Choosing A Conveyor Belt Used in Mining
Conveyor belt systems play a crucial role in the mining industry, significantly impacting the efficiency and effectiveness of material transportation.Conveyor belt used in mining ores, concentrates, and tailings. Essential for mining efficiency, belts require proper maintenance. The advent of the conveyor belt used in mining has revolutionized the way materials are moved within mining operations. These systems allow for the continuous and automated transportation of large quantities of mined materials, reducing the need for manual labor and minimizing downtime. By streamlining the process, conveyor belts have increased productivity and safety in mining environments. The conveyor belt used in mining is a testament to technological advancement, making the extraction and processing of minerals faster, safer, and more cost-effective than traditional methods.
The Basics of Conveyor Belt Used in Mining Systems
The Role and Design of Conveyor Belt Systems in Mining
The conveyor belt used in mining is a fundamental tool for transporting materials efficiently and safely across various distances within a mining operation. These systems are designed to streamline the movement of raw materials, such as ores and coal, from the excavation site to processing facilities, storage areas, or directly to loading points for further transport. The conveyor belt used in mining enhances productivity, reduces manual labor, and improves safety by minimizing the need for human interaction with heavy and potentially hazardous materials.
Key Components of Conveyor Belt Systems
Understanding the basics of conveyor belt systems in mining involves recognizing the essential components that make these systems effective.
- Belt: The actual conveyor belt used in mining is typically made from a variety of materials, including rubber, PVC, and steel-reinforced fabrics, designed to handle the harsh conditions of mining environments.
- Pulleys: Pulleys are critical for guiding and driving the conveyor belt. They include drive pulleys that move the belt and idler pulleys that support the belt and help maintain its alignment.
- Motor: A powerful motor drives the conveyor belt system, ensuring it moves at the required speed to transport materials efficiently.
- Frame: The frame provides structural support for the conveyor system, ensuring stability and durability.
- Rollers: Rollers, or idlers, support the belt and the material being transported, reducing friction and wear on the belt.
Design Considerations for Conveyor Belt Used in Mining
The design of conveyor belt systems in mining must consider several factors to ensure efficiency and reliability. These factors include:
- Load Capacity: The system must be designed to handle the maximum load expected in the mining operation, including both the weight of the materials and the speed at which they need to be transported.
- Belt Width and Speed: The width and speed of the conveyor belt used in mining should be chosen based on the type and volume of material being transported. Wider belts and higher speeds are necessary for large-scale operations.
- Durability: The conveyor belt used in mining must be durable enough to withstand the abrasive nature of mined materials and the harsh operating conditions, such as extreme temperatures and exposure to chemicals.
- Maintenance Requirements: Easy access for maintenance and repairs is essential to minimize downtime. The design should allow for quick replacement of components and easy inspection.
- Safety Features: Safety is paramount in mining operations. Conveyor belt systems should include features such as emergency stop mechanisms, guards to prevent accidental contact with moving parts, and sensors to detect belt misalignment or material blockages.
Examples of Conveyor Belt Systems in Mining
- Overland Conveyors: These long-distance conveyor belts transport materials across vast areas from the mine to the processing plant. They are designed to handle large volumes and can be several kilometers long.
- Underground Conveyors: Conveyor belts used in underground mining must navigate confined spaces and sharp turns. These systems are crucial for transporting materials from deep within the earth to the surface.
- High Angle Conveyors: These conveyors are used to transport materials up steep inclines. They are equipped with special cleats or buckets to prevent materials from sliding back.
- Portable Conveyors: Portable conveyor belts can be easily moved and adjusted to different positions within the mining site. They are often used for temporary setups or in areas where flexibility is needed.
- Stacker Conveyors: Stacker conveyors are used to pile bulk materials into stockpiles. They are essential for creating organized and accessible storage areas within the mining operation.
The conveyor belt used in mining is a vital component of modern mining operations. Its design and implementation are crucial for ensuring the efficient, safe, and cost-effective transport of materials. By understanding the basics of these systems, including their key components and design considerations, mining professionals can make informed decisions that enhance their operations.
Composition of Conveyor Belt Used in Mining
The composition of a conveyor belt used in mining applications is critical to its performance, durability, and suitability for different mining conditions. Here is a detailed breakdown of the components and materials typically used in mining conveyor belts:
1. Cover Material
The cover is the outer layer of the conveyor belt, which comes into direct contact with the material being transported. The cover material must be chosen based on the specific requirements of the mining application.
- Rubber: The most common cover material, offering excellent abrasion resistance, flexibility, and resilience. Rubber covers can be formulated to provide additional properties such as heat, oil, and chemical resistance.
- Polyvinyl Chloride (PVC): Used for belts that need to be resistant to chemicals and oils. PVC covers are durable and provide good resistance to abrasion.
- Polyurethane (PU): Known for its high resistance to wear and tear, PU covers are suitable for applications involving sharp or abrasive materials.
2. Carcass Material
The carcass is the internal layer of the conveyor belt, providing structural strength and flexibility. It is usually composed of multiple layers of fabric or steel cords.
- Fabric: Commonly made from materials such as polyester, nylon, or cotton. Fabric carcasses are used in light to medium-duty applications. They provide good flexibility and strength.
- EP (Polyester/Nylon): A popular fabric carcass material, combining the strength of polyester with the flexibility of nylon.
- NN (Nylon/Nylon): Offers high strength and excellent fatigue resistance.
- Steel Cord: Used for heavy-duty and high-tension applications. Steel cord belts provide exceptional strength, durability, and resistance to impact.
- Galvanized Steel: Steel cords are often coated with zinc to enhance corrosion resistance.
3. Additional Components
Additional layers and materials may be included in the conveyor belt design to enhance performance and durability.
