Essential Guide to Coal Mining Steel Tube Return Rollers
Coal mining is an essential industry that has fueled the development and growth of many economies worldwide. It involves the extraction of coal from the Earth, which is a critical energy resource for generating electricity and steel production. The process of coal mining requires robust and efficient material handling systems to manage the extraction, transportation, and processing of coal. Effective materials handling is crucial as it ensures operational efficiency, safety, and the sustainability of resources.The introduction of coal mining steel tube return rollers has revolutionized the coal mining industry by enhancing conveyor reliability and durability. This improvement helps minimize downtime and maintenance costs, thereby optimizing the coal handling process and increasing overall productivity in mining operations.
The Coal Mining Process Steps and the Role of Conveyors Featuring Coal Mining Steel Tube Return Rollers
The coal mining process is a comprehensive sequence of operations involving the extraction, processing, and transportation of coal from underground mines. This process is typically divided into several major steps: site preparation, coal extraction, coal loading and transportation, processing, and coal recovery. Integral to these operations are conveyor systems equipped with coal mining steel tube return rollers, which play a crucial role in the efficiency and safety of these processes.
- Site Preparation and Initial Extraction:
Before coal can be extracted, the mining site needs extensive preparation where the surface layer is removed to expose the coal seams. Conveyors equipped with coal mining steel tube return rollers are set up to handle the removed soil, facilitating a smoother and more organized site preparation phase. The durability and reliability of these rollers ensure the handling systems can withstand the harsh mining environment and manage high loads, which is critical in the initial mining stages. - Coal Cutting and Retrieval:
In this step, specialized machines cut through the coal seam. The cut coal is then collected and loaded onto conveyors. Here, coal mining steel tube return rollers support the conveyor belts, preventing them from sagging under the heavy weight of the coal, which helps in the efficient transfer of coal from the face to the processing unit or the surface. - Coal Transportation to Processing Plants:
Once coal is extracted and collected, it needs to be sent to processing plants for purification and grading. Conveyors with coal mining steel tube return rollers are crucial here as they facilitate the long-distance transport of coal across the mining site to the processing area. The steel tube return rollers ensure that the conveyor belts run smoothly, minimizing disruptions due to belt misalignment or excessive wear and tear. - Processing and Quality Control:
At the processing plants, coal is cleaned, sorted, and prepared for sale. Throughout this phase, conveyors continue to play an essential role, and the coal mining steel tube return rollers ensure the conveyance system operates at peak efficiency. These rollers help maintain the belt’s integrity and alignment, which is crucial for the precise handling required during the coal grading and chemical treatment processes. - Loading for Shipment:
The final step in the coal mining process is the loading of processed coal for shipment to customers. Again, conveyors with coal mining steel tube return rollers are indispensable. They transport the processed coal to the loading docks. The robust nature of the steel tube return rollers guarantees that even with heavy, continuous loads, the conveyor belts remain stable and functional, preventing spillage and ensuring that the coal reaches its destination in optimal condition.
Throughout all these steps, coal mining steel tube return rollers are fundamental to the success and efficiency of conveyor systems in coal mining operations. Their ability to support and stabilize the conveyor belts not only enhances the system’s reliability and efficiency but also significantly reduces maintenance needs and downtime, thereby supporting continuous and cost-effective coal production.
What is a Coal Mining Steel Tube Return Roller?
A coal mining steel tube return roller is a specialized component of the conveyor systems used in coal mines. These rollers are crucial in the operation of conveyor belts that facilitate the movement of coal from the mining face to the surface and then on to processing plants. The “return roller” is aptly named as it supports the return path of the belt, which would otherwise sag and potentially cause operational problems due to the heavy load of coal being transported.
