Common Issues Requiring Conveyor Roller Repair
Conveyor roller repair is crucial for maintaining the overall efficiency of conveyor systems. Regular maintenance and timely repairs of conveyor rollers ensure smooth operation, preventing unexpected breakdowns that can halt production lines. Well-maintained rollers reduce friction and wear on the conveyor belt, extending its lifespan and minimizing downtime. Furthermore, addressing issues promptly through conveyor roller repair enhances safety by preventing accidents caused by faulty equipment. Investing in regular conveyor roller repair not only boosts productivity but also reduces long-term operational costs by avoiding major repairs or replacements. Therefore, the importance of conveyor roller repair cannot be overstated for any industry relying on conveyor systems.
Common Issues Requiring Conveyor Roller Repair
Conveyor systems are integral to many industrial operations, facilitating the smooth and efficient movement of materials. However, like any mechanical system, conveyor rollers are subject to wear and tear, necessitating regular maintenance and occasional repairs. Understanding common issues that require conveyor roller repair is crucial for maintaining the efficiency and longevity of the conveyor system. This section will identify and describe typical problems that necessitate conveyor roller repair, such as misalignment, wear and tear, and material buildup.
Misalignment
One of the most common issues requiring conveyor roller repair is misalignment. Misalignment can occur for various reasons, including improper installation, uneven loads, or structural shifts within the conveyor framework. When rollers are misaligned, the conveyor belt can drift off track, causing uneven wear and potential damage to both the belt and the rollers. Misalignment can also lead to increased friction and resistance, which can reduce the efficiency of the conveyor system and increase energy consumption.
Detecting misalignment early is essential to prevent more severe damage. Regular inspections should be conducted to check for signs of belt drift, unusual noises, or visible gaps between rollers and the belt. Correcting misalignment typically involves adjusting the position of the rollers and ensuring that the conveyor frame is level and stable. In some cases, more extensive repairs may be required if the misalignment has caused significant wear or damage.
Wear and Tear
Wear and tear is an inevitable consequence of continuous operation and is a primary reason for conveyor roller repair. Rollers are subjected to constant friction and pressure as materials move along the conveyor system. Over time, this can lead to surface degradation, reduced roller diameter, and even cracking or pitting. Worn rollers can negatively impact the performance of the conveyor system by increasing friction and resistance, leading to higher energy consumption and reduced throughput.
Regular monitoring and maintenance can help mitigate the effects of wear and tear. Roller surfaces should be inspected for signs of wear, such as thinning, rough patches, or cracks. In many cases, worn rollers can be resurfaced to restore their original dimensions and smoothness. However, if the damage is extensive, the rollers may need to be replaced entirely. Using high-quality materials and lubricants can also help extend the lifespan of the rollers and reduce the frequency of repairs.
Material Buildup
Material buildup is another common issue that necessitates conveyor roller repair. As materials are transported along the conveyor, debris, dust, and residues can accumulate on the rollers. This buildup can cause the rollers to become sticky or uneven, leading to increased friction and potential damage to the conveyor belt. Material buildup can also contribute to misalignment and wear and tear, compounding the need for repairs.
Preventing material buildup requires regular cleaning and maintenance of the conveyor system. Rollers should be inspected frequently and cleaned to remove any accumulated debris. In addition, using appropriate cleaning agents and techniques can help prevent the buildup of sticky or abrasive materials. Implementing a regular cleaning schedule can significantly reduce the frequency and severity of conveyor roller repair, ensuring smooth and efficient operation.
Bearing Failure
Bearings are essential for the smooth and frictionless rotation of rollers in a friction drive roller conveyor system. However, bearings are also susceptible to wear and tear, contamination, and misalignment, which can lead to bearing failure. When bearings fail, the rollers can become noisy, generate excessive heat, and eventually seize up, causing significant disruptions to the conveyor system.
Identifying bearing failure early can help prevent more extensive damage to the rollers and the conveyor system. Regular inspections should include checking for signs of bearing wear, such as unusual noises, vibrations, or heat. Lubrication is essential to prevent bearing failure; bearings should be regularly lubricated according to the manufacturer’s specifications. If bearings are damaged or worn, they should be replaced promptly to avoid further issues.
Structural Damage
Structural damage to the conveyor frame or support structures can also necessitate conveyor roller repair. Structural damage can occur due to accidents, overloading, or long-term wear and tear. When the conveyor frame is damaged, it can lead to misalignment, increased wear on the rollers and belt, and reduced overall efficiency.
