PVG Conveyor Belt:Solid Woven Conveyor Belts
A PVG conveyor belt is a high-performance belt designed for demanding industrial applications. This type of conveyor belt combines polyvinyl chloride (PVC) with nitrile rubber (NBR) to create a product that offers superior resistance to fire, impact, and abrasion. PVG conveyor belts are particularly favored in industries where safety and durability are paramount, such as mining and heavy manufacturing. The blend of materials in a PVG conveyor belt ensures it can withstand harsh environments while maintaining its integrity and performance over time. Key features of PVG conveyor belts include flame resistance, excellent mechanical properties, and enhanced flexibility, making them ideal for a wide range of applications.
PVG Conveyor Belt VS PVC Conveyor Belt
Feature | PVG Conveyor Belt | PVC Conveyor Belt |
---|---|---|
Material Composition | Polyvinyl Chloride with a rubber top cover | Polyvinyl Chloride |
Applications | Suitable for underground mining, where flame resistance is crucial | Ideal for general material handling, food processing, and packaging industries |
Durability | High durability due to rubber cover; excellent wear and tear resistance | Moderate durability; suitable for lighter to medium-duty applications |
Flame Resistance | Excellent flame resistance, suitable for environments with stringent safety requirements | Good flame resistance but not as high as PVG belts |
Oil and Chemical Resistance | Good resistance to oils and chemicals due to rubber cover | Good resistance to oils and chemicals, but generally less than PVG belts |
Temperature Range | Typically operates in a broader temperature range | Suitable for a moderate temperature range |
Flexibility | Less flexible due to the rubber cover | More flexible, allowing for smaller pulley diameters |
Maintenance | Requires regular inspection and maintenance due to the rubber cover | Easier to maintain, typically requires less frequent maintenance |
Cost | Generally more expensive due to added rubber cover | More cost-effective for general applications |
Tensile Strength | Higher tensile strength, suitable for heavy-duty applications | Moderate tensile strength, suitable for standard applications |
Weight | Heavier due to the rubber cover | Lighter, making it easier to handle and install |
Surface Texture | Rougher surface texture due to the rubber cover, providing better grip | Smoother surface texture, suitable for applications requiring hygiene and ease of cleaning |
- PVG Conveyor Belts: Best suited for heavy-duty applications, especially in environments requiring high flame resistance and durability. They are more robust but also heavier and costlier.
- PVC Conveyor Belts: Ideal for general-purpose applications where flexibility, ease of maintenance, and cost-effectiveness are important. They are lighter and more suitable for light to medium-duty tasks.
Choosing between PVG and PVC conveyor belts depends on the specific requirements of your application, including the environment, load capacity, and safety standards.
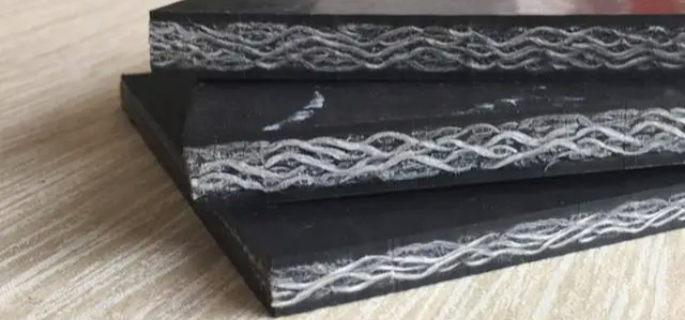
Features of PVG Conveyor Belt
PVG conveyor belts are designed for heavy-duty applications, offering a combination of durability and safety features. Here are the key features of PVG conveyor belts:
- Polyvinyl Chloride (PVC) Base: The base of the belt is made of PVC, providing a strong and flexible foundation.
- Rubber Top Cover: The top cover is made of rubber, enhancing durability and providing excellent grip.
- Underground Mining: Specifically designed for environments where flame resistance is crucial.
- Heavy-Duty Applications: Suitable for transporting heavy loads in harsh conditions.
- Industries: Commonly used in mining, quarrying, and construction industries.
- High Wear Resistance: The rubber top cover provides excellent resistance to abrasion and wear.
- Longevity: Designed for long service life even in demanding conditions.
- High Flame Resistance: Complies with stringent safety standards, making it ideal for underground and high-risk environments.
- Safety Compliance: Meets or exceeds industry standards for flame resistance, such as MSHA (Mine Safety and Health Administration) requirements.
- Good Resistance: The rubber cover provides good resistance to oils and chemicals, making it suitable for various industrial applications.
