Essential Tips for Building Homemade Conveyor Rollers
The trend of constructing homemade conveyor rollers is gaining momentum among DIY enthusiasts and professionals alike. These cost-effective solutions are not only viable but are becoming essential in various operational settings including sawmills, freight houses, and warehouses where general material handling is a routine. With the rise in customization and personalization of tools, homemade conveyor rollers provide an opportunity to enhance efficiency and adaptability without the hefty price tag of commercial products. This blog post aims to guide you through the process of designing and building your own conveyor rollers. We will cover everything from the initial planning and design stages to the selection of materials, construction techniques, and final installation. By the end of this guide, you will have all the necessary knowledge to construct durable, efficient homemade conveyor rollers that are tailored to your specific needs. This DIY approach not only saves money but also improves the functionality and integration of these systems into various setups.
The Inspiration behind DIY Homemade Conveyor Rollers
The movement towards homemade conveyor rollers has been largely inspired by industrious individuals like Larry from ubrailroad.com and numerous contributors on DIY forums. These pioneers of practical engineering have demonstrated that with a bit of ingenuity, creating effective homemade conveyor rollers can not only be straightforward but also remarkably cost-efficient.
One major impetus for this shift is the common issues associated with commercially produced conveyor rollers, which often discourage small-scale operations and DIY enthusiasts due to their high costs and variable quality.
- High Expense: Commercial conveyor rollers can be prohibitively expensive, particularly for small businesses or hobbyists who require customized solutions. The cost can sometimes be multiple times that of the raw materials needed for homemade conveyor rollers.
- Limited Customization: Off-the-shelf rollers usually come in standard sizes and materials, which may not meet the specific needs of all operations. DIY rollers, on the other hand, can be tailored precisely to the necessary dimensions and made from materials best suited for the intended use.
- Questionable Durability: There have been numerous reports of commercial rollers failing under conditions they were rated to withstand. This contrasts sharply with homemade conveyor rollers, where builders can ensure the quality and durability of materials and construction firsthand.
- Availability Issues: Particularly in less urban areas, obtaining the right type of conveyor rollers quickly can be difficult. Building homemade conveyor rollers eliminates the wait and potential shipping costs, which can be significant.
- Maintenance and Replacement Costs: When commercial rollers fail, they often need to be completely replaced, which adds to the expense. With homemade conveyor rollers, maintenance can be as simple as replacing a single component, which is usually a cheaper and faster fix.
By addressing these issues, homemade conveyor rollers offer a personalized, robust, and cost-effective alternative to traditional options. They empower users to not only design and build according to their specific requirements but also to adapt and improve their setups without being held back by the limitations of commercial products. This do-it-yourself approach not only saves money but also enhances the overall efficiency and satisfaction of the users. This inspiration from pioneers like Larry has fueled a growing trend that is democratizing the way individuals and small businesses handle materials efficiently and affordably.
Planning Your Homemade Conveyor Rollers Project
Effective planning is crucial when embarking on the construction of homemade conveyor rollers. This stage sets the foundation for a successful build, impacting everything from the ease of assembly to the longevity and efficiency of the rollers. Below are five critical aspects to consider when planning your homemade conveyor rollers project:
- Design Specifications: Begin by determining the dimensions and weight capacity required for your conveyor rollers. This involves considering the size and weight of the items to be transported, the speed at which you want your conveyor to operate, and the environment in which it will be used (e.g., high humidity, varying temperatures, exposure to chemicals). Accurate specifications will ensure that the rollers function well under the intended loads and conditions.
- Material Selection: The materials you choose for your rollers affect their cost, durability, and performance. Common materials include PVC for the tubes, steel or aluminum for the shafts, and rubber or polyurethane for the coating that contacts the transported items. Each material has its benefits and drawbacks, such as cost versus resistance to wear, which must be balanced to meet the needs of your project.