Inspecting the conveyor frame and support structures for signs of damage should be part of a regular maintenance routine. Any cracks, bends, or deformities should be addressed promptly to prevent further issues. Repairing structural damage may involve welding, reinforcing, or replacing damaged components. Ensuring that the conveyor is not overloaded and that loads are evenly distributed can help prevent structural damage and reduce the need for repairs.
Environmental Factors
Environmental factors, such as exposure to moisture, chemicals, and extreme temperatures, can also contribute to the need for conveyor roller repair. Moisture can cause rust and corrosion, while chemicals can degrade roller materials and lubricants. Extreme temperatures can lead to thermal expansion and contraction, causing misalignment and increased wear.
Protecting the conveyor system from environmental factors is essential to reduce the frequency of repairs. Using corrosion-resistant materials, applying protective coatings, and ensuring proper ventilation can help mitigate the effects of moisture, chemicals, and temperature extremes. Regular inspections and maintenance can also help identify and address environmental damage before it leads to more severe issues.
Conveyor Roller Repair Techniques
Conveyor roller repair is a multifaceted process that requires a thorough understanding of various techniques to ensure effective and lasting repairs. Different methods are employed depending on the type and extent of damage to the rollers. This section will outline various methods used for repairing conveyor rollers, including resurfacing, rebalancing, and bearing replacement.
Resurfacing
Resurfacing is a common technique used in conveyor roller repair to restore the surface of worn or damaged rollers. This process involves removing the worn or damaged surface layer and applying a new layer of material to restore the roller’s original dimensions and smoothness. Resurfacing can be done using various methods, such as grinding, polishing, or applying a new coating.
Grinding involves removing the damaged surface layer using abrasive tools to create a smooth and even surface. This method is suitable for rollers with minor surface wear or damage. Polishing is a similar process that uses finer abrasives to achieve a higher level of smoothness and finish. Applying a new coating, such as rubber or polyurethane, can provide additional protection and enhance the roller’s performance.
Resurfacing is a cost-effective way to extend the lifespan of conveyor rollers and reduce the need for replacement. It is essential to choose the appropriate resurfacing method and materials based on the type of roller and the operating conditions to ensure optimal results.
Rebalancing
Rebalancing is another crucial technique in conveyor roller repair, particularly for rollers that have become unbalanced due to wear, misalignment, or structural damage. An unbalanced roller can cause vibrations, increased wear on the conveyor belt, and reduced efficiency.
Rebalancing involves adjusting the roller’s weight distribution to ensure even rotation and smooth operation. This process can include adding or removing material from specific areas of the roller, aligning the roller within the conveyor frame, and ensuring that the bearings are properly aligned and lubricated.
Balancing equipment and techniques vary depending on the type and size of the roller. Precision instruments, such as dynamic balancers, can measure and correct imbalances with high accuracy. Ensuring that rollers are balanced is essential for maintaining the overall efficiency and longevity of the conveyor system.
Bearing Replacement
Bearings are critical components of conveyor rollers, allowing smooth and frictionless rotation. Over time, bearings can wear out, become contaminated, or fail due to lack of lubrication or misalignment. Bearing replacement is a common and necessary part of conveyor roller repair to maintain optimal performance.
Replacing bearings involves removing the old or damaged bearings and installing new ones. The process can vary depending on the type of bearing and roller. Some bearings are press-fit, requiring specialized tools to remove and install, while others are secured with set screws or bolts. It is essential to choose the correct type and size of bearing to ensure compatibility and optimal performance.
Proper lubrication is crucial for the longevity of the new bearings. Bearings should be lubricated according to the manufacturer’s specifications, and the lubrication schedule should be part of the regular maintenance routine. In addition to replacing bearings, it is also essential to check and correct any underlying issues, such as misalignment or contamination, that may have contributed to the bearing failure.
Welding and Structural Repairs
In cases where conveyor rollers have suffered significant structural damage, welding and other structural repair techniques may be required. Structural repairs can include fixing cracks, reinforcing weak areas, and replacing damaged sections of the roller or conveyor frame.
Welding is a common technique used to repair cracks or fractures in metal rollers or frames. This process involves heating and fusing the damaged metal to create a strong and durable bond. Reinforcing weak areas may involve adding additional material or supports to strengthen the roller or frame. In some cases, damaged sections may need to be cut out and replaced with new material. If you need to replace a damaged roller, you can look for a metal roller for sale to find a suitable replacement.
Structural repairs require skilled technicians with experience in welding and fabrication. It is essential to ensure that the repairs are performed to a high standard to prevent further damage and maintain the safety and efficiency of the conveyor system.
Lubrication and Cleaning
Lubrication and cleaning are essential maintenance practices that play a significant role in conveyor roller repair. Proper lubrication reduces friction and wear, while regular cleaning prevents material buildup and contamination.