- Wide Operating Range: Can operate efficiently in a broad range of temperatures, suitable for different environmental conditions.
- High Tensile Strength: Capable of handling heavy loads and high-stress conditions without stretching or breaking.
- Rough Surface: The rubber cover offers a rough texture, providing better grip and preventing slippage of materials.
- Heavy Load Handling: Designed to carry heavy loads, making it suitable for bulk material handling.
- Durability and Strength:PVG conveyor belts are renowned for their exceptional durability and strength. These belts are constructed using high-quality materials that resist wear and tear, even under the most demanding conditions. The core of a PVG conveyor belt typically consists of a robust fabric, such as polyester or nylon, which is coated with a polyvinyl chloride (PVC) and nitrile butadiene rubber (NBR) blend. This combination ensures that the belt can withstand high loads and abrasive materials commonly found in mining environments.
- Oil and Chemical Resistance:One of the standout features of PVG conveyor belts, as detailed in the Continental conveyor belt catalog PDF, is their resistance to oils and chemicals. This resistance is crucial in mining operations where the belt may come into contact with various substances that could otherwise degrade the material. The PVC/NBR coating provides a protective layer that prevents oils and chemicals from penetrating the belt, thereby extending its lifespan and maintaining its performance.
- Fire Resistance:Safety is a paramount concern in mining operations, and PVG conveyor belts are designed with fire resistance in mind. The materials used in these belts are inherently flame-retardant, meeting international safety standards. This fire-resistant property is essential for protecting workers and equipment from potential fire hazards, ensuring a safer working environment.
- Low Elongation and High Flexibility:PVG conveyor belts exhibit low elongation, meaning they do not stretch significantly under tension. This characteristic ensures that the belt maintains its shape and functionality, reducing the need for frequent adjustments and maintenance. Additionally, these belts are highly flexible, allowing them to navigate complex conveyor systems with ease. The combination of low elongation and high flexibility makes PVG conveyor belts ideal for intricate mining conveyor belt systems.
- Anti-static Properties:The build-up of static electricity can pose a significant risk in mining operations, potentially leading to fires or explosions. PVG conveyor belts are designed with anti-static properties to mitigate this risk. The materials used in these belts dissipate static electricity, ensuring safe operation in environments where combustible materials are present.
- Customizable Specifications:The Continental conveyor belt catalog PDF highlights the customizable nature of PVG conveyor belts. These belts can be tailored to meet specific operational requirements, including different widths, lengths, and thicknesses. Customization ensures that each conveyor belt fits perfectly within the existing infrastructure, optimizing performance and efficiency.
PVG conveyor belts are engineered for robustness and safety, making them ideal for demanding industrial applications, especially in environments where flame resistance and heavy load handling are critical. Their combination of PVC and rubber materials provides a balance of flexibility, durability, and resistance to harsh conditions.
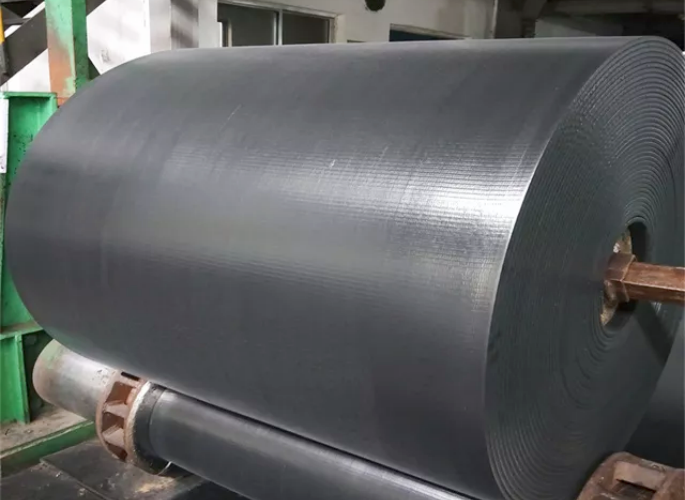
PVG Conveyor Belt Applications in Mining Conveyor Belt Systems
PVG (Polyvinyl Chloride with a rubber top cover) conveyor belts are specifically designed to meet the demanding requirements of the mining industry. Here are the key applications and benefits of using PVG conveyor belts in mining conveyor belt systems:
Underground Mining
- Flame Resistance: PVG conveyor belts are highly flame-resistant, making them suitable for use in underground mining where fire hazards are a significant concern. They comply with stringent safety standards such as MSHA (Mine Safety and Health Administration) regulations.
- Durability: The combination of PVC and rubber provides excellent resistance to abrasion and wear, which is crucial in the harsh underground mining environment.
