Various Conveyor Rollers Sizes:Diameter 、Length And Custom
Selecting the correct conveyor roller size is paramount for ensuring efficiency and durability in industrial and manufacturing applications. The right size not only optimizes the operation of the conveyor system but also minimizes wear and tear, thereby extending the equipment’s lifespan. This introductory guide aims to provide a thorough exploration of various conveyor roller sizes and their respective applications. Understanding the intricacies of conveyor roller size can dramatically affect system performance and operational costs. By delving into this guide, readers will gain the knowledge needed to make informed decisions on the most appropriate conveyor roller size for their specific operational needs, ensuring that their systems are both effective and efficient.
What are Conveyor Roller Sizes
Conveyor rollers come in a variety of sizes to suit different applications and conveyor systems. The size of a conveyor roller typically includes the diameter and length of the roller. Here are some common conveyor roller sizes:
Diameter Sizes
- Small Diameter Rollers: 1-2 inches (25-50 mm)
- Medium Diameter Rollers: 3-5 inches (75-127 mm)
- Large Diameter Rollers: 6 inches and above (150 mm and above)
Length Sizes
- Short Rollers: 12-18 inches (300-450 mm)
- Medium Length Rollers: 24-36 inches (600-900 mm)
- Long Rollers: 42 inches and above (1067 mm and above)
Additional Specifications
- Wall Thickness: Varies depending on the material and load requirements, typically ranging from 0.065 inches (1.65 mm) to 0.375 inches (9.52 mm).
- Shaft Diameter: The diameter of the shaft or axle of the roller, commonly 0.5 inches (12.7 mm) to 1.5 inches (38 mm).
- Material: Rollers can be made from various materials, including steel, stainless steel, aluminum, PVC, and nylon, depending on the application requirements.
Custom Sizes
- Many manufacturers offer custom roller sizes to meet specific needs, taking into account the load, speed, environment, and other factors.
Specific Examples
- Standard Duty Rollers: Typically have diameters ranging from 1.9 inches (48.26 mm) to 2.5 inches (63.5 mm).
- Heavy Duty Rollers: Typically have diameters ranging from 3 inches (76.2 mm) to 5 inches (127 mm) or more.
Conveyor Roller Size Chart
The conveyor roller size chart serves as an essential tool for selecting the correct roller dimensions for various applications. This chart lists standard roller diameters, lengths, and recommends suitable applications based on these measurements. For instance, common sizes highlighted in the chart include rollers with diameters of 1 inch and 4 inches. The 1-inch diameter rollers are typically used in less demanding environments, whereas the 4-inch rollers are suited for heavier loads. This comprehensive overview allows users to quickly identify the conveyor roller size needed for their specific systems, enhancing both efficiency and reliability.
Roller Diameter | Roller Length | Roller Length | Roller Length | Load Capacity (lbs) | Material |
---|---|---|---|---|---|
1.5 inches (38 mm) | 12-42 inches (305-1067 mm) | 0.5 inches (12.7 mm) | 0.065 inches (1.65 mm) | 50-100 | Steel, PVC |
1.9 inches (48.26 mm) | 12-48 inches (305-1220 mm) | 0.625 inches (15.88 mm) | 0.075 inches (1.90 mm) | 100-200 | Steel, Stainless Steel, PVC |
2.5 inches (63.5 mm) | 18-60 inches (457-1524 mm) | 0.75 inches (19.05 mm) | 0.090 inches (2.29 mm) | 200-300 | Steel, Aluminum |
3 inches (76.2 mm) | 24-72 inches (610-1829 mm) | 1 inch (25.4 mm) | 0.125 inches (3.18 mm) | 300-500 | Steel, Nylon |
4 inches (101.6 mm) | 24-84 inches (610-2134 mm) | 1.25 inches (31.75 mm) | 0.140 inches (3.56 mm) | 500-800 | Steel, Stainless Steel |
5 inches (127 mm) | 30-96 inches (762-2438 mm) | 1.5 inches (38.1 mm) | 0.188 inches (4.78 mm) | 800-1200 | Steel |
6 inches (152.4 mm) | 36-120 inches (914-3048 mm) | 1.75 inches (44.45 mm) | 0.250 inches (6.35 mm) | 1200-2000 | Steel |
Notes:
- Roller Diameter: The external diameter of the roller.
