Guide to Used Steel Rollers for Sale: Types and Tips
Steel rollers are fundamental components in numerous industries, including manufacturing, logistics, and packaging, where they facilitate the movement and processing of materials efficiently. These rollers, essential for assembly lines and transport systems, vary in design to suit specific tasks, such as heavy-load handling or delicate material manipulation. Highlighting the relevance for regional businesses, there is a notable market for used steel rollers for sale, especially in areas like Wichita, Kansas. Here, companies can access a range of pre-owned steel rollers, offering them a cost-effective solution without compromising on quality or functionality, making it an attractive option for businesses aiming to optimize their operations economically.
Types of Steel Rollers Available: Finding the Right Used Steel Rollers for Sale
When looking to purchase used steel rollers for sale, understanding the different types available and their specific advantages is crucial. Steel rollers are integral to numerous mechanical systems and vary greatly to accommodate diverse industrial needs. Here, we detail four primary types of steel rollers: gravity roller conveyors, conveyor rollers, and slip rollers, each tailored for distinct operational requirements.
Gravity Roller Conveyors
Gravity roller conveyors are the simplest and most common type of roller system, relying on gravity to move products along a downward-sloped pathway. These rollers are typically used in material handling applications, such as moving boxes or pallets across a factory floor.
Benefits:
- Cost-Effectiveness: Operating without electricity or motors, these conveyors reduce energy costs and minimize initial investment, making them ideal for small to medium-sized enterprises.
- Ease of Installation: Their modular design allows for quick assembly and disassembly, facilitating rapid deployment and reconfiguration in dynamic manufacturing environments.
- Low Maintenance: With fewer mechanical parts subject to wear and tear, gravity roller conveyors require minimal upkeep, lowering the total cost of ownership.
- Versatility: Adjustable components, such as roller diameter and spacing, make these systems adaptable to a wide range of products and packaging types.
- Energy Efficiency: The absence of motorized parts translates into a greener operation with reduced carbon footprint, essential for sustainability-focused businesses.
- Noise Reduction: They operate significantly quieter than motor-driven conveyors, improving the work environment and complying with noise regulations in industrial zones.
- Scalability: Additional sections can be added as demand grows, ensuring that the system can evolve with the business without extensive modifications.
Conveyor Rollers
Conveyor rollers are part of powered conveyor systems and are designed to handle higher loads and controlled movement. These are essential in industries where precise material handling and speed are necessary.
Benefits:
- Controlled Movement: Enhanced control over movement allows for the synchronization of logistics operations, crucial in assembly lines where timing and placement are key.
- Increased Productivity: Automation capabilities of powered conveyor rollers streamline processes, significantly boosting throughput and reducing cycle times.
- Durability: Constructed from robust materials, these rollers can endure rigorous use in demanding industrial settings, ensuring longevity and reliability.
- Flexibility: Capable of handling diverse loads, conveyor rollers can be customized with various coverings to grip, sort, and transport different materials safely.
- Safety: Automated systems reduce the need for direct human interaction with heavy loads, thus decreasing the likelihood of workplace accidents.
- Integration: Advanced integration with digital tracking and management systems allows for real-time data collection and analytics, optimizing the logistics chain.
- Customization: Features like adjustable speeds, reversible operations, and accumulation capabilities allow for tailored solutions that meet specific production needs.
Slip Rollers
Slip rollers, specifically designed for metal fabrication, are used to bend metal sheets into curves or cylinders. They are crucial in automotive, aerospace, and metalworking industries.
Benefits:
- Precision: High precision in metal forming ensures that each piece meets exact specifications, which is crucial for quality control in metal fabrication.
- Versatility in Materials: The ability to work with a range of metal types and thicknesses allows manufacturers to diversify their product offerings without requiring additional equipment.
- Adjustable: Features such as variable roller speeds and adjustable roller spacing accommodate different material properties and bending radii, enhancing product customization.
- Efficiency: Automation of bending processes reduces the need for manual labor, allowing faster production rates and lower labor costs.
- Quality Finish: Precision engineering of slip rollers ensures that metal sheets are bent without damaging the material, maintaining aesthetic and structural integrity.
