Optimizing Underground Conveyor Belt Operations
Underground conveyor belts play a pivotal role in mining operations, serving as the lifeline for transporting materials from deep within the earth to the surface. The efficiency and reliability of these conveyor systems are critical in underground settings, where challenging conditions demand robust equipment. An effective underground conveyor belt not only enhances productivity but also ensures the safety of the mining personnel by enabling smooth and continuous operations. Understanding these systems’ significance helps in appreciating the technological strides in mining logistics.
What are Underground Conveyor Belts
Definition and Basic Mechanics
An underground conveyor belt is a specialized conveyor system designed for the unique demands of subterranean mining operations. These belts are engineered to transport mined materials such as coal, ore, and other resources over long distances, through complex mine layouts, and from deep within the earth to the surface. The basic mechanics involve a continuous belt made from durable materials that is driven by motorized pulleys and rollers. The belt loops over a series of frames that support it within the mine’s shafts and tunnels.
Differences Between Underground and Overland Conveyor Systems
- Environmental Conditions: Underground conveyor belts operate in harsh environments where they are exposed to dust, moisture, and abrasive materials, unlike overland conveyors that typically navigate less hostile conditions.
- Design and Material Use: The materials used for underground conveyor belt system are selected for their durability and resistance to tearing, puncturing, and fire hazards. Overland conveyors may use lighter materials since they face fewer environmental threats.
- Safety Features: Safety is paramount in underground operations, leading to stringent standards for underground conveyor belts in terms of fire resistance and emission controls, which are less critical for overland systems.
- Maintenance Accessibility: Maintaining an underground conveyor belt is more challenging due to limited access and confined spaces, requiring more compact and modular design solutions compared to overland systems.
- Energy Efficiency: The design of underground conveyor belts often emphasizes energy efficiency to handle the high costs and logistical challenges of operating in a subterranean environment.
- Cost Implications: The initial installation and ongoing maintenance costs for underground conveyor belts are generally higher due to their robust construction and the complexity of the environment in which they operate.
- Length and Scale: Underground belts are often shorter than overland belts due to the confined spaces of mine shafts, although they must handle similar or greater loads.
- Conveyor Routing: Underground conveyor belts frequently need to navigate complex routes with multiple vertical and horizontal turns; overland conveyors typically have more straightforward, linear routes.
Understanding these differences is crucial for anyone involved in the design, operation, or maintenance of underground conveyor belt systems, as they impact the overall efficiency and safety of mining operations.
Key Manufacturers and Suppliers of Underground Conveyor Belts
Overview of Leading Manufacturers
The market for underground conveyor belts is dominated by several key manufacturers renowned for their robust and innovative solutions tailored to meet the harsh conditions of subterranean mining. Among them, West River Conveyors stands out as a leader in providing highly specialized underground conveyor belt systems. Other notable companies include:
- Continental AG: Known for their high-end, durable conveyor belts, Continental AG offers technologies that enhance efficiency and safety in underground mining operations.
- Bridgestone Corporation: Bridgestone adapts its expertise in rubber technology to produce underground conveyor belts that are highly resistant to the tough mining environment.
- Fenner Dunlop: Specializing in mining conveyor belts, Fenner Dunlop focuses on belts that offer exceptional fire resistance and longevity.
- Komatsu Mining Corp.: They provide comprehensive conveyor systems that include belts specifically designed for underground mining applications.
- Bando Chemical Industries: With a strong focus on research and development, Bando produces high-quality conveyor belts that cater to the specific needs of underground mining.
- Phoenix Conveyor Belt Systems: Phoenix designs conveyor belts that are robust, with specific enhancements for high-speed and large-capacity underground mining operations.
Technological and Material Advancements
The manufacturers of underground conveyor belts continuously invest in research and development to push the boundaries of technology in materials and design, ensuring their products can withstand the demanding conditions of underground mines. Innovations include:
- High-Tensile Fabrics: These fabrics increase the belt’s strength and reduce the likelihood of tears and punctures, which are common in rocky underground environments.
- Advanced Rubber Compounds: Enhanced rubber compounds improve fire resistance and reduce the risk of belt ignition, a critical safety aspect in underground mining.
