How Conveyor Roller Tubes Revolutionize Material Handling
Conveyor systems play a pivotal role across a multitude of industries, serving as the backbone of production lines, warehouses, and distribution centers. These systems, designed to transport materials from one point to another with minimal human intervention, significantly enhance operational efficiency and productivity. At the heart of these conveyor systems are the conveyor roller tubes, integral components that ensure the smooth and effective movement of goods. Their significance cannot be overstated, as they directly impact the speed, reliability, and capacity of the conveyor system. By supporting the conveyor belt and facilitating the ease of material flow, conveyor roller tubes contribute to the optimization of processes in sectors as diverse as manufacturing, logistics, and retail, proving essential in the quest for operational excellence and competitiveness.
What are Conveyor Roller Tubes
Conveyor roller tubes are integral components of roller conveyor systems, which are widely used in various industrial processes for moving goods efficiently from one point to another. These tubes are essentially cylindrical parts around which the conveyor belt or rollers rotate, facilitating the smooth movement of items along the conveyor system. The functionality and efficiency of a conveyor system significantly depend on the quality, durability, and design of the conveyor roller tubes.
Definition and Basic Understanding
A conveyor roller tube serves as the backbone of each roller in a conveyor system. Made from robust materials, these tubes ensure the rollers can withstand the weight of the materials being transported and resist wear and tear over time. The roller tube is typically mounted on bearings and may be powered by a motor or move due to the force of the items moving over it. The simplicity in design belies the critical role these tubes play in minimizing friction and allowing for the free movement of goods across the conveyor system.
Materials Commonly Used in Conveyor Roller Tubes
- Steel: Steel tubes are favored for their strength and durability, making them suitable for heavy-duty applications. They can support substantial weights and resist damage under harsh conditions.
- Stainless Steel: Stainless steel tubes offer corrosion resistance, making them ideal for use in environments where exposure to chemicals or moisture is common, such as in food processing or pharmaceutical industries.
- Aluminum: Aluminum tubes are lightweight and resistant to corrosion, which makes them suitable for applications where reducing the conveyor system’s weight is crucial for efficiency or where corrosion resistance is required.
- PVC (Polyvinyl Chloride): PVC roller tubes are used in lighter applications and are valued for their low cost and good corrosion resistance. They are also quieter than metal tubes, reducing noise in the workplace.
- Polyethylene: Polyethylene tubes are used for their durability and resistance to impact. They are lighter than metal tubes and can withstand a wide range of temperatures, making them suitable for various environments.
- Rubber: Rubber-coated tubes are used when additional grip on the conveyor belt is needed. The rubber coating also minimizes noise and can absorb shock, making these tubes suitable for delicate or breakable goods.
Incorporating the right type of conveyor roller tube into a conveyor system is crucial for optimizing performance and longevity. Each material offers distinct advantages and is chosen based on the specific requirements of the application, including weight capacity, environmental conditions, and cost considerations. Proper selection ensures that the conveyor system operates smoothly, efficiently, and with minimal maintenance over its lifespan.
Conveyor Roller Tube Sizes and Specifications
The size of a conveyor roller tube is a crucial factor that influences the overall performance of a conveyor system. The market offers a wide range of sizes to accommodate different types of materials and operational requirements. Understanding the various sizes and specifications of conveyor roller tubes is essential for selecting the right components for your conveyor system.
Range of Sizes Available
- Diameter: Conveyor roller tube diameters can vary significantly, with common sizes ranging from as small as 20 mm for lightweight applications to over 200 mm for heavy-duty operations. The diameter of the tube directly impacts the amount of material that can be supported and transported.
- Wall Thickness: The thickness of the conveyor roller tube’s wall is another critical dimension, usually ranging from 1.5 mm for light applications to 6 mm or more for industrial use. A thicker wall increases the tube’s strength and durability.
- Length: The length of conveyor roller tubes can also vary, typically ranging from 100 mm for small conveyor systems to over 3,000 mm for large-scale operations. The length is chosen based on the width of the materials to be transported and the space available for the conveyor system.
- Custom Sizes: Besides standard sizes, manufacturers often offer custom-sized tubes to meet specific operational needs or to fit unique conveyor layouts.
Impact on Conveyor System’s Performance
The size of a conveyor roller tube significantly impacts the conveyor system’s efficiency and the types of materials it can handle. Here are some key considerations:
- Load Capacity: Larger diameter tubes can support heavier loads, making them suitable for industries that transport heavy or bulky materials. Conversely, smaller diameters are sufficient for lighter loads, such as those found in packaging or assembly lines.
