Unveiling the Power of Impact Roller Technology
Impact roller technology represents a significant advancement in the field of construction and engineering, offering a revolutionary approach to compaction and ground stabilization. Unlike traditional compaction methods that rely on static weight or vibration to compact materials, impact roller technology utilizes a dynamic, high-energy process to achieve deeper and more uniform compaction. This technology employs specially designed rollers, characterized by their non-cylindrical shape, to deliver forceful impacts to the ground, effectively compacting a wide range of soil types and materials. The distinct advantage of impact roller technology lies in its ability to penetrate deeper soil layers, ensuring a more stable and durable foundation for construction projects. By introducing the concept of impact rollers, this technology diverges from conventional equipment, providing a solution that not only enhances the efficiency of compaction tasks but also contributes to the longevity and reliability of construction and engineering projects. Through its innovative design and operation, impact roller technology has become an indispensable tool in modern construction, paving the way for more efficient, effective, and environmentally friendly compaction methods.
The Mechanism Behind Impact Roller Technology: Enhancing Compaction Efficiency
Impact roller technology represents a significant advancement in the field of ground compaction, offering a unique and effective solution for soil stabilization and compaction projects. Unlike traditional rolling methods, impact roller technology utilizes a distinct design and working principle that sets it apart, making it particularly effective for a wide range of compaction tasks. This section delves into the design principles, working mechanisms, and unique features of impact rollers, highlighting how these aspects contribute to their effectiveness in compaction projects.
Design Principles of Impact Rollers
The core design principle behind impact roller technology is the use of a non-cylindrical, multi-sided drum or module, as opposed to the traditional cylindrical rollers found in conventional compaction equipment. This innovative design allows impact rollers to deliver high-energy impacts to the ground, significantly enhancing compaction efficiency and effectiveness.
The multi-sided drum is engineered to rotate about its axis as the roller moves forward, with each side designed to lift and then forcefully impact the ground surface. This action mimics the effect of repeatedly dropping a heavy weight onto the soil, thereby delivering a much more intense compaction force than that achieved through standard rolling action.
Working Principles of Impact Rollers
Impact rollers operate on the principle of converting potential energy into kinetic energy to deliver powerful compaction forces. As the multi-sided drum rotates, it reaches a point where one of its sides is elevated due to the geometric shape. This elevation increases the potential energy of the drum. When the elevated side rotates to the point where it loses support, it falls under gravity, converting the potential energy into kinetic energy as it impacts the ground.
This kinetic energy is then transferred to the soil, compacting it more effectively than traditional methods. The frequency and intensity of these impacts can be adjusted by altering the speed of the roller and the geometric design of the drum, allowing for customization based on the specific requirements of the compaction project.
Unique Features of Impact Roller Technology
- Non-Cylindrical, Multi-Sided Drum: The key feature of impact roller technology is its uniquely designed drum, which can have three to five sides, depending on the model. This design is crucial for generating the lift and subsequent impactful compaction force.
- Depth of Influence: Impact rollers are capable of affecting soil compaction at much greater depths than traditional rollers. This is due to the high-energy impact delivered by the drum, which can penetrate deeper soil layers, making impact rollers ideal for projects requiring deep compaction.
- Energy Efficiency: By utilizing the gravitational force as the primary source of energy for compaction, impact rollers are highly energy-efficient. The design ensures that the maximum amount of energy is transferred to the soil with minimal loss, making the compaction process more sustainable and cost-effective.
- Versatility: The design of impact rollers allows them to be effective on a wide range of soil types and conditions. Whether dealing with cohesive soils or non-cohesive materials, impact rollers can achieve desired compaction levels, making them versatile tools for various projects.
The mechanism behind impact roller technology is a testament to innovative engineering, offering a more effective and efficient method for soil compaction. The unique design and working principles of impact rollers, characterized by their non-cylindrical, multi-sided drums, enable them to deliver high-energy impacts to the ground. This technology not only enhances the depth and quality of compaction but also brings energy efficiency and versatility to compaction projects, making impact rollers a valuable asset in the construction and civil engineering industries.
Applications and Advantages of Impact Roller Technology
Impact roller technology has revolutionized the construction, mining, and engineering sectors by offering a more efficient and effective solution for soil compaction and ground stabilization. This technology is distinguished by its ability to deliver high-energy impacts to the ground, significantly improving compaction depth and uniformity across various applications. Below, we explore the diverse applications of impact roller technology and analyze its advantages over traditional compaction methods.
