Essential Belt Conveyor Details: Components and Functions
Belt conveyors are integral components in various industrial applications, providing efficient and reliable material handling solutions. These systems are widely used in industries such as mining, manufacturing, and logistics, where they facilitate the smooth transport of materials over long distances. The purpose of this blog post is to delve into belt conveyor details, offering a comprehensive understanding of their systems and components. By exploring conveyor belt details, we aim to provide valuable insights into their fundamental principles, essential components, and various types, helping you appreciate their role in enhancing operational efficiency and productivity in industrial settings.
What are Belt Conveyor Details
Belt conveyors are vital to many industrial operations, providing an efficient and effective means of transporting materials over varying distances. This section delves into the belt conveyor details, offering an in-depth look at their definition, fundamental principles, and essential components.
Belt Conveyor Basics
Definition of Belt Conveyor Systems
Belt conveyors are mechanical devices used to transport materials from one location to another. They consist of two or more pulleys (sometimes referred to as drums), with a continuous loop of material – the conveyor belt – that rotates around them. One or both of the pulleys are powered, moving the belt and the material on the belt forward. The powered pulley is called the drive pulley, while the unpowered pulley is known as the idler pulley. Belt conveyors are commonly used in various industries, including mining, manufacturing, and logistics, due to their ability to move large volumes of material quickly and efficiently.
Fundamental Principles of Belt Conveyor Systems
The fundamental operation of a belt conveyor system revolves around several core principles:
- Continuous Loop Movement: The conveyor belt forms a continuous loop around the pulleys, providing a constant movement of materials. This loop can vary in length and width depending on the application.
- Pulley System: The drive pulley, powered by an electric motor, moves the belt, while the idler pulleys support the belt and ensure smooth operation. The tension in the belt is adjusted by tensioning devices, which are crucial for maintaining efficiency and preventing slippage.
- Material Handling: Materials are loaded onto the conveyor belt at one end and transported to the other end. Depending on the type of conveyor belt and the materials being transported, the belt may have features such as cleats, sidewalls, or special surface coatings to improve handling.
- Support Structure: The belt is supported by a frame or structure that holds the pulleys and provides the necessary stability. This structure can be customized to fit the specific needs of the operation, including the length, width, and incline of the conveyor.
Essential Components and Functions
To fully understand belt conveyor details, it’s important to explore the various components that make up these systems and their specific functions.
Drive System
The drive system is the powerhouse of the belt conveyor. It consists of an electric motor, a gear reducer, and the drive pulley. The motor powers the pulley, which in turn moves the belt. The efficiency of the drive system directly impacts the overall performance of the conveyor. Factors such as motor power, gear ratios, and pulley diameter are critical in determining the conveyor’s capability to handle specific loads and materials.
Conveyor Belt
The conveyor belt itself is a crucial component, made from various materials depending on the application. Common materials include rubber, PVC, and fabric, each offering different properties such as flexibility, durability, and resistance to wear and tear. The design of the belt can also vary, with some featuring cleats or sidewalls to prevent materials from falling off during transport.
Idlers
Idlers are rollers that support the conveyor belt and help maintain its shape and tension. They are typically spaced at regular intervals along the length of the conveyor. Idlers reduce friction and wear on the belt, contributing to the smooth operation of the system. There are different types of idlers, including carrying idlers, return idlers, and impact idlers, each serving a specific purpose in supporting the belt.
Belt Tensioning System
Proper tensioning of the conveyor belt is crucial for its efficient operation and longevity. The tensioning system consists of devices such as take-up frames and tensioning screws that adjust the tension in the belt to prevent slippage and ensure smooth movement. Incorrect tensioning can lead to belt misalignment, increased wear, and reduced efficiency.
Pulleys
Pulleys are essential components that drive and support the conveyor belt. There are different types of pulleys used in belt conveyors, including drive pulleys, tail pulleys, snub pulleys, and bend pulleys. Each type of pulley has a specific function, such as providing the driving force, changing the direction of the belt, or adjusting the belt’s tension. The design and material of the pulleys can significantly impact the performance and durability of the conveyor system.
Loading and Discharge Devices
Loading and discharge devices are mechanisms that facilitate the loading of materials onto the conveyor belt and their discharge at the destination. These devices can vary widely depending on the type of materials being handled and the specific requirements of the operation. Common loading devices include chutes, hoppers, and feeders, while discharge devices may include plows, scrapers, and diverters. The design and efficiency of these devices play a critical role in the overall performance of the conveyor system.
