Integrating Metal Detector Belt Conveyor Systems in Production
In the intricate dance of modern industry, the metal detector belt conveyor system plays a pivotal role, ensuring the seamless blend of safety and efficiency across countless production lines. This sophisticated machinery combines the relentless motion of conveyor belts with the precision of metal detection, creating an indispensable tool for industries ranging from food processing to pharmaceuticals and beyond. The aim of this post is not only to demystify the underlying mechanics of these systems but also to traverse the vast landscape of their applications and the myriad options available in the market. As we delve into the world of belt conveyor metal detectors, we uncover the layers of technology and innovation that safeguard the integrity of products and processes, reinforcing the bedrock of industrial reliability and consumer trust.
What are Metal Detector Belt Conveyor Systems
The metal detector on conveyor belt stands as a cornerstone in the realm of industrial safety and efficiency, marrying the relentless functionality of conveyor belts with the precision of metal detection technology. This section aims to unravel the layers of this sophisticated system, shedding light on its operational essence, the integral components that constitute its framework, and the remarkable adaptability it offers to cater to a myriad of industrial applications.
At its core, the working principle of a metal detector belt conveyor system revolves around the detection of metallic contaminants within products as they traverse the conveyor belt. This system employs a highly sensitive metal detector that creates an electromagnetic field. As products pass through this field, any metallic elements within them alter the field’s frequency. This disturbance is promptly detected, triggering a response mechanism—often a halt in conveyor movement or an automatic rejection of the contaminated product—thereby ensuring the integrity of the production line.
Delving into the components, a metal detector belt conveyor system is comprised of two main elements: the metal detector itself and the conveyor belt mechanism. The metal detector, often housed in a rectangular or tunnel-like aperture, encompasses coils that generate the electromagnetic field. The conveyor belt, typically fabricated from materials that do not interfere with metal detection, such as PVC or polyurethane, moves products through the detector’s aperture. This belt is supported by rollers and powered by a motor, ensuring a steady and controlled product flow through the detection zone.
The hallmark of these systems lies in their customizability and versatility, accommodating the diverse needs of various industries. Drawing from the approach of companies like CASSEL Inspection, which specializes in crafting tailor-made metal detection solutions, it becomes evident how these systems can be fine-tuned. Factors such as the sensitivity of the detection system can be adjusted based on the specific types of metals that need to be identified, and the size of the aperture can be modified to accommodate products of varying dimensions. Furthermore, the speed of the conveyor belt can be calibrated to match the pace of existing production lines, ensuring seamless integration.
This adaptability extends to the systems’ rejection mechanisms, which can be customized to handle contaminated products in a manner that suits the operational workflow, be it through stop-and-alarm, air blast, or diverting arms. Such bespoke solutions underscore the capability of belt conveyor metal detectors to meld into the unique fabric of different production environments, from the high-speed demands of the food industry to the precision-critical realm of pharmaceutical manufacturing.
The metal detector belt conveyor system embodies a synergy of technology and flexibility, providing a robust solution for safeguarding product quality and enhancing operational efficiency across a broad spectrum of industries.
Applications Across Industries with Metal Detector Belt Conveyor Systems
The versatility of the metal detector belt conveyor system is showcased through its critical applications across a spectrum of industries. Each sector leverages these systems to meet unique challenges, from ensuring product purity to adhering to stringent safety standards.
Key Industries and Specific Applications
Here, we explore seven key industries and specific applications where these systems play an indispensable role.
- Food Processing: In this industry, the metal detector on conveyor belt is paramount for detecting metal contaminants in products ranging from bakery goods to meats and dairy. The system ensures that items like broken machinery parts or lost processing tools don’t compromise food safety, thereby maintaining compliance with health regulations and protecting consumer well-being.
- Pharmaceuticals: Precision is paramount in pharmaceutical manufacturing, where even the smallest metal particle can have significant consequences. Metal detector belt conveyor systems are employed to scrutinize pills, capsules, and powders, ensuring that the final products are free from metallic contaminants, thus safeguarding patient health and upholding industry standards.
- Textiles: The textile industry uses these systems to detect metal objects that could have been inadvertently sewn into garments or textiles during production. This not only prevents potential injury to consumers but also protects sewing and weaving machinery from damage.
