V Shaped Roller Conveyor: Industry Applications
Roller conveyors are essential tools in modern manufacturing and distribution, facilitating the smooth and efficient movement of goods across numerous industries. Among these, the v shaped roller conveyor stands out for its design, which is tailored to handle materials that require precise alignment during transport. This type of conveyor is particularly valued in sectors where stability and accuracy are critical, such as in assembly lines and packaging facilities. It leverages the unique V-shaped configuration to guide materials securely, reducing the risk of misalignment and enhancing overall workflow efficiency.V shaped roller conveyors transport heavy materials with stability, reducing side movement, ideal for loading and unloading applications.
What Is V Shaped Roller Conveyor
The v shaped roller conveyor is a specialized conveyor system meticulously engineered to enhance the handling and transport of cylindrical or rounded objects. This system is pivotal in industries where stability and precision are crucial, such as in material processing or assembly lines where cylindrical materials like pipes and rolls are predominant. Its design maximizes efficiency by reducing material slippage and ensuring proper alignment throughout the transport process. By diving deeper into the structure and function of this conveyor type, we can appreciate its impact on industrial operations, boosting productivity and minimizing operational hiccups.
Design Features of the V-Shaped Roller Conveyor
Before delving into the specific design elements, it’s essential to understand that the v shaped roller conveyor is crafted to offer unmatched reliability and precision. This conveyor’s architectural integrity stems from its innovative features, which cater specifically to the unique demands of handling round materials.
- Robust Construction: Made primarily of heavy-duty metals like steel, ensuring longevity and resilience under industrial conditions.
- Customizable Groove Widths: Features adjustable groove settings to handle various diameters, enhancing its versatility.
- Dense Roller Placement: Rollers are strategically placed close together to provide continuous support and reduce the risk of material sagging or falling.
- Enhanced Load Capacity: Engineered to support heavy loads, making it suitable for industrial applications without compromising performance.
- Scalable and Modular: Fits seamlessly into larger systems, offering easy scalability and flexibility in design.
- Precision Bearings: Incorporates high-quality bearings that facilitate smoother roller operations and decrease maintenance frequency.
- Impact and Wear Resistance: Designed to withstand the harsh environments of industrial settings, including resistance to impacts and continuous wear.
- Accessible Maintenance Points: Strategically placed access points simplify maintenance routines, promoting longevity and consistent performance.
- Advanced Material Handling: Tailored specifically to manage the challenges associated with cylindrical objects, ensuring safety and efficiency.
Operational Mechanics of the V-Shaped Roller Conveyor
Understanding the operational dynamics of the v shaped roller conveyor reveals why it is such a valuable asset in specific sectors. The operational mechanics focus on enhancing throughput while ensuring the integrity of handled materials.
- Material Alignment: The V-shaped groove precisely aligns materials, preventing shifts and ensuring consistent movement.
- Utilization of Gravity: Employs gravity where possible to facilitate movement, reducing the need for additional power.
- Low-Friction Design: Minimizes resistance during operation, which helps in maintaining the speed and efficiency of the conveyor.
- Speed Control Capabilities: Allows for the adjustment of operational speeds to sync with varying production demands.
- Seamless Automation Integration: Designed to integrate easily with modern automated systems for improved control and monitoring.
- Comprehensive Safety Features: Includes numerous safety measures to protect both the operation process and the workforce.
- Energy Efficient Operations: Built to operate with minimal energy, reducing operational costs and environmental impact.
- Even Load Distribution: Ensures that loads are evenly distributed along the conveyor, which prevents wear and extends the conveyor’s life.
- Flexible Application Use: While it’s specialized, adjustments and modifications allow it to handle various other types of items efficiently.
By elaborating on these points, we can see how the v shaped roller conveyor not only meets but often exceeds the requirements of industries reliant on precise and stable material handling.