Heavy Load Transportation
- High Tensile Strength: PVG belts are capable of handling heavy loads and high-stress conditions, making them ideal for transporting large quantities of mined materials.
- Bulk Material Handling: These belts are designed to carry bulk materials such as coal, ore, and aggregate efficiently and reliably.
Harsh Environmental Conditions
- Wide Temperature Range: PVG conveyor belts can operate in a broad range of temperatures, suitable for both hot and cold mining environments.
- Chemical and Oil Resistance: The rubber top cover provides resistance to chemicals and oils, protecting the belt from potential damage caused by exposure to various substances found in mining operations.
Inclined Conveying
- Better Grip: The rough surface texture of the rubber cover provides enhanced grip, making PVG belts suitable for inclined conveying applications where materials need to be transported up steep slopes.
- Reduced Slippage: The increased traction helps reduce material slippage, ensuring a continuous flow of materials.
Long-Distance Conveying
- Extended Service Life: The high durability and wear resistance of PVG belts make them suitable for long-distance conveying, reducing the need for frequent replacements and minimizing downtime.
- Consistent Performance: These belts maintain their integrity and performance over long distances, which is essential in large-scale mining operations.
Safety and Compliance
- Regulatory Compliance: PVG conveyor belts meet or exceed various industry safety standards, ensuring compliance with mining regulations and enhancing overall safety in mining operations.
- Fire Safety: The flame-resistant properties of PVG belts contribute to a safer working environment by reducing the risk of fire.
PVG conveyor belts are an excellent choice for mining conveyor belt systems due to their flame resistance, high tensile strength, durability, and ability to operate in harsh environmental conditions. They are well-suited for underground mining, heavy load transportation, inclined conveying, and long-distance conveying applications. The use of PVG belts helps enhance safety, reliability, and efficiency in mining operations, making them a preferred option in the industry.
Maintenance Tips for PVG Conveyor Belt in Mining Conveyor Belt Systems
Maintaining PVG conveyor belts in mining applications is crucial for ensuring their longevity and efficiency. Mining environments are particularly harsh, and the conveyor belts are subjected to heavy loads, abrasive materials, and continuous operation. Therefore, regular and proactive maintenance is essential. Here are some practical tips for maintaining PVG conveyor belts in mining conveyor belt systems:
Regular Inspections
Conducting regular inspections is the first step in maintaining a PVG conveyor belt. Inspect the belt for any signs of wear, damage, or misalignment. Look for issues such as cracks, fraying, or cuts on the belt surface, which could indicate underlying problems. Also, check for unusual noise or vibrations during operation, as these could be signs of potential issues that need addressing.
Cleaning and Debris Removal
Mining environments can cause a significant buildup of debris and material on the conveyor belt and its components. Regular cleaning is essential to prevent this debris from causing damage or obstructing the belt’s movement. Use appropriate cleaning tools and solutions to remove any accumulated dirt, dust, and material from the belt and surrounding areas.
Lubrication of Moving Parts
Lubricating the moving parts of the conveyor system is vital for reducing friction and wear. Ensure that all bearings, rollers, and other moving components are properly lubricated according to the manufacturer’s recommendations. Use high-quality lubricants that are compatible with the materials and conditions in the mining environment.
Tension and Alignment Adjustment
Proper tension and alignment of the PVG conveyor belt are crucial for its efficient operation. Check the belt tension regularly to ensure it is within the recommended range. An overly tight belt can cause excessive wear, while a loose belt can lead to slippage and misalignment. Adjust the alignment of the belt to ensure it runs smoothly along the conveyor system without deviating from its path.
Monitoring Belt Wear and Tear
Monitor the wear and tear of the PVG conveyor belt over time. Keep track of any changes in the belt’s condition and address minor issues before they become significant problems. Use wear indicators, if available, to gauge the belt’s condition accurately. Replace the belt or its components as needed to prevent unexpected downtime.
Training and Education
Ensure that all personnel involved in the operation and maintenance of PVG conveyor belts are adequately trained and educated. Provide training on proper maintenance techniques, safety protocols, and the specific requirements of PVG conveyor belts. Educated personnel are more likely to identify and address issues promptly, reducing the risk of equipment failure.
Documentation and Record-Keeping
Maintain detailed records of all maintenance activities, inspections, and repairs performed on the PVG conveyor belt. Documenting these activities helps track the belt’s condition over time and identify recurring issues. Use this information to develop a proactive maintenance schedule and make informed decisions about belt replacements and upgrades.