Lubrication involves applying appropriate lubricants to the bearings and moving parts of the rollers. The type and frequency of lubrication depend on the operating conditions and manufacturer specifications. Over-lubrication can attract dust and debris, leading to contamination, while under-lubrication can cause increased friction and wear.
Regular cleaning involves removing debris, dust, and material buildup from the rollers and conveyor system. Cleaning agents and techniques should be chosen based on the type of materials being transported and the operating environment. Implementing a regular cleaning and lubrication schedule can significantly reduce the frequency and severity of conveyor roller repair, ensuring smooth and efficient operation.
Conveyor Roller Repair: Essential Tools and DIY Tips
Effective maintenance and timely repair of conveyor rollers are critical to ensuring smooth operations and minimizing downtime in various industrial settings. Understanding the tools required for conveyor roller repair and knowing how to undertake DIY repairs can save time and money. This detailed guide will explore the essential tools and equipment needed for effective conveyor roller repair and provide practical DIY tips for those looking to manage repairs independently.
Tools and Equipment for Conveyor Roller Repair
Repairing conveyor rollers involves various tasks, from diagnosing issues to replacing worn-out parts. Having the right tools and equipment is essential for efficient and successful repairs. Here are some of the key tools and equipment necessary for conveyor roller repair:
1. Welding Machines
Welding machines are crucial for repairing and reinforcing conveyor rollers, especially when dealing with metal components. Welding can help fix cracks, reattach broken parts, and ensure the structural integrity of the rollers. Types of welding machines commonly used include MIG welders, TIG welders, and arc welders. Each type has its advantages depending on the specific repair needs:
- MIG Welders: Suitable for quick and easy welding tasks, providing strong welds with minimal cleanup.
- TIG Welders: Ideal for precision welding, offering clean and high-quality welds, especially on thin materials.
- Arc Welders: Robust and versatile, suitable for heavy-duty repairs on thicker materials.
2. Alignment Tools
Proper alignment of conveyor rollers is crucial to prevent uneven wear and ensure smooth operation. Misalignment can cause excessive friction, leading to premature failure of the rollers and the conveyor belt. Essential alignment tools include:
- Laser Alignment Systems: These provide precise alignment, reducing the risk of human error and ensuring optimal performance.
- Dial Indicators: Useful for measuring alignment deviations and ensuring rollers are perfectly aligned within the conveyor system.
- Straight Edges and Levels: Simple yet effective tools for basic alignment tasks, ensuring rollers are parallel and level.
3. Lubrication Systems
Lubrication is vital for reducing friction and wear on conveyor rollers. Proper lubrication systems ensure that the rollers operate smoothly and efficiently. Essential lubrication tools include:
- Grease Guns: Used to apply lubricant to roller bearings and other moving parts, ensuring they remain well-lubricated.
- Automatic Lubricators: These provide continuous lubrication, reducing the need for manual intervention and ensuring consistent performance.
- Oilers and Lubricant Applicators: Various types of oilers and applicators are available for applying different types of lubricants to specific areas of the conveyor rollers.
4. Bearing Pullers
Bearing pullers are essential for removing and replacing roller bearings without causing damage. Proper bearing maintenance is crucial for the smooth operation of conveyor rollers. Types of bearing pullers include:
- Two-Jaw and Three-Jaw Pullers: Versatile and commonly used for removing bearings from various positions.
- Hydraulic Pullers: Provide greater force and ease of use, especially for larger and more stubborn bearings.
- Slide Hammer Pullers: Ideal for pulling bearings from tight or hard-to-reach spaces.
5. Hand Tools and Power Tools
A variety of hand tools and power tools are essential for conveyor roller repair, including:
- Wrenches and Socket Sets: For tightening and loosening bolts and nuts on roller components.
- Screwdrivers: Necessary for disassembling and reassembling roller parts.
- Impact Wrenches: Provide extra torque for loosening tight or rusted bolts.
- Grinders and Sanders: Useful for smoothing and preparing surfaces for welding or other repairs.
6. Inspection and Diagnostic Tools
Effective conveyor roller repair starts with accurate diagnosis of the issues. Inspection and diagnostic tools include:
- Inspection Cameras: Allow for detailed visual inspections of hard-to-reach areas within the conveyor system.
- Thermal Imagers: Detect heat patterns that indicate friction or overheating, helping identify potential issues.
- Vibration Analyzers: Measure vibration levels to detect imbalances or misalignments in the rollers.
