Conveyor Belt Rubber Grade And Specifications
Conveyor belts are fundamental components used across various industries to facilitate the efficient transport of goods and materials. These belts, typically made from durable materials, can significantly enhance productivity in manufacturing, mining, packaging, and many other sectors. The efficiency and safety of these systems heavily rely on selecting the appropriate rubber grade. This blog post focuses specifically on understanding the intricacies and applications of different conveyor belt rubber grade options. Each grade of rubber offers unique properties that make it suitable for specific environments and tasks, highlighting the importance of informed selection to optimize performance and cost-efficiency.
What are Rubber Grades in Conveyor Belts
Rubber grades in conveyor belts refer to the specific types of rubber compounds used in the belts, each designed to handle different materials and environmental conditions. These grades determine the belt’s resistance to wear, heat, oils, chemicals, and other factors. Here are the primary rubber grades commonly used in conveyor belts:
Rubber Grade | Characteristics | Applications |
---|---|---|
Grade M | Good balance of tensile strength, abrasion resistance, and flexibility | General material handling (coal, ore, sand, gravel) |
Grade N | Moderate oil resistance, prevents swelling and degradation | Materials with moderate oil content (greasy substances) |
Grade RMA I | Superior abrasion resistance, high tensile strength | Highly abrasive materials (crushed rock, ore, limestone) |
Grade RMA II | Good abrasion resistance, economical | General-purpose applications with moderate abrasion |
Grade S | Super heat resistance, retains properties at high temperatures | High-temperature materials (hot asphalt, clinker, foundry sand) |
Grade T | High tear resistance, durable | Sharp, high-impact materials (scrap metal, glass, logs) |
Grade E | Extreme oil resistance, prevents swelling and softening | High oil content materials (grains, soybeans, wood chips) |
Grade F | Flame retardant, often self-extinguishing | Underground mining, power plants, fire-prone environments |
Grade HR | Good heat resistance, maintains flexibility and strength | Elevated temperature materials (less extreme than Grade S) |
Grade FR | Meets fire safety standards, self-extinguishing properties | Hazardous environments with fire risks |
Grade CR | Resistant to chemical attack, prevents degradation | Chemical processing, handling acidic or alkaline materials |
Grade FDA | Made from non-toxic, food-safe materials, meets FDA standards | Food processing and handling |
Conveyor belt rubber grade M is harder, more abrasion-resistant, stronger, durable, resists cuts, gouges, and remains flexible in low temperatures.
Key Properties:
- Abrasion Resistance: Essential for materials causing wear and tear.
- Heat Resistance: Important for handling high-temperature materials.
- Oil Resistance: Prevents degradation from oils and greases.
- Flame Resistance: Crucial for safety in fire-prone environments.
- Chemical Resistance: Protects against chemical corrosion.
- Tear Resistance: Ensures durability against sharp and high-impact materials.
Each rubber grade is tailored to meet specific operational requirements, ensuring optimal performance, longevity, and safety of the conveyor belt in its intended application.
Basic Conveyor Belt Rubber Grades
Selecting the right conveyor belt rubber grade is essential for ensuring optimal performance and longevity in various industrial applications. The grade of the rubber affects everything from abrasion resistance to chemical resilience, making it crucial to choose wisely based on the specific needs of the operation.
Grade 1 vs Grade 2 Conveyor Belts
Here is a comparison table for Grade 1 and Grade 2 conveyor belts, highlighting their characteristics and applications:
Property/Characteristic | Grade 1 Conveyor Belts | Grade 2 Conveyor Belts |
---|---|---|
Abrasion Resistance | Superior abrasion resistance, higher durability | Good abrasion resistance, moderate durability |
Tensile Strength | Higher tensile strength, capable of withstanding more stress | Adequate tensile strength for general applications |
Applications | Highly abrasive materials (e.g., crushed rock, ore, limestone) | General-purpose applications (e.g., bulk handling of coal, sand, gravel) |
Cost | Higher cost due to superior materials and performance | More cost-effective, suitable for less demanding applications |
Use Case | Environments with severe wear and tear requirements | Environments with moderate wear and tear requirements |
Durability | Longer lifespan in abrasive conditions | Sufficient lifespan for general use conditions |
Detailed Characteristics:
Grade 1 Conveyor Belts:
- Abrasion Resistance: These belts are designed to handle highly abrasive materials. They offer superior wear resistance, making them suitable for applications where the belt surface is exposed to rough materials that can cause significant wear and tear.