- Mining: In the mining sector, belt conveyor metal detectors are utilized to identify and segregate metallic ores from non-valuable rocks and minerals. This application not only streamlines the extraction process but also enhances the efficiency and profitability of mining operations.
- Recycling: Recycling facilities rely on these systems to separate metal items from other materials, ensuring the purity of recycled batches and preventing damage to processing equipment. This application is crucial for both environmental sustainability and operational efficiency.
- Packaging: In packaging industries, ensuring that products are free from metal contamination before they are sealed is vital. Metal detector belt conveyor systems check packaged goods for any metallic foreign bodies, ensuring product integrity and compliance with safety standards.
- Consumer Goods Manufacturing: From toys to electronics, ensuring products are free of metal contaminants is crucial for consumer safety and product quality. These systems detect any unintended metal parts or fragments that could pose risks to end-users.
Specific Applications
Specific applications in these industries highlight the adaptability of metal detector belt conveyor systems:
- In food processing, these systems can be tailored to detect specific types of metals, including ferrous, non-ferrous, and stainless steel, in various food products.
- In pharmaceuticals, they ensure that highly sensitive products are inspected at high speeds without compromising the detection accuracy.
- In the textile industry, they help in protecting delicate machinery and ensuring product quality by detecting even the smallest metal contaminants.
- In mining, these systems are engineered to operate in harsh environments, distinguishing valuable metallic ores from other materials.
- In recycling, they play a critical role in the sorting process, contributing to more efficient recycling streams.
- In packaging, they ensure that the final stage of production is secure, checking sealed packages for any form of metal contamination.
- In consumer goods manufacturing, they provide an essential quality control step, ensuring that products are safe and meet regulatory standards.
Through these diverse applications, metal detector belt conveyor systems demonstrate their indispensable value across industries, ensuring safety, quality, and efficiency in production processes.
Choosing the Best Metal Detector Belt Conveyor System for Your Needs
Selecting the ideal belt conveyor metal detector for your operational needs involves a comprehensive evaluation of various factors to ensure efficiency, compatibility, and cost-effectiveness. This section delves into the crucial aspects to consider, ensuring you make an informed decision tailored to your specific requirements.
Sensitivity and Detection Capabilities
The sensitivity of a metal detector belt conveyor system is paramount. It determines the smallest size of metal contaminants that can be detected. Consider systems that offer high sensitivity and the ability to detect various metal types, including ferrous, non-ferrous, and stainless steel, which are commonly found in processing environments.
System Size and Scalability
The physical dimensions of the metal detector on conveyor belt should align with your existing production line. Evaluate the total length, width, and height to ensure it fits seamlessly into your space. Additionally, consider the scalability of the system to accommodate future expansion or modifications to your product range.
Throughput and Speed
Assess the system’s capacity to handle your expected throughput. High-speed operations require a metal detector belt conveyor system capable of maintaining accuracy at increased velocities, ensuring no compromise on detection capabilities.
Product and Packaging Adaptability
Your chosen system should be versatile enough to handle a wide range of products and packaging types. This adaptability is crucial for businesses that deal with multiple products, as it ensures the system remains effective across various items without the need for constant recalibration.
Integration with Existing Lines
The ability of the metal detector on conveyor belt to integrate with existing production lines is critical. Look for systems that offer compatibility with your current setup, including software integration, to facilitate a seamless inclusion into your operational flow.
Regulatory Compliance
Ensure the metal detector belt conveyor system meets the relevant industry standards and regulations. This compliance is essential for maintaining product safety and quality, as well as for avoiding potential legal issues.
Maintenance and Support
Consider the maintenance requirements and the availability of support services for the metal detector on conveyor belt. Opt for solutions that offer easy access to parts, straightforward maintenance procedures, and reliable customer support to mitigate downtime.
Cost-Efficiency
While the initial investment is an important consideration, also evaluate the long-term cost-efficiency of the system. This includes maintenance costs, energy consumption, and the potential reduction in waste and product recalls due to improved detection rates.
Selecting the right metal detector belt conveyor system necessitates a careful analysis of these factors. It’s not just about the immediate needs but also about future-proofing your production line for adaptability, efficiency, and compliance. Taking the time to thoroughly evaluate these aspects will ensure that your investment enhances your operational capabilities and contributes to the overall success of your business.