DIY Conveyor Roller Repair Tips
Undertaking conveyor roller repair yourself can be a cost-effective solution, provided you follow proper safety precautions and have a good understanding of the repair process. Here are some practical DIY tips for conveyor roller repair:
1. Safety Precautions
Safety should always be the top priority when performing conveyor roller repair. Here are some key safety precautions to follow:
- Wear Appropriate PPE: Personal protective equipment (PPE) such as gloves, safety goggles, and steel-toed boots should always be worn to protect against injuries.
- Lockout/Tagout Procedures: Ensure the conveyor system is properly shut down and locked out to prevent accidental startup during repair.
- Work in a Well-Ventilated Area: Ensure adequate ventilation, especially when using welding machines or working with lubricants and solvents.
2. Identify the Problem
Accurate diagnosis of the issue is crucial for effective repair. Common problems with conveyor rollers include misalignment, bearing failure, and surface damage. Use inspection and diagnostic tools to identify the specific issue before proceeding with repairs.
3. Step-by-Step Repair Guide
Here’s a general step-by-step guide to DIY conveyor roller repair:
- Disassemble the Roller: Remove the roller from the conveyor system and disassemble it using appropriate tools such as wrenches and screwdrivers.
- Inspect and Clean Components: Inspect all components for wear and damage. Clean the roller and its parts thoroughly to remove dirt, debris, and old lubricant.
- Replace Damaged Parts: Replace any damaged or worn-out parts, such as bearings or seals, using suitable replacement parts.
- Align and Reassemble: Reassemble the roller, ensuring all components are properly aligned. Use alignment tools to verify proper alignment.
- Lubricate: Apply the appropriate lubricant to the bearings and other moving parts. Use grease guns or automatic lubricators for consistent application.
- Test the Roller: Reinstall the roller in the conveyor system and test it to ensure it operates smoothly and without issues.
4. Regular Maintenance
Regular maintenance is essential to prevent issues and extend the lifespan of your conveyor rollers. Establish a maintenance schedule that includes regular inspections, cleaning, lubrication, and alignment checks. Keeping detailed records of maintenance activities can help track the condition of the rollers and plan for timely repairs or replacements.
5. Common Troubleshooting Tips
Here are some common troubleshooting tips for conveyor roller issues:
- Slippage: If the roller is slipping, check for contamination on the roller surface and clean it. Ensure proper tension in the conveyor belt and consider using grip tape for additional traction.
- Noise: Unusual noises can indicate misalignment or bearing failure. Inspect the roller and bearings, realign if necessary, and replace any damaged bearings.
- Overheating: Overheating may be caused by insufficient lubrication or excessive friction. Ensure proper lubrication and check for misalignment or other issues causing friction.
6. Know When to Call a Professional
While DIY repair can be cost-effective, some repairs may require professional expertise. If you encounter complex issues or are unsure about any aspect of the repair, it’s best to call a professional to ensure the repair is done correctly and safely.
Conveyor roller repair is a critical aspect of maintaining the efficiency and longevity of your conveyor system. Having the right tools and equipment, such as welding machines, alignment tools, and lubrication systems, is essential for effective repair. Additionally, following practical DIY tips, including safety precautions, accurate problem diagnosis, and regular maintenance, can help you successfully undertake conveyor roller repair yourself. By understanding the importance of proper maintenance and repair, you can ensure the smooth operation of your conveyor system, reduce downtime, and extend the life of your conveyor rollers.
Cost Considerations in Conveyor Roller Repair
When it comes to maintaining the efficiency and functionality of a conveyor system, timely conveyor roller repair is essential. However, understanding the cost implications of such repairs can be complex due to various influencing factors. This section will provide a comprehensive examination of the factors that affect the cost of conveyor roller repair, including the extent of damage, the type of roller, and labor charges. By understanding these elements, you can better manage your maintenance budget and ensure cost-effective repairs.
Factors Influencing the Cost of Conveyor Roller Repair
1. Extent of Damage
The degree of damage to the conveyor rollers is one of the most significant factors affecting repair costs. Minor issues, such as surface wear or slight misalignment, can often be resolved with minimal expense. However, more severe problems, such as significant structural damage or complete bearing failure, can require extensive repairs or even replacement of parts, leading to higher costs.
- Minor Damage: Surface wear, small dents, or minor misalignment can usually be repaired quickly and inexpensively. These repairs might involve simple tasks such as cleaning, realignment, or minor welding.
- Moderate Damage: Issues like worn-out bearings, significant dents, or misaligned rollers might require more time and parts to repair. This can involve replacing bearings, more extensive welding, or realigning multiple rollers.