Purpose and Functionality of Coal Mining Steel Tube Return Rollers
- Support and Stabilize the Conveyor Belt:
The primary function of coal mining steel tube return rollers is to support the empty running side of the conveyor belt. This is essential to stabilize the belt’s path and prevent it from sagging or swinging, which can occur due to the uneven weight distribution of loaded coal on the operational side. - Reduce Belt Wear and Tear:
By providing a consistent and stable support structure, coal mining steel tube return rollers significantly reduce the wear and tear on the conveyor belt. Less contact between the belt and the conveyor frame means fewer abrasions and a longer life for the belt itself, which is a critical cost-saving in coal mining operations. - Facilitate Efficient Coal Transport:
These rollers ensure that the conveyor belt moves smoothly, facilitating the efficient transport of coal throughout the mining operation. The smooth motion of the belt enabled by the rollers reduces coal spillage that can occur with more erratic movements, enhancing overall operational efficiency. - Maintain Belt Alignment:
Coal mining steel tube return rollers help maintain proper conveyor belt alignment. Misalignment can lead to rapid degradation of the belt and inefficient coal transport. The cylindrical shape and smooth surface of steel tube return rollers ensure that the belt runs straight along the conveyor framework. - Handle Heavy Loads:
The design of coal mining steel tube return rollers allows them to handle the heavy and often uneven loads associated with coal mining. Their robust construction helps withstand the harsh mining environment and the abrasive nature of coal, which demands durability and resilience from all conveyor components.
Coal mining steel tube return rollers are indispensable elements within conveyor systems used in coal mining. Their role in supporting and maintaining the conveyor belt not only ensures the efficient movement of coal but also extends the operational lifespan of the conveyor system itself, thereby optimizing the coal mining process and reducing downtime and maintenance costs. Their specific design and material composition are tailored to meet the rigorous demands of the coal mining industry, proving their critical value in these challenging environments.
The Significance of Coal Mining Steel Tube Return Rollers in Maintaining Belt Integrity
The integrity of conveyor belts is critical in the coal mining industry, where the belts are subjected to heavy loads and continuous operation. Coal mining steel tube return rollers play an essential role in maintaining this integrity by providing consistent support and stability to the return side of the conveyor belts. These rollers are strategically placed along the conveyor framework to ensure that the belts remain functional and efficient over their lifespan.
Detailed Function and Operation of Coal Mining Steel Tube Return Rollers
- Preventing Belt Sagging:
One of the primary functions of coal mining steel tube return rollers is to prevent the conveyor belt from sagging. Sagging can lead to several operational problems, including material spillage, belt misalignment, and increased wear and tear. The cylindrical shape and robust build of steel tube return rollers provide a solid base that supports the belt evenly across its width, preventing any droop and maintaining a smooth surface for the coal to travel on. - Enhancing Belt Life:
By preventing sagging and reducing the incidence of misalignments, coal mining steel tube return rollers considerably enhance the life of conveyor belts. Less sagging means reduced stress and strain on the belt fibers, which in turn diminishes the risk of premature wear and tear. This not only extends the belt’s operational life but also reduces maintenance and replacement costs. - Improving Material Handling Efficiency:
Efficient material handling is crucial in coal mining operations to ensure timely and cost-effective transportation of coal. Coal mining steel tube return rollers facilitate this efficiency by enabling smoother belt movements. This smoothness ensures that the coal remains stable on the conveyor, minimizing spillage and improving the overall handling process. - Maintaining Optimal Belt Tension:
Proper belt tension is essential for optimal conveyor operation. Coal mining steel tube return rollers help in maintaining this tension by ensuring that the belt does not become too slack or overly taut. Correct tension helps prevent slippage at the drive pulleys and excessive wear on the belt and rollers. - Facilitating Easy Maintenance and Replacement:
The design of coal mining steel tube return rollers allows for easy maintenance and replacement. These rollers can be quickly and easily accessed and replaced if they wear down or fail, which is crucial in minimizing downtime in coal mining operations. Their standard cylindrical design and modular assembly mean that they can be interchanged with minimal operational disruption.
Role of Coal Mining Steel Tube Return Rollers in Conveyor Systems
Coal mining steel tube return rollers are integral to the structural integrity of conveyor systems. They support the belt’s weight, distribute loads evenly, and reduce operational stresses. Their impact on the conveyor system’s longevity and efficiency underscores their significance in the coal mining industry. By ensuring that the conveyor belts operate smoothly and reliably, coal mining steel tube return rollers not only preserve the belts’ integrity but also enhance the overall productivity and safety of the mining operation.