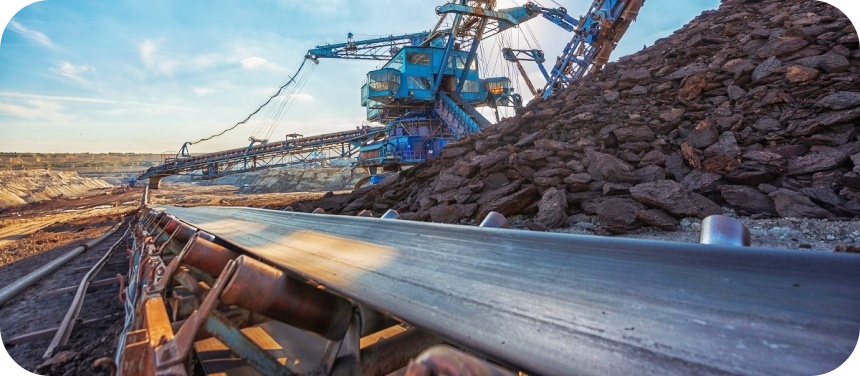
In-Depth Look at Conveyor Belt Types
Understanding the different types of conveyor belts is essential for selecting the right system for a specific application. Here are some common types of conveyor belts and their characteristics:
Flat Belt Conveyors
Flat belt conveyors are the most widely used type of conveyor belt. They consist of a flat, continuous belt that is supported by idlers and driven by a motor. These conveyors are ideal for transporting a wide range of materials, including packages, bulk materials, and unit loads. Flat belt conveyors are known for their simplicity, versatility, and cost-effectiveness.
Modular Belt Conveyors
Modular belt conveyors use a series of interlocking plastic or metal modules that form a continuous belt. These conveyors are highly adaptable and can be customized to fit specific applications. Modular belt conveyors are often used in industries such as food processing, packaging, and automotive manufacturing, where flexibility and ease of cleaning are important.
Cleated Belt Conveyors
Cleated belt conveyors feature raised cleats or ribs on the surface of the belt. These cleats help to prevent materials from sliding off the belt, making them ideal for transporting loose or bulk materials, as well as items that need to be inclined or declined during transport. Cleated belt conveyors are commonly used in agriculture, construction, and mining industries.
Specialized Conveyors
Specialized conveyors are designed for specific applications and can include inclined, curved, and long-distance conveyors. Inclined conveyors are used to move materials up or down a slope, while curved conveyors are used to navigate tight spaces and change the direction of the material flow. Long-distance conveyors are used to transport materials over extended distances, often through challenging terrains or harsh environments.
Detailed Conveyor Belt Specifications
To fully understand belt conveyor details, it’s important to consider the specific specifications and customizations that can be applied to these systems. Specifications can include belt width, length, speed, and load capacity, as well as the type of materials used for the belt and other components. Customizations may involve special coatings, reinforcements, or design modifications to meet the unique needs of an application. Detailed specifications are often provided in technical documents or manuals, which can be valuable resources for selecting and maintaining belt conveyor systems.
By understanding the fundamental principles and essential components of belt conveyor systems, as well as the various types of conveyors available, you can make informed decisions about the best conveyor solutions for your needs. Belt conveyor details encompass a wide range of factors, from the design and materials to the specific applications and performance requirements. Whether you are involved in mining, manufacturing, logistics, or any other industry that relies on efficient material handling, a thorough understanding of belt conveyor details can help you optimize your operations and achieve greater productivity.
Essential Components and Functions of Belt Conveyor Details
Understanding the essential components and functions of belt conveyor systems is crucial for optimizing their performance and ensuring efficient material handling. This section delves into the key elements that make up these systems and how they contribute to the overall functionality and efficiency of belt conveyors.
Drive System
The Power Behind Belt Conveyors
The drive system is the powerhouse of a belt conveyor, providing the necessary force to move the belt and the materials it carries. This system typically includes an electric motor, a gear reducer, and the drive pulley. The electric motor generates the power, which is then transferred through the gear reducer to the drive pulley, ultimately causing the belt to move. The efficiency of the drive system directly impacts the performance of the conveyor.
