Navigating Stainless Steel Roller Prices: Key Insights Revealed
Stainless steel rollers are indispensable components in various industrial sectors, including manufacturing, packaging, and material handling, due to their exceptional durability, resistance to corrosion, and ability to maintain cleanliness. The choice of stainless steel as a material enhances the longevity and reliability of these rollers, making them an essential element in environments where these properties are critical. However, the cost of acquiring these vital components can significantly impact operational budgets, making the understanding of stainless steel roller prices crucial for potential buyers. It’s not merely about finding a product that fits the operational needs but also about ensuring that the investment aligns with financial constraints and delivers value over time. As such, a deep dive into the factors that influence stainless steel roller prices is necessary. This exploration is not only beneficial for budgeting and planning but also vital for making informed decisions that affect the efficiency and productivity of industrial operations.
Factors Influencing Stainless Steel Roller Prices
Understanding the intricacies behind stainless steel roller prices is essential for anyone in the market for these industrial components. Several key factors come into play, each influencing the final cost to varying degrees. This section delves into four specific examples of these factors: material grade, manufacturing process, market demand, and additional features or specifications.
Material Grade
The material grade of stainless steel directly impacts the stainless steel roller price. Higher-grade materials, known for their superior corrosion resistance and strength, command higher prices. For instance, grade 304 stainless steel is widely used for its excellent corrosion resistance and value. In contrast, grade 316 offers even higher corrosion resistance but at a higher cost, affecting the overall price of the roller. Similarly, specialty grades tailored for extreme environments or specific industrial applications can significantly alter the price.
Manufacturing Process
The manufacturing process employed to produce stainless steel rollers also plays a crucial role in determining the price. Techniques such as cold rolling offer precise dimensions and smoother surfaces but at a higher production cost. Advanced welding techniques to ensure seamlessness or specialized finishes for enhanced durability can further increase the price. Moreover, the complexity of the design and the precision required in the manufacturing process can escalate costs, reflecting in the stainless steel roller price.
Market Demand
Market demand is a dynamic factor influencing stainless steel roller prices. During periods of high demand, prices tend to increase due to the principles of supply and demand. Industries experiencing growth spur demand for stainless steel rollers, pushing prices upward. Conversely, during downturns or when alternative materials become more popular, prices may stabilize or decrease. Additionally, global economic conditions, including tariffs and trade policies, can impact material costs and availability, affecting the final price of stainless steel rollers.
Additional Features or Specifications
The inclusion of additional features or specifications can also affect the stainless steel roller price. Rollers equipped with specialized bearings for high-speed operations, coatings for extra protection against chemicals or wear, and custom dimensions or profiles for specific applications often carry a premium. These enhancements, while increasing performance and lifespan, contribute to the cost of manufacturing and, consequently, the market price of the roller.
The stainless steel roller price is influenced by a complex interplay of factors. Buyers must consider not only the upfront cost but also the value these rollers bring to their operations in terms of durability, performance, and suitability for specific applications. An understanding of these factors can guide purchasers in making informed decisions that balance cost with operational needs.
Heavy Duty Stainless Steel Roller Price
The heavy-duty stainless steel roller price reflects the necessity for durability, precision, and the ability to withstand extreme conditions in industrial applications. These rollers are designed to operate under high stress, in corrosive environments, or where high degrees of cleanliness are required. The pricing of these heavy-duty variants is influenced by their enhanced specifications, material choice, and the additional manufacturing processes they must undergo to meet stringent requirements. Below, we discuss how these factors impact the cost, providing specific examples of industrial applications.
Enhanced Material Specifications
For heavy-duty applications, the choice of higher-grade stainless steel significantly influences the stainless steel roller price. For example, rollers designed for use in the chemical industry or marine environments might utilize duplex stainless steel, known for its exceptional strength and corrosion resistance. This material choice, while increasing durability, also elevates the cost due to the higher price of the alloy and the complexity of working with it.
Advanced Manufacturing Processes
The manufacturing processes for heavy-duty stainless steel rollers involve additional steps to ensure that they can withstand the rigors of their intended use. Techniques such as precision machining to achieve tighter tolerances and heat treatments to enhance strength contribute to the overall cost. For instance, rollers used in high-speed printing presses require precise dimensional accuracy to prevent paper slippage, increasing production costs.