- Conveyor Speed: The diameter of the roller tubes also affects the conveyor speed. Larger rollers can help achieve higher speeds due to their ability to minimize the rotational friction.
- Material Handling: The size and specifications of conveyor roller tubes must be matched with the types of materials they are intended to carry. For instance, longer tubes are needed to support wider items securely, while thicker-walled tubes are chosen for their durability in handling abrasive or corrosive materials.
- Operational Environment: The size and material of the conveyor roller tube must also be suitable for the operational environment. For example, larger tubes may be required in outdoor or harsh environments to withstand external pressures and maintain system integrity.
Selecting the appropriate size and specifications for a conveyor roller tube is essential for ensuring the conveyor system operates efficiently, safely, and effectively. It requires a careful assessment of the system’s intended use, the properties of the materials to be conveyed, and the operational environment. By understanding the range of sizes available and their impact on system performance, engineers and system designers can make informed decisions that optimize productivity and longevity.
Conveyor Roller Tube Pricing Insights
The pricing of conveyor roller tubes is influenced by a myriad of factors, reflecting the complexity and customization involved in their manufacturing and use. Understanding these factors can help businesses make informed purchasing decisions, balancing initial costs with long-term benefits. Additionally, investing in quality conveyor roller tubes can offer significant advantages in terms of durability and cost savings.
Factors Influencing Price
- Material: The choice of material (e.g., steel, stainless steel, aluminum, PVC, polyethylene, rubber) significantly affects the price. Metals are typically more expensive than plastic varieties due to their durability and load-bearing capacity.
- Size: Larger diameter and thicker wall conveyor roller tubes are more costly due to the increased amount of material required for their manufacture.
- Manufacturer: Prices can vary between manufacturers based on their production costs, brand reputation, and quality of materials used.
- Quantity: Ordering in bulk often results in lower per-unit costs due to economies of scale.
- Customization: Custom sizes or features (e.g., special coatings, high precision bearings) add to the cost.
- Quality: Higher quality tubes, which are more durable and offer better performance, tend to be more expensive.
- Market Demand: Fluctuations in demand can influence prices, with higher demand leading to higher prices.
- Shipping and Handling: The cost of transportation and handling, especially for heavy or oversized items, can significantly affect the overall cost.
Benefits of Investing in Quality Conveyor Roller Tubes
- Enhanced Durability: High-quality materials resist wear and tear, extending the life of the conveyor system.
- Reduced Maintenance Costs: Durable tubes require less frequent replacements and repairs, leading to long-term savings.
- Improved Efficiency: Quality tubes ensure smoother operations, minimizing downtime and increasing productivity.
- Better Load Capacity: Stronger materials can handle heavier loads without deforming or breaking.
- Resistance to Environmental Factors: High-grade materials can withstand harsh environments, including exposure to chemicals, moisture, and extreme temperatures.
- Lower Operational Noise: Quality tubes, especially those made from certain plastics or rubber-coated, operate more quietly.
- Enhanced Safety: Reliable and durable tubes reduce the risk of accidents due to system failure.
- Flexibility in Application: Quality tubes can be designed to fit a wide range of applications, providing more versatility.
- Sustainability: Longer-lasting tubes mean less waste and reduced need for frequent replacements, contributing to environmental sustainability.
- Cost-Efficiency Over Time: While the initial investment may be higher, the long-term savings in maintenance, replacements, and improved efficiency can outweigh the initial cost.
Investing in quality conveyor roller tubes is not just about purchasing a component for a conveyor system; it’s about investing in the longevity and efficiency of the entire operation. The right choice can lead to significant savings and operational advantages in the long run.
Used Conveyor Roller Tube Market Insights
The market for used conveyor roller tubes is a significant segment within the broader conveyor system industry, offering cost-effective solutions for businesses looking to optimize their operations without the hefty price tag of new equipment. These used tubes can be found through various channels, including online marketplaces, auctions, industrial resell shops, and directly from facilities that are upgrading or closing down.
Advantages of Opting for Used Conveyor Roller Tubes
- Cost Savings: The most apparent benefit is the substantial reduction in costs, making it an attractive option for budget-conscious businesses.
- Immediate Availability: Used tubes are often immediately available, eliminating the lead times associated with ordering new tubes.
- Environmental Sustainability: Purchasing used tubes contributes to environmental sustainability by reducing the demand for new materials and minimizing waste.
- Tested Durability: Used tubes have been tested in real-world conditions, providing a clear indication of their durability.