- Severe Damage: Severe structural damage, cracked rollers, or broken components often require substantial repairs or complete replacement of the roller. This not only increases material costs but also labor costs due to the complexity and time required for the repair.
2. Type of Roller
Different types of conveyor rollers have varying repair costs due to their construction, materials, and specific uses. Here are some common types of rollers and how they impact repair costs:
- Steel Rollers: These are durable and commonly used in heavy-duty applications. Repairing steel rollers can involve welding, replacing bearings, and realignment, which can be moderately expensive depending on the damage.
- Plastic Rollers: Often used in lighter applications, plastic rollers are generally cheaper to repair but might not be as durable as steel rollers. Repairing plastic rollers can involve replacing damaged sections or bearings, usually at a lower cost.
- Rubber-Coated Rollers: These rollers provide additional grip and cushioning. Repairing rubber-coated rollers can be more expensive due to the need to replace the rubber coating in addition to any structural repairs.
- Silicone Rollers: Used in specific applications requiring high heat resistance or non-stick surfaces. Repairing silicone rollers can be costly due to the specialized materials and processes involved.
3. Labor Charges
Labor costs are a significant component of conveyor roller repair expenses. These costs can vary widely depending on the complexity of the repair, the time required, and the expertise needed. Here are some factors that influence labor charges:
- Hourly Rates: The hourly rates for repair technicians can vary based on their experience, the region, and the complexity of the repair. Skilled technicians with specialized knowledge of conveyor systems may charge higher rates.
- Repair Time: The amount of time required for the repair directly impacts labor costs. Simple repairs may take just a few hours, while complex repairs involving multiple rollers or significant damage can take several days.
- Availability of Technicians: In some areas, there may be a limited number of qualified technicians available, which can drive up labor costs. Additionally, emergency repairs or after-hours work can incur premium rates.
- On-Site vs. Off-Site Repair: Repairs performed on-site can save time and reduce downtime for the conveyor system but may be more expensive due to travel costs and on-site service charges. Off-site repairs may require transporting the rollers to a repair facility, which adds to the overall cost.
Additional Cost Considerations
1. Replacement Parts
The cost of replacement parts can significantly influence the overall repair cost. High-quality parts may be more expensive but can provide better performance and longer lifespan, reducing the need for frequent repairs. It’s essential to balance the cost of parts with their quality and suitability for the specific application.
- Bearings: Replacing worn-out or damaged bearings is a common repair task. High-quality bearings can be costly, but they ensure smooth operation and longevity of the rollers.
- Seals and Gaskets: These components help protect the internal parts of the rollers from contaminants. Replacing seals and gaskets is usually a minor cost but essential for maintaining roller performance.
- Roller Surface: Repairing or replacing the surface material of rollers, such as rubber or silicone coatings, can add to the cost. Specialized coatings may be more expensive but necessary for specific applications.
2. Preventive Maintenance
Investing in preventive maintenance can help reduce the frequency and severity of repairs, ultimately lowering the long-term costs associated with conveyor roller repair. Regular inspections, lubrication, and alignment checks can identify potential issues before they become major problems.
- Regular Inspections: Conducting routine inspections allows for early detection of wear and damage, enabling timely repairs that are usually less expensive than major overhauls.
- Lubrication: Proper lubrication reduces friction and wear on roller components, extending their lifespan and reducing the need for frequent repairs.
- Alignment: Ensuring rollers are correctly aligned prevents uneven wear and reduces the risk of damage to both rollers and conveyor belts.
3. Downtime Costs
The cost of conveyor roller repair is not limited to the direct expenses of parts and labor. Downtime associated with repairs can have a significant financial impact, particularly in industries where continuous operation is critical. Minimizing downtime through efficient repair processes and preventive maintenance is essential for controlling overall costs.
- Production Losses: Downtime can lead to lost production time, affecting overall productivity and profitability. Planning repairs during scheduled maintenance windows can help mitigate this impact.
- Emergency Repairs: Unplanned downtime due to sudden roller failure may require emergency repairs, which can be more expensive due to expedited service charges and potential overtime labor costs.
4. Professional vs. DIY Repairs
Deciding between professional and DIY repairs can also influence the cost of conveyor roller repair. While DIY repairs may seem cost-effective initially, they require proper tools, expertise, and time. Professional repairs, although more expensive, ensure high-quality work and reduce the risk of further damage or safety issues.
- DIY Repairs: Suitable for minor repairs and maintenance tasks, provided the necessary skills and tools are available. DIY repairs can save labor costs but may result in higher costs if mistakes are made.
- Professional Repairs: Recommended for complex repairs and critical systems where precision and reliability are paramount. Professional services ensure thorough and accurate repairs, reducing the risk of recurring issues.