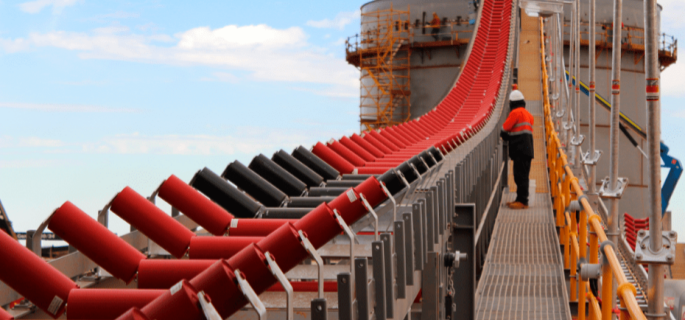
To Explore Types of V Shaped Roller Conveyor
Roller conveyors are integral to material handling systems, and their types vary based on the needs of different industries. Among them, the v shaped roller conveyor is distinct due to its unique design that optimizes material handling for specific shapes and sizes. Here, we focus on several types of roller conveyors and provide a detailed comparison between the v shaped roller conveyor and traditional belt conveyors.
Different Types of Roller Conveyors
Roller conveyors are versatile components used in various industries to facilitate the transportation and handling of goods. They come in different types based on their design and utility, ensuring that there is a suitable conveyor for almost any material handling need. Among the numerous varieties, here’s an in-depth look at several common types, highlighting the unique v shaped roller conveyor for its specialized applications.
- Gravity Roller Conveyors: These conveyors use the natural force of gravity to move items, making them energy-efficient and cost-effective. They are ideal for items with sufficient weight to overcome inertia and friction, often used in warehouses and assembly lines.
- Powered Roller Conveyors: Equipped with motors, these conveyors can handle heavier loads and control the speed at which items move, offering precise control over material handling processes. They are commonly used in automotive and packaging industries.
- Flexible Roller Conveyors: Known for their adjustability, these conveyors can be expanded, curved, or contracted to fit various spaces and routes. They are perfect for loading docks and retail backrooms where space and layout flexibility are key.
- Accumulation Roller Conveyors: Designed to allow products to accumulate with minimal pressure, preventing damage during halts in the production line. These systems are essential in applications where products need to be queued for processing.
- Chain-Driven Roller Conveyors: These are robust and suitable for heavy loads, as the rollers are powered by a chain link across the width of the conveyor. They are most beneficial in heavy manufacturing and automotive industries where durability is crucial.
- Lineshaft Roller Conveyors: Utilizing a shaft beneath the rollers to drive them, these conveyors are best for lightweight products and applications where quiet operation is necessary. They are often used in food processing and pharmaceutical industries.
- V Shaped Roller Conveyor: Specifically engineered with a V-shaped groove, this conveyor excels in handling cylindrical or rounded objects by stabilizing and guiding them efficiently. It’s particularly useful in industries like manufacturing and materials handling where precise movement of such items is crucial.
Each type of roller conveyor has its unique set of benefits tailored to specific industrial needs, making them indispensable in modern manufacturing and logistics operations. The v shaped roller conveyor, in particular, offers specialized advantages for handling cylindrical materials that are not typically feasible with flat conveyors.
Request a quote for our durable conveyor rollers here!
Comparison of V Shaped Roller Conveyor with Belt Conveyors
Feature | V Shaped Roller Conveyor | Belt Conveyor |
---|---|---|
Material Handling | Excellent for cylindrical objects due to the V-groove that aligns and stabilizes | Best for a wide variety of flat-bottomed goods |
Efficiency | High efficiency in specific applications like handling pipes or round materials | Generally efficient for bulk and diverse items |
Application Specificity | Ideal for industries where rolling or cylindrical shapes are common | Versatile use across many industries without specific shape requirements |
Maintenance | Requires regular inspection of rollers and alignment | Needs monitoring for belt wear and tear, alignment |
This outline not only introduces the types of roller conveyors, focusing specifically on the v shaped roller conveyor, but also compares these with traditional belt conveyors, providing a clear perspective on their advantages and suitability for different applications.