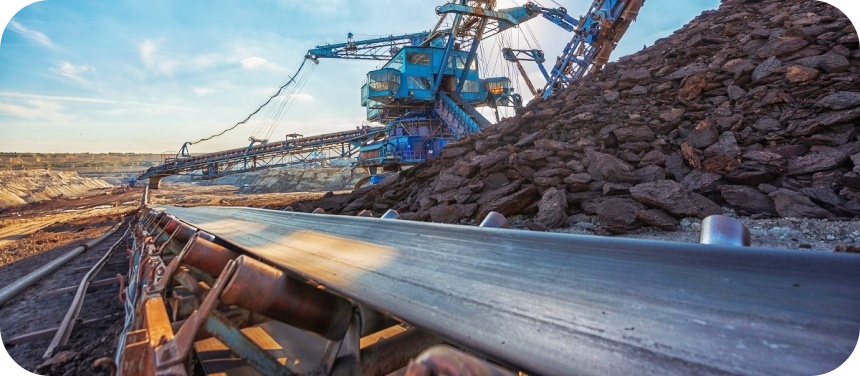
Cost Considerations for Metal Detector Belt Conveyor Systems
When evaluating the investment in a metal detector belt conveyor system, understanding the myriad of cost considerations is crucial. These considerations not only encompass the initial purchase price but also the broader implications on operational efficiency and long-term financial health. Below, we explore the factors that influence the pricing of these systems and the long-term benefits of choosing a high-quality setup.
Influencing Factors on Pricing
- Advanced Detection Technologies: The sophistication of the technology employed significantly impacts cost. Systems utilizing cutting-edge detection algorithms and multi-frequency scanning capabilities tend to command higher prices due to their enhanced sensitivity and accuracy.
- System Size and Configuration: The dimensions and layout of a metal detector belt conveyor system play a pivotal role in determining its price. Larger systems designed for high-volume production lines are generally more expensive due to the increased material and manufacturing requirements.
- Customization and Integration: Custom features tailored to specific production needs, such as reject systems, product guides, and integration with existing manufacturing lines, can elevate the system’s cost due to the additional engineering and fabrication involved.
- Material and Build Quality: The choice of materials, such as stainless steel for corrosion resistance and hygiene in food processing, influences the price. Higher quality materials and construction translate to increased durability but at a higher cost.
- Compliance and Certification: Systems designed to meet specific industry standards and certifications, such as those required for food safety or pharmaceutical applications, can be more expensive due to the rigorous testing and quality control measures necessary.
- Sensitivity and Detection Range: The ability to detect a wide range of metal contaminants, including non-ferrous and stainless steel, with high sensitivity typically results in a higher price point due to the advanced technology required.
- Operational Speed and Efficiency: Systems capable of maintaining high detection accuracy at elevated operational speeds often command a premium. This capability is essential for maintaining productivity in fast-paced production environments.
- Software and Connectivity Features: Advanced software features for data logging, system monitoring, and remote diagnostics add value to the system but also contribute to the cost. Connectivity options for integration into broader production management systems can also be a factor.
- After-sales Support and Warranty: Comprehensive after-sales support, including training, maintenance services, and extended warranty options, can influence the overall investment in a metal detector belt conveyor system.
- Brand and Manufacturer Reputation: Established brands known for quality and reliability may offer their systems at a premium, reflecting the perceived value and trust in their products.
Long-Term Benefits of a High-Quality System
- Reduced Product Waste: By accurately detecting and rejecting contaminated products, high-quality systems minimize waste, translating to significant cost savings over time.
- Compliance with Industry Regulations: Investing in a system that meets regulatory standards helps avoid costly fines and recalls, protecting your bottom line.
- Protection of Brand Reputation: Ensuring product safety and quality safeguards your brand’s reputation, crucial for maintaining customer trust and loyalty.
- Operational Efficiency: Advanced systems integrate seamlessly with existing lines, enhancing productivity and reducing downtime due to false rejects or maintenance needs.
- Scalability: High-quality systems are designed with scalability in mind, allowing for future expansion or adaptation to new products without necessitating a complete system overhaul.
- Long-Term Reliability: Durable materials and construction ensure the system withstands the rigors of continuous operation, reducing the need for frequent repairs or replacements.