Applications of Impact Roller Technology:
Soil Compaction: Ideal for preparing the ground for residential, commercial, and industrial construction projects, ensuring a stable and durable foundation.
Road Construction: Used in the construction and rehabilitation of roads and highways, impact rollers enhance the strength and longevity of the road base.
Mining Operations: In mining, impact rollers are employed to compact tailings and other waste materials, reducing environmental impact and improving site stability.
Landfill Compaction: Essential for waste management and environmental protection, impact rollers compact landfill sites more efficiently, maximizing space and minimizing settlement.
Agricultural Land Improvement: Farmers use impact roller technology to break up hardpan layers, improving water infiltration and root penetration for better crop yields.
Airport Runway Construction: Ensures the compaction of runway subgrades to meet strict safety and performance standards.
Advantages of Impact Roller Technology:
Advantage | Impact Roller Technology | Traditional Methods |
---|---|---|
Compaction Depth | Achieves deeper compaction, reaching several meters below the surface. | Limited to the top few centimeters to a meter of soil. |
Efficiency | High-energy impacts result in faster compaction over large areas. | Time-consuming, requiring multiple passes to achieve desired compaction. |
Uniformity | Delivers more uniform compaction, reducing the risk of uneven settling. | Can result in variable compaction, leading to potential structural issues. |
Environmental Benefits | Reduces the need for material removal and transport, lowering carbon emissions. | Often requires excavation and replacement of unsuitable materials, increasing environmental impact. |
Cost-Effectiveness | Lower operational costs due to faster completion and reduced material handling. | Higher costs associated with longer project durations and additional material processing. |
Versatility | Effective on a wide range of soil types and conditions. | May require different equipment for different soil types, increasing project complexity. |
Impact roller technology stands out for its ability to transform the compaction process, offering significant advantages in terms of depth, efficiency, and environmental impact. By leveraging this innovative approach, projects can achieve more stable and durable foundations, roads, and structures, ensuring their longevity and safety. The comparison table highlights the clear benefits of choosing impact roller technology over traditional compaction methods, making it a preferred choice for modern construction and engineering projects.
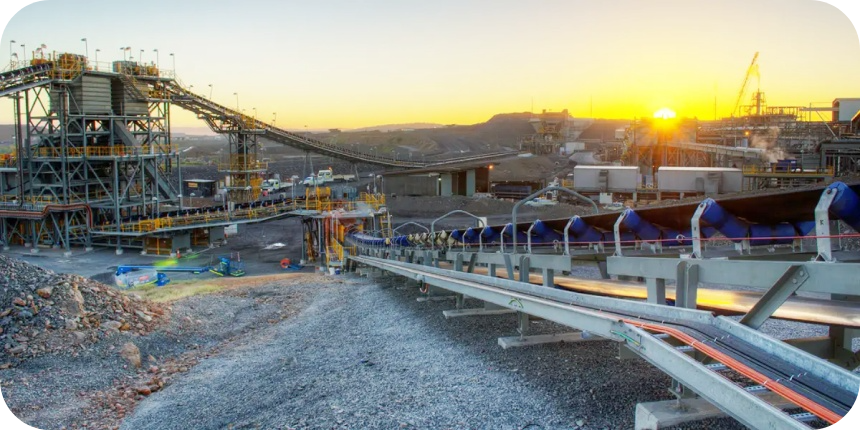
Understand the Cost and Price of Impact Roller Technology
The adoption of impact roller technology in construction and engineering projects represents a significant advancement in compaction and ground stabilization methods. However, understanding the cost and price associated with this technology is crucial for businesses and project managers considering its implementation. Several factors influence the cost and price of impact roller technology, each contributing to the overall investment required to incorporate this innovative solution into operations.