- Electric Motor: The type and power of the electric motor are selected based on the required speed and load capacity of the conveyor. Motors can range from small fractional horsepower units to large, high-power motors capable of driving extensive conveyor systems.
- Gear Reducer: The gear reducer adjusts the motor’s output speed to the desired belt speed. It ensures that the power from the motor is efficiently transferred to the drive pulley.
- Drive Pulley: The drive pulley, which is connected to the motor and gear reducer, transfers the power to the conveyor belt, causing it to move. The design and material of the drive pulley are crucial for preventing slippage and ensuring smooth operation.
The efficiency and reliability of the drive system are essential for maintaining the productivity and longevity of the belt conveyor.
Conveyor Belt
Materials, Designs, and the Role of the Conveyor Belt
The conveyor belt itself is a critical component, determining the system’s ability to handle different types of materials and operating conditions. Conveyor belts are made from various materials and designed in different configurations to suit specific applications. Here are five examples of conveyor belt materials and designs:
- Rubber Belts: These are commonly used in mining and heavy-duty industries due to their durability and resistance to abrasion. Rubber belts are suitable for transporting bulk materials such as ores, coal, and aggregates.
- PVC Belts: Polyvinyl chloride (PVC) belts are widely used in food processing, packaging, and light manufacturing. They are known for their flexibility, smooth surface, and resistance to chemicals and oils.
- Fabric Belts: Fabric belts, often made from polyester or nylon, provide a balance between strength and flexibility. They are used in various applications, including logistics and warehousing, where a lightweight and adaptable belt is required.
- Modular Plastic Belts: These belts consist of interlocking plastic modules, offering high versatility and easy maintenance. They are ideal for applications requiring frequent cleaning and belt replacement, such as in the food and beverage industry.
- Metal Belts: Metal conveyor belts are used in high-temperature environments and applications requiring high strength and durability, such as in the automotive and electronics industries. These belts can withstand extreme conditions and heavy loads.
Each type of conveyor belt is designed to meet specific operational needs, contributing to the overall performance and efficiency of the conveyor system.
Idlers
Supporting the Conveyor Belt and Maintaining Its Structure
Idlers are rollers that support the conveyor belt, helping to maintain its shape and tension. They are strategically placed along the conveyor length to reduce friction and wear on the belt. Idlers play a crucial role in ensuring smooth and efficient belt operation. There are different types of idlers, each serving a specific function:
- Carrying Idlers: Positioned on the carrying side of the belt, these idlers support the load and help maintain the belt’s alignment.
- Return Idlers: Located on the return side of the belt, return idlers support the empty belt as it returns to the loading point, preventing sagging and maintaining proper tension.
- Impact Idlers: Installed at loading points, impact idlers have reinforced rollers to absorb the impact of falling materials, protecting the belt from damage.
- Transition Idlers: Placed at the transition points where the belt changes from flat to troughed or vice versa, transition idlers help the belt conform to the required shape without causing stress or damage.
- Self-aligning Idlers: These idlers automatically adjust to maintain proper belt alignment, preventing misalignment and reducing wear on the belt and structure.
Properly designed and maintained idlers are essential for the longevity and efficiency of the conveyor system.
Belt Tensioning System
Crucial for Conveyor Belt Operations and Longevity
The belt tensioning system is responsible for maintaining the correct tension in the conveyor belt, which is crucial for preventing slippage, misalignment, and excessive wear. Proper tensioning ensures smooth and efficient operation, extending the lifespan of the belt and reducing maintenance costs. Key components of the tensioning system include:
- Take-up Frames: These frames house the tensioning devices and are typically mounted on the conveyor structure. They allow for easy adjustment of the belt tension.
- Tensioning Screws: Used to adjust the position of the take-up frames, tensioning screws enable precise control of the belt tension. They are often located at the ends of the conveyor or at intermediate points along the length.
- Counterweights: In some systems, counterweights are used to apply tension to the belt. These weights provide a constant force, ensuring consistent tension throughout the operation.
- Automatic Tensioning Devices: Advanced systems may use automatic tensioning devices that continuously monitor and adjust the belt tension in real-time, optimizing performance and reducing the need for manual adjustments.
Proper belt tensioning is essential for preventing common issues such as belt slippage, misalignment, and premature wear, contributing to the overall efficiency and reliability of the conveyor system.
