The Role of Garland Impact Rollers
The evolution of conveyor technology has been pivotal in advancing industrial material handling, streamlining the transportation of bulk materials across various sectors, including mining, agriculture, and manufacturing. At the heart of these conveyor systems are idlers, which play a crucial role in supporting the conveyor belt and the materials it carries. Among the innovations in this field, the introduction of garland impact roller marks a significant advancement. These specialized rollers are designed to enhance conveyor performance and durability, particularly in applications where the conveyor belt is subjected to high impact forces, such as loading zones. Garland impact rollers consist of a series of closely spaced rollers mounted on a flexible chain or wire rope, allowing them to flex and absorb the impact of heavy materials more effectively than traditional idlers. This flexibility not only reduces the wear and tear on the conveyor belt but also distributes the load more evenly across the roller, improving the overall efficiency and lifespan of the conveyor system.
Understanding Garland Impact Rollers
Garland impact rollers are an innovative solution in the field of material handling, specifically designed to enhance the efficiency and longevity of conveyor systems. These rollers stand out from traditional conveyor rollers due to their unique design and functionality, which are tailored to address the challenges of handling materials with high impact and varying loads. Below, we delve into the specifics of what makes garland impact rollers distinct and superior in certain applications compared to traditional conveyor rollers.
Comparison Table: Garland Impact Rollers vs. Traditional Conveyor Rollers
Feature | Garland Impact Roller | Traditional Conveyor Roller |
---|---|---|
Design | Consists of a series of rollers connected in a flexible configuration | Typically a single, rigid roller |
Impact Absorption | High, due to the flexibility and multiple points of contact | Lower, as impact is distributed over a single, rigid surface |
Flexibility | Can adjust to varying loads and sizes of materials | Less adaptable to changes in load size and weight |
Durability | Enhanced, due to the ability to absorb impacts better | Can be compromised with heavy or sharp materials |
Application | Ideal for high-impact areas, such as loading zones | Suited for low-impact, uniform load applications |
Design and Functionality
The design of the garland impact roller is what sets it apart from its traditional counterparts. This design incorporates a series of rollers linked together in a garland-like configuration, allowing for a level of flexibility and adaptability not seen in standard conveyor rollers. This flexibility is crucial in absorbing the impact of materials as they are loaded onto the conveyor, distributing the force across multiple rollers and reducing the stress on any single point.
The functionality of garland impact rollers is centered around their ability to handle high-impact situations with ease. The unique design allows these rollers to adjust to the size and weight of varying loads, providing consistent support and reducing the likelihood of damage to both the conveyor system and the materials being transported. This adaptability not only enhances the efficiency of material handling operations but also significantly extends the lifespan of the conveyor system by mitigating wear and tear.
Furthermore, the garland impact roller’s design facilitates easier maintenance and replacement. In the event of wear or damage, individual rollers within the garland can be replaced without the need to dismantle the entire system, thereby reducing downtime and maintenance costs.
Garland impact rollers offer a robust and flexible solution for handling materials in high-impact environments. Their innovative design and superior impact absorption capabilities make them a valuable addition to any material handling operation, providing benefits that traditional conveyor rollers cannot match.
Benefits of Using Garland Impact Rollers
Garland impact rollers represent a significant advancement in conveyor technology, offering a range of benefits that enhance the efficiency and durability of conveyor systems. These rollers are designed to provide superior belt support, reduce wear and tear on the conveyor belt, and improve the overall material handling process. Below, we explore the key benefits of using garland impact rollers, supported by case studies that demonstrate their effectiveness in various industrial settings.