- Cost-Effective: The reduction in manual labor and increased production speed translate into lower production costs and higher profitability.
- Space-Saving: Compact design maximizes the use of floor space, an important consideration for workshops and factories with limited area.
Each type of used steel roller serves a specific function that can significantly enhance operational efficiency and cost-effectiveness in different industrial settings. When searching for used steel rollers for sale, it’s essential to consider the specific needs of your operations to select the right type that offers the most benefits.
Advantages of Buying Used Steel Rollers for Sale
Purchasing used steel rollers for sale offers a multitude of advantages for businesses across various sectors. These benefits not only encompass significant cost savings but also contribute to environmental sustainability and operational efficiency. Here are eight key advantages of choosing used steel rollers:
- Cost-effectiveness: Buying used steel rollers greatly reduces the initial expenditure when compared to purchasing new equipment. This affordability allows businesses to allocate financial resources to other essential areas like research and development or marketing.
- Environmental Benefits: Choosing used steel rollers helps in reducing the demand for new raw materials, which decreases the environmental footprint of manufacturing new equipment. This choice supports sustainability initiatives by promoting the reuse and recycling of industrial machinery.
- Immediate Availability: Used steel rollers are often readily available for immediate purchase and deployment, bypassing the lengthy production and delivery times associated with ordering new equipment from manufacturers.
- Proven Performance: Pre-owned steel rollers have a track record of performance, having already been tested in real-world applications. This history can provide assurance of their capability and reliability.
- Lower Depreciation: The rate of depreciation for used equipment is significantly lower than that for new machines. This slower depreciation means businesses can retain more value of their investment over time.
- Flexibility in Resale: There’s a vibrant market for used steel rollers, providing businesses the flexibility to sell equipment when it’s no longer needed, often recouping a substantial portion of the initial cost.
- Access to Discontinued Models: Used markets may offer models that are no longer in production, providing businesses an opportunity to purchase machines that match their existing equipment without needing system upgrades.
- Support for Smaller Businesses: The lower cost of used steel rollers makes them accessible to smaller businesses or startups, leveling the playing field and fostering greater competition within various industries.
Useful Tips on Buying Used Steel Rollers for Sale
Ensuring the quality of used steel rollers is crucial to making a sound investment. Here are tips to help prospective buyers select the best possible equipment:
- Check for Wear and Tear: Examine the used steel rollers for any signs of excessive wear or damage that could impair functionality or lead to costly repairs down the line.
- Verify Operational History: Ask for the service history and maintenance logs to understand how the equipment has been used and maintained by the previous owner.
- Request Operational Demonstrations: Seeing the steel rollers in operation can provide insights into their current condition and performance capabilities.
- Ensure Compatibility: Confirm that the used steel rollers will integrate smoothly with existing systems to avoid additional expenses in adaptation or modifications.
- Assess Availability of Spare Parts: Make sure that spare parts are readily available, especially for older or discontinued models, to ensure continued operation without disruptions.
- Maintain Condition for Resale: Keep the equipment in good condition and document all maintenance and repairs to enhance its resale value if you decide to upgrade or sell in the future.
- Partner with Reputable Dealers: Choose to buy from well-known and reputable dealers who offer warranties or return policies that provide a safety net for your purchase.
- Check for Safety Compliance: Ensure that the used steel rollers comply with current safety standards to protect your workers and avoid legal issues.
By following these tips, businesses can confidently invest in used steel rollers, securing equipment that meets their needs while maximizing the benefits discussed above.
Where to Find Used Steel Rollers for Sale Near Wichita, KS
Finding used steel rollers for sale near Wichita, KS, involves exploring local dealers and popular online platforms that offer a range of equipment options. Whether you need rollers for large industrial projects or smaller tasks, the Wichita area and broader Kansas region offer numerous reliable sources.
Local Options in Wichita and Broader Kansas Area
For those looking to physically inspect equipment before purchase, the local dealers in Wichita and surrounding areas of Kansas provide a viable solution. These businesses often have knowledgeable staff, competitive pricing, and sometimes even the ability to refurbish equipment.