Understanding the cost considerations in conveyor roller repair is essential for effective maintenance planning and budget management. The extent of damage, type of roller, labor charges, and additional factors such as replacement parts, preventive maintenance, and downtime all contribute to the overall cost of repairs. By carefully evaluating these factors and investing in preventive measures, you can minimize repair costs and ensure the reliable operation of your conveyor system. Whether opting for professional services or undertaking DIY repairs, making informed decisions will help maintain the efficiency and longevity of your conveyor rollers.
Professional Conveyor Roller Repair Services
In the fast-paced world of industrial operations, maintaining the efficiency and reliability of conveyor systems is paramount. Conveyor roller repair is a critical aspect of this maintenance, ensuring that the systems run smoothly and without interruption. While some minor repairs and maintenance tasks can be handled in-house, there are significant advantages to hiring professional services for conveyor roller repair. This section will discuss the benefits of engaging professional services, emphasizing expertise, efficiency, and long-term savings.
Expertise and Experience
Professional conveyor roller repair services bring a wealth of expertise and experience to the table. These companies employ skilled technicians who are well-versed in the intricacies of conveyor systems and their components. Their deep understanding of various types of conveyor rollers, such as gravity rollers, powered rollers, and idler rollers, allows them to diagnose and address issues accurately and efficiently.
Professionals are trained to identify subtle signs of wear and potential problems that might go unnoticed by untrained personnel. They can conduct thorough inspections and use advanced diagnostic tools to pinpoint issues, ensuring that repairs are both precise and effective. This level of expertise is crucial for maintaining the optimal performance of conveyor systems and preventing minor issues from escalating into major problems.
Efficiency and Reduced Downtime
One of the most significant advantages of hiring professional services for conveyor roller repair is the efficiency they bring to the process. Professionals are equipped with specialized tools and equipment designed specifically for conveyor roller repair, enabling them to perform repairs quickly and effectively. Their familiarity with the repair process and access to high-quality replacement parts ensure that repairs are completed in a timely manner.
Efficient repairs translate to reduced downtime for your conveyor systems. Minimizing downtime is crucial in industrial operations, where even a short interruption can lead to significant production losses. By hiring professionals, you can ensure that your conveyor systems are up and running as quickly as possible, maintaining productivity and meeting production targets.
Long-Term Savings
Investing in professional conveyor roller repair services can lead to substantial long-term savings. While the upfront cost of hiring professionals may seem higher than handling repairs in-house, the long-term benefits far outweigh the initial expense. Professional repairs are often more durable and reliable, reducing the likelihood of recurring issues and the need for frequent repairs.
Additionally, professionals can provide valuable advice on maintenance practices and system improvements that can enhance the longevity and performance of your conveyor rollers. Implementing their recommendations can lead to fewer breakdowns, lower maintenance costs, and extended equipment life, resulting in significant cost savings over time.
Safety and Compliance
Safety is a paramount concern in industrial environments. Professional conveyor roller repair services prioritize safety in all their operations. Their technicians are trained in industry best practices and safety protocols, ensuring that repairs are conducted safely and in compliance with relevant regulations. This focus on safety helps prevent accidents and injuries, protecting both your workforce and your equipment.
Compliance with industry standards and regulations is another critical aspect of professional services. Professionals stay updated on the latest regulatory requirements and ensure that all repairs meet or exceed these standards. This compliance not only enhances safety but also helps avoid potential fines and legal issues associated with non-compliance.
Comprehensive Services
Professional conveyor roller repair companies offer comprehensive services that go beyond simple repairs. These services can include preventive maintenance programs, system audits, and performance optimization. By taking a holistic approach to conveyor system maintenance, professionals can identify and address underlying issues that may affect the overall efficiency and reliability of your system.
Preventive maintenance programs, in particular, are invaluable for reducing the frequency and severity of conveyor roller repairs. Professionals can develop customized maintenance schedules based on your specific operational needs, ensuring that your conveyor rollers are regularly inspected, cleaned, and lubricated. This proactive approach helps catch potential problems early, preventing costly breakdowns and extending the life of your equipment.
Access to Advanced Technology
Professional conveyor roller repair services have access to advanced technology and tools that may not be available to in-house maintenance teams. This technology can include precision alignment tools, laser measurement systems, and specialized diagnostic equipment. Utilizing these advanced tools allows professionals to perform repairs with a high degree of accuracy and efficiency.
For example, precision alignment tools can ensure that rollers are perfectly aligned, reducing wear and improving the performance of the conveyor system. Laser measurement systems can detect minute deviations and imperfections that might affect roller performance. By leveraging advanced technology, professional services can provide higher quality repairs that enhance the overall performance and reliability of your conveyor system.