Key Benefits
Benefit | Description |
---|---|
Improved Belt Support | Garland impact rollers offer a flexible support system that conforms to the belt's shape, distributing weight and impact forces more evenly across the belt surface. This reduces stress and deformation, leading to smoother operation. |
Reduced Belt Wear | The enhanced support provided by garland impact rollers minimizes direct impact and friction on the conveyor belt, significantly reducing wear and extending the belt's lifespan. |
Increased Material Handling Efficiency | With better belt support and reduced wear, garland impact rollers contribute to a more efficient material handling process. They ensure that the conveyor system operates smoothly, with fewer interruptions for maintenance and repairs. |
Adaptability to Various Conditions | Garland impact rollers are designed to perform in a wide range of environmental conditions, including extreme temperatures and high levels of dust and moisture, making them suitable for diverse industrial applications. |
Ease of Maintenance | The design of garland impact rollers allows for easy replacement and maintenance, reducing downtime and operational costs. |
Case Studies
- Mining Industry Application: In a large mining operation, the introduction of garland impact rollers led to a noticeable reduction in conveyor belt damage caused by the heavy and abrasive materials being transported. The improved belt support and reduced wear resulted in a 20% increase in the belt’s service life, significantly lowering replacement costs and downtime.
- Bulk Material Handling Facility: A bulk material handling facility reported enhanced operational efficiency after replacing traditional idlers with garland impact rollers. The facility experienced a smoother material flow, with a marked decrease in instances of belt misalignment and slippage. This led to a more reliable material handling process, with reduced maintenance requirements.
- Agricultural Products Manufacturer: An agricultural products manufacturer observed an improvement in conveyor performance in their processing plant after implementing garland impact rollers. The rollers’ ability to adapt to varying loads and conditions without compromising belt integrity was particularly beneficial, ensuring uninterrupted operation during peak harvest periods.
Garland impact rollers offer a range of benefits that significantly enhance the performance and durability of conveyor systems. Their ability to provide improved belt support, reduce wear, and increase efficiency makes them a valuable addition to various industrial applications. The case studies highlighted above demonstrate the tangible improvements that can be achieved by incorporating garland impact rollers into material handling systems.
Optimize processes with our conveyor rollers. Reach out now!
Types of Garland Impact Roller
Garland impact rollers come in various types, each designed to cater to specific needs and conditions within conveyor systems. Here are the main types of garland impact rollers:
Three-Roll Garland Impact Rollers
- Configuration: Consists of three rollers connected by a flexible link.
- Application: Suitable for moderate impact areas and standard conveyor belt widths.
- Advantages: Provides a good balance between flexibility and support.

Five-Roll Garland Impact Rollers
- Configuration: Consists of five rollers, providing more points of support.
- Application: Ideal for wider belts and areas with higher impact loads.
- Advantages: Offers enhanced load distribution and shock absorption.

Suspended Garland Impact Rollers
- Configuration: Rollers are suspended on chains or cables, allowing more movement.
- Application: Used in areas where the conveyor needs to accommodate variations in material size and weight.
- Advantages: Provides additional flexibility and can adapt to uneven loads.

Fixed Frame Garland Impact Rollers
- Configuration: Rollers are mounted on a fixed frame, providing rigid support.
- Application: Suitable for environments where stability is crucial, such as heavy impact zones.
- Advantages: Offers consistent support and reduces belt sagging.
Trough Garland Impact Rollers
- Configuration: Rollers are arranged in a trough shape to cradle the conveyor belt.
- Application: Ideal for bulk material handling, ensuring the material stays centered on the belt.
- Advantages: Prevents spillage and keeps materials aligned on the conveyor belt.
Self-Cleaning Garland Impact Rollers
- Configuration: Designed with features to prevent material buildup on the rollers.
- Application: Used in environments where sticky or wet materials are handled.
- Advantages: Reduces maintenance needs and prolongs roller life by preventing clogging.

Rubber-Coated Garland Impact Rollers
- Configuration: Rollers have a rubber coating for enhanced impact resistance.
- Application: Suitable for high-impact areas where materials are dropped onto the conveyor belt.
- Advantages: Provides superior shock absorption and protects the belt from damage.
High-Temperature Garland Impact Rollers
- Configuration: Made with materials that can withstand high temperatures.
- Application: Used in environments with extreme temperatures, such as steel mills and foundries.
- Advantages: Maintains performance and longevity under high-temperature conditions.
Heavy-Duty Garland Impact Rollers
- Configuration: Built with reinforced materials to handle extreme loads and impacts.