- Roller Length: The length of the roller, which is usually determined by the width of the conveyor.
- Shaft Diameter: The diameter of the internal shaft or axle on which the roller rotates.
- Wall Thickness: The thickness of the roller’s outer material.
- Load Capacity: The maximum load that each roller can support, which can vary based on material and construction.
- Material: The material from which the roller is made, affecting its strength, weight, and suitability for different environments.
This chart provides a general overview and typical sizes; however, custom sizes and specifications can be manufactured to meet specific requirements. For exact details and to ensure proper fit and function within a conveyor system, it’s advisable to consult with the roller manufacturer or a conveyor system specialist.
Selecting the Right Conveyor Roller Sizes
Selecting the right conveyor roller sizes involves considering several factors to ensure optimal performance and efficiency of your conveyor system. Here are key considerations and steps to help you choose the appropriate roller sizes:
Load Capacity
- Weight of Items: Determine the maximum weight of the items being conveyed. Choose rollers that can handle this load without deforming or failing.
- Distribution of Weight: Ensure that the load is evenly distributed across the rollers to avoid excessive wear on specific rollers.
Roller Diameter
- Load Requirements: Larger diameter rollers can support heavier loads and reduce the deflection under load.
- Speed and Efficiency: Larger rollers can reduce the number of revolutions needed, thus reducing wear and increasing the lifespan of the rollers.
Roller Length
- Conveyor Width: The roller length should match the width of the conveyor system.
- Item Dimensions: Ensure that the rollers are long enough to support the items being conveyed without sagging or falling off.
Shaft Diameter and Wall Thickness
- Structural Integrity: Thicker shafts and walls increase the strength and load-bearing capacity of the rollers.
- Environmental Factors: In harsh environments, thicker walls can provide additional durability and resistance to damage.
Material
- Application Needs: Different materials are suited for different environments and applications.
- Steel: Ideal for heavy loads and high-impact applications.
- Stainless Steel: Suitable for corrosive environments, such as food processing or chemical industries.
- PVC/Nylon: Lightweight and corrosion-resistant, suitable for light to medium loads.
- Aluminum: Lightweight and durable, suitable for various industrial applications.
Environmental Conditions
- Temperature: High or low temperatures can affect the material choice and size. For example, extreme heat may require rollers made from heat-resistant materials.
- Corrosive Environments: Stainless steel or coated rollers are preferred in corrosive environments.
Speed Requirements
- Operational Speed: Higher speeds may require larger rollers to reduce rotational speed and wear.
- Smooth Operation: Larger diameters can provide smoother operation at higher speeds.
Specific Application Requirements
- Special Conditions: Applications such as cleanrooms or chemical plants may have specific requirements for material and construction.
- Customization: Consider if custom roller sizes or materials are needed for your specific application.
Steps to Select the Right Roller Size
- Assess Your Needs: Understand the specifics of what you are conveying, including weight, size, and environmental conditions.
- Consult Specifications: Refer to standard roller size charts and specifications to find suitable options.
- Evaluate Load Capacity: Choose a roller size that can handle the maximum load with a margin for safety.
- Consider Material: Select the material that best suits your application needs and environmental conditions.
- Check Compatibility: Ensure the selected rollers are compatible with your conveyor system in terms of length, diameter, and mounting options.
- Seek Expert Advice: When in doubt, consult with a conveyor system specialist or manufacturer to get recommendations tailored to your specific requirements.
By carefully considering these factors, you can select the right conveyor roller sizes to ensure efficient and reliable operation of your conveyor system.