- Flexibility in Purchase Quantity: There’s often no minimum order quantity, allowing for more flexible purchasing options.
- Wide Selection: The used market can offer a variety of tubes from different manufacturers and of different materials.
- Potential for High-Quality Finds: It’s possible to find high-quality tubes that are in excellent condition for a fraction of the cost of new ones.
- Ease of Replacement: For older conveyor systems, finding matching replacement tubes might be easier in the used market.
- Cost-Effective Testing: Businesses looking to experiment with different tube sizes or materials can do so more affordably.
- Support for Smaller Projects: Ideal for smaller projects or for companies just starting out that might not require brand new equipment.
Potential Drawbacks of Used Conveyor Roller Tubes
- Wear and Tear: Used tubes may come with wear and tear, potentially reducing their lifespan.
- Limited Lifespan: The remaining useful life of a used tube may be shorter than that of a new one, requiring earlier replacement.
- Unknown History: Without a clear usage history, it’s challenging to predict the durability and potential issues.
- Inconsistencies in Quality: The condition of used tubes can vary widely, leading to inconsistencies in performance.
- Limited Warranty and Support: Used tubes often come with limited or no warranty, posing a risk if they fail.
- Compatibility Issues: Matching used tubes with existing systems can be challenging due to wear or outdated specifications.
- Cost of Refurbishment: Any savings may be offset by the need to refurbish or modify the tubes for specific uses.
- Availability of Specific Types: Finding the exact size, material, or type needed can be more difficult in the used market.
- Potential for Hidden Damage: There’s always a risk of internal damage that isn’t immediately apparent.
- Efficiency Concerns: Older or worn tubes may not operate as efficiently as new ones, potentially affecting the overall system performance.
When considering used conveyor roller tubes, it’s essential to weigh these advantages and drawbacks carefully. Inspection and, if possible, testing of the used tubes can mitigate some risks. This balanced approach can help businesses make informed decisions that align with their operational needs and budget constraints.
The Mechanics Behind Conveyor Roller Tube Operations
Roller conveyors are a fundamental part of material handling systems, designed to efficiently move goods across short or long distances within a facility. At the heart of these systems are the conveyor roller tubes, which play a crucial role in both gravity-driven and powered conveyors. Understanding how roller conveyors work, including the role of conveyor roller tubes, is essential for optimizing the design and functionality of these systems.
Simplified Explanation of Roller Conveyor Mechanics
Roller conveyors consist of a series of evenly spaced rollers mounted on a frame, creating a smooth, flat surface that supports and moves items along. These rollers rotate around a tube, facilitating the movement of goods. In gravity roller conveyors, items move down a slight incline due to gravity, while powered roller conveyors use motors to drive the rotation of the rollers, propelling items along the conveyor.
Roles of Conveyor Roller Tubes in Conveyor Operations
- Support and Move Loads: The primary function of conveyor roller tubes is to support the load being transported and facilitate its movement across the conveyor system.
- Reduce Friction: Roller tubes are designed to minimize friction, allowing goods to move smoothly with minimal force, whether from gravity or a motor.
- Adapt to Various Load Types: Depending on their material and design, roller tubes can handle a wide range of load types, from lightweight packages to heavy pallets.
- Facilitate Speed Control: In powered conveyors, the diameter and material of the roller tube can influence the speed at which items are moved, allowing for precise control over the flow of goods.
- Enable Accumulation: Some powered roller conveyors are designed to allow items to accumulate in certain areas without causing damage or excessive pressure, thanks to the use of specially designed roller tubes.
- Impact Resistance: Roller tubes, especially those made from durable materials, provide impact resistance, protecting both the conveyor system and the goods it transports.
- Resist Environmental Damage: Roller tubes made from materials like stainless steel or coated with special finishes can resist damage from harsh environments, chemicals, and moisture.
- Contribute to System Longevity: High-quality conveyor roller tubes are key to the longevity and reliability of the conveyor system, reducing the need for frequent maintenance and replacement.
- Energy Efficiency: In powered systems, the design and material of the roller tube can impact the conveyor’s energy efficiency, with smoother, less friction-prone tubes requiring less power to move goods.
The efficiency, durability, and functionality of a roller conveyor system are significantly influenced by the design and quality of its conveyor roller tubes. These components not only support and move loads but also contribute to the system’s overall performance and longevity. Understanding these roles is crucial for anyone involved in the design, operation, or maintenance of roller conveyor systems, as it highlights the importance of selecting the right type of conveyor roller tube for specific applications and environments.