Customized Solutions
Every conveyor system is unique, with its own set of challenges and requirements. Professional conveyor roller repair services can provide customized solutions tailored to your specific needs. They can assess your system, understand your operational requirements, and develop repair and maintenance strategies that address your unique challenges.
Customized solutions can include the selection of specific materials and coatings for rollers that are best suited to your operational environment, recommendations for system upgrades, and the development of maintenance protocols that align with your production schedule. By providing tailored solutions, professional services ensure that your conveyor system operates at peak efficiency, minimizing downtime and maximizing productivity.
Preventive Maintenance to Reduce Conveyor Roller Repair Needs
Preventive maintenance is a proactive approach to maintaining the efficiency and longevity of conveyor systems. By regularly inspecting and servicing conveyor rollers, you can significantly reduce the frequency and severity of repairs, ensuring smooth and reliable operation. This section will suggest preventive maintenance practices that can minimize the need for conveyor roller repair, such as regular inspections and timely lubrication.
Regular Inspections
Conducting regular inspections is one of the most effective preventive maintenance practices for conveyor rollers. Inspections help identify potential issues early, allowing for timely repairs before they escalate into major problems. During inspections, technicians should check for signs of wear, misalignment, material buildup, and other common issues.
Key areas to inspect include:
- Roller Surfaces: Check for signs of wear, such as thinning, rough patches, or cracks. Worn surfaces can increase friction and reduce efficiency.
- Bearings: Inspect bearings for signs of wear, noise, or excessive heat. Properly functioning bearings are essential for smooth roller operation.
- Alignment: Ensure that rollers are properly aligned within the conveyor frame. Misalignment can cause uneven wear and potential damage to the belt and rollers.
- Structural Integrity: Check the conveyor frame and support structures for signs of damage or deformation. Structural issues can affect the alignment and performance of the rollers.
- Material Buildup: Look for debris, dust, or material buildup on the rollers. Buildup can cause rollers to become sticky or uneven, leading to increased wear and potential damage.
Regular inspections should be scheduled based on the operational demands and environmental conditions of your conveyor system. More frequent inspections may be required in harsh or high-use environments.
Timely Lubrication
Proper lubrication is critical for the longevity and performance of conveyor rollers. Lubrication reduces friction, prevents wear, and protects against corrosion and contamination. Bearings and other moving parts should be regularly lubricated according to the manufacturer’s specifications.
When lubricating conveyor rollers, consider the following:
- Type of Lubricant: Use the appropriate lubricant for your specific roller type and operating conditions. High-temperature or high-load environments may require specialized lubricants.
- Frequency: Lubricate rollers at intervals recommended by the manufacturer or based on operational demands. Over-lubrication can attract debris and lead to contamination, while under-lubrication can cause increased wear and friction.
- Application Method: Apply lubricant evenly and thoroughly to all moving parts. Ensure that lubricant reaches the internal components of bearings and other critical areas.
Regular lubrication not only extends the life of conveyor rollers but also enhances the overall efficiency and reliability of the conveyor system.
Cleaning and Debris Removal
Keeping conveyor rollers clean and free of debris is essential for preventing material buildup and ensuring smooth operation. Regular cleaning helps prevent issues such as increased friction, misalignment, and wear.
Effective cleaning practices include:
- Scheduled Cleaning: Develop a regular cleaning schedule based on the type of materials being transported and the operating environment. More frequent cleaning may be required in dusty or abrasive environments.
- Appropriate Cleaning Agents: Use cleaning agents suitable for the materials being transported and the roller surfaces. Avoid harsh chemicals that could damage rollers or conveyor components.
- Thorough Cleaning: Remove all debris, dust, and material buildup from rollers and surrounding areas. Pay special attention to areas where buildup is more likely to occur, such as near bearings and under the conveyor belt.
Regular cleaning not only reduces the need for conveyor roller repair but also improves the overall hygiene and safety of the conveyor system.
Alignment and Adjustment
Ensuring proper alignment and adjustment of conveyor rollers is crucial for maintaining optimal performance and reducing wear. Misalignment can cause uneven wear on rollers and belts, increased friction, and potential damage.
Alignment and adjustment practices include:
- Regular Checks: Conduct regular alignment checks to ensure that rollers are properly aligned within the conveyor frame. Use precision alignment tools for accurate measurements.
- Adjustments: Make necessary adjustments to roller positions and conveyor frame components to correct any misalignment. Ensure that rollers are level and parallel to each other.