- Tensile Strength: Grade 1 belts have a higher tensile strength, which means they can withstand greater mechanical stress and are less likely to stretch or break under heavy loads.
- Applications: These belts are ideal for industries such as mining, where the material being conveyed (like rock or ore) is very abrasive. They are also used in industries where the conveyor system is subject to heavy impacts or requires a longer lifespan under harsh conditions.
- Cost: Due to the use of high-quality materials and advanced manufacturing processes, Grade 1 belts are more expensive. However, their durability and longer lifespan can offset the higher initial cost in the long run.
Grade 2 Conveyor Belts:
- Abrasion Resistance: While Grade 2 belts also offer good abrasion resistance, it is at a lower level compared to Grade 1. These belts are designed for general-purpose applications where the material is not as abrasive.
- Tensile Strength: Grade 2 belts have adequate tensile strength for most standard applications. They are capable of handling everyday loads but may not perform as well as Grade 1 belts under extreme stress.
- Applications: These belts are suitable for a wide range of industries, including agriculture, construction, and general material handling. They are used for conveying bulk materials such as coal, sand, and gravel, where the conditions are less harsh.
- Cost: Grade 2 belts are more cost-effective, making them a practical choice for many industries. They provide a good balance between performance and cost, suitable for operations with moderate wear and tear requirements.
Grade 1 conveyor belts are designed for heavy-duty applications with high abrasion and tensile strength requirements, making them suitable for more demanding environments. Grade 2 conveyor belts, on the other hand, are ideal for general-purpose applications, offering a balance between cost and performance for less demanding conditions.
Specialty Grades and Their Applications
Beyond the basic grades, there are specialty conveyor belt rubber grades designed to address specific industrial challenges:
Fire-Resistant Belts
Fire-resistant conveyor belts are crucial in industries where the transported materials or the environments are highly flammable, such as in coal mining, power plants, and timber processing. These belts are treated to self-extinguish flames and prevent fire propagation, enhancing safety standards.
Oil-Resistant Belts
Oil-resistant belts are essential in industries where oils and greases are prevalent, such as the automotive industry and food processing plants. These belts prevent the rubber from swelling, which can affect performance and lifespan.
Heat-Resistant Belts
Designed to withstand high temperatures, heat-resistant belts are used in cement factories and steel mills where materials at elevated temperatures are a norm. They resist cracking and hardening, maintaining operational integrity under thermal stress.
Chemical-Resistant Belts
These belts are tailored for chemical plants or fertilizer production, where exposure to aggressive chemicals is common. They are formulated to resist corrosion and maintain structural integrity.
Antistatic Belts
In environments where static electricity could pose a fire or explosion risk, such as in grain elevators or chemical plants, antistatic belts are used to safely discharge static charges.
High-Abrasion Belts
High-abrasion belts are preferred in sand quarries and mineral processing plants where the material itself is highly abrasive. These belts feature thick covers that resist wear and tear, ensuring longevity and reduced maintenance costs.
Each of these specialty conveyor belt rubber grades plays a pivotal role in its respective industry by offering tailored properties that meet specific operational demands, enhancing both safety and efficiency. Selecting the right grade involves understanding both the material properties and the environmental conditions of the application area.
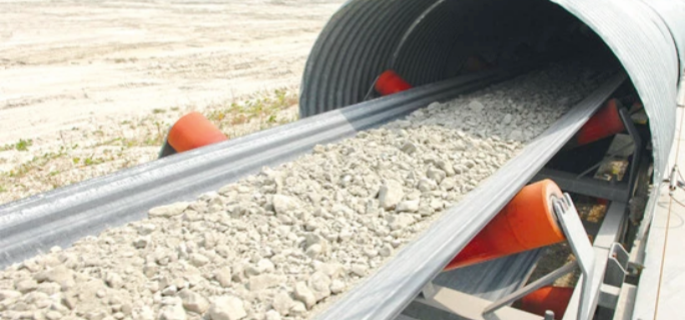
Rating Standards for Conveyor Belt Rubber Grade
Conveyor belt rubber grades are classified based on their resistance to wear, heat, and other environmental conditions. Here are the main rating standards for conveyor belt rubber grades:
1. DIN (Deutsches Institut für Normung) Standards
- DIN 22102: This German standard covers the specifications for textile-reinforced conveyor belts for general use. It specifies the tensile strength and elongation at break.
