The Durability of High Impact PVC Conveyor Roller Explained
Conveyor systems are integral to the operations of various industries, facilitating the efficient movement of goods and materials across production lines and warehouses. At the heart of these systems are the rollers, which bear the weight of materials and propel them forward with minimal effort. Among the diverse types of rollers available, high impact PVC conveyor roller stands out for their durability and performance. These rollers are specifically designed to withstand the rigors of heavy loads and high-impact conditions, making them a crucial component in environments where resilience and reliability are paramount. The introduction of high impact PVC conveyor roller has significantly enhanced the efficiency and longevity of conveyor systems, underscoring their importance in modern industrial operations.
What Is High Impact PVC Conveyor Roller
In the realm of material handling and conveyor systems, the choice of roller material plays a pivotal role in the efficiency, durability, and overall performance of the system. Among the various materials available, high impact PVC has emerged as a standout option for rollers, thanks to its unique blend of properties that cater to demanding industrial environments. Let’s delve into what makes high impact PVC conveyor rollers a preferred choice for businesses looking to optimize their conveyor systems.
Definition and Characteristics of High Impact PVC Conveyor Rollers
High impact PVC conveyor roller is specialized components designed for conveyor systems that require durability and resistance against significant forces and wear. These rollers are made from high-impact polyvinyl chloride (PVC), a material known for its toughness and resilience. Here are eight distinct characteristics that define these rollers:
- Durability: High-impact PVC is resistant to cracking and breaking under heavy loads, ensuring a long service life.
- Corrosion Resistance: Unlike metal rollers, high-impact PVC is impervious to rust and corrosion, making it ideal for use in environments with moisture or chemical exposure.
- Lightweight: PVC rollers are significantly lighter than their metal counterparts, reducing the overall weight of the conveyor system and the energy required to operate it.
- Noise Reduction: High impact PVC conveyor rollers operate more quietly than metal rollers, contributing to a more pleasant working environment.
- Low Maintenance: These rollers require less maintenance due to their resistance to wear and the absence of rust.
- Chemical Resistance: PVC is resistant to many chemicals, making these rollers suitable for industries where spills might occur.
- Cost-Effectiveness: Despite their high performance, high-impact PVC rollers are often more affordable than those made from other high-durability materials.
- Ease of Installation: Their lightweight nature makes high-impact PVC rollers easier to handle and install, reducing setup times.
Comparison with Other Materials: Why Choose PVC for High-Impact Applications?
When comparing high impact PVC conveyor rollers to those made from other materials, several advantages become apparent:
- Weight: High-impact PVC is much lighter than steel or aluminum, making for easier handling and lower shipping costs.
- Corrosion Resistance: Unlike metal rollers, PVC is naturally resistant to corrosion and will not degrade in humid or corrosive environments.
- Cost: PVC rollers are generally less expensive to manufacture and purchase than those made from metals or high-grade composites.
- Noise: PVC rollers operate more quietly than metal rollers, reducing noise pollution in the workplace.
- Maintenance: The need for lubrication and rust prevention is significantly reduced with PVC rollers, lowering maintenance costs and downtime.
- Chemical Resistance: PVC’s resistance to chemicals surpasses that of metals, which can oxidize or corrode when exposed to certain substances.
- Impact Resistance: High-impact PVC absorbs shocks and impacts better than many metals, which can dent or deform under similar conditions.
- Non-Conductive: PVC is a poor conductor of electricity, making high-impact PVC rollers a safer choice in environments where electrical hazards are a concern.
- Customization: PVC can be easily manufactured in various colors and specifications, allowing for better integration into specific conveyor system designs.
High impact PVC conveyor rollers offer a compelling combination of durability, cost-effectiveness, and operational efficiency, making them a superior choice for many high-impact applications across diverse industries. Their unique properties and advantages over traditional materials underscore why high-impact PVC is increasingly preferred for modern conveyor systems.
Benefits of High Impact PVC Conveyor Roller
The adoption of high impact PVC conveyor roller in various industries has been a game-changer in the way conveyor systems operate and perform. These rollers, made from high-impact polyvinyl chloride (PVC), offer a suite of benefits that address many of the challenges faced by traditional materials used in conveyor systems. Here are nine compelling advantages of using high impact PVC conveyor roller:
- Durability and Resistance to Wear and Tear: High impact PVC conveyor rollers are renowned for their exceptional durability. The material’s resistance to breaking, cracking, and wear under heavy loads ensures that these rollers can withstand the rigors of daily operation without significant degradation, extending the lifespan of the conveyor system.