- Balancing: Balance rollers to ensure even weight distribution and smooth rotation. Unbalanced rollers can cause vibrations and increased wear.
Proper alignment and adjustment help prevent issues such as belt drift, uneven wear, and increased energy consumption, reducing the need for frequent repairs.
Training and Education
Training and educating maintenance personnel on proper conveyor roller maintenance practices is essential for effective preventive maintenance. Well-trained personnel can identify potential issues early, perform routine maintenance tasks accurately, and implement best practices for repair and lubrication.
Training programs should cover:
- Inspection Techniques: Teach personnel how to conduct thorough inspections and identify signs of wear, misalignment, and material buildup.
- Lubrication Practices: Provide guidance on selecting and applying the appropriate lubricants for different roller types and operating conditions.
- Cleaning Methods: Educate personnel on effective cleaning techniques and the importance of keeping rollers and conveyor systems free of debris.
- Alignment and Adjustment: Train personnel on proper alignment and adjustment procedures to ensure optimal roller performance.
FAQs about Conveyor Roller Repair
Maintaining a conveyor roller involves several key practices to ensure longevity and optimal performance. Firstly, regular inspections are crucial. Check for signs of wear and tear, misalignment, or unusual noises, which can indicate underlying issues. Cleaning the rollers is also essential; remove any debris, dirt, or material buildup that can cause blockages or reduce efficiency. Lubrication plays a vital role in maintenance; ensure that bearings and moving parts are adequately lubricated to minimize friction and wear. It’s also important to check and tighten any loose bolts or connections to prevent accidents or equipment damage. Implementing a preventive maintenance schedule can help identify potential problems before they become severe, reducing downtime and repair costs. By following these steps, you can maintain your conveyor rollers effectively, ensuring smooth operation and extending their lifespan.
The rollers on a conveyor are commonly referred to as “conveyor rollers.” These components are essential parts of a conveyor system, designed to support and transport materials along the conveyor belt. Conveyor rollers can vary in type, such as gravity rollers, driven rollers, and idler rollers, each serving a specific function within the system. Gravity rollers rely on the force of gravity to move materials, making them ideal for non-powered systems. Driven rollers are powered by motors and are used in automated systems to control the movement of materials. Idler rollers, on the other hand, are free-rolling and help support the conveyor belt, ensuring smooth and even distribution of load. Each type of roller is designed to handle different loads and environments, contributing to the overall efficiency and effectiveness of the conveyor system.
Conveyor rollers are attached to the conveyor frame in several ways, depending on the type of conveyor and its design. One common method is using spring-loaded shafts that allow the rollers to be easily inserted and removed from the frame. This design provides flexibility and simplifies maintenance and replacement processes. Another method involves using set screws or bolts to secure the rollers in place. These fasteners ensure a firm attachment, preventing the rollers from moving or becoming dislodged during operation. In some systems, roller brackets or mounting blocks are used to hold the rollers. These brackets can be adjusted to accommodate different roller sizes and positions, offering versatility in roller placement. Proper attachment is crucial for maintaining the alignment and smooth operation of the conveyor system, ensuring that the rollers can support and transport materials effectively.
The primary purpose of rollers in a conveyor system is to facilitate the smooth and efficient movement of materials along the conveyor belt. Conveyor rollers support the weight of the conveyed materials, reducing friction and wear on the belt, which extends the life of the conveyor system. By evenly distributing the load, rollers help prevent material buildup and reduce the risk of belt misalignment or damage. Additionally, rollers can be designed to handle various types of materials, from lightweight packages to heavy industrial goods, making them versatile components in different industries. They also contribute to the overall efficiency of the conveyor system by ensuring that materials are transported quickly and reliably, reducing manual handling and increasing productivity. Whether in manufacturing, warehousing, or distribution, conveyor rollers play a crucial role in streamlining operations and enhancing material handling processes.
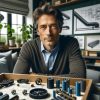
Jordan Smith, a seasoned professional with over 20 years of experience in the conveyor system industry. Jordan’s expertise lies in providing comprehensive solutions for conveyor rollers, belts, and accessories, catering to a wide range of industrial needs. From initial design and configuration to installation and meticulous troubleshooting, Jordan is adept at handling all aspects of conveyor system management. Whether you’re looking to upgrade your production line with efficient conveyor belts, require custom conveyor rollers for specific operations, or need expert advice on selecting the right conveyor accessories for your facility, Jordan is your reliable consultant. For any inquiries or assistance with conveyor system optimization, Jordan is available to share his wealth of knowledge and experience. Feel free to reach out at any time for professional guidance on all matters related to conveyor rollers, belts, and accessories.