Selecting Polyurethane Conveyor Rollers for Industries
In today’s diverse industrial landscape, conveyor rollers are indispensable for the seamless operation of manufacturing and processing lines. Their role in ensuring efficient product movement and handling across facilities is critical. Among the various materials used to manufacture these rollers, polyurethane stands out due to its remarkable properties. Polyurethane conveyor rollers offer enhanced durability and resistance, making them a preferred choice for businesses looking to optimize their operations. Their utility in reducing downtime and maintenance costs is a key driver of their increasing adoption in sectors ranging from mining to food processing.
Benefits of Polyurethane Conveyor Rollers
Polyurethane conveyor rollers are increasingly favored in modern industries due to their exceptional qualities and versatility. Here, we explore the myriad advantages they offer, which can significantly enhance industrial operations.
Durability and Performance
Polyurethane is renowned for its durability, making polyurethane conveyor rollers a robust choice for demanding environments. These rollers exhibit outstanding abrasion resistance, which prolongs their lifespan and minimizes the need for frequent replacements. Compared to rollers made from materials like rubber or metal, polyurethane stands out for its ability to withstand wear and tear, maintaining its integrity even under continuous operation. Below is a comparative table illustrating the longevity and performance of polyurethane against other common materials:
Material | Abrasion Resistance | Average Lifespan |
---|---|---|
Polyurethane | High | Up to 10 years |
Rubber | Medium | 3-5 years |
Metal | Low | 5-7 years |
Versatility in Applications
The use of polyurethane conveyor rollers spans a wide range of industries, underscoring their versatility. In mining, they are crucial for transporting raw extracted materials, which often involve rough and abrasive substances. In manufacturing settings, these rollers are essential for moving components along production lines with precision and care, preventing damage during handling. Additionally, in the food processing industry, polyurethane’s compliance with health and safety standards makes these rollers ideal for handling consumable goods. They do not degrade easily and resist contamination, ensuring safe contact with food products.
Additional Benefits
- Reduced Noise Levels: Polyurethane rollers operate more quietly compared to their metal counterparts, contributing to a more pleasant and compliant work environment.
- Shock Absorption: These rollers can absorb impacts, reducing the stress on the conveyor system and the goods being transported.
- Chemical Resistance: Polyurethane is resistant to many chemicals, making it suitable for industries where exposure to aggressive substances is common.
- Non-Marking: Unlike rubber rollers, polyurethane does not leave marks on the surfaces of transported goods, which is critical in industries like printing and paper manufacturing.
- Energy Efficiency: The smooth operation of polyurethane rollers reduces the energy needed to drive conveyor systems.
- Load Capacity: They can handle heavier loads without deformation, maintaining performance under pressure.
- Maintenance Ease: Polyurethane rollers require less maintenance due to their inherent resistance to wear and environmental factors.
- Customizability: Available in various hardness levels and sizes, these rollers can be customized to meet specific operational requirements.
- Cost-Effectiveness: While the initial cost may be higher, the long-term savings in maintenance and replacement expenses make polyurethane rollers a cost-effective solution.
- Weather Resistance: Effective in both hot and cold climates, resisting weather-related degradation.
- Hygienic Options: Specially formulated versions are available for stringent hygiene requirements in medical and food industries.
These benefits of pu conveyor roller illustrate why they are a superior choice for enhancing the efficiency and effectiveness of conveyor systems across various sectors.
Types of Polyurethane Conveyor Rollers
Polyurethane conveyor rollers are adaptable to a wide range of applications, thanks to their various designs and specifications. Understanding the different types available can help industries select the perfect roller for their specific needs.
Standard Polyurethane Rollers
Standard polyurethane rollers are the most common type used in various industries due to their general-purpose design. They typically feature a solid polyurethane coating over a metal core, which provides a balance of strength and flexibility. These rollers are used in applications ranging from light to medium load material handling, such as in packaging lines, assembly operations, and printing processes. Their resistance to abrasion and chemicals makes them particularly useful in environments where rollers are exposed to harsh substances or require frequent cleaning.