While the initial cost of a metal detector belt conveyor system can be significant, understanding the factors that influence pricing and recognizing the long-term financial benefits of a quality investment is crucial. A well-chosen system not only enhances operational efficiency and product safety but also contributes to sustained financial health through compliance, waste reduction, and brand protection.
DIY vs. Professional Solutions for Metal Detector Belt Conveyor Systems
In the realm of metal detection within industrial settings, stakeholders often deliberate between constructing a DIY metal detector belt conveyor system and investing in a professional, custom-made solution. This decision is pivotal, as it affects not just the immediate functionality of the production line but also its long-term reliability and efficiency. Below, we dissect the advantages and disadvantages of each approach, emphasizing the critical factors such as reliability, efficiency, and support services.
Pros of DIY Metal Detector Belt Conveyor Systems:
- Cost Savings: Initial costs can be lower with DIY solutions, as you can potentially save on labor and some materials, making it an attractive option for budget-conscious operations.
- Customization: Building your own system allows for tailored adjustments to fit specific needs or constraints within your production environment that off-the-shelf solutions might not accommodate.
- Hands-On Control: DIY projects offer complete control over every aspect of the system, from design to implementation, allowing for a deeper understanding of its operation and maintenance.
- Flexibility in Design and Materials: You have the liberty to choose from a wider range of materials and components that may better suit your specific application or budgetary constraints.
- Learning Opportunity: The process of designing and constructing a DIY system can provide valuable insights and knowledge about the inner workings and troubleshooting of metal detection systems.
Cons of DIY Metal Detector Belt Conveyor Systems:
- Time and Resource Intensive: Designing and building a system from scratch requires a significant investment of time and resources, which can detract from other critical business operations.
- Reliability Concerns: Without the expertise and precision of professional manufacturers, DIY systems may lack in reliability, potentially leading to higher rates of false positives/negatives and system failures.
- Lack of Support: DIY systems do not come with professional support services, leaving you to deal with any issues or breakdowns without expert assistance.
- Compliance Risks: Ensuring that a DIY system meets all industry regulations and standards can be challenging, risking non-compliance and associated penalties.
- Efficiency Doubts: Professional systems are designed for optimal efficiency and integration into production lines. A DIY system might not achieve the same level of seamless operation, potentially affecting overall productivity.
Professional Metal Detector Belt Conveyor Systems:
Investing in a professional solution offers several advantages that are crucial for industrial applications:
- Reliability: Professional systems are engineered and tested to meet high standards of reliability, ensuring consistent operation and detection accuracy.
- Efficiency: These systems are designed for optimal integration with existing production lines, minimizing disruptions and maximizing throughput.
- Compliance Assurance: Professional solutions are built to comply with industry regulations, providing peace of mind and avoiding potential legal issues.
- Support Services: Access to expert support and maintenance services ensures that any issues are promptly and effectively resolved, minimizing downtime.
- Long-Term Investment: While the initial cost may be higher, the durability, reliability, and efficiency of a professional system often translate to a better long-term investment.
While a DIY metal detector belt conveyor system might seem appealing for its potential cost savings and customization, the importance of reliability, efficiency, and professional support in industrial applications cannot be understated. A professional solution not only ensures compliance with industry standards but also provides the peace of mind that comes with reliable operation and expert support, making it a worthwhile investment for businesses prioritizing productivity and quality.
Innovative Features and Advancements in Metal Detector Belt Conveyor Systems
The landscape of metal detection in conveyor systems is continually evolving, driven by technological advancements and the growing demands of various industries for higher precision, efficiency, and integration. The latest innovations in belt conveyor metal detector technology not only aim to enhance detection capabilities but also to improve user interaction and integration with existing production line technologies. Here, we delve into eight cutting-edge advancements that are setting new standards in the field.
Enhanced Sensitivity and Selectivity
Modern systems boast significantly improved sensitivity, capable of detecting even the smallest metal contaminants. This advancement is crucial for industries where product purity is paramount. Additionally, selectivity enhancements allow for the discrimination between different types of metals, enabling more targeted detection.
Multi-Frequency Operation
The latest metal detector belt conveyor systems utilize multi-frequency technology, allowing for the simultaneous transmission of multiple frequencies. This feature enhances detection capabilities across a broader range of metal types and sizes, particularly beneficial for products with high product effect, such as those with high moisture or salt content.