- Low Maintenance Requirements and Ease of Cleaning: Unlike metal rollers that may rust or require regular lubrication, high impact PVC conveyor rollers demand minimal maintenance. Their non-porous surface is easy to clean, reducing downtime and labor costs associated with maintenance.
- Cost-effectiveness: The initial investment in high impact PVC conveyor roller is often lower than that for rollers made from other materials. Additionally, their durability and low maintenance requirements contribute to significant long-term savings, making them a cost-effective solution for businesses.
- Lightweight Nature and Its Impact on Operational Efficiency: The lightweight property of high-impact PVC reduces the overall weight of the conveyor system, leading to lower energy consumption during operation. This not only enhances operational efficiency but also contributes to energy savings.
- Corrosion Resistance: High-impact PVC is inherently resistant to corrosion and chemical exposure, making these rollers ideal for use in environments where moisture, acids, and other corrosive substances are present. This feature eliminates the need for frequent replacements due to corrosion.
- Noise Reduction: Conveyor systems equipped with high-impact PVC rollers operate more quietly compared to those with metal rollers. The reduced noise levels contribute to a more pleasant and safer working environment for employees.
- Impact Absorption: High-impact PVC has excellent shock-absorbing properties, which help in minimizing the impact on goods during transportation. This is particularly beneficial for fragile items, ensuring they are less likely to be damaged while moving along the conveyor.
- Non-Conductive Material: Being a non-conductive material, high-impact PVC provides an added safety benefit in environments where electrical hazards are a concern. This feature helps in preventing electrical shocks and sparks, enhancing workplace safety.
- Versatility in Applications: Thanks to its numerous benefits, high impact PVC conveyor rollers are versatile and can be used across a wide range of industries, including food processing, pharmaceuticals, manufacturing, and more. Their adaptability to different environments and applications makes them a universally appealing choice for conveyor systems.
The benefits of high impact PVC conveyor roller extend beyond mere durability and cost savings. They contribute to safer, more efficient, and more reliable conveyor system operations, making them an indispensable component in modern industrial applications.
Applications and Uses of High Impact PVC Conveyor Roller
The adaptability and resilience of high impact PVC conveyor roller have made them a cornerstone in the operational efficiency of myriad industrial sectors. These rollers not only meet the diverse demands of different environments but also enhance the productivity and safety of conveyor systems. Below, we delve into the industries and specific applications where the unique attributes of high impact PVC conveyor rollers are not just beneficial but often critical for success.
Industries Ideal for High Impact PVC Conveyor Rollers
High impact PVC conveyor rollers are engineered to perform under challenging conditions, making them suitable for a wide array of industries:
- Food and Beverage Processing: Their resistance to corrosion and ease of cleaning meet the hygiene standards of the food industry.
- Pharmaceutical Manufacturing: The inert nature of PVC ensures these rollers are safe for environments where contamination control is paramount.
- Packaging and Distribution Centers: The robustness and low maintenance cater to the high demands of packaging and distribution operations.
- Chemical Processing Plants: PVC’s resistance to chemicals makes these rollers ideal for transporting materials in corrosive environments.
- Agriculture: Suited for the harsh conditions of agricultural processing, thanks to their moisture resistance and durability.
- Marine and Dockside Operations: The saline and moist conditions of marine environments are no match for the corrosion-resistant properties of PVC.
- Automotive Manufacturing: Capable of handling the heavy loads and abrasive conditions of automotive production lines.
Specific Applications Highlighting the Versatility of High Impact PVC Conveyor Rollers
The practical applications of high impact PVC conveyor rollers are as varied as the industries they serve, demonstrating their versatility:
- Bottling Lines: Essential for the gentle and hygienic transport of bottles through various stages of filling and packaging.
- Assembly Lines: Their durability ensures the smooth movement of components across different manufacturing sectors.
- Sorting Systems: Facilitate the efficient sorting of packages, crucial for logistics and distribution centers.