Industrial Applications
Specific examples of industrial applications that necessitate the use of heavy-duty stainless steel rollers include:
- Mining and Quarrying: Rollers in these sectors need to resist abrasive dust and heavy loads, driving up their price due to the need for robust construction and special sealing technologies.
- Food Processing: Here, the demand for stainless steel rollers with food-grade finishes and the ability to be frequently washed down without corrosion adds to the cost.
- Pharmaceutical Manufacturing: Rollers used in this industry must not only withstand chemical exposure but also meet strict hygiene standards, necessitating premium materials and finishes.
- Automotive Assembly Lines: The heavy loads and continuous operation require rollers that can maintain precision under stress, leading to higher prices for these specialized components.
Impact of Durability and Specifications on Cost
The durability and specifications required for heavy loads directly impact the heavy-duty stainless steel roller price. These rollers often feature enhanced load-bearing capabilities, specialized surface treatments to resist wear and tear, and custom engineering to meet specific operational requirements. Each of these factors adds to the manufacturing complexity and material costs, increasing the overall price of the roller. However, the investment in high-quality, heavy-duty rollers can lead to longer service life, reduced maintenance costs, and improved efficiency, ultimately providing value over time despite the higher initial expense.
The heavy-duty stainless steel roller price is a function of the materials, manufacturing processes, and specifications required to meet the demands of extreme industrial applications. Understanding these factors can help buyers make informed decisions, ensuring they invest in rollers that offer the best balance of performance, durability, and cost-effectiveness for their specific needs.
Used Stainless Steel Roller Price
The used stainless steel roller price offers an attractive alternative for budget-conscious buyers seeking quality components for their industrial setups. The secondary market for these rollers is vibrant, driven by the need for cost efficiency without compromising on the essential benefits that stainless steel rollers provide. This section provides insights into the market for used or refurbished steel rollers and shares tips for assessing quality to ensure a cost-effective purchase.
Insights into the Market
The market for used stainless steel rollers is shaped by several factors that influence price, including the condition of the roller, its age, and the specific type or grade of stainless steel. Refurbished rollers, which have been restored to a condition that is similar to new, often command higher prices than those sold as-is. However, they still represent a significant saving compared to new items. The availability of used rollers varies by industry, with more common types being easier and cheaper to procure than specialized or custom-made rollers.
Tips for Assessing Quality
- Inspect for Wear and Tear: Carefully examine the roller for signs of excessive wear, such as deep scratches or dents, which could impact its functionality. The extent of wear and tear can significantly affect the used stainless steel roller price.
- Check for Corrosion: While stainless steel is resistant to corrosion, improper use or maintenance can lead to damage. Presence of rust or pitting on the roller surface could indicate neglect.
- Verify Operational Integrity: If possible, test the roller under load or ask for a demonstration. This can help assess whether the roller can perform as required for your specific application.
- Inquire About History: Understanding the roller’s history, including its previous application and maintenance record, can provide insights into its condition and expected lifespan.
Making a Cost-Effective Purchase
When navigating the used stainless steel roller price, balancing cost savings with quality assurance is key. Potential buyers should consider:
- Warranty or Guarantee: Some sellers offer a warranty on used or refurbished rollers, providing an added layer of security.
- Supplier Reputation: Purchasing from reputable suppliers who are known for quality refurbishing processes can mitigate risks.
- Compatibility: Ensure the roller fits your system’s specifications. Mismatches can negate any initial savings through increased adaptation costs.
- Long-Term Value: Assess the roller’s remaining lifespan against its cost to determine if it offers true value over time.
The decision to purchase used stainless steel rollers can significantly reduce capital expenditure, allowing for the allocation of resources to other areas of need. By thoroughly assessing the condition and suitability of the used rollers, buyers can secure equipment that meets their operational requirements at a fraction of the cost of new equipment. This approach not only optimizes budget allocation but also supports sustainability by extending the service life of industrial components.
Stainless Steel Roller Price in the USA
The stainless steel roller price in the USA is influenced by a complex interplay of factors, including the costs associated with local manufacturing and importation. This section offers a comparative analysis of prices within the American market and examines how the origin of manufacture affects the final pricing of these essential industrial components.
