Steel Conveyor Rollers with Bearings: Industry Applications
Steel conveyor rollers with bearings are integral components of conveying systems, known for their ability to handle various industrial applications. They consist of cylindrical steel rollers equipped with bearings, enabling smooth, efficient movement of materials along conveyor belts. Their robust construction makes them ideal for industries requiring durable, high-load equipment. Heavy-duty steel conveyor rollers with bearings are often found in mining and packaging sectors due to their reliability under continuous operation. Omni-directional rollers, on the other hand, provide multi-directional mobility, making them valuable in complex systems needing precise control. Their adaptability and versatility ensure seamless integration into diverse material handling setups, highlighting their essential role across multiple industries.
Key Features and Benefits of Steel Conveyor Rollers with Bearings
Steel conveyor rollers with bearings offer a multitude of key features and benefits, enhancing the efficiency and reliability of conveyor systems in various industrial settings:
- Durability and Strength: Steel conveyor rollers with bearings are designed with a robust construction that withstands heavy loads and adverse environmental conditions, making them ideal for heavy-duty applications in industries like mining and construction.
- Precision Bearings: The inclusion of precision bearings significantly reduces friction and wear, facilitating smooth, efficient movement of materials across the conveyor system. This feature ensures prolonged operational life and reduced maintenance costs.
- Compatibility and Versatility: These rollers are compatible with a wide range of conveyor systems and can be adapted to meet specific industry requirements, such as adjustable lengths and diameters for different conveyor setups.
- Corrosion Resistance: Coated with materials that resist rust and corrosion, steel conveyor rollers with bearings can operate effectively in environments that are humid or exposed to chemicals.
- Energy Efficiency: The smooth operation of these rollers minimizes energy consumption by reducing the load on conveyor motors, making the systems more energy-efficient and cost-effective to operate.
- Noise Reduction: Steel conveyor rollers with bearings are engineered to operate quietly, reducing noise pollution in the workplace, which is particularly beneficial in operations that run continuously.
- High Load Capacity: These rollers are capable of handling extremely high loads, which makes them indispensable in industries that move large volumes of goods or heavy materials.
- Easy Installation and Maintenance: Designed for easy installation, these rollers can be quickly integrated into existing systems with minimal downtime. Maintenance is straightforward due to their simple structure and accessibility.
- Speed Capability: They can operate at higher speeds compared to non-bearing rollers, suitable for industries that require fast-paced production lines.
- Thermal Stability: Steel conveyor rollers with bearings perform well under varying temperature conditions, maintaining their integrity and functionality even when exposed to extreme heat or cold.
- Longevity and Cost-Effectiveness: With their durable design and efficient operation, steel conveyor rollers with bearings offer an excellent return on investment by extending the lifespan of conveyor systems and reducing the need for frequent replacements.
These features make steel conveyor rollers with bearings a crucial component in enhancing the productivity and operational efficiency of various conveyor systems across multiple industries.
Types of Steel Conveyor Rollers with Bearings
Steel conveyor rollers with bearings come in various types, each tailored to accommodate specific industrial requirements. Their design allows efficient handling of materials in different operational settings, ensuring seamless movement and productivity in conveyor systems.
Heavy Duty Steel Conveyor Rollers
Heavy duty steel conveyor rollers with bearings are engineered to endure the most challenging environments where high loads and constant use are the norms. They are often deployed in industries like mining, construction, and manufacturing, where efficiency and reliability are paramount.
Key Features:
- High Load Support: Designed with reinforced steel and precision bearings, these rollers can manage exceptionally heavy loads, enabling them to handle bulk materials and equipment.
- Enhanced Durability: Constructed from high-grade steel, they resist deformation, bending, and cracking, crucial for rugged operations.
- Reduced Downtime: Their robust design minimizes maintenance, ensuring conveyor systems remain operational for longer periods.
- Impact Resistance: Heavy duty rollers are built to absorb impacts from dropped materials, preventing roller damage and conveyor belt wear.
- Extended Lifespan: Thick-walled tubing and hardened surfaces extend the operational life of these rollers, saving on replacement costs.