Common Uses of Roller Conveyors and Conveyor Roller Tube Applications
Roller conveyors are versatile systems widely used across numerous industries to streamline the movement of goods, materials, and products. Central to these systems are the conveyor roller tubes, which support and facilitate the efficient transport of items. Their design and material composition allow for a broad range of applications, demonstrating the flexibility and essential nature of roller conveyors in various sectors.
Industries and Applications
- Manufacturing: In the manufacturing industry, roller conveyors are used to transport parts between different stages of the production process, from assembly to packaging.
- Distribution and Logistics: Distribution centers and warehouses utilize roller conveyors for sorting, distributing, and preparing goods for shipment, enhancing the efficiency of operations.
- Food Processing: Roller conveyors, especially those with stainless steel tubes, are employed in food processing plants for the hygienic movement of ingredients and packaged products.
- Pharmaceuticals: In pharmaceutical manufacturing, conveyors transport products through controlled environments, maintaining cleanliness and reducing manual handling.
- Agriculture: Used for handling grain, produce, and other agricultural products, roller conveyors streamline the processing and packaging operations within the agricultural sector.
- Retail: Back-of-house operations in retail environments use roller conveyors to manage inventory, facilitating the movement of stock to and from storage areas.
- Recycling Facilities: Roller conveyors play a crucial role in recycling operations, moving materials through sorting and processing stages efficiently.
- Airports: Baggage handling systems rely on roller conveyors to transport luggage between check-in, security, and aircraft loading areas, showcasing their capability to handle varying loads and sizes.
Commonly Moved Items
- Boxes: Cardboard boxes of various sizes are the most common items transported on roller conveyors, used extensively in distribution centers and warehouses.
- Pallets: Heavy-duty roller conveyors with robust conveyor roller tubes are designed to move pallets loaded with goods, facilitating bulk handling.
- Totes and Bins: Plastic totes and bins containing parts or products are easily handled by roller conveyors, particularly in manufacturing and distribution settings.
- Bags: From small retail packages to large sacks of materials in the agriculture sector, bags are routinely transported on roller conveyors.
- Components and Parts: In assembly lines, roller conveyors move components and parts between workstations, aiding in the manufacturing process.
- Beverage Containers: Bottles, cans, and kegs are transported through beverage manufacturing and bottling plants using roller conveyors, demonstrating their ability to handle delicate items.
The versatility of roller conveyors and conveyor roller tubes is evident in their wide-ranging applications across different industries. By supporting the movement of various items, from the smallest component to bulk pallets, these systems enhance operational efficiency, safety, and productivity. The specific design and material of the conveyor roller tube are selected based on the application’s demands, ensuring optimal performance and durability.
Choosing the Right Conveyor Roller Tube
Selecting the appropriate conveyor roller tube is pivotal for ensuring the efficiency, durability, and cost-effectiveness of a conveyor system. Various factors, including size, material, and the operational environment, play a crucial role in this selection process. Here are 12 tips to guide you in choosing the right conveyor roller tube for specific applications, highlighting the importance of each consideration.
Tips for Selection
- Understand the Application: Clearly define the purpose of the conveyor system—considering the types of items being moved, their weight, and how they will interact with the conveyor roller tube.
- Size Matters: Choose the right diameter and wall thickness for the roller tube based on the load it needs to support. Larger, heavier items require larger, more robust tubes.
- Material Selection: Select the material that best suits the application. Steel and stainless steel offer strength and durability, while aluminum and plastics like PVC provide lightweight and corrosion-resistant options.
- Assess the Load: Consider both the weight and the distribution of the load. Unevenly distributed loads may require stronger or differently designed roller tubes.
- Consider the Environment: The operating environment is crucial—wet, corrosive, or extreme temperature conditions demand materials and coatings that can withstand these elements.
- Price vs. Quality: While budget constraints are real, investing in higher-quality materials can reduce long-term costs related to maintenance, replacement, and downtime.
- Evaluate Manufacturer Options: Research manufacturers to find those with reputable products and support services. Manufacturer reputation can be a proxy for product quality.
- Customization Needs: Determine if your conveyor system requires custom-sized roller tubes. Customization can solve specific challenges but may increase costs.
- Maintenance and Replacement: Consider ease of maintenance and replacement. Selecting roller tubes that are easy to replace or maintain can significantly reduce downtime.
- Energy Efficiency: For powered conveyors, consider the energy efficiency of the roller tube design. Less friction and smoother operations can lead to lower energy costs.