Emergency Maintenance Procedures
Develop and implement emergency maintenance procedures for unexpected breakdowns or issues with the PVG conveyor belt. Ensure that personnel know how to quickly and safely address problems to minimize downtime. Keep essential spare parts and tools readily available to facilitate prompt repairs.
Collaboration with Manufacturers
Collaborate with the manufacturers of PVG conveyor belts to stay informed about the latest maintenance recommendations and best practices. Manufacturers can provide valuable insights and support for maintaining the belts in optimal condition. Utilize their expertise to enhance your maintenance program and ensure the longevity of the conveyor belts.
Maintaining PVG conveyor belts in mining conveyor belt systems requires a proactive and comprehensive approach. Regular inspections, cleaning, lubrication, tension adjustment, and monitoring are essential for ensuring the belts’ longevity and efficiency. Proper training, documentation, and emergency procedures further contribute to effective maintenance. By following these practical tips, mining operations can maximize the performance and lifespan of their PVG conveyor belts, leading to increased productivity and reduced downtime.
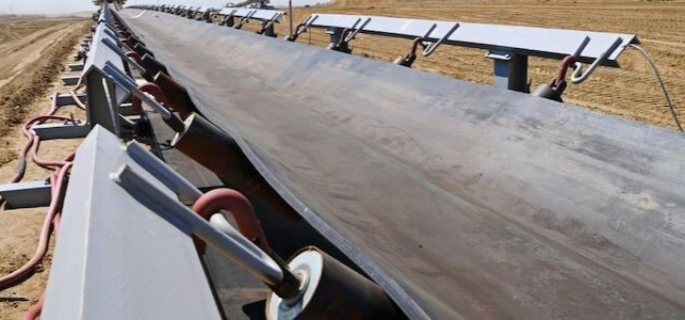
Safety Standards for PVG Conveyor Belt in Mining Conveyor Belt Systems
Safety is a paramount concern in mining operations, and ensuring the safe use of PVG conveyor belts is essential to protect workers and equipment. Adhering to established safety standards and protocols is crucial for minimizing risks and maintaining a safe working environment. Here are the key safety standards and protocols for using PVG conveyor belts in mining conveyor belt systems:
Compliance with Regulatory Standards
PVG conveyor belts used in mining must comply with relevant regulatory standards and guidelines. These standards, set by organizations such as the Mine Safety and Health Administration (MSHA) and the International Organization for Standardization (ISO), specify the safety requirements for conveyor belts in mining applications. Ensure that the PVG conveyor belts meet or exceed these standards to guarantee their safety and performance.
Flame Resistance
One of the critical safety features of PVG conveyor belts is their flame resistance. Mining environments, particularly underground mines, are susceptible to fires due to the presence of flammable materials and machinery. PVG conveyor belts are designed to resist ignition and prevent the spread of flames, thereby enhancing safety. Ensure that the belts used in mining operations are certified for flame resistance and regularly inspect them for signs of wear that could compromise this safety feature.
Hazard Identification and Risk Assessment
Conduct thorough hazard identification and risk assessment for all conveyor belt systems in the mining operation. Identify potential hazards associated with the use of PVG conveyor belts, such as mechanical failures, fire risks, and belt misalignment. Assess the likelihood and impact of these hazards and implement appropriate control measures to mitigate risks. Regularly review and update the risk assessment to account for any changes in the operation or equipment.
Safety Training and Awareness
Provide comprehensive safety training for all personnel involved in the operation and maintenance of PVG conveyor belts. Training should cover safe work practices, emergency procedures, and the specific safety features of PVG conveyor belts. Ensure that workers are aware of the potential hazards and know how to respond effectively in case of an emergency. Promote a culture of safety awareness and encourage workers to report any safety concerns or incidents.
Emergency Stop Devices
Install emergency stop devices along the length of the PVG conveyor belt system. These devices allow workers to quickly halt the operation of the conveyor belt in case of an emergency, preventing accidents and minimizing damage. Ensure that the emergency stop devices are easily accessible and regularly tested to confirm their functionality. Train workers on how to use these devices effectively and include them in emergency response drills.
Guarding and Protective Measures
Implement guarding and protective measures to prevent workers from coming into contact with moving parts of the PVG conveyor belt system. Install guards, barriers, and covers to enclose the belt and its components, reducing the risk of entanglement or injury. Ensure that these protective measures are regularly inspected and maintained to remain effective. Additionally, use warning signs and labels to highlight potential hazards and safe operating procedures.