Coal mining steel tube return rollers are indispensable in maintaining the integrity and functionality of conveyor belts in the harsh environments of coal mining. Their role in preventing belt sagging, enhancing belt life, maintaining optimal tension, and facilitating maintenance activities makes them a vital component of the coal mining infrastructure. Their effective operation ensures the continuous, efficient, and safe transport of coal, which is fundamental to the profitability and viability of coal mining enterprises.
The Strip Ratio in Coal Mining and Conveyor Efficiency with Coal Mining Steel Tube Return Rollers
The strip ratio is a fundamental aspect in the economics of surface coal mining operations and refers to the volume of overburden (or waste material) that must be removed in order to extract a certain volume of coal. This ratio significantly affects the cost of production and the environmental impact of mining. An optimal strip ratio, which balances extraction costs with mining efficiency, is crucial for the profitability of mining operations. The use of efficient conveyor systems, especially those incorporating coal mining steel tube return rollers, plays a pivotal role in managing and optimizing these ratios.
The Strip Ratio and Its Economic Implications
The strip ratio is expressed as a volume over volume measure, typically bank cubic meters (BCM) of overburden to tonnes of coal. A lower strip ratio means less waste material is moved per unit of coal, which results in reduced mining costs and less environmental degradation. Conversely, a high strip ratio indicates more overburden removal costs and potentially limits the economic viability of the mine.
- Lowering Operational Costs:
Efficient material handling enabled by advanced conveyor systems with coal mining steel tube return rollers significantly reduces the time and energy needed to transport overburden and coal. By optimizing conveyor efficiency, mines can lower the cost per ton of coal extracted, making high strip ratio reserves more economically viable. - Enhancing Material Handling Capacity:
Conveyors fitted with coal mining steel tube return rollers have higher reliability and can handle larger volumes of material with reduced maintenance issues. This capability is crucial in effectively managing the strip ratio by ensuring that overburden is removed efficiently and promptly, which is essential in maintaining a steady coal extraction rate. - Reducing Environmental Impact:
By improving the efficiency of material transport systems, the amount of fuel and emissions associated with the removal of overburden can be significantly reduced. This not only lowers the operation’s carbon footprint but also minimizes the overall environmental impact, aligning with global environmental standards and regulations. - Increasing System Longevity and Reliability:
Coal mining steel tube return rollers contribute to the longevity and reliability of conveyor systems. They reduce the wear and tear on the belt, minimize operational disruptions, and maintain continuous flow of materials, which is critical in achieving an optimal strip ratio.
Role of Coal Mining Steel Tube Return Rollers in Optimizing the Strip Ratio
Conveyor systems equipped with coal mining steel tube return rollers enhance the operational efficiency of coal mines by:
- Stabilizing the Conveyor Belt:
These rollers provide crucial support to the return side of the conveyor belt, preventing sagging and ensuring that the belt runs smoothly. This stability is vital for the efficient movement of large volumes of overburden and coal, which directly influences the strip ratio. - Minimizing Maintenance Downtime:
The robust design of coal mining steel tube return rollers ensures that they are less likely to fail and require less frequent maintenance. This reliability is essential for continuous conveyor operation, especially in mines where the strip ratio is high and large amounts of overburden need to be moved quickly. - Improving Material Transfer Efficiency:
Smooth and reliable belt operation facilitated by steel tube return rollers reduces material spillage during transfer. This efficiency is crucial for maintaining a low strip ratio, as it ensures that all moved material contributes to reaching the mining objectives without unnecessary loss or delay. - Supporting Higher Load Capacities:
Steel tube return rollers are designed to support higher load capacities. This capability allows for the transportation of heavier loads of overburden, which optimizes the material handling process and helps in maintaining an efficient strip ratio.
Coal mining steel tube return rollers are integral to the efficiency of conveyor systems used in coal mining. Their impact on maintaining belt integrity, reducing operational costs, and supporting environmental initiatives makes them a key factor in optimizing the strip ratio and ensuring the economic sustainability of coal mining operations. Their use not only enhances conveyor reliability and efficiency but also contributes significantly to the economic and environmental aspects of coal mining.