- Loading and Unloading Areas: The toughness of PVC rollers is ideal for the rigors of loading docks and freight areas.
- Clean Rooms: Their non-shedding and easy-to-clean characteristics make them suitable for sensitive manufacturing environments.
- Freezer and Cold Storage: PVC’s performance is unaffected by extreme cold, making these rollers perfect for cold storage applications.
- Wet and Washdown Environments: Water resistance and ease of cleaning are key for operations in food processing plants.
- Recycling Facilities: The abrasive materials of recycling processes are well-handled by the durable nature of PVC rollers.
- Airport Baggage Handling: The reliability and robustness of PVC rollers ensure the efficient movement of luggage in airport systems.
Through these applications, high impact PVC conveyor rollers prove to be an indispensable asset across industries, enhancing operational efficiency, safety, and reliability in conveyor systems worldwide. Their broad usability showcases the material’s superior performance in meeting the rigorous demands of modern industrial applications.
High Impact PVC Conveyor Roller Parts and Maintenance
In the world of material handling and conveyor systems, the integrity and performance of conveyor rollers are paramount. High impact PVC conveyor rollers, in particular, offer a blend of durability and efficiency that is unmatched in many industrial applications. Understanding the components that make up these rollers, as well as implementing a robust maintenance strategy, is crucial for maximizing their operational lifespan and ensuring the smooth running of conveyor systems. Let’s delve into the anatomy of a high impact PVC conveyor roller and explore practical maintenance tips to keep them in top condition.
Overview of the Components That Make Up a High Impact PVC Conveyor Roller
The construction of a high impact PVC conveyor roller is a testament to engineering designed for resilience and performance. Each component plays a critical role in the roller’s functionality:
- Tube: The body of the roller, crafted from high-impact PVC, provides a durable surface for material transport.
- Shaft: A central rod, usually made of steel, that provides structural support and connects the roller to the conveyor framework.
- Bearings: Positioned at each end of the tube, bearings ensure the smooth rotation of the roller with minimal friction.
- End Caps: These components secure the bearings in place and help maintain the roller’s structural integrity.
- Spring-Loaded Axles: Facilitate easy installation and removal, allowing for quick maintenance or replacement.
- Seals: Protect the internal components from dust, moisture, and other environmental contaminants.
- Sprockets or Gears: Essential for driven rollers, these parts engage with the conveyor’s drive mechanism.
- Spacer Tubes: Maintain the correct spacing between bearings, ensuring even load distribution and preventing deformation.
Tips for Maintaining and Extending the Lifespan of High Impact PVC Conveyor Rollers
Maintaining high impact PVC conveyor roller is not just about preserving their physical condition; it’s about ensuring the efficiency and reliability of the entire conveyor system. Here are essential maintenance tips:
- Regular Cleaning: Prevent the accumulation of debris that can impair roller function and lead to wear.
- Lubrication of Bearings: Even though PVC rollers are low maintenance, the bearings still require occasional lubrication to operate smoothly.
- Inspection Schedule: Conduct routine inspections to identify and address wear, damage, or misalignment early.
- Proper Installation: Correct installation and alignment are crucial to prevent uneven wear and extend roller life.
- Load Capacity Adherence: Avoid exceeding the roller’s load capacity to prevent stress and potential damage.
- Environment Control: Minimize exposure to harsh conditions, such as extreme temperatures and corrosive substances, to preserve roller integrity.
- Replacement of Worn Parts: Promptly replace any component showing signs of wear to maintain optimal performance.
- Use of Compatible Cleaning Agents: Choose cleaning agents that are safe for PVC to avoid material degradation.
- Training of Personnel: Ensure that staff are knowledgeable about proper roller handling and maintenance practices.
By paying close attention to the construction and care of high impact PVC conveyor roller, businesses can significantly enhance the longevity and performance of their conveyor systems. Proper maintenance not only contributes to operational efficiency but also to the safety and productivity of the material handling process.
Types of High Impact PVC Conveyor Roller
The functionality and efficiency of belt conveyors are significantly influenced by the type of rollers they employ. Among the myriad options available, high impact PVC conveyor rollers have emerged as a standout choice for a multitude of applications, thanks to their unique properties and benefits. This section aims to compare high impact PVC conveyor rollers with other common types of rollers used in belt conveyors, highlighting their distinct advantages and situational benefits that make them particularly suited for specific industrial environments.