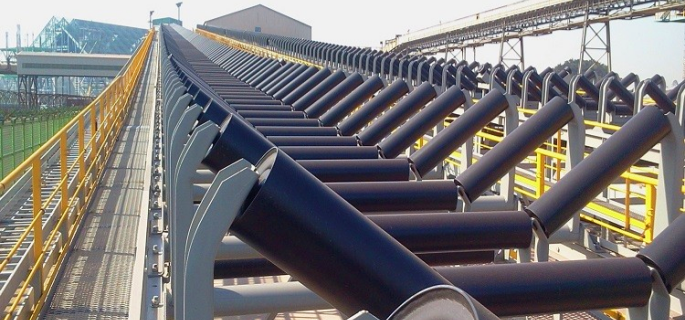
Carbon Steel V Shaped Roller Conveyor
A carbon steel V-shaped roller conveyor is a robust and efficient material handling system designed to transport items securely and reliably. Constructed from high-quality carbon steel, this conveyor is built to withstand heavy loads and harsh industrial environments.
Key Features:
- Durable Construction: The use of carbon steel ensures excellent strength and durability, making the conveyor suitable for handling a wide range of materials, including heavy and abrasive items.
- V-Shaped Rollers: The V-shaped design of the rollers helps to stabilize cylindrical or irregularly shaped items, preventing them from rolling off or becoming misaligned during transport. This feature is particularly beneficial for transporting pipes, rods, or similar items.
- Smooth Transport: The rollers facilitate smooth and consistent movement of materials along the conveyor path, reducing friction and minimizing the risk of damage to the items being conveyed.
- Versatility: This type of conveyor is highly versatile and can be used in various industries, including manufacturing, mining, automotive, and construction. It is ideal for applications where maintaining the orientation and stability of items is crucial.
- Customizable Design: Carbon steel V-shaped roller conveyors can be customized to meet specific operational requirements, including adjustable roller spacing, conveyor length, and height. Additional features like side guards or supports can also be added.
- Low Maintenance: The sturdy construction and quality materials used in these conveyors result in low maintenance requirements, reducing downtime and operational costs.
- Corrosion Resistance: While carbon steel is strong, it can be coated or treated to improve its resistance to corrosion, making the conveyor suitable for both indoor and outdoor use.
- Cost-Effective: Due to the durability and low maintenance needs, carbon steel V-shaped roller conveyors offer a cost-effective solution for long-term material handling needs.
Applications:
- Manufacturing Plants: Efficiently move raw materials and finished products.
- Mining Operations: Transport ores and other mined materials.
- Automotive Industry: Handle parts and components with care.
- Construction Sites: Move building materials like pipes and rods securely.
In summary, a carbon steel V-shaped roller conveyor is an essential component in various industrial operations, providing a reliable, efficient, and durable solution for transporting materials while ensuring their stability and alignment.
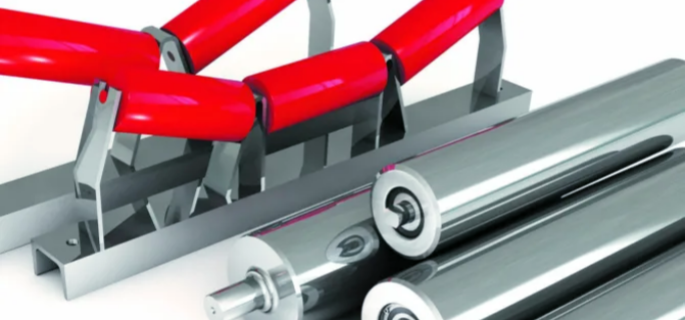
Benefits of Using V Shaped Roller Conveyor
The v shaped roller conveyor system offers a multitude of advantages specifically designed to improve handling efficiency and product safety in various industries. Here we outline the key benefits of integrating this type of conveyor into an operational setting.
- Reduced Material Misalignment: The V-shaped design ensures that cylindrical materials remain aligned and centered during movement.
- Enhanced Stability for Round Objects: The unique groove provides a natural cradle for rounded items, significantly enhancing stability.
- Increased Durability: Constructed from robust materials such as carbon steel, these conveyors withstand harsh industrial environments.
- Improved Product Safety: The design minimizes the risk of materials falling off the conveyor, reducing potential damage.