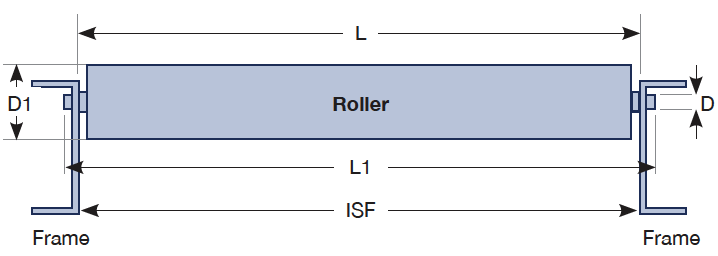
Heavy Duty Conveyor Roller Sizes
In industrial settings, selecting the right conveyor roller size for heavy-duty applications is critical. Heavy-duty conveyor roller dimensions are designed to withstand rigorous operations and heavy loads, making them ideal for industries such as mining, steel manufacturing, and heavy machinery production. For example, rollers may come in diameters of 3.5 inches, 4 inches, 5 inches, 6 inches, and up to 7 inches. These sizes ensure that the rollers can support the weight and volume of materials transported in such environments, significantly reducing the risk of downtime due to mechanical failures.
1 Inch Diameter Conveyor Rollers
Conveyor rollers with a 1-inch diameter are versatile and suitable for a wide range of applications, from packaging lines to small parts handling systems. These rollers are advantageous due to their ability to handle light to medium loads with ease, making them perfect for industries like electronic component assembly and food processing. Some typical uses include conveyor lines in pharmaceuticals, small container transfers, document handling systems, and light agricultural product transportation.
4 Inch Diameter Conveyor Rollers
The 4-inch diameter conveyor rollers are crucial for applications requiring the movement of heavy loads, such as in automotive assembly lines or large-scale distribution centers. These rollers provide robust support for large items, heavy boxes, or pallets, ensuring smooth operations under considerable weight. Applications typically benefiting from this size include pallet handling systems, heavy appliance manufacturing lines, and large-scale agricultural product processing. The use of 4-inch rollers underscores their capacity to handle not just heavier weights, but also higher volumes, making them indispensable in industrial environments.
How to Choose Conveyor Roller Belt Speed and Belt Width
Choosing the appropriate conveyor roller belt speed and belt width is crucial for ensuring efficient and reliable conveyor system performance. Here’s a guide to help you make the right decisions:
What Is Conveyor Roller Belt Speed
1. Determine Material Characteristics:
- Type of Material: Understand the type of material you are conveying (e.g., bulk materials, packaged goods).
- Material Density: Know the density of the material as it affects the belt’s load-carrying capacity.
- Flow Rate: Assess the desired flow rate or throughput.
2. Calculate Belt Speed:
- Formula: Belt speed (m/s) = (flow rate (kg/s) / (belt width (m) x material density (kg/m^3)))
- Industry Standards: Common belt speeds range from 0.5 m/s to 3.5 m/s depending on the application.
3. Consider the Type of Conveyor:
- Flat Belt Conveyors: Typically operate at lower speeds.
- Trough Belt Conveyors: Can handle higher speeds for bulk materials.
- High-Speed Conveyors: Used for applications requiring fast material movement.
4. Evaluate Conveyor Length and Incline:
- Longer Conveyors: May require higher speeds to maintain throughput.
- Inclined Conveyors: Slower speeds are preferable to prevent material rollback.
Choosing Conveyor Belt Width
1. Determine Material Load and Flow:
- Load Size: The width of the belt should accommodate the maximum load size.
- Flow Rate: Ensure the belt width supports the desired flow rate without overloading.
2. Standard Belt Widths:
- Common widths include 18″, 24″, 30″, 36″, 42″, 48″, 54″, 60″, and 72″.
- Choose a width that provides adequate clearance for the material.
3. Consider Conveyor Type and Application:
- Heavy-Duty Applications: Require wider belts to handle larger loads.
- Packaging and Sorting: May need narrower belts for precise handling.
4. Account for Space and Installation Constraints:
- Ensure the chosen belt width fits within the physical constraints of your facility.
- Consider space for maintenance and adjustments.
Balancing Speed and Width
1. Optimize for Efficiency:
- Balance belt speed and width to maximize throughput without compromising material handling.