Pulleys
Types of Pulleys and Their Functions
Pulleys are critical components of belt conveyors, responsible for driving and guiding the belt. Different types of pulleys are used in conveyor systems, each serving a specific function. Here are five examples:
- Drive Pulley: The drive pulley is connected to the motor and gear reducer, providing the driving force that moves the belt. It is typically located at the discharge end of the conveyor.
- Tail Pulley: Positioned at the loading end of the conveyor, the tail pulley guides the belt as it transitions from the return side to the carrying side. It also helps in maintaining proper belt tension.
- Snub Pulley: Snub pulleys are used to increase the contact angle between the belt and the drive pulley, improving traction and reducing slippage. They are usually located close to the drive pulley.
- Bend Pulley: Bend pulleys change the direction of the belt, allowing for more complex conveyor layouts. They are often used in combination with other pulleys to navigate tight spaces.
- Take-up Pulley: The take-up pulley is part of the tensioning system, helping to maintain proper belt tension. It is typically mounted on the take-up frames and adjusted as needed.
The design and material of pulleys are crucial for ensuring smooth and efficient belt operation, reducing wear and extending the lifespan of the conveyor system.
Loading and Discharge Devices
How Materials Are Loaded Onto and Discharged from the Belt
Loading and discharge devices are essential for the efficient handling of materials on a conveyor belt. These devices ensure that materials are properly loaded onto the belt and accurately discharged at the destination. Key components include:
- Chutes: Conveyor belt chutes are used to guide materials onto the conveyor belt, ensuring a smooth and controlled transfer. They can be designed to accommodate different types of materials and loading conditions.
- Hoppers: Hoppers are large containers that hold materials before they are loaded onto the conveyor belt. They are often used in bulk material handling applications to regulate the flow of materials.
- Feeders: Feeders control the rate at which materials are loaded onto the conveyor belt, ensuring consistent and efficient loading. They can be mechanical or automated, depending on the application.
- Plows: Plows are used to divert materials from the conveyor belt at specific discharge points. They are commonly used in multi-discharge conveyor systems.
- Scrapers: Scrapers clean the belt as it returns from the discharge point, removing any residual materials and preventing buildup. They are essential for maintaining belt hygiene and preventing contamination.
By understanding the essential components and functions of belt conveyor systems, you can optimize their performance and ensure efficient material handling in various industrial applications. Proper selection, design, and maintenance of these components are key to achieving operational efficiency and productivity.
In-Depth Look at elt Conveyor Details Types
Understanding the various types of conveyor belts is crucial for selecting the right system for your specific industrial needs. Each type of belt offers unique advantages and applications. This section provides an in-depth look at different conveyor belt types, emphasizing their common uses, advantages, and specific industrial applications.
Flat Belt Conveyors
Common Uses and Advantages
Flat belt conveyors are among the most versatile and widely used types of conveyors. They consist of a continuous flat belt supported by rollers or a flat surface. These conveyors are ideal for transporting a wide range of materials in various industries due to their simplicity and efficiency. Here are five examples of their common uses and advantages:
- Manufacturing: In manufacturing plants, flat belt conveyors are used to transport parts, assemblies, and finished products between workstations. Their smooth surface ensures delicate items are moved without damage.
- Food Processing: Flat belts made from food-grade materials are used in the food processing industry to transport raw ingredients and packaged goods. They are easy to clean and maintain, ensuring hygienic conditions.
- Packaging: In packaging operations, flat belt conveyors efficiently move products through different stages of the packaging process, from filling to sealing and labeling.
- Distribution Centers: Flat belt conveyors are used in distribution centers to sort and transport packages quickly and efficiently, facilitating smooth logistics operations.
- Airport Baggage Handling: At airports, flat belt conveyors are integral to the baggage handling systems, transporting luggage from check-in areas to loading points and vice versa.
The primary advantages of flat belt conveyors include their versatility, ease of maintenance, and ability to handle a wide range of materials.
Modular Belt Conveyors
Their Adaptability and Areas of Application
Modular belt conveyors are constructed from interlocking plastic or metal modules, providing high adaptability and durability. These conveyors are designed to accommodate complex routing, making them suitable for a variety of applications. Here are five examples of their adaptability and areas of application:
- Automotive Industry: In automotive manufacturing, modular belt conveyors handle heavy parts and assemblies. Their robust design allows for the transport of car components through different stages of production.
