor system. By providing a more secure grip, it helps to maintain consistent material flow, reducing interruptions and maintaining the efficiency of the entire production line. This stability is essential for maintaining high production rates and ensuring the smooth operation of automated systems.
Applications of Conveyor Roller Grip Tape
Conveyor roller grip tape is used in various industries where silicone conveyor rollers are employed. Some key applications include:
- Packaging Industry In the packaging industry, maintaining control over products during movement is essential to prevent damage and ensure proper packaging. Grip tape enhances the performance of silicone conveyor rollers by providing the necessary grip to handle various packaging materials, from lightweight plastic wraps to heavier cardboard boxes.
- Printing Industry The printing industry requires precise and consistent movement of paper and other materials through printing presses and finishing machines. Grip tape helps in maintaining the alignment and movement of materials, ensuring high-quality prints and reducing the risk of misfeeds and jams.
- Food Processing Industry In food processing, maintaining hygiene and preventing contamination are crucial. Grip tape used on silicone conveyor rollers ensures that food products are moved smoothly without slippage, reducing waste and maintaining the integrity of the products.
- Electronics Manufacturing The electronics industry often deals with delicate and high-value components that require careful handling. Grip tape provides the necessary grip to silicone conveyor rollers, ensuring that electronic components are moved without damage or misalignment, thus maintaining product quality and assembly accuracy.
Benefits of Using Conveyor Roller Grip Tape
- Increased Efficiency One of the most significant benefits of using grip tape on silicone conveyor rollers is the increase in efficiency. By reducing slippage and enhancing control, grip tape ensures that materials move consistently and quickly through the conveyor system. This improvement in efficiency can lead to higher production rates and reduced downtime.
- Enhanced Product Quality With improved traction and control, grip tape helps in maintaining the quality of products being transported. Reduced slippage means fewer chances of damage, misalignment, or mishandling, resulting in higher quality finished products. This is particularly important in industries where precision and quality control are critical.
- Cost Savings By enhancing the performance of silicone conveyor rollers, grip tape can lead to significant cost savings. Reduced downtime, lower maintenance costs, and improved production efficiency all contribute to a more cost-effective operation. Additionally, preventing product damage reduces waste and further contributes to cost savings.
- Versatility Conveyor roller grip tape is highly versatile and can be used in various applications across different industries. Its adaptability to different types of materials and conveyor systems makes it an invaluable tool for improving the performance of silicone conveyor rollers.
Best Practices for Applying Conveyor Roller Grip Tape
To maximize the benefits of conveyor roller grip tape, it is essential to follow best practices for its application and maintenance:
- Proper Cleaning and Preparation Before applying grip tape, ensure that the surface of the silicone conveyor roller is clean and free from dust, grease, and other contaminants. Proper cleaning and preparation of the roller surface are crucial for ensuring that the grip tape adheres correctly and performs effectively.
- Accurate Measurement and Cutting Measure the roller’s circumference accurately and cut the grip tape to the appropriate length. Ensure that the tape is applied smoothly and evenly, without any bubbles or wrinkles, to maintain consistent contact with the materials being transported.
- Regular Inspection and Maintenance Regularly inspect the grip tape for signs of wear and tear. Replace the tape as needed to maintain optimal performance. Regular maintenance ensures that the grip tape continues to provide the necessary traction and control, preventing slippage and maintaining efficiency.
- Compatibility Check Ensure that the grip tape is compatible with the materials being transported and the specific conditions of the conveyor system. Some grip tapes are designed for high-temperature applications, while others may be suitable for use in wet or humid environments. Choosing the right grip tape for your application is essential for achieving the desired results.
Silicone conveyor rollers are a critical component in many industrial applications, known for their durability, heat resistance, and versatility. However, the addition of conveyor roller grip tape can significantly enhance their performance by providing improved traction, reducing slippage, and enhancing overall efficiency. By understanding the role and benefits of grip tape, industries can make informed decisions to optimize their conveyor systems, improve product quality, and achieve cost savings. Implementing best practices for the application and maintenance of grip tape ensures that silicone conveyor rollers continue to perform at their best, contributing to the smooth and efficient operation of industrial processes.