User-Friendly Interfaces
Advancements in user interface design have made systems more accessible and easier to operate. Touchscreen panels, intuitive software, and customizable settings ensure that operators can quickly adapt to the system, reducing training time and enhancing productivity.
Advanced Data Analytics
Incorporating advanced data analytics and reporting capabilities allows for real-time monitoring and historical data analysis. This feature aids in identifying trends, optimizing system performance, and ensuring compliance with regulatory standards.
Tunnel Metal Detectors
Tunnel metal detectors represent a significant innovation, offering enhanced detection capabilities by surrounding the product completely. This design improves sensitivity and accuracy, particularly for bulk or continuous product flows.
Integration with Other Technologies
Integration capabilities have seen considerable advancements, with systems now designed to seamlessly connect with other production line technologies. This integration facilitates automated product handling, rejection systems, and overall line management, creating a cohesive and efficient production process.
Adaptive Phase Technology
This technology adjusts the system’s phase angle to counteract product effect, significantly improving detection in challenging product conditions. Adaptive phase technology ensures consistent performance across a wide range of products without the need for frequent recalibration.
Hygienic Design and Construction
For industries where sanitation is critical, such as food and pharmaceuticals, advancements in hygienic design and construction materials have been a focus. Systems are now available with features like open-frame designs, water-resistant finishes, and easy-to-clean surfaces to meet stringent hygiene standards.
The continuous innovation in metal detector belt conveyor systems is transforming the capabilities and applications of these essential industrial tools. From enhanced sensitivity and user-friendly interfaces to integration with broader production technologies and hygienic designs, these advancements are not only elevating the standards of metal detection but are also paving the way for more efficient, reliable, and compliant production processes.
Request a quote for our high-quality conveyor belts today.
FAQs about Metal Detector Belt Conveyor System
Metal detectors integrated into conveyor belt systems work by generating a magnetic field that extends over and around the belt. When a metal object passes through this field, it disturbs the field’s frequency. The detector’s control unit, which is tuned to a specific frequency range, registers this disturbance. The system then sends a signal that can either trigger an alarm or activate a rejection mechanism to remove the metal-contaminated product from the production line. This process is highly automated and can detect various metal types, including ferrous, non-ferrous, and stainless steel contaminants, ensuring that only clean product passes through.
Generally, metal detectors are designed to ignore the conveyor belt itself. This is achieved through the calibration process, where the belt is present, and the metal detector is tuned to not react to it. However, the belt’s material plays a significant role in this process. Conveyor belts for use in metal detector applications are often made from non-metallic materials to avoid triggering the detector. Any metal components, such as staples or clips in the belt, could be detected, so belts in metal detector systems are usually constructed without such materials, or with materials that the detector can discriminate against.
Conveyor belts often use multiple types of sensors for different purposes. In the context of a metal detector belt conveyor system, the primary sensor is the metal detector itself, which uses electromagnetic induction to detect metal contaminants. Additionally, other sensors may be used to monitor various aspects of the conveyor system’s operation, such as speed sensors to ensure the belt maintains a consistent speed for accurate metal detection and positioning sensors to identify the specific location of a detected contaminant on the belt.
A conveyor belt system functions by continuously moving a belt over a series of rollers. The belt’s movement is usually powered by a motor-driven pulley with another pulley at the opposite end for tension. These systems are designed to transport materials from one point to another over a fixed path. The belt itself can be made of various materials, such as rubber, plastic, or metal, depending on the application. In production settings, the system can be customized to carry products through different stages of processing, with sensors and other control mechanisms regulating the flow of goods for efficient and automated operations.
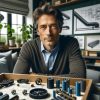
Jordan Smith, a seasoned professional with over 20 years of experience in the conveyor system industry. Jordan’s expertise lies in providing comprehensive solutions for conveyor rollers, belts, and accessories, catering to a wide range of industrial needs. From initial design and configuration to installation and meticulous troubleshooting, Jordan is adept at handling all aspects of conveyor system management. Whether you’re looking to upgrade your production line with efficient conveyor belts, require custom conveyor rollers for specific operations, or need expert advice on selecting the right conveyor accessories for your facility, Jordan is your reliable consultant. For any inquiries or assistance with conveyor system optimization, Jordan is available to share his wealth of knowledge and experience. Feel free to reach out at any time for professional guidance on all matters related to conveyor rollers, belts, and accessories.