- Beverage Bottling: Modular belts are ideal for beverage bottling plants, where they transport bottles through washing, filling, capping, and labeling processes. Their easy-to-clean design ensures compliance with hygiene standards.
- Pharmaceutical Industry: In pharmaceutical manufacturing, modular belts move products through various processing stages. Their ability to be easily sterilized makes them suitable for environments requiring high cleanliness levels.
- Electronics Manufacturing: Modular belt conveyors are used in electronics manufacturing to transport delicate components and assemblies. Their flexibility allows for precise positioning and handling.
- Warehouse Automation: In automated warehouses, modular belts are part of complex conveyor systems that sort and route products efficiently. Their adaptability to different configurations enhances automation capabilities.
The key advantages of modular belt conveyors include their flexibility, durability, and ease of maintenance. They can be easily reconfigured or repaired, minimizing downtime and increasing operational efficiency.
Cleated Belt Conveyors
Design Benefits for Specific Industrial Tasks
Cleated belt conveyors feature raised cleats or ribs on the belt surface, which help to prevent material slippage and provide additional grip. These conveyors are particularly useful for transporting loose or bulk materials, especially on inclines and declines. Here are five examples of their design benefits for specific industrial tasks:
- Agriculture: In agricultural settings, cleated belt conveyors are used to transport grain, seeds, and other bulk materials. The cleats prevent materials from sliding back, ensuring efficient handling.
- Construction: Cleated belts are used in construction to move sand, gravel, and other bulk construction materials. Their design allows for the transportation of heavy loads on steep inclines.
- Recycling: In recycling facilities, cleated belts transport sorted materials, such as plastic, glass, and metal, to different processing areas. The cleats ensure that materials remain securely on the belt.
- Mining: Cleated belts are used in mining operations to transport minerals and ores. The raised cleats provide the necessary grip to move heavy materials through rugged terrain.
- Food Industry: In the food industry, cleated belts are used to transport bulk food items like vegetables, fruits, and grains. The cleats help in maintaining the position of the items on the belt, especially during washing and sorting processes.
The design benefits of cleated belt conveyors include enhanced grip, prevention of material slippage, and the ability to handle steep inclines, making them ideal for specific industrial tasks that require efficient material handling.
Get in touch for personalized pricing and solutions for Conveyor Belts.
Specialized Conveyors
Insight into Inclined, Curved, and Long-Distance Conveyors
Specialized conveyors are designed to meet specific requirements and challenges that standard conveyors might not address. These include inclined, curved, and long-distance conveyors, each offering unique solutions for different industrial applications.
Inclined Conveyors
Inclined conveyors are used to transport materials between different elevations, such as from a lower floor to an upper floor. They are commonly used in industries where materials need to be moved vertically. The key benefits include:
- Space Utilization: Inclined conveyors optimize space by allowing materials to be transported vertically, reducing the need for extensive horizontal space.
- Efficiency: They provide an efficient solution for moving materials to higher elevations, minimizing manual labor and increasing productivity.
Curved Conveyors
Curved conveyors are designed to navigate tight spaces and change the direction of material flow. They are essential in facilities where the layout requires materials to be transported around corners or through complex pathways. The key benefits include:
- Space Optimization: Curved conveyors make efficient use of available space by allowing for smooth directional changes without the need for additional equipment.
- Flexibility: They offer flexibility in system design, enabling the creation of customized conveyor paths to suit specific layout requirements.
Long-Distance Conveyors
Long-distance conveyors are used to transport materials over extended distances, often through challenging terrains or harsh environments. They are essential in industries such as mining and bulk material handling. The key benefits include:
- Cost-Effectiveness: Long-distance conveyors reduce the need for multiple transfer points and intermediate handling, lowering operational costs.
- Efficiency: They provide a continuous and efficient method of transporting large volumes of materials over long distances, improving overall productivity.
By exploring these belt conveyor details, you gain a comprehensive understanding of the different types of conveyors and their specific applications. Each type of conveyor offers unique advantages that can significantly enhance the efficiency and productivity of various industrial processes. Whether you need a versatile flat belt conveyor, an adaptable modular belt conveyor, a specialized cleated belt conveyor, or a purpose-built inclined, curved, or long-distance conveyor, understanding these details will help you select the right system for your needs.