- Energy-Efficient Designs: Newer belt designs focus on reducing energy consumption, which is crucial for mines looking to lower operational costs and environmental impact.
- Smart Conveyor Technologies: Integration of sensors and monitoring technologies help in real-time condition monitoring of the belt, predicting maintenance needs and avoiding downtime.
- Modular and Scalable Designs: Some manufacturers offer modular belt systems that can be easily expanded or modified as the mine develops or as production needs change.
These advancements by manufacturers of underground conveyor belts not only enhance the operational efficiency and safety of the mining operations but also contribute to significant cost savings over the life of the mining project. Understanding the capabilities and offerings of these key players helps mining operations choose the right partners to meet their specific underground conveyor needs.
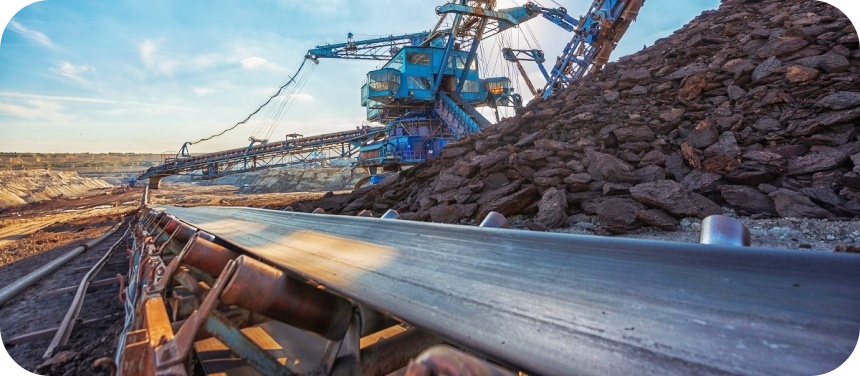
Design and Structure of Underground Conveyor Belts
Structural Design Considerations
The design and structure of underground conveyor belts are crucial for ensuring the efficiency, durability, and safety of the conveyor system. Here are five key considerations:
- Belt Material: The choice of material is critical for withstanding the abrasive and harsh environments of underground mining. Materials need to be tough, resistant to cuts, abrasions, and punctures.
- Belt Width and Thickness: The width and thickness of the belt must be sufficient to handle the expected load and throughput. Wider and thicker belts are often used in higher capacity environments to ensure stability and longevity.
- Conveyor Frame and Support: The frame of the conveyor must be robust enough to support the weight of the loaded belt and withstand the harsh underground conditions. This includes selecting materials that are resistant to corrosion and deformation.
- Drive and Tension Systems: Efficient drive systems are essential for the smooth operation of underground conveyor belts. Tensioning mechanisms ensure the belt operates smoothly without slippage or excessive wear.
- Safety Features: Features such as emergency stop systems, belt alignment, and tear detection are crucial for the safe operation of underground conveyors. These systems help prevent accidents and reduce downtime.
Importance of Material Selection and Design Specifics
The selection of appropriate materials and the specifics of the conveyor belt design are vital for both durability and operational efficiency. Key elements include:
- Steel-Cord Rubber Belts: For high strength and durability, steel-cord rubber belts are often used in underground mining operations. These belts are designed to handle high tensions and are less prone to elongation compared to fabric belts.
- Fire Resistance: Given the potential for fires in underground mining environments, belts must be designed with materials that are fire-resistant or self-extinguishing to meet safety regulations.
- Impact Resistance: The belt must be able to absorb impacts from large, heavy, or sharp materials that are commonly handled in mining operations.
- Flexibility: Despite their strength, belts must also maintain flexibility to navigate through tight and complex conveyor paths underground.
- Wear Resistance: The ability of the belt to resist wear and tear extends its operational life and reduces maintenance costs. This includes resistance to harsh mining elements like oils, greases, and various chemicals.
- Low Stretch: Low-stretch belts are essential in underground settings to maintain consistent tension over long distances, reducing the workload on the drive systems.
- Energy Efficiency: Advanced materials and designs can reduce the amount of energy required to operate the belts, which is a significant factor in total mining costs.
- Ease of Maintenance: Designing belts with modular components or features that allow for easy repairs and maintenance can significantly reduce downtime and operational costs.