Comparison of High-Impact PVC Rollers with Other Types of Conveyor Rollers
The table below provides a comparative overview of high-impact PVC rollers against steel, aluminum, and rubber-coated rollers across various attributes:
Feature | High-Impact PVC Rollers | Steel Rollers | Aluminum Rollers | Rubber-Coated Rollers |
---|---|---|---|---|
Weight | Lightweight, reducing system load | Heavier, increasing system load | Lightweight, similar to PVC | Moderate, adding some system load |
Durability | Highly durable with excellent wear resistance | Very durable but prone to corrosion | Less durable than steel but resistant to corrosion | Good durability with cushioning properties |
Maintenance | Low maintenance and easy to clean | High maintenance, susceptible to rust | Low maintenance, easier to handle | Requires maintenance to retain coating integrity |
Cost | Cost-effective with low long-term maintenance costs | Initially higher cost plus maintenance expenses | Moderate cost with low maintenance | Variable, often higher due to specialized coatings |
Noise Level | Quiet operation, ideal for noise-sensitive environments | Can be noisy, requiring additional noise reduction measures | Quieter operation than steel | Reduces noise and vibration, offering a quieter operation |
Corrosion Resistance | Excellent, suitable for corrosive environments | Requires coatings to prevent corrosion | Naturally resistant to corrosion | Depends on the rubber type, generally good |
Chemical Resistance | Excellent, can withstand various chemicals | Moderate, can be affected by certain chemicals | Good, suitable for many environments | Good, but dependent on rubber material |
Impact Resistance | Excellent, absorbs impacts well | Moderate, can dent under heavy impacts | Moderate, less impact-resistant than steel | High, provides excellent cushioning and impact absorption |
Application Versatility | Extremely versatile, suitable for a wide range of industries | Best suited for heavy-duty and industrial applications | Ideal for light to medium-duty applications | Preferred for delicate or impact-sensitive materials |
Situational Advantages of Using High-Impact PVC Rollers
High impact PVC conveyor roller offers distinct advantages in various operational scenarios, making them a preferred choice for many industries:
- Corrosive Environments: Their superior corrosion resistance makes them ideal for use in chemical processing or outdoor environments.
- Food Processing Industries: The non-toxic and easy-to-clean nature of PVC rollers ensures compliance with hygiene standards.
- Quiet Operation Needs: Facilities close to residential areas or those requiring minimal operational noise benefit from the quiet performance of PVC rollers.
- Energy Efficiency Goals: The lightweight nature of PVC rollers contributes to lower energy consumption in conveyor operations.
- Budget Constraints: Offering a balance between cost-effectiveness and performance, PVC rollers are suitable for cost-sensitive projects.
- Low Maintenance Requirements: Operations aiming to reduce downtime will appreciate the minimal maintenance needs of PVC rollers.
- High-Speed Applications: Their durability and smooth operation make PVC rollers suitable for high-speed conveying needs.
- Variable Climate Conditions: PVC rollers perform consistently across a range of temperatures, making them versatile for different environmental conditions.
- Chemical Processing: The chemical resistance of PVC rollers ensures safe material handling in environments exposed to harsh chemicals.
The selection of high impact PVC conveyor roller can significantly enhance the performance, efficiency, and reliability of belt conveyor systems across a broad spectrum of industrial applications. Their unique combination of durability, cost-effectiveness, and operational advantages makes them a compelling choice for modern conveying needs.
Roller Conveyor vs Belt Conveyor
In the realm of material handling and logistics, roller and belt conveyors are two fundamental types of systems used to transport goods across various distances and environments. Each system has distinct mechanisms of operation, suitability for different types of cargo, and inherent advantages and disadvantages. Understanding these differences is crucial, especially when considering the application of high impact PVC conveyor rollers, which can significantly affect the efficiency, durability, and cost-effectiveness of a conveyor system.
Fundamental Differences Between Roller and Belt Conveyors
Roller and belt conveyors serve the same primary function but do so in fundamentally different ways. Here’s how they compare:
- Mechanism of Operation: Roller conveyors move goods over a series of rotating cylinders or rollers, whereas belt conveyors use a continuous looped belt driven by pulleys.