- Skim Coats: Thin layers of rubber applied between plies in fabric belts to improve adhesion and protect the carcass from moisture and chemicals.
- Breaker Ply: An additional layer of fabric or steel cords placed between the cover and carcass to enhance impact resistance and reduce cover damage.
- Bottom Cover: Similar to the top cover, the bottom cover protects the carcass from wear and abrasion from the conveyor system components.
4. Special Coatings and Treatments
In some mining applications, conveyor belts may receive special coatings or treatments to address specific operational challenges.
- Fire Retardant Coatings: Used in underground mining to reduce the risk of fire.
- Anti-static Treatments: Applied to reduce the buildup of static electricity, which can be hazardous in certain mining environments.
- Cold-resistant Treatments: Enhance the belt’s performance in low-temperature conditions.
The composition of a conveyor belt for mining applications typically includes:
- Cover Material: Rubber, PVC, or PU for abrasion, chemical, and temperature resistance.
- Carcass Material: Fabric (e.g., EP, NN) or steel cords for strength and flexibility.
- Additional Components: Skim coats, breaker ply, and bottom cover for enhanced durability and performance.
- Special Coatings and Treatments: Fire retardant, anti-static, and cold-resistant for specific operational needs.
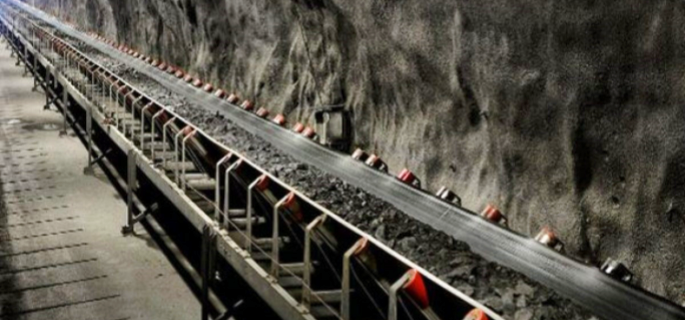
Types and Uses of Conveyor Belt Used in Mining
Detailed Examination of Different Types of Conveyor Belts Used in Mining
Conveyor belts are essential in the mining industry, offering a reliable and efficient means of transporting materials. There are various types of conveyor belts used in mining, each designed to meet specific needs and operational requirements. Understanding these different types and their applications can help mining operations select the most suitable belt for their processes.
Types of Conveyor Belts Used in Mining
Flat Conveyor Belts
Flat conveyor belts are among the most basic and widely used types in mining. They consist of a continuous belt made from materials such as rubber, PVC, or synthetic fabrics. The belt is supported by rollers or a flat surface, creating a smooth pathway for material transportation.
Flat conveyor belts are ideal for transporting bulk materials over short to medium distances. They are commonly used in surface mining operations where materials like coal, ores, and aggregates need to be moved from excavation sites to processing plants or storage areas. Their simplicity and ease of maintenance make them a popular choice for many mining operations.
Troughed Conveyor Belts
Troughed conveyor belts have a U-shaped cross-section, formed by arranging idlers in a trough configuration. This design helps to center the load and prevent spillage, allowing the belt to carry loose bulk materials more effectively.
These belts are particularly suited for transporting loose materials such as coal, sand, and gravel. The troughed shape increases the belt’s capacity and stability, making it suitable for both surface and underground mining operations. Troughed belts can handle higher loads and navigate inclines and declines, making them versatile for various mining environments.
Pipe Conveyor Belts
Pipe conveyor belts are designed to form a closed tube-like shape when loaded, providing an enclosed system for material transport. This design protects the material from environmental elements and prevents spillage, making it an ideal choice for transporting sensitive or hazardous materials.
Pipe conveyor belts are used in scenarios where materials need to be transported over long distances, through complex routes, or in areas with environmental constraints. They are particularly useful in transporting fine or hazardous materials, as the enclosed design minimizes dust and prevents material loss. These belts are often used in both surface and underground mining operations where protection and containment of materials are crucial.
Chevron Conveyor Belts
Chevron conveyor belts have a distinctive V-shaped pattern on the surface, which helps to grip loose materials and prevent them from sliding back on steep inclines. These belts are specifically designed for inclined transportation.
Steel Cord Conveyor Belts
Steel cord conveyor belts are reinforced with steel cables, providing exceptional strength and durability. These belts are designed for heavy-duty applications and can handle high-tension loads over long distances.
Specialized Conveyor Belts for Extreme Conditions
Specialized conveyor belts are designed to withstand extreme conditions such as high temperatures, abrasive materials, or exposure to chemicals. These belts are made from materials that offer enhanced durability, resistance to wear and tear, and the ability to operate in challenging environments.
Specialized conveyor belts are essential in mining operations that involve harsh conditions. For example, heat-resistant belts are used in operations where materials are transported at high temperatures, such as in metal smelting or foundry processes. Similarly, abrasion-resistant belts are used for transporting sharp and abrasive materials like iron ore and quartz. These specialized belts ensure reliability and longevity in demanding mining environments.
The Role of Each Belt Type in Different Mining Processes and Environments
Each type of conveyor belt used in mining plays a specific role in the overall mining process. Understanding the unique characteristics and applications of these belts is essential for optimizing material handling and improving operational efficiency.