Factors Influencing Cost and Price:
Factor | Description |
---|---|
Equipment Size | Larger impact rollers, capable of covering more area and achieving deeper compaction, typically come at a higher price due to the increased material and manufacturing efforts required. |
Design Complexity | The complexity of the impact roller's design, including the shape of the drum and the integration of advanced features for better compaction and efficiency, can significantly affect the cost. |
Technological Advancements | Impact rollers equipped with the latest technology for monitoring compaction depth, GPS tracking, and automation features tend to be more expensive due to the research and development costs involved. |
Manufacturing Materials | The choice of materials used in manufacturing impact rollers, especially those designed to withstand heavy loads and harsh conditions, can also impact the price. High-quality steel or specialized alloys are often used for durability but come at a higher cost. |
Initial Investment vs. Long-Term Savings:
Aspect | Initial Investment | Long-Term Savings |
---|---|---|
Purchase Price | Higher upfront cost due to advanced design and technology. | Reduced need for replacements or repairs thanks to durable construction. |
Operational Efficiency | Investment in training and potentially higher fuel costs for operation. | Significant savings in time and resources due to faster compaction and fewer passes required. |
Maintenance Costs | Initial setup and calibration costs. | Lower long-term maintenance expenses due to robust design and fewer mechanical issues. |
Material Handling | Possible additional costs for transporting and setting up larger equipment. | Savings on material costs by improving in-situ compaction, reducing the need for additional fill materials. |
What is the cost and price of impact roller technology involves a comprehensive analysis of both the initial investment and the potential long-term savings. While the upfront cost of acquiring and implementing impact roller technology may be higher than traditional compaction methods, the efficiency gains, durability, and reduced maintenance requirements offer significant savings over time. This technology not only enhances the quality of compaction projects but also contributes to more sustainable construction practices by minimizing environmental impact and resource consumption. By carefully considering these factors, businesses can make informed decisions about integrating impact roller technology into their operations, balancing initial costs with the promise of long-term operational benefits and savings.
Components and Parts of Impact Roller Equipment: Ensuring Efficiency in Impact Roller Technology
Impact roller technology, a pivotal innovation in the field of ground compaction, relies on a sophisticated assembly of components and parts to deliver its unparalleled compaction force. At the heart of this technology are the impact drum, buffer mechanism, and hydraulic system, each playing a crucial role in the operation and effectiveness of impact roller equipment. Understanding these components, along with the importance of maintenance and parts availability, is essential for ensuring the longevity and reliability of impact roller technology.
Key Components of Impact Drum Equipment
Impact Drum
The impact drum is the core component of impact roller technology, distinguished by its non-cylindrical, multi-sided design. Unlike traditional cylindrical rollers, the impact drum features several flat sides that create a unique rolling and impacting action. As the drum rotates, each flat side lifts and then forcefully impacts the ground, delivering a high-energy blow that compacts the soil beneath. The design and material of the impact drum are critical for its performance, requiring precision engineering to achieve the desired compaction depth and efficiency.
Buffer Mechanism
The buffer mechanism is integral to impact roller technology, designed to absorb the shock generated during the impact process. This mechanism ensures that the force exerted by the drum does not damage the equipment or transfer excessive vibration to the operator or the towing vehicle. Buffer mechanisms typically include springs, damping rubber pads, and hydraulic buffers, which work together to mitigate the shock and ensure smooth operation. The effectiveness of the buffer mechanism directly influences the durability and operational comfort of the impact roller equipment.
Hydraulic System
Impact roller technology often incorporates a hydraulic system to facilitate the movement and control of the impact drum. This system powers the actuating lift cylinder, which raises and lowers the drum for compaction or transportation. The hydraulic system is connected to the towing vehicle, providing a reliable and efficient means of transferring hydraulic energy to the impact drum. The design and maintenance of the hydraulic system are vital for the seamless operation of impact roller equipment, ensuring that the drum can be precisely controlled to deliver consistent compaction results.
Importance of Maintenance and Parts Availability
The longevity and reliability of impact roller technology significantly depend on regular maintenance and the availability of replacement parts. Proper maintenance ensures that each component of the impact roller equipment functions optimally, reducing the risk of breakdowns and extending the equipment’s service life. Key maintenance tasks include regular inspections of the impact drum, buffer mechanism, and hydraulic system, along with timely replacement of worn or damaged parts.
Parts availability is equally important, as it allows for quick repairs and minimizes downtime. Manufacturers of impact roller equipment should provide comprehensive support, offering easy access to genuine replacement parts and technical assistance. This support ensures that impact roller technology remains a reliable and effective solution for ground compaction projects.
The components and parts of impact roller equipment, including the impact drum, buffer mechanism, and hydraulic system, are fundamental to the operation and effectiveness of impact roller technology. Regular maintenance and parts availability are crucial for ensuring the longevity and reliability of this innovative compaction solution. By understanding and addressing these aspects, users can maximize the benefits of impact roller technology, achieving efficient and consistent soil compaction across a wide range of applications.