Fire Detection and Suppression Systems
Install fire detection and suppression systems in areas where PVG conveyor belts are used, particularly in underground mining operations. These systems can quickly detect and extinguish fires, minimizing damage and preventing the spread of flames. Regularly test and maintain the fire detection and suppression systems to ensure their reliability. Train workers on the proper use of fire extinguishers and other firefighting equipment.
Regular Safety Audits and Inspections
Conduct regular safety audits and inspections of the PVG conveyor belt systems to identify and address potential safety issues. Use checklists and standardized procedures to systematically evaluate the safety of the belts and their components. Document the findings and take corrective actions to resolve any identified issues. Involve workers in the safety audits to leverage their firsthand knowledge and experience.
Incident Reporting and Investigation
Implement a robust incident reporting and investigation process to address safety incidents related to PVG conveyor belts. Encourage workers to report any accidents, near misses, or safety concerns without fear of reprisal. Investigate incidents thoroughly to determine their root causes and implement corrective actions to prevent recurrence. Use the findings from incident investigations to improve safety protocols and training programs.
Adhering to safety standards and protocols is essential for ensuring the safe use of PVG conveyor belts in mining conveyor belt systems. Compliance with regulatory standards, flame resistance, hazard identification, safety training, emergency stop devices, guarding measures, fire detection, regular safety audits, and incident reporting are critical components of a comprehensive safety program. By prioritizing safety and implementing these measures, mining operations can protect workers, equipment, and the environment, fostering a safer and more efficient workplace.
Installation Guide for PVG Conveyor Belt in Mining Conveyor Belt System
Proper installation of PVG conveyor belts is crucial for ensuring optimal performance and longevity. A well-installed belt minimizes downtime, reduces maintenance costs, and enhances the efficiency of mining operations. This section provides a detailed, step-by-step guide on installing PVG conveyor belts in mining conveyor belt systems, drawing on best practices and recommendations from industry experts.
Pre-installation Preparation
- Inspection and Preparation of Equipment
Before installation, thoroughly inspect the conveyor system and the PVG conveyor belt. Ensure that all components, including pulleys, rollers, and idlers, are in good condition and free from damage. Clean the conveyor system to remove any debris or contaminants that could affect the installation process.
- Measuring and Cutting the Belt
Measure the length and width of the conveyor system to determine the exact dimensions required for the PVG conveyor belt. Using a sharp cutting tool, cut the belt to the appropriate size, ensuring clean and straight edges. This precision is vital for seamless installation and optimal performance.
Installation Steps
- Positioning the Belt
Carefully position the PVG conveyor belt on the conveyor system. Ensure that the belt is centered on the frame and aligned with the pulleys. This alignment is crucial to prevent tracking issues and uneven wear.
- Securing the Belt Ends
Attach the ends of the PVG conveyor belt to the conveyor frame using appropriate fasteners or clamps. These should be tightened securely to prevent slippage but not so tight as to cause damage to the belt.
- Splicing the Belt
If the belt is not a continuous loop, splicing will be necessary. Follow the manufacturer’s instructions for the splicing method, whether it be mechanical fasteners or vulcanization. Ensure that the splice is secure and smooth to prevent any weak points that could lead to failure.
- Tensioning the Belt
Proper tensioning is critical for the performance of the PVG conveyor belt. Use a tensioning device to apply the correct amount of tension as specified by the manufacturer. Avoid over-tensioning, as this can cause excessive wear and reduce the lifespan of the belt.
- Tracking the Belt
Run the conveyor system at a slow speed to check the tracking of the belt. Adjust the tracking mechanisms to ensure that the PVG conveyor belt runs smoothly along the center of the conveyor frame. Proper tracking prevents the belt from drifting and reduces the risk of damage.
- Final Adjustments and Testing
Once the belt is properly tensioned and tracked, conduct a final inspection to ensure all components are correctly installed and secure. Run the conveyor system at its operational speed to test the belt’s performance. Monitor for any signs of misalignment, slippage, or other issues, and make necessary adjustments.
Post-installation Maintenance
- Regular Inspections
Conduct regular inspections of the PVG conveyor belt and the conveyor system. Look for signs of wear, damage, or misalignment, and address any issues promptly to prevent more significant problems.
- Cleaning and Lubrication
Keep the belt and the conveyor system clean to prevent the build-up of debris that could affect performance. Lubricate moving parts as recommended by the manufacturer to ensure smooth operation.
- Tension and Tracking Adjustments
Periodically check the tension and tracking of the PVG conveyor belt. Make adjustments as necessary to maintain optimal performance and extend the belt’s lifespan.