Heavy-Duty Rollers
Heavy-duty polyurethane rollers are engineered for environments where rollers must withstand exceptionally high loads and stress. These rollers often have a thicker polyurethane layer and a reinforced core to handle the demands of mining, metal processing, and heavy manufacturing. The durability and resilience of heavy-duty rollers ensure they can endure the rigors of moving large, heavy products without deforming or breaking, thereby minimizing downtime and maintenance costs.
Small Diameter Rollers
Small diameter polyurethane conveyor rollers are specifically designed for precision applications where space is limited and handling small or delicate items is essential. These rollers are commonly found in industries like electronics manufacturing, where they facilitate the gentle transport of sensitive components. The small diameter allows these rollers to make tight turns and handle smaller objects without causing damage, making them ideal for detailed assembly and sorting tasks.
Custom Conveyor Rollers
Custom conveyor rollers cater to specific operational requirements that standard rollers may not meet. Manufacturers offer custom designs where clients can specify everything from the roller’s diameter and length to the hardness of the polyurethane. This flexibility allows the rollers to be perfectly suited to unique applications, such as food processing lines that require non-standard sizes or special health compliance, or in environments with unusual temperature extremes where standard rollers might fail.
By offering these diverse types of urethane conveyor rollers, manufacturers ensure that there is a roller option available for virtually any industrial scenario. This variety not only helps in optimizing the conveyor system’s performance but also enhances overall operational efficiency and safety.
Features of Polyurethane Conveyor Rollers
Polyurethane conveyor rollers are designed to meet the high demands of modern industrial operations. Their construction incorporates several key features that contribute to their performance and versatility.
With Bearings
One of the crucial enhancements in polyurethane conveyor rollers is the inclusion of bearings. Bearings play a pivotal role in enabling smoother operations, reducing friction and wear during use. Polyurethane rollers equipped with high-quality bearings can handle higher speeds and longer operational periods without significant degradation. This feature is especially beneficial in applications such as distribution centers and assembly lines, where rollers need to perform reliably under continuous use.
Load Capacity
The load capacity of polyurethane conveyor rollers varies depending on their design and size. Rollers designed to handle heavy loads are constructed with a thicker polyurethane layer and stronger core materials. Below is a table that displays the typical load capacities for different types of polyurethane rollers:
Roller Type | Maximum Load Capacity |
---|---|
Standard Rollers | Up to 200 lbs |
Heavy-Duty Rollers | 500 lbs and above |
Small Diameter Rollers | Up to 100 lbs |
Custom Rollers | Varies by specification |
Chemical Resistance
Polyurethane is highly resistant to many chemicals, oils, and solvents, which makes these rollers suitable for harsh environments where exposure to such substances is common.
Non-Marking
A significant advantage of polyurethane rollers is that they do not mark surfaces. This is crucial in industries like printing and paper handling, where maintaining the integrity of materials is essential.
Customizability
Polyurethane rollers can be customized in terms of hardness, size, and even color, according to specific industry needs. This allows for a precise match with the operational requirements, enhancing efficiency and reducing the risk of equipment mismatch.
These features make polyurethane conveyor rollers a highly adaptable and efficient choice for a wide range of industrial applications, supporting not only the current needs but also the evolving demands of various sectors.
Purchasing and Replacement of Polyurethane Conveyor Rollers
Ensuring the efficient operation of your conveyor systems involves timely maintenance and knowing where to find quality replacements for polyurethane conveyor roller. This section delves into practical tips for purchasing new rollers and guidelines for replacing them.
Finding Polyurethane Conveyor Rollers
Identifying reliable sources for polyurethane conveyor rollers are crucial for maintaining optimal performance. Here are 8 tips for where to find quality rollers, including specific suppliers and platforms:
Direct from Manufacturers: Companies like Urethane Innovators, Inc. and Sunray, Inc. specialize in producing high-quality polyurethane rollers and often provide customization options.
Industrial Supply Companies: Global industrial equipment suppliers like McMaster-Carr and Grainger offer a wide range of conveyor rollers, including polyurethane options, with extensive product descriptions and customer service.
