Top Factors Affecting Conveyor Belt Rubber Quality
The performance and longevity of conveyor belts heavily depend on the conveyor belt rubber quality. High-quality rubber ensures not only the durability but also the efficiency of conveyor systems across various industries, from mining to packaging. Using the right rubber material can significantly reduce the maintenance frequency and operational costs, as it is better suited to withstand abrasion, heat, and other environmental stresses. This introduction delves into the critical role of rubber quality in optimizing conveyor belt operations, highlighting how premium materials can lead to enhanced system reliability and productivity.
Assessing Conveyor Belt Rubber Quality: Types and Specifications
Types of Rubber Used in Conveyor Belts
The selection of rubber material plays a pivotal role in the performance and durability of conveyor belts. There are primarily two types of rubber used: natural and synthetic. Natural rubber is valued for its elasticity and tensile strength, making it ideal for conveyor belts that require flexibility and durability under strain. On the other hand, synthetic rubbers such as styrene-butadiene rubber (SBR) and polyurethane are chosen for their abrasion resistance and ability to withstand chemicals and oils. Each type of rubber is suited for different industrial environments, and the conveyor belt rubber quality directly impacts the belt’s ability to perform in specific settings. For example, belts in recycling plants often use SBR for its resistance to wear and tear, whereas food processing belts may use FDA-approved rubber materials that are safe for contact with food.
Standard Specifications for Conveyor Belts
Understanding the specification standards is crucial for ensuring the conveyor belt rubber quality meets the operational demands of different industries. These specifications are outlined by various standards organizations, such as the International Organization for Standardization (ISO) and the Rubber Manufacturers Association (RMA). ISO standards, for instance, specify the minimum requirements for tensile strength, elongation, and wear resistance, which are critical for determining the quality and suitability of rubber conveyor belts in different applications. Similarly, the RMA has developed grading systems like RMA Grade I and II, which define levels of quality based on the rubber’s resistance to abrasion. These standards help manufacturers and end-users select the appropriate quality of rubber that not only enhances the efficiency of their conveyor systems but also extends the lifespan of the belts under different operational stresses.
Enhancing Performance with High Conveyor Belt Rubber Quality: Heat Resistant Conveyor Belts
Specifications for Heat Resistance
Heat resistant conveyor belts are designed to withstand elevated temperatures, which is crucial in industries like metalworking, cement manufacturing, and glass production. The specification of these belts focuses on their ability to maintain integrity and functionality at high temperatures. These specifications include the maximum operating temperature the rubber can withstand without degrading, which often ranges from 150°C to 200°C. The conveyor belt rubber quality is assessed based on its thermal stability and its resistance to cracking, hardening, or swelling. High-quality heat resistant rubber compounds, such as ethylene propylene diene monomer (EPDM) or chlorobutyl rubber, are specifically engineered to reduce heat-induced aging, thereby prolonging the life of the belt under severe thermal conditions.
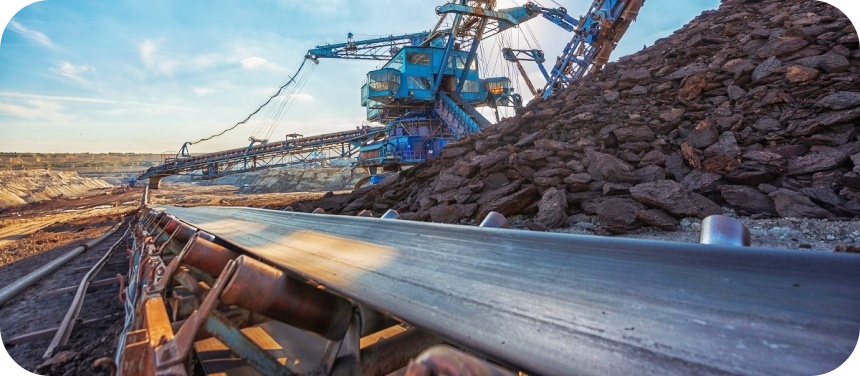
Material and Composition
The materials used for heat resistant conveyor belts include a blend of rubber compounds that have been specifically formulated to resist the effects of high temperatures. These materials are chosen based on their thermal, chemical, and mechanical properties. For instance, EPDM is favored for its excellent heat resistance and aging properties, while silicon rubber is selected for operations requiring even higher temperature thresholds. The conveyor belt rubber quality in these belts is critical because it must not only resist heat but also maintain flexibility and mechanical strength at elevated temperatures. These materials are often reinforced with fibers or other composites to enhance their structural integrity and reduce elongation at high temperatures. Understanding the composition and engineering behind these rubber materials helps in selecting the right belt for specific high-heat applications, ensuring both safety and efficiency in operations.