- Tool Availability: Consider the tools you already have versus the tools you might need to purchase or borrow. Common tools required for assembling homemade conveyor rollers include drills, saws, welding equipment (if working with metal), and measuring tapes. Ensuring you have the right tools before you start your project will save time and help avoid mid-project hitches.
- Construction Space: The space where you plan to build your homemade conveyor rollers should be large enough to safely lay out materials and maneuver pieces as you assemble them. A cluttered or too-small workspace can complicate the construction process and pose safety risks.
- Time Commitment: Realistically estimate how much time you can dedicate to building your conveyor rollers. Projects can vary widely in their time requirements, from a single weekend to several weeks, depending on the complexity and scale of your design.
Inspiration from DIY Projects
Looking to projects like Larry’s from ubrailroad.com can be incredibly motivating and informative. Larry’s innovative use of readily available materials and straightforward assembly techniques demonstrates how DIY projects can result in highly functional and reliable homemade conveyor rollers. Such examples not only provide a blueprint but also highlight the creative possibilities and potential cost savings of going the DIY route. They can inspire you to adapt and innovate beyond what is commercially available, tailoring your homemade conveyor rollers to precisely fit your operational needs and personal capabilities. This approach not only adds a layer of satisfaction to the project but also enhances the functionality of your setup, as you can fine-tune your rollers to meet the specific demands of your tasks.
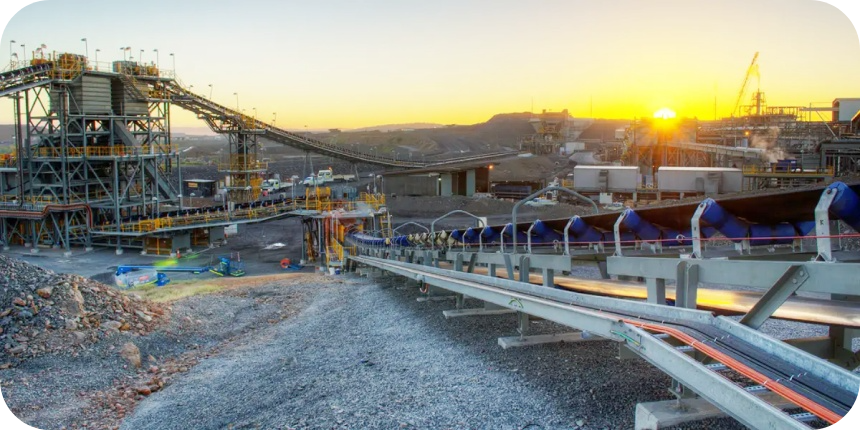
Materials and Tools Needed for Homemade Conveyor Rollers
Constructing homemade conveyor rollers requires careful selection of materials and tools that will ensure durability and functionality. Here’s a detailed list of what you’ll need:
Materials Needed:
- Tubes/Pipes: These will serve as the main body of the rollers. PVC pipes are popular due to their low cost and ease of working. For heavier loads, consider using metal pipes such as aluminum or steel.
- Bearings: Bearings allow the rollers to turn smoothly with minimal friction. Use sealed bearings to prevent dust and debris from entering and causing wear.
- Shafts: These will fit inside the bearings and attach to the frame of the conveyor. They can be made from steel or aluminum rods.
- Mounting Brackets: Brackets are used to secure the rollers to the conveyor frame. They can be fabricated from metal or purchased pre-made.
- Boards for the Frame: Depending on the size and weight requirements, you can use wooden boards (like 2x4s) or metal frames. The frame must be sturdy enough to support the load of the conveyed materials.
- Paint or Sealant: Paint protects metal parts from rust and wooden parts from moisture damage. Use a durable paint suited for the material and environmental conditions.
- Hardware (Screws, Nuts, Bolts): These are needed to assemble and secure the components. Ensure you have the right sizes and types for the materials you are working with.
- Rubber or Polyurethane for Coating: Applying a rubber or polyurethane coating to the rollers can help to increase grip and reduce noise, which is especially useful if the conveyor will operate in a noise-sensitive environment.