- Customization: Many underground operations require customized belt designs to meet specific mining conditions, load requirements, and transportation distances.
- Environmental Factors: Consideration of the environmental impact of materials and the production process of the belts also plays a role in the selection process, aiming to reduce the overall environmental footprint of mining operations.
These design specifics ensure that underground conveyor belts not only meet the demanding conditions of underground mining but also contribute to the overall safety and efficiency of mining operations.
Innovations in Conveyor Technology for Underground Conveyor Belts
Innovative Features
The technological landscape of underground conveyor belts is evolving rapidly, incorporating a range of innovative features that enhance both functionality and safety. Among these innovations, some noteworthy ones include:
- Smart Monitoring Systems: Integration of IoT sensors that provide real-time data on belt health, speed, and efficiency, enabling proactive maintenance and operational adjustments.
- Advanced Material Technologies: Use of new composite materials for belts that are lighter, stronger, and more durable than traditional materials.
- Energy Recovery Systems: Systems that capture the energy generated by the conveyor during downhill segments and convert it into electricity, reducing overall energy consumption.
- Improved Fire Resistance: Development of new materials and coatings that significantly enhance fire resistance, crucial in underground environments.
- Automated Inspection Systems: Drones and robotic systems that perform regular inspections of underground conveyor belts to detect wear, alignment issues, or other potential faults.
- Enhanced Load Sensing: Technology that dynamically measures load distribution across the belt, optimizing throughput and reducing wear.
- Modular Design: Conveyor systems designed with modular components for quick assembly and disassembly, facilitating easier maintenance and modifications.
- Virtual Reality Training: Use of VR for training personnel on the maintenance and operation of underground conveyor belts without the need to access the site.
Latest Advancements in Conveyor Frame Design
The frame design of underground conveyor belts has also seen significant advancements that impact their effectiveness and sustainability in mining operations:
- Lightweight Materials: Utilization of high-strength, lightweight alloys that reduce the overall weight of the conveyor structure, thereby saving energy and decreasing operational costs.
- Corrosion-Resistant Coatings: Application of advanced coatings that prevent rust and corrosion, which can be particularly problematic in the damp and variable conditions found in underground mines.
- Flexible Joint Systems: Innovative joint designs that allow the conveyor frame to flex in response to shifts in the mine’s structure, thus preventing damage.
- Enhanced Structural Integrity: Computational modeling and materials science have led to designs that maximize the load-bearing capabilities while minimizing material use and weight.
- Shock Absorption Features: Integration of shock absorbers that reduce the impact of heavy loads on the conveyor belt and frame, extending the lifespan of both.
- Scalable Designs: Frames designed to be easily extended or retracted to accommodate changes in mining operations or shifting production demands.
- Eco-friendly Manufacturing Processes: Adoption of greener manufacturing techniques that reduce the carbon footprint associated with producing conveyor frames.
- Integrated Systems: Frames that integrate seamlessly with other mining infrastructure, such as loaders and dump systems, enhancing the overall efficiency of the mining operation.
These innovations in the design and technology of underground conveyor belts not only optimize the extraction and transportation processes but also contribute to a safer and more environmentally responsible mining environment. Each advancement plays a critical role in addressing the challenges faced by today’s underground mining operations, pushing the boundaries of what is possible in the industry.
Safety and Environmental Considerations of Underground Conveyor Belts
Safety Features of Underground Conveyor Belts
Safety is paramount in underground mining operations, especially concerning conveyor belt systems. The inherent risks associated with these environments necessitate robust safety features to ensure the well-being of workers and the integrity of operations. Here, we delve into seven essential safety features specifically tailored for underground conveyor belts, emphasizing fire resistance and dust control.
Fire Resistance Measures
The underground conveyor belt environment poses a significant fire hazard due to the presence of combustible materials and the potential for friction-induced heat generation. To mitigate this risk, conveyor belts are constructed using fire-resistant materials such as neoprene or synthetic rubber compounds. These materials have high resistance to ignition and flame spread, minimizing the likelihood of conveyor belt fires.
In addition to fire-resistant materials, conveyor belt systems are equipped with advanced fire detection and suppression systems. Smoke and heat detectors strategically placed along the conveyor belt continuously monitor for any signs of fire. Upon detection, automatic sprinkler systems or chemical suppression agents are activated to extinguish the fire promptly, preventing its escalation and minimizing damage to equipment and personnel.
