Selecting the Right Troughing Roller: Factors to Consider
In the intricate world of conveyor systems, the troughing roller stands out as a pivotal component, essential for the efficient and smooth operation of belt conveyors. These rollers are specially designed to form the belt into a trough shape, enhancing the conveyor’s ability to carry bulk materials securely and efficiently. Their role is not just limited to transportation; troughing rolls also contribute significantly to the stability and longevity of the conveyor belt itself by evenly distributing load and reducing material spillage. Given the demanding environments where these systems operate—ranging from mining sites to manufacturing plants—the quality and design of troughing rollers are crucial for maintaining operational efficiency and minimizing downtime. This introductory exploration emphasizes the importance of understanding troughing rollers, as they are fundamental in optimizing the performance of conveyor systems and ensuring the seamless movement of materials across various industries.
What are Troughing Rollers
A troughing roller is a specialized component in conveyor belt systems designed to support and shape the belt into a trough, optimizing the belt’s ability to carry bulk materials. It consists of a series of rollers set at angles to each other, creating a cradle that supports the belt and its contents. This configuration not only maximizes the quantity of material that can be transported but also enhances the stability of the cargo during transit.
The term “troughing idler” refers to a group of these rollers that work together to maintain the trough shape of the conveyor belt. It’s an essential part of the system that includes the troughing rollers and often a central idler roller that assists in maintaining the belt’s shape and direction. The alignment and spacing of these idlers are critical for the efficient function of the conveyor, affecting everything from material spillage to belt wear.
Return rollers play several pivotal roles in the conveyor system, ensuring its smooth and efficient operation:
- Supporting the Belt: They provide support to the underside of the conveyor belt. This is crucial for the belt’s return path, ensuring it maintains a consistent and stable line.
- Maintaining Belt Tension: These rollers help maintain proper belt tension, which is vital for preventing slippage on the drive pulley and ensuring smooth operation.
- Protecting the Belt: By supporting the return side of the belt, return rollers prevent sagging and dragging, which can lead to premature wear and tear on the conveyor belt.
- Reducing Material Build-up: Keeping the return path stable and well-supported reduces the risk of material build-up on the belt that could otherwise be dragged back into the conveyor system.
- Energy Efficiency: Properly aligned and functioning return rollers reduce the friction and resistance on the conveyor belt as it moves, leading to lower energy consumption and operating costs.
- System Longevity: By ensuring that the belt operates smoothly and remains free from unnecessary strain or damage, return rollers contribute significantly to the overall longevity of the conveyor system.
Understanding the design and function of troughing rollers, troughing idlers, and return rollers is essential for anyone involved in the selection, maintenance, or operation of conveyor systems. These components are critical for the efficient and effective transportation of materials, directly impacting the productivity and operational costs of a wide range of industrial activities.
Different Types of Troughing Rollers
In the domain of conveyor systems, the diversity in the types of troughing rolls configurations plays a critical role in tailoring the system to specific operational needs. Below is an elaboration on various kinds of troughing rollers, highlighting their application and how they differentiate from one another, presented in a table format for clarity:
Type of Troughing Roller | Description | Application |
---|---|---|
Standard Troughing Rollers | These rollers have a fixed angle and are the most common type used in conveyor systems. They form the belt into a standard trough shape, ideal for general material handling. | Widely used in industries like mining, agriculture, and manufacturing for the transportation of bulk materials. |
Impact Troughing Rollers | Designed with a series of rubber discs or rings, these rollers are used in the loading area of the conveyor to absorb the impact of falling materials, protecting the belt and structure. | Essential in the initial loading zones where material drop height can cause damage to the belt or system. |
Adjustable Troughing Rollers | These rollers can adjust their angle to accommodate various belt widths and material loads, providing flexibility in conveyor design. | Useful in applications where material flow or belt width may vary, such as in adjustable conveyor systems or multi-product lines. |
Transition Troughing Rollers | Transition rollers gradually change the belt shape from flat to troughed or vice versa, helping to stabilize the material as it is loaded onto the belt or discharged. | Positioned at the head and tail of the conveyor, where the belt transitions from the loading zone or shifts back to a flat configuration before unloading. |
Retractable Troughing Rollers | These rollers can be retracted to allow for easy cleaning or maintenance of the conveyor belt and are often spring-loaded. | Ideal for industries requiring stringent hygiene standards or where rapid clearing of the belt path is necessary, such as in food processing or pharmaceuticals. |
Self-Aligning Troughing Rollers | Equipped with a pivoting mechanism, these rollers adjust their position automatically to maintain the belt's alignment along the conveyor's path. | Critical in long-distance conveying where belt misalignment can lead to increased wear and operational issues. |
Understanding the different types of troughing rollers and their specific applications is crucial for designing an efficient and effective conveyor system. Each type serves a unique purpose, ensuring that the conveyor can handle the intended materials with optimal efficiency, minimize wear and tear on the system, and adapt to varying operational conditions.
