Maximizing Efficiency with Drag Belt Conveyor Systems
The drag belt conveyor stands as a paragon of modern engineering in the realm of material handling, revolutionizing operations across various industries. This innovative system, known for its robust design and operational efficiency, offers an unparalleled solution for the transportation of bulk materials. The drag belt conveyor distinguishes itself by providing a reliable and versatile method of moving goods, ensuring minimal material degradation and maximum productivity. Its unique mechanism, which involves dragging the material along a fully enclosed path, offers a dust-free and controlled environment, making it an ideal choice for industries prioritizing cleanliness and precision. With its adaptability to various materials and conditions, the drag belt conveyor is not just a piece of equipment; it’s a pivotal asset in the optimization of industrial operations.
What is Drag Belt Conveyor Systems
The Mechanics Behind Drag Belt Conveyors
Drag belt conveyors represent a significant leap in the technology of material handling. Unlike traditional belt conveyors that rely on a continuous belt loop, drag belt conveyors employ a chain-driven belt. The belt is equipped with paddles or flights attached at regular intervals that drag the material along the conveyor path. This unique mechanism ensures that the material is moved smoothly and consistently, minimizing spillage and ensuring a controlled flow. The enclosed design of the conveyor not only preserves the integrity of the material but also protects it from external contaminants, making it an ideal choice for industries where material purity is paramount.
Distinguishing Features from Traditional Conveyors
Drag belt conveyors differ from traditional conveyors in several key aspects. Firstly, the drag mechanism reduces the risk of material slippage, a common issue in standard belt conveyors, especially when handling wet or sticky materials. Secondly, the enclosed design significantly reduces dust and spillage, promoting a cleaner and safer work environment. Lastly, drag belt conveyors are known for their durability and low maintenance requirements, thanks to the robust construction and fewer moving parts, making them a cost-effective solution in the long run.
Versatility Across Industries
The versatility of drag belt conveyors makes them suitable for a wide range of industries. In the agricultural sector, they are used for the gentle handling of grains and other produce, preserving quality while ensuring efficient transport. In the mining industry, drag belt conveyors are instrumental in moving large volumes of ore and other materials from the extraction site to processing facilities. The construction industry benefits from the conveyor’s ability to handle a variety of materials, from sand and gravel to concrete and rubble, streamlining operations and enhancing productivity.
Handling a Wide Range of Materials
Drag belt conveyors are adept at handling a diverse array of materials. Their robust design allows for the transportation of heavy and abrasive materials without significant wear and tear. Additionally, the gentle dragging action is ideal for delicate materials that are prone to breakage or degradation. The conveyor’s enclosed structure also means that materials with varying levels of moisture content can be transported without the risk of drying out or becoming excessively moist, preserving the material’s quality throughout the transportation process.
Efficiency in Material Handling
The efficiency of drag belt conveyors is evident in their ability to move materials over long distances with minimal energy consumption. The conveyor’s design allows for straight, inclined, or even vertical transportation, providing flexibility in layout design and maximizing space utilization. The ability to have multiple inlets and outlets along the conveyor path also allows for the simultaneous handling of different materials, further enhancing the system’s efficiency.
Drag belt conveyors are a testament to innovation in material handling. Their unique design, coupled with their versatility and efficiency, makes them an invaluable asset in various industries. By understanding the working principle and applications of drag belt conveyors, industries can leverage these systems to optimize their operations, reduce costs, and enhance productivity.
