The Rubber Coated Impact Conveyor Roller on Efficiency
In the bustling world of industrial operations, the efficiency and longevity of conveyor systems are paramount. At the heart of these systems lie the rubber coated impact conveyor rollers, a critical component that significantly enhances the performance and durability of conveyor belts. These rollers, coated with a resilient rubber layer, are pivotal in various industries, including mining, manufacturing, and logistics, for their ability to absorb impacts, reduce noise, and prevent damage to the conveyor belt. With a focus on the used, best, and readily available rubber coated impact conveyor roller for sale, this guide aims to provide valuable insights into selecting the right rollers that meet the operational demands and budget constraints of businesses. Whether upgrading an existing system or setting up a new conveyor line, understanding the significance of these rollers is the first step towards optimizing your material handling processes.
What Is Rubber Coated Impact Conveyor Roller
In the intricate world of conveyor systems, the components that make up the machinery are as crucial as the system itself. Among these, rubber coated impact conveyor rollers stand out for their critical role in enhancing the functionality and longevity of conveyor belts. These rollers are not just another part; they are a testament to engineering ingenuity aimed at solving several operational challenges. Let’s delve deeper into what these rollers are and the myriad of benefits they bring to conveyor systems across various industries.
What are Rubber Coated Impact Conveyor Rollers?
Rubber coated impact conveyor rollers are specialized components designed for conveyor systems, where they play a crucial role in facilitating the smooth and efficient movement of goods. These rollers are characterized by their durable steel core, which is thoroughly coated with a layer of rubber. This unique construction offers several advantages:
- Shock Absorption: The rubber coating absorbs the impact between the conveyor belt and the roller, protecting the belt from damage.
- Noise Reduction: They significantly reduce operational noise, contributing to a quieter work environment.
- Increased Grip: The rubber surface increases friction, ensuring materials move smoothly without slippage.
- Corrosion Resistance: Rubber is resistant to water and chemicals, protecting the steel core from rust and corrosion.
- Vibration Dampening: Helps in minimizing vibrations, which can extend the life of other conveyor components.
- Energy Efficiency: By reducing friction and improving belt grip, these rollers can lead to lower energy consumption.
- Versatility: Suitable for various applications, including heavy-duty industries like mining and lighter operations such as packaging.
- Longevity: The protective rubber coating extends the life of the rollers by guarding against wear and tear.
- Maintenance Reduction: Their durability and resistance to damage mean less frequent replacements and repairs.
The Role and Benefits of Using Rubber Coating on Impact Conveyor Rollers
The application of rubber coating on impact conveyor rollers is not just a matter of enhancing their physical properties; it also significantly impacts their performance and the overall efficiency of the conveyor system:
- Improved Conveyor Belt Life: By absorbing impacts, the rubber coating prevents tears and reduces wear on the conveyor belt.
- Enhanced Product Safety: Sensitive or fragile materials are less likely to be damaged during transport due to the cushioning effect of the rubber.
- Operational Versatility: These rollers can be used in various environmental conditions, including wet, dry, or chemically aggressive areas.
- Load Distribution: The rubber surface evenly distributes the load across the roller, preventing material concentration that can cause belt misalignment.
- Customization Options: Rubber coatings can be tailored in hardness and thickness to match specific operational needs.
- Reduced Downtime: With enhanced durability and resistance to damage, conveyor systems experience less downtime for maintenance.
- Cost Efficiency: Although the initial investment may be higher, the long-term savings in maintenance and replacement costs are significant.
- Environmental Resistance: The rubber coating is designed to withstand extreme temperatures, UV light, and ozone, ensuring performance in various climates.
- Safety for Workers: Reduced noise and vibration contribute to a safer and more comfortable working environment, reducing the risk of hearing damage and fatigue.
Incorporating rubber coated impact conveyor rollers into a conveyor system brings a multitude of benefits, from operational efficiency and safety to long-term cost savings. Their design and material composition make them an indispensable component in modern industrial operations.