The Principle of Operation of Troughing Rollers
The principle of operation of troughing rollers within a conveyor system is fundamental to the efficient and effective movement of materials. These rollers are strategically designed and positioned to support and shape the conveyor belt into a trough, maximizing the belt’s capacity to transport bulk materials securely from one point to another.
At the core of their function, troughing rollers are mounted on the carrying side of the conveyor system. Typically arranged in sets of three or more, depending on the width of the belt and the load it must carry, these rollers create a concave shape that cradles the material being transported. The central roller is usually positioned horizontally, with the adjacent rollers set at specific angles to form the trough shape. These angles can vary based on the application but commonly range between 20 to 45 degrees, providing a balance between carrying capacity and stability.
The operation begins when the conveyor belt, driven by motors, moves over the troughing rollers. The shape of the rollers forces the belt to conform to a troughed profile, increasing the belt’s depth and width that contacts the material. This transformation significantly enhances the belt’s ability to carry larger volumes of material while reducing spillage along the conveyor’s edges.
Moreover, the trough design facilitated by these rollers also contributes to the material’s stability during transport. By centering and containing the material within the trough, it minimizes shifting and spillage, especially important in high-speed or long-distance conveying scenarios. This stability is crucial not only for maintaining material integrity but also for preventing potential damage to the conveyor system itself.
Additionally, troughing rolls play a vital role in the overall maintenance and longevity of the conveyor belt. By evenly distributing the weight of the material across the width of the belt, these rollers reduce uneven wear and tear. Furthermore, their design often includes features such as sealed bearings and robust construction materials to withstand the operational stresses, contributing to the rollers’ durability and reducing the need for frequent replacements.
The principle of operation of troughing rollers within a conveyor system embodies a blend of engineering precision and practical design. They are indispensable in enhancing the conveyor belt’s capacity, efficiency, and longevity, ultimately contributing to the smooth and effective transportation of materials across various industrial applications.
Troughing Rollers Pricing
The pricing of troughing rollers can be influenced by a multitude of factors, each playing a pivotal role in determining the cost-effectiveness and suitability of these components for various conveyor system applications. Understanding these factors is crucial for making informed purchasing decisions. Here are ten key factors that significantly influence the price of troughing rollers:
- Material Quality and Type: The materials used in manufacturing troughing rollers, such as steel, rubber-coated, polyurethane, or composite materials, greatly affect their price. High-quality, durable materials typically command a higher price due to their longevity and performance.
- Roller Size and Dimensions: The size and dimensions of the rollers, including diameter and length, can influence the price. Larger rollers designed for heavy-duty applications are generally more expensive than smaller ones.
- Load Capacity: Troughing rollers designed to support higher load capacities require more robust construction, which can increase the price.
- Bearing Type and Quality: Bearings are critical for the smooth operation of troughing rollers. High-quality, sealed bearings designed for high load capacities and longevity tend to increase the overall cost.
- Brand Reputation: Rollers manufactured by well-known, reputable brands often come at a premium, reflecting the quality, reliability, and after-sales support associated with the brand.
- Customization and Special Features: Customized rollers designed to meet specific operational requirements, such as adjustable angles, self-cleaning features, or special coatings for corrosion resistance, can significantly increase the price.
- Quantity Ordered: The total quantity of troughing rollers ordered can affect the price, with bulk orders often qualifying for discounts.
- Supply Chain and Manufacturing Costs: Variations in the cost of raw materials, labor, and manufacturing processes can affect the price of troughing rollers. Economic conditions and supply chain disruptions can also lead to price fluctuations.
- Shipping and Handling: The cost of shipping and handling, influenced by the weight and dimensions of the rollers, as well as the distance they need to be transported, can add to the overall cost.
- Market Demand and Availability: Market dynamics, including demand for troughing rollers and the availability of specific types or brands, can influence pricing. Higher demand and lower supply can lead to increased prices.