Dust Control Mechanisms
Dust emissions are a prevalent concern in underground mining operations, particularly during material handling processes involving conveyor belts. Dust particles not only pose respiratory health risks to workers but also increase the likelihood of equipment malfunctions and explosions. To address this issue, modern underground conveyor belt systems incorporate several dust control mechanisms.
One effective method is the installation of dust suppression systems along the conveyor route. These systems utilize water sprays or misting nozzles to dampen airborne dust particles, preventing their dispersal into the surrounding environment. Additionally, enclosed conveyor belt structures equipped with sealed covers help contain dust emissions, minimizing exposure to workers and reducing the accumulation of dust on equipment and surfaces.
Environmental Impacts and Mitigation Strategies
In addition to safety concerns, underground conveyor belt systems also pose various environmental impacts, ranging from air and water pollution to habitat disruption. Here, we examine nine environmental impacts associated with underground mining operations and discuss how modern conveyor belt designs are addressing these concerns through innovative mitigation strategies.
Air Pollution
The operation of underground conveyor belts can contribute to air pollution through the release of dust particles and particulate matter into the atmosphere. These airborne pollutants not only degrade air quality but also pose health risks to nearby communities and ecosystems. To mitigate air pollution, conveyor belt systems are equipped with efficient dust suppression mechanisms, as discussed earlier, to minimize the generation and dispersion of dust emissions.
Water Contamination
Another significant environmental impact of underground mining activities is the potential contamination of water sources due to the discharge of wastewater and chemical pollutants. Conveyor belt systems play a crucial role in material transport within mining operations, and any leakage or spillage of hazardous substances from the conveyor can result in water contamination. To prevent this, underground conveyor belts are designed with leak-proof seals and containment systems to prevent the escape of fluids and contaminants into the surrounding environment.
Habitat Disruption
The construction and operation of underground conveyor belts can lead to habitat disruption and fragmentation, particularly in ecologically sensitive areas. To mitigate habitat disruption, conveyor belt routes are carefully planned to minimize disturbance to wildlife habitats and sensitive ecosystems. Additionally, environmental impact assessments are conducted to identify potential impacts on biodiversity and ecosystem services, allowing for the implementation of mitigation measures such as habitat restoration and wildlife corridors.
Safety and environmental considerations are of utmost importance in underground mining operations, particularly concerning conveyor belt systems. By incorporating robust safety features and innovative mitigation strategies, modern underground conveyor belt system designs strive to ensure the protection of both workers and the environment, fostering sustainable and responsible mining practices.
This section will expand upon these topics, delving into the intricacies of safety features essential for underground conveyor belts and exploring the environmental impacts associated with such systems. Through comprehensive analysis and discussion, readers will gain insights into the challenges and solutions at the intersection of safety, environmental stewardship, and mining operations.
Installation and Maintenance Challenges of Underground Conveyor Belts
Challenges in Installing and Maintaining Underground Conveyor Systems
Installing and maintaining underground conveyor belt systems present a myriad of challenges due to the unique characteristics of underground mining environments. From initial setup to ongoing maintenance, ensuring the smooth operation of conveyor systems requires careful planning, specialized equipment, and adherence to stringent safety protocols. In this section, we explore eight key challenges encountered in the installation and maintenance of underground conveyor systems.
Limited Access and Space Constraints
One of the primary challenges in installing underground conveyor belts is the limited access and confined spaces within underground mining environments. Unlike surface installations, which offer ample space for equipment maneuverability, underground settings impose tight constraints that necessitate innovative installation techniques and compact conveyor designs. Overcoming these challenges often involves modular conveyor components that can be assembled underground or specialized equipment capable of navigating narrow tunnels and shafts.
Ground Instability and Geological Hazards
Ground instability and geological hazards pose significant risks to underground conveyor systems during both installation and operation. The dynamic nature of underground geology, including rockfalls, subsidence, and seismic activity, can compromise the structural integrity of conveyor installations, leading to equipment damage and safety hazards. Mitigating these risks requires thorough geological surveys, engineering assessments, and the implementation of reinforcement measures such as rock bolting and ground support systems.