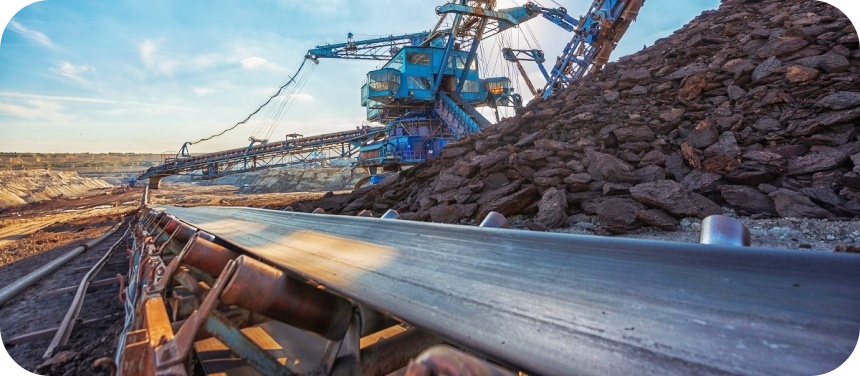
Exploring the Components of Drag Belt Conveyors
What is the Anatomy of Drag Belt Conveyors
Drag belt conveyors, a vital component in various industrial processes, consist of several key parts, each playing a crucial role in the conveyor’s operation. Understanding these components is essential for anyone involved in the selection, maintenance, or operation of drag belt conveyors.
- Drag Chain: The drag chain is the backbone of the conveyor. Made of durable materials like steel, it is designed to withstand the rigors of continuous operation and the abrasive nature of the materials being conveyed. The chain’s primary function is to pull the material along the conveyor path.
- Flights: Attached to the drag chain are flights, which are paddle-like structures that physically push or drag the material through the conveyor. The design and material of the flights are chosen based on the type of material being conveyed to ensure efficient movement and to minimize wear.
- Tubular or U-Shaped Troughs: Drag belt conveyors typically utilize either tubular or U-shaped troughs to contain the material being conveyed. Tubular troughs are completely enclosed, which helps in controlling dust and spillage, making them suitable for handling fine or hazardous materials. U-shaped troughs, on the other hand, are partially open and are often used for materials that are larger or more abrasive.
- Drive System: The drive system powers the conveyor, typically consisting of a motor, gearbox, and drive sprockets. This system must be powerful enough to move the loaded conveyor but also designed for energy efficiency.
- Tensioning System: To ensure the drag chain operates smoothly, a tensioning system is used to maintain the correct chain tension, preventing slack that could lead to operational issues or chain wear.
- Inlets and Outlets: Strategically placed along the conveyor, inlets and outlets facilitate the controlled feeding and discharge of materials. Their design is critical for maintaining the flow rate and preventing blockages.
- Control Systems: Modern drag belt conveyors often incorporate advanced control systems that allow for precise control of the conveyor’s speed and operation, enhancing efficiency and safety.
Each component of the drag belt conveyor is designed to work in harmony, ensuring minimal material degradation and maximum operational efficiency. Regular maintenance of these components is crucial for the longevity and effectiveness of the conveyor system.
Choosing the Right Drag Belt Conveyor Manufacturer
Selecting a Manufacturer for Your Drag Belt Conveyor Needs
Choosing the right manufacturer for a drag belt conveyor is crucial for ensuring you get a reliable, efficient, and durable system. Here are key factors to consider:
- Industry Experience: Look for manufacturers with extensive experience in your specific industry. They will have a better understanding of your unique needs and challenges.
- Product Quality: High-quality materials and construction are essential for a conveyor that will be durable and reliable. Check the manufacturer’s track record for product quality.
- Customization Capabilities: Each application may have specific requirements. A good manufacturer should be able to customize the conveyor to meet your specific needs.
- Customer Service: After-sales support is crucial. Choose a manufacturer that offers excellent customer service, including installation, maintenance, and repair services.
- Innovative Solutions: Manufacturers who invest in research and development can offer more advanced and efficient conveyor solutions.
Leading Drag Belt Conveyor Manufacturers
Several manufacturers stand out in the market for their quality drag belt conveyors:
- Company A: Known for their robust and durable conveyors, Company A offers a range of customizable options and has a strong focus on customer service.
- Company B: With a reputation for innovation, Company B offers state-of-the-art drag belt conveyors that are efficient and feature advanced control systems.
- Company C: Specializing in heavy-duty applications, Company C’s conveyors are known for their reliability and longevity, even in the toughest industrial environments.