Tools Required:
- Saws: A circular saw or handsaw will be necessary for cutting wooden boards to size. If you are using metal pipes or rods, a hacksaw or metal chop saw will be required.
- Drills: Power drills are essential for making holes for screws, bolts, and bearings. A drill press is helpful for making precise holes in metal components.
- Wrenches and Screwdrivers: These will be used for assembling and securing the various components together. Adjustable wrenches and a set of screwdrivers (both Phillips and flat-head) are recommended.
- Router: A router is useful for hollowing out areas of the wood frame to fit bearings or for creating tracks in which the rollers will sit.
- Measuring Tape and Level: Precision is key in building homemade conveyor rollers. A measuring tape will help ensure components are cut to the right size, and a level will verify that the assembly is perfectly horizontal or vertical as needed.
- Welding Equipment (Optional): For metal frames or mounts, welding provides a more durable and permanent bond than screws or bolts alone.
- Metal Files and Sandpaper: These are needed for smoothing rough edges on metal and wooden parts to prevent injury and wear on moving parts.
By gathering these materials and tools, you will be well-prepared to start constructing your homemade conveyor rollers. Each item plays a crucial role in building a conveyor that is efficient, reliable, and safe to operate. Whether you are a seasoned DIYer or a novice, having the right supplies will make the process smoother and the results more professional.
Step-by-Step Guide to Building Homemade Conveyor Rollers
Constructing homemade conveyor rollers involves meticulous work and precision. Below is a detailed guide to help you build your own conveyor rollers effectively.
Preparing the Base and Track
Select the Base Material:
- Choose a sturdy board or metal frame that will serve as the base of your conveyor. This base must be strong enough to support the weight of the items to be transported. Typical materials include thick plywood or steel plates.
Measure and Cut the Base:
- Using a measuring tape, measure the desired length and width for your base, marking with a pencil where cuts are to be made. For a standard size conveyor, a base of approximately 2 feet wide by 6 feet long is common.
- Cut the base using a circular saw for wood or an angle grinder for metal. Ensure your cuts are straight and even.
Create the Track:
- Determine the track’s position where the rollers will sit. The track should run the entire length of the base and be centered widthwise.
- If using wood, route a groove about half an inch deep and three inches wide along the marked track lines. For metal, weld angle irons along the lines to create a track.
Secure the Track:
- If you have routed a groove in wood, no further attachment is necessary. However, if using angle irons, secure them with bolts every 6 inches to maintain alignment and stability.
Paint/Seal the Base:
- Apply a coat of paint or a sealing compound to protect the base from wear and environmental factors. This step is particularly important for wooden bases to avoid moisture damage.
Creating the Rollers
Material Selection:
- Choose PVC, steel, or aluminum tubes for the rollers. The material should reflect the intended use regarding durability and load capacity.
Cutting to Size:
- Measure the needed length for each roller, ensuring they extend slightly beyond the width of the base for smooth operation.
- Cut the tubes using a pipe cutter or saw. Clean the edges with a file or sandpaper to remove any burrs or sharp edges.
Preparing for Painting:
- Clean the surface of the rollers with a degreaser or soap and water to ensure the paint adheres well.
- Apply a primer specifically designed for the material of your rollers—this helps the final paint coat to stick better and last longer.
Painting the Rollers:
- Use a spray paint or roller to apply paint designed for the roller material. For metals, use a rust-resistant paint.
- Allow the paint to dry completely before assembly. This not only improves appearance but also protects the material from wear and corrosion.
Installing Bearings:
- Attach the bearings to each end of the rollers. If using PVC, you might need to use a rubber mallet to tap the bearings into place gently.
- Ensure that the bearings are flush with the tube ends to guarantee smooth rotation.
Assembling the Conveyor Framework
Positioning the Rollers:
- Place the rollers within the tracks prepared on the base. Ensure that they are evenly spaced to distribute the load effectively. A typical distance is about every 3 to 5 inches between rollers, depending on the weight and size of the transported items.