- Wichita Material Recovery: This facility not only sells used industrial equipment like steel rollers but also buys and recycles machinery, offering a sustainable option for businesses. Their vast inventory allows for various industrial choices.
- Kansas Surplus Equipment Dealers: Located throughout Kansas, these dealers specialize in a wide range of industrial surplus goods. They often have a rotating inventory, so frequent visits can be beneficial to find the right steel rollers.
- Industrial Surplus Inc.: Known for a robust selection, this Wichita-based outlet provides quality used equipment with the opportunity for buyers to come and inspect items firsthand, ensuring the purchase meets their specifications.
- Wichita Equipment Auctions: Regularly scheduled auctions are a staple in Wichita, where buyers can bid on used steel rollers that come from various industries, offering potential savings against retail prices.
- Midwest Machinery Inc.: This dealer services the broader Kansas area and is known for its reliability and varied stock. They often feature different types of steel rollers, suitable for various industrial applications.
- Wichita Industrial Sales and Service: This entity prides itself on excellent customer service and maintains a selection of used industrial equipment, including robust steel rollers, with a focus on meeting the needs of local industries.
- Kansas Industrial Rebuilders: Not only does this nearby Wichita dealer sell used equipment, but they also offer refurbishing services. This is an excellent option for those looking to customize their steel rollers while ensuring operational efficiency.
Popular Platforms and Local Dealers for Used Rollers
Online platforms and specialized dealers expand the possibilities for finding used steel rollers, providing access to a wider range of equipment from the convenience of your office or home. These platforms often feature listings from various dealers, giving buyers the chance to compare prices and specifications.
- eBay: A well-known marketplace with a specific section for industrial goods. It features numerous listings for used steel rollers, posted by sellers from Wichita and beyond, allowing for competitive pricing and variety.
- MachineryTrader: This platform is renowned for its focus on industrial machinery, showcasing listings from Kansas dealers frequently. It’s an excellent resource for finding specific types of steel rollers.
- Craigslist Wichita: Known for local classifieds, Craigslist offers a straightforward way to find used steel rollers nearby. Listings are typically from local businesses or individuals looking to upgrade or liquidate their equipment.
- BidSpotter: Specializing in auctions, BidSpotter hosts many industrial auctions that can include steel rollers. It’s an ideal site for finding deals through auction dynamics.
- MachineTools: This specialized site lists all kinds of machine tools, including steel rollers. Its comprehensive search features allow filtering by location, ensuring you can find options close to Wichita.
- Surplus Record: A dedicated resource for used machinery, Surplus Record compiles listings from various dealers, including those in the Kansas area, making it easier to locate the equipment you need.
- IronPlanet: Known for its robust selection of heavy equipment, IronPlanet offers an array of used steel rollers suitable for different industrial purposes, with detailed condition and operational reports.
These local options and popular platforms are ideal starting points when searching for used steel rollers for sale in and around Wichita, KS. Each provides a unique set of advantages, from hands-on inspection and direct negotiations to convenient online browsing and purchasing.
How to Inspect Used Steel Rollers for Sale Before Purchase
When exploring used steel rollers for sale, conducting a comprehensive inspection is essential to ensure you are investing in equipment that meets both your quality standards and operational needs. This guide will outline a detailed approach to inspecting the physical condition, operational efficiency, and safety features of used steel rollers, along with an emphasis on the importance of assessing wear and tear and maintenance history.
Step-by-Step Inspection Guide
Begin your inspection with a systematic approach to evaluate all critical aspects of the used steel rollers. This ensures you identify any potential issues that could affect performance or safety.
- Visual Inspection: Thoroughly examine the steel rollers for any visible signs of damage such as dents, cracks, or excessive rust. Such defects might indicate past heavy use or poor maintenance.
- Roller Condition: Check each roller for uniformity and surface wear. Uneven wear or damaged surfaces can impair functionality and lead to further damage or inefficiency in operation.
- Frame Integrity: Inspect the frame for structural soundness. Ensure there are no fractures or significant rust that could compromise the roller’s stability and performance.