Features of Steel Tube Return Rollers in Coal Mining
Steel tube return rollers are pivotal components in the conveyor systems used in coal mining. These rollers are designed to meet the rigorous demands of the mining environment, offering durability, efficiency, and reliability that are crucial for the continuous operation necessary in coal mines. The design and material specifications of coal mining steel tube return rollers, along with their advantages over other materials, highlight their importance in enhancing conveyor system performance.
Design and Material Specifications of Coal Mining Steel Tube Return Rollers
- Material Composition:
Coal mining steel tube return rollers are typically made from heavy-duty steel. This material is chosen for its high strength-to-weight ratio, excellent wear resistance, and ability to withstand the harsh environmental conditions of a coal mine, including moisture and extreme dust. - Tube Thickness:
The tubes used in these rollers are generally thicker than those in standard rollers to prevent deformation under the weight of heavy loads. This thickness ensures that the rollers can support the weight of coal and overburden without bending or breaking. - Bearing and Seal Types:
High-quality, sealed-for-life bearings are used to minimize maintenance requirements and enhance the longevity of the rollers. The seals protect the bearings from dust and water ingress, which are prevalent in the mining environment, thus preserving their functionality and reliability. - Shaft Material and Design:
The shafts of coal mining steel tube return rollers are usually made from cold-drawn steel, which provides superior strength and precision. They are designed to ensure a snug fit within the tube, maximizing the contact area with the bearings to distribute loads evenly and improve the roller’s overall stability. - Surface Treatment:
These rollers often undergo surface treatments such as galvanization or the application of corrosion-resistant coatings. Such treatments enhance the rollers’ resistance to corrosive substances and abrasion, extending their operational life significantly.
Advantages of Using Steel Tube Return Rollers Over Other Materials
- Increased Durability:
Steel tube return rollers offer significantly greater durability than rollers made from materials like plastic or even aluminum. Steel’s inherent strength and resistance to wear and tear mean that these rollers can handle the heavy and abrasive loads typical of coal mining operations without suffering rapid degradation. - Better Load-Bearing Capacity:
The robust nature of steel allows these rollers to support heavier loads over longer periods without deformation. This capability is crucial in mining, where downtime caused by equipment failure carries a high cost. - Lower Maintenance Costs:
The use of sealed-for-life bearings and corrosion-resistant coatings on coal mining steel tube return rollers reduces the need for frequent maintenance. These features prevent the ingress of debris and moisture, which can lead to bearing failures and other common issues in lesser materials. - Enhanced Performance in Harsh Environments:
Steel is ideally suited for use in the variable and harsh conditions of coal mines. It withstands the abrasive nature of coal dust, moisture, and chemical exposures much better than other materials, ensuring consistent performance and reliability. - Improved Conveyor Efficiency:
The smooth and consistent surface provided by steel tube return rollers facilitates a steadier belt movement, reducing vibrations and belt slippage. This not only extends the life of the conveyor belt but also enhances the overall efficiency of the material handling system.
The design and material specifications of coal mining steel tube return rollers are tailored to meet the challenges of the mining industry. Their advantages over other materials make them a superior choice, ensuring reliability, reducing operational costs, and maintaining efficiency in the demanding environment of coal mining. These features collectively make steel tube return rollers an indispensable component of coal mining conveyor systems.
Coal Mining Equipment List: From Excavators to Rollers, Including Coal Mining Steel Tube Return Rollers
In the extensive and demanding context of coal mining, a wide range of heavy equipment is required to handle the tasks from extraction to material transport. This equipment varies from massive excavators and draglines to conveyors equipped with specialized components such as coal mining steel tube return rollers. Each piece of equipment plays a critical role in the mining process, ensuring efficient, safe, and economical coal extraction and processing.