- Company D: Offers a balance of quality and affordability, making their conveyors a popular choice for small to medium-sized businesses.
When choosing a manufacturer, consider visiting their facility, speaking to their existing customers, and comparing quotes and specifications from multiple suppliers. The right manufacturer will not only provide a high-quality conveyor but also become a valuable partner in your operational success.
Cost Considerations and Pricing of Drag Belt Conveyors
Factors Influencing the Price of Drag Belt Conveyors
When it comes to the pricing of drag belt conveyors, several factors come into play, each contributing to the final cost. Understanding these factors is crucial for anyone planning to invest in a drag belt conveyor system.
- Material Quality: The type of materials used in the construction of drag belt conveyors significantly affects the price. High-quality materials like reinforced steel or specialized alloys, which offer durability and longevity, tend to increase the cost.
- Size and Capacity: The size of the conveyor and its load capacity are directly proportional to its cost. Larger conveyors designed to handle heavier loads require more material and robust construction, leading to higher prices.
- Design Complexity: The complexity of the conveyor’s design also impacts the cost. Conveyors with intricate designs, specialized components, or customized features for specific applications will be more expensive than standard models.
- Additional Features: Features such as advanced control systems, integrated sensors, and safety mechanisms can add to the cost. While these features enhance efficiency and safety, they require additional technology and engineering, increasing the overall price.
Budgeting for a Drag Belt Conveyor System
When budgeting for a drag belt conveyor, it’s important to consider both the initial purchase price and the long-term operational costs. Here are some tips:
- Assess Your Needs: Clearly define what you need the conveyor to do. This will help in choosing a system that fits your requirements without paying for unnecessary features.
- Get Multiple Quotes: Obtain quotes from different suppliers to compare prices and specifications. This will help you find the best value for your investment.
- Consider Operational Costs: Factor in the costs of energy consumption, maintenance, and potential downtime. A cheaper conveyor might cost more in the long run if it’s less efficient or requires frequent repairs.
Long-Term Benefits of Investing in Quality
Investing in a high-quality drag belt conveyor system can bring several long-term benefits:
- Reduced Downtime: Quality conveyors are less likely to break down, ensuring consistent operation and reducing costly downtime.
- Lower Maintenance Costs: Durable materials and robust construction mean fewer repairs and lower maintenance costs over the conveyor’s lifespan.
- Increased Efficiency: High-quality conveyors often operate more efficiently, saving energy and time, and increasing overall productivity.
- Longer Lifespan: A well-built conveyor will last longer, providing a better return on investment over time.
Maintenance and Spare Parts for Drag Belt Conveyors
The Importance of Regular Maintenance
Regular maintenance is crucial for ensuring the longevity and consistent performance of drag belt conveyors. Proper maintenance helps in identifying and addressing potential issues before they lead to breakdowns, ensuring the conveyor operates efficiently and safely.
Key Maintenance Practices
- Regular Inspections: Conducting routine inspections can help identify wear and tear, misalignments, or other issues that might affect the conveyor’s performance.
- Lubrication: Regular lubrication of moving parts is essential to reduce friction and prevent wear.
- Cleaning: Keeping the conveyor clean from debris and dust can prevent damage and maintain efficiency.
- Record Keeping: Maintaining records of maintenance activities helps in tracking the conveyor’s condition and planning future maintenance work.
Sourcing Spare Parts
When it comes to sourcing spare parts for drag belt conveyors, it’s important to focus on quality to ensure the longevity and efficiency of the repairs.
- Identify Common Wear-and-Tear Components: Common components that may require replacement include chains, belts, bearings, and sprockets. Knowing these parts helps in keeping a stock of essential spares.
- Choose Quality Parts: Opt for parts from reputable manufacturers or suppliers to ensure they meet the necessary quality standards and are compatible with your conveyor system.
- Work with Trusted Suppliers: Establish relationships with trusted suppliers who can provide quality parts and advice on replacements.
- Consider Custom Parts: For unique or older conveyor systems, custom parts may be necessary. Work with suppliers who can fabricate or source these specialized components.