Harsh Operating Conditions
Underground mining environments subject conveyor systems to harsh operating conditions characterized by high humidity, temperature extremes, abrasive materials, and corrosive substances. These conditions accelerate equipment wear and deterioration, necessitating regular maintenance and the use of durable materials resistant to corrosion, abrasion, and environmental degradation. Additionally, specialized sealing mechanisms and protective coatings are employed to safeguard conveyor components from moisture ingress and chemical exposure.
Ventilation and Air Quality
Maintaining adequate ventilation and air quality is crucial for the health and safety of underground mining personnel and the optimal performance of conveyor systems. However, the confined nature of underground spaces and the presence of dust, fumes, and other airborne contaminants pose challenges to effective ventilation and air quality management. Implementing ventilation systems with sufficient airflow and filtration capabilities is essential for controlling airborne pollutants and ensuring a safe working environment for conveyor maintenance personnel.
Tips and Strategies for Effective Maintenance
Effective maintenance is paramount to ensuring the longevity, reliability, and operational efficiency of underground conveyor belt systems. By adopting proactive maintenance practices and leveraging advanced technologies, mining operators can minimize downtime, reduce maintenance costs, and optimize conveyor performance. Here, we present twelve tips and strategies for effective maintenance of underground conveyor systems.
Regular Inspections and Condition Monitoring
Routine inspections and condition monitoring are essential for identifying potential issues and addressing them before they escalate into costly failures. Implementing a structured inspection schedule and utilizing technologies such as vibration analysis, thermal imaging, and oil analysis can help detect early signs of wear, misalignment, and other mechanical problems.
Lubrication Management
Proper lubrication is critical for reducing friction, preventing component wear, and extending the service life of conveyor systems. Establishing a comprehensive lubrication management program involves selecting the appropriate lubricants, applying them at recommended intervals, and ensuring proper lubricant storage and handling practices are followed.
Training and Skills Development
Investing in training and skills development for maintenance personnel is essential for ensuring they possess the knowledge and expertise required to maintain underground conveyor systems effectively. Providing training on equipment operation, maintenance procedures, and safety protocols empowers personnel to perform their duties competently and safely.
Emergency Preparedness and Response
Preparing for potential emergencies, such as conveyor belt fires, equipment breakdowns, or personnel injuries, is vital for minimizing disruptions to mining operations and ensuring the safety of personnel. Developing emergency response plans, conducting regular drills, and equipping maintenance teams with appropriate firefighting equipment and first aid supplies are essential components of effective emergency preparedness.
The installation and maintenance of underground conveyor belt systems present numerous challenges, ranging from limited access and geological hazards to harsh operating conditions and ventilation requirements. By addressing these challenges with innovative solutions and implementing proactive maintenance practices, mining operators can optimize the performance and reliability of underground conveyor systems, contributing to safer and more efficient underground mining operations.
Case Studies and Real-World Applications of Underground Conveyor Belts
Real-World Examples of Underground Conveyor Belts in Action
Underground conveyor belts are vital components in numerous mining operations worldwide. Here are six notable examples demonstrating their utility and effectiveness:
- The Northparkes Mine (Australia): Utilizes an advanced underground conveyor belt system that integrates automated loading and predictive maintenance technologies. This system not only enhances safety by reducing human involvement in high-risk areas but also increases operational efficiency.
- The Kidd Creek Mine (Canada): Features a deep underground conveyor belt capable of handling large volumes of copper and zinc ore over long distances. This system is particularly noted for its durability and reliability in one of the world’s deepest base-metal mines.
- The Stillwater Mine (USA): Employs a state-of-the-art conveyor belt system designed for the challenging conditions of platinum and palladium mining. The system’s design includes features that minimize downtime and maintenance costs, critical in maintaining the profitability of precious metal extraction.
- The Muruntau Gold Mine (Uzbekistan): Uses an extensive underground conveyor belt setup to transport gold ore across its vast operations, demonstrating the belt’s capacity for heavy-load applications and its importance in maintaining continuous flow in gold mining operations.
- The El Teniente Mine (Chile): Implements sophisticated underground conveyor belts to manage the transportation of copper from one of the world’s largest underground mines. The belts are tailored to handle the high corrosivity of copper ore while ensuring minimal environmental impact.