Overview of Heavy Equipment Used in Coal Mining
- Excavators:
These are essential for removing overburden and are some of the largest machines found on a mine site. Hydraulic excavators are particularly effective in digging out earth and loading it onto transport vehicles or conveyors. - Draglines:
Draglines are massive earth movers that remove overburden in strip mining operations. They feature a large bucket suspended from a boom and use a dragging motion to scoop the overburden, clearing the way for miners to reach coal seams. - Continuous Miners:
These machines are used in underground mining operations to extract coal from the seam. They use a rotating drum equipped with teeth that scrape coal from the seam as it moves along the face. - Roof Bolters:
Essential for maintaining the structural integrity of the mine in underground operations, roof bolters are used to install bolts in the roof of the mine to prevent collapses. - Shuttle Cars and Conveyors:
Once the coal is cut, it must be transported from the face to the surface. Shuttle cars are used in underground mines to transport coal to a transfer point, where conveyors equipped with coal mining steel tube return rollers take over the task of surface transport. - Loaders and Trucks:
In open-pit mining, loaders and large trucks are used to transport coal from the mining site to the processing plant. Loaders scoop up the coal after it has been fragmented in blasts and load it into haul trucks. - Conveyors:
These are especially vital as they transport coal across different points in the mine. Equipped with coal mining steel tube return rollers, they ensure the continuous, efficient, and safe transfer of coal.
Emphasis on the Inclusion of Coal Mining Steel Tube Return Rollers in Equipment Lists
Coal mining steel tube return rollers are crucial for the effective functioning of conveyors. Their role and benefits include:
- Supporting the Conveyor Belt:
These rollers support the weight of the conveyor belt along with the coal it carries. This support is crucial to prevent sagging of the belt, which can lead to operational failures. - Enhancing Conveyor Reliability:
By ensuring that the conveyor belt remains intact and free from unnecessary stress, coal mining steel tube return rollers enhance the overall reliability of the conveyor system. This reliability is critical in maintaining continuous production and reducing downtime. - Improving Efficiency:
The smooth operation of conveyor systems aided by steel tube return rollers minimizes the belt’s resistance and the energy required to drive it. This efficiency is essential for reducing operational costs associated with coal transport. - Reducing Maintenance Costs:
Durable materials and robust construction of coal mining steel tube return rollers ensure they last longer and require less frequent replacements, reducing the overall maintenance costs of conveyor systems. - Preventing Material Spillage:
Well-supported belts result in fewer instances of misalignment and spillage. Coal mining steel tube return rollers thus play a significant role in preventing coal spillage, which is a common issue with less robust conveyor setups.
From the giant draglines to the essential coal mining steel tube return rollers, each piece of equipment in the coal mining industry is tailored to fulfill a specific role in the mining and material handling process. The inclusion of these rollers in the equipment list underscores their importance in enhancing conveyor belt integrity, operational efficiency, and overall mine productivity. Their strategic deployment in coal mining operations is indicative of their pivotal role in achieving economic and safety targets in the challenging environment of coal mining.
Choosing the Right Coal Mining Steel Tube Return Roller
Selecting the appropriate coal mining steel tube return roller is crucial for maintaining the efficiency, safety, and longevity of conveyor systems in coal mining operations. The right rollers can significantly enhance conveyor performance, reduce maintenance costs, and prolong the operational lifespan of both the rollers and the conveyor belt. Below are key factors to consider when choosing coal mining steel tube return rollers and the importance of their quality, durability, and compatibility.
Factors to Consider When Selecting Coal Mining Steel Tube Return Rollers
- Load Capacity:
The chosen rollers must be capable of supporting the weight of both the conveyor belt and the material it carries. Higher load capacities are essential for rollers to withstand the heavy and variable loads associated with coal mining without deforming or failing. - Material Quality:
Rollers should be constructed from high-grade steel that offers excellent wear resistance and strength. The quality of the material affects not only the durability but also the performance of the rollers in harsh mining conditions. - Bearing Type:
Bearings are critical for the smooth operation of return rollers. Select bearings that are sealed and designed for high loads and harsh environments to ensure they remain operational without frequent maintenance. - Dimensional Compatibility:
The size and shape of the rollers must fit perfectly with the existing conveyor setup. Incorrectly sized rollers can lead to issues such as belt slippage, increased wear on the rollers and the belt, and ultimately, system failure. - Environmental Resistance:
Consider rollers that are treated or coated to resist the harsh mining environment, including exposure to dust, water, and variable temperatures. Treatments such as galvanization or the use of corrosion-resistant alloys can significantly extend the life of return rollers.
