Ashland Conveyor Rollers: Key Features Explained
Ashland Conveyor is renowned for its extensive range of conveyor systems, including the highly versatile Ashland Conveyor Rollers. These rollers are integral components of both simple and complex material handling setups, catering to a diverse array of industries. The adaptability of Ashland Conveyor Rollers allows for their use in various applications, from light-duty packaging lines to heavy-duty industrial manufacturing processes. They are designed to meet the specific needs of different sectors, ensuring efficient and reliable movement of goods across numerous environments. This introduction will delve deeper into how these rollers can optimize operations and contribute significantly to the streamlining of production and distribution processes.
Ashland Conveyor Rollers for Sale
Ashland Conveyor offers a diverse array of Ashland Conveyor Rollers tailored to meet the needs of different industries and applications. The company provides a variety of rollers, each designed to optimize efficiency and functionality across various systems.
Variety of Rollers
Ashland Conveyor provides an extensive selection of conveyor rollers, ensuring that there is an option available for any requirement. Among the types available are:
- Standard Steel Rollers: These are robust and suitable for general purpose applications. Their durability makes them ideal for handling heavy loads.
- Plastic Rollers: Lightweight and corrosion-resistant, these rollers are perfect for environments where moisture or chemical exposure is a concern.
- Grooved Rollers: Designed to handle belts and provide directional stability to the conveyor system.
- Tapered Rollers: These are used in curved conveyors, aiding in maintaining the alignment of packages as they move.
Each type of Ashland Conveyor Roller has distinct features and benefits. For example, steel rollers are highly durable and capable of handling high load capacities, while plastic rollers offer a quiet operation and resistance to corrosion, making them suitable for food processing environments.
Gravity Conveyor Rollers
Gravity conveyor rollers function by allowing goods to move by force of gravity or manual push, making them a cost-effective solution for many industries. Common uses of gravity rollers include:
- Material Handling in Warehouses: Facilitating the easy movement of boxes and pallets.
- Assembly Lines: Providing efficient product movement and assembly point transitions.
- Loading and Unloading Areas: Speeding up the process of loading goods onto trucks or storage areas.
- Packaging Stations: Assisting in the smooth transit of products through packaging processes.
When comparing gravity rollers to other types of conveyor rollers, gravity rollers typically require less maintenance and energy, as they do not rely on motor power. This comparison can be illustrated through detailed tables showing energy consumption, maintenance costs, and operational efficiency.
Power Belt Conveyor Rollers
Power belt conveyor rollers play a critical role in powered conveyor systems by using motorized belts to move goods efficiently through production lines or distribution centers. The advantages of using belt-driven rollers include:
- Increased Speed and Efficiency: Motorized movement speeds up the transport of goods, particularly over long distances.
- Enhanced Control: Belt-driven systems allow for more precise control of the movement and positioning of goods, which is crucial for delicate or high-value items.
- Versatility: These rollers can be used in a variety of settings, from heavy manufacturing to distribution centers.
- Reduced Labor Costs: Automation reduces the need for manual handling, thereby lowering labor costs and enhancing safety.
Ashland Conveyor Rollers are designed to enhance the functionality and efficiency of both gravity and power-driven conveyor systems, making them indispensable in modern industrial operations.
Ashland Conveyor Rollers Parts
Maintaining optimal performance of conveyor systems is crucial for operational efficiency, which is why understanding the parts and maintenance of ashland conveyor roller is essential. This section provides an overview of the key replacement parts and offers practical tips for maintaining your Ashland conveyor rollers. Additionally, it includes a guide on selecting the right parts to ensure your conveyor system continues to operate effectively.
Overview of Replacement Parts and Maintenance Tips
Ashland Conveyor Rollers are designed for durability and longevity, but regular maintenance and timely replacement of certain parts are essential to avoid downtime.
- Roller Bearings: Essential for smooth roller operation, they must be inspected regularly and replaced if they show signs of wear or damage.
- Axles and Shafts: These components support the rollers and must be checked for bending or breakage.
- Drive Belts: For powered roller systems, worn or slack drive belts can affect the efficiency of the entire system and should be replaced as needed.
- Frame and Brackets: Structural components that must be routinely inspected for integrity and stability.
Maintenance tips for Ashland Conveyor Rollers include regular lubrication of bearings, periodic adjustment of roller alignment, and immediate replacement of any worn or damaged parts. Regular cleaning of the rollers and the conveyor track can also prevent material build-up that might hinder roller movement.
Guide on How to Select the Right Parts for Your Conveyor System
Selecting the right parts for your Ashland Conveyor Rollers is crucial for maintaining system performance and extending its lifespan.
- Identify the Specific Roller Model: Ensure the parts are compatible with the specific model of Ashland Conveyor Rollers you have in your system.