- Efficient Handling of Cylindrical Materials: Specifically engineered for cylindrical objects, ensuring optimal handling without the need for additional equipment.
- Low Maintenance Requirements: The simplicity of the design and the quality of the materials reduce the need for frequent maintenance.
- Energy Efficiency: Many models are designed to use gravity or minimal power, leading to lower energy consumption.
- Customizable Configurations: Can be tailored to specific industry needs, including adjustable widths and lengths.
- Seamless Integration: Easily integrates into existing conveyor systems without extensive modifications.
- Cost-Effective Operations: By reducing material damage and improving efficiency, these conveyors can lead to significant cost savings over time.
Each benefit of the v shaped roller conveyor highlights its capacity to meet specific industrial needs, making it a valuable asset for businesses that require precise and reliable handling of cylindrical or round objects.
Application of V Shaped Roller Conveyor
A V-shaped roller conveyor is a specialized type of material handling equipment designed to transport items securely, especially those that are cylindrical or have irregular shapes. Here are some detailed applications of V-shaped roller conveyors:
Manufacturing Industry
- Pipe and Tube Handling: Ideal for transporting pipes, tubes, and cylindrical objects, ensuring they remain aligned and stable during movement.
- Assembly Lines: Used to move components between different stages of assembly, particularly where orientation and stability are crucial.
Mining Industry
- Ore Transport: Efficiently moves mined materials such as ore, rocks, and minerals, ensuring they do not roll off the conveyor.
- Drill Rods: Handling and transporting drill rods and other cylindrical mining equipment.
Automotive Industry
- Parts Conveyance: Transporting automotive parts like drive shafts, axles, and other elongated components.
- Assembly Processes: Moving components through various stages of assembly while maintaining proper orientation.
Construction Industry
- Building Materials: Transporting construction materials such as metal rods, rebar, and pipes safely and securely.
- Pre-fabricated Components: Moving pre-fabricated construction elements within manufacturing facilities or on construction sites.
Logistics and Warehousing
- Storage and Retrieval: Facilitating the efficient storage and retrieval of cylindrical items in warehouses.
- Order Fulfillment: Enhancing the picking and packing processes by moving products efficiently through fulfillment centers.
Food and Beverage Industry
- Bottling Operations: Transporting bottles, cans, and other cylindrical containers through various stages of the bottling process.
- Ingredient Handling: Moving cylindrical or tubular containers of ingredients in food processing facilities.
Textile Industry
- Rolls of Fabric: Transporting rolls of fabric, carpet, and other textile materials securely, ensuring they do not unroll or become misaligned.
Aerospace Industry
- Component Transport: Moving elongated aerospace components such as struts and shafts within manufacturing and assembly facilities.
- Tool Handling: Efficiently handling and transporting specialized tools and equipment used in aerospace manufacturing.
Pharmaceutical Industry
- Container Handling: Transporting cylindrical containers, vials, and tubes through various stages of the production and packaging process.
- Production Lines: Enhancing the efficiency and safety of production lines dealing with fragile or precisely oriented items.
Energy Sector
- Wind Turbine Components: Handling and transporting long, cylindrical components such as turbine blades and towers.
- Pipeline Construction: Moving sections of pipelines and related equipment during assembly and installation processes.
V-shaped roller conveyors are versatile and essential in various industries for transporting cylindrical and irregularly shaped items securely and efficiently, improving overall operational effectiveness and safety.