- The LKAB Mines (Sweden): These iron ore mines incorporate an innovative underground conveyor system that is crucial for the transportation of iron ore from deep beneath the Arctic Circle. The system is renowned for its robustness and ability to operate efficiently in extreme cold.
Case Studies from Notable Mining Operations
Detailed case studies further illustrate the impact and importance of these systems in global mining operations:
- The Grasberg Mine, Indonesia: This case study focuses on the implementation of an underground conveyor belt system in one of the world’s largest gold and copper mines. The study highlights how the conveyor system has been instrumental in reducing reliance on truck haulage, thereby lowering operational costs and significantly reducing the mine’s carbon footprint.
- The Palabora Mining Company, South Africa: Here, the underground conveyor belt system was revamped to incorporate advanced material handling technologies. The case study details the challenges faced during the installation of the new system, including the integration of the conveyor into existing mine infrastructure, and the subsequent improvements in ore handling capacity and safety performance.
- The Codelco Andina Mine, Chile: This study examines the adaptation of existing underground conveyor belt systems to extend deeper into the mine. The focus is on how the design modifications addressed the challenges of increased depth, such as enhanced belt strength, improved fire resistance, and integration of real-time monitoring systems for predictive maintenance.
These case studies and examples demonstrate the critical role that underground conveyor belts play in modern mining operations, showcasing their ability to enhance productivity, improve safety, and reduce environmental impacts across diverse mining environments.
Have questions about our Underground Conveyor Belts? Fill out the form, and our team will respond promptly.
Future Trends in Conveyor Technology for Underground Conveyor Belts
Predictions for Future Developments in Conveyor Belt Technology
The future of underground conveyor belt technology looks promising with several innovative trends poised to redefine how these systems operate in mining environments. Here are eight key developments expected to shape the future:
- Increased Automation: The trend towards full automation will continue, with underground conveyor belts becoming more integrated with automated loading and monitoring systems. This integration will enhance efficiency and reduce the need for human intervention in dangerous underground environments.
- Sustainable Materials: There will be a greater focus on using sustainable and eco-friendly materials in the manufacturing of conveyor belts. These materials will need to maintain the high durability required for underground conditions while reducing environmental impact.
- Enhanced Sensor Technology: The use of sensors on conveyor belts will become more sophisticated, allowing for real-time data analysis on wear and tear, temperature changes, and other critical factors that affect the belt’s performance and longevity.
- Improved Energy Efficiency: As energy costs continue to rise, the drive towards more energy-efficient conveyor systems will intensify. Innovations may include energy-generating conveyor systems that can harness the power of gravity and motion to feed power back into the grid.
- Advanced Wear Detection: Technologies that predict when parts of the belt are likely to fail and notify maintenance teams in advance will become standard. This predictive maintenance will help to minimize downtime and extend the lifespan of the conveyor system.
- Higher Durability Designs: Advances in materials science will likely lead to new compositions for belts that are even more resistant to the harsh conditions found underground, such as extreme abrasion, moisture, and temperatures.
- Smart Routing and Load Management: Future underground conveyor belts could incorporate smart routing capabilities that adjust paths dynamically based on real-time workflow and load requirements, optimizing the mining process and material flow.
- Blockchain for Supply Chain Tracking: The implementation of blockchain technology could revolutionize how conveyor belt maintenance logs are kept, ensuring an immutable record of repairs, replacements, and maintenance for compliance and operational efficiency.
How These Advancements Could Further Enhance Mining Operations
Each of these advancements will significantly contribute to more streamlined, cost-effective, and safer mining operations:
- Automation and sensor technology will reduce the risks associated with human presence in dangerous underground areas, while ensuring continuous operation without human error.
- Sustainable materials and energy efficiency will not only lower operational costs but also help mining companies meet increasingly stringent environmental regulations.
- Advanced wear detection and higher durability designs will decrease maintenance costs and downtime, enhancing the overall productivity of mining operations.
- Smart routing will ensure optimal material flow and resource allocation, which can greatly improve the efficiency of the mining process.