- Consider the Load Requirements: Choose parts that can handle the load requirements of your conveyor. For example, heavier loads may require more robust bearings and axles.
- Evaluate the Environment: If the conveyor operates in a harsh environment, select parts that are designed for high resistance to wear, corrosion, or chemical exposure.
- Consult Technical Support: Ashland Conveyor’s customer service can provide expert advice and recommendations on the appropriate parts for your specific conveyor system.
By following these guidelines and understanding the key aspects of ashland roller conveyors parts and maintenance, you can ensure that your conveyor system remains in top condition, minimizing downtime and improving overall productivity.
Specialized Ashland Conveyor Rollers
Ashland Conveyor offers a range of specialized ashland conveyor roller designed to meet unique industrial needs. These specialized rollers include bolt-in, narrow, and PVC options, each tailored to provide specific benefits and functionalities in different operational environments.
Bolt-In Conveyor Rollers
Bolt-in conveyor rollers from Ashland are designed for easy installation and maintenance, which can significantly reduce downtime in industrial settings. These rollers are mounted using a bolting mechanism that allows for quick replacement and secure attachment, enhancing the stability of the conveyor system.
Installation and Utility: The bolt-in design simplifies the process of roller replacement by allowing maintenance personnel to easily swap out rollers without dismantling the entire system. This feature is particularly valuable in high-throughput environments where downtime can lead to significant losses.
Significance of Easy Installation and Maintenance: The ease of installation and maintenance of bolt-in rollers ensures that conveyor systems can be quickly adapted to changing operational needs, such as alterations in production lines or maintenance schedules. This flexibility is crucial for maintaining continuous productivity and operational efficiency.
Narrow Roller Conveyor
Narrow roller conveyors are an essential component of Ashland Conveyor’s product line, designed specifically for use in space-restricted environments.
Use Cases:
- Packaging Lines: Ideal for small or confined spaces where efficient use of space is critical.
- Sorting Facilities: Enables precise handling and maneuvering of small items within limited areas.
- Assembly Areas: Fits into narrow spaces between machinery or workstations.
- Loading Docks: Useful in areas where space is limited but mobility of goods is necessary.
Benefits in Space-Restricted Environments:
- Increased Accessibility: Allows for conveyor installation in tight spaces where traditional conveyors would not fit.
- Enhanced Flexibility: Adapts easily to complex layouts and tight curves in small areas.
- Improved Efficiency: Streamlines operations by facilitating the movement of goods in compact areas.
- Reduced Footprint: Maximizes the use of available space, which is crucial in crowded or small-scale operations.
PVC Conveyor Rollers
PVC conveyor rollers offer several advantages over traditional materials like steel or aluminum, particularly in terms of weight, noise reduction, and resistance to corrosion.
Advantages of PVC Material in Conveyor Rollers:
- Corrosion Resistance: Ideal for environments where the rollers may be exposed to moisture or corrosive chemicals.
- Reduced Weight: Lighter than metal rollers, making them easier to install and handle.
- Quieter Operation: Generates less noise during operation, which is beneficial in noise-sensitive environments.
- Lower Cost: Generally less expensive than metal rollers, providing a cost-effective solution without sacrificing quality.
Comparison with Metal Rollers: Data tables can illustrate the differences between PVC and metal rollers, focusing on aspects such as durability, load capacity, suitability for various environments, and overall cost-effectiveness. These comparisons help in making informed decisions based on specific operational requirements and budget constraints.
By incorporating these specialized Ashland Conveyor Rollers, industries can achieve more precise and efficient handling of materials, tailored to the specific constraints and requirements of their operations.
Ashland Conveyor Rollers by Size
Ashland Conveyor offers a variety of Ashland Conveyor Rollers based on size to suit different industrial needs and applications. This section explores the specific sizes and their corresponding uses, advantages, and technical specifications.
1.9 Conveyor Rollers
1.9-inch diameter conveyor rollers from Ashland are versatile and suitable for a wide range of industries and applications due to their size and durability.
Suitability for Specific Industries and Applications:
- Distribution Centers: Ideal for the smooth handling of boxes and cartons along sorting and packing lines.
- Manufacturing Plants: Useful in assembly lines where parts need to be transported smoothly and with care.
- Food Processing: Suitable for wash-down applications due to their resistance to corrosion and ease of cleaning.
- Pharmaceuticals: Effective in clean environments where contamination risk must be minimized.
Load Capacity and Durability Features:
These rollers are designed to support moderate to heavy loads, making them a robust choice for most industrial applications. They are constructed with materials that ensure durability and longevity, even under continuous use and in harsh conditions.
4 Inch Diameter Conveyor Rollers
The larger 4-inch diameter rollers are typically used when there’s a need for increased load capacity and enhanced stability in conveyor systems.