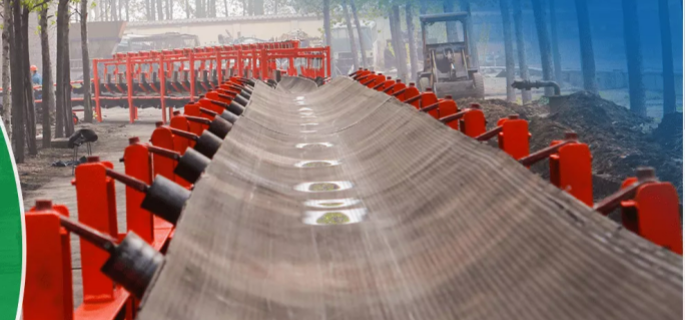
Maintain of V Shaped Roller Conveyor
Maintaining a V-shaped roller conveyor is crucial to ensure its longevity, performance, and safety. Here are the key maintenance practices to keep your V-shaped roller conveyor in optimal condition:
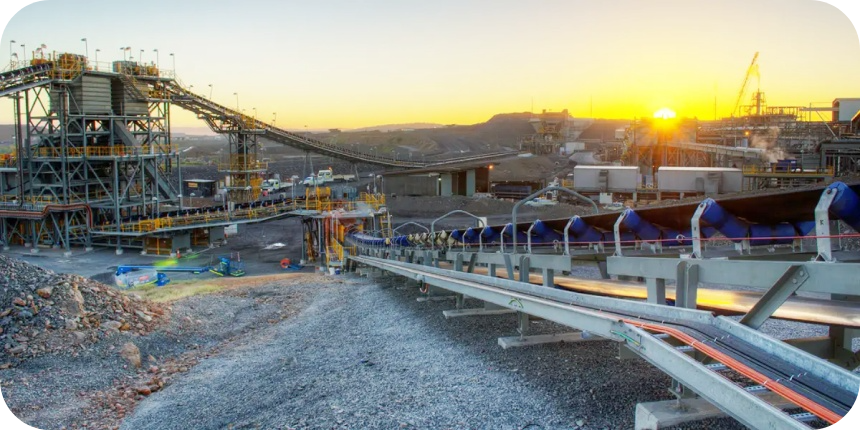
Regular Inspection
- Visual Checks: Perform regular visual inspections to detect any signs of wear, damage, or misalignment of the rollers and frame.
- Check for Debris: Ensure that there is no accumulation of debris or materials on the conveyor that could interfere with its operation.
Lubrication
- Roller Bearings: Lubricate the roller bearings periodically according to the manufacturer’s recommendations to ensure smooth operation.
- Moving Parts: Apply lubricant to all moving parts to reduce friction and prevent wear.
Alignment
- Roller Alignment: Ensure that all rollers are properly aligned to prevent uneven wear and ensure smooth material flow.
- Frame Alignment: Check and correct the alignment of the conveyor frame to prevent misalignment issues.
Cleaning
- Regular Cleaning: Keep the conveyor and surrounding area clean to prevent the buildup of dust, dirt, and materials that could hinder performance.
- Remove Debris: Regularly remove any debris or material buildup from the V-shaped rollers and the conveyor bed.
Component Inspection and Replacement
- Rollers: Inspect rollers for wear, cracks, or damage and replace them if necessary.
- Bearings: Check the condition of bearings and replace them if they show signs of wear or damage.
- Belt and Chains: Inspect any belts or chains used in the conveyor system for wear and replace them as needed.
Tension Adjustment
- Belt Tension: If the conveyor uses a belt, ensure that the tension is properly adjusted to prevent slippage or excessive wear.
- Chain Tension: For chain-driven conveyors, check and adjust the chain tension to ensure smooth operation.
Safety Checks
- Safety Guards: Ensure that all safety guards are in place and secure to prevent accidents.
- Emergency Stops: Test emergency stop mechanisms regularly to ensure they are functioning correctly.
Preventive Maintenance Schedule
- Create a Schedule: Develop a preventive maintenance schedule based on the manufacturer’s recommendations and the conveyor’s usage.
- Record Keeping: Maintain detailed records of all maintenance activities, inspections, and repairs. This helps in identifying patterns and planning future maintenance.
Training
- Train Personnel: Ensure that maintenance personnel are properly trained in the correct procedures for inspecting, cleaning, lubricating, and adjusting the conveyor.
- Operational Training: Train operators on proper use and daily checks to catch issues early.
Monitoring Wear Patterns
- Identify Issues: Regularly monitor wear patterns on rollers and other components to identify potential issues early.
- Address Causes: Investigate and address the root causes of abnormal wear to prevent recurring problems.
Spare Parts Inventory
- Stock Critical Parts: Keep an inventory of critical spare parts like rollers, bearings, and belts to minimize downtime during repairs.