Belt Conveyor Details Specifications
Understanding the specific details and specifications of belt conveyors is crucial for selecting the right system for industrial applications. This section delves into the industrial belt conveyor details, highlighting specific adaptations and customizations that enhance performance and efficiency in various settings.
Industrial Belt Conveyor Details
Specific Adaptations and Customizations in Industrial Settings
Industrial belt conveyors are often customized to meet the unique requirements of different applications. These customizations can include variations in belt width, length, speed, and load capacity, as well as the materials used for the belt and other components. Here are some detailed considerations and examples of adaptations in industrial belt conveyor systems:
1. Belt Width and Length
The width and length of a conveyor belt are crucial factors that determine its capacity and suitability for specific tasks.
- Belt Width: The width of the belt is chosen based on the size and type of materials being transported. Wider belts are used for bulk materials or large items, while narrower belts are suitable for smaller, lighter items. For example, a mining operation transporting large quantities of ore might use a belt width of 1.5 meters, whereas a packaging line for small consumer goods might use a belt width of 0.5 meters.
- Belt Length: The length of the belt depends on the distance the materials need to be transported. In long-distance conveyor systems, the belt length can be several kilometers. For instance, a conveyor system in a mining operation might have a length of 5 kilometers to transport materials from the extraction site to the processing plant.
2. Belt Speed and Load Capacity
The speed and load capacity of a conveyor belt are critical for ensuring efficient operation and meeting production targets.
- Belt Speed: The speed at which the belt moves is determined by the requirements of the process it supports. Higher speeds are used for lightweight materials and high-throughput applications, while lower speeds are better for heavy or fragile materials. For example, a high-speed conveyor might move at 3 meters per second for packaging operations, whereas a slower belt might move at 0.5 meters per second for handling heavy automotive parts.
- Load Capacity: The load capacity of the belt must be sufficient to handle the maximum weight of the materials being transported. This is influenced by factors such as belt strength, pulley design, and motor power. For example, a conveyor belt used in an aggregate processing plant might have a load capacity of 500 kg per meter, while one used in an electronics assembly line might have a load capacity of 50 kg per meter.
3. Belt Materials and Surface Treatments
The material and surface treatment of the conveyor belt are chosen based on the nature of the materials being transported and the operating environment.
- Rubber Belts: Rubber belts are durable and resistant to abrasion, making them suitable for heavy-duty applications such as mining and construction. They can also be reinforced with steel or fabric for added strength.
- PVC Belts: PVC belts are flexible and resistant to oils and chemicals, making them ideal for food processing and packaging applications. They can be easily cleaned and maintained, ensuring hygiene standards are met.
- Fabric Belts: Fabric belts, such as those made from polyester or nylon, offer a balance of strength and flexibility. They are commonly used in logistics and warehousing for their lightweight and adaptable properties.
- Special Coatings: Conveyor belts can be coated with materials such as Teflon or silicone to provide additional properties, such as heat resistance or non-stick surfaces. These coatings are useful in applications where the belt is exposed to high temperatures or sticky materials.
4. Pulley Design and Arrangement
The design and arrangement of pulleys are essential for ensuring the smooth operation and longevity of the conveyor belt.
- Drive Pulleys: Drive pulleys are typically made from high-strength materials such as steel or aluminum and are designed to provide maximum traction with the belt. They can be coated with rubber or other materials to increase friction and prevent slippage.
- Idler Pulleys: Idler pulleys support the belt and help maintain proper tension. They are often arranged in sets along the length of the conveyor to distribute the load evenly and reduce wear on the belt.
- Snub Pulleys: Snub pulleys are used to increase the angle of contact between the belt and the drive pulley, improving traction and reducing the risk of slippage.
5. Custom Features and Accessories
Industrial belt conveyors can be equipped with various custom features and accessories to enhance their performance and adapt to specific requirements.
- Sidewalls and Cleats: Sidewalls and cleats can be added to the belt to prevent materials from falling off and to provide additional grip for inclined or declined transport.
- Belt Tracking Systems: Belt tracking systems ensure that the belt remains centered on the pulleys, preventing misalignment and reducing wear. These systems can be automatic or manually adjusted.
- Load Sensors and Weighing Systems: Load sensors and weighing systems can be integrated into the conveyor to monitor the weight of materials being transported, ensuring that the load capacity is not exceeded and providing data for process control.