Regular maintenance and the use of quality spare parts are essential for the optimal performance and longevity of drag belt conveyors. By investing in these areas, businesses can ensure their conveyor systems continue to operate effectively, minimizing downtime and maximizing productivity.
Advanced Design Considerations and Customization of Drag Belt Conveyors
Tailoring Drag Belt Conveyors to Specific Needs
The design and customization of drag belt conveyors are critical factors that determine their efficiency and effectiveness in various industrial applications. Advanced design calculations and customization options allow these conveyors to meet specific operational requirements, adapting to unique material handling challenges.
Advanced Design Calculations
- Load and Capacity Assessment: Calculations begin with assessing the load capacity, considering the type and volume of materials to be handled. This determines the size, strength, and speed of the conveyor.
- Material Characteristics: Understanding the material characteristics, such as abrasiveness, corrosiveness, and bulk density, influences the choice of materials used in conveyor construction.
- Conveyor Path and Incline: The path and incline of the conveyor are designed based on the spatial constraints and material flow requirements, ensuring efficient movement of materials.
- Drive and Motor Specifications: The power requirements are calculated to determine the appropriate motor and drive specifications, ensuring sufficient power for continuous operation.
- Safety and Compliance: Design calculations also include safety factors and compliance with industry standards and regulations.
Customization Options
- Material of Construction: Options like stainless steel, hardened alloys, or coated materials cater to different operational environments.
- Conveyor Length and Width: Customizable dimensions to fit specific spatial requirements and material volumes.
- Flight Design: Tailored flight designs for optimal material handling, whether for fine powders or large lumps.
- Control Systems: Integration of advanced control systems for automated operations and real-time monitoring.
Case Studies: Custom-Designed Drag Belt Conveyors
- Mining Industry: A custom-designed drag belt conveyor was implemented in a mining operation to handle abrasive materials. The conveyor was built with reinforced materials and a specialized flight design to withstand the harsh environment, resulting in increased efficiency and reduced maintenance costs.
- Agricultural Sector: In a grain handling facility, a drag belt conveyor was customized with a dust-tight enclosure and gentle handling design to prevent grain damage and loss, significantly improving the facility’s operational efficiency.
- Chemical Processing Plant: A chemical plant required a corrosion-resistant conveyor for handling aggressive materials. A drag belt conveyor with specialized coatings and materials was designed, ensuring safe and efficient material transport.
These case studies demonstrate how custom-designed drag belt conveyors can effectively address unique challenges, enhancing operational efficiency and productivity.
Need a custom quote for your Drag Belt Conveyors ? Submit your details today.
Making an Informed Purchase: Drag Belt Conveyor for Sale
Guidelines for Purchasing a Drag Belt Conveyor
When considering the purchase of a drag belt conveyor, whether new or used, it’s crucial to make an informed decision that aligns with your operational needs. Here’s a comprehensive guide to help you through the process.
Evaluating a Used Drag Belt Conveyor
- Condition Assessment: Examine the overall condition of the conveyor, looking for signs of wear, corrosion, or damage.
- Operational History: Inquire about the conveyor’s operational history, including usage duration, maintenance records, and any repairs or modifications.
- Compatibility with Materials: Ensure the conveyor is suitable for the type of materials you plan to handle, considering factors like abrasiveness, temperature, and corrosiveness.
- Capacity and Throughput: Verify that the conveyor’s capacity aligns with your material handling requirements.
Checklist for Evaluating a Drag Belt Conveyor
- Structural Integrity: Check the frame, chain, flights, and trough for structural soundness.
- Motor and Drive System: Assess the condition and performance of the motor and drive system.
- Safety Features: Ensure that all safety features are intact and functional.
- Ease of Maintenance: Consider the ease of accessing and replacing wear parts.
- Manufacturer Reputation: Research the manufacturer’s reputation for quality and reliability.
- Warranty and Support: Inquire about any remaining warranty and the availability of after-sales support.