- Application: Suitable for mining, quarrying, and other heavy-duty applications.
- Advantages: Offers maximum durability and support for the heaviest loads.
Light-Duty Garland Impact Rollers
- Configuration: Designed for lighter loads and less demanding environments.
- Application: Used in packaging, light manufacturing, and food processing industries.
- Advantages: Cost-effective solution for light-duty applications.
Garland impact rollers are versatile components designed to enhance the performance and longevity of conveyor systems by providing impact resistance and flexibility. The choice of garland impact rollers depends on the specific requirements of the application, including load capacity, environmental conditions, and material characteristics. Selecting the right type ensures efficient material handling and minimizes maintenance needs.
Size of Garland Impact Roller
The size of garland impact rollers can vary depending on the specific requirements of the conveyor system they are being used in. Here are some common dimensions and specifications typically associated with garland impact rollers:
Common Dimensions and Specifications
1. Diameter
- Standard Sizes: 89 mm, 102 mm, 114 mm, 127 mm, and 152 mm.
2. Length
- Standard Lengths: Can range from 200 mm to 1600 mm, depending on the number of rollers in the garland and the conveyor width.
3. Number of Rollers
- Typical Configurations: 3-roll and 5-roll garlands are common, but configurations can be customized based on the application.
4. Shaft Diameter
- Standard Sizes: Usually between 20 mm and 40 mm.
5. Bearing Size
- Standard Sizes: Typically correspond to the roller diameter and shaft size, commonly using standard industrial bearings.
Technical of Garland Impact Roller
Garland impact rollers are a critical component in heavy-duty conveyor systems, designed to absorb shock and reduce the wear and tear on conveyor belts. Below are the technical details and features of garland impact rollers:
Technical Specifications
1. Roller Diameter
- Common Sizes: 89 mm, 102 mm, 114 mm, 127 mm, and 152 mm.
- Selection: The diameter is chosen based on the application requirements and the size of the conveyor system.
2. Roller Length
- Standard Lengths: Ranges from 200 mm to 1600 mm.
- Customization: Length can be customized based on the conveyor width and the number of rollers in the garland assembly.
3. Shaft Diameter
- Standard Sizes: Typically between 20 mm and 40 mm.
- Material: Made from high-strength steel to withstand heavy loads and impacts.
4. Number of Rollers
- Configurations: Usually available in 3-roll and 5-roll garlands.
- Custom Configurations: Can be tailored to specific conveyor designs and load requirements.
5. Bearing Specifications
- Bearing Types: Deep groove ball bearings or spherical roller bearings.
- Bearing Size: Selected to match the roller diameter and shaft size, ensuring smooth operation and long service life.
6. Material Composition
- Roller Shell: Typically made from high-strength steel, rubber-coated for impact absorption.
- Shaft: High-strength steel, sometimes galvanized or coated for corrosion resistance.
- Bearings: High-quality, sealed bearings to protect against dust and moisture.
7. Impact Resistance
- Rubber Coating: Rollers are often coated with a thick layer of rubber to absorb shocks and reduce damage to the conveyor belt.
- Durability: Designed to withstand heavy impact loads from falling materials.
Key Features
- Shock Absorption
- Reduces wear and tear on the conveyor belt by absorbing the impact of heavy and abrasive materials.
- Durability
- Made from robust materials to ensure long service life even in harsh operating conditions.
- Flexibility
- Garland design allows for flexibility in the assembly, which helps in maintaining belt alignment and reducing structural stress.
- Ease of Maintenance
- Designed for easy installation and replacement, minimizing downtime in operations.
- Customizability
- Can be customized in terms of conveyor roller size, number of rollers, and materials to suit specific applications.
Garland Impact Roller Selection and Installation Guide
Selecting the right garland impact roller for your conveyor system is crucial for optimizing performance and extending the lifespan of your equipment. This guide provides insights into choosing the appropriate garland impact roller based on key factors such as belt width, material type, and conveyor speed. Additionally, we offer a detailed step-by-step installation guide to ensure proper setup and functionality.