Comparative Analysis in the USA
In the USA, stainless steel roller prices vary widely based on size, grade, and specific application requirements. For example:
- Small Rollers for Conveyor Systems: Smaller rollers designed for light to medium load conveyor systems in distribution centers might be priced differently depending on whether they are standard sizes or require custom specifications.
- Food Industry Rollers: Rollers used in the food industry, which require specific grades of stainless steel to meet hygiene standards, typically command a premium over those used in less regulated sectors.
- Heavy-Duty Industrial Rollers: Large, heavy-duty rollers designed for mining or agricultural equipment are on the higher end of the price spectrum, reflecting the need for durability and performance under harsh conditions.
- Precision Rollers for Printing and Packaging: High-precision rollers used in the printing and packaging industry, where exact tolerances are critical, also tend to have higher prices due to the advanced manufacturing techniques required.
Local Manufacturing vs. Importation
The origin of stainless steel rollers significantly impacts their price in the USA for several reasons:
- Manufacturing Costs: Locally manufactured rollers often have higher prices due to the relatively high labor and production costs in the USA. However, buying American-made products can mean shorter lead times and better quality control, potentially offsetting the higher initial cost.
- Import Tariffs and Duties: Imported rollers may be subject to tariffs and import duties, which can increase their cost. These additional charges are particularly relevant in times of trade tensions or when protective tariffs are in place to safeguard domestic industries.
- Transportation and Logistics: The cost of shipping large or heavy items like industrial rollers from overseas can be substantial, adding to the final price. This factor is less significant for domestically produced rollers, where transportation distances are generally shorter.
- Exchange Rates: Fluctuations in currency exchange rates can affect the price of imported stainless steel rollers. A stronger US dollar makes imports more affordable, whereas a weaker dollar does the opposite, making domestically manufactured rollers more competitively priced in comparison.
The decision between opting for locally manufactured stainless steel rollers versus imported ones involves considering not only the initial purchase price but also the total cost of ownership, which includes factors such as delivery times, potential for custom orders, and the ease of resolving any issues that may arise. While the stainless steel roller price in the USA may initially seem higher for domestic products, the long-term benefits of local sourcing, including supporting the national economy and ensuring quick access to support and replacements, can provide significant value to businesses.
Assessing the Impact of Stainless Steel Roller Price on Machinery Cost and Value
The stainless steel roller price is not only relevant to the rollers themselves but also plays a significant role in the overall cost and valuation of machines that utilize these components. Stainless steel rollers are integral to the functionality and efficiency of various machinery across industries, from printing and textile manufacturing to food processing and conveyance systems. This section provides an overview of the machines that rely on these rollers and how their requirements influence the stainless steel roller price, accompanied by case studies highlighting common applications.
Influence on Machine Price
Machines that incorporate stainless steel rollers often see a direct impact on their price due to the quality, precision, and durability requirements of these components. High-quality rollers can enhance machine performance, extend service life, and reduce maintenance needs, factors that are reflected in the machine’s initial cost. The specific requirements for the rollers, such as their size, grade of stainless steel, surface finish, and tolerance levels, can significantly vary, influencing the final pricing of the machinery.
Case Studies of Common Applications
- Printing Presses: Modern printing machines require rollers that can maintain precise tension and pressure across various media types to ensure high-quality prints. The precision and quality of the stainless steel rollers used in these machines directly affect the clarity and consistency of the print, thereby influencing the machine’s price. Maintenance and replacement costs for these high-precision rollers can also impact the overall cost-effectiveness of the equipment.
- Food Processing Equipment: Rollers in food processing machines must meet stringent hygiene and corrosion resistance standards, necessitating the use of high-grade stainless steel. The additional requirements for food-grade finishes and the ability to withstand frequent cleaning with harsh chemicals contribute to the stainless steel roller price, affecting the overall cost of the machinery.
- Textile Machinery: In the textile industry, rollers are used for fabric guiding, tensioning, and stretching. The need for smooth, non-abrasive surfaces to prevent fabric damage requires specialized finishes on the stainless steel rollers, adding to the machine’s price. The durability and quality of these rollers are crucial for ensuring continuous operation and fabric quality.