- DIN 22131: This standard applies to steel-cord conveyor belts. It specifies the requirements for tensile strength and elongation.
2. ISO (International Organization for Standardization) Standards
- ISO 14890: This standard specifies the rubber-covered conveyor belts of textile construction for general use.
- ISO 284: This specifies the electrical conductivity of the conveyor belt. It’s important for belts used in hazardous environments to prevent static electricity buildup.
- ISO 340: This standard specifies the flame retardant properties of the belt, crucial for belts used in underground mining.
3. RMA (Rubber Manufacturers Association) Standards
- RMA Grade 1: This grade offers superior abrasion resistance, making it suitable for applications with a lot of wear and tear.
- RMA Grade 2: This grade provides good abrasion resistance but at a lower level compared to Grade 1. It’s more cost-effective and suitable for general use.
4. ARPM (Association for Rubber Products Manufacturers) Standards
- ARPM Grade I: Similar to RMA Grade 1, it offers excellent abrasion resistance and is used in highly abrasive applications.
- ARPM Grade II: Comparable to RMA Grade 2, it is used in general-purpose applications where the material does not have severe abrasion.
5. MOR (Moderate Oil Resistant) and OR (Oil Resistant) Grades
- MOR Grade: This grade is designed for materials with moderate oil content. It offers resistance to swelling and softening caused by oils.
- OR Grade: This grade is for materials with high oil content and offers superior resistance to oils and greases.
6. Heat Resistant Grades
- HR (Heat Resistant): This grade is used for materials that are exposed to high temperatures. It’s designed to retain its physical properties despite heat exposure.
- SHR (Super Heat Resistant): Suitable for applications with even higher temperature ranges than HR grade.
7. Fire Resistant Grades
- FR (Fire Resistant): This grade is essential for underground mining and other hazardous environments where fire resistance is crucial.
8. Food Grade (FDA) Standards
- FDA Approved: These belts are made from non-toxic materials that are safe for use in food processing and handling applications.
9. Chemical Resistant Grades
- CR (Chemical Resistant): These belts are designed to handle exposure to various chemicals without degrading.
Key Properties Considered in Rating:
- Abrasion Resistance: The ability to withstand wear and tear from materials.
- Heat Resistance: The ability to perform under high temperatures without degrading.
- Oil Resistance: The ability to resist swelling and degradation from oils and greases.
- Flame Resistance: The ability to resist catching fire and self-extinguishing properties.
- Chemical Resistance: The ability to withstand exposure to various chemicals.
Each of these standards ensures that the conveyor belts meet the necessary requirements for their specific applications, providing safety, durability, and efficiency in material handling processes.
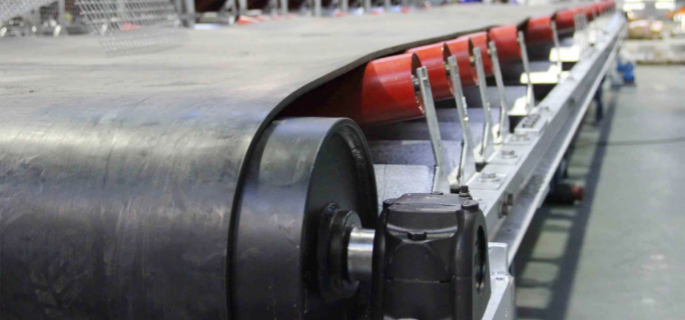
Key Specifications of Conveyor Belt Rubber Grades
When selecting a conveyor belt rubber grade, understanding the key specifications is crucial. These specifications typically include the material composition, thickness, tensile strength, and environmental resistance characteristics of the belt. Each of these factors plays a significant role in determining the belt’s suitability for specific applications.