Conveyor Belt Testing Standards and Conveyor Belt Rubber Quality
Testing standards for conveyor belts are crucial to ensuring the safety, performance, and durability of these essential components in various industrial applications. Such standards are designed to rigorously assess the quality of the conveyor belt rubber, a key material in the manufacturing of these belts.
Importance of Conveyor Belt Testing Standards
Conveyor belt testing standards are vital for maintaining high conveyor belt rubber quality. These standards help determine the physical, chemical, and mechanical properties of the rubber used in the belts. By adhering to these standards, manufacturers can ensure that the conveyor belts are capable of withstanding the harsh conditions they are subjected to in industrial environments. This includes resistance to abrasion, extreme temperatures, and potentially corrosive chemicals.
The primary purpose of these testing standards is to prevent failures that could lead to costly downtime and, more importantly, safety hazards. Regular testing and compliance with established standards ensure that the conveyor belts are safe for continuous operation, reducing the risk of accidents that could endanger workers.
Key Testing Methods
Several key testing methods are used to evaluate conveyor belt rubber quality. These include:
- Tensile Strength Test: This test measures the force required to break a rubber sample and helps determine the strength and stretchability of the belt.
- Abrasion Resistance Test: It evaluates how well the rubber can withstand surface wear caused by friction.
- Ageing Test: This test involves exposing the rubber to various environmental factors such as heat, oxygen, and ozone to assess how it ages under different conditions.
- Chemical Resistance Test: Determines the resilience of rubber against chemicals that could potentially degrade its material properties.
Compliance and Certification
To ensure high conveyor belt rubber quality, manufacturers must comply with international standards such as ISO 14890, which specifies requirements for rubber or plastics-covered conveyor belting of textile construction for general use. Another important standard is the ASTM D378, which focuses on rubber belting and its ability to resist the deteriorating effects of ozone and ultraviolet light.
Manufacturers that adhere to these testing standards are often eligible for certifications that can enhance their marketability and assure customers of the product’s reliability and safety. Compliance not only reflects on the quality and integrity of the conveyor belts but also on the company’s commitment to safety and durability.
By implementing rigorous conveyor belt testing standards, the industry can assure that the products used are of the highest quality, which is essential for the safety and efficiency of operations in various sectors such as mining, manufacturing, and transportation. This adherence to high-quality standards in conveyor belt rubber quality not only enhances the operational efficiency but also significantly reduces maintenance costs and downtime.
Interested in our conveyor belts? Complete the inquiry form, and we’ll provide detailed information tailored to your needs.
Conveyor Belt Rubber Quality and Conveyor Belt Performance
The performance of conveyor belts in various industries largely hinges on the rubber quality used in their construction. Good quality rubber ensures that conveyor belts can handle the demanding tasks they are designed for, while also extending their operational life.
Impact of Conveyor Belt Rubber Quality on Belt Durability
The durability of a conveyor belt is critically dependent on the quality of the rubber it is made from. High-quality rubber helps in maintaining the structural integrity of the conveyor belt under varying operational stresses including weight, tension, and environmental exposure.
High-Quality Rubber and Conveyor Belt Longevity
Using high-grade rubber in conveyor belts can significantly extend their lifespan. Quality rubber materials are engineered to be more resistant to wear and tear, abrasion, and degradation from oils and chemicals. This resistance is crucial in harsh industrial environments where belts are exposed to strenuous conditions.
Case Studies Demonstrating Benefits of Superior Rubber Quality
- Mining Industry: In a case study of a mining company, belts made from high-quality rubber demonstrated a 30% increase in service life compared to standard belts, reducing both downtime and maintenance costs.
- Manufacturing Sector: A conveyor system used in a car manufacturing plant was switched to high-quality rubber belts, which resulted in a 25% reduction in belt replacement frequency.
- Food Processing: Belts with superior rubber quality used in a food processing plant showed less wear from acidic and oily substances, leading to improved hygiene and reduced contamination risks.
- Packaging Industry: A packaging facility reported fewer operational interruptions after upgrading to high-quality rubber conveyor belts, citing enhanced resistance to mechanical damage.
- Recycling Operations: Enhanced rubber quality in belts used for recycling operations contributed to better handling of sharp and abrasive materials, thereby extending the equipment’s operational life.
- Airport Logistics: High-quality rubber belts used in airport baggage handling systems offered improved performance under continuous operation, showcasing significant resilience to the heavy loads and constant motion.
Challenges in Conveyor Belt Rubber Quality Assurance
Ensuring consistent quality of the rubber used in conveyor belts presents several challenges, which manufacturers must address to maintain performance and reliability.