Selecting the Right Garland Impact Roller
The selection of a garland impact roller should be tailored to the specific needs of your conveyor system. The table below outlines the primary considerations to keep in mind when choosing the right garland impact roller.
Factor | Consideration | Recommendation |
---|---|---|
Belt Width | The width of the conveyor belt determines the size of the garland impact roller needed. | Select a garland impact roller that spans the entire width of the belt to ensure even distribution of impact forces. |
Material Type | The type of material being conveyed affects the choice of roller, as abrasive or sharp materials require more durable rollers. | Choose rollers made from materials that can withstand the characteristics of the conveyed material, such as high-density polyethylene (HDPE) for abrasive materials. |
Conveyor Speed | The speed at which the conveyor operates can influence the impact force on the rollers. | For higher speed conveyors, select garland impact rollers designed for high impact absorption to minimize wear and tear. |
Installation Guide for Garland Impact Roller
Installing a garland impact roller requires careful attention to detail and adherence to safety protocols. Follow this step-by-step guide to ensure a successful installation:
Preparation
- Gather necessary tools, including wrenches, a level, and safety equipment (gloves, safety glasses).
- Ensure the conveyor system is powered off and locked out to prevent accidental activation.
Removal of Existing Rollers (if applicable)
- Carefully remove any existing rollers from the conveyor frame to make room for the garland impact roller.
- Inspect the frame for damage or wear that could affect the new installation.
Positioning the Garland Impact Roller
- Place the garland impact roller in the desired location, typically at the loading zone where impact forces are highest.
- Use the level to ensure the roller is positioned horizontally across the conveyor frame.
Securing the Roller
- Secure the garland impact roller to the conveyor frame using the provided brackets and bolts.
- Tighten all fasteners to the manufacturer’s specifications to ensure stability and performance.
Adjustment for Optimal Performance
- Adjust the spacing and angle of the garland impact roller, if necessary, to match the belt’s width and the material flow.
- Ensure that the roller is set at the correct height to engage with the material effectively without causing unnecessary drag or wear.
Safety Checks and Testing
- Conduct a thorough inspection of the installation to ensure all components are securely fastened and properly aligned.
- Remove any tools or debris from the area, and then power on the conveyor system to test the functionality of the garland impact roller.
- Observe the roller during operation to confirm that it is absorbing impacts as intended and that there is no unusual noise or vibration.
Maintenance Planning
- Establish a maintenance schedule based on the manufacturer’s recommendations to inspect and replace any worn components of the garland impact roller.
- Regular maintenance ensures the longevity and efficiency of the roller and the conveyor system as a whole.
By following these selection and installation guidelines, you can enhance the performance and durability of your conveyor system with the right garland impact roller. Proper selection based on specific operational needs and careful installation are key to maximizing the benefits of this innovative solution.
Essential Maintenance and Care for Your Garland Impact Roller
Maintaining your garland impact roller is crucial for ensuring its longevity and optimal performance. Regular and proper care not only extends the life of your equipment but also prevents potential operational issues that could lead to downtime or costly repairs. In this section, we will delve into the best practices for maintaining your garland impact roller and provide common troubleshooting tips for resolving issues with the garland impact drum.
Best Practices for Maintaining Your Garland Impact Roller
Regular Inspections: Conduct thorough inspections of the garland impact roller regularly. Look for signs of wear and tear, such as cracks, corrosion, or any deformation on the rollers and the frame. Early detection of these issues can prevent them from escalating into more significant problems.
Lubrication: Proper lubrication is essential for the smooth operation of the garland impact roller. Ensure that all moving parts, especially bearings, are adequately lubricated to reduce friction and wear. Follow the manufacturer’s recommendations on the type of lubricant to use and the frequency of lubrication.
Cleaning: After each use, clean the garland impact roller to remove any debris, dust, or materials that may have accumulated. This helps in preventing the buildup of materials that could interfere with the roller’s functionality or cause premature wear.
Adjustment and Alignment: Check the alignment of the garland impact roller regularly. Misalignment can lead to uneven wear and tear, affecting the roller’s performance and the quality of the work. If necessary, adjust the rollers to ensure they are correctly aligned according to the manufacturer’s specifications.