- Conveyor Systems: Industrial conveyor systems use stainless steel rollers for their durability and ability to handle heavy loads without deformation. The size and load-bearing capacity of these rollers can greatly vary, influencing the stainless steel roller price. Conveyor systems in industries such as mining, automotive, and logistics particularly benefit from the long service life and low maintenance requirements of high-quality stainless steel rollers.
The integration of stainless steel rollers into machinery represents a critical investment in the machine’s performance, longevity, and reliability. While the initial cost may be higher, the use of these rollers can lead to reduced downtime, lower maintenance costs, and improved product quality, justifying the premium in the stainless steel roller price. Buyers and manufacturers alike must consider these factors when evaluating machinery investments to ensure they achieve the best balance of cost, performance, and durability.
Decoding the Stainless Steel Roller Price in Conveyor System Investments
The stainless steel roller price is a critical component in determining the overall cost of stainless steel roller conveyor systems. These conveyors are favored in industries where hygiene, corrosion resistance, and durability are paramount, such as food processing, pharmaceuticals, and chemical manufacturing. This section provides a breakdown of the costs associated with stainless steel roller conveyors and outlines the key factors to consider when investing in such a system.
Breakdown of Costs
The cost of a stainless steel roller conveyor system encompasses several elements beyond the basic price of the rollers. These include:
- Roller Material and Grade: The grade of stainless steel affects resistance to corrosion and strength, influencing the price. Higher grades with enhanced properties cost more but offer better longevity and performance under harsh conditions.
- Conveyor Frame Material: While the rollers might be stainless steel, the frame can also be made of the same material or a less expensive metal. A stainless steel frame increases the system’s overall cost but provides superior durability and resistance to corrosive environments.
- Customization and Size: Custom-sized conveyors or those requiring specific features to accommodate unique products or processes can significantly increase the cost. Customization may involve unique roller diameters, widths, or spacing to suit particular handling requirements.
- Additional Features: Features such as integrated motors, adjustable speeds, side guides, and special coatings for the rollers can all contribute to the final price. These enhancements improve functionality and efficiency but at an additional cost.
Factors to Consider When Investing
When considering the investment in a stainless steel roller conveyor system, several factors come into play:
- Operational Environment: The specific conditions under which the conveyor will operate can dictate the necessary grade of stainless steel and any additional protective features. Environments with high moisture, acidic substances, or salt exposure require higher grades to prevent corrosion.
- Load Requirements: The weight and size of the items the conveyor will transport influence the type of rollers needed. Heavier loads require more robust rollers and stronger frame construction, impacting the stainless steel roller price and overall system cost.
- Maintenance and Cleaning: The ease of maintenance and cleaning should be considered, especially in industries where hygiene is a priority. Systems designed for easy disassembly and cleaning may cost more upfront but save on maintenance and ensure compliance with hygiene standards.
- Future Scalability: The potential need to expand or modify the conveyor system in the future should be considered. Investing in a modular system might be more costly initially but allows for easier and cost-effective adjustments as operational needs change.
Investing in a stainless steel roller conveyor system requires careful consideration of both the initial stainless steel roller price and the long-term benefits it offers. Factors such as operational efficiency, durability, and compliance with industry standards play a crucial role in the decision-making process. By evaluating these considerations, businesses can ensure they select a conveyor system that provides the best value and performance for their specific needs.
Evaluating Heavy-Duty Steel Rollers Versus Stainless Steel Roller Price Impacts
The stainless steel roller price often sets a benchmark in the market for heavy-duty roller applications, yet it’s insightful to examine how heavy-duty steel rollers, not specifically made of stainless steel, fit into the pricing spectrum. These rollers, crafted from materials such as carbon steel or alloy steel, are designed for environments where the anti-corrosive properties of stainless steel are not a necessity. This section delves into the price range of these heavy-duty steel rollers and compares their applications and cost-effectiveness with their stainless steel counterparts.
Price Range Examination
Heavy-duty steel rollers made from carbon or alloy steel typically come at a lower price point than those made from stainless steel due to the cost of materials. The price for these rollers is influenced by the steel grade, the complexity of the manufacturing process, and the scale of production. However, the absence of stainless steel’s anti-corrosive properties means that these rollers may require additional treatments or coatings to extend their lifespan, depending on the application, which can affect the overall cost.