2. Prevent Overloading:
- Ensure the belt width is sufficient to prevent material spillage and overloading at high speeds.
3. Maintain System Longevity:
- Avoid excessive speeds that can lead to increased wear and tear on the conveyor components.
Practical Steps to Implement
Conduct a Material Analysis:
- Understand the properties and behavior of the material being conveyed.
Perform Calculations:
- Use the formulas provided to calculate the optimal belt speed and width.
Consult Industry Standards:
- Refer to industry guidelines and best practices for specific conveyor applications.
Seek Expert Advice:
- Engage with conveyor system experts or suppliers to validate your choices.
Choosing the right conveyor roller belt speed and width involves understanding your material characteristics, calculating the necessary parameters, and balancing efficiency with practical constraints. By carefully considering these factors, you can optimize your conveyor system for better performance and longevity.
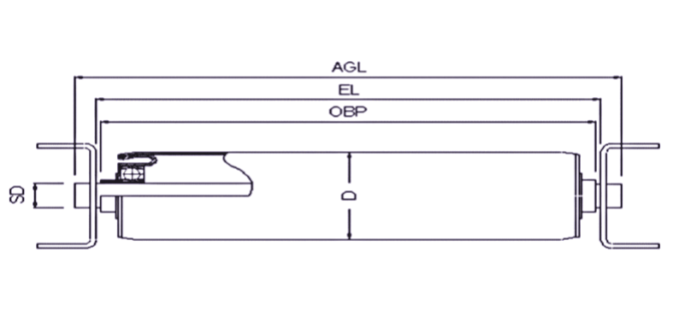
Specialty Conveyor Rollers of Conveyor Roller Size
Conveyor Roller with Bracket
Understanding the functionality and benefits of conveyor roller sizes that come equipped with brackets is essential for optimizing specific conveyor setups. These specialized rollers are designed to offer additional support and alignment within the conveyor framework, enhancing both stability and performance. Examples of applications benefiting from rollers with brackets include:
- Inclined Conveying Systems: Rollers with brackets help maintain alignment and prevent slippage in systems that transport goods at an angle.
- Curved Conveyor Sections: In curves, brackets provide the necessary support to keep rollers in place, ensuring smooth and consistent movement.
- Adjustable Conveyor Lines: Brackets allow for easy adjustments in the roller position, accommodating different product sizes and operational requirements.
- Heavy Load Applications: Enhanced support from brackets allows these rollers to handle heavier loads without bending or misalignment.
- High-Speed Operations: In systems where conveyors operate at high speeds, the additional stability from brackets helps in reducing vibrations and maintaining efficiency.
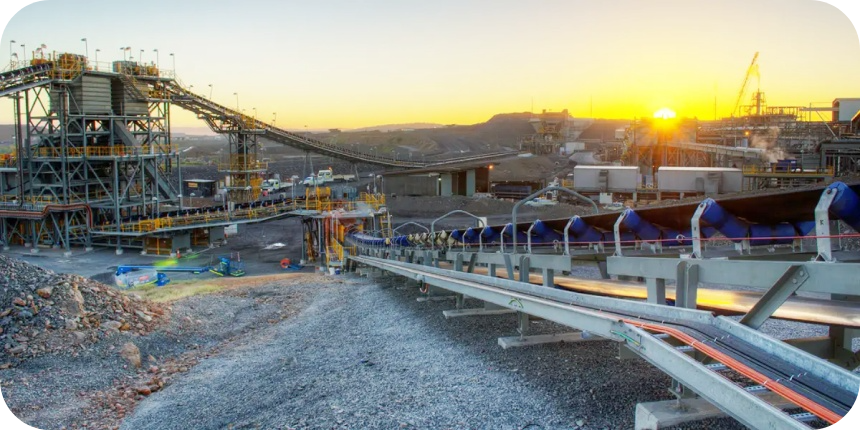
Conveyor Roller with Sprocket
Conveyor roller sizes that include sprockets play a critical role in chain-driven conveyor systems, significantly boosting their efficiency and reliability. These rollers are equipped with teethed sprockets that mesh with the conveyor’s chain, ensuring precise and consistent movement across the conveyor line. This arrangement is particularly advantageous in applications requiring synchronized operations or precise positioning of items along the conveyor.