- Splice and Joint Maintenance
Regularly inspect splices and joints for signs of wear or damage. Reinforce or repair as needed to prevent belt failure and maintain the integrity of the conveyor system.
Safety Considerations
- Personal Protective Equipment (PPE)
Ensure that all personnel involved in the installation and maintenance of PVG conveyor belts wear appropriate PPE, including gloves, safety glasses, and hard hats.
- Lockout/Tagout Procedures
Follow lockout/tagout procedures to ensure the conveyor system is de-energized and safe to work on. This step is crucial to prevent accidental startup and injuries.
- Training and Supervision
Ensure that all personnel involved in the installation and maintenance of PVG conveyor belts are properly trained and supervised. Familiarity with the equipment and procedures reduces the risk of accidents and errors.
Installing a PVG conveyor belt in a mining conveyor belt system requires careful preparation, precise execution, and ongoing maintenance. By following the steps outlined in this guide, mining professionals can ensure a successful installation that maximizes the performance and longevity of their conveyor system. Proper installation not only enhances efficiency but also contributes to a safer and more reliable mining operation.
Technical Specifications of PVG Conveyor Belt in Continental Conveyor Belt Catalog PDF
PVG conveyor belts, as outlined in the Continental conveyor belt catalog PDF, are designed to meet the demanding requirements of various industrial applications, particularly in mining. These belts combine polyvinyl chloride (PVC) with nitrile rubber (NBR) to offer a unique blend of properties that ensure durability, safety, and efficiency. This section delves into the technical specifications of PVG conveyor belts provided in the Continental catalog, highlighting their construction, physical properties, and performance characteristics.
Construction and Material Composition
- Top Cover: The top cover of PVG conveyor belts is made from a blend of PVC and NBR. This combination provides exceptional resistance to fire, oil, and wear, making it suitable for harsh environments. The thickness of the top cover can vary depending on specific application requirements, typically ranging from 1.5 mm to 6 mm.
- Carcass: The carcass of a PVG conveyor belt consists of multiple layers of synthetic fabrics such as polyester and nylon. This multi-ply structure enhances the belt’s tensile strength and flexibility, ensuring it can handle heavy loads and withstand harsh conditions. The number of plies and the fabric type are tailored to meet the specific needs of the application.
- Bottom Cover: Similar to the top cover, the bottom cover is also made of PVC and NBR. This layer provides additional protection against fire and abrasion, contributing to the overall durability of the belt. The thickness of the bottom cover is generally less than that of the top cover.
Physical Properties
- Tensile Strength: The tensile strength of PVG conveyor belts is a measure of their ability to withstand pulling forces. According to the Continental catalog, PVG belts have a tensile strength ranging from 500 N/mm to 3150 N/mm, depending on the belt’s construction and the number of plies. This high conveyor belt tensile strength ensures that the belts can handle heavy loads without stretching or breaking.
- Elongation at Break: Elongation at break indicates the belt’s ability to stretch under tension before breaking. PVG conveyor belts from Continental typically exhibit elongation values between 10% and 20%, providing a balance between flexibility and strength. This property ensures that the belts can absorb shocks and impacts without failing.
- Abrasion Resistance: Abrasion resistance is critical for conveyor belts used in mining and other abrasive environments. PVG conveyor belts have excellent abrasion resistance, as measured by the DIN 22102 standard. These belts typically show a material loss of less than 120 mm³, ensuring long-lasting performance even in abrasive conditions.
- Fire Resistance: One of the most critical properties of PVG conveyor belts is their fire resistance. These belts are designed to meet stringent fire resistance standards such as ISO 340 and EN 12882. The fire-resistant properties are achieved through the use of flame-retardant materials in the belt’s construction, ensuring safety in underground mining operations.
Performance Characteristics
- Impact Resistance: PVG conveyor belts are designed to withstand the impacts associated with handling heavy and sharp materials. The combination of PVC and NBR provides excellent impact resistance, preventing damage to the belt and reducing maintenance needs. This property is particularly important in mining operations, where belts are exposed to continuous impacts from ore and other materials.
- Flexibility: Flexibility is a crucial characteristic for conveyor belts used in complex industrial applications. PVG conveyor belts maintain their flexibility across a wide range of temperatures, including extreme cold. This flexibility allows the belts to navigate tight bends and curves without compromising their structural integrity.
- Chemical Resistance: The PVC and NBR blend used in PVG conveyor belts offers resistance to oils, chemicals, and solvents. This chemical resistance is essential for applications where the belts are exposed to harsh substances, preventing degradation and maintaining performance over time.