The Advantages of Rubber Coated Impact Conveyor Roller
Rubber coated impact conveyor rollers are integral to the efficiency and longevity of conveyor systems across various industries. These rollers, with their robust design and rubber coating, bring forth a multitude of benefits that enhance the functionality and durability of conveyor systems. Here are nine key advantages of using rubber coated impact conveyor roller:
- Durability and Resistance to Wear and Tear: The rubber coating on these rollers provides an extra layer of protection against the daily grind of materials passing over them, significantly extending their lifespan compared to uncoated rollers.
- Shock Absorption Capabilities: The rubber material acts as a cushion for the impact between the conveyor belt and the roller, safeguarding the belt and the materials being conveyed from damage.
- Noise Reduction Benefits: One of the standout features of rubber coated impact conveyor roller is their ability to operate quietly. The rubber coating absorbs sound, leading to a more pleasant working environment that is less disruptive for workers.
- Enhanced Traction: The rubber surface increases the grip on the materials being transported, reducing slippage and improving the efficiency of the conveyor system.
- Moisture and Chemical Resistance: Rubber coated impact conveyor rollers are resistant to moisture and various chemicals, making them suitable for use in harsh environments without corroding or degrading.
- Improved Conveyor Belt Alignment: The friction between the rubber coating and the conveyor belt helps to keep the belt properly aligned, reducing maintenance needs and preventing potential operational issues.
- Energy Savings: By reducing friction and improving the conveyor belt’s grip, these rollers can contribute to lower energy consumption of the conveyor system, leading to cost savings over time.
- Versatile Application: Thanks to their robust design and protective coating, rubber coated impact conveyor rollers are suitable for a wide range of applications, from heavy-duty mining operations to light-duty packaging lines.
- Reduced Maintenance Costs: The combination of durability, resistance to wear and tear, and the protective qualities of the rubber coating means that these rollers require less frequent replacement and maintenance, contributing to lower operational costs.
Incorporating rubber coated impact conveyor roller into a conveyor system not only enhances its performance but also contributes to a safer, more efficient, and cost-effective operation. Their wide range of benefits makes them a preferred choice for businesses looking to optimize their material handling processes.
Types of Rubber Coated Impact Conveyor Roller
The versatility of rubber coated impact conveyor rollers is evident in the variety of types available, each designed to meet specific industrial needs. Understanding these types and their applications is crucial for optimizing conveyor system performance.
Rubber Conveyor Roller
Rubber conveyor rollers are primarily used to facilitate the movement of goods across a conveyor belt. These rollers are coated with a layer of rubber to enhance grip and protect the materials being conveyed.
- Durability: The rubber coating provides a protective layer, reducing wear and extending the roller’s lifespan.
- Traction: Improved grip prevents slippage of materials, ensuring smooth conveyor operations.
- Material Protection: Soft rubber surface minimizes damage to fragile goods during transport.
- Versatility: Suitable for various industries, including packaging, manufacturing, and distribution.
- Customization: Available in different hardness levels to match the application’s requirements.
- Moisture Resistance: Rubber’s natural resistance to water makes these rollers ideal for damp or humid environments.
- Temperature Resistance: Capable of operating in a wide range of temperatures without degradation.
- Maintenance: Easy to clean and maintain, reducing downtime.
- Cost-Effectiveness: Offers a balance between performance and affordability.
Rubber Drive Roller
Rubber drive rollers are critical in transmitting power within conveyor systems. Their rubber coating ensures efficient transfer of motion from the drive unit to the conveyor belt.
- Power Transmission: Excellent at transferring motor power to the conveyor belt with minimal slippage.
- Energy Efficiency: Reduces energy consumption by optimizing the transfer of power.
- Load Handling: Capable of moving heavy loads without deforming or losing grip.
- Speed Control: Allows for precise control over conveyor speed due to its high friction surface.
- Noise Reduction: Acts to dampen operational noise, contributing to a quieter workspace.
- Vibration Absorption: Minimizes vibrations, protecting sensitive goods and machinery components.
- Longevity: The rubber coating is resistant to cuts and abrasions, ensuring long-term use.
- Adaptability: Performs well under various environmental conditions, including exposure to chemicals.
- Ease of Replacement: Designed for quick and easy replacement to minimize operational disruptions.