Impact Roller Technology on the Market
Navigating the market for impact roller technology requires a discerning eye and an understanding of what makes this equipment a valuable asset in construction and compaction projects. With various models available, such as the Impact Drum Compactor, Impactor 3000, Impactor 3000h, and Impactor 2000 Concrete Breaker, it’s essential to know how to assess the condition of the equipment, the reputation of the seller, and ensure that you’re making a wise investment. Here’s a comprehensive guide to finding impact roller technology for sale and making an informed purchase decision.
Assessing Equipment Condition:
When considering the purchase of impact roller technology, the condition of the equipment is paramount. Look for signs of wear and tear, especially on critical components like the drum, bearings, and hydraulic systems. Ask for maintenance records and inspection reports to gauge how well the equipment has been cared for. If possible, conduct a physical inspection or hire a professional to assess the equipment’s condition. This step is crucial in avoiding costly repairs down the line.
Evaluating Seller Reputation:
The reputation of the seller can provide valuable insights into the quality of the equipment and the level of customer service you can expect. Research the seller’s history, read customer reviews, and check for any complaints or accolades from industry associations. A reputable seller should be transparent about the equipment’s history, provide clear and detailed information, and be willing to answer any questions you may have.
Ensuring Value for Your Money:
To ensure you’re getting the best value for your money, compare prices and features of similar impact roller technology models on the market. Consider the equipment’s age, condition, and any included warranties or service agreements. Don’t hesitate to negotiate the price, especially if you’ve identified any issues during your assessment. Remember, the cheapest option isn’t always the best value; consider the long-term benefits and potential savings in maintenance and operational efficiency.
Highlights of Specific Models:
- Impact Drum Compactor: Known for its robust design and versatility in compacting a wide range of materials. Ideal for large-scale projects requiring deep compaction.
- Impactor 3000 and 3000h: These models are designed for heavy-duty applications, offering high-energy impact compaction suitable for challenging ground conditions.
- Impactor 2000 Concrete Breaker: Specialized for breaking and compacting concrete, this model combines the benefits of impact rolling with the ability to tackle hard materials.
Each of these models serves specific applications, from general soil compaction to targeted tasks like concrete breaking. When selecting impact roller technology, consider the specific needs of your projects and the features that will best meet those requirements.
Discover our premium conveyor rollers. Inquire for more information!
Future Trends in Impact Roller Technology: Shaping the Next Generation of Compaction
Impact roller technology, a cornerstone in the field of ground compaction and soil stabilization, is poised for significant advancements and broader applications in the coming years. As industries continue to seek more efficient, sustainable, and cost-effective solutions, the future of impact roller technology is being shaped by ongoing research, development efforts, and technological innovations. This section explores potential future developments in impact roller technology, including technological advances and new applications in construction, engineering, and beyond, while highlighting how these efforts are driving the evolution of buffer roller technology.
Technological Advances in Impact Roller Technology
The next generation of impact roller technology is expected to see substantial technological improvements aimed at enhancing efficiency, effectiveness, and environmental sustainability. Key areas of focus include:
- Advanced Materials: The development of new materials for the construction of impact drums and buffer mechanisms can lead to lighter, more durable, and more efficient impact rollers. Advanced composites or high-strength alloys could reduce the overall weight of the equipment, improving fuel efficiency and reducing carbon emissions without compromising compaction performance.
- Smart Systems Integration: Integrating smart technologies, such as IoT (Internet of Things) sensors and AI (Artificial Intelligence) algorithms, into impact roller equipment can revolutionize how compaction projects are managed and executed. These technologies could enable real-time monitoring of soil compaction levels, equipment performance, and operational efficiency, allowing for automated adjustments to optimize results.
- Enhanced Buffer Mechanisms: Future developments in buffer technology are likely to focus on improving shock absorption and energy transfer efficiency. Innovations may include adaptive buffering systems that automatically adjust based on soil conditions and compaction requirements, minimizing wear on the equipment and enhancing operator comfort.
- Sustainability Focus: As environmental considerations become increasingly important, future impact roller technology will likely emphasize sustainability. This could involve the development of electric or hybrid propulsion systems to replace traditional diesel engines, significantly reducing the environmental footprint of compaction projects.