- Low Maintenance: The durability and resistance properties of PVG conveyor belts result in lower maintenance requirements compared to traditional belts. These belts can withstand rigorous use in demanding environments, reducing the need for frequent repairs and replacements. This translates to lower maintenance costs and increased operational efficiency.
Customization Options
Continental offers a range of customization options for their PVG conveyor belts to meet specific application requirements. These customization options include variations in belt width, length, cover thickness, and the number of plies. Customers can tailor the belts to their unique needs, ensuring optimal performance in their operational environments.
The technical specifications of PVG conveyor belts as outlined in the Continental conveyor belt catalog PDF highlight their robust construction, excellent physical properties, and superior performance characteristics. With a composition that includes a blend of PVC and NBR, these belts offer exceptional flame resistance, impact resistance, and durability. The detailed specifications provided by Continental ensure that customers can select the right PVG conveyor belt for their specific applications, ensuring reliable and efficient material handling in challenging environments such as mining.
Advantages of PVG Conveyor Belt in Mining Conveyor Belt Systems
PVG conveyor belts are highly esteemed in the mining industry due to their exceptional durability, performance, and safety features. These belts, composed of polyvinyl chloride (PVC) and nitrile rubber (NBR), offer numerous benefits that make them ideal for the rigorous demands of mining operations. This section discusses the various advantages of using PVG conveyor belts in mining conveyor belt systems, emphasizing their durability, performance, and cost-effectiveness.
Durability and Longevity
- High Abrasion Resistance: PVG conveyor belts are designed to withstand the abrasive nature of materials such as ore and coal. Their high abrasion resistance ensures that they can handle continuous exposure to harsh conditions without significant wear and tear. This durability translates to a longer service life, reducing the frequency of belt replacements and associated downtime.
- Impact Resistance: The robust construction of PVG conveyor belts, combining PVC and NBR, provides excellent impact resistance. This feature allows the belts to absorb shocks and impacts from heavy and sharp materials, maintaining their integrity and reducing the risk of damage. This impact resistance is particularly beneficial in mining operations where the belts are subjected to constant impacts.
- Chemical Resistance: PVG conveyor belts offer superior resistance to oils, chemicals, and solvents commonly found in mining environments. This chemical resistance ensures that the belts do not degrade when exposed to harsh substances, maintaining their performance and longevity.
Superior Performance
- Flame Resistance: Safety is a top priority in mining operations, and PVG conveyor belts provide excellent flame resistance. These belts are designed to resist ignition and prevent the spread of fire, enhancing the safety of underground mining operations and protecting both personnel and equipment. Compliance with stringent fire resistance standards such as ISO 340 and EN 12882 ensures that PVG conveyor belts meet the highest safety requirements.
- Flexibility: PVG conveyor belts maintain their flexibility across a wide range of temperatures, including extreme cold. This flexibility allows the belts to navigate complex mine layouts, including sharp turns and elevation changes, without compromising performance. The ability to remain flexible ensures smooth and efficient material transport, even in challenging environments.
- Low Maintenance: The durability and resistance properties of PVG conveyor belts result in lower maintenance requirements compared to traditional belts. These belts can withstand rigorous use in demanding environments, reducing the need for frequent repairs and replacements. This translates to lower maintenance costs and increased operational efficiency.
Cost-Effectiveness
- Reduced Maintenance Costs: The durability and resistance properties of PVG conveyor belts result in lower maintenance requirements. These belts can withstand rigorous use, reducing the need for frequent repairs and replacements. This translates to lower maintenance costs and increased operational efficiency.
- Increased Operational Efficiency: PVG conveyor belts enhance the overall efficiency of mining operations by ensuring the reliable and continuous transport of materials. Their robust performance reduces downtime and minimizes disruptions, allowing mining companies to maintain high productivity levels. The extended service life of PVG conveyor belts means that mining companies can invest in fewer belt replacements over time, reducing the total cost of ownership and providing a better return on investment.
Environmental Benefits
- Lower Emissions: The production of PVG conveyor belts generates fewer emissions compared to conventional rubber belts. This reduction in emissions contributes to a smaller carbon footprint and aligns with the mining industry’s goals of sustainability.
- Recyclability: PVG conveyor belts are easier to recycle, reducing waste and promoting more sustainable practices. The recyclability of these belts ensures that they can be repurposed or disposed of in an environmentally responsible manner.
Enhanced Safety Features
- Fire-Resistant Properties: As mentioned earlier, the flame-resistant properties of PVG conveyor belts significantly improve safety in underground mining operations. These belts help prevent fires and protect workers and equipment from fire-related hazards.