Pricing variations among different types, brands, and specifications of troughing rollers reflect the diverse needs and preferences of users. For instance, standard steel troughing rollers might be more cost-effective for general applications, whereas specialized polyurethane-coated rollers, designed for specific environmental conditions or material handling requirements, could be more expensive but offer better value in terms of durability and performance.
The pricing of troughing rollers is multifaceted, influenced by material choices, design specifications, brand reputation, and market conditions, among other factors. Understanding these elements can help buyers navigate the market and select the most suitable troughing rollers for their conveyor systems, balancing cost with performance requirements.
Buying Troughing Rollers
When it comes to enhancing or maintaining the efficiency of a conveyor system, selecting the right troughing roller is paramount. Below are eight key considerations to keep in mind when purchasing troughing rolls, followed by insights on where and how to find them for sale.
Considerations When Buying Troughing Rollers:
- Operational Requirements: Assess the specific needs of your conveyor system, including load capacity, belt speed, and material type. This will guide you in choosing rollers that best fit your operational demands.
- Material and Quality: Evaluate the materials used in the rollers for durability and suitability for your application, considering factors like corrosion resistance and wear resistance.
- Size and Specifications: Ensure the dimensions (diameter and length) of the troughing rollers match your conveyor belt’s width and design requirements.
- Load Capacity: Consider the maximum load the rollers need to support without deformation or failure, ensuring smooth operation under full load conditions.
- Brand and Manufacturer Reputation: Research manufacturers and brands for their reliability, quality assurance, and after-sales support. Customer reviews and industry recommendations can offer valuable insights.
- Maintenance and Lifespan: Look for rollers designed for easy maintenance and long service life to reduce downtime and replacement costs.
- Customization Options: If your application requires special features (e.g., self-cleaning, shock-absorbing, adjustable angles), verify the availability of customized solutions.
- Price and Budget Considerations: While price is an important factor, it should be weighed against the quality, features, and expected lifespan of the rollers to ensure cost-effectiveness in the long term.
Finding Troughing Rollers for Sale:
- Manufacturer Websites: Directly visiting the websites of manufacturers specializing in conveyor components is a reliable starting point.
- Industrial Supply Companies: Many industrial suppliers offer a wide range of troughing rollers from various brands and manufacturers.
- Online Marketplaces: Platforms like Alibaba, Amazon Business, and eBay cater to industrial and commercial buyers with listings for troughing rollers.
- Trade Shows and Expos: Industry-specific trade shows are excellent for exploring products firsthand and meeting suppliers and manufacturers.
- Local Distributors and Dealers: Checking with local or regional distributors can provide the advantage of quicker delivery times and localized support.
- Industry Forums and Networks: Engaging with online forums and networking groups can offer recommendations and insights from peers.
- Catalogs and Brochures: Requesting product catalogs from manufacturers can help compare different options in detail.
- Direct Sales Representatives: Some companies offer direct consultation with sales reps to tailor products to your specific needs.
- Referrals: Recommendations from industry contacts or businesses in similar operations can lead to trusted suppliers.
- Specialized Industrial Stores: Some brick-and-mortar stores focus on industrial components and can offer troughing rollers among their products.
Purchasing the right troughing roller involves careful consideration of your system’s needs and a thorough search for a reputable supplier that offers quality products within your budget. By combining the considerations for selection with strategic search methods for finding troughing rollers for sale, you can ensure the longevity and efficiency of your conveyor system.
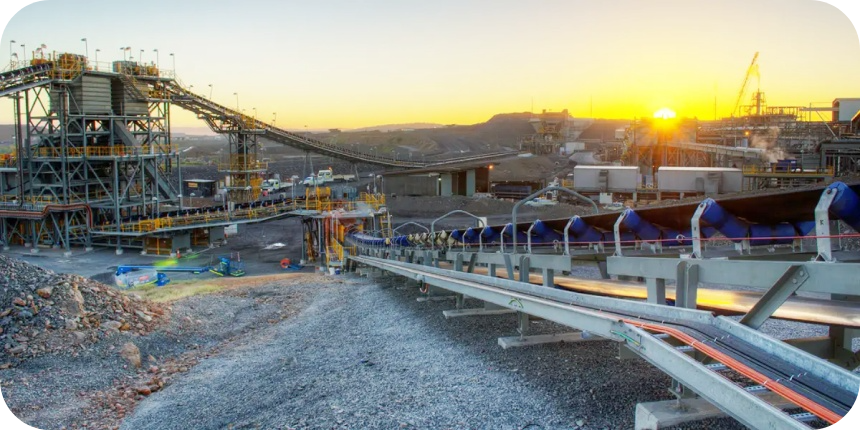
PPI Idlers Catalog and Precision Pulley Catalog: A Comprehensive Guide to Troughing Rollers
The troughing roller is an indispensable component of any conveyor system, dictating efficiency, reliability, and the overall handling capacity of the system. The PPI Idlers Catalog and the Precision Pulley Catalog are two key resources offering in-depth insights into high-quality troughing rolls, their features, and benefits. Below, we delve into the offerings presented in the PPI Idlers Catalog, followed by an examination of eight notable features and ten benefits outlined in the Precision Pulley Catalog, specifically focusing on their troughing roller products.