Silicone Conveyor Roller: Features of Rubber Coated Conveyor Rollers
Rubber coated conveyor rollers are a vital component in many industrial applications, offering a combination of durability, flexibility, and enhanced grip. These rollers are designed to improve the handling and movement of materials, providing better control and reducing the risk of slippage. This section will explore the key features and benefits of rubber coated conveyor rollers, highlighting their role in enhancing the performance and efficiency of conveyor systems.
Key Features of Rubber Coated Conveyor Rollers
- Enhanced Grip and Traction One of the primary features of rubber coated conveyor rollers is their enhanced grip and traction. The rubber coating provides a high-friction surface that significantly reduces the risk of slippage. This improved traction ensures that materials are securely moved along the conveyor system, maintaining consistent flow and preventing disruptions.
- Shock Absorption Rubber coated rollers are designed to absorb shock and vibrations during the transportation of materials. This shock absorption capability is particularly beneficial in applications where materials are loaded onto the conveyor with force, such as in mining or heavy manufacturing. By absorbing the impact, rubber coated rollers help to protect both the conveyor system and the materials being transported from damage.
- Noise Reduction The rubber coating on these rollers also contributes to noise reduction in conveyor systems. By dampening vibrations and reducing metal-to-metal contact, rubber coated rollers help to create a quieter working environment. This noise reduction is especially important in industries where maintaining a low noise level is crucial for worker comfort and safety.
- Durability and Longevity Rubber coated conveyor rollers are known for their durability and long service life. The rubber coating provides a protective layer that resists wear and tear, extending the lifespan of the rollers. This durability makes them suitable for heavy-duty applications and environments where the rollers are subjected to constant use and harsh conditions.
- Flexibility and Versatility The flexibility of the rubber coating allows these rollers to adapt to various shapes and sizes of materials, providing uniform pressure and contact. This versatility makes rubber coated rollers suitable for a wide range of applications, from handling delicate items in the electronics industry to transporting heavy loads in manufacturing and logistics.
Benefits of Rubber Coated Conveyor Rollers
- Improved Material Handling The enhanced grip and traction provided by rubber coated conveyor rollers lead to improved material handling. Materials are less likely to slip or shift during transportation, ensuring accurate and efficient movement. This improvement in material handling is crucial for maintaining productivity and reducing waste.
- Protection of Materials Rubber coated rollers offer better protection for the materials being transported. The cushioning effect of the rubber coating helps to prevent damage to delicate or fragile items, ensuring that they reach their destination in good condition. This protection is particularly important in industries such as food processing, electronics, and pharmaceuticals, where product integrity is paramount.
- Enhanced Safety By reducing slippage and providing better control, rubber coated conveyor rollers contribute to a safer working environment. The reduction in the risk of materials falling off the conveyor helps to prevent accidents and injuries. Additionally, the noise reduction benefits of rubber coated rollers create a more comfortable and safer workplace for employees.
- Cost Savings The durability and longevity of rubber coated conveyor rollers result in cost savings over time. With less frequent need for replacements and repairs, maintenance costs are reduced. The improved efficiency and reduced downtime also contribute to overall cost savings, making rubber coated rollers a cost-effective choice for many industries.
- Versatility in Applications Rubber coated conveyor rollers are highly versatile and can be used in a wide range of applications across different industries. Their adaptability to various materials and conditions makes them a valuable asset in industries such as manufacturing, logistics, packaging, and more. This versatility ensures that companies can rely on rubber coated rollers for diverse material handling needs.
Applications of Rubber Coated Conveyor Rollers
- Manufacturing Industry In the manufacturing industry, rubber coated conveyor rollers are used to handle a variety of materials, from raw materials to finished products. Their ability to provide consistent grip and control ensures smooth and efficient production processes. Rubber coated rollers are particularly beneficial in applications where materials need to be moved accurately and quickly, such as in assembly lines and automated systems.
- Logistics and Warehousing The logistics and warehousing sectors rely on rubber coated conveyor rollers for the efficient movement of goods. These rollers help in the transportation of packages, pallets, and other items, ensuring that they are moved securely and efficiently through the warehouse or distribution center. The durability and shock absorption properties of rubber coated rollers make them ideal for handling heavy and bulky items.