- Emergency Stop Mechanisms: Many PVG conveyor belts are designed with integrated emergency stop mechanisms, allowing workers to quickly halt the belt’s operation in case of an emergency. This feature enhances safety by preventing accidents and minimizing potential damage.
The advantages of using PVG conveyor belt in mining conveyor belt systems are numerous and significant. Their durability, superior performance, cost-effectiveness, environmental benefits, and enhanced safety features make them an ideal choice for demanding mining applications. PVG conveyor belts offer a reliable and efficient solution for the continuous transport of materials, ensuring the smooth operation of mining processes. By investing in PVG conveyor belts, mining companies can achieve greater productivity, reduced maintenance costs, and improved safety, ultimately enhancing their overall operational efficiency.
FAQs about PVG Conveyor Belt
A PVG belt is a type of conveyor belt that features a blend of polyvinyl chloride (PVC) and nitrile rubber (NBR). This combination results in a belt with enhanced flame resistance, making it ideal for underground mining applications where fire safety is a critical concern. PVG belts are known for their excellent resistance to impact, abrasion, and moisture, ensuring durability and reliability in harsh environments. They are designed to convey materials over long distances and through rough terrains while maintaining structural integrity and performance.
The primary difference between PVC (polyvinyl chloride) and PVG (a blend of PVC and nitrile rubber) conveyor belts lies in their composition and properties. PVC belts are made entirely of polyvinyl chloride, which makes them lightweight, resistant to chemicals, and suitable for general material handling tasks. They are often used in light to medium-duty applications. On the other hand, PVG belts combine PVC with nitrile rubber, enhancing their flame resistance, impact resistance, and overall durability. This makes PVG belts more suitable for heavy-duty applications, especially in environments where fire safety is crucial, such as underground mining.
Conveyor belts come in various types, each designed for specific applications. The main types include:
Flat Belts: Used for general material handling, flat belts are simple and efficient, suitable for conveying items on a flat surface.
Modular Belts: Made of interlocking plastic segments, modular belts are highly durable and easy to clean, making them ideal for the food and beverage industry.
Cleated Belts: Featuring raised sections or cleats, these belts prevent material slippage, making them suitable for incline and decline conveying.
Chevron Belts: Designed with a V-shaped pattern, chevron belts enhance grip and prevent rollback, commonly used in bulk material handling.
Roller Belts: Equipped with rollers, these belts reduce friction and are used for heavy-duty applications, such as moving heavy loads.
Wire Mesh Belts: Constructed from metal wires, these belts are used in high-temperature applications like baking, drying, and cooling processes.
PIW stands for “Pounds per Inch of Width” and is a measurement of the strength of a conveyor belt. It indicates the belt’s capacity to withstand the forces exerted on it during operation. The PIW rating helps determine the belt’s tensile strength and its ability to handle heavy loads. For example, a conveyor belt with a PIW rating of 200 can withstand 200 pounds of force per inch of its width. This rating is crucial for selecting the appropriate belt for specific applications, ensuring that the belt can handle the required load without stretching or breaking. The PIW rating also affects the belt’s durability and lifespan, making it a key factor in conveyor belt selection.
The Harmonized System (HS) code for PVC conveyor belts typically falls under Chapter 39 of the HS code, which covers plastics and articles thereof. Specifically, the HS code for PVC conveyor belts is 3926.90. This code is used for “Other articles of plastics and articles of other materials of headings 3901 to 3914.” The exact classification may vary slightly depending on the specific characteristics of the conveyor belt and the regulations of the importing country.
It’s important to consult with a customs broker or the official customs website of the importing country for precise classification and to ensure compliance with local regulations. The HS code helps in standardizing the identification of goods for customs and international trade purposes, facilitating the efficient movement of goods across borders.
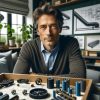
Jordan Smith, a seasoned professional with over 20 years of experience in the conveyor system industry. Jordan’s expertise lies in providing comprehensive solutions for conveyor rollers, belts, and accessories, catering to a wide range of industrial needs. From initial design and configuration to installation and meticulous troubleshooting, Jordan is adept at handling all aspects of conveyor system management. Whether you’re looking to upgrade your production line with efficient conveyor belts, require custom conveyor rollers for specific operations, or need expert advice on selecting the right conveyor accessories for your facility, Jordan is your reliable consultant. For any inquiries or assistance with conveyor system optimization, Jordan is available to share his wealth of knowledge and experience. Feel free to reach out at any time for professional guidance on all matters related to conveyor rollers, belts, and accessories.