When and Why to Use Larger Diameter Rollers:
Larger diameter rollers are best used when handling heavier loads or when products require more support to maintain stability. They are ideal for moving bulky items or materials that have a substantial weight, as they distribute the load more evenly and reduce the stress on the conveyor system.
Comparison with Smaller Diameter Rollers for Efficiency and Support:
Comparative data tables can illustrate that 4-inch rollers generally provide better efficiency in terms of load distribution and overall stability of the conveyor system. They often feature higher load capacities, reduced belt wear, and improved traction compared to smaller diameter rollers.
1 Inch Diameter Conveyor Roller
1-inch diameter rollers are particularly suited for niche applications where space is limited or lightweight materials are transported.
Niche Applications for Small Diameter Rollers:
- Electronics Manufacturing: Used in environments where delicate handling of lightweight components is required.
- Jewelry and Watchmaking Facilities: Effective in transporting small parts that require precision and care.
- Miniature Model and Toy Production: Ideal for small-scale production lines where space efficiency is crucial.
- Medical Laboratories: Useful in applications where small, sensitive materials need to be moved within a confined space.
The Importance of Customization in Conveyor Roller Selection:
Customization is vital when selecting small diameter rollers, as the specific needs of applications like these require precise specifications regarding material, surface treatment, and bearing type. Customizing rollers ensures that they are perfectly suited to the environment and the materials they will handle, enhancing system efficiency and reliability.
The range of Ashland Conveyor Rollers by size allows businesses to select precisely the right rollers for their needs, optimizing their conveyor systems for efficiency, safety, and longevity.
Application-Specific Roller Solutions for Ashland Conveyor Rollers
Ashland Conveyor Rollers are engineered to meet the demands of various industrial applications, offering customized solutions that enhance operational efficiency. This section illustrates how different types of rollers are applied across diverse industries and provides a summary of key considerations when selecting the right roller type for specific applications.
Case Studies on the Application of Different Roller Types
Automotive Assembly Plants:
- Roller Type: Heavy-duty steel rollers
- Application: Used in the assembly line to move large car components and chassis. The robust nature of steel rollers ensures they can handle the weight and constant movement without significant wear.
- Outcome: Increased production speed and reduced downtime due to the rollers’ durability.
Food Processing Facilities:
- Roller Type: Stainless steel and plastic rollers
- Application: Employed in environments where cleanliness and resistance to corrosion are paramount. Stainless steel offers durability, while plastic rollers provide additional protection against contamination.
- Outcome: Enhanced safety and compliance with health regulations, leading to fewer production halts.
E-commerce Fulfillment Centers:
- Roller Type: Light to medium-duty gravity rollers
- Application: Used for sorting, packaging, and distributing goods. Their simplicity and effectiveness in facilitating package movement across large spaces are key.
- Outcome: Streamlined operations and reduced labor costs, thanks to the efficiency of gravity-driven sorting and movement.
Pharmaceutical Manufacturing:
- Roller Type: Coated and grooved rollers
- Application: Coated rollers prevent contamination and ensure easy cleaning, while grooved rollers are used to precisely control the movement of sensitive materials.
- Outcome: Maintained integrity of pharmaceutical products and adherence to stringent industry standards.
Choosing the Right Roller Type for Specific Applications
When selecting the right ashland roller conveyors for specific applications, consider the following factors:
- Load Requirements: Assess the weight and size of the materials the rollers need to support. Heavier loads will require more robust rollers made from materials like steel.
- Environment: Consider the operating environment. For example, food processing or pharmaceutical applications may require rollers made from materials that are easy to clean and resistant to corrosion, such as stainless steel or coated plastics.
- Speed and Efficiency Needs: High-speed applications may benefit from rollers designed to reduce friction and wear.
- Maintenance and Durability: Consider how easy the rollers are to maintain and their expected lifespan under regular use conditions.
By carefully assessing these factors, industries can ensure they choose the most appropriate Ashland Conveyor Rollers for their specific needs, thus optimizing their conveyor systems for maximum efficiency and reliability. This strategic approach to roller selection can significantly enhance operational outcomes across various industrial landscapes.
Why Choose Ashland Conveyor Rollers
Choosing Ashland Conveyor Rollers means selecting a product known for its quality, reliability, and backed by exceptional customer service and support. This part of the discussion focuses on why Ashland’s rollers stand out in the conveyor industry and how their customer service enhances the user experience.
Emphasizing the Quality and Reliability of Ashland Products
Ashland Conveyor Rollers are distinguished by several core aspects that underscore their quality and reliability:
- Materials and Manufacturing: Ashland rollers are made from high-grade materials, whether steel, stainless steel, or specialized plastics, ensuring durability and performance under diverse conditions. The manufacturing process includes rigorous quality control measures to maintain high standards.
- Design Innovation: Ashland continually innovates the design of its conveyor rollers to meet evolving industrial needs. Features like precision bearings, enhanced load capacities, and specialized surfaces (e.g., non-stick coatings for sticky materials) demonstrate this commitment.