- Bearing and Shaft Inspection: Assess the condition of bearings and shafts for signs of wear or deterioration. Listen for noises or rough movement as these could suggest the need for replacement or maintenance.
- Alignment Check: Ensure that all rollers are properly aligned. Misalignment can cause uneven wear and operational issues, affecting the lifespan and efficiency of the rollers.
- Operational Test: Conduct a test run to monitor the rollers under operation. This can reveal hidden issues such as vibrations, abnormal noises, or mechanical failures not visible during static inspections.
- Safety Features: Verify that all safety mechanisms are present and fully operational. Check for any modifications or removal of original safety features.
- Material Handling Capability: Test the rollers with the type of material they will be handling. Confirm that the system can manage the expected load and operates smoothly under typical conditions.
Importance of Wear and Tear and Maintenance History
Introduction: Understanding the historical upkeep and the current state of wear and tear can significantly impact the operational lifespan and efficiency of used steel rollers. This examination helps forecast future maintenance needs and costs.
- Wear Patterns: Study the wear patterns on the rollers. Irregular or uneven patterns often suggest improper use or alignment issues, which can affect performance.
- Repair Records: Investigate any records of past repairs. Frequent or major repairs might indicate underlying problems that could persist or reoccur.
- Replacement Parts: Identify any components that have been replaced. High-quality, recently replaced parts may enhance the roller’s functionality, whereas older or low-quality parts may shorten its lifespan.
- Maintenance Routine: Review the maintenance schedule followed by the previous owner. Regular, documented maintenance usually means the equipment has been well cared for.
- Lubrication History: Check the lubrication intervals and methods used. Proper lubrication is crucial for minimizing friction and wear, which prolongs the life of moving parts.
- Corrosion Inspection: Examine the rollers and associated metal components for any signs of corrosion, which can weaken the metal and lead to structural failures.
- Operational Logs: If available, look through operational logs that detail the duration and intensity of the roller’s use. High usage levels can accelerate wear and reduce the expected service life.
By following these detailed guidelines, you ensure that the used steel rollers for sale you consider will be thoroughly vetted for quality, safety, and longevity, ultimately providing peace of mind and a sound investment in your operational assets.
Comparison: Buying New vs. Used Steel Rollers for Sale
When you are in the market for used steel rollers for sale, it is crucial to weigh your options against purchasing new rollers. This comparison will delve into the specifics like initial costs, longevity, performance implications, and practical scenarios to help you decide whether new or used steel rollers are the best fit for your needs.
Detailed Comparison: Buying New vs. Used Steel Rollers
Here’s a more detailed comparison in table format to clarify the pros and cons of buying new versus used steel rollers:
Factor | Buying New Steel Rollers | Buying Used Steel Rollers |
---|---|---|
Initial Cost | Significantly higher due to brand-new condition and absence of wear. | Substantially lower, often 50-70% cheaper, offering initial cost savings. |
Availability | May involve lead times for manufacturing and shipping. | Typically available immediately, which is crucial for urgent needs. |
Warranty and Support | Usually includes full manufacturer warranties and customer support. | Often sold as-is, with limited or no warranty; support depends on seller. |
Longevity | Expected to have a longer operational life due to no prior use. | Remaining useful life varies widely based on past use and maintenance. |
Performance | Delivers optimal performance with the latest technology and no wear. | Performance can be compromised by wear and prior use unless refurbished. |
Maintenance | Lower maintenance costs initially as parts are new and fully functional. | May require more frequent maintenance and inspection to ensure reliability. |
Depreciation | Higher depreciation rate, especially in the first years after purchase. | Lower depreciation; much of the value has already depreciated. |
Scenarios for Buying New and Used Steel Rollers
When to Buy New:
- Customization Needs: Essential when specific customizations or modifications are needed that used equipment cannot provide, ensuring compatibility with existing systems.
- Reliability and Uptime: For operations where equipment downtime has significant cost implications, new equipment is less likely to require repairs, offering greater reliability.
- Technological Advancements: Beneficial when the operation demands the highest efficiency and latest technology to maintain competitive edge and operational cost savings.
- Regulatory Compliance: Necessary in industries with stringent safety and environmental regulations that used equipment might not meet.