- High Torque Capacity: They effectively transmit high torque from motors to ensure consistent conveyor movement, vital for high-production lines.
- Customization Options: Can be produced in different diameters and lengths, with various bearing types to fit specific conveyor requirements.
- Improved Sealing: Effective sealing mechanisms shield bearings from dust, moisture, and corrosive agents, protecting internal components.
Omni Conveyor Rollers
Omni conveyor rollers with bearings offer 360-degree movement, making them ideal for conveyor systems that need to handle intricate or irregular paths. Their ability to provide multi-directional mobility allows them to change the direction of conveyed items efficiently.
Key Features:
- 360-Degree Movement: Bearings within the rollers enable movement in any direction, essential for conveying products requiring orientation changes.
- Flexibility in Layout Design: They enable the creation of complex conveyor paths without additional guiding systems, ideal for space-constrained settings.
- Smooth Operation: Facilitates gentle handling of products, ensuring precise movement across different sections of the conveyor.
- Minimal Space Requirement: Compact design allows the conveyor system to fit in areas with limited space while maintaining efficiency.
- Low Maintenance: Sealed bearings and pre-lubricated components require minimal upkeep, reducing system downtime.
- Adaptable Speed: Can accommodate varying speeds, ensuring compatibility with different production line requirements.
- Custom Load Capacities: Available in a range of load-bearing capacities to suit the specific needs of various industries.
- Versatile Application: Suitable for packaging, sorting, and distribution centers due to its ability to handle items with different shapes and weights.
Industrial Conveyor Rollers
Industrial steel conveyor rollers with bearings are designed for industries that handle large volumes of materials, ensuring that production lines remain efficient and productive. These rollers are essential in environments like mining, food processing, and logistics where reliability is a top priority.
Key Features:
- Robust Material Handling: Strong enough to transport large quantities of goods while maintaining smooth and controlled movement.
- High Efficiency: Provides rapid transit of materials, allowing the entire production system to operate with fewer bottlenecks.
- Scalability: Easily integrates into existing conveyor systems, enabling expansion for growing industrial needs.
- Resistance to Wear and Tear: Made from abrasion-resistant materials to withstand friction and wear over long periods of use.
- Temperature Resistance: Suitable for operations that require extreme heat or cold, such as foundries or refrigeration units.
- Easy Integration: Compatible with existing conveyor frameworks, reducing the need for significant modifications during installation.
- Customizable Designs: Available in different diameters, thicknesses, and finishes to meet specific industry requirements.
- Energy Efficient: Precision bearings reduce friction, requiring less energy for operation and contributing to overall system efficiency.
These types of steel conveyor rollers with bearings deliver optimal performance, whether moving heavy loads, providing omni-directional maneuverability, or enhancing efficiency in industrial settings.
Specialized Designs of Steel Conveyor Rollers with Bearings
Steel conveyor rollers with bearings come in various specialized designs to meet specific material handling needs. Each design is optimized for distinct applications, improving conveyor system reliability and efficiency.
Concave Conveyor Rollers
Concave steel conveyor rollers with bearings are crafted with a curved or crowned surface to handle bulk materials and rounded items. The distinctive shape of these rollers keeps materials centered, reducing spillage and promoting consistent flow.
Key Features:
- Item Stabilization: The curved profile effectively grips rounded items, preventing them from sliding off during transit and keeping products centered for easier downstream processing.
- Bulk Material Handling: Designed for conveying granular or loose materials that would otherwise roll or scatter, providing reliable movement and minimizing spillage.
- Minimized Spillage: The curvature ensures that materials stay within the conveyor’s width, limiting product loss, particularly in high-speed operations.
- Adaptability: Available in varying degrees of curvature, from mild crowns to more pronounced shapes, accommodating different product sizes and shapes.
- High Load Capacity: Fabricated with heavy-duty bearings and steel to withstand substantial loads of loose or bagged materials.
- Durability: Constructed from abrasion-resistant steel, these rollers can endure harsh industrial conditions, including dust, moisture, and heavy impacts.