Importance of Quality, Durability, and Compatibility in Coal Mining Steel Tube Return Rollers
- Quality of Construction:
High-quality steel tube return rollers ensure optimal performance under the rigorous conditions of coal mining. Quality affects not only the durability but also the safety of the conveyor system, as poorly manufactured rollers can lead to operational failures. - Durability and Wear Resistance:
Rollers must be able to withstand constant use under heavy loads. Durability directly impacts the frequency and cost of maintenance. Highly durable rollers reduce the need for frequent replacements, saving both time and money. - Compatibility with Conveyor Systems:
Ensuring that the rollers are compatible with the existing conveyor system is crucial. Incompatibility can cause increased mechanical stresses and operational inefficiencies, leading to premature wear and system malfunctions. - Resistance to Environmental Factors:
Steel tube return rollers must be able to operate effectively despite the presence of abrasive particulates, moisture, and chemicals. Enhanced resistance to these factors prevents degradation and extends the roller’s lifespan. - Maintenance Requirements:
Choose rollers that are easy to maintain and replace. Rollers with features such as sealed bearings or self-cleaning mechanisms can significantly decrease downtime and labor costs associated with maintenance.
When choosing the right coal mining steel tube return roller, it is essential to consider factors such as load capacity, material quality, bearing type, dimensional compatibility, and environmental resistance. The selected rollers should also exhibit high quality, durability, and compatibility with the existing conveyor systems to ensure operational efficiency, safety, and cost-effectiveness. These considerations will help maintain the integrity of the conveyor belt and the continuous, smooth operation of coal mining activities.
Case Studies: Success Stories Utilizing Coal Mining Steel Tube Return Rollers
The implementation of coal mining steel tube return rollers has significantly improved the efficiency and durability of conveyor systems in various mining operations around the world. These real-life success stories not only underscore the practical benefits of using high-quality steel tube return rollers but also highlight expert testimonies on their performance. Here are five detailed examples of coal mining operations that have benefited from utilizing these specialized rollers:
Real-Life Examples of Operational Improvements
- The Wyoming Coal Mining Project:
In the expansive coal fields of Wyoming, USA, one of the largest surface mines implemented steel tube return rollers across their over 20 miles of conveyor systems. The result was a dramatic reduction in maintenance downtime by 75% and a significant increase in belt life. The steel tube rollers provided much-needed durability against the abrasive coal dust and harsh environmental conditions. - The Queensland Coal Association (QCA) Initiative:
Several mines in Queensland, Australia, participated in a study to replace traditional rollers with coal mining steel tube return rollers. These mines saw an average increase in overall conveyor efficiency by 30%, with the new rollers offering better support to the conveyor belts and reducing instances of belt misalignment and slippage. - The Siberian Coal Energy Company (SUEK):
This Russian coal giant reported a 50% decrease in operational costs related to conveyor maintenance after switching to steel tube return rollers. The rollers’ robust construction meant they could handle the extreme cold and load capacities much more effectively than the previous materials used. - The South African Coal Mining Holdings:
A prominent coal miner in South Africa enhanced conveyor lifespans across their operations by integrating coal mining steel tube return rollers. The change not only improved belt life by 40% but also reduced energy consumption due to decreased friction and smoother belt operation. - The India-based Singareni Collieries Company Limited (SCCL):
SCCL noted a 60% reduction in conveyor-related downtime after adopting steel tube return rollers. The enhanced roller design provided by the steel tubes allowed for better debris management, which is critical given the region’s high dust levels.