- Quick Access: Ensure that spare parts are readily accessible to maintenance personnel.
Benefits of Proper Maintenance
- Extended Lifespan: Proper maintenance extends the life of the conveyor system, reducing the need for costly replacements.
- Reduced Downtime: Regular maintenance prevents unexpected breakdowns, ensuring continuous operation and productivity.
- Improved Safety: Well-maintained conveyors are safer to operate, reducing the risk of accidents and injuries.
- Cost Savings: Preventive maintenance reduces repair costs and downtime, leading to overall cost savings.
By adhering to these maintenance practices, you can ensure that your V-shaped roller conveyor operates efficiently, safely, and reliably, minimizing downtime and extending its service life.
FAQs about V Shaped Roller Conveyor
Conveyor rollers come in various types, each designed to fulfill specific industrial requirements and applications. The main types include gravity rollers, which use the force of gravity to move items and are often used in manual loading tasks; powered rollers, which are driven by motors and are used in automated systems for consistent and controlled movement; and grooved rollers, which have grooves that can drive belts for additional traction. Other specialized types include impact rollers, designed to absorb shock and reduce damage to the conveyor belt at loading points; and plastic rollers, which are used in environments where corrosion and sanitation are concerns.
A crowned roller is a type of roller that has a slightly larger diameter in the middle than at the ends. This design helps to maintain the positioning and tracking of conveyor belts, ensuring they stay centered during operations. Crowning is a common technique used in belt conveyors to handle slight misalignments and side forces, reducing the risk of the belt slipping off the rollers. Crowned rollers are particularly useful in applications where the conveyor path has curves or where the belt environment may cause lateral movement.
The main difference between a drive roller and a driven roller lies in their roles within a conveyor system. A drive roller is motorized and provides the necessary power to move the conveyor belt or rollers. This roller is the primary force driver in conveyor systems. On the other hand, a driven roller is not motorized; instead, it is moved by the belt or by other rollers. Driven rollers serve to guide, support, and shape the belt but do not contribute to its motive power. The configuration of drive and driven rollers can significantly affect the efficiency and functionality of a conveyor system.
While roller conveyors are advantageous for many reasons, they also have several disadvantages. They can be limited in the types of materials they can handle effectively, especially if those materials are small or have irregular bottoms that do not interact well with rollers. Roller conveyors typically require a flat bottom surface for smooth operation. They can also generate significant noise, particularly in extensive systems or when handling heavy or rough materials. Furthermore, roller conveyors may require frequent maintenance to keep the rollers and bearings in good working order, and they are not always suitable for high-speed or precision applications.
Conveyor belts come in various shapes tailored to specific applications. The most common is the flat belt, used for transporting items in manufacturing and warehousing. V-shaped belts stabilize cylindrical objects, ideal for pipes and tubes. Cleated belts, with raised sections, handle loose materials on inclines. Modular belts, made of interlocking plastic, navigate complex paths in the food and automotive industries. Curved belts manage turns in distribution centers. Inclined and declined belts move materials between different elevations. Trough belts carry bulk items like coal and grains. Sidewall belts prevent spillage on steep inclines. Chevron belts transport loose materials without slipping. Roller top belts, featuring embedded rollers, facilitate sorting and merging in packaging. Each shape enhances the efficiency and safety of material handling across diverse industries.
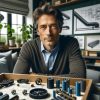
Jordan Smith, a seasoned professional with over 20 years of experience in the conveyor system industry. Jordan’s expertise lies in providing comprehensive solutions for conveyor rollers, belts, and accessories, catering to a wide range of industrial needs. From initial design and configuration to installation and meticulous troubleshooting, Jordan is adept at handling all aspects of conveyor system management. Whether you’re looking to upgrade your production line with efficient conveyor belts, require custom conveyor rollers for specific operations, or need expert advice on selecting the right conveyor accessories for your facility, Jordan is your reliable consultant. For any inquiries or assistance with conveyor system optimization, Jordan is available to share his wealth of knowledge and experience. Feel free to reach out at any time for professional guidance on all matters related to conveyor rollers, belts, and accessories.