- Assembly Lines: Rollers with sprockets ensure that components move in perfect sync, which is crucial for assembly operations requiring precise timing and positioning.
- Packaging Industries: These rollers facilitate the smooth and accurate movement of products into packaging machines, improving throughput and reducing downtime.
- Automotive Manufacturing: The precise control afforded by sprocketed rollers is essential for moving large automotive parts through various stages of assembly.
- Food Processing: In environments where cleanliness and precision are paramount, sprocketed rollers help maintain the pace and flow of production without compromising hygiene.
- Pharmaceuticals: These rollers support the stringent requirements for precise and contamination-free handling of pharmaceutical products.
Incorporating specialized conveyor roller sizes like those with brackets or sprockets can significantly enhance the functionality and efficiency of various industrial conveyor systems.
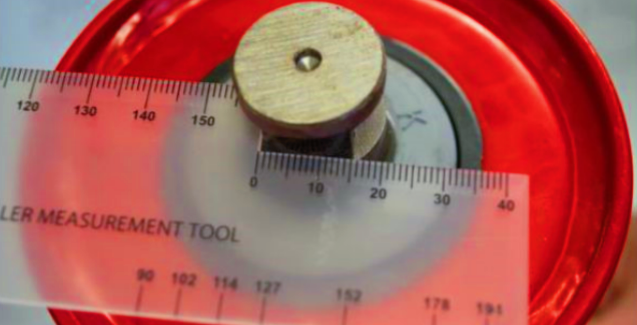
Accessories and Replacement Parts About Conveyor Roller Size
Conveyor Roller Parts
Proper maintenance and timely replacement of conveyor roller parts are crucial to ensure the longevity and efficiency of conveyor systems. Common parts that often need attention, depending on the roller conveyor dimensions and system requirements, include:
- Bearings: Essential for smooth roller operation, bearings must be lubricated and checked regularly to prevent failures.
- Axles: Axles connect the roller to the conveyor frame, and worn or corroded axles can impair roller functionality.
- End Caps: These protect the internal components of the rollers from dust, debris, and moisture, which can cause damage over time.
- Mounting Brackets: Critical for securing rollers in place, these brackets may require replacement if they become bent or damaged.
- Drive Belts: For powered roller systems, drive belts must be in good condition to ensure effective power transfer from motors to rollers.
These parts are integral to maintaining the functionality and efficiency of your conveyor system, tailored to fit various conveyor roller sizes and types.
Conveyor Roller Replacement
Replacing conveyor rollers is a necessary aspect of managing a high-performing conveyor system. Effective replacement depends not only on the condition of the rollers but also on choosing the right conveyor roller size and type for your specific application. Here are key considerations and steps for replacing conveyor rollers:
- Assessment: Regularly inspect rollers for signs of wear, such as uneven rotation, noise, or visible damage. Early identification helps prevent system disruptions.
- Matching Roller Size: Ensure that the replacement roller matches the exact specifications of the conveyor roller dimensions needed for your system. This includes diameter, length, and load capacity.
- Removal of Old Rollers: Safely disconnect or dismantle the part of the conveyor system that holds the damaged roller. This may involve loosening brackets or removing pins.
- Installation of New Rollers: Insert the new roller into the conveyor frame, securing it with the necessary hardware, such as axles, pins, or brackets.
- Testing: Once the roller is installed, test the conveyor system to ensure that the new roller integrates smoothly and operates as expected.
By following these steps, you can ensure that your conveyor system remains efficient and minimizes downtime due to worn or damaged rollers. Regular checks and maintenance tailored to the specific conveyor roller size and type of your system are key to long-term performance and reliability.