PPI Idlers Catalog Overview:
The PPI Idlers Catalog serves as a pivotal resource for those seeking robust and efficient troughing roller solutions. It offers a comprehensive overview of various idler products, designed to meet a broad spectrum of operational needs across industries. The catalog emphasizes the importance of precision-engineered troughing rollers in enhancing conveyor belt performance and longevity. It details an array of idler types, including standard troughing idlers, impact idlers, and specialty idlers, each tailored for specific conditions and load requirements.
Precision Pulley Catalog: Features and Benefits
Features:
- Advanced Material Technology: Utilizes high-grade materials for enhanced durability and performance under harsh operational conditions.
- Innovative Design Solutions: Offers a variety of trough angles and idler configurations to optimize material handling and reduce spillage.
- Sealed for Protection: Features sealed bearings and dust-proof designs to extend the lifespan of the rollers and minimize maintenance.
- Energy Efficient Operation: Engineered for low rolling resistance, reducing power consumption and operational costs.
- Customization Options: Provides custom-engineered solutions to meet unique system requirements, including variable belt widths and load capacities.
- Ease of Installation: Designed for quick and easy installation, reducing downtime and labor costs.
- Comprehensive Range: Includes a wide range of idler types and sizes, ensuring suitability for various conveyor systems and applications.
- Quality Assurance: Each product undergoes rigorous testing and quality checks to ensure reliability and performance.
Benefits:
- Increased Operational Efficiency: Enhanced belt support and reduced spillage lead to higher operational efficiency and material handling capacity.
- Reduced Maintenance Costs: Durable materials and sealed designs minimize wear and tear, extending the service life of the rollers.
- Lower Energy Consumption: The low rolling resistance design contributes to significant energy savings over the conveyor’s lifespan.
- Enhanced System Reliability: High-quality components and rigorous testing ensure reliable operation and reduced downtime.
- Flexibility in Application: A wide range of products and customization options allow for tailored solutions, fitting specific operational needs.
- Improved Safety: The design and quality of the products contribute to safer operational conditions and reduced risk of accidents.
- Cost-Effective Solutions: The combination of durability, energy efficiency, and reduced maintenance costs leads to a lower total cost of ownership.
- Environmental Consideration: Energy-efficient designs and reduced material spillage contribute to a smaller environmental footprint.
- Technical Support: Comprehensive technical support and documentation assist in optimal product selection and maintenance.
- Industry Compliance: Products designed to meet or exceed industry standards and regulations, ensuring compatibility and safety across operations.
Both the PPI Idlers Catalog and the Precision Pulley Catalog are instrumental in guiding the selection of the right troughing rollers for any conveyor system, offering detailed insights into the features and benefits that define high-quality components. Through these catalogs, users gain access to a wealth of information that aids in optimizing conveyor performance, enhancing operational efficiency, and ensuring the longevity of the conveyor system.
Conveyor Idlers and Return Rollers: Enhancing Efficiency with Troughing Rollers
In the intricate design of conveyor systems, troughing rollers play a pivotal role, working closely with conveyor idlers and return rollers to ensure smooth, efficient material transport. This section delves into the essential functions of conveyor idlers and their interconnectedness with troughing rollers, alongside the critical role of return rollers in maintaining system integrity.
Conveyor Idlers and Their Relation to Troughing Rollers:
Conveyor idlers are cylindrical rods that support the conveyor belt and the material being transported. They are strategically placed along the conveyor frame to provide a smooth surface for the belt to roll over. Troughing rollers are a specialized type of idler designed with a slight curve to form the conveyor belt into a trough shape, significantly enhancing the belt’s capacity to carry materials. These troughing rolls are typically installed in the loading and material-carrying sections of the conveyor, where their unique design minimizes spillage and optimizes material handling efficiency.