Rubber Roller Covering
Rubber roller covering refers to the process of applying a rubber coat to existing rollers, offering a cost-effective way to enhance performance without the need for complete replacement.
- Customization: Tailored to fit the specific dimensions and requirements of existing rollers.
- Restoration: Revitalizes worn or damaged rollers, extending their service life.
- Surface Options: Available in a range of textures, from smooth to patterned, for different applications.
- Chemical Resistance: Provides protection against corrosive substances, preserving the roller’s core.
- Impact Absorption: Excellent for applications where rollers are subject to heavy impacts.
- Sealing Properties: Helps in sealing the ends of rollers to prevent ingress of contaminants.
- Aesthetic Improvement: Can be used to improve the appearance of old rollers, maintaining a professional look.
- Retrofitting: Allows for the upgrade of conveyor systems without significant modifications.
- Environmental Suitability: Can be formulated to resist UV light, ozone, and extreme weather conditions.
To Choose the Right Type of Rubber Coating
Selecting the appropriate rubber coating for impact conveyor rollers involves considering several factors:
- Application Requirements: Assess the primary function of the roller within the conveyor system.
- Material Characteristics: Consider the types of materials being conveyed, including weight, texture, and sensitivity.
- Environmental Conditions: Evaluate the operating environment, including temperature, humidity, and exposure to chemicals.
- Load Capacity: Determine the maximum load the rollers need to support.
- Speed Requirements: Identify the desired speed of the conveyor system.
- Maintenance Considerations: Factor in the ease of maintenance and cleaning.
- Budget Constraints: Balance performance needs with available budget.
- Durability Expectations: Consider the expected lifespan and wear resistance.
- Regulatory Compliance: Ensure the chosen rollers meet industry standards and regulations.
By carefully assessing these points, businesses can select the rubber coated impact conveyor roller type that best suits their operational needs, optimizing efficiency and productivity.
How to Select the Best Rubber Coated Impact Conveyor Roller
In the realm of material handling and conveyor systems, the selection of the best rubber coated impact conveyor roller is not just a matter of choice but a critical decision that affects the overall efficiency, safety, and cost-effectiveness of the operation. The right roller can significantly enhance the conveyor’s performance, while a poor choice can lead to frequent maintenance issues, operational downtime, and increased costs. Here, we delve into the essential factors and tips that guide you in selecting the highest quality rubber coated impact conveyor rollers for your specific needs.
Factors to Consider
When it comes to choosing the right rubber coated impact conveyor roller, several key factors come into play. These considerations ensure that the roller not only fits the system but also enhances its operation:
- Material Type: Different materials require different types of rubber coatings for optimal interaction and longevity.
- Load Capacity: It’s crucial to select rollers that can handle the weight and stress of the materials being transported.
- Operating Environment: Environmental conditions such as temperature, moisture, and chemical exposure can significantly affect roller performance.
- Speed Requirements: The operational speed of the conveyor system dictates the need for rollers designed to minimize friction and wear at higher speeds.
- Abrasion Resistance: In environments where materials are abrasive, choosing rollers with high abrasion-resistant coatings is vital.
- Impact Resistance: For systems prone to heavy impacts, selecting rollers with enhanced impact resistance prevents premature failure.
- Maintenance Needs: Opting for rollers that are easy to maintain and clean can reduce downtime and operational costs.
- Compatibility: Ensuring that the rollers are compatible with the existing system prevents the need for unnecessary modifications.
Tips on Identifying High-Quality Rubber Coated Rollers
Identifying high-quality rubber coated impact conveyor rollers involves more than just examining specifications. It’s about understanding the nuances that contribute to the roller’s performance and durability:
- Certifications: Quality rollers often come with certifications that attest to their manufacturing and performance standards.
- Manufacturer Reputation: A reputable manufacturer is more likely to produce high-quality, reliable rollers.
- Material Specifications: Detailed specifications can help you understand if the roller’s material composition suits your needs.
- Warranty: A strong warranty indicates the manufacturer’s confidence in their product’s performance and durability.