Online Marketplaces: Amazon Business and eBay are good sources for both new and used rollers, providing customer reviews and competitive pricing.
Specialty Conveyor Stores: Conveyor Roller Plus and Ultimation Industries focus specifically on conveyor components and can offer expert advice along with their products.
Local Industrial Suppliers: Check local industrial hardware stores which may have quick delivery options and the possibility to inspect the products in person.
Trade Shows and Industrial Fairs: Events like the International Manufacturing Technology Show (IMTS) allow direct interaction with manufacturers and firsthand comparison of products.
Referral and Industry Contacts: Networking within industry forums and trade associations can lead to recommendations for reputable suppliers.
Used and Surplus Equipment Dealers: For cost-effective solutions, companies like Surplus Industrial Supply often stock used or surplus rollers that are still in good condition.
For Sale and For Sale Near Me
When searching for polyurethane conveyor rollers for sale, consider these 12 pieces of advice to ensure you get the best value:
Define Your Requirements: Clearly understand the specifications needed for your conveyor system to ensure compatibility.
Compare Prices Online: Use tools like Google Shopping to compare prices from multiple suppliers.
Check Supplier Credibility: Look for suppliers with high ratings and positive customer feedback.
Consider Custom Orders: If standard sizes don’t fit, custom-made rollers might be necessary.
Negotiate Bulk Deals: If ordering in large quantities, negotiate for bulk pricing.
Check for Return Policy: Ensure there’s a solid return policy in case the products don’t meet expectations.
Look for Warranty: Prefer rollers that come with a manufacturer’s warranty.
Assess After-Sales Support: Good customer service can be invaluable for future maintenance or issues.
Investigate Lead Times: Understand how long it will take for the rollers to be delivered.
Inspect Used Rollers: If buying used, inspect for any wear and tear or operational defects.
Seasonal Discounts and Sales: Keep an eye out for sales during off-peak times or end of fiscal periods.
Local vs. Imported: Consider whether local suppliers or international orders offer better value for your specific needs.
Replacement Rollers for Conveyors
Proper maintenance includes knowing when and how to replace polyurethane conveyor rollers to prevent downtime. Here are some guidelines:
- Regular Inspections: Implement a schedule for regular inspections to monitor the condition of rollers.
- Identify Wear and Tear: Replace rollers showing signs of significant wear, such as cracks, flattening, or reduced flexibility.
- Follow Manufacturers’ Recommendations: Adhere to the usage and replacement guidelines provided by the roller manufacturer.
- Keep Spares on Hand: Maintain a stock of spare rollers to allow quick replacements when necessary.
- Training: Ensure maintenance personnel are trained on how to identify and replace worn rollers efficiently.
Manufacturers and Customization of Polyurethane Conveyor Rollers
Selecting the right manufacturer and understanding the customization options available are crucial steps in optimizing your conveyor system with polyurethane conveyor rollers. This section details leading manufacturers and highlights the extensive customization possibilities that can tailor rollers to specific operational needs.
Conveyor Rollers Manufacturers
The market boasts several leading manufacturers known for their quality and innovation in producing polyurethane conveyor rollers.
Manufacturer | Specialization | Notable Features |
---|---|---|
Gram Conveyor | Comprehensive conveyor solutions | Custom engineering and robust support services |
Urethane Innovators | High-performance polyurethane products | Custom formulations for unique applications |
Superior Rollers | Eco-friendly production processes | Uses renewable materials in roller production |
Precision Pulley & Idler | Precision conveyor components | Advanced design and precision in every product |
Rollex Group | European market leader | High-quality standards and extensive range |
Sunray, Inc. | Quick turnaround customization | Specializes in rapid delivery of custom orders |
These manufacturers stand out due to their commitment to quality, customer service, and innovative solutions. Whether you’re looking for standard products or specialized components, these companies offer reliable and effective solutions tailored to a broad range of industrial needs.