Material Types and Composition
The material types used in rubber conveyor belts vary widely and are chosen based on the demands of the application. Natural rubber, styrene-butadiene rubber, and nitrile rubber are common materials, each offering different levels of flexibility, wear resistance, and oil resistance. The choice of rubber grade directly impacts the belt’s performance, especially in harsh or specialized environments such as those involving oils, chemicals, or extreme temperatures.
Structural Features
The structural integrity of a conveyor belt depends on its design and construction. Key features include the carcass, which is typically made of fabrics like polyester, nylon, or cotton, and the cover, which is composed of the rubber grade specifically chosen for its protective properties. The thickness of the rubber cover, often tailored to the conveyor belt rubber grade, provides resistance against abrasion, impacts, and cuts, extending the belt’s operational life.
Tensile Strength and Durability
Tensile strength is a critical specification for rubber conveyor belts, indicating the maximum load the belt can handle without breaking. Higher tensile strength is essential for heavy-duty applications, and the selected rubber grade often determines this property. Durability also encompasses the belt’s ability to resist wear and tear over time, a factor heavily influenced by the rubber composition and quality.
Environmental Resistance
Environmental resistance is another key specification driven by the conveyor belt rubber grade. This includes the belt’s ability to withstand exposure to various temperatures, chemicals, and UV light. Some rubber grades are specifically engineered to resist fire, static electricity, or oily substances, making them indispensable in specific industrial settings.
Reference Standards
For comprehensive technical details on these specifications, consulting the conveyor belt specification standards PDF is advisable. These documents provide standardized guidelines and testing methods to ensure that the conveyor belt meets industry requirements and safety standards, helping stakeholders make informed choices based on the specified conveyor belt rubber grade.
Understanding these specifications is fundamental when choosing the right rubber grade for a conveyor belt, as it ensures optimal performance and safety in its intended application environment.
Factors Influencing the Selection of Conveyor Belt Rubber Grades
The selection of the appropriate conveyor belt rubber grade is a critical decision that can significantly affect the performance and durability of a conveyor system. Various factors must be considered to ensure that the chosen rubber grade meets the demands of the application. This selection is influenced by factors such as load size, operating conditions, and environmental influences. Understanding these factors, along with the nomenclature and manufacturer specifications, is vital for making an informed decision.
Load Size and Material Type
The size and type of the load that the conveyor will carry are primary considerations. Heavy or sharp materials require a higher grade of rubber that can resist cuts, tears, and abrasions. For example, mining operations dealing with sharp rocks will benefit from a Grade 1 rubber, which offers superior durability and abrasion resistance compared to a Grade 2 rubber used in lighter applications like the packaging industry.
Operating Conditions
The operational environment of the conveyor belt significantly impacts the choice of rubber grade. This includes factors such as the speed of the conveyor, the length of travel, and whether the belt is exposed to continuous or intermittent use. High-speed belts under continuous operation require robust rubber grades that can withstand the stress and heat generated from rapid movement over long distances.
Environmental Factors
Environmental conditions such as temperature, exposure to chemicals, moisture, and UV light also play a crucial role in selecting the right conveyor belt rubber grade. Belts operating in extreme temperatures, whether hot or cold, need rubber grades specifically formulated to maintain their integrity and performance under such conditions. Similarly, belts used in chemical plants must be resistant to the specific chemicals they will encounter.
Importance of Conveyor Belt Nomenclature and Manufacturer Specifications
- Standardization: Understanding the nomenclature helps in identifying standardized features of conveyor belts as per industry norms, ensuring compatibility and efficiency.
- Performance Matching: Matching the specifications to operational needs ensures that the conveyor belt performs optimally under the given conditions.
- Safety Compliance: Proper selection based on nomenclature and specifications helps in adhering to safety standards, reducing the risk of accidents.
- Cost Efficiency: Knowledge of specifications can prevent over-specifying or under-specifying the required rubber grade, optimizing costs without compromising on performance.
- Durability and Longevity: Selecting the correct rubber grade as per specifications can significantly increase the durability and lifespan of the conveyor belt.