- Blockchain technology will provide a secure and transparent method for tracking and verifying all maintenance activities, enhancing the reliability and trustworthiness of mining operations.
These future trends represent a significant leap forward in the technology of underground conveyor belts, promising to transform the landscape of mining operations by making them more efficient, safer, and more environmentally friendly.
FAQs about Underground Conveyor Belt
There are three primary types of conveyors commonly used in various industries. Each type is designed to meet specific transportation and material handling requirements:
Belt Conveyors: Often considered the most common type, belt conveyors feature continuous belts made from flexible materials like rubber, PVC, or fabric. They are used for transporting goods over short to long distances on flat or inclined paths. Belt conveyors are versatile and can handle a wide range of products, from small parts to larger items.
Roller Conveyors: Roller conveyors consist of series of cylindrical rollers that are typically powered by gravity or motorized systems. They are well-suited for heavy or bulky items that need to be moved smoothly along the process line. Roller conveyors are mainly used in warehouses, distribution centers, and manufacturing facilities.
Overhead Conveyors: These conveyors utilize a track, whether manual or powered, from which carriers or hooks hang to transport parts or materials. They are used in situations where the product needs to be hung, such as in paint or curing operations, and in industries where floor space is a constraint.
In addition to these three types, various specialized conveyors exist, such as screw conveyors, pneumatic conveyors, and walking beam systems, each serving unique applications.
Grounding a conveyor belt is crucial for safety and to prevent static electricity buildup that can lead to shocks or fires. The grounding process typically involves the following steps:
Install a Grounding Rod: Drive a copper rod at least six feet deep into the ground below your facility’s foundation to ensure a secure earth connection.
Connect Grounding Wire: Use a heavy copper wire to connect the grounding rod to the conveyor frame. Where you make this connection is critical; it should be made directly on the metal frame of the conveyor, not on a painted surface or a plate that may not guarantee a solid electrical connection.
Secure and Maintain: Ensure the connection is secure and perform regular maintenance checks to see that no corrosion or loosening occurs over time, which could compromise the ground.
Additionally, in very dry environments where static could be more of an issue, using additional methods like watering the area around the grounding rod or using static tinsel can improve conductivity.
Flat belts and conveyor belts are both used for material transport but they differ primarily in size and application. Flat belts are generally less than 100 mm in width and are used in applications where lightweight materials or components are moved. They are often found in machinery transmissions and are used to transfer motion from one wheel to another.
Conveyor belts, on the other hand, have a width of 100 mm or more and are designed for moving products along a line in an automated or semi-automated manner. They are sturdier, can handle heavier loads, and can be customized with various surface materials to suit different operational conditions, such as temperature, friction, and resistance to chemicals.
There is a wide variety of conveyor belts available to cater to diverse operational needs. The most common types of conveyor belts include:
General Purpose Belts: These are versatile and can carry a variety of goods.
Plastic Modular Belts: These are made of plastic modules and are easy to clean and maintain.
Flat Belts: As mentioned before, these are less than 100 mm in width and used in transmission or lightweight transport.
Cleated Conveyor Belts: These have vertical cleats to prevent product slippage in inclined or vertical conveyance.
Wire Mesh Belts: Suited for hot or cold items and for items that will benefit from the belt’s large open area.
Filter Belts: These belts are designed to drain or filter out unwanted substances.
In addition, there are application-specific belts such as food-grade belts for the food industry, and high-temperature-resistant belts for operations involving high heat. Each type offers different features to solve industry-specific challenges.
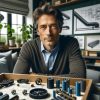
Jordan Smith, a seasoned professional with over 20 years of experience in the conveyor system industry. Jordan’s expertise lies in providing comprehensive solutions for conveyor rollers, belts, and accessories, catering to a wide range of industrial needs. From initial design and configuration to installation and meticulous troubleshooting, Jordan is adept at handling all aspects of conveyor system management. Whether you’re looking to upgrade your production line with efficient conveyor belts, require custom conveyor rollers for specific operations, or need expert advice on selecting the right conveyor accessories for your facility, Jordan is your reliable consultant. For any inquiries or assistance with conveyor system optimization, Jordan is available to share his wealth of knowledge and experience. Feel free to reach out at any time for professional guidance on all matters related to conveyor rollers, belts, and accessories.