- Material Compatibility: Roller conveyors are best for solid, rigid items, while belt conveyors can handle both solid and loose materials.
- System Flexibility: Roller conveyors offer more flexibility in layout design, easily incorporating curves and elevations, whereas belt conveyors are more straightforward, typically running in straight lines.
- Efficiency and Energy Use: Roller conveyors, particularly gravity-fed systems, are more energy-efficient, relying on natural forces or minimal power for movement. Belt conveyors, though requiring more energy, provide consistent and controlled movement.
- Maintenance and Durability: Generally, roller conveyors are easier and less expensive to maintain than belt conveyors, which may suffer from belt wear and tear.
- Cost Implications: The initial setup cost for roller conveyors can be lower, but complex systems might increase the overall expense. Belt conveyors tend to have a higher initial cost but are more efficient for continuous, long-distance operation.
- Operational Speed: Belt conveyors typically allow for faster transport speeds compared to roller conveyors.
- Load Handling: Belt conveyors are often capable of handling heavier loads over longer distances with ease.
Pros and Cons of Each System
Roller Conveyors
Pros:
- Modularity: Easily reconfigured or expanded to meet changing operational needs.
- Low Maintenance: Simpler design means fewer parts to maintain or replace.
- Energy Efficiency: Especially in manual or gravity-fed systems, they consume less energy.
- Versatile Handling: Can accommodate a wide range of product sizes and weights.
- Product Accumulation: Ideal for systems requiring accumulation without back pressure.
Cons:
- Size Limitations: Products must be large enough to span the distance between rollers.
- Handling Restrictions: Not suitable for very small, loose, or irregularly shaped items without additional equipment.
- Manual Intervention: Some gravity systems may require manual assistance to ensure smooth operation.
- Distance Limitations: Less efficient over long distances compared to belt conveyors.
Belt Conveyors
Pros:
- Versatile Material Handling: Capable of transporting a wide variety of materials, including loose and granular items.
- Long-Distance Efficiency: Ideal for moving materials over long distances and through complex routes.
- Controlled Movement: Offers consistent speed and precise control over material flow.
- Environmental Protection: Can be enclosed to protect materials from the external environment.
Cons:
- Higher Costs: More expensive to install and maintain due to the complexity and the need for frequent belt replacements.
- Continuous Operation: Not well-suited for operations requiring accumulation or batching of products.
- Wear and Tear: Belts are susceptible to damage from sharp objects or extreme conditions.
- Maintenance Requirements: Requires regular inspection and maintenance to ensure operational efficiency.
How to Choose the Right High Impact PVC Conveyor Roller
The selection of the appropriate conveyor roller is a pivotal decision in the design and implementation of a conveyor system. This choice directly impacts the system’s efficiency, operational cost, and maintenance requirements. Among the myriad of options available, high impact PVC conveyor rollers stand out for their adaptability and performance across various applications. Understanding the critical factors that influence roller selection and recognizing the specific advantages of high-impact PVC rollers can guide you to make an informed decision that aligns with your operational needs and goals.
Factors to Consider When Selecting Conveyor Rollers
When navigating the selection process for conveyor rollers, several key considerations come into play, ensuring the chosen rollers meet the system’s demands:
- Load Requirements: Understanding the weight and nature of the materials the system will convey is crucial to select rollers that can bear the load without compromise.
- Environmental Conditions: The operating environment’s characteristics, such as exposure to chemicals, moisture, and temperature variations, significantly influence roller material choice.
- Speed of Operation: The intended speed of the conveyor system dictates the need for rollers designed to handle specific operational velocities.
- Maintenance and Durability: Evaluating the expected lifespan and upkeep needs of the rollers ensures they match your facility’s maintenance capabilities.
- Noise Considerations: For environments where reducing operational noise is essential, selecting rollers designed for quiet operation is key.
- Installation and Replacement: The ease with which rollers can be installed and replaced affects downtime and maintenance efficiency.
- Cost: Balancing the initial investment against long-term operational and maintenance costs is vital for economic efficiency.
- Compatibility with Existing Systems: Ensuring the new rollers integrate seamlessly with the current conveyor setup prevents compatibility issues.