Applications and Pricing Comparison
Heavy-duty steel rollers are utilized across a broad range of industrial applications, from manufacturing lines and assembly plants to heavy load transportation systems. Their robustness makes them suitable for environments where high strength and durability are required, but exposure to corrosive elements is minimal.
To provide a clearer understanding, below is a comparative overview presented in a table format, highlighting the typical applications and pricing differences between heavy-duty steel rollers and stainless steel variants.
Feature | Heavy-Duty Steel Rollers | Stainless Steel Rollers |
---|---|---|
Material Cost | Generally lower due to less expensive materials. | Higher due to the cost of stainless steel. |
Durability | High strength; may require coatings for corrosion resistance. | Naturally high corrosion resistance; durable without additional treatments. |
Applications | Suitable for environments where corrosion is not a concern, such as manufacturing and heavy load bearing. | Preferred in corrosive environments, such as food processing and chemical handling. |
Maintenance | May require more maintenance if not properly coated or if the coating wears off. | Typically lower maintenance due to inherent corrosion resistance. |
Price Range | More cost-effective initially but may incur additional costs for coatings or maintenance. | Higher initial cost but potentially lower total cost of ownership due to durability and low maintenance needs. |
This comparison highlights the key differences in applications and the impact on the stainless steel roller price versus heavy-duty steel rollers. While stainless steel rollers are an investment in durability and corrosion resistance, heavy-duty steel rollers offer a more budget-friendly option in environments where these characteristics are not critical. Ultimately, the choice between these two types of rollers should be based on the specific requirements of the application, considering both the initial investment and the long-term operational costs.
Comparing Steel Hand Rollers to Automated Systems: A Stainless Steel Roller Price Perspective
In exploring the stainless steel roller price, it’s essential to consider the niche yet significant market of steel hand rollers. These manual devices, utilized in various settings from construction to printing, offer a contrast to the more commonly discussed automated stainless steel rollers. Steel hand rollers are valued for their precision, portability, and direct control, catering to specific applications where machinery cannot replicate the required touch or pressure. This section outlines their applications and price points and compares them with automated stainless steel rollers.
Applications and Price Points
Steel hand rollers are deployed in diverse environments, each with unique demands:
- Construction and Flooring: Used for flattening, smoothing, or applying materials like roofing, waterproofing membranes, or vinyl flooring. Price points vary based on size and the specific design tailored to material handling.
- Printmaking: Essential in traditional printmaking techniques for evenly applying pressure to transfer ink from a plate to paper. The cost reflects the precision and material quality needed for artistic applications.
- Leather Working: Employed for flattening or bonding layers of leather, hand rollers in this niche are priced for their durability and the smooth finish they can achieve on sensitive materials.
- Pottery and Clay Work: Used to roll out clay to a consistent thickness or to apply patterns. Price points are influenced by the material of the roller and the complexity of designs it can produce.
Comparison with Automated Stainless Steel Rollers
While steel hand rollers and automated stainless steel rollers serve vastly different purposes, comparing them illuminates the considerations behind the stainless steel roller price and the broader market dynamics.
Feature | Steel Hand Rollers | Automated Stainless Steel Rollers |
---|---|---|
Application | Direct, manual applications requiring personal control. | Large-scale, automated processes needing consistent results. |
Material | Often high-quality steel, not necessarily stainless. | Primarily stainless steel for its durability and corrosion resistance. |
Cost Factors | Size, complexity, and specific application design. | Material grade, manufacturing technology, and precision engineering. |
Price Range | Generally lower, reflecting the manual nature and smaller scale. | Higher, due to advanced engineering, material costs, and automation features. |
This comparison highlights how the stainless steel roller price is part of a broader spectrum of costs, influenced by the application’s scale, automation level, and material requirements. While automated rollers represent a significant investment in industrial efficiency and longevity, steel hand rollers cater to a market that values craftsmanship, direct control, and the ability to work closely with materials. The choice between these tools depends on the specific needs of the task at hand, balancing the benefits of manual precision against the efficiency and consistency of automation.