- Food Processing Industry In the food processing industry, maintaining hygiene and preventing contamination are critical. Rubber coated conveyor rollers are used to handle food products, ensuring that they are moved smoothly and without damage. The non-toxic and non-reactive properties of the rubber coating make these rollers safe for use in food processing applications.
- Textile Industry The textile industry uses rubber coated conveyor rollers for various fabric processing applications, including dyeing, printing, and finishing. The rollers’ flexibility and ability to provide uniform pressure make them ideal for guiding, smoothing, and pressing fabrics. The cushioning effect of the rubber coating also helps to protect delicate fabrics from damage.
- Electronics Manufacturing In the electronics industry, rubber coated conveyor rollers are used in the assembly and testing of electronic components. The rollers’ ability to handle delicate and high-value components without causing damage is crucial for maintaining product quality. The enhanced grip and control provided by the rubber coating ensure accurate and efficient movement of components through the manufacturing process.
Rubber coated conveyor rollers play a vital role in enhancing the performance and efficiency of conveyor systems across various industries. Their key features, including enhanced grip and traction, shock absorption, noise reduction, durability, and flexibility, make them an invaluable asset for improving material handling and ensuring smooth operation. The benefits of rubber coated rollers, such as improved material handling, protection of materials, enhanced safety, cost savings, and versatility, make them a preferred choice for many industrial applications. By understanding the features and benefits of rubber coated conveyor rollers, companies can make informed decisions to optimize their conveyor systems, enhance productivity, and achieve better results.
Silicone Conveyor Roller: Maintenance Tips for Silicone Conveyor Roller
Silicone conveyor rollers are an integral part of various industrial applications, known for their durability, heat resistance, and non-stick properties. To maximize their lifespan and maintain their performance, regular maintenance is crucial. This section will provide practical advice on maintaining and extending the life of silicone conveyor rollers, ensuring they continue to operate efficiently and effectively in your production processes.
Regular Inspection and Cleaning
- Routine Inspections Conducting regular inspections of your silicone conveyor rollers is essential for early detection of potential issues. Look for signs of wear and tear, such as cracks, abrasions, or deformation. Regular inspections allow you to identify problems before they escalate, preventing costly downtime and repairs.
- Cleaning Procedures Keeping your silicone conveyor rollers clean is vital for maintaining their performance. Accumulated dirt, debris, and residues can affect the rollers’ grip and efficiency. Use appropriate cleaning agents that do not damage the silicone material. For instance, mild detergents or specialized silicone roller cleaners can effectively remove contaminants without harming the rollers.
- Frequency of Cleaning The frequency of cleaning depends on the specific application and the environment in which the rollers operate. In industries with high levels of dust or residue, such as food processing or printing, more frequent cleaning may be necessary. Establish a cleaning schedule based on the operating conditions and follow it diligently to ensure optimal roller performance.
Lubrication and Material Compatibility
- Proper Lubrication While silicone rollers generally have self-lubricating properties, some applications may benefit from additional lubrication. Use lubricants that are compatible with silicone materials to avoid degradation. Avoid petroleum-based lubricants, as they can cause the silicone to swell or break down. Silicone-based or dry lubricants are typically the best choices.
- Material Compatibility Ensure that the materials being transported on silicone conveyor rollers are compatible with silicone. Certain chemicals or materials can react with silicone, causing it to degrade or lose its properties. Conduct compatibility tests if necessary to ensure the longevity of your rollers.
Preventive Maintenance and Roller Alignment
- Preventive Maintenance Plans Implement a preventive maintenance plan that includes regular inspections, cleaning, and lubrication. Document all maintenance activities and keep a detailed log to track the condition of the rollers and the effectiveness of your maintenance efforts. Preventive maintenance helps in identifying and addressing potential issues before they cause significant problems.
- Roller Alignment Proper alignment of silicone conveyor rollers is crucial for efficient operation. Misaligned rollers can cause uneven wear, increase the risk of slippage, and reduce the overall lifespan of the rollers. Regularly check and adjust the alignment of the rollers to ensure they are parallel and properly positioned within the conveyor system.