Replacement of Worn Parts: Inspect the rollers and other components for wear. Replace any parts that are worn out or damaged. Using worn-out parts can not only affect the performance of the garland impact roller but also pose a safety risk.
Common Troubleshooting Tips for Garland Impact Drum Problems
Noise or Vibration: If the garland impact roller starts making unusual noises or vibrates excessively, check for loose components or misalignment. Tighten any loose parts and realign the roller as needed.
Decreased Performance: If the roller is not performing as expected, check for clogged or dirty components. Clean the roller thoroughly and check for any parts that may need lubrication or replacement.
Roller Movement Issues: Difficulty in roller movement can be due to insufficient lubrication or damaged bearings. Ensure that all moving parts are well-lubricated and replace any bearings that show signs of wear or damage.
Material Buildup: Material buildup on the roller can affect its performance. Regularly clean the roller to remove any materials that are stuck to it. Use appropriate tools and follow safety guidelines while cleaning.
By following these maintenance and care practices, you can ensure that your garland impact roller remains in top condition, providing reliable performance for years to come. Regular maintenance not only saves you time and money in the long run but also ensures that your projects are completed efficiently and effectively.

Garland Impact Roller Cost and Availability
Investing in a garland impact roller for your conveyor system involves understanding the cost implications and knowing where to find quality products. This section provides an overview of the cost considerations associated with garland impact rollers and offers guidance on where to purchase them.
Cost Considerations
The cost of a garland impact roller can vary widely based on factors such as size, material, and the specific needs of your conveyor system. Below is a table that outlines the key cost considerations when investing in a garland impact roller, including the initial purchase price and the potential savings on maintenance and downtime.
Cost Factor | Description | Impact |
---|---|---|
Initial Purchase Price | The upfront cost of acquiring a garland impact roller. | Higher initial investment compared to traditional rollers, but justified by enhanced durability and performance. |
Installation Costs | Expenses related to installing the garland impact roller, including labor and any necessary modifications to the conveyor system. | One-time cost that can vary depending on the complexity of the installation. |
Maintenance Savings | Reduced maintenance costs due to the durability and design of the garland impact roller, which can withstand high-impact conditions better than traditional rollers. | Significant long-term savings as a result of fewer replacements and repairs. |
Downtime Reduction | Savings achieved by minimizing conveyor downtime, thanks to the enhanced reliability and longevity of the garland impact roller. | Can result in substantial cost savings over time, as downtime can be costly in terms of lost production and efficiency. |
Availability and Purchasing Recommendations
Garland impact rollers are available from a variety of manufacturers and suppliers specializing in conveyor system components. When looking for garland impact rollers for sale, consider the following recommendations to ensure you are getting a quality product from a reputable source:
- Manufacturer Reputation: Research manufacturers to find those with a strong reputation in the industry for quality and reliability. Look for companies with positive reviews and testimonials from other customers.
- Product Range: Choose a supplier that offers a wide range of garland impact roller options to ensure you can find a product that matches your specific requirements in terms of size, material, and design.
- Customer Support: Good customer support is crucial, especially when it comes to technical products like garland impact rollers. Look for suppliers that offer comprehensive support, including installation guidance and after-sales service.
- Warranty and Guarantees: Check if the manufacturer offers warranties or guarantees on their products. This can provide peace of mind and protection for your investment.
- Global Availability: For businesses operating in multiple countries, consider suppliers with a global distribution network to ensure consistent product availability and support across all your operations.
To find reputable manufacturers and suppliers, start by conducting online searches, attending industry trade shows, and consulting with other professionals in the material handling sector. Additionally, industry associations and publications can be valuable resources for identifying leading suppliers of garland impact rollers.
By carefully considering the cost implications and selecting a reputable supplier, you can ensure that your investment in a garland impact roller enhances the efficiency and longevity of your conveyor system, providing significant long-term value.