Industrial Steel Roller
The stainless steel roller price within the context of industrial applications highlights the complexity and variability inherent in industrial equipment procurement. Industrial steel rollers, encompassing both stainless steel variants and other types of steel rollers, are crucial components in numerous sectors, including manufacturing, logistics, and material handling. Their pricing dynamics are influenced by a range of factors from material specifications to customization requirements. This section delves into these aspects, offering insights into the pricing of industrial steel rollers and the impact of customization on cost.
Pricing Dynamics
The price of industrial steel rollers is influenced by several key factors:
- Material Type and Grade: The choice between stainless steel, carbon steel, and alloy steel, each with its grade and properties, directly affects the price. Stainless steel rollers, especially those in higher grades, command a premium due to their corrosion resistance and durability.
- Manufacturing Process: Techniques such as forging, casting, and machining impact the final cost. More complex manufacturing processes that enhance precision or durability can increase prices.
- Size and Weight: Larger and heavier rollers require more material and more complex manufacturing processes, leading to higher costs.
- Market Demand: Fluctuations in demand for industrial steel rollers can cause price variability. High demand in sectors like e-commerce logistics can drive up prices due to increased need for conveyor systems.
Role of Customization in Cost Determination
Customization plays a pivotal role in determining the stainless steel roller price. Tailoring rollers to specific industrial applications can significantly affect cost due to the additional design, engineering, and manufacturing efforts required. Examples of customization that impact price include:
- Surface Treatments: Custom coatings or treatments to enhance corrosion resistance, reduce wear, or improve traction can increase the price. For example, a non-stick coating for rollers used in packaging or food processing adds to the cost.
- Bearing Integrations: Incorporating specialized bearings to handle higher speeds or loads requires precision engineering, adding to the price.
- Custom Dimensions: Rollers designed to fit specific machinery or conveyance systems outside of standard sizes necessitate unique manufacturing setups and can lead to higher prices.
- Specialized Features: Features such as integrated sensors for condition monitoring or temperature resistance for use in high-heat environments tailor the roller to specific needs but also add to the manufacturing complexity and cost.
In conclusion, the stainless steel roller price in industrial settings is not a static figure but a reflection of a multitude of factors, including material choice, manufacturing processes, and particularly customization. The degree of customization required for a roller to meet the unique demands of an application can significantly elevate its price, underscoring the importance of precise specification and design in the procurement process. These factors combined determine the overall value proposition of industrial steel rollers, balancing initial costs against performance, durability, and operational efficiency.
Steel Slip Roller
In the realm of metalworking, the stainless steel roller price also extends to specialized equipment like steel slip rollers. These tools are essential for bending and shaping sheet metal into curves, tubes, and coils, serving a vital function in workshops and manufacturing settings where metal fabrication is required. The versatility and precision of steel slip rollers make them indispensable for creating metalwork pieces with specific curvature and dimensions, ranging from automotive parts to architectural metalwork.
Overview of Steel Slip Rollers and Their Uses
Steel slip rollers are designed to manipulate sheet metal through a series of adjustable rollers, allowing the user to control the radius of the curve produced. These machines can handle various metal thicknesses and widths, depending on their design and capacity. Specific uses include:
- Automotive Bodywork: Creating curved panels and components for car restoration and customization.
- Architectural Metalwork: Shaping metal for decorative trim, roofing components, and structural features.
- HVAC Ductwork: Fabricating ducts and vents with precise curves for heating, ventilation, and air conditioning systems.
- Art and Sculpture: Enabling artists to form complex shapes and structures for metal sculptures.
Pricing Guide for Steel Slip Rollers
The stainless steel roller price for slip rollers is influenced by several factors that prospective buyers should consider. These include the roller’s size, capacity (the maximum thickness, and width of metal it can handle), and the level of precision it offers. Additionally, features such as motorization, programmability, and construction materials (e.g., carbon steel versus stainless steel) play significant roles in determining the price. Here’s a general guide:
- Entry-Level Manual Rollers: Suitable for hobbyists and small workshops, these models are typically the most affordable, designed for light-duty work with thinner metals.
- Mid-Range Manual and Motorized Rollers: Offering a balance between capability and cost, these models can handle a wider range of metal thicknesses and widths, with motorized options reducing manual labor.
- High-End and Industrial Rollers: Designed for heavy-duty use in industrial settings, these rollers feature larger capacities, motorization, and advanced features like programmable control systems for precision work.