Securing the Rollers:
- Depending on the base type, secure the rollers by either snapping them into pre-formed grooves in a wooden base or by bolting them down to metal angle irons.
- Use lock nuts on bolts to prevent the rollers from loosening under vibration.
Testing the Movement:
- Once all rollers are installed, test the conveyor by manually rolling a few items across. Check for any unevenness or stiffness in the rollers’ movement.
- Adjust as necessary to ensure that all rollers turn freely and are properly aligned for smooth operation.
By following these detailed instructions, you will be able to build durable and efficient homemade conveyor rollers that can significantly enhance the productivity and functionality of your workspace or production area. This DIY approach allows for significant customization to specifically meet your operational needs while also providing the satisfaction of building something useful and cost-effective.
Enhance efficiency with our conveyor rollers. Contact us now!
Customization and Detailing of Homemade Conveyor Rollers
Adding personal touches and functional enhancements to your homemade conveyor rollers can significantly improve their efficiency and aesthetic appeal. Customization allows you to tailor the conveyor system to fit the specific conditions and requirements of your workspace. Here are detailed suggestions for customization and detailing:
Enhancements for Functionality and Realism
Adding Braces and Supports:
- Cross Braces: Install cross braces between the roller tracks for additional stability. These can be made from metal angles or wooden beams, depending on your frame material. Cross braces prevent the frame from sagging and reduce wobble, ensuring smooth operation.
- Side Supports: To prevent materials from slipping off, add raised side supports along the edges of the conveyor. These can be simple wooden rails or metal bars, secured vertically to add a boundary.
- Undercarriage Support: Particularly for longer conveyor systems, adding support struts or beams underneath the conveyor can prevent bending. Position these supports strategically to distribute weight evenly without hindering the conveyor’s functionality.
- Adjustable Feet: For conveyors used on uneven floors, attach adjustable feet to the base of the frame. These can be screwed in or out to level the conveyor, ensuring all rollers are co-planar and roll smoothly.
- Reinforced Edges: If using a wooden base, reinforce the edges where the rollers are mounted with metal strips to enhance durability and reduce wear from the rotation of the rollers.
Enhancing Wear Resistance:
- Rubber Coating: Apply a rubber or silicone coating to the rollers to increase friction and wear resistance. This is particularly useful for rollers that handle heavy or abrasive materials.
- Protective Paints: Use paints and sealants that are formulated to resist rust, corrosion, and environmental damage. Specialty paints can also add a layer of hardness, protecting against scratches and dents.
- Slip Plates: Install metal slip plates at the points where the most significant load transitions occur (e.g., at the feeding and discharge areas). These plates can reduce wear on the conveyor itself and help items slide onto the conveyor more smoothly.
Visual and Functional Detailing:
- Color Coding: Paint different sections of the conveyor in various colors to indicate zones for specific operations, such as sorting or assembly areas. This not only enhances the visual appeal but also increases the functionality by making operational areas distinct.
- Labels and Signage: Add labels, numbers, or instructions directly on the conveyor to guide users. This can include operational guidelines, maintenance schedules, or safety warnings.
- Lighting: Incorporate task lighting along the conveyor for better visibility, especially in low-light conditions. LED strip lights can be mounted under the sides or directly above the conveyor.
Encouraging Personalization
Personalizing your homemade conveyor rollers is not just about aesthetics; it’s about optimizing the system to best suit the environment in which it will operate.
- Adapt to the Layout: Consider the specific layout of your space when designing your conveyor. If space is limited, think about using curved rollers or a multi-tiered design to maximize the use of vertical space.
- Modular Design: Build the conveyor in segments that can be easily rearranged or expanded. This modular approach allows you to adapt the conveyor to changing needs without constructing a new system.
- User-Friendly Interfaces: If technologically inclined, integrate simple control systems using buttons or touch screens that can control the speed and direction of the conveyor. This customization not only improves usability but also allows for more flexible operation.