The relationship between conveyor idlers and troughing rollers is foundational to the conveyor’s operational effectiveness. Troughing rollers, being a specific kind of idler, are crucial for:
- Maximizing Load Capacity: By shaping the belt into a trough, they increase the volume of material that can be transported, thereby improving efficiency.
- Reducing Material Spillage: The trough design helps contain the material within the center of the belt, minimizing spillage and waste.
- Enhancing Belt Stability: The trough shape stabilizes the belt under heavy loads, preventing belt misalignment and reducing maintenance needs.
Description and Functionality of Conveyor Return Rollers:
Conveyor return rollers, another essential component, are situated along the return path of the belt. These rollers support the belt’s weight as it travels back to the beginning of the conveyor to complete the loop. While they do not directly interact with the material being conveyed, their role is vital for:
- Maintaining Belt Tension: Properly installed return rollers ensure that the conveyor belt maintains the correct tension, preventing slippage and misalignment.
- Protecting the Belt: By supporting the return side of the conveyor belt, return rollers prevent sagging and potential damage to the belt’s underside, extending its lifespan.
- Ensuring Smooth Operation: Return rollers contribute to the overall smooth operation of the conveyor system, reducing vibrations and wear on the belt.
Both conveyor idlers, including troughing rollers, and return rollers, are integral to the conveyor system’s design and functionality. They work in tandem to ensure that the conveyor belt operates smoothly, efficiently, and with minimal downtime. Understanding their specific roles and functionalities highlights the importance of selecting high-quality components and maintaining them properly to maximize the conveyor system’s operational life and efficiency.
Ensure smooth operations with our reliable conveyor rollers.
FAQs about Troughing Roller
A troughing roller is a key component found in conveyor systems, particularly bulk handling conveyors. It is designed to support and shape the conveyor belt to form a ‘trough’, which helps contain the material being transported. This is achieved through a specially designed roller assembly featuring rollers angled at about 20 to 45 degrees on either side of a flat, center roller. The angles form the shape of a trough, hence the name “troughing roller”.
Idler rollers, also known as conveyor rollers, serve a critical function in conveying systems. They are primarily designed to support and shape the conveyor belt, essentially facilitating the smooth transport of materials. Idler rollers also help reduce the drag and friction generated during the conveyor belt’s operation. Additionally, they play a significant role in maintaining the belt’s alignment, reducing the likelihood of belt wander, and mitigating the damage caused by potential material buildup. Despite their seemingly basic function, idler rollers are integral to maintaining the efficiency and longevity of conveyor systems.
The angle of a troughing idler, also known as the trough angle, typically ranges from 20 to 45 degrees. This angle is created by positioning the side rollers at an incline relative to the flat center roller, forming a ‘trough’ shape. The precise angle used can be adjusted depending on the requirements of the material being transported and the specific conveyor design. A larger angle forms a deeper trough and can help contain more material, but it can also contribute to more belt strain and increased power requirements for the conveyor.
Roller conveyors are differentiated mainly based on their configuration and the type of operation they’re designed for. The three primary types include:
Gravity Roller Conveyors: These are non-powered conveyor systems where products are moved using gravity or manual pushing. They are commonly used for simple applications, such as moving boxes or pallets.
Chain-Driven Roller Conveyors: In these systems, a chain links all rollers together, moving them at the same time. These types are often used for heavy items, like pallets and industrial containers.
Line Shaft Roller Conveyors: These conveyors have a shaft that runs the length of the conveyor. The shaft, powered by a motor, provides the drive for each roller individually through belts and pulleys. They are typically used in packaging and manufacturing for lighter loads.
Each type is designed for different use cases and offers a distinct set of advantages catered to specific operational needs.
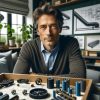
Jordan Smith, a seasoned professional with over 20 years of experience in the conveyor system industry. Jordan’s expertise lies in providing comprehensive solutions for conveyor rollers, belts, and accessories, catering to a wide range of industrial needs. From initial design and configuration to installation and meticulous troubleshooting, Jordan is adept at handling all aspects of conveyor system management. Whether you’re looking to upgrade your production line with efficient conveyor belts, require custom conveyor rollers for specific operations, or need expert advice on selecting the right conveyor accessories for your facility, Jordan is your reliable consultant. For any inquiries or assistance with conveyor system optimization, Jordan is available to share his wealth of knowledge and experience. Feel free to reach out at any time for professional guidance on all matters related to conveyor rollers, belts, and accessories.