Investing in a steel slip roller involves balancing the cost with the specific needs of the work to be undertaken. For those engaged in regular sheet metal work requiring high precision and versatility, investing in a mid-range to high-end model can provide the necessary functionality and efficiency. Meanwhile, hobbyists or those with occasional metalworking projects might find entry-level manual rollers to be a cost-effective solution. Understanding the stainless steel roller price in this context allows buyers to make informed decisions based on their operational requirements and budget constraints.
Navigating Stainless Steel Roller Price for Steel Roller Wheels
The stainless steel roller price extends its relevance to the specialized segment of steel roller wheels, essential components in numerous applications, from material handling equipment to heavy machinery. These wheels come in various forms to suit different operational needs, with material choice playing a significant role in determining their price and performance. This section explores the diversity of steel roller wheels available in the market and discusses how the choice between stainless steel and regular steel impacts their pricing and application suitability.
Variety of Steel Roller Wheels
Steel roller wheels are designed to meet a wide range of industrial requirements, including load-bearing capacity, environmental resistance, and operational speed.
- Conveyor Wheels: Used in conveyor systems to facilitate the smooth movement of goods and materials. These wheels are designed for high durability and can accommodate various weights and speeds.
- Track Wheels: Specifically designed to run on tracks, such as those used in gate systems or sliding doors in industrial settings. Their design focuses on precise alignment and smooth operation.
- Load Wheels: Used in material handling equipment like pallet jacks and forklifts, load wheels are designed to bear heavy weights while ensuring minimal wear and tear on surfaces.
- Guide Wheels: Employed in machinery to guide or align moving parts or materials. These wheels often require high precision and minimal friction to function effectively.
Material Choice and Its Impact on Price
The choice between stainless steel and regular steel in roller wheels significantly affects their suitability for various environments and, consequently, their price.
- Stainless Steel Roller Wheels: Known for their corrosion resistance, stainless steel wheels are ideal for environments prone to moisture or chemical exposure, such as food processing plants or outdoor applications. The durability and maintenance-free aspect of stainless steel make it a preferred choice despite its higher price point compared to regular steel.
- Regular Steel Roller Wheels: These wheels are typically less expensive than their stainless steel counterparts and are suitable for environments where corrosion is not a significant concern. Regular steel wheels can be coated or treated to enhance their resistance to rust and wear, though these treatments can add to the overall cost and require periodic maintenance.
The decision between stainless steel and regular steel roller wheels involves weighing the initial cost against the expected lifespan, maintenance requirements, and environmental suitability. Stainless steel roller wheels, while more expensive, offer long-term value in harsh or demanding conditions by minimizing the need for replacements and maintenance. In contrast, regular steel wheels represent a cost-effective solution for applications where environmental conditions are controlled or less severe.
The stainless steel roller price reflects not just the material’s inherent qualities but also its ability to meet the specific demands of various applications. When selecting steel roller wheels, understanding the implications of material choice on performance and cost is crucial for making informed decisions that align with operational needs and budget considerations.
The Value Behind Stainless Steel Roller Price with Bearings
The stainless steel roller price becomes particularly noteworthy when considering rollers equipped with bearings. This combination is crucial for applications demanding high durability, precision, and smooth operation. Stainless steel rollers with bearings bring added value to various industrial setups by enhancing performance and extending the equipment’s service life. This section explores the cost implications and the importance of these specialized rollers in applications where reliability and longevity are paramount.
Added Value and Cost Implications
Stainless steel rollers equipped with bearings offer several advantages that justify their price point, including:
- Reduced Friction: Bearings significantly lower the friction between the roller and the surface it moves upon, enhancing efficiency and reducing wear. This feature is critical in high-speed applications where excessive friction can lead to premature equipment failure.
- Enhanced Load Distribution: The inclusion of bearings allows for better distribution of loads across the roller, preventing deformation and ensuring consistent performance even under heavy weights. This capability is vital in material handling and manufacturing processes.
- Improved Precision: Bearings contribute to the precise movement and alignment of rollers, which is essential in applications requiring high levels of accuracy, such as in printing and packaging industries.
- Increased Durability: The combination of stainless steel and high-quality bearings offers exceptional resistance to corrosion and wear. This durability is crucial in harsh environments, such as those exposed to chemicals or moisture, where lesser materials might fail.