- Compliance with Standards: Confirm that the conveyor meets relevant industry standards and regulations.
- Cost-Benefit Analysis: Weigh the cost of the conveyor against the benefits and savings it offers.
- Future Expansion: Consider if the conveyor can be adapted or expanded for future operational changes.
- Test Run: If possible, conduct a test run to observe the conveyor in operation.
By thoroughly evaluating these aspects, you can ensure that the drag belt conveyor you purchase will meet your operational needs and provide a reliable solution for your material handling requirements.
FAQs about Drag Belt Conveyor
A drag conveyor, also known as a drag chain conveyor, is a type of conveyor system used for moving bulk materials. It consists of a chain or multiple chains with attached paddles or flights that drag material through a trough or enclosed tube. This design is particularly effective for moving materials horizontally or at a slight incline. Drag conveyors are commonly used in industries like agriculture, mining, chemical processing, and manufacturing.
Drag chain conveyors and belt conveyors are both used for transporting materials, but they have distinct mechanisms and are suitable for different types of material handling requirements.
Drag Chain Conveyor:
Mechanism: Utilizes a chain or chains with attached paddles or flights to drag material through a trough or tube.
Material Handling: Ideal for moving granular, lumpy, or sticky materials, and is often used for materials that are abrasive or hot.
Enclosed System: Typically operates within an enclosed space, which is beneficial for controlling dust and spillage.
Maintenance: Generally requires less maintenance and is more durable, especially for handling abrasive materials.
Belt Conveyor:
Mechanism: Uses a continuous belt looped over pulleys to transport materials.
Material Handling: Suitable for a wide range of materials, including boxes, bags, or loose materials like sand or gravel.
Open System: Often operates in an open environment, though enclosed belt conveyors are also available.
Maintenance: Can require more maintenance, especially in the case of belt wear and tear or alignment issues.
There are various types of conveyors used in different industries, but three common types include:
Belt Conveyors: These are the most common type of conveyor and consist of a continuous belt looped over pulleys. They are used for transporting materials over a flat or inclined path and are suitable for a wide range of materials, from packaged goods to bulk solids.
Roller Conveyors: These conveyors use a series of rollers to move goods. They can be powered or gravity-driven and are ideal for handling items with a flat bottom, like boxes or pallets. Roller conveyors are commonly used in warehousing and logistics.
Chain Conveyors: These use a chain or multiple chains to move pallets or other large, heavy items. They are particularly useful in heavy-duty applications where robust material handling is required.
Drag conveyor chains, essential components of drag conveyors, come in various types, each designed for specific material handling requirements. Three common types include:
Standard Drag Chain: This is the most basic type of drag chain, consisting of a series of metal links connected in a chain. It is suitable for general material handling applications and is commonly used for moving granular or lumpy materials.
Forged Chain: Forged chains are made from heat-treated alloy steel, making them stronger and more durable than standard chains. They are ideal for heavy-duty applications where the conveyor must handle high loads or abrasive materials.
Drop Forged Chain: This type of chain is known for its high strength and durability. It is manufactured through a process of drop forging, which increases its resistance to wear and tear. Drop forged chains are used in demanding applications, such as in industries handling minerals, chemicals, or other abrasive materials.
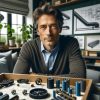
Jordan Smith, a seasoned professional with over 20 years of experience in the conveyor system industry. Jordan’s expertise lies in providing comprehensive solutions for conveyor rollers, belts, and accessories, catering to a wide range of industrial needs. From initial design and configuration to installation and meticulous troubleshooting, Jordan is adept at handling all aspects of conveyor system management. Whether you’re looking to upgrade your production line with efficient conveyor belts, require custom conveyor rollers for specific operations, or need expert advice on selecting the right conveyor accessories for your facility, Jordan is your reliable consultant. For any inquiries or assistance with conveyor system optimization, Jordan is available to share his wealth of knowledge and experience. Feel free to reach out at any time for professional guidance on all matters related to conveyor rollers, belts, and accessories.