Flat Conveyor Belts
- Role: Basic material transport over short to medium distances
- Environment: Surface mining, straightforward transport routes
- Process: Moving bulk materials from excavation to processing or storage
Troughed Conveyor Belts
- Role: Handling loose bulk materials with increased capacity
- Environment: Surface and underground mining, varied terrain
- Process: Transporting coal, sand, gravel with minimal spillage
Pipe Conveyor Belts
- Role: Enclosed transport for sensitive or hazardous materials
- Environment: Long-distance transport, environmentally sensitive areas
- Process: Containing and protecting materials during transport
Specialized Conveyor Belts
- Role: Operating in extreme conditions with enhanced durability
- Environment: High temperatures, abrasive materials, chemical exposure
- Process: Transporting materials in harsh mining environments, ensuring longevity and reliability
The conveyor belt used in mining is a critical component that significantly impacts the efficiency and safety of mining operations. By understanding the different types of conveyor belts, including flat belts, troughed belts, pipe belts, and specialized belts for extreme conditions, mining ope
Uses of Conveyor Belts in Mining Operations
The conveyor belt used in mining plays a pivotal role in various stages of the mining process. Here are some key uses:
- Material Extraction: Conveyor belts are used to transport extracted materials from the mining site to processing areas. This includes raw ore, coal, and other mined substances.
- Processing: During the processing stage, conveyor belts move materials through different processing units, such as crushers, screens, and washing plants, ensuring a continuous flow.
- Waste Management: Conveyor belts are employed to transport waste materials to designated disposal sites, helping to maintain a clean and efficient mining operation.
- Loading and Unloading: Conveyor belts facilitate the loading and unloading of materials onto trucks, trains, or ships for further transportation, streamlining the logistics of mining operations.
- Stockpiling: Conveyor belts are used to create stockpiles of processed materials, providing organized and easily accessible storage solutions.
Conveyor Belt Used in Mining PDF Resources
For those seeking in-depth knowledge about conveyor belts used in mining, various PDF resources are available that provide comprehensive information. These documents often include technical specifications, design considerations, maintenance guidelines, and case studies that illustrate successful implementations in different mining operations. By exploring these resources, mining professionals can gain valuable insights into optimizing their conveyor belt systems for maximum efficiency and safety.
Understanding the different types of conveyor belts used in mining and their specific applications is crucial for selecting the right belt for any mining operation. Whether it’s the simplicity of flat belts, the capacity of troughed belts, the protection of pipe belts, the grip of chevron belts, or the strength of steel cord belts, each type offers unique advantages that cater to specific mining needs.

Conveyor Belt Used in Mining Applications
Material Handling:
- Transporting Raw Materials:
- Conveyor belts are used to transport raw materials such as ore, coal, sand, and gravel from the extraction sites to processing plants. This ensures a continuous and efficient flow of materials, minimizing delays and maximizing productivity.
- In open-pit mining, conveyor belts can span several kilometers, moving vast quantities of materials quickly and efficiently.
- In some operations, conveyor systems are integrated with truck haulage systems to optimize the transportation process.
- Moving Materials Within the Mining Site:
- Within the mining site, conveyor belts facilitate the movement of materials between different stages of the mining process, including from the mining face to the processing plant, stockpiles, and loading areas.
- Conveyors can be designed to handle various types of materials, from fine powders to large rocks, ensuring versatility in their application.
Overburden Removal:
- Efficient Transportation:
- Overburden, the soil, and rock covering a mineral deposit, needs to be removed to access the valuable minerals beneath. Conveyor belts provide a cost-effective and efficient solution for transporting this overburden to designated waste dumps.
- They can handle large volumes of material, reducing the reliance on trucks and other heavy machinery, which are often more expensive to operate and maintain.
- Minimizing Environmental Impact:
- By using conveyor belts for overburden removal, mining operations can minimize their environmental footprint. Conveyor systems can be designed to reduce dust generation and noise pollution, contributing to a more environmentally friendly mining process.
Underground Mining:
- Conveying Extracted Materials:
- In underground mining, conveyor belts are essential for moving extracted materials from the mine to the surface. This process involves navigating through narrow tunnels and shafts, where space is limited, and traditional transportation methods are impractical.
- Belt systems are designed to handle the specific challenges of underground mining, such as sharp turns, steep inclines, and varying loads.
- Suitable for Confined Spaces:
- Conveyor belts used in underground mining are compact and flexible, making them suitable for confined spaces. They can be installed in narrow tunnels and can navigate complex routes with ease, ensuring efficient material transport.
- Modern conveyor systems can also be equipped with automation and remote control features, enhancing safety and operational efficiency in underground environments.
Processing Plants:
- Feeding Materials into Crushers and Grinders:
- In processing plants, conveyor belts play a crucial role in feeding raw materials into crushers, grinders, and other processing equipment. This ensures a consistent and controlled flow of materials, optimizing the processing efficiency and reducing downtime.
- Automated conveyor systems can adjust the feed rate based on the processing requirements, ensuring optimal performance of the equipment.
- Moving Processed Materials:
- After processing, conveyor belts transport the finished products to storage areas or loading zones, where they are prepared for shipment. This includes moving processed minerals to stockpiles, silos, or directly to trucks, trains, or ships for transportation.
- Conveyor belts help streamline the entire processing operation, reducing manual handling and improving overall productivity.
Enhanced Applications and Benefits:
- Customization and Scalability:
- Conveyor belt systems can be customized to meet the specific needs of a mining operation, from the size and type of materials being transported to the layout of the mining site. This flexibility allows for scalable solutions that can grow with the operation.
- Safety and Monitoring:
- Advanced conveyor systems are equipped with safety features such as emergency stop buttons, guards, and automated monitoring systems. These features help prevent accidents and ensure the safety of workers.
- Real-time monitoring allows for the detection of potential issues before they become major problems, reducing downtime and maintenance costs.
- Environmental Considerations:
- Conveyor belts contribute to more sustainable mining practices by reducing the reliance on fossil fuels. They generate fewer emissions compared to traditional transportation methods like trucks.
- Innovations in conveyor belt materials and designs are making them more environmentally friendly, with options for recyclable materials and energy-efficient operation.