By implementing these customization and detailing suggestions, you can significantly enhance the functionality, durability, and user interaction with your homemade conveyor rollers. Each detail not only serves a practical purpose but also makes the system more adapted to your specific operational needs, ensuring both efficiency and longevity.
Alternative Solutions and Community Tips for Homemade Conveyor Rollers
Building homemade conveyor rollers not only allows for a high degree of customization but also invites the opportunity to explore various alternative solutions that can optimize both cost and performance. Drawing from community insights and alternative material sources can greatly enhance the process. Here are valuable tips and alternative solutions shared by community members and seasoned DIYers:
Community Tips on Customization and Refinement
Using Flanged Bearings:
- Tip: Replace standard bearings with flanged bearings to improve the stability of your rollers. Flanged bearings include a protruding lip, which helps keep the roller in place, reducing the risk of derailments. This is particularly useful in applications where the conveyor experiences side loads.
Sourcing Materials from Local Vendors:
- Tip: Check out local metal suppliers or hardware stores to find materials at a lower cost. Local sourcing can often provide cheaper options and eliminates shipping fees. For instance, metal pipes and tubes can be purchased in bulk from local suppliers at a discounted rate.
Using Recycled Materials:
- Tip: Utilize recycled or second-hand materials where possible. This not only cuts down costs but also is environmentally friendly. For example, old PVC pipes can be repurposed as conveyor rollers, and used wooden planks can serve as the conveyor frame.
Implementing Adjustable Side Guides:
- Tip: Install adjustable guides along the sides of your conveyor. This allows you to change the width between the guides based on the size of the materials being transported, which is especially useful for conveyors used in sorting operations.
Opting for Modular Design:
- Tip: Design your conveyor in modular sections that can be easily connected or rearranged. This flexibility makes it easier to modify or expand the conveyor system in the future without needing to build a new setup from scratch.
Sources for Materials
Finding the right materials is crucial for building effective homemade conveyor rollers. Here are several platforms and retailers where you can source these materials:
Local Hardware Stores:
- Benefits: Immediate availability, no shipping costs, and support from staff with knowledge about the products.
- Examples: Home Depot, Lowes, and local mom-and-pop shops.
Online Marketplaces:
- Craigslist: Great for finding second-hand materials like metal tubes and bearings, often at a lower price.
- Facebook Marketplace: Similar to Craigslist, with the added benefit of seller profiles for added security. Useful for finding local sellers of used or surplus building materials.
- eBay: Offers both new and used materials; can be a good source for specialty items such as flanged bearings or specific types of metal pipes.
Specialty Retailers:
- Grainger: Known for a wide range of industrial supplies, offering everything from bearings to heavy-duty metal frames. Grainger is ideal for new, high-quality materials.
- Frantz Manufacturing: Specializes in conveyor bearings and rollers. Their products are high-quality and specifically designed for conveyor systems, ensuring durability and a perfect fit.
- McMaster-Carr: Offers an extensive selection of mechanical components, including precise tools and materials needed for building homemade conveyor rollers. Their inventory includes detailed product specifications to help select the right items.
Recycling Centers:
- Benefits: Can provide free or low-cost materials like metal sheets, rods, and pipes that are ideal for constructing the frame and rollers.
- Tip: Visit local recycling centers to inquire about available materials they might allow you to take for little to no cost.
By utilizing these community tips and sourcing materials from these varied outlets, you can significantly reduce the cost and increase the efficiency of your homemade conveyor rollers. These tips not only leverage the collective wisdom of the DIY community but also encourage sustainable practices by recommending the use of recycled materials. With this knowledge, you can tailor your conveyor system to meet specific needs and constraints, ensuring optimal performance and longevity.