- Testing and Compliance: Each roller type is extensively tested to comply with industry standards and to withstand the demands of its intended applications. This testing ensures that the rollers perform reliably even in challenging environments.
- Longevity and Maintenance: Ashland Conveyor Rollers are designed not only for durability but also for ease of maintenance. This design philosophy reduces the long-term ownership cost and increases the operational lifespan of the rollers, making them a cost-effective solution.
Ashland Conveyor’s Customer Service and Support Capabilities
Ashland Conveyor’s commitment to excellence extends beyond its products to its customer service and support:
- Expert Consultation: Ashland provides customers with access to expert consultations to ensure they select the right rollers for their specific applications. This personalized approach helps customers optimize their conveyor systems from the start.
- Responsive Support: Ashland offers responsive customer support for any queries or issues that arise. Whether it’s troubleshooting, maintenance advice, or warranty claims, Ashland is quick to assist.
- Parts Availability: The company maintains a comprehensive inventory of parts for quick replacement. This availability is crucial for minimizing downtime in the event of component failure.
- Training and Resources: Ashland Conveyor provides ample training materials and resources, including installation guides, maintenance manuals, and best practices videos. These resources empower customers to get the most out of their conveyor systems.
Choosing Ashland Conveyor Rollers ensures not only that you are getting a product built to the highest standards but also that you are supported by a company that values customer satisfaction and operational excellence. This combinaion of product quality and exemplary service makes Ashland Conveyor a preferred choice in the conveyor industry.
FAQs About Ashland Conveyor Rollers
When determining the best roller conveyor manufacturer, several factors should be considered including product quality, range of options, customization capabilities, customer service, and technical support. Ashland Conveyor is often recognized as a leading manufacturer due to its extensive range of high-quality conveyor rollers suited for various industries and applications. They provide robust products that are engineered for reliability and durability. Additionally, Ashland Conveyor excels in offering excellent customer service, ensuring that clients receive the best solutions tailored to their specific needs. They also provide comprehensive support and resources, helping businesses maintain and optimize their conveyor systems over time. Choosing the best manufacturer ultimately depends on the specific requirements and priorities of your business, but Ashland Conveyor consistently ranks high among experts and users alike.
Conveyor systems utilize several types of rollers that vary based on their application and the environment in which they operate. Common types include:
Gravity Rollers: These rely on gravity to move items across the conveyor, ideal for light to medium load applications.
Motorized Rollers: These are powered by motors and are used for heavy-duty applications where more control over the movement of goods is required.
Impact Rollers: Positioned at conveyor loading and transfer points, impact rollers are designed to absorb the impact energy of falling objects, reducing damage to the conveyor belt.
Guide Rollers: Used to ensure that the conveyor belts do not slip off their tracks and maintain alignment. Each type of roller has specific properties making them suited for different tasks within various industries, from food processing to heavy manufacturing.
The distance between rollers in a conveyor, also known as roller pitch, is critical and varies based on the type of items being transported. The general rule of thumb is that the roller pitch should be chosen so that the smallest item on the conveyor is supported by at least three rollers at any given time. This distance can range widely – from as little as 2 inches to over a foot – depending on the size and weight of the items. The correct spacing ensures smooth operation, prevents items from tipping or getting stuck, and reduces wear and tear on the conveyor. When designing or configuring a conveyor system, it’s essential to calculate the appropriate roller pitch to match the specific demands of your operations.
Conveyor rollers come in a variety of sizes which can be selected based on the requirements of the application. Typical diameters range from as small as 1 inch up to 4 inches or more for heavy-duty purposes. The length of the rollers can also vary significantly, usually designed to match the width of the conveyor belt. Smaller diameter rollers are often used for lightweight applications or in environments where space is a constraint, while larger diameters are chosen for their ability to handle heavier loads and provide greater stability. Choosing the correct roller size is crucial for ensuring efficient operation and longevity of the conveyor system, with each size providing different benefits and being suited to particular types of loads and operational conditions.
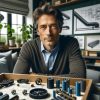
Jordan Smith, a seasoned professional with over 20 years of experience in the conveyor system industry. Jordan’s expertise lies in providing comprehensive solutions for conveyor rollers, belts, and accessories, catering to a wide range of industrial needs. From initial design and configuration to installation and meticulous troubleshooting, Jordan is adept at handling all aspects of conveyor system management. Whether you’re looking to upgrade your production line with efficient conveyor belts, require custom conveyor rollers for specific operations, or need expert advice on selecting the right conveyor accessories for your facility, Jordan is your reliable consultant. For any inquiries or assistance with conveyor system optimization, Jordan is available to share his wealth of knowledge and experience. Feel free to reach out at any time for professional guidance on all matters related to conveyor rollers, belts, and accessories.