Testimonies from Industry Experts on Steel Tube Return Rollers
- Mining Engineer from Wyoming:
“The adoption of steel tube return rollers was a game changer for our operations. Their durability under heavy load significantly outperforms traditional rollers, and we’ve seen a substantial decrease in belt damage incidents.” - Conveyor Technician in Queensland:
“These rollers are far superior in managing the harsh conditions of coal mining. They maintain their integrity longer than any other type we’ve used, which means less frequent replacements and more consistent operation.” - Operations Manager at SUEK:
“We were particularly impressed with how well the steel tube return rollers performed under the severe Siberian winter conditions. Their performance exceeded our expectations, providing reliable service without the need for constant maintenance.” - Maintenance Supervisor in South Africa:
“The coal mining steel tube return rollers have not only saved us on maintenance costs but have also improved our environmental compliance by reducing debris and dust escape.” - Chief Mechanical Engineer at SCCL:
“Switching to steel tube return rollers significantly lowered our operational interruptions. The smooth running of belts has improved coal handling efficiency and reduced power consumption, which is a huge plus for us.”
These case studies and expert testimonies clearly illustrate the substantial benefits of using coal mining steel tube return rollers. Their ability to improve conveyor reliability, efficiency, and sustainability in coal mining operations makes them a critical component in modern mining infrastructures around the globe. The positive impacts are felt not just in reduced operational costs but also in enhanced safety and environmental performance.
Future Developments and Technological Advancements in Coal Mining Steel Tube Return Rollers
The coal mining industry continuously seeks to optimize efficiency and reduce operational costs through technological advancements. Coal mining steel tube return rollers, critical components of conveyor systems, are central to these innovations. Future developments in roller technology are poised to further enhance their performance, durability, and environmental compatibility. Here are five examples of potential innovations in roller technology aimed at the coal mining industry, along with expected improvements and research areas in materials and design.
Innovations in Roller Technology
- Smart Roller Technology:
Future coal mining steel tube return rollers could incorporate sensors to monitor their health and the status of the conveyor belt in real-time. These smart rollers would use IoT (Internet of Things) connectivity to predict failures before they occur, significantly reducing downtime and maintenance costs. - High-Performance Coatings:
The application of advanced coatings that resist wear and reduce friction could improve the longevity and efficiency of rollers. Coatings such as tungsten carbide or specialized polymers could prevent material build-up, facilitating cleaner and smoother operations. - Improved Bearing Designs:
Bearings are a critical failure point in return rollers. Research into self-lubricating, high-load bearings could lead to developments where bearings have longer lifespans and are capable of withstanding the severe loads and environmental conditions found in coal mining. - Modular Roller Designs:
Developing modular rollers that can be easily assembled or disassembled on-site would simplify the replacement process and minimize conveyor downtime. These designs would allow for quick swaps of individual components, such as bearings or seals, without the need to replace the entire roller. - Eco-friendly Materials:
As the industry moves towards more sustainable practices, the development of return rollers from recycled or eco-friendly materials could gain traction. These materials must maintain the strength and durability standards required for the harsh mining environment while reducing the carbon footprint of their production and disposal.
Potential Future Improvements and Research in Materials and Design
- Composite Materials:
Investigating the use of composite materials that combine the strength of steel with the lightness of aluminum or plastics could result in rollers that are lightweight, reducing energy consumption, yet still durable enough for heavy-duty use. - Thermal Spraying Techniques:
Research into thermal spraying techniques to apply surface coatings could enhance the wear resistance of rollers. By applying layers of protective materials, rollers can be customized for specific conditions, such as high-moisture environments or areas with high particulate concentrations. - Advanced Fabrication Methods:
The use of advanced fabrication methods such as 3D printing could revolutionize the manufacturing of coal mining steel tube return rollers. This technology could allow for the precise creation of rollers with complex internal geometries or integrated sensors without significant additional cost. - Vibration Dampening Technologies:
Developing rollers with built-in vibration dampening features would help prolong the life of the conveyor belt and reduce noise, which is a significant issue in many mining operations. This technology would also improve the working conditions for miners by reducing the ambient noise level. - Temperature Resistant Materials:
Exploring materials that are resistant to temperature changes can lead to rollers that perform consistently across a range of environmental conditions. This is particularly important in open-pit mines where temperature variations between day and night can be extreme.
The future of coal mining steel tube return rollers looks promising with the integration of advanced technologies and materials aimed at improving their functionality and efficiency. These advancements will not only enhance the operational capabilities of coal mining conveyor systems but also contribute to the industry’s sustainability goals. As research continues and these technologies mature, we can expect to see even more innovative solutions being implemented in mining operations worldwide.