Common Issues in Maintaining Consistent Rubber Quality
- Variability in Raw Material Supply: The quality of natural and synthetic rubber can vary significantly, affecting the final product.
- Production Process Inconsistencies: Small deviations in the manufacturing process can lead to significant differences in the quality of the rubber.
- Aging and Environmental Factors: Rubber can degrade over time due to exposure to heat, light, and oxygen, which can alter its properties even before use.
- Chemical Contamination: During processing, contamination from other materials can affect the rubber’s properties.
- Storage Conditions: Improper storage conditions can accelerate the degradation of rubber quality.
- Technical Skills: The lack of skilled workforce can lead to errors in the mixing and curing processes, crucial for achieving desired rubber properties.
- Quality Control Measures: Inadequate quality control can miss detecting flaws in rubber quality.
- Economic Pressures: Financial constraints might lead manufacturers to opt for cheaper, lower-quality materials.
Strategies to Overcome Rubber Quality Challenges
- Tightened Supply Chain Management: Implementing rigorous checks and balances on the supply chain to ensure high-quality raw materials.
- Advanced Manufacturing Techniques: Employing state-of-the-art manufacturing technologies to maintain consistency.
- Regular Quality Testing: Implementing comprehensive testing regimes to assess rubber quality at every stage of production.
- Environmental Control: Maintaining controlled environments in both manufacturing and storage to preserve rubber integrity.
- Training Programs: Investing in continuous training for employees to enhance their technical capabilities.
- Investment in R&D: Developing new rubber compounds that are more resistant to environmental and operational stresses.
- Partnering with Reputable Suppliers: Collaborating only with suppliers who adhere to high standards of quality.
- Implementing Lean Manufacturing Principles: To reduce waste and variability in the production process.
By focusing on these aspects of conveyor belt rubber quality, manufacturers can not only ensure the production of high-quality belts but also enhance their reputation in a competitive market, fostering trust and reliability among users.
Specification Sheets and Purchasing Tips for Conveyor Belt Rubber Quality
Understanding specification sheets and following informed purchasing tips are fundamental for acquiring conveyor belts with the highest rubber quality. These documents and practices ensure that the selected belts meet the necessary operational standards and durability requirements.
Reading a Belt Conveyor Specification Sheet
Interpreting a conveyor belt specification sheet accurately is crucial to ensure that the belt selected will meet the requirements of the application while maintaining optimal conveyor belt rubber quality.
Guide to Interpreting a Conveyor Belt Specification Sheet
- Material Specifications: Identify the type of rubber material used and its suitability for different environmental conditions such as temperature and chemical exposure.
- Tensile Strength: Check the tensile strength rating, which indicates the maximum load that the belt can handle.
- Elongation: Understand the elongation properties, which show how much the belt can stretch without losing its original shape.
- Abrasion Resistance: Look for the abrasion resistance level, critical for determining how well the belt withstands surface wear.
- Chemical Resistance: Assess the chemical resistance capabilities to ensure the belt will not degrade in environments where chemicals are present.
- Temperature Tolerance: Evaluate the temperature range the rubber can withstand without losing its integrity.
- Load Capacity: Note the maximum load capacity to ensure the belt can handle the intended weight without failure.
- Belt Thickness and Width: These dimensions are vital for matching the belt to the conveyor system and its operational demands.
Key Metrics and Features to Consider
- Flexibility and Bend Radius: These factors are important for systems that require the belt to bend around tight corners.
- Speed: The belt’s operating speed should match the conveyor system’s requirements without risking premature wear.
- Joining Method: Understanding the belt’s joining mechanism, such as vulcanized joints versus mechanical fasteners, can affect installation and maintenance.
- Lifespan and Warranty: Consider the expected lifespan and warranty conditions, which reflect the manufacturer’s confidence in their product.
Recommendations for Purchasing High-Quality Rubber Conveyor Belts
Selecting the right conveyor belt involves more than just understanding specification sheets; it requires a strategic approach to match the belt’s properties with the application’s specific needs.
Tips on Selecting the Right Rubber Conveyor Belt
- Assess Application Needs: Define what the primary use of the conveyor belt will be and the specific demands of the environment, including load type and size.
- Material Quality: Opt for belts made from high-quality rubber to ensure durability and resistance to environmental factors.
- Manufacturer Reputation: Choose products from manufacturers with strong reputations for producing high-quality conveyor belts.
- Customization Options: Consider if the conveyor belt needs customization options like coatings or cleats for specific applications.
- Cost vs. Benefit: Analyze the cost-effectiveness of the belt by considering its operational benefits over its lifespan.