By leveraging the advantages of conveyor belts, mining operations can achieve higher efficiency, improved safety, and reduced environmental impact, making them a vital component in the modern mining industry.
How to Choose Conveyor Belt Used in Mining
Choosing the right conveyor belt for mining operations is crucial for ensuring efficiency, safety, and cost-effectiveness. Here is a detailed guide on how to select the appropriate conveyor belt for mining applications:
1. Understand the Type of Material
- Material Properties: Consider the size, weight, abrasiveness, and moisture content of the material to be transported. Different materials may require different belt properties.
- Temperature: Ensure the belt can withstand the temperature of the material and the operating environment.
2. Conveyor Belt Types
- Fabric Belts: Suitable for light to medium-duty applications. These belts are flexible and offer good resistance to abrasion and impact.
- Steel Cord Belts: Ideal for heavy-duty applications, providing high strength and durability. They are often used in long-distance and high-capacity systems.
- Rubber Belts: Commonly used for general mining purposes. They offer good flexibility and resistance to wear and tear.
- PVC and PU Belts: Used for specific applications where resistance to chemicals or oil is necessary.
3. Consider Load and Speed
- Load Capacity: Ensure the belt can handle the maximum load without stretching or breaking.
- Speed: The speed of the conveyor should match the requirements of the mining operation to optimize productivity and reduce wear.
4. Environmental Conditions
- Temperature Range: Choose a belt that can operate efficiently in the temperature range of your mining environment.
- Humidity and Moisture: In wet conditions, select belts with waterproof properties or special coatings to prevent slippage and degradation.
- Chemical Exposure: If the belt will be exposed to chemicals, choose materials that are resistant to chemical corrosion.
5. Durability and Maintenance
- Abrasion Resistance: Select belts with high abrasion resistance for handling sharp or coarse materials.
- Maintenance: Consider belts that are easy to maintain and repair to minimize downtime. Modular belts can be a good choice for easy replacement of damaged sections.
6. Safety and Compliance
- Fire Resistance: In underground mining, belts should be fire-resistant to prevent fire hazards.
- Compliance: Ensure the conveyor belt complies with local and international safety and quality standards.
7. Cost and Efficiency
- Initial Cost vs. Long-term Cost: While high-quality belts may have a higher initial cost, they can offer longer service life and lower maintenance costs.
- Energy Efficiency: Choose belts that reduce energy consumption, contributing to overall operational efficiency.
8. Special Requirements
- Incline or Decline Conveying: If the conveyor needs to operate on an incline or decline, select a belt with appropriate traction and support properties.
- Custom Solutions: For unique mining operations, consider custom-designed belts tailored to specific needs.
Selecting the right conveyor belt for mining involves a thorough understanding of the material, environmental conditions, load capacity, durability, safety, and cost. By carefully evaluating these factors, you can ensure optimal performance, safety, and cost-effectiveness in your mining operations.
Finding the Right Conveyor Belt Used in Mining Operations
Guidance on Selecting the Appropriate Conveyor Belt Used in Mining for Sale
Choosing the right conveyor belt used in mining is critical for ensuring efficient and safe material handling. The selection process involves evaluating various factors to match the specific needs of a mining operation. With numerous options available, understanding the key considerations can help in making an informed decision that enhances productivity and minimizes downtime.
Factors Influencing the Choice of Conveyor Belt Used in Mining
Several factors influence the selection of a conveyor belt used in mining. These factors include the type of material being transported, the width and length of the belt, the required tension, and essential safety features. Below, we discuss these factors in detail and provide examples to illustrate their importance.
1. Material Type
The type of material being transported significantly affects the choice of conveyor belt. Different materials have varying characteristics, such as weight, size, abrasiveness, and moisture content, which determine the belt’s material and design.For transporting sharp and abrasive materials like iron ore, a steel-reinforced conveyor belt would be ideal due to its high resistance to wear and tear. Conversely, for softer materials like coal, a rubber belt would suffice, providing adequate durability without the need for steel reinforcement.
2. Belt Width
The width of the conveyor belt used in mining is another crucial factor. The belt width must accommodate the volume and size of the material being transported, ensuring efficient and smooth operation without spillage.In a large-scale mining operation where significant quantities of bulk material need to be transported, a wider belt (e.g., 1200mm) would be necessary to handle the load effectively. For smaller operations or narrow passageways, a narrower belt (e.g., 800mm) might be more appropriate.
3. Belt Tension
The required tension of the conveyor belt depends on the weight of the material and the distance it needs to be transported. Proper tension ensures that the belt runs smoothly without slipping or breaking.For long-distance transportation of heavy materials, a high-tension conveyor belt with steel cords would be ideal. This type of belt can handle the increased tension required to move large loads over extended distances. In contrast, for shorter distances with lighter materials, a fabric-reinforced belt with lower tension requirements might be sufficient.
4. Safety Features
Safety is paramount in mining operations. The conveyor belt used in mining must include various safety features to protect workers and equipment. These features can range from emergency stop mechanisms to fire-resistant materials.In underground mining, where fire hazards are a significant concern, using a conveyor belt made of fire-resistant materials is crucial. Additionally, incorporating emergency stop switches along the belt’s length can provide a quick shutdown in case of an emergency, preventing accidents and injuries.
5. Environmental Conditions
The operating environment of the mining site also impacts the choice of conveyor belt. Factors such as temperature, humidity, and exposure to chemicals must be considered to ensure the belt’s longevity and performance.In a mining operation located in a region with extreme temperatures, selecting a conveyor belt designed to withstand such conditions is essential. For instance, a belt with heat-resistant properties would be necessary for operations involving high-temperature materials or environments. Similarly, in wet or chemically aggressive environments, a belt with corrosion-resistant features would be ideal.