- Long-term Investment: Ideal when the equipment is expected to be in use for an extended period, making the higher upfront cost a worthwhile investment over time.
- High-Usage Applications: When the equipment will be used extensively, the longevity and lower long-term cost of ownership of new equipment can justify the initial expense.
- Financial Flexibility: When budget constraints are less of a concern, and the focus is on acquiring top-quality equipment with all the benefits of new technology and warranty.
When to Buy Used:
- Budget Constraints: When initial cost is a significant factor, and the savings can be allocated to other areas of the business.
- Short-term Requirements: Ideal for projects that have a finite timeline, where the equipment will not be needed on a long-term basis.
- Immediate Need: Crucial when equipment is needed immediately to meet project deadlines or replace failed machinery without the wait.
- Non-critical Use: Suitable for situations where the equipment will serve as a backup or is not critical to core business operations.
- Stable Technology: When the technology of the equipment does not evolve rapidly, making older models nearly as effective as new ones.
- High Wear Environments: In environments where equipment is subject to extreme conditions that will lead to rapid wear, used equipment can be more cost-effective.
- Business Expansion: Useful for startups or businesses in expansion mode where cost savings are vital for funding growth in other crucial areas.
By providing a clearer understanding through this expanded comparison and scenarios, businesses can better assess their specific needs against the advantages and drawbacks of buying new versus used steel rollers for sale. This decision-making process ensures that you choose the best option for your operational requirements and financial constraints.
Installation and Maintenance Tips for Used Steel Rollers for Sale
Ensuring the proper installation and ongoing maintenance of used steel rollers for sale is crucial for maximizing their efficiency and extending their operational life. The following sections provide detailed guidelines for both installing these rollers correctly and maintaining them effectively.
Installation Tips for Used Steel Rollers
Proper installation of used steel rollers is foundational to their performance and longevity. Missteps in installation can lead to operational inefficiencies, increased wear and tear, or even premature failure of the equipment.
- Inspect Before Installation: Thoroughly examine the rollers for any structural damages, such as cracks or bent frames, which could have been overlooked during the purchase. Address any issues before proceeding with installation.
- Clean All Components: Remove any dirt, grime, or rust from the rollers and their components. This ensures that no abrasive particles are present that could cause damage during operation.
- Check Alignment: Use precise tools to check the alignment of the rollers. Proper alignment is crucial for uniform distribution of load and smooth operation, which helps in avoiding uneven wear on the rollers.
- Lubricate Moving Parts: Apply a high-quality lubricant to all moving parts to reduce friction. Select a lubricant that is suitable for the specific type of material and expected environmental conditions of operation.
- Securely Fasten All Hardware: Double-check all connections and fastenings for tightness and stability. Use a torque wrench to ensure that all bolts and nuts are tightened to the manufacturer’s specifications.
- Test Rollers After Installation: Conduct a dry run without load to ensure that the rollers operate smoothly. This is a critical step to confirm that the installation has been done correctly before full operational use.
- Train Operators: Provide comprehensive training for all operators on the correct operation of the rollers, focusing on safety and efficiency. Ensure they understand the specifics of the used equipment.
- Install Safety Measures: Implement all necessary safety protocols, including barriers, guards, and emergency stops. Safety installations are vital to protect both the operators and the equipment.
Maintenance Tips for Steel Rollers
Regular and proactive maintenance of steel rollers is essential to ensure their optimal performance and to prevent downtime. A well-maintained roller can significantly outlast one that is neglected, making maintenance a key aspect of operational management.
- Regular Inspection: Schedule and conduct regular inspections to identify potential issues early on. Look for signs of wear, such as cracks, rusting, or unexpected noises that might indicate a problem.
- Maintain Proper Lubrication: Continuously monitor and maintain the lubrication of the rollers. Frequent checks will help you ensure that all components are well-lubricated and operating smoothly, which is crucial for their longevity.
- Clean Rollers Regularly: Establish a routine cleaning schedule to keep the rollers and their environment free from debris and buildup. Accumulated materials can cause damage over time or even sudden malfunctions.