- Customer Reviews: Feedback from other users can provide real-world insights into the roller’s quality and reliability.
- Customization Options: The ability to customize rollers to specific needs often correlates with higher quality.
- Technical Support: Good manufacturers provide excellent technical support, helping you choose the right roller for your application.
- Sample Testing: Testing a sample in your own system can be the ultimate test of a roller’s suitability and quality.
- Price Comparison: While not the only factor, comparing prices can help ensure you’re getting the best value for the quality.
By carefully considering these factors and following these tips, you can make an informed decision when selecting rubber coated impact conveyor rollers, ensuring that your conveyor system operates efficiently, safely, and cost-effectively.
Used vs. New Rubber Coated Impact Conveyor Roller
When it comes to enhancing or maintaining a conveyor system, one critical decision is whether to invest in new or used rubber coated impact conveyor roller. This choice can significantly affect both the performance and the cost-effectiveness of your conveyor operations.
Pros and Cons of Buying Used Rubber Coated Impact Conveyor Rollers
Pros:
- Cost Savings: The most apparent advantage is the potential for significant cost savings compared to purchasing new rollers.
- Environmental Impact: Opting for used rollers can be a more sustainable choice, reducing waste and the demand for new materials.
- Immediate Availability: Used rollers are often available for immediate delivery, bypassing potential manufacturing or shipping delays associated with new orders.
- Proven Performance: Some users prefer equipment that has been “broken in” and has a known performance record in real-world conditions.
- Refurbishment Potential: Used rollers can sometimes be refurbished or re-coated, extending their service life at a fraction of the cost of new ones.
Cons:
- Wear and Tear: Used rollers may have reduced lifespan and efficiency due to previous wear.
- Unknown History: The history of used rollers, including exposure to harsh conditions or chemicals, may not be fully known.
- Maintenance Costs: There may be higher maintenance or replacement costs sooner than with new rollers.
- Limited Selection: Finding used rollers that match your specific requirements in terms of size, material, and coating can be challenging.
Assessing the Condition of Used Rollers
To ensure that used rubber coated impact conveyor rollers meet your needs, consider the following points:
- Visual Inspection: Check for visible signs of wear, such as cracks, tears, or significant abrasions on the rubber coating.
- Manufacturer and Model: Verify the manufacturer and model to ensure compatibility with your system and to check if the rollers were designed for your intended application.
- Operational History: Inquire about the operational history, including the type of environment they were used in and the materials they conveyed.
- Bearing Condition: Bearings are critical to roller performance; assess their condition or consider if they can be easily replaced.
- Rubber Hardness: Measure the hardness of the rubber coating to ensure it matches the requirements of your application.
- Dimensional Accuracy: Ensure the rollers are still within their original dimensional tolerances, as wear and tear can alter their shape and size.
- Compatibility with Your Conveyor: Confirm that the rollers are fully compatible with your conveyor system, including the mounting and drive mechanisms.
- Safety Standards: Check that the rollers still meet relevant safety and operational standards for your industry.
- Warranty or Guarantee: While used equipment often comes without a warranty, some suppliers may offer a short-term guarantee or return policy for peace of mind.
By carefully considering these factors, you can make an informed decision between used and new rubber coated impact conveyor roller, ensuring that your conveyor system operates efficiently and cost-effectively.
Where to Find Rubber Coated Impact Conveyor Rollers for Sale
Securing high-quality rubber coated impact conveyor roller is pivotal for the efficiency and longevity of your conveyor system. Identifying reputable suppliers and understanding the significance of certifications can guide you to make informed purchasing decisions.
Finding Reputable Suppliers and Manufacturers
- Industry Trade Shows: Trade shows offer a platform to meet multiple suppliers, compare products firsthand, and discuss your needs directly.
- Online Directories: Websites like ThomasNet and Alibaba list manufacturers and suppliers, complete with ratings and reviews to help gauge reliability.
- Referrals: Recommendations from industry peers or associations can lead you to trusted suppliers known for quality products.
- Manufacturer Websites: Directly visiting the websites of known manufacturers can provide detailed product information and direct sales options.