Making the Right Choice
To select the appropriate conveyor belt used in mining, it’s important to conduct a thorough assessment of the operational requirements and environmental conditions. Consulting with conveyor belt manufacturers and suppliers can provide valuable insights and recommendations based on specific needs. Additionally, reviewing technical specifications and case studies can help in understanding the performance and suitability of different conveyor belt types for various mining applications.
Finding the right conveyor belt used in mining involves careful consideration of multiple factors, including the type of material being transported, the belt’s width and tension, essential safety features, and the environmental conditions of the mining site. By understanding these factors and their impact on the conveyor belt’s performance, mining operations can select a belt that enhances efficiency, safety, and longevity. Investing in the right conveyor belt not only improves productivity but also ensures the smooth and safe transportation of materials, ultimately contributing to the overall success of the mining operation.
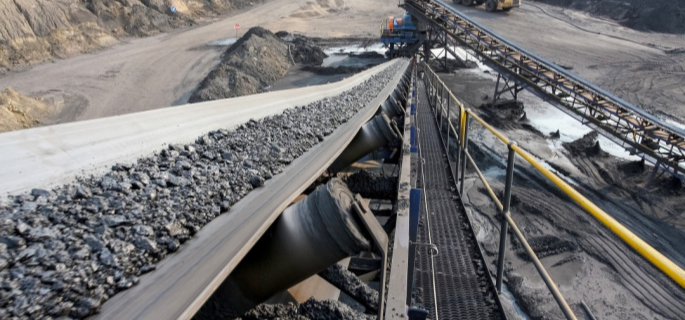
The Manufacturing Landscape About Conveyor Belt Used in Mining
Profiles of Leading Mining Conveyor Belt Manufacturers
The global mining industry relies heavily on the quality and reliability of conveyor belts to ensure smooth and efficient operations. Several manufacturers specialize in producing high-performance conveyor belts used in mining, each bringing unique strengths and innovations to the market. Understanding the profiles of these leading manufacturers can help mining operations choose the best supplier for their needs.
1. GRAM Conveyor
GRAM Conveyor is a distinguished company in the conveyor belt industry, particularly recognized for its expertise in designing and manufacturing conveyor systems for the mining sector. With a commitment to quality and innovation, GRAM Conveyor has established itself as a reliable partner for mining operations around the world.
- Utilizes cutting-edge materials and manufacturing processes to ensure long-lasting performance in harsh mining conditions.
- Focuses on sustainability throughout the product lifecycle, from manufacturing to disposal.
- Implements technologies that minimize energy loss and enhance operational efficiency.
- Combines global standards with local expertise to deliver customized solutions tailored to specific regional requirements.
2.Fenner Dunlop
Fenner Dunlop is a prominent name in the conveyor belt industry, particularly known for its expertise in producing mining conveyor belts. With over 150 years of experience, the company offers a wide range of conveyor belts tailored for various mining applications.
- Extensive product range including steel cord, fabric, and solid woven belts
- Advanced technology for enhanced durability and performance
- Strong focus on research and development to innovate new products
- Comprehensive support services including installation and maintenance
2. Continental AG
Continental AG is a global leader in the manufacturing of conveyor belts, providing solutions for various industries, including mining. The company is renowned for its high-quality products and commitment to sustainability.
- Use of environmentally friendly materials and production processes
- Advanced monitoring systems for real-time belt performance tracking
- Extensive global network for timely support and service
- Innovative solutions like the ContiTech series for high-stress environments
3. Bridgestone Corporation
Bridgestone Corporation, a well-known name in the rubber industry, also excels in producing robust conveyor belts used in mining. Their belts are designed to withstand the harsh conditions typical of mining operations.
- High tensile strength belts for heavy-duty applications
- Focus on safety with fire-resistant and anti-static properties
- Continuous innovation in belt materials and design
- Strong after-sales service and technical support
4. Goodyear Rubber Products
Profile: Goodyear Rubber Products, a division of Veyance Technologies, has a long history of manufacturing reliable conveyor belts for the mining industry. They are known for their durable and efficient belt solutions.
- Wide range of belt types including textile, steel cord, and specialty belts
- Emphasis on customization to meet specific client needs
- Strong R&D team focused on developing cutting-edge products
- Comprehensive training programs for customers on belt maintenance and safety
5. Sparks Belting
Sparks Belting is a lesser-known but highly reputable manufacturer specializing in conveyor belts for mining and other heavy industries. They provide tailored solutions to meet unique operational demands.
- Custom belt fabrication to meet specific operational requirements
- High-performance materials for increased belt life and efficiency
- Excellent customer service with quick response times
- Focus on sustainability and eco-friendly production methods
Importance of Choosing a Reliable Manufacturer
Selecting a reliable manufacturer for conveyor belts used in mining is crucial for several reasons. A trustworthy manufacturer not only provides high-quality products but also offers comprehensive support and services that are essential for the longevity and efficiency of mining operations. Here are some key aspects to consider:
1. Quality Assurance
Reliable manufacturers adhere to stringent quality control processes to ensure their products meet the highest standards. This includes using premium materials, employing advanced manufacturing techniques, and conducting thorough testing to ensure durability and performance.
2. Innovative Solutions
Leading manufacturers invest heavily in research and development to create innovative products that can withstand the demanding conditions of mining operations. These innovations can lead to improved efficiency, reduced downtime, and enhanced safety.
3. Comprehensive Support
A good manufacturer offers more than just products. They provide a range of support services, including installation, maintenance, training, and emergency repairs. This support is vital for keeping the conveyor systems running smoothly and minimizing operational disruptions.
4. Customization Options
Every mining operation has unique requirements. Reliable manufacturers offer customization options to tailor conveyor belts to specific needs, ensuring optimal performance and compatibility with existing systems.