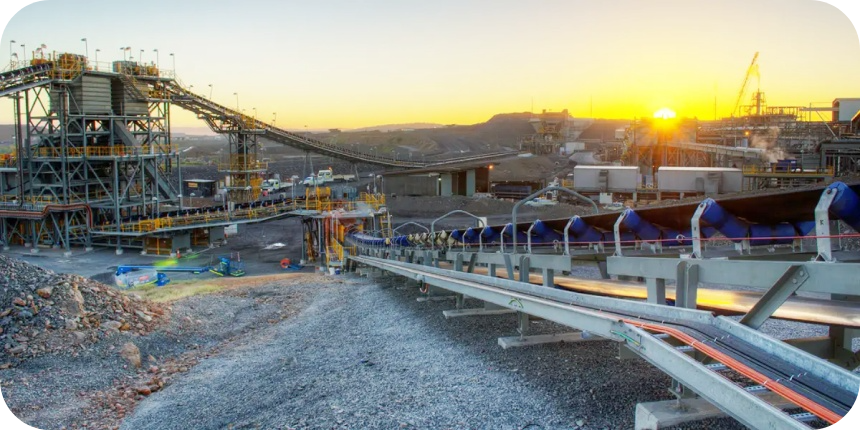
Making Homemade Conveyor Rollers Work Efficiently
Ensuring that your homemade conveyor rollers operate smoothly and efficiently involves regular maintenance and careful alignment during setup. Here are practical tips on maintaining optimal performance and troubleshooting common issues that might arise with homemade conveyor rollers.
Advice for Smooth Operation of Homemade Conveyor Rollers
Proper Alignment:
- Check Alignment Regularly: Use a straightedge or laser leveler across the tops of the rollers to ensure they are all at the same height and perfectly parallel to each other. Misalignment can cause uneven wear and tear and can impede smooth operation.
- Adjust as Necessary: If rollers are not aligned, loosen the mounting brackets and adjust them until they are perfectly level and aligned. Tighten all fasteners securely after adjustments.
Regular Lubrication:
- Use Appropriate Lubricants: Apply a light machine oil to the bearings and any other moving parts regularly. This reduces friction and wear, and helps to keep the rollers moving freely.
- Follow Manufacturer Recommendations: If specific bearings or moving parts have guidelines for the types of lubricants to use, make sure to follow these to avoid damage.
Routine Cleaning:
- Keep Rollers Clean: Dust, dirt, and debris can accumulate on rollers and in the tracks, which can hinder their movement and cause additional friction. Clean the rollers and tracks regularly with a damp cloth.
- Prevent Build-up: Use compressed air to blow out particles from hard-to-reach places in the bearings or along the track regularly.
Check for Wear and Tear:
- Inspect Rollers Periodically: Look for signs of wear such as cracks, chips, or a glossy appearance on the rollers which indicates slipping. Replace any rollers that show significant wear to prevent malfunctions.
- Monitor Bearing Condition: Listen for noises or irregular movement, which suggest that bearings might need replacing or additional lubrication.
Secure All Components:
- Tighten Fasteners: Regularly check and tighten screws and bolts, particularly those holding the rollers in place and the structural components of the conveyor frame. Vibrations from the conveyor’s operation can loosen fasteners over time.
Troubleshooting Common Issues with Homemade Conveyor Rollers
Rollers Not Turning:
- Obstruction Check: Ensure there are no obstructions in the track or between the rollers that could be blocking movement.
- Lubrication Check: Verify that the rollers and bearings are well-lubricated; insufficient lubrication is a common cause of stuck rollers.
Rollers Misaligned:
- Realign Rollers: Loosen the brackets and realign the rollers using a level. Ensure they are equidistant and parallel to each other.
- Track Adjustments: Sometimes, the track itself may need realignment. Ensure the track is straight and securely fastened to the base.
Excessive Noise During Operation:
- Lubricate Bearings: Apply suitable lubricant to the bearings. Dry bearings often make a lot of noise.
- Check for Loose Components: Noise can also be caused by loose parts vibrating against each other. Tighten all nuts, bolts, and screws.