- Maintenance Requirements: Understanding the properties of different rubber grades helps in anticipating maintenance needs and scheduling preventative maintenance, thus reducing downtime.
- Customization Options: Familiarity with conveyor belt specifications and nomenclature allows for customization according to specific operational needs, enhancing productivity.
- Warranty and Support: Manufacturers often provide warranties and support based on compliance with their specified grades and conditions of use, which can be crucial for maintaining operational integrity over time.
The selection of the correct conveyor belt rubber grade is a complex decision that requires careful consideration of various operational, environmental, and material factors. Thorough knowledge of the conveyor belt nomenclature and adherence to manufacturer specifications ensures that the selected belt will perform effectively, safely, and economically.
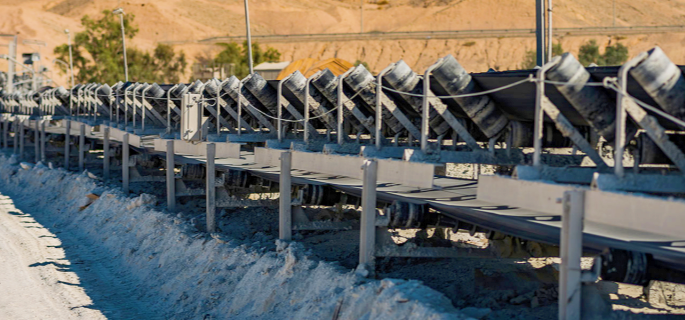
The Importance of Conveyor Belt Rubber Grade
When it comes to industrial applications, particularly in the handling and transportation of materials, the quality and type of conveyor belts used are paramount. Among the many factors that contribute to the optimal performance of conveyor belts, the conveyor belt rubber grade is one of the most crucial. This term refers to the different types of rubber formulations that are used to make conveyor belts, each designed to meet specific operational needs and environmental conditions.
Roles of Conveyor Belt Specifications in Operational Efficiency and Safety
The specification of the conveyor belt rubber grade plays multiple roles in ensuring that the conveyor system operates efficiently and safely. Here are ten key roles:
- Abrasion Resistance: Higher rubber grades offer better resistance against wear and tear from rough materials, thus extending the belt’s operational life.
- Tear Resistance: Certain rubber grades are engineered to withstand cuts and tears, which is crucial in environments where sharp objects are common.
- Temperature Tolerance: Rubber grades are designed to perform under various temperature ranges. Some are suited for extreme cold, while others can withstand high heat, affecting their application in different industries.
- Chemical Resistance: The ability to resist different chemicals without degrading is essential for belts used in chemical processing or places where oils, fats, or other aggressive substances are present.
- Load Support: The strength and elasticity of the rubber grade influence how much weight the belt can support without sagging or breaking.
- Energy Efficiency: Some rubber grades are designed to minimize energy consumption by reducing belt drag and improving glide over conveyor components.
- Impact Resistance: In industries like mining and quarrying, impact resistance is vital to absorb shocks and prevent punctures or damages to the belt.
- Antistatic Properties: Certain environments require belts with antistatic features to prevent electrical discharges. Specific rubber grades are tailored for these needs.
- Hygienic Properties: Food processing and pharmaceutical industries need rubber grades that are non-toxic and easy to clean to maintain hygiene standards.
- Maintenance Requirements: Choosing the right conveyor belt rubber grade can reduce the frequency and cost of maintenance due to its adapted properties to specific operational challenges.
Selecting the correct conveyor belt rubber grade is not just about cost-effectiveness; it’s about matching the belt’s properties to the specific demands of the operation. This tailored approach ensures not only the longevity of the belt but also the safety and efficiency of the entire conveyor system. This strategic selection becomes a cornerstone in the operational success of industries relying heavily on conveyor systems.