Replacement and Handling
- Timely Replacement Knowing when to replace silicone conveyor rollers is essential for maintaining optimal performance. Even with regular maintenance, rollers will eventually reach the end of their service life. Monitor the condition of the rollers and replace them when signs of excessive wear or damage are evident. Timely replacement prevents unexpected breakdowns and keeps the production line running smoothly.
- Proper Handling and Storage Proper handling and storage of silicone conveyor rollers can extend their lifespan. Avoid dropping or mishandling the rollers, as this can cause damage to the silicone surface. Store rollers in a clean, dry environment away from direct sunlight and extreme temperatures to prevent degradation.
Troubleshooting Common Issues
- Addressing Slippage Slippage is a common issue that can occur with silicone conveyor rollers. If you notice slippage, check for contaminants on the roller surface and clean them thoroughly. Ensure that the rollers are properly aligned and that the tension of the conveyor belt is appropriate. In some cases, applying a compatible grip tape can enhance the traction and reduce slippage.
- Dealing with Wear and Tear Wear and tear are inevitable with regular use of silicone conveyor rollers. Monitor the rollers for signs of wear, such as thinning of the silicone coating or visible abrasions. Address these issues promptly by either resurfacing the rollers or replacing them if necessary. Implementing regular maintenance practices can minimize wear and extend the life of the rollers.
- Temperature-Related Issues Silicone conveyor rollers are known for their heat resistance, but extreme temperatures can still affect their performance. Ensure that the operating environment is within the recommended temperature range for silicone rollers. If the rollers are exposed to high temperatures, monitor them closely for signs of thermal degradation and adjust the maintenance schedule accordingly.
Best Practices for Maintenance
- Training and Education Provide training and education to maintenance personnel on the specific requirements of silicone conveyor rollers. Ensure that they are familiar with the proper cleaning, lubrication, and inspection techniques. Educated maintenance staff can perform tasks more effectively and identify potential issues early.
- Using Quality Replacement Parts When replacing silicone conveyor rollers or components, use high-quality parts from reputable suppliers. Quality replacement parts ensure compatibility and reliability, reducing the risk of premature failure and maintaining the performance of the conveyor system.
- Customizing Maintenance Plans Customize your maintenance plan based on the specific needs of your operation. Consider factors such as the type of materials being transported, the operating environment, and the production volume. Tailoring the maintenance plan to your unique requirements ensures that the silicone conveyor rollers receive the appropriate care and attention.
Benefits of Regular Maintenance
- Extended Roller Lifespan Regular maintenance significantly extends the lifespan of silicone conveyor rollers. By addressing issues promptly and performing routine cleaning and lubrication, you can maximize the durability and performance of the rollers, reducing the need for frequent replacements.
- Improved Efficiency and Productivity Well-maintained silicone conveyor rollers contribute to the overall efficiency and productivity of the conveyor system. Reduced downtime, fewer interruptions, and consistent material handling result in smoother operations and higher production rates.
- Cost Savings Investing in regular maintenance can lead to substantial cost savings over time. Preventive maintenance helps avoid costly repairs and replacements, minimizes downtime, and extends the service life of the rollers. The cost of regular maintenance is often much lower than the expenses associated with unexpected breakdowns and emergency repairs.
- Enhanced Safety Proper maintenance of silicone conveyor rollers enhances the safety of the conveyor system. By reducing the risk of slippage, misalignment, and other issues, maintenance helps prevent accidents and injuries. A well-maintained system provides a safer working environment for employees.
Maintaining and extending the life of silicone conveyor roller requires a proactive approach that includes regular inspections, cleaning, lubrication, and timely replacements. By implementing preventive maintenance plans, ensuring proper alignment, and addressing common issues promptly, you can maximize the performance and longevity of your silicone conveyor rollers. These maintenance tips not only improve the efficiency and productivity of your conveyor system but also contribute to cost savings and enhanced safety. Understanding the importance of regular maintenance and following best practices will ensure that your silicone conveyor rollers continue to operate at their best, supporting the smooth and efficient functioning of your industrial processes.