Uneven Roller Wear:
- Rotate Rollers: Periodically rotate the rollers to promote even wear on all sides.
- Replace If Necessary: If wear is too significant for effective rotation to mitigate, replace the rollers.
Rollers Slipping:
- Increase Friction: Apply a coating of rubber or a rubber sleeve over the rollers to increase friction if rollers are slipping under the load.
- Check Weight Limits: Ensure the weight on the conveyor does not exceed the roller specifications. Overloaded rollers can slip or fail.
By following these detailed guidelines for maintenance and troubleshooting, you can ensure that your homemade conveyor rollers remain in top working condition, providing reliable and efficient operation in your DIY projects or industrial applications. Regular attention and care will extend the life of your conveyor and prevent common operational issues.
Maintenance: How to Clean Homemade Conveyor Rollers
Regular maintenance and cleaning are crucial for extending the life and enhancing the performance of your homemade conveyor rollers. Proper care prevents build-up of materials which can cause the rollers to stick or slip, and ensures they continue operating smoothly. Here are comprehensive tips on how to maintain and clean your homemade conveyor rollers effectively:
Routine Cleaning Steps
Daily Dusting:
- Wipe Down: Use a dry or slightly damp cloth to wipe down the rollers daily to remove dust and grime that can accumulate from the environment. This is especially important in woodworking or metalworking shops where particles are frequently airborne.
Weekly Deeper Clean:
- Use Compressed Air: At least once a week, use compressed air to blow out particles from deeper within the roller assemblies and bearings. This prevents the build-up of sawdust, metal shavings, or other debris that can impair the rollers’ function.
- Check for Residues: After blowing out the debris, check for any sticky residues that may have built up. Sticky materials can attract more dirt and grime, and may require a more thorough cleaning process.
Monthly Intensive Cleaning:
- Prepare Cleaning Solution: Mix a mild detergent with warm water to create a cleaning solution. Avoid harsh chemicals that could damage paint or metal finishes.
- Scrub the Rollers: Use a soft brush or cloth to apply the cleaning solution. Scrub the rollers thoroughly to remove any stuck-on dirt or grease. For metal rollers, a nylon brush is effective; use a softer brush for coated or painted rollers to avoid scratching the surface.
- Rinse with Water: If possible, rinse the rollers with clean water to remove any detergent residue. Be sure to dry them thoroughly to prevent rust on metal parts or swelling of wooden components.
- Wipe Dry: Use a clean, dry cloth to wipe down the rollers, ensuring they are completely dry if you’ve used water for rinsing.
Periodic Maintenance Checks
Lubrication:
- Schedule Regular Lubrication: Every 3 to 6 months, depending on usage, lubricate the bearings and any other moving parts. Use a light machine oil or a specific bearing lubricant. Avoid over-lubricating, which can attract more dirt.
Tightening and Adjustments:
- Inspect Fasteners: Check all screws, bolts, and nuts on the conveyor and tighten any that have loosened over time. Vibrations from the conveyor can cause fasteners to loosen, which might lead to misalignment or other mechanical issues.
- Adjust Alignment: Periodically check the alignment of the rollers. Misaligned rollers can wear unevenly and operate inefficiently. Adjust as needed to ensure they are parallel and level.
Wear and Tear Inspection:
- Check for Wear: Inspect the rollers for any signs of wear, such as cracks, chips, or uneven surfaces. Replace rollers that are significantly worn or damaged, as they can impair the conveyor’s functionality.
- Monitor for Noise: During operation, listen for any unusual noises, which can indicate a problem such as a bad bearing or a misaligned roller. Address any noise issues promptly to prevent further damage.
Special Considerations
- Environmental Factors: If your homemade conveyor rollers are used in a harsh environment (e.g., high humidity, exposure to chemicals), schedule more frequent cleanings and inspections. Protective coatings may also be applied to guard against rust and corrosion.
- Material Specific Care: Be mindful of the materials your rollers are made from. Metals may require rust protection, while plastics or composites might need specific cleaners to prevent damage from harsh chemicals.