Importance in Applications Requiring Smooth Operations and Longevity
The integration of bearings into stainless steel rollers underscores their importance in numerous industrial applications:
- Conveyor Systems: In food processing and pharmaceuticals, where contamination must be minimized, stainless steel rollers with bearings ensure clean, smooth operations.
- Automated Assembly Lines: Precision and reliability are critical in automotive and electronics manufacturing. Rollers with bearings facilitate the smooth and accurate movement of components.
- Heavy Machinery: In construction and mining equipment, the robustness of stainless steel rollers with bearings supports the machinery’s weight and the rugged conditions it operates in.
- Aerospace and Aviation: The need for precision and durability in the handling and manufacturing of aerospace components makes stainless steel rollers with bearings an essential choice.
The stainless steel roller price, when bearings are included, reflects these components’ ability to significantly improve operational efficiency and longevity. While the initial cost might be higher compared to standard rollers, the long-term benefits of reduced maintenance, fewer replacements, and increased productivity make them a cost-effective solution for many industrial applications. Investing in stainless steel rollers with bearings is a strategic decision that prioritizes performance, durability, and overall value in the lifecycle of industrial machinery and equipment.
FAQs About Stainless Steel Roller Price
A stainless steel roller is a cylindrical component extensively utilized in various industrial applications, ranging from conveyor systems to machinery that requires smooth material handling. These rollers are crafted from stainless steel, a notable alloy recognized for its exceptional resistance to corrosion, heat, and chemical damage, making it an ideal choice for environments where these factors are a concern. Stainless steel rollers stand out for their durability and ability to maintain hygiene, critical in sectors like food processing, pharmaceuticals, and chemical manufacturing.
The design and functionality of stainless steel rollers cater to the need for reliable, long-lasting operation in demanding settings. They facilitate the smooth movement of goods and materials, minimizing friction and wear over time. The choice of stainless steel enhances the roller’s longevity, ensuring they can withstand rigorous cleaning processes without deteriorating. This resilience against harsh conditions not only prolongs the life of the rollers but also supports the operational efficiency and safety standards required in many industries.
Steel rollers are primarily constructed from various types of steel, each selected for its specific properties to meet diverse industrial requirements. The core materials include carbon steel, alloy steel, and stainless steel, tailored to the application’s environmental and mechanical demands.
Carbon Steel: A popular choice for its balance of durability, strength, and cost-effectiveness. Carbon steel rollers are suitable for applications where high strength is needed, but exposure to corrosive elements is minimal. They can be coated or treated for additional surface protection.
Alloy Steel: These rollers are made from steel mixed with other elements like chromium, nickel, or manganese to enhance specific properties such as hardness, toughness, and resistance to wear and corrosion. Alloy steel rollers are utilized in applications requiring additional durability and resistance to harsh conditions.
Stainless Steel: Valued for its exceptional corrosion resistance and hygiene, stainless steel is the material of choice for rollers in environments prone to chemical exposure, moisture, and the need for regular cleaning. Its composition includes chromium, which forms a passive layer of chromium oxide on the surface, protecting the roller from rust and deterioration.
Each type of steel offers unique benefits, with the selection depending on the operational requirements, including load capacity, speed, environmental conditions, and budget constraints. The manufacturing process, including forging, casting, or machining, further influences the roller’s characteristics, ensuring they meet the specific needs of various industrial applications.
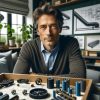
Jordan Smith, a seasoned professional with over 20 years of experience in the conveyor system industry. Jordan’s expertise lies in providing comprehensive solutions for conveyor rollers, belts, and accessories, catering to a wide range of industrial needs. From initial design and configuration to installation and meticulous troubleshooting, Jordan is adept at handling all aspects of conveyor system management. Whether you’re looking to upgrade your production line with efficient conveyor belts, require custom conveyor rollers for specific operations, or need expert advice on selecting the right conveyor accessories for your facility, Jordan is your reliable consultant. For any inquiries or assistance with conveyor system optimization, Jordan is available to share his wealth of knowledge and experience. Feel free to reach out at any time for professional guidance on all matters related to conveyor rollers, belts, and accessories.