- Safety and Compliance: Adhering to industry-specific safety standards and regulations is non-negotiable when selecting conveyor components.
Why High-Impact PVC Rollers Might Be the Right Choice for Your Application
High impact PVC conveyor roller offers distinct advantages that make them a compelling choice for a broad spectrum of conveyor system applications:
- Adaptability: Their robust construction makes them suitable for both light and heavy-duty applications, showcasing unparalleled versatility.
- Resistance to Corrosion: These rollers excel in environments prone to moisture or chemical exposure, maintaining integrity where metal rollers might fail.
- Minimal Maintenance: The durable nature of high-impact PVC minimizes the need for frequent maintenance, offering long-term cost savings.
- Reduced Operational Noise: The material properties of PVC allow for quieter operation, ideal for noise-sensitive settings.
- Energy Efficiency: The lightweight design of PVC rollers contributes to lower energy consumption by the conveyor system.
- Economic Value: High-impact PVC rollers provide a cost-effective solution, balancing initial costs with durability and low maintenance.
- Hygienic Operation: The ease of cleaning PVC rollers makes them particularly suitable for industries where cleanliness is paramount.
- Impact Durability: Designed to withstand significant forces, these rollers offer enhanced durability for handling rough or heavy materials.
In making the critical decision of selecting the right conveyor roller, considering the operational requirements and environmental conditions is essential. High-impact PVC conveyor rollers, with their broad range of benefits from durability to cost-effectiveness, present a viable option for many applications. Their suitability for diverse operational contexts, combined with their performance advantages, makes them a valuable component in optimizing conveyor system efficiency and reliability.
High Impact PVC Conveyor Roller for Sale
Finding high-quality high impact PVC conveyor roller is crucial for ensuring the efficiency, reliability, and longevity of your conveyor system. These rollers are pivotal in various industries for their durability and performance under demanding conditions. Here, we will explore where to find these essential components and what critical aspects to consider when selecting a supplier or manufacturer.
Tips on Where to Find High-Quality High Impact PVC Conveyor Roller
- Industry Trade Shows: Trade shows and exhibitions focused on material handling and conveyor systems are excellent places to find leading suppliers and manufacturers of high impact PVC conveyor roller.
- Online Marketplaces: Platforms like Alibaba, ThomasNet, and IndustryNet can connect you with numerous suppliers and manufacturers worldwide.
- Manufacturer Websites: Directly visiting the websites of companies that specialize in conveyor systems and components often provides comprehensive product catalogs and contact information.
- Industry Forums and Publications: Engaging with online forums and reading industry publications can offer insights into reputable suppliers known for high-quality products.
- Referrals from Industry Peers: Recommendations from colleagues or industry contacts can lead you to trusted suppliers with proven track records.
- Social Media and Professional Networks: LinkedIn and other social media platforms can be valuable resources for finding suppliers and reading customer reviews.
- Local Industrial Supply Stores: Some local stores may carry a range of conveyor rollers or can order high-impact PVC rollers from their network of suppliers.
- Direct Factory Outlets: Purchasing directly from the factory or manufacturer can ensure product quality and offer more competitive pricing.
- Specialized Conveyor System Consultants: Consultants with expertise in conveyor systems often have established relationships with suppliers and can recommend high-quality components.
What to Look for in a Supplier or Manufacturer
- Reputation: Look for suppliers with positive reviews and testimonials from previous customers, indicating reliability and quality.
- Quality Certifications: Suppliers that adhere to industry standards and possess quality certifications (e.g., ISO) are more likely to offer high-quality products.
- Product Range: Choose a supplier with a wide range of conveyor components, ensuring they can meet all your system needs.
- Customization Options: Suppliers who offer customization can provide rollers tailored to your specific requirements.
- Technical Support: A supplier that offers comprehensive technical support can assist with product selection, installation, and maintenance.
- Warranty and Return Policy: Look for favorable warranty terms and a clear return policy to protect your investment.
- Lead Times: Consider the supplier’s ability to fulfill orders promptly, ensuring your operations are not delayed.
- Competitive Pricing: While quality should not be compromised for cost, competitive pricing is important for budget considerations.