FAQs about Silicone Conveyor Roller
Silicone rollers are widely used in various industrial applications due to their unique properties. These rollers are made from silicone rubber, which is known for its high temperature resistance, flexibility, and durability. Silicone rollers are commonly used in printing and laminating industries where heat and pressure are applied. They are ideal for applications involving high temperatures because silicone can withstand heat without degrading. Additionally, silicone rollers provide excellent release properties, making them suitable for use in processes where non-stick surfaces are required, such as in the production of adhesive tapes, labels, and films. The flexibility and resilience of silicone also make these rollers effective in providing uniform pressure distribution, ensuring high-quality results in applications like embossing and coating.
Conveyor systems utilize various types of rollers, each designed to serve a specific function within the system. The primary types of rollers used in conveyors include:
Gravity Rollers: These are non-powered rollers that rely on the force of gravity to move items along the conveyor. They are commonly used in warehouses and assembly lines for the transportation of lightweight to moderately heavy items.
Powered Rollers: These rollers are driven by motors or other mechanical means. They are used in applications where controlled movement and precise handling of items are required. Powered rollers are ideal for heavy-duty and high-speed conveyor systems.
Impact Rollers: These rollers are designed to absorb impact and reduce damage to the conveyor and the items being transported. They are typically placed at points where materials are loaded onto the conveyor.
Guide Rollers: These rollers help to keep items aligned and in place as they move along the conveyor. They are essential in ensuring smooth and accurate transportation, particularly in systems that handle irregularly shaped items.
Each type of roller is selected based on the specific needs of the conveyor system and the nature of the items being transported.
Conveyor rollers are made from a variety of materials, each chosen for its specific properties to suit different applications. Common materials used for conveyor rollers include:
Steel: Steel rollers are durable and can handle heavy loads, making them ideal for heavy-duty applications such as in mining, quarrying, and industrial manufacturing. They are resistant to wear and can operate in harsh environments.
Aluminum: Aluminum rollers are lightweight and corrosion-resistant, making them suitable for applications where weight is a concern or where the rollers are exposed to moisture and chemicals. They are often used in food processing and packaging industries.
Plastic: Plastic rollers, typically made from materials like PVC or polyethylene, are lightweight, corrosion-resistant, and suitable for handling lighter loads. They are commonly used in the food, pharmaceutical, and electronics industries.
Rubber-Coated: Rubber-coated rollers provide additional grip and cushioning, making them ideal for handling delicate or fragile items. The rubber coating also helps to reduce noise and absorb shock.
The choice of material depends on factors such as load capacity, environmental conditions, and the specific requirements of the conveyor system.
Rubber rollers are versatile components used in a wide range of industrial applications due to their flexibility, durability, and cushioning properties. Some of the common uses of rubber rollers include:
Printing: In the printing industry, rubber rollers are used to transfer ink onto paper or other substrates. Their ability to provide even pressure distribution ensures high-quality prints.
Conveying: Rubber rollers are used in conveyor systems to transport materials. The rubber surface provides excellent grip, reducing the risk of slippage and ensuring smooth movement of items.
Laminating: Rubber rollers are employed in laminating processes to apply pressure and heat, ensuring proper adhesion of layers. They are commonly used in the production of laminated sheets, films, and packaging materials.
Textile Processing: In the textile industry, rubber rollers are used in various stages of fabric processing, including dyeing, printing, and finishing. They help in guiding, smoothing, and pressing the fabric.
Metalworking: Rubber rollers are used in metalworking for applications such as polishing, finishing, and coating metal surfaces. The rubber coating helps to protect delicate surfaces and improve the quality of the finish.
The adaptability and resilience of rubber rollers make them suitable for numerous applications across different industries, providing reliable performance and contributing to the efficiency of various processes.
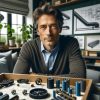
Jordan Smith, a seasoned professional with over 20 years of experience in the conveyor system industry. Jordan’s expertise lies in providing comprehensive solutions for conveyor rollers, belts, and accessories, catering to a wide range of industrial needs. From initial design and configuration to installation and meticulous troubleshooting, Jordan is adept at handling all aspects of conveyor system management. Whether you’re looking to upgrade your production line with efficient conveyor belts, require custom conveyor rollers for specific operations, or need expert advice on selecting the right conveyor accessories for your facility, Jordan is your reliable consultant. For any inquiries or assistance with conveyor system optimization, Jordan is available to share his wealth of knowledge and experience. Feel free to reach out at any time for professional guidance on all matters related to conveyor rollers, belts, and accessories.