- Monitor Load Capacities: Regularly check that the load capacities are not being exceeded. Exceeding the specified capacity can strain the rollers and lead to significant damage or failure.
- Schedule Preventative Maintenance: Develop a preventative maintenance plan based on the manufacturer’s guidelines and stick to it. This may include replacing worn parts, updating software, or recalibrating machinery.
- Address Issues Promptly: Respond to any identified issues without delay. Quick resolution of small problems can prevent them from escalating into more significant issues that could be costly and time-consuming to resolve.
- Keep Maintenance Records: Maintain detailed records of all maintenance activities. These records are invaluable for tracking the history of the equipment, planning future maintenance, and resolving specific operational issues that may arise.
By carefully following these installation and maintenance tips, you can significantly enhance the operational reliability and lifespan of your used steel rollers for sale, ensuring they continue to provide value and service in your operations.
Success Stories and Case Studies of Used Steel Rollers for Sale
In the Wichita area and beyond, several businesses have demonstrated significant operational improvements and cost savings by integrating used steel rollers for sale into their processes. These detailed case studies and anecdotes highlight the practical benefits and efficiency gains achieved through such investments.
Case Study 1: Wichita Manufacturing Facility
Company: AeroParts & Supply Midwest
Story: AeroParts & Supply Midwest, which specializes in aircraft parts manufacturing, opted for used steel rollers to enhance their assembly line as part of a strategic initiative to reduce operational costs while maintaining high production standards. This transition has allowed them to handle a higher volume of parts with greater precision and speed.
Quote: “Integrating used steel rollers not only cut our costs by 30% but also boosted our output significantly, proving that quality doesn’t always have to come at a high price,” says Jake Harmon, Plant Manager.
Outcome: The company has reported a smoother workflow and a noticeable improvement in the assembly line’s output, attributing this success to the robustness and reliability of the used steel rollers.
Case Study 2: Kansas Logistics Hub
Company: Sunflower Supply Chain Solutions
Story: At Sunflower Supply Chain Solutions, the adoption of used steel rollers in their distribution center has revamped their sorting and packaging operations. This strategic enhancement has streamlined their process flow, reducing package handling times and increasing overall throughput.
Quote: “Our decision to invest in used steel rollers paid off faster than anticipated, significantly enhancing our operational throughput and reducing system downtime,” notes CEO Linda Morris.
Outcome: The installation of used steel rollers has led to an improvement in system efficiency and a reduction in mechanical breakdowns, which were common with their previous equipment.
Case Study 3: Wichita Metalworks
Company: SteelCraft Fabrications
Story: SteelCraft Fabrications incorporated used steel rollers to better manage the increased demand for heavier, more complex metalwork projects. This upgrade has enabled them to broaden their market offerings and take on projects that were previously beyond their capacity.
Quote: “The used steel rollers have been a game-changer for us, enabling larger-scale projects and enhancing our workshop’s capability,” explains Michael Trent, Owner and Lead Designer.
Outcome: The company has successfully completed several large-scale projects since the integration of used steel rollers, leading to higher client satisfaction and an expanded client base.
Case Study 4: Kansas Agricultural Co-op
Company: Prairie Grain Partners LLC
Story: This agricultural cooperative introduced used steel rollers into their grain processing facility to cope with the increased volume during the harvest season. This has significantly quickened their processing times, allowing them to handle greater volumes efficiently.
Quote: “With the used steel rollers, we’ve managed to speed up processing by 40% during peak times, which has been crucial for meeting market demands,” says Sarah Jennings, Operations Manager.
Outcome: The cooperative has experienced a smoother, faster grain processing operation, which has been vital during peak harvest periods, enhancing their market responsiveness and profitability.
Case Study 5: Wichita Auto Components Manufacturer
Company: AutoTech Components
Story: AutoTech Components used the installation of used steel rollers to streamline their production lines, thereby improving both the speed and safety of their assembly processes. This strategic update has enabled them to meet higher production quotas and reduce workplace accidents.
Quote: “The upgraded assembly line with used steel rollers has notably increased our production efficiency and significantly improved our safety records,” remarks Tom Franklin, Safety Officer.