Choosing the Right Manufacturer for Conveyor Roller Size
Conveyor Roller Manufacturer
Selecting a reliable conveyor roller manufacturer is critical to ensuring that you receive products of high quality, durability, and consistent performance. The right manufacturer will have a proven track record in producing conveyor rollers that meet specific industry standards and requirements. When assessing conveyor roller manufacturers, consider the following key aspects:
- Quality Assurance: A reputable manufacturer will have stringent quality control processes in place to ensure that every conveyor roller meets the required specifications and performance standards. This includes regular testing and inspections during the manufacturing process.
- Product Range: Choose a manufacturer that offers a wide range of conveyor roller sizes and types to suit different industrial applications. A diverse product range indicates the manufacturer’s capability to cater to various customer needs.
- Customization Capabilities: Depending on your specific needs, you may require custom conveyor roller sizes or features. A good manufacturer should be able to provide custom solutions that fit your specific conveyor system requirements.
- Technical Support: Reliable manufacturers provide excellent customer service and technical support. This includes assistance with choosing the correct conveyor roller size, installation guidance, and help with troubleshooting any issues that arise.
- Industry Reputation: Look for a manufacturer with a solid reputation in the industry. This can be gauged through customer reviews, case studies, and industry awards. A well-regarded manufacturer is likely to provide reliable and high-quality conveyor rollers.
By carefully selecting a conveyor roller manufacturer that meets these criteria, you ensure that your conveyor systems operate efficiently, with minimal downtime and maintenance costs. Moreover, the right manufacturer will help you select the ideal conveyor roller size for your specific application, ensuring optimal system performance.
Steps to Choose the Right Manufacturer
1. Research and Shortlist Manufacturers:
- Online Research: Conduct thorough online research to identify potential manufacturers.
- Industry Networks: Use industry networks, trade shows, and professional associations to find reputable manufacturers.
2. Evaluate Manufacturer Capabilities:
- Product Range: Assess the range of conveyor rollers offered by each manufacturer.
- Customization Options: Confirm their ability to customize products according to your specifications.
3. Request Samples and Prototypes:
- Sample Evaluation: Request samples or prototypes to evaluate the quality and suitability of the rollers for your application.
- Testing: Conduct in-house testing or third-party testing to ensure the rollers meet your requirements.
4. Assess Manufacturer’s Production Facilities:
- Site Visits: If possible, visit the manufacturer’s production facilities to assess their production capabilities and quality control processes.
- Production Capacity: Ensure the manufacturer can meet your demand in terms of volume and delivery timelines.
5. Review Terms and Conditions:
- Pricing: Compare pricing from different manufacturers, but don’t compromise on quality for cost.
- Delivery and Lead Times: Check the delivery schedules and lead times to ensure they align with your project timelines.
6. Check References and Reviews:
- Customer Feedback: Speak to other customers who have used the manufacturer’s products.
- Online Reviews: Read online reviews and ratings to gauge customer satisfaction and potential issues.
Choosing the right manufacturer for conveyor roller size involves thorough research, evaluation of product quality, and ensuring the manufacturer’s ability to meet your specific needs. By considering factors such as reputation, quality standards, customization capabilities, and customer support, you can select a manufacturer that will provide reliable and efficient conveyor rollers for your system.
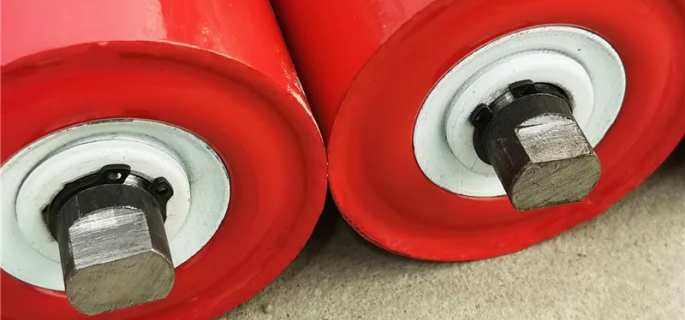
Making Your Purchase for Conveyor Roller Size
Conveyor Roller Size for Sale
When looking to purchase conveyor rollers, several key factors should be considered to ensure that you select the most suitable options for your system. Understanding the importance of conveyor roller size, material, and other critical features can greatly influence the effectiveness and longevity of your conveyor system.