Customization Options
Customization is a key advantage when selecting polyurethane conveyor rollers, as it allows rollers to be specifically tailored to meet the precise requirements of different conveyor systems. Here’s how businesses can approach customization:
- Determine Specifications: Start by determining the necessary specifications such as diameter, length, load capacity, and hardness based on your conveyor’s requirements.
- Consultation with Manufacturers: Engage with manufacturers to discuss your needs. Most manufacturers like those listed above offer consultation services to help identify the best configurations for your system.
- Select Material and Hardness: Choose the polyurethane material and hardness that best suit your application, considering factors like environment, load, and speed.
- Request Prototypes: Some manufacturers offer prototypes to test in your system before committing to a large order.
- Custom Colors and Markings: Manufacturers can often provide rollers in custom colors or with markings for identification or aesthetic purposes.
- Additional Features: Consider additional features like anti-static properties, temperature resistance, or reinforced cores for enhanced performance.
- Lead Time and Pricing: Discuss lead times and pricing for custom orders to ensure they meet your project timelines and budget.
By leveraging these customization options, businesses can enhance the functionality and efficiency of their conveyor systems, ensuring that the polyurethane conveyor rollers perfectly align with their operational needs and environmental conditions. This section highlights the importance of working closely with manufacturers to fully utilize the potential of custom solutions in conveyor technology.
FAQs about Polyurethane Conveyor Rollers
When using polyurethane, it’s important to select rollers that complement its properties to maximize the efficiency and lifespan of the conveyor system. Rollers designed specifically for use with polyurethane are typically made from steel or aluminum cores coated with a polyurethane layer. The choice between these materials often depends on the specific needs of the application, such as load capacity, speed of operation, and environmental factors like exposure to chemicals or temperature extremes. Steel rollers with polyurethane coating are commonly used due to their strength and durability, making them suitable for heavy-duty applications. Aluminum rollers, on the other hand, are lighter and can be used where weight reduction is crucial, though they may not handle heavier loads as effectively.
PU coating, or polyurethane coating, on rollers refers to a layer of polyurethane elastomer that is applied to the surface of a roller, typically over a metal core. This coating is engineered to provide a protective barrier against wear, abrasion, and corrosion, thereby extending the roller’s operational life. The thickness and type of PU coating can be varied according to the needs of the application, allowing for customization in terms of hardness, elasticity, and resistance properties. PU-coated rollers are particularly beneficial in applications that involve the handling of delicate materials, as the soft surface reduces the risk of damaging the goods. Moreover, the PU coating enhances the grip and traction of the rollers, ensuring efficient movement of items across the conveyor system.
The type of roller to use for a conveyor belt depends on the application’s specific requirements, including the weight of materials being transported, the operating environment, and the desired speed of the conveyor. For general use, steel rollers are commonly employed due to their strength and durability, suitable for heavy loads and high-speed operations. However, for applications where noise reduction is important or non-marking is required, polyurethane-coated rollers are preferred. They offer quieter operation and prevent damage to sensitive materials. In environments where corrosion resistance is needed, such as in chemical processing or outdoor settings, stainless steel or plastic rollers might be used. Additionally, for precise control and positioning of goods, motor-driven rollers (MDRs) provide an effective solution, allowing for speed and directional adjustments on the conveyor belt.
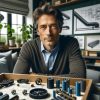
Jordan Smith, a seasoned professional with over 20 years of experience in the conveyor system industry. Jordan’s expertise lies in providing comprehensive solutions for conveyor rollers, belts, and accessories, catering to a wide range of industrial needs. From initial design and configuration to installation and meticulous troubleshooting, Jordan is adept at handling all aspects of conveyor system management. Whether you’re looking to upgrade your production line with efficient conveyor belts, require custom conveyor rollers for specific operations, or need expert advice on selecting the right conveyor accessories for your facility, Jordan is your reliable consultant. For any inquiries or assistance with conveyor system optimization, Jordan is available to share his wealth of knowledge and experience. Feel free to reach out at any time for professional guidance on all matters related to conveyor rollers, belts, and accessories.