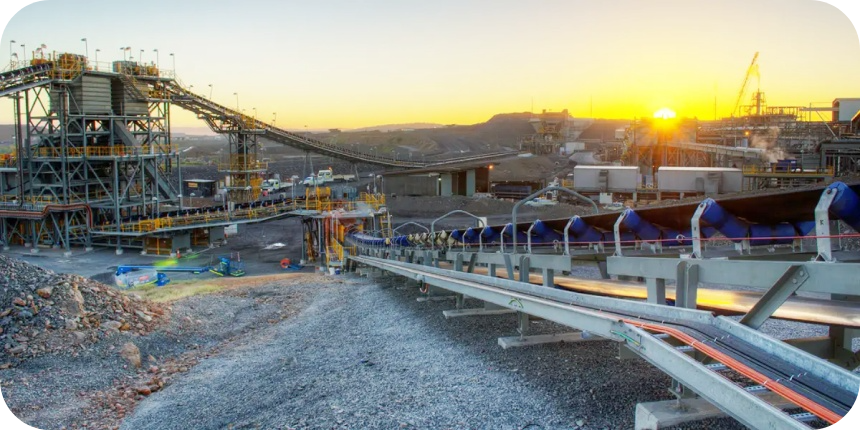
Innovations and Future Trends in Conveyor Technology: The Role of Garland Impact Roller
As we look towards the future of conveyor technology, it’s clear that innovation and efficiency are at the forefront of industry trends. Among these advancements, the garland impact roller stands out as a pivotal component in the evolution of conveyor systems. This section delves into the speculative future developments in conveyor technology, emphasizing the innovative solutions such as garland impact rollers, and discusses how advances in materials and design are set to further improve the efficiency and reliability of these systems.
The Future Development of Conveyor Technology and the Garland Impact Roller
The conveyor industry is poised for a wave of innovation, with the garland impact roller playing a crucial role. These rollers, known for their flexibility and durability, are expected to become even more integral as conveyor systems become more sophisticated. Future developments may include:
Smart Garland Impact Rollers: Integration of IoT (Internet of Things) technology into garland impact rollers could lead to smart conveyor systems capable of real-time monitoring and adjustment. These smart rollers could automatically adjust their operation based on the load, speed, and other operational parameters, significantly enhancing efficiency and reducing wear and tear.
Advanced Materials: The use of new, high-performance materials in the construction of garland impact rollers is anticipated. Materials such as ultra-high molecular weight polyethylene (UHMWPE) and reinforced composites could offer improved wear resistance, reduced weight, and longer service life, contributing to more sustainable and cost-effective conveyor operations.
Modular and Scalable Designs: Future garland impact rollers might feature modular designs that allow for easy customization and scalability. This flexibility would enable conveyor systems to adapt to changing operational needs, such as varying load sizes and weights, with minimal downtime for adjustments.
Advances in Materials and Design
The evolution of materials and design in conveyor technology promises to bring significant improvements to the efficiency and reliability of these systems. Key areas of advancement include:
Eco-friendly Materials: With a growing emphasis on sustainability, the development of eco-friendly materials for garland impact rollers and other conveyor components is becoming a priority. These materials aim to reduce the environmental impact of production and disposal, aligning with global sustainability goals.
Enhanced Durability and Efficiency: Advances in material science and engineering are expected to produce garland impact rollers that are not only more durable but also more efficient. By reducing friction and improving wear resistance, these advancements could lead to lower energy consumption and operational costs.
Customization and Precision Engineering: Future trends also point towards increased customization and precision engineering in the design of garland impact rollers. Tailored solutions that meet specific operational requirements will enhance system performance and reliability, ensuring that conveyor systems can handle a wider range of materials and operating conditions with greater precision.
The future of conveyor technology is bright, with innovative solutions such as the garland impact roller at the heart of this evolution. As advances in materials and design continue to unfold, we can expect to see conveyor systems that are more efficient, reliable, and adaptable to the changing needs of industries worldwide. The integration of smart technologies and sustainable practices will further enhance the capabilities of these systems, ensuring their place in the future of material handling and transportation.