New Applications in Construction and Engineering
As impact roller technology evolves, its applications are expected to expand beyond traditional soil compaction and stabilization projects. Potential new applications include:
- Urban Infrastructure Projects: Advanced impact roller technology could be tailored for use in sensitive urban environments, where traditional compaction methods may be too disruptive. This includes compacting subgrades for roads, sidewalks, and bike paths with minimal vibration and noise.
- Disaster Recovery and Mitigation: Impact rollers could play a crucial role in disaster recovery efforts, such as compacting debris fields following earthquakes or landslides, or stabilizing flood-damaged soils. Their ability to rapidly compact large areas could significantly speed up recovery operations.
- Agriculture and Land Management: Innovations in impact roller technology could lead to applications in agriculture and land management, such as compacting and stabilizing land for irrigation projects, or preparing soil for large-scale planting operations.
Shaping the Future of Buffer Roller Technology
Ongoing research and development efforts are crucial in driving the future of impact roller technology. Collaborations between manufacturers, academic institutions, and industry stakeholders are fostering innovation, leading to the development of more advanced, efficient, and environmentally friendly compaction solutions. As these efforts continue, the potential of impact roller technology to transform construction, engineering, and beyond becomes increasingly evident.
FAQs about Impact Roller Technology
An impact roller, a pivotal component in modern construction and compaction projects, operates on a fundamentally different principle compared to traditional rollers. Unlike the latter, which rely on static weight or vibration to compact materials, an impact roller utilizes kinetic energy to achieve compaction. The roller is equipped with a heavy-duty drum, often non-cylindrical and multisided, designed to lift and then forcefully drop onto the ground surface as it rotates. This action delivers high-energy impacts to the soil or material beneath, effectively compacting it to a significant depth.
The working mechanism of an impact roller is based on converting the potential energy of the raised drum into kinetic energy upon impact. As the drum rotates, its uniquely shaped sides cause it to repeatedly lift and fall, creating a series of powerful impacts. This process not only compacts the surface layer but also transmits energy deeper into the ground, achieving compaction at depths that traditional rollers cannot reach. The frequency and intensity of these impacts can be adjusted by altering the roller’s weight, the shape of the drum, and the speed at which the roller is towed, allowing for customization based on the specific requirements of the project.
Impact rollers are particularly effective in compacting loose, granular materials and can significantly improve the density and stability of the soil. This method of compaction is highly efficient, enabling large areas to be treated in a relatively short amount of time, and is less likely to cause damage to adjacent structures due to the focused nature of the energy application.
Impact rollers are utilized in a wide range of applications across the construction, mining, and agricultural sectors due to their ability to achieve deep and uniform soil compaction. Their primary application is in the preparation of foundations for buildings, roads, and other infrastructure, where a stable and compacted ground base is essential for long-term durability and safety. By effectively compacting the soil, impact rollers help prevent settling and shifting that can lead to structural damage over time.
In road construction, impact rollers are used to compact the subgrade and base layers before asphalt or concrete is laid, ensuring a firm, stable foundation that can withstand heavy traffic loads. This application is critical for the longevity and reliability of roadways, reducing the need for frequent repairs and maintenance.
In the mining industry, impact rollers are employed to compact tailings and other waste materials, facilitating the reclamation of land and reducing environmental impact. The deep compaction achieved by these rollers is also beneficial for constructing stable embankments and dams.
Agriculturally, impact rollers are used to break up hardpan layers in the soil, improving water infiltration and root penetration, which can lead to increased crop yields. This application is particularly valuable in regions with compacted or poorly structured soils.
Furthermore, impact rollers are instrumental in large-scale earthworks projects, including the construction of landfills, where their ability to compact various materials helps maximize space efficiency and ensure environmental compliance.
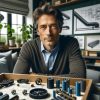
Jordan Smith, a seasoned professional with over 20 years of experience in the conveyor system industry. Jordan’s expertise lies in providing comprehensive solutions for conveyor rollers, belts, and accessories, catering to a wide range of industrial needs. From initial design and configuration to installation and meticulous troubleshooting, Jordan is adept at handling all aspects of conveyor system management. Whether you’re looking to upgrade your production line with efficient conveyor belts, require custom conveyor rollers for specific operations, or need expert advice on selecting the right conveyor accessories for your facility, Jordan is your reliable consultant. For any inquiries or assistance with conveyor system optimization, Jordan is available to share his wealth of knowledge and experience. Feel free to reach out at any time for professional guidance on all matters related to conveyor rollers, belts, and accessories.