- Conveyor Roller Size: Ensure that the roller size is compatible with your system. This includes the diameter and length of the rollers, which should match the specifications required for your operations to maintain efficiency and reduce wear.
- Material: The material of the conveyor rollers affects their durability and suitability for different environments.While plastic rollers might be better for lighter loads and corrosive environments, Steel rollers are robust and ideal for heavy-duty applications .
- Load Capacity: Check the load capacity of the rollers. It’s important that the rollers can handle the weight and type of materials they will be transporting to avoid breakdowns and maintain safety.
- Manufacturer Reputation: Choose rollers from manufacturers with good reputations for quality and reliability. Research their track record, read customer reviews, and perhaps even contact existing users to gauge satisfaction levels.
- Warranty and Support: Look for products that come with warranties and good customer support. Having support from the manufacturer can be invaluable for addressing any issues that arise and for guidance on maintenance and replacements.
Contacting Suppliers
Once you have a clear idea of the type and size of conveyor rollers needed, the next step is to reach out to reputable suppliers or manufacturers. It is crucial to engage with suppliers who are known for their quality products and reliability. When contacting suppliers, provide them with detailed specifications of your conveyor roller size and other requirements. Ask for detailed product information, pricing, and availability. Also, inquire about customization options if your application requires specific modifications. This direct communication helps in making an informed decision and ensures that you receive conveyor rollers that perfectly match your system’s needs and expectations. Remember, a trustworthy supplier will be keen to understand your needs and offer solutions that enhance the performance of your conveyor system.
Your source for top conveyor rollers – contact us now!
FAQs About Conveyor Roller Size
The standard size of a conveyor roller can vary widely depending on the application and the system it is used in. However, typical diameters for conveyor rollers range from 0.75 inches to 8 inches. The most common diameters are between 1.9 inches and 3.5 inches. The face length of the rollers can also vary, generally extending from a few inches up to several feet, tailored to match the width of the conveyor belts they support. It’s important to select a roller size that matches the requirements of the specific conveyor system to ensure efficient operation and minimal wear and tear.
To accurately measure a conveyor roller, you need to determine three key dimensions: the diameter, the face length, and the axle size. The diameter can be measured using a caliper; it’s the distance across the roller, passing through the center. The face length is the width of the roller and can be measured from one end to the other, excluding any axles or hardware protruding beyond the body of the roller. Finally, measure the axle size by determining the diameter of the shaft or axle that fits through the roller’s bearings. These measurements are crucial for ensuring the replacement rollers fit perfectly into your existing system.
Choosing the right conveyor rollers involves several considerations to ensure compatibility with your system and optimal performance. First, determine the load requirements—both weight and type of materials—as this will influence the roller material and size. Consider the environment in which the system operates; for instance, choose corrosion-resistant materials for humid or chemically active environments. Evaluate the speed at which your conveyor will operate, as this will impact the type of bearings needed. Lastly, consider the manufacturer’s reputation and the availability of replacements and support. Selecting rollers that are too small or too large can lead to inefficiencies and increased maintenance costs, so it’s important to match the roller specifications precisely to your system’s needs.
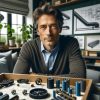
Jordan Smith, a seasoned professional with over 20 years of experience in the conveyor system industry. Jordan’s expertise lies in providing comprehensive solutions for conveyor rollers, belts, and accessories, catering to a wide range of industrial needs. From initial design and configuration to installation and meticulous troubleshooting, Jordan is adept at handling all aspects of conveyor system management. Whether you’re looking to upgrade your production line with efficient conveyor belts, require custom conveyor rollers for specific operations, or need expert advice on selecting the right conveyor accessories for your facility, Jordan is your reliable consultant. For any inquiries or assistance with conveyor system optimization, Jordan is available to share his wealth of knowledge and experience. Feel free to reach out at any time for professional guidance on all matters related to conveyor rollers, belts, and accessories.