FAQs About Coal Mining Steel Tube Return Roller
In coal mining, several types of conveyors are used depending on the site, the specific requirements of the operation, and the material being transported. The most common types of conveyors used in coal mining include:
Belt Conveyors: These are the most widely used conveyors in coal mines due to their versatility, efficiency, and cost-effectiveness. Belt conveyors consist of a continuous belt that rides on roller supports or over a flat pan that extends over the path. They can move coal over long distances, and can navigate terrain that would be challenging for other types of machinery.
Chain Conveyors: Chain conveyors are typically used to transport coal short distances from the face under the coal mine to the primary crusher or the transportation system. They utilize a powered continuous chain arrangement, carrying a series of single pendants. These conveyors are particularly useful for their high-load carrying capacity and their ability to operate in rugged environments.
Screw Conveyors: These conveyors are used for more granular or smaller sized materials. Screw conveyors utilize a helical screw element that rotates to move the material along the screw’s axis. In coal mining, they are used for fine grained coal, dust, and particles that require precise movements.
Overland Conveyors: When coal needs to be transported over significant distances outside the mining area, overland conveyors are utilized. These specialized belt conveyors are engineered to cover long distances, navigating through curves and undulations where required.
Shuttle Conveyors: These conveyors are movable and reversible, which is ideal for filling multiple hoppers uniformly. Shuttle conveyors allow for coal to be discharged at any point along the track which is especially useful in bulk handling applications.
Each type of conveyor has specific features that make it suitable for certain operations and not for others. The choice of conveyor system depends largely on the mine layout, the extraction method, and the nature of the coal being processed.
Rollers in the mining industry, particularly in coal mining, are critical components of conveyor systems. They are designed to facilitate the smooth and efficient transport of materials through the mining site. Rollers are essentially the backbone of any conveyor belt system, including:
Steel Tube Return Rollers: These rollers support the return side of the conveyor belt and are essential for preventing the belt from sagging under the weight of the coal being transported. Their robust construction helps in maintaining the belt’s integrity and alignment, which are crucial for the smooth operation of the conveyor.
Impact Rollers: Placed at points where material is loaded onto the belt, impact rollers absorb the shock and stress of falling materials. In coal mining, these rollers are positioned in the loading zone to reduce the impact on the conveyor belt when coal is dumped from trucks or loaders, which helps in extending the belt’s lifespan.
Guide Rollers: Guide rollers help to keep the conveyor belt in place, preventing lateral movements that could lead to misalignments or potential derailments. They are particularly important in the rough terrain of mining environments.
Spiral Rollers: These are used to remove dirt, dust, and other particulate build-ups from the belt, which is a common issue in the mining industry. Spiral rollers brush against the belt as it moves, cleaning it effectively.
Rubber-Coated Rollers: These rollers are used to enhance the grip between the belt and the roller, which helps in preventing slippage due to the heavy loads of coal. The rubber coating also reduces wear-and-tear on both the rollers and the belt.
Choosing the right type of roller and maintaining them properly is crucial for the efficiency of conveyor belts in the mining industry. They must be rugged enough to withstand harsh mining conditions while ensuring the conveyor belt operates smoothly. This not only optimizes the transportation process but also minimizes downtime due to mechanical failures.
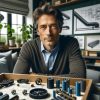
Jordan Smith, a seasoned professional with over 20 years of experience in the conveyor system industry. Jordan’s expertise lies in providing comprehensive solutions for conveyor rollers, belts, and accessories, catering to a wide range of industrial needs. From initial design and configuration to installation and meticulous troubleshooting, Jordan is adept at handling all aspects of conveyor system management. Whether you’re looking to upgrade your production line with efficient conveyor belts, require custom conveyor rollers for specific operations, or need expert advice on selecting the right conveyor accessories for your facility, Jordan is your reliable consultant. For any inquiries or assistance with conveyor system optimization, Jordan is available to share his wealth of knowledge and experience. Feel free to reach out at any time for professional guidance on all matters related to conveyor rollers, belts, and accessories.