5. Sustainability
In today’s environmentally conscious world, choosing a manufacturer committed to sustainability is important. This includes using eco-friendly materials, reducing waste, and implementing energy-efficient production processes.
The conveyor belt used in mining is a critical component that significantly impacts the efficiency and safety of mining operations. By understanding the profiles of leading manufacturers such as Fenner Dunlop, Continental AG, Bridgestone Corporation, Goodyear Rubber Products, and Sparks Belting, mining companies can make informed decisions when selecting a supplier. Emphasizing the importance of quality, innovation, comprehensive support, customization, and sustainability, these manufacturers stand out in the industry. Choosing a reliable manufacturer ensures that the conveyor belt systems not only meet operational demands but also contribute to the overall success and sustainability of mining activities.
Conveyor Belt Used in Mining Underground Excellence
The Unique Challenges and Requirements for Conveyor Belts in Underground Mining
Underground mining presents a unique set of challenges that require specialized solutions for material transportation. The conveyor belt used in mining, particularly in underground environments, must be designed to address these specific challenges to ensure efficient and safe operations.
Space Constraints and Complex Routes
One of the primary challenges in underground mining is the limited space and the complex network of tunnels. Conveyor belts used in these settings must be flexible enough to navigate tight corners and steep inclines. Unlike surface mining, where space is more abundant, underground mining requires conveyor belts that can adapt to the confined and often irregular pathways within the mine.
Durability and Robustness
The conveyor belt used in mining underground must be exceptionally durable to withstand harsh conditions. These belts are exposed to abrasive materials, high impact loads, and sometimes even corrosive environments. The materials used in the construction of these belts must be robust enough to handle such extreme conditions without frequent maintenance or replacement.
Dust and Moisture Management
Underground mines often have higher levels of dust and moisture compared to surface mines. Conveyor belts used in mining must be able to operate efficiently in these conditions. Dust suppression systems and moisture-resistant materials are crucial to maintaining the belt’s integrity and performance. Effective dust management also contributes to a safer working environment by reducing the risk of respiratory issues among miners.
Safety Standards and Technological Advancements Tailored for Underground Mining Conveyor Systems
Safety is paramount in underground mining operations, and the conveyor belt used in mining plays a critical role in ensuring the safety of the workforce. Various safety standards and technological advancements have been developed to enhance the safety and efficiency of these conveyor systems.
Fire Resistance
One of the most significant safety concerns in underground mining is the risk of fire. Conveyor belts used in mining must comply with stringent fire safety standards. Fire-resistant belts are designed to minimize the spread of flames and produce less smoke, providing additional time for workers to evacuate in case of a fire. Materials like PVC and specially treated rubber are commonly used to enhance the fire-resistant properties of these belts.
Anti-Static Properties
Underground mines can be prone to static electricity buildup, which poses a risk of sparks and potential explosions. Conveyor belts with anti-static properties are essential to prevent such occurrences. These belts are treated to dissipate static electricity, reducing the risk of accidental ignition of flammable gases or dust present in the mine.
Real-Time Monitoring and Automation
Technological advancements have led to the development of real-time monitoring and automation systems for conveyor belts used in mining. Sensors and monitoring devices can track the belt’s performance, detect anomalies, and provide real-time data on belt speed, tension, and alignment. Automated systems can adjust the belt’s operation based on these data, ensuring optimal performance and reducing the risk of mechanical failures.
Emergency Stop Mechanisms
Safety mechanisms such as emergency stop systems are crucial in underground mining conveyor belts. These systems allow workers to quickly halt the conveyor belt in case of an emergency, preventing accidents and potential injuries. Emergency stop buttons are strategically placed along the conveyor’s length to ensure they are easily accessible in case of an urgent situation.
Maintenance and Inspection
Regular maintenance and inspection are vital to the safe operation of conveyor belts in underground mining. Maintenance schedules should be strictly adhered to, and belts should be inspected for wear and tear, misalignment, and other issues. Advanced technologies like predictive maintenance, which uses data analytics to predict potential failures before they occur, can significantly enhance the reliability and safety of conveyor belt systems.
The conveyor belt used in mining, particularly in underground environments, must be designed to address unique challenges and adhere to stringent safety standards. From navigating confined spaces to managing dust and moisture, these belts require robust materials and advanced technologies to operate efficiently and safely. Fire-resistant and anti-static properties, real-time monitoring, and emergency stop mechanisms are crucial features that enhance the safety and reliability of underground mining conveyor systems. By incorporating these advancements, mining operations can ensure the smooth and safe transport of materials, ultimately contributing to the overall success and safety of the mining process.
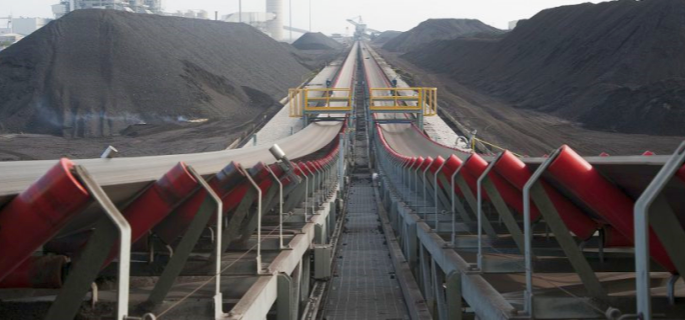
Invest in Efficiency of Conveyor Belt Used in Mining
How to Find High-Quality Mining Conveyor Belts for Sale
Finding the right conveyor belt used in mining is a critical step for ensuring efficient material handling and overall operational success. With numerous suppliers and options available, it’s essential to know where to look and what to consider when searching for high-quality mining conveyor belts for sale. Here are some key strategies to help you identify the best conveyor belts for your mining needs.