- Smooth Transport: Offers smooth product handling with reduced jolts and bumps, minimizing damage to fragile goods.
- Precision Bearings: Ensures efficient movement with minimal resistance, reducing energy consumption and maintaining a steady, consistent flow of products.
4-Inch Conveyor Rollers
4-inch steel conveyor rollers with bearings are compact yet durable rollers. These rollers are a perfect solution for conveyor systems where space is limited but consistent, smooth movement is crucial.
Key Features:
- Compact Design: The small diameter allows them to fit snugly into conveyor systems with limited spacing while still providing reliable support for efficient transport.
- Precision Handling: Equipped with bearings that provide smooth rotation, making them suitable for handling delicate or lightweight items.
- Easy Integration: Their standardized size enables them to be installed in most conveyor frameworks without extensive modifications.
- Custom Lengths: Available in different lengths and axle diameters to accommodate various conveyor system designs and requirements.
- Versatility: These rollers can handle light to medium loads in various sectors, including packaging, manufacturing, and logistics, offering adaptability across diverse applications.
- High-Speed Capability: The bearings enable high-speed rotation, making them suitable for fast-paced production lines where quick material transfer is necessary.
- Low Maintenance: Sealed and pre-lubricated bearings reduce the need for frequent servicing, lowering maintenance costs and ensuring continuous system operation.
- Energy Efficiency: Bearings minimize friction, leading to lower energy consumption and operational costs, making these rollers an energy-efficient choice for small systems.
Replacement Conveyor Rollers
Replacement steel conveyor rollers with bearings are designed to seamlessly replace worn-out or outdated components, ensuring compatibility and enhancing the longevity of conveyor systems.
Key Features:
- Custom Design: Tailored to match the precise dimensions and specifications of existing conveyor systems, replacement rollers can fit seamlessly, ensuring compatibility and reliable operation.
- Quick Installation: Pre-assembled rollers can be quickly installed, reducing downtime and ensuring that conveyor systems are up and running with minimal disruption.
- Extended Lifespan: High-quality steel and precision bearings prolong the operational life of these rollers, reducing the frequency and cost of future replacements.
- Compatibility: Available in a wide range of diameters, finishes, and bearing types, these rollers can suit different operational needs and environments.
- Enhanced Performance: New rollers improve overall efficiency and reduce noise levels, ensuring smoother and quieter movement compared to worn-out components.
- Reduced Downtime: Made from robust materials, these rollers can withstand rigorous use, minimizing the need for frequent repairs or replacements.
- Corrosion Resistance: Coated to resist corrosion, rust, and chemical exposure, these rollers are ideal for challenging environments.
- Economic Solution: Offers a cost-effective approach to revitalize old conveyor systems without a complete overhaul, significantly improving system performance.
Each specialized design of steel conveyor rollers with bearings provides optimized performance for conveyor systems, enhancing productivity and efficiency across industries.
Selection Criteria for Steel Conveyor Rollers with Bearings
Selecting the right steel conveyor rollers with bearings is essential for optimizing the performance and durability of conveyor systems. Below are 11 critical selection criteria:
- Load Capacity: Select rollers that can handle the maximum expected load plus an additional safety margin to ensure durability and safety.
- Operating Environment: Choose materials and finishes appropriate for the environmental conditions, such as temperature extremes, moisture, and chemical exposure.
- Speed and Efficiency Requirements: Opt for rollers designed to operate efficiently at the desired speed to maintain productivity without compromising system integrity.
- Roller Diameter: Match the roller diameter to the scale of the operation and the physical size of the materials being transported.
- Material Type: Decide between different metals or coatings based on the environment and the type of goods being conveyed, considering factors like corrosion resistance and strength.
- Roller Length: Ensure the length of the roller is sufficient to support the width of the conveyor belt and the items being moved.
- Bearing Type: Choose bearing types that suit the load and speed requirements of the conveyor, with options for sealed or shielded bearings for added protection against contaminants.
- Mounting and Alignment: Ensure the mounting system allows for easy installation and precise alignment to prevent operational issues.