Outcome: Since upgrading their conveyor systems with used steel rollers, AutoTech Components has seen an increase in production efficiency and a notable decrease in the incidence of workplace injuries.
These detailed case studies from various sectors in Wichita and surrounding areas demonstrate how incorporating used steel rollers for sale can lead to substantial operational benefits, including cost savings, increased efficiency, and expanded production capabilities. Each business’s experience underscores the value and versatility of used industrial equipment in diverse settings.
Legal and Safety Considerations for Used Steel Rollers for Sale
Purchasing used steel rollers for sale involves careful consideration of legal and safety issues to ensure compliance with regulations and to protect your operations and workforce. This section provides a structured overview of key legal considerations and safety protocols necessary for acquiring used industrial equipment.
Legal Considerations When Purchasing Used Industrial Equipment
Buying used industrial equipment like steel rollers comes with specific legal considerations that are crucial to avoid potential legal issues and ensure smooth integration into your operations. It’s important to thoroughly understand these factors to safeguard your investment.
- Compliance with Regulations: Check that the used equipment complies with industry-specific regulations and standards to prevent any legal issues that could arise from non-compliance.
- Ownership Documentation: Confirm the legitimacy of the ownership documents provided by the seller to avoid purchasing stolen or disputed equipment.
- Warranties and Liabilities: Understand any warranties that come with the equipment, noting what liabilities the seller might limit, which could affect your rights as a buyer.
- Environmental Compliance: Ensure that the equipment meets environmental standards related to emissions and hazardous materials, critical for maintaining legal and operational compliance.
- Import and Export Restrictions: Be aware of any legal restrictions on importing or exporting used equipment, which can affect availability and lead to additional costs or legal complications.
- Contractual Obligations: Review the purchase agreement thoroughly to identify any terms that could impose unexpected obligations on your business.
- Dispute Resolution: Establish a clear understanding of the mechanisms in place for resolving any disputes related to the equipment purchase, including the jurisdiction and legal process.
Safety Protocols and Certifications to Check When Purchasing Used Steel Rollers
Ensuring the safety of used steel rollers is paramount not only for compliance with legal standards but also for the protection of your employees and operations. It’s essential to verify that all safety protocols and certifications are up to date before completing a purchase.
- Safety Standards Compliance: Verify that the steel rollers meet all relevant safety standards, which helps prevent workplace accidents and ensures compliance with regulatory requirements.
- Operational Safety Inspections: Have the equipment inspected by a certified professional to identify any potential safety hazards that could affect its safe operation.
- Maintenance Records: Check the historical maintenance records for insights into the equipment’s upkeep and to gauge its condition and reliability.
- Safety Guards and Features: Inspect the equipment for all necessary safety features, such as guards and emergency stops, to ensure they are present and functional.
- Certification Labels: Look for up-to-date certification labels on the equipment, which signify compliance with safety standards.
- Training Requirements: Assess whether additional training will be required for your team to operate the equipment safely and effectively.
- Material Safety Data Sheets (MSDS): For equipment previously used with hazardous substances, ensure that MSDS are available for safe handling and compliance with health and safety regulations.
By addressing these comprehensive legal and safety considerations, you can confidently proceed with purchasing used steel rollers for sale. These steps will help protect your business from unforeseen liabilities and enhance safety in your operational environment.
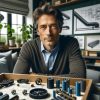
Jordan Smith, a seasoned professional with over 20 years of experience in the conveyor system industry. Jordan’s expertise lies in providing comprehensive solutions for conveyor rollers, belts, and accessories, catering to a wide range of industrial needs. From initial design and configuration to installation and meticulous troubleshooting, Jordan is adept at handling all aspects of conveyor system management. Whether you’re looking to upgrade your production line with efficient conveyor belts, require custom conveyor rollers for specific operations, or need expert advice on selecting the right conveyor accessories for your facility, Jordan is your reliable consultant. For any inquiries or assistance with conveyor system optimization, Jordan is available to share his wealth of knowledge and experience. Feel free to reach out at any time for professional guidance on all matters related to conveyor rollers, belts, and accessories.