- Consult with Experts: When in doubt, consult with engineers or specialists. Their expertise can guide you in selecting the most appropriate conveyor roller tube for your needs.
- Future-Proofing: Think about not only current needs but also potential future requirements. Choosing a slightly more capable roller tube than currently needed can offer flexibility for future changes.
Importance of Considering the Environment
The environment in which the conveyor will operate cannot be overstressed. Wet conditions require tubes that resist rust and corrosion, while environments with chemical exposures need materials that can withstand such harsh conditions without degrading. Similarly, extreme temperatures can affect the material properties of the roller tubes, making it essential to choose materials that retain their integrity and functionality under such conditions.
By taking these factors into account, businesses can ensure they select the right conveyor roller tube that not only meets their current requirements but also is a cost-effective, durable, and efficient solution for their conveying needs. This comprehensive approach to selection will result in a conveyor system that is well-suited to the application, environment, and operational demands, providing a robust platform for material handling tasks.
FAQs about Conveyor Roller Tube
Rollers on a conveyor, often referred to as conveyor rollers, are the cylindrical components that make up the part of the conveyor system where the material is actually moved. These rollers are mounted along the length of the conveyor frame and may rotate freely or be driven, depending on the type of conveyor system. They work by providing a rolling surface that items can move over, reducing the amount of friction and making it easier and more efficient to move goods from one point to another. Conveyor rollers are crucial for the functionality of conveyors as they dictate the smoothness of the transportation process and can significantly influence the conveyor’s overall performance. Depending on their application, they can be made from various materials such as steel, plastic, or rubber, each offering different benefits in terms of strength, friction, and suitability for different environments.
A roller conveyor is a type of conveyor system that utilizes a series of rollers mounted within a frame to transport materials across a flat or inclined plane. Roller conveyors are versatile and adaptable to a wide range of industrial, commercial, and retail applications, making them a popular choice for moving boxes, pallets, and other items. They can be powered, where the rollers are driven by motors, or gravity-fed, where items move down the conveyor due to the force of gravity. The simplicity of their design allows for easy maintenance and the ability to handle a wide variety of loads, sizes, and materials. Roller conveyors are particularly valued for their efficiency and the ability to streamline the material handling process, contributing to improved workflow and productivity.
The components of a roller conveyor include the conveyor frame, rollers, bearings, axle, drive unit (for powered conveyors), and any additional accessories or modifications such as stops, gates, or turntables. The frame serves as the foundation and support structure for the entire conveyor, providing stability and alignment for the rollers. Rollers are the moving parts that transport materials along the conveyor. Bearings within the rollers ensure smooth rotation and reduce friction. The axle connects the rollers to the frame and can be fixed or spring-loaded. In powered roller conveyors, a drive unit, which may include motors and gearboxes, is responsible for moving the rollers. Accessories can be added to meet specific operational needs, such as controlling the flow of materials or integrating the conveyor into larger systems. Each component plays a critical role in the conveyor’s efficiency and functionality.
Conveyor rollers can be made from a variety of materials, each selected based on the specific needs of the application, the environment in which they will operate, and the materials they will be transporting. Common materials include steel, stainless steel, aluminum, plastic, and rubber. Steel rollers are known for their strength and durability, making them suitable for heavy-duty applications. Stainless steel offers added resistance to corrosion, ideal for use in food processing or pharmaceutical industries. Aluminum rollers provide a lightweight alternative, often used in applications requiring ease of manual handling. Plastic rollers are useful in environments where corrosion resistance is necessary or where lighter loads are being moved. Rubber-coated or rubberized rollers offer the advantage of increased grip and reduced noise, making them suitable for delicate or slippery items. The choice of material impacts the roller’s performance, longevity, and maintenance requirements.
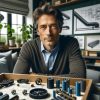
Jordan Smith, a seasoned professional with over 20 years of experience in the conveyor system industry. Jordan’s expertise lies in providing comprehensive solutions for conveyor rollers, belts, and accessories, catering to a wide range of industrial needs. From initial design and configuration to installation and meticulous troubleshooting, Jordan is adept at handling all aspects of conveyor system management. Whether you’re looking to upgrade your production line with efficient conveyor belts, require custom conveyor rollers for specific operations, or need expert advice on selecting the right conveyor accessories for your facility, Jordan is your reliable consultant. For any inquiries or assistance with conveyor system optimization, Jordan is available to share his wealth of knowledge and experience. Feel free to reach out at any time for professional guidance on all matters related to conveyor rollers, belts, and accessories.