FAQs about Garland Impact Roller
Impact rollers in belt conveyors play a crucial role in absorbing and dissipating the forces generated by falling materials at loading points or transfer points. These rollers are strategically placed where the material drops significantly onto the conveyor belt to prevent damage to the belt itself and to minimize the wear and tear on the conveyor system. The design of impact rollers typically involves a series of robust, cushioned rollers that are capable of withstanding high impact forces. They are constructed from durable materials and often feature a rubber coating or sleeves to enhance their impact-absorbing capabilities. By effectively absorbing the shock and vibration caused by heavy or sharp materials, impact rollers extend the lifespan of the conveyor belt and reduce maintenance needs, ensuring smoother and more efficient operation of the conveyor system.
Garland idlers consist of a string of rollers linked together to form a flexible chain. This design allows the idler to adjust and conform to the belt’s shape and the varying loads that pass over it, providing a more even distribution of weight and reducing stress on individual rollers. Garland idlers are used in areas of the conveyor system that require enhanced flexibility and impact absorption, such as at loading zones or along curved sections of the conveyor. The flexibility of garland idlers makes them particularly effective in handling materials that are irregular in size or shape, as they can adapt to the load more effectively than traditional, rigid idler frames. This adaptability not only improves the efficiency of material handling but also contributes to the longevity of the conveyor belt and the overall system by minimizing wear and tear.
Carrying idlers and impact idlers serve distinct functions within a conveyor system. Carrying idlers, also known as troughing idlers, are primarily used to support the conveyor belt and the material being transported along the length of the conveyor. They are positioned along the conveying side of the belt and are designed to help maintain the belt’s shape and alignment, ensuring smooth and efficient transport of materials.
Impact idlers, on the other hand, are specifically designed to absorb the shock and impact of material falling onto the conveyor belt at loading or transfer points. They are constructed to be more robust than carrying idlers, often featuring reinforced frames and rollers with cushioning materials, such as rubber, to effectively dissipate the energy of falling materials. This specialization helps protect the conveyor belt from damage and reduces wear on the system.
The main difference between the two lies in their purpose and construction: carrying idlers support the belt and load under normal conditions, while impact idlers provide additional protection against the forces of impact at critical points along the conveyor.
Idler roller conveyors utilize various types of idlers to support the conveyor belt and facilitate the transport of materials. The primary types of idler rollers include:
Carrying Idlers (Troughing Idlers): These are the most common type of idlers, used to support the conveyor belt and material. They are typically arranged in a trough shape to contain the material being transported.
Impact Idlers: Placed at loading and transfer points where material falls onto the belt, impact idlers are designed to absorb the shock and protect the belt.
Return Idlers: These idlers support the return side of the belt as it loops back to the beginning of the conveyor system. They can be flat or slightly troughed to minimize belt wear.
Guide Idlers: Guide idlers are used to keep the conveyor belt centered and prevent it from drifting off to the sides. They are crucial for maintaining the alignment of the belt.
Garland Idlers: Consisting of a chain of rollers linked together, garland idlers offer flexibility and adaptability, particularly useful in curved sections of the conveyor or where variable loads are expected.
Each type of idler plays a specific role in the conveyor system, contributing to its overall efficiency, durability, and smooth operation. The selection of idler types depends on the conveyor design, material characteristics, and operational requirements.
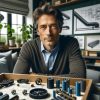
Jordan Smith, a seasoned professional with over 20 years of experience in the conveyor system industry. Jordan’s expertise lies in providing comprehensive solutions for conveyor rollers, belts, and accessories, catering to a wide range of industrial needs. From initial design and configuration to installation and meticulous troubleshooting, Jordan is adept at handling all aspects of conveyor system management. Whether you’re looking to upgrade your production line with efficient conveyor belts, require custom conveyor rollers for specific operations, or need expert advice on selecting the right conveyor accessories for your facility, Jordan is your reliable consultant. For any inquiries or assistance with conveyor system optimization, Jordan is available to share his wealth of knowledge and experience. Feel free to reach out at any time for professional guidance on all matters related to conveyor rollers, belts, and accessories.