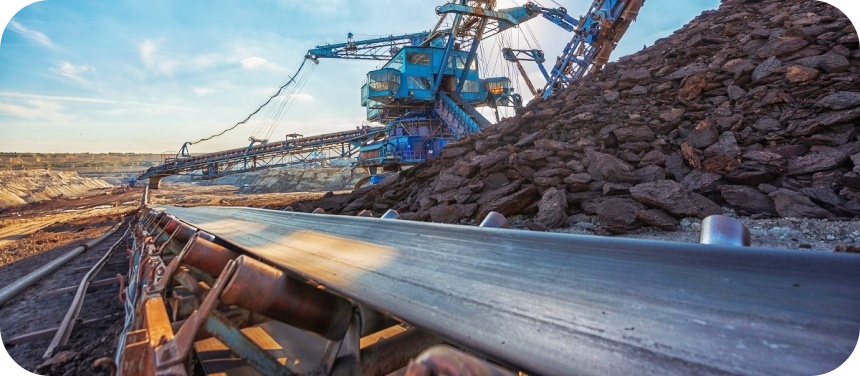
Pricing and Availability of Different Conveyor Belt Rubber Grade
The pricing and availability of various conveyor belt rubber grades are influenced by a range of factors from the type of rubber used to the specific requirements of different industries. Understanding how these grades affect the cost and how they are sourced can help businesses make informed purchasing decisions.
Impact of Rubber Grades on Conveyor Belt Pricing
The cost of conveyor belts is significantly influenced by the grade of rubber used. Higher-grade rubbers, such as Grade 1, which offer superior durability and resistance to harsh conditions, are generally more expensive. These grades are composed of higher quality materials and often incorporate advanced technologies for enhanced performance characteristics like heat resistance, oil resistance, or fire retardancy.
Conversely, lower grades such as Grade 2 are less costly but are suited for less demanding applications. They are typically less robust in terms of performance and longevity, which reflects in their lower price point. Specialty grades, tailored for specific conditions such as extreme temperatures or chemical exposures, may come at a premium due to their specialized nature and the complexity of their manufacturing processes.
Tips on Sourcing and Negotiating with Conveyor Belt Manufacturers
- Understand Your Needs: Before negotiating, clearly define what you need in terms of rubber grade, belt specifications, and performance requirements.
- Research Suppliers: Identify several manufacturers that offer the conveyor belt rubber grade you need. Evaluate their reputation, reliability, and the range of products they offer.
- Check Availability: Some rubber grades might be less readily available due to demand or production complexity. Check with suppliers about lead times and potential delays.
- Request Samples: Where possible, ask for samples of the conveyor belts to assess their quality and whether they meet your specifications before making a large purchase.
- Discuss Pricing Options: Explore volume discounts, long-term contracts, or other pricing strategies that can lower costs.
- Negotiate Payment Terms: Favorable payment terms can ease cash flow, so try to negotiate terms that are advantageous to your business.
- Inquire About Customizations: If you have specific needs, inquire about the possibility and cost of customizations.
- Evaluate Warranty and Support: Understand the warranty offered on the conveyor belts and what it covers. Good after-sales support can be a deciding factor.
- Consider Total Cost of Ownership: Evaluate not only the purchase price but also the longevity and maintenance costs associated with different rubber grades.
- Check Certifications: Ensure that the conveyor belt rubber grades meet all relevant industry standards and certifications, which can provide assurance of quality and compliance.
- Plan for Future Needs: Consider whether your chosen supplier can meet future demand and scaling requirements.
- Build Relationships: Developing a good relationship with suppliers can lead to better deals, improved support, and more reliable supply chains over time.
By understanding the implications of different conveyor belt rubber grades on pricing and availability and by following these sourcing tips, businesses can negotiate more effectively with manufacturers and secure the best possible deals, ensuring that they receive conveyor belts that meet their operational needs at the most competitive prices.
Improve efficiency with our reliable conveyor belt products.
FAQs about Conveyor Belt Rubber Grade
Conveyor belt grades are standardized categories defined to help identify the durability and specific use-case of different conveyor belts. These grades are typically determined based on various factors including the tensile strength of the belt, abrasion resistance, and other special features like heat or oil resistance. In general, conveyor belts are categorized into several grades – Grade 1, Grade 2, and special grades like Grade M24, among others. Each grade serves different operational needs ranging from general material handling to specific applications that require high resistance to abrasion or tear. For instance, belts used in mining operations where sharp and heavy materials are transported might require a different grade compared to belts used in packaging industries. Understanding the specific grade suitable for an application ensures longevity and efficiency in operation, minimizing downtime and maintenance costs.