Research Reputable Suppliers
Start by researching reputable suppliers who specialize in conveyor belts for mining. Look for companies with a proven track record of providing high-quality products and excellent customer service. Suppliers such as Fenner Dunlop, Continental AG, and Bridgestone Corporation are known for their reliable and durable mining conveyor belts.
Read Reviews and Testimonials
Customer reviews and testimonials can provide valuable insights into the performance and reliability of conveyor belts from different suppliers. Look for feedback on the durability, efficiency, and ease of maintenance of the belts. Positive reviews from other mining operations can be a good indicator of a high-quality product.
Request Product Samples
Before making a large purchase, request product samples from potential suppliers. Testing the samples in your mining environment can help you assess their suitability for your specific needs. This hands-on evaluation can reveal critical performance characteristics that may not be evident from product specifications alone.
Compare Technical Specifications
Review and compare the technical specifications of conveyor belts from different suppliers. Pay attention to details such as tensile strength, abrasion resistance, and temperature tolerance. Ensure that the belts meet the specific requirements of your mining operations, such as load capacity and environmental conditions.
Consult Industry Experts
Industry experts and consultants can provide valuable advice on selecting the best conveyor belt for your mining operations. They can help you understand the latest technologies and trends in conveyor belt manufacturing, ensuring that you make an informed decision.
Factors to Consider When Purchasing a Conveyor Belt for Mining Operations
When purchasing a conveyor belt used in mining, several critical factors should be considered to ensure that the chosen belt meets the operational demands and provides long-term value. Here are five key factors to consider:
1. Cost
Cost is an important factor when purchasing a conveyor belt, but it should not be the sole consideration. While it’s essential to stay within budget, opting for the cheapest option can often lead to higher costs in the long run due to frequent replacements and maintenance. Consider the total cost of ownership, which includes the initial purchase price, installation, maintenance, and potential downtime costs.
2. Durability
Durability is crucial for conveyor belts used in mining, as they must withstand harsh conditions and heavy loads. Look for belts made from high-quality materials that offer excellent resistance to abrasion, impact, and chemical exposure. Durable belts reduce the frequency of replacements and maintenance, contributing to increased operational efficiency.
3. Maintenance Requirements
Consider the maintenance requirements of the conveyor belt. Easy-to-maintain belts reduce downtime and maintenance costs. Look for features such as easy access for inspection and repairs, modular components that can be quickly replaced, and advanced monitoring systems that detect issues before they lead to failures.
4. Environmental Conditions
The environmental conditions of the mining site should influence the choice of conveyor belt. Factors such as temperature extremes, humidity, and exposure to chemicals can affect the belt’s performance and lifespan. Choose belts that are specifically designed to operate in your mine’s environmental conditions.
5. Load Capacity
Ensure that the conveyor belt can handle the maximum load expected in your mining operations. The belt’s width, tensile strength, and overall design should match the volume and weight of the materials being transported. Overloading a belt can lead to premature wear and failure.
Investing in the right conveyor belt used in mining is crucial for the efficiency and safety of mining operations. By researching reputable suppliers, reading reviews, testing product samples, comparing technical specifications, and consulting with industry experts, you can find high-quality mining conveyor belts for sale. Consider factors such as cost, durability, maintenance requirements, environmental conditions, and load capacity when making your purchase decision. By carefully evaluating these factors, you can select a conveyor belt that meets your specific needs, enhances operational efficiency, and provides long-term value for your mining operations.
Maintaining Conveyor Belt Used in Mining
Maintaining conveyor belts used in mining is critical to ensure continuous operation, safety, and longevity of the equipment. Here are key maintenance practices:
Regular Inspections
Visual Inspections:
- Check for signs of wear and tear, such as fraying edges, cracks, and cuts on the belt surface.
- Look for misalignment of the belt and any abnormal noises during operation.
- Inspect the belt for any buildup of materials that might affect its performance.
Mechanical Inspections:
- Inspect the conveyor structure, including rollers, pulleys, and idlers, for proper alignment and wear.
- Ensure that the tension of the belt is correct and adjust if necessary.
- Check for proper lubrication of bearings and moving parts.
Preventive Maintenance
Scheduled Maintenance:
- Develop and adhere to a regular maintenance schedule based on the manufacturer’s recommendations and the operating conditions of the conveyor system.
- Perform thorough inspections and maintenance tasks during scheduled downtimes to avoid unexpected breakdowns.
Component Replacement:
- Replace worn or damaged components promptly to prevent further damage and ensure the efficient operation of the conveyor system.
- Keep an inventory of critical spare parts to minimize downtime during repairs.
Cleaning and Lubrication
Cleaning:
- Regularly clean the belt and surrounding components to remove debris, dirt, and material buildup that can cause wear and reduce efficiency.
- Use appropriate cleaning methods and tools to avoid damaging the belt.
Lubrication:
- Lubricate bearings, rollers, and other moving parts as per the manufacturer’s guidelines to reduce friction and wear.
- Ensure that lubricants used are suitable for the specific environment and operating conditions of the conveyor.
Monitoring and Diagnostics
Automated Monitoring Systems:
- Utilize automated monitoring systems to continuously track the condition of the conveyor belt and its components.
- Implement sensors to detect temperature changes, belt slippage, misalignment, and other anomalies.
Data Analysis:
- Analyze data collected from monitoring systems to predict potential failures and schedule preventive maintenance.
- Use diagnostic tools to identify specific issues and address them before they escalate.
Training and Safety
Training:
- Provide comprehensive training for maintenance personnel on the proper inspection, maintenance, and repair techniques for conveyor belts.
- Ensure that workers are familiar with safety procedures and the use of personal protective equipment (PPE).
Safety Protocols:
- Implement and enforce strict safety protocols to protect workers during maintenance activities.