- Online Forums and Groups: Industry-specific online communities can offer insights into where to find reliable roller suppliers.
- Distributor Networks: Established distributors often have partnerships with multiple manufacturers, offering a range of products and expert advice.
- Local Industrial Suppliers: Local suppliers can provide personalized service and quicker delivery times, along with easier returns or exchanges if needed.
- Product Catalogs: Comprehensive catalogs from manufacturers or distributors can help you compare specifications and pricing at your leisure.
The Importance of Certifications and Standards
- Quality Assurance: Certifications like ISO9001:2008 ensure that the manufacturer adheres to internationally recognized quality management principles.
- Product Safety: Standards such as MA (Mining Safety) and TUV (Technical Inspection Association) certify that products meet specific safety requirements.
- Consistency: Certified manufacturers are more likely to provide products that consistently meet or exceed quality and performance expectations.
- Reliability: Certifications are indicative of a manufacturer’s commitment to reliability and continuous improvement.
- Compliance: Adhering to industry standards ensures that products comply with legal and regulatory requirements.
- Customer Confidence: Purchasing from certified suppliers increases confidence in the durability and performance of the rollers.
- Global Recognition: International standards facilitate the acceptance of products in markets worldwide, ensuring compatibility and performance.
- Environmental Responsibility: Certifications can also indicate a manufacturer’s commitment to environmental management and sustainability practices.
- Risk Reduction: Certified products reduce the risk of failures and downtime, contributing to smoother operations and lower maintenance costs.
When searching for rubber coated impact conveyor roller for sale, prioritizing suppliers who demonstrate a commitment to quality and safety through certifications and standards is crucial. This approach not only ensures the acquisition of superior products but also supports the overall success and efficiency of your conveyor system.
Maintenance and Care for Rubber Coated Impact Conveyor Roller
Ensuring the longevity and optimal performance of rubber coated impact conveyor roller is crucial for maintaining the efficiency of conveyor systems. Proper maintenance and care routines can significantly extend the life of these rollers, prevent downtime, and save costs associated with replacements and repairs.
Basic Maintenance Tips
- Regular Inspections: Conduct routine inspections to check for signs of wear, damage, or misalignment. Early detection of issues can prevent more serious problems down the line.
- Lubrication: Keep the roller bearings lubricated according to the manufacturer’s recommendations. Proper lubrication reduces friction, wear, and overheating.
- Alignment Checks: Ensure that the rollers are correctly aligned. Misalignment can cause uneven wear and tear, reducing the efficiency of the conveyor system.
- Load Distribution: Monitor the distribution of materials on the conveyor to avoid overloading certain sections. Uneven loads can lead to premature wear of the rollers.
- Cleaning Schedule: Implement a regular cleaning schedule to remove debris, dust, and other materials that could degrade the rubber coating over time.
- Temperature Monitoring: Avoid exposing the rollers to extreme temperatures, which can affect the rubber’s elasticity and overall durability.
- Replacement Planning: Plan for timely replacements based on the expected lifespan of the rollers and the specific demands of your operation.
- Use of Compatible Materials: Ensure that the materials being conveyed are compatible with the rubber coating to prevent chemical degradation.
- Professional Assessments: Periodically, have a professional assess the condition of the rollers and the conveyor system to identify any potential issues that may not be immediately apparent.
Cleaning and Storing Tips
- Cleaning Agents: Use cleaning agents that are compatible with the rubber coating. Harsh chemicals can damage the rubber and reduce the roller’s lifespan.
- Soft Cleaning Tools: Use soft brushes or cloths to clean the rollers. Abrasive tools can scratch or wear away the rubber coating.
- Regular Cleaning: Clean the rollers regularly to prevent the buildup of materials that could cause the rollers to stick or degrade.
- Dry After Cleaning: Ensure that the rollers are thoroughly dried after cleaning to prevent moisture from causing rust or corrosion on the metal parts.
- Proper Storage: If storing spare rollers, keep them in a cool, dry place away from direct sunlight, which can cause the rubber to deteriorate.
- Avoid Stacking: When storing, avoid stacking the rollers on top of each other as the weight can deform the rubber coating.