- Noise Level: Consider the operational noise level; opt for rollers designed to operate quietly if necessary, especially in noise-sensitive environments.
- Maintenance Requirements: Select rollers that offer ease of maintenance, including features like self-lubricating bearings or easy access for replacement.
- Cost vs. Longevity: Balance initial cost against expected lifespan and maintenance needs, investing more in high-quality components that will reduce long-term costs associated with downtime and repairs.
By carefully considering each of these factors, you can ensure that the steel conveyor rollers with bearings you choose will meet the demands of your specific applications and provide long-term reliability.
FAQs about Steel Conveyor Rollers with Bearings
For conveyor belt rollers, the type of bearings recommended largely depends on the specific requirements of the conveyor system, including load, speed, and environmental conditions. Generally, precision ball bearings are ideal for high-speed conveyor applications where minimal friction is crucial. These bearings are sealed and lubricated to withstand demanding conditions and reduce maintenance requirements. For heavier loads and slower speeds, tapered roller bearings are preferred due to their ability to handle both radial and axial loads more effectively. Additionally, spherical roller bearings are recommended for applications involving high load capacities and harsh conditions because they can tolerate misalignment and are highly durable. When selecting bearings, consider factors such as the load capacity, speed of the conveyor, and the environment in which the conveyor will operate (e.g., presence of dust, moisture, or corrosive substances).
Conveyor rollers are classified based on their functionality and the materials they are designed to handle. The most common types include gravity rollers, which use the force of gravity to move items and are ideal for manual movement or when slight inclines are involved. Driven rollers, connected by belts or chains, are powered by motors, making them suitable for automated systems. Grooved rollers are designed to interact with belts or o-rings on their surface, providing additional traction. Impact rollers are placed at loading points to absorb the shock of heavy materials hitting the conveyor. Finally, plastic rollers, which are lightweight and resistant to corrosion, are used when a non-metallic option is necessary due to environmental factors or the need for a quieter operation. Each type serves different operational needs, making it essential to understand the specific requirements of your conveyor system before choosing.
The key difference between a drive roller and a driven roller lies in their roles within a conveyor system. A drive roller is actively powered by a motor or a mechanical input and transmits this power to move the conveyor belt or rollers. This roller is crucial for the propulsion of the belt and often requires a more robust build to handle the motor’s torque. In contrast, a driven roller is one that is moved by the belt or by other rollers and does not have its own power source. Driven rollers are typically used to support the belt and guide it smoothly around the conveyor’s path. They rely on the motion imparted by the drive roller and are essential for distributing the load across the conveyor, reducing wear and stress on the system.
An idler roller is a non-powered roller typically used in a conveyor system to support the weight of the belt and the materials being transported. These rollers are strategically placed along the length of the conveyor to maintain the belt’s tension and alignment, ensuring smooth operation. Idler rollers help distribute the load evenly, preventing excessive wear and prolonging the belt’s life. They come in various sizes and designs, including flat, troughing, and return rollers, each tailored to specific functions within the conveyor system. Flat idlers are used primarily in flat belt applications, troughing idlers guide the belt into a trough shape to contain the material being transported, and return idlers support the underside of the belt as it cycles back to the beginning of the conveyor loop.
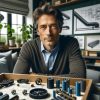
Jordan Smith, a seasoned professional with over 20 years of experience in the conveyor system industry. Jordan’s expertise lies in providing comprehensive solutions for conveyor rollers, belts, and accessories, catering to a wide range of industrial needs. From initial design and configuration to installation and meticulous troubleshooting, Jordan is adept at handling all aspects of conveyor system management. Whether you’re looking to upgrade your production line with efficient conveyor belts, require custom conveyor rollers for specific operations, or need expert advice on selecting the right conveyor accessories for your facility, Jordan is your reliable consultant. For any inquiries or assistance with conveyor system optimization, Jordan is available to share his wealth of knowledge and experience. Feel free to reach out at any time for professional guidance on all matters related to conveyor rollers, belts, and accessories.