- Use lockout/tagout procedures to ensure that the conveyor system is de-energized and safe to work on during maintenance.
Environmental Considerations
Dust Control:
- Implement dust control measures, such as dust collectors and suppression systems, to reduce the accumulation of dust on the belt and surrounding components.
- Regularly clean and maintain dust control equipment to ensure its effectiveness.
Spillage Management:
- Install skirting and sealing systems to minimize material spillage from the conveyor belt.
- Regularly inspect and maintain these systems to prevent excessive material loss and environmental contamination.
Record Keeping
Maintenance Logs:
- Maintain detailed records of all maintenance activities, including inspections, repairs, and replacements.
- Use these records to track the history of the conveyor belt and identify patterns that may indicate recurring issues.
Performance Metrics:
- Monitor key performance metrics, such as belt speed, load capacity, and operational efficiency, to assess the effectiveness of maintenance practices.
- Use this data to optimize maintenance schedules and improve overall performance.
By implementing these maintenance practices, mining operations can ensure the reliable and efficient performance of conveyor belts, reducing downtime and extending the lifespan of the equipment.
FAQs About Conveyor Belt Used in Mining
The most commonly used type of belt in mines is the troughed conveyor belt. This belt features a U-shaped cross-section formed by a series of idlers arranged in a trough configuration. The design of the troughed conveyor belt helps to center the load and prevent material spillage, making it ideal for transporting loose bulk materials like coal, ores, and aggregates. Troughed belts are widely used in both surface and underground mining due to their versatility and ability to handle various types of materials efficiently. Their capacity to carry large volumes of material over long distances and navigate inclines and declines makes them indispensable in mining operations.
In mining operations, several types of conveyor belts are employed to meet specific needs. These include:
Flat Conveyor Belts: These are simple and widely used for short to medium-distance transportation of bulk materials.
Troughed Conveyor Belts: Ideal for transporting loose materials with their U-shaped design to prevent spillage.
Pipe Conveyor Belts: These belts form an enclosed tube shape, protecting the material from environmental elements and preventing spillage.
Chevron Conveyor Belts: Featuring a V-shaped pattern, these belts are designed to transport materials on steep inclines without rollback.
Steel Cord Conveyor Belts: Reinforced with steel cables, these belts are used for heavy-duty applications requiring high tensile strength and durability.
Each type is chosen based on the specific requirements of the mining operation, including material type, transportation distance, and environmental conditions.
Conveyor belts in mining are primarily used for the efficient transportation of materials. Their main functions include:
Material Extraction: Moving raw materials from the mining site to processing areas.
Processing: Transporting materials through various stages of processing, such as crushing, screening, and washing.
Waste Management: Conveying waste materials to designated disposal areas, maintaining a clean and efficient operation.
Loading and Unloading: Facilitating the transfer of materials onto trucks, trains, or ships for further transportation.
Stockpiling: Creating organized and accessible stockpiles of processed materials.
Conveyor belts enhance productivity, reduce manual labor, and improve safety by providing a continuous, automated flow of materials.
The thickness of a mining conveyor belt varies depending on the type of belt and its intended use. Generally, mining conveyor belts range from 5mm to 20mm in thickness. Factors influencing belt thickness include the material being transported, the required tensile strength, and the environmental conditions.
Examples:
Flat Conveyor Belts: Typically around 5mm to 10mm thick, suitable for lighter loads and shorter distances.
Steel Cord Conveyor Belts: These belts can be thicker, often ranging from 15mm to 20mm, designed to handle heavy loads and high-tension applications.
Chevron Conveyor Belts: With their patterned surface, these belts are usually around 10mm to 15mm thick, ideal for transporting materials on steep inclines.
Selecting the appropriate belt thickness is crucial for ensuring durability, efficiency, and safety in mining operations.
A mining belt is primarily made of a combination of rubber, fabric, and steel cords. The outer layer, usually made of rubber, provides resistance to abrasion and environmental conditions, making it durable for the harsh environments of mining operations. Inside the rubber layers, there are fabric layers made from materials like polyester, nylon, or aramid, which add flexibility and strength. For heavy-duty applications, steel cords are integrated within the belt, providing high tensile strength and reducing the risk of elongation under heavy loads. These steel cords are coated with zinc to protect against corrosion. The combination of these materials ensures the belt can handle the extreme conditions of mining, such as heavy impacts, sharp materials, and high loads.
The speed of a mining conveyor belt can vary significantly depending on the specific application and design of the system. Typically, mining conveyor belts move at speeds ranging from 1 to 6 meters per second (approximately 3.3 to 19.7 feet per second). The speed is determined by factors such as the type of material being transported, the distance it needs to cover, and the capacity requirements of the mining operation. Higher speeds are often used for transporting lighter materials over longer distances, while lower speeds are more common for heavy, bulky materials or shorter transport distances. The optimal speed ensures efficient material handling while maintaining the longevity and reliability of the conveyor system.
Last Updated on August 6, 2024 by Jordan Smith
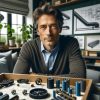
Jordan Smith, a seasoned professional with over 20 years of experience in the conveyor system industry. Jordan’s expertise lies in providing comprehensive solutions for conveyor rollers, belts, and accessories, catering to a wide range of industrial needs. From initial design and configuration to installation and meticulous troubleshooting, Jordan is adept at handling all aspects of conveyor system management. Whether you’re looking to upgrade your production line with efficient conveyor belts, require custom conveyor rollers for specific operations, or need expert advice on selecting the right conveyor accessories for your facility, Jordan is your reliable consultant. For any inquiries or assistance with conveyor system optimization, Jordan is available to share his wealth of knowledge and experience. Feel free to reach out at any time for professional guidance on all matters related to conveyor rollers, belts, and accessories.