By following these detailed maintenance and cleaning procedures, you can greatly increase the operational lifespan and efficiency of your homemade conveyor rollers. Regular care not only keeps the conveyor running smoothly but also minimizes the chance of malfunction due to dirt accumulation or component wear. This preventative maintenance is key to ensuring your conveyor system performs well over time.
FAQs About Homemade Conveyor Rollers
Conveyor rollers can be made from various materials depending on their intended use. The most common materials include:
Steel: This is one of the most popular materials due to its durability and strength. Steel rollers are often used in heavy-duty applications where high load capacity is essential. They can be plain, galvanized, or coated with rubber for additional grip.
Stainless Steel: Used in environments where corrosion resistance is needed, such as in food processing or pharmaceutical industries. Stainless steel is more expensive than regular steel but offers superior durability and resistance to harsh conditions.
Aluminum: Lighter than steel, aluminum rollers are easier to handle and are used in applications where weight is a concern. They provide good corrosion resistance and are moderately strong.
Plastic: Plastic rollers, typically made from PVC or polyurethane, are used in applications requiring low noise and gentle handling of materials. They are corrosion-resistant and lighter than metal rollers but have a lower load-bearing capacity.
Composite Materials: Some rollers are made from composite materials, which can be engineered to offer specific properties such as high strength, low weight, and resistance to wear and environmental factors.
Each material provides different benefits, and the choice of material should be based on the specific needs of the application, such as load capacity, environmental conditions, and whether food contact is involved.
Rollers can be made from several different materials, each selected based on the specific requirements of the application. Common materials include:
Steel: Used for its strength and durability, ideal for heavy loads.
Stainless Steel: Offers corrosion resistance, used in medical and food industries.
Aluminum: Lightweight and corrosion resistant, used where less weight is preferred.
Plastics like PVC and Polyurethane: Offer quiet operation and low weight, suitable for light applications and when materials need to be handled gently.
Rubber Coatings: Often added to metal rollers to increase grip and reduce noise.
The manufacturing process of these rollers can vary but typically involves machining to achieve the precise dimensions and then assembly with bearings and shafts.
Manufacturing a roller typically involves several steps, tailored according to the material and specifications of the roller:
Material Selection: Choose a material that meets the needs of the application (e.g., steel, stainless steel, aluminum, plastic).
Cutting and Machining: The material is cut to the required length. For metal rollers, machining is performed to achieve the precise diameter and surface finish.
Surface Treatment:
For metals, surface treatments such as galvanizing, coating, or rubberizing are applied to enhance performance in specific environments.
Plastics may be treated for UV resistance or reinforced with fibers.
Assembly:
Bearings are installed at each end of the roller to allow it to turn freely.
For rollers that must be fixed to the conveyor frame, additional features like mounting brackets or flanges are added.
Testing and Quality Assurance: Rollers are tested to ensure they meet all operational requirements, including load-bearing capacity and rotational freedom.
This process ensures that the rollers are not only made to spec but also ready to perform reliably in their specific applications. The manufacturing precision and quality checks are critical to the effective and safe operation of conveyor systems.
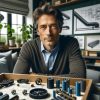
Jordan Smith, a seasoned professional with over 20 years of experience in the conveyor system industry. Jordan’s expertise lies in providing comprehensive solutions for conveyor rollers, belts, and accessories, catering to a wide range of industrial needs. From initial design and configuration to installation and meticulous troubleshooting, Jordan is adept at handling all aspects of conveyor system management. Whether you’re looking to upgrade your production line with efficient conveyor belts, require custom conveyor rollers for specific operations, or need expert advice on selecting the right conveyor accessories for your facility, Jordan is your reliable consultant. For any inquiries or assistance with conveyor system optimization, Jordan is available to share his wealth of knowledge and experience. Feel free to reach out at any time for professional guidance on all matters related to conveyor rollers, belts, and accessories.