- Certification and Standards: Look for belts that comply with international standards like ISO or ASTM to ensure they meet global quality benchmarks.
- Supplier Reliability: Evaluate the reliability of the supplier in terms of product availability, delivery, and customer support.
- After-Sales Service: Ensure that the manufacturer or supplier offers excellent after-sales service, including technical support and warranty.
- Sustainability: Consider the environmental impact of the manufacturing and disposal of the conveyor belt.
Consulting with Experts
- Expert Advice: Engage with industry experts or engineers to help match your specific operational requirements with the most suitable conveyor belt options.
- Technical Evaluations: Consider having potential belts tested under conditions that mirror your operational environment to ensure they will perform as needed.
Through careful evaluation of specification sheets and strategic purchasing decisions, businesses can ensure they invest in conveyor belts that offer superior performance and long-term reliability, all while maintaining excellent conveyor belt rubber quality.
FAQs about Conveyor Belt Rubber Quality
Rubber conveyor belts are designed with various specifications to meet the wide range of application needs in industries. The key specifications include belt width, thickness, length, and rubber grade. Belt width usually ranges from 400mm to over 2000mm, depending not only on the conveyor system’s size but also on the bulk material it carries. Thickness varies, often from 8mm to 20mm, based on the material type and usage intensity. Length is customized according to the installation requirements. Additionally, the belts are reinforced with materials like nylon, polyester, or steel to enhance strength and durability. The choice of specifications directly impacts the belt’s performance, supporting the effective, efficient movement of goods across varying distances and environments. Identifying the right specifications is crucial, requiring an understanding of the operational context, including the type of materials transported, conveyor speed, environmental conditions, and load size.
The composition of rubber in conveyor belts is crucial for determining their performance characteristics and longevity. Typically, the rubber material in conveyor belts is a compound mixture that includes natural rubber (NR), styrene-butadiene rubber (SBR), or nitrile rubber (NBR) as the primary elastomers. These are combined with carbon black, sulfur, and other chemical accelerators in the vulcanization process to enhance the material’s desired properties. For instance, natural rubber provides high tensile strength and elasticity, making it suitable for heavy-duty tasks. SBR is valued for its abrasion resistance and is often used in the handling of abrasive materials. NBR, on the other hand, offers excellent resistance to oils and chemicals, making it ideal for industrial applications where oils are present. The specific composition mix can vary, aiming to achieve the optimal balance between durability, flexibility, heat resistance, and the capability to handle various environmental stressors.
The primary distinction between Grade 1 and Grade 2 conveyor belts lies in their durability and resistance to abrasions, cut, and gouge. Grade 1 conveyor belts are designed for superior performance, offering higher resistance to cuts and gouges, making them suitable for conveying sharp, heavy materials that could damage the belt surface. They generally have a higher tensile strength and better elongation properties, which translates to enhanced durability and a longer lifespan, particularly in severe service conditions. Grade 2 belts, while still robust and capable of handling bulk materials efficiently, are tailored for applications with a moderate impact on the belt’s surface. They are more suited to transporting non-sharp materials and are favored for their cost-effectiveness in less demanding environments. The choice between the two grades largely depends on the operational requirements, material characteristics, and the specific challenges of the application area.
The specification of a conveyor belt refers to a comprehensive set of characteristics designed to match the demands of the application it serves. These specifications include the belt’s physical dimensions (length, width, thickness), material composition, strength rating (tensile strength), reinforcement type (such as fabric, steel cord), and cover properties (abrasion resistance, chemical resistance, heat resistance). Additionally, the specifications may include the belt’s grade, which is an indication of its quality and capability to withstand different operational challenges like abrasive materials, oils, and impact. Proper specification is critical for ensuring that the conveyor belt performs efficiently and reliably, minimizing downtime and maintenance costs. It requires a deep understanding of the material handling process, including the types of materials transported, environmental conditions, and the mechanical demands on the conveyor system.
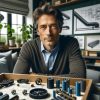
Jordan Smith, a seasoned professional with over 20 years of experience in the conveyor system industry. Jordan’s expertise lies in providing comprehensive solutions for conveyor rollers, belts, and accessories, catering to a wide range of industrial needs. From initial design and configuration to installation and meticulous troubleshooting, Jordan is adept at handling all aspects of conveyor system management. Whether you’re looking to upgrade your production line with efficient conveyor belts, require custom conveyor rollers for specific operations, or need expert advice on selecting the right conveyor accessories for your facility, Jordan is your reliable consultant. For any inquiries or assistance with conveyor system optimization, Jordan is available to share his wealth of knowledge and experience. Feel free to reach out at any time for professional guidance on all matters related to conveyor rollers, belts, and accessories.