The primary difference between Grade 1 and Grade 2 conveyor belts lies in their durability and intended use. Grade 1 belts are designed with higher tensile strength and better elongation, making them more suitable for applications where the conveyor belt is subjected to severe impact, sharp materials, and extreme wear conditions. This grade often adheres to stricter quality standards in terms of cut and gouge resistance, making them ideal for heavy-duty applications such as mining or handling of coarse materials.
On the other hand, Grade 2 belts are tailored for less severe conditions, typically offering moderate resistance to abrasion and impact. They are suited for conveying bulk materials in general-purpose applications like agriculture, light mining, and packaging operations. Although they are durable, Grade 2 belts are not built to withstand the same level of abuse as Grade 1 belts, and thus, they are usually less expensive. The choice between Grade 1 and Grade 2 will largely depend on the operational demands and specific challenges faced by the conveyor system.
Rubber conveyor belts are designed with specific specifications to meet diverse operational demands. These specifications encompass a wide range of characteristics, including belt width, thickness, tensile strength, elongation at break, abrasion resistance, and thermal resistance, among others. For instance, the carcass of the belt, which is the core strength-bearing component, can be made from various materials such as nylon, polyester, steel, or a combination thereof.
The cover grade of the belt (e.g., abrasion-resistant, heat-resistant, oil-resistant, etc.) is also a crucial specification, determining the belt’s suitability for different environmental conditions or the type of materials it can safely transport. Further specifications may detail the belt’s resistance to impacts, its electrical conductivity properties, or its ability to resist chemicals and other potentially damaging substances. Understanding these specifications is vital for selecting a conveyor belt that not only fits the application but also operates efficiently and lasts as long as possible.
Conveyor belt grade M24 is a specific category within the broad spectrum of conveyor belt grades, designed primarily for transporting highly abrasive materials like sand, coal, granite, and more. This grade is characterized by high resistance to abrasion, making it suitable for applications in industries such as mining, construction, and aggregate production where the conveyor belt is exposed to harsh materials and conditions on a regular basis.
The “M” in M24 indicates that the belt is suitable for mechanical applications, and the number 24 refers to its tensile strength, which is measured in MPa (Megapascal). M24 grade belts are often made with a blend of natural and synthetic rubbers to achieve the optimal balance of flexibility, wear resistance, and toughness. Additionally, these belts are capable of withstanding moderately adverse weather conditions, including exposure to rain and sunlight, which makes them versatile for indoor and outdoor operations. Selecting an M24 grade conveyor belt can significantly enhance the durability and efficiency of material handling systems in abrasive environments.
M Grade in conveyor belts refers to a high-quality rubber compound characterized by its superior hardness, abrasion resistance, and strength. This grade is designed to handle tough and abrasive materials, making it ideal for industries such as mining, quarrying, and heavy material handling. The enhanced hardness and strength of M Grade rubber provide excellent resistance to cuts and gouges, ensuring a longer lifespan even in demanding environments. Additionally, M Grade belts maintain flexibility at lower temperatures, which allows them to perform effectively across a range of operating conditions. This grade meets stringent elongation requirements, indicating its robustness and durability under heavy loads and impacts. Overall, M Grade conveyor belts offer reliable and long-lasting performance, reducing maintenance costs and downtime in high-wear applications.
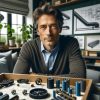
Jordan Smith, a seasoned professional with over 20 years of experience in the conveyor system industry. Jordan’s expertise lies in providing comprehensive solutions for conveyor rollers, belts, and accessories, catering to a wide range of industrial needs. From initial design and configuration to installation and meticulous troubleshooting, Jordan is adept at handling all aspects of conveyor system management. Whether you’re looking to upgrade your production line with efficient conveyor belts, require custom conveyor rollers for specific operations, or need expert advice on selecting the right conveyor accessories for your facility, Jordan is your reliable consultant. For any inquiries or assistance with conveyor system optimization, Jordan is available to share his wealth of knowledge and experience. Feel free to reach out at any time for professional guidance on all matters related to conveyor rollers, belts, and accessories.