Incorporating high impact PVC conveyor roller into your system requires careful consideration of both the product and the supplier. By following these tips on where to find these rollers and what to look for in a supplier, you can ensure that you invest in components that enhance the efficiency and longevity of your conveyor system. High impact PVC conveyor rollers, with their exceptional durability and performance, are an investment in the smooth and reliable operation of your material handling processes.
FAQs about High Impact PVC Conveyor Roller
The type of roller used for a conveyor belt largely depends on the application, material being transported, and the environment in which the conveyor system operates. Common types of rollers include steel, plastic, and rubber-coated rollers. Steel rollers are durable and suitable for heavy-duty applications but can be noisy and prone to corrosion. Plastic rollers, particularly those made from high-impact PVC, are lightweight, corrosion-resistant, and operate quietly, making them ideal for various applications, including those requiring sanitary conditions. Rubber-coated rollers provide additional grip and are beneficial for transporting delicate items that might be damaged by harder surfaces. The choice of roller should consider factors such as load capacity, speed requirements, potential environmental exposures (e.g., chemicals, moisture), and noise considerations. Each type of roller offers unique advantages, and the selection process should align with the specific needs of the conveyor system to ensure efficiency and longevity.
Impact rollers, or impact idlers, are specialized rollers designed to absorb the shock and impact of falling materials at loading points within a belt conveyor system. Positioned at the conveyor’s feed and transfer points, impact rollers play a crucial role in extending the belt’s lifespan and protecting the conveyor structure from damage. These rollers are typically constructed with a series of rubber discs mounted on a heavy-duty steel frame, providing a cushioned, shock-absorbing surface that reduces the force of materials as they are loaded onto the belt. The use of impact rollers is particularly important in applications involving heavy or abrasive materials, where the force of dropping these materials could otherwise cause premature wear and tear on the conveyor belt and structure. By dissipating the energy of falling materials, impact rollers help maintain the integrity of the conveyor system and reduce maintenance costs over time.
Calculating the motor power required for a roller conveyor involves considering several factors, including the total load on the conveyor, the conveyor length, the speed at which the conveyor needs to operate, and the friction coefficient between the rollers and the belt. A basic formula to estimate motor power (P) in kilowatts (kW) is: P = (F x v) / 1000, where F is the total force needed to move the conveyor and its load in Newtons (N), and v is the conveyor speed in meters per second (m/s). The total force (F) can be calculated by summing the frictional resistance of the conveyor and the force needed to move the load, which depends on the weight of the load and the friction coefficient. It’s important to note that this formula provides an estimate, and other factors such as the efficiency of the motor, the type of drive system used, and potential inclines in the conveyor path should also be considered. Consulting with a conveyor system engineer or using detailed calculation tools provided by conveyor manufacturers is recommended for precise motor power selection.
The HS (Harmonized System) code for conveyor rollers is a standardized international code used to classify traded products for customs, tariffs, and statistical purposes. The specific HS code for conveyor rollers can vary depending on the country and the specific type of roller. Generally, conveyor rollers fall under the category of machinery parts and can be classified under the HS code 8431, which pertains to parts suitable for use solely or principally with the machinery of headings 8425 to 8430. For more detailed classification, such as distinguishing between types of rollers or materials (e.g., plastic, steel), additional digits are added to the HS code. It’s important to consult the latest customs tariff schedules or speak with a customs broker to determine the precise HS code applicable to conveyor rollers in your specific context, as codes and classifications can change and may vary by country.
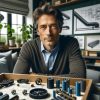
Jordan Smith, a seasoned professional with over 20 years of experience in the conveyor system industry. Jordan’s expertise lies in providing comprehensive solutions for conveyor rollers, belts, and accessories, catering to a wide range of industrial needs. From initial design and configuration to installation and meticulous troubleshooting, Jordan is adept at handling all aspects of conveyor system management. Whether you’re looking to upgrade your production line with efficient conveyor belts, require custom conveyor rollers for specific operations, or need expert advice on selecting the right conveyor accessories for your facility, Jordan is your reliable consultant. For any inquiries or assistance with conveyor system optimization, Jordan is available to share his wealth of knowledge and experience. Feel free to reach out at any time for professional guidance on all matters related to conveyor rollers, belts, and accessories.