- Protective Coverings: Use protective coverings to shield stored rollers from dust and debris.
- Rotation: If possible, rotate the stored rollers periodically to prevent the rubber from settling or deforming in one position.
Adhering to these maintenance and care tips for rubber coated impact conveyor roller can significantly enhance their performance and longevity. This proactive approach not only ensures the smooth operation of your conveyor system but also contributes to a more cost-effective and reliable material handling solution.
FAQs about Rubber Coated Impact Conveyor Roller
For conveyor belts, the choice of roller is crucial for the efficiency and longevity of the conveyor system. The most common type of roller used is the carrying roller, also known as the idler roller. These rollers support the conveyor belt and the material being transported. They are spaced throughout the length of the conveyor to prevent the belt from sagging under the weight of the load. Carrying rollers are typically made from steel or heavy-duty plastic, depending on the application and the weight of the materials being moved. For heavier loads or harsher environments, steel rollers are preferred for their durability and strength. In environments where corrosion resistance or quieter operation is needed, plastic rollers may be used. The choice between these materials and roller types depends on the specific requirements of the conveyor system, including load weight, belt speed, and environmental conditions.
Impact rollers, or impact idlers, are specialized rollers designed to absorb the shock and impact of falling material near the loading zone of a conveyor belt. This area is subject to higher stress and wear as materials are dropped onto the belt from a height, which can cause damage to both the belt and the standard rollers. Impact rollers are constructed with a series of rubber discs or rings mounted on a steel frame to cushion the blow of material. These rubber components help distribute the force of the impact, reducing damage and wear to the conveyor belt and ensuring smoother operation. Impact rollers are essential for extending the lifespan of conveyor systems in industries where bulk materials, such as in mining, quarrying, and aggregate, are frequently loaded onto the belt.
Roller conveyors are versatile systems used to move goods and materials through manufacturing and distribution environments. There are several types of roller conveyors, each suited to different applications:
Gravity Roller Conveyors: Use gravity to move items across a slight downward slope. They are cost-effective and require no power source.
Powered Roller Conveyors: Use motors to move materials along the conveyor path. They are suitable for heavier loads or where controlled speeds are necessary.
Accumulation Conveyors: Allow products to accumulate without pressure, reducing the risk of damage. They can be either gravity-powered or motorized.
Flexible Roller Conveyors: Can be expanded, contracted, and curved, making them adaptable to various spaces and applications.
Live Roller Conveyors: Powered rollers that move the load. Ideal for heavy loads and are used in automated and semi-automated production environments.
Each type offers unique benefits and is chosen based on the specific needs of the operation, such as load weight, speed requirements, and the degree of automation.
For conveyor belt rollers required to hold heavy radial loads, such as in mining, quarrying, or bulk material handling, heavy-duty rollers with reinforced structures and high-quality bearings are used. These rollers are typically made from steel due to its strength and durability under heavy loads. The bearings play a crucial role in supporting the radial loads while allowing the roller to turn smoothly. Tapered roller bearings are often used in these applications for their ability to handle both radial and axial loads effectively. Additionally, these heavy-duty rollers may feature special sealing mechanisms to protect the bearings from dust, debris, and water, ensuring longer life and reliability under harsh operating conditions. The design and materials of these rollers are critical to their performance, ensuring they can withstand the demands of heavy-duty applications without failure.
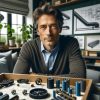
Jordan Smith, a seasoned professional with over 20 years of experience in the conveyor system industry. Jordan’s expertise lies in providing comprehensive solutions for conveyor rollers, belts, and accessories, catering to a wide range of industrial needs. From initial design and configuration to installation and meticulous troubleshooting, Jordan is adept at handling all aspects of conveyor system management. Whether you’re looking to upgrade your production line with efficient conveyor belts, require custom conveyor rollers for specific operations, or need expert advice on selecting the right conveyor accessories for your facility, Jordan is your reliable consultant. For any inquiries or assistance with conveyor system optimization, Jordan is available to share his wealth of knowledge and experience. Feel free to reach out at any time for professional guidance on all matters related to conveyor rollers, belts, and accessories.