- Dust and Containment Covers: Dust and containment covers are used to protect the materials being transported and to prevent dust and debris from contaminating the environment. These covers can be made from various materials, including metal and plastic, and can be designed to be easily removable for maintenance.
6. Environmental Considerations
The operating environment plays a significant role in the design and specification of conveyor belts.
- Temperature Resistance: Belts used in high-temperature environments, such as foundries or baking ovens, must be made from materials that can withstand extreme heat without degrading.
- Corrosion Resistance: In corrosive environments, such as chemical processing plants or marine applications, belts and components must be made from materials that resist corrosion, such as stainless steel or coated metals.
- Moisture and Water Resistance: Belts used in wet or humid environments need to be resistant to moisture and water absorption to prevent degradation and maintain performance.
By understanding the detailed specifications of belt conveyors, including belt width, length, speed, load capacity, materials, pulley design, custom features, and environmental considerations, you can select the right conveyor system for your specific industrial needs. Customizing these elements to suit the unique requirements of your application will enhance the efficiency, reliability, and longevity of your conveyor system. Detailed knowledge of belt conveyor details ensures that your material handling operations are optimized for maximum productivity and minimal downtime.
Design Considerations for Belt Conveyor Details
Designing an efficient and effective belt conveyor system requires careful consideration of various factors that influence its performance and longevity. This section explores the critical design considerations for belt conveyor details, including material characteristics, environmental conditions, and principles of efficient design.
Factors Influencing the Design of Belt Conveyors
The design of a belt conveyor system is influenced by several key factors, each impacting the system’s functionality and efficiency. Understanding these factors helps in creating a conveyor that meets the specific needs of an application.
1. Material Characteristics
The properties of the materials being transported play a significant role in the design of the conveyor belt.
- Bulk Density: The bulk density of the material affects the load capacity and design of the belt. For example, materials with high bulk density, such as iron ore, require a stronger, more durable belt compared to materials with low bulk density, like sawdust. Additionally, conveyor belt rubber density plays a crucial role in ensuring the belt’s strength and durability for handling varying material densities.
- Particle Size and Shape: The size and shape of the particles influence the type of belt and the spacing of the idlers. Fine, powdery materials may require a belt with sidewalls to prevent spillage, while large, irregularly shaped materials may need a more robust belt with reinforced edges.
- Abrasion and Corrosiveness: Materials that are highly abrasive or corrosive necessitate belts made from specific materials that can withstand wear and tear. For example, belts used in the mining industry are often made from abrasion-resistant rubber, while those in chemical plants may require corrosion-resistant coatings.
- Moisture Content: The moisture content of the material can affect the choice of belt material and surface treatment. Wet or sticky materials may need belts with non-stick surfaces or special coatings to prevent clogging and buildup.
- Temperature Sensitivity: Materials that are sensitive to temperature changes may require belts with thermal resistance. For example, in food processing, conveyor belts must handle both hot and cold items without degrading.
2. Environmental Conditions
The operating environment significantly influences the design and material selection for belt conveyors.
- Temperature: Extreme temperatures, whether hot or cold, require belts made from materials that can withstand these conditions without losing integrity. For example, belts in a foundry must endure high heat, while those in refrigerated environments must remain flexible at low temperatures.
- Humidity and Moisture: High humidity and moisture levels can lead to belt degradation and slippage. In such environments, belts made from water-resistant materials or with special coatings are necessary to maintain performance and durability.
- Dust and Contaminants: Dusty environments, such as those found in cement plants or grain handling facilities, require belts with dust-resistant properties to prevent contamination and ensure smooth operation.
- Chemical Exposure: In environments with exposure to chemicals, such as in pharmaceutical or chemical processing plants, belts must be resistant to chemical reactions that could weaken the material or cause contamination.
- Outdoor Conditions: Outdoor conveyors must withstand weather conditions such as rain, wind, and UV radiation. Belts designed for outdoor use often include weather-resistant materials and protective covers to enhance longevity.
3. Load and Speed Requirements
The load capacity and speed of the conveyor affect the design of the belt and drive system.
- Load Capacity: The design must accommodate the maximum load that the conveyor will carry, including safety factors. Overloading can lead to belt failure and increased maintenance costs.
- Speed: The speed at which the belt moves is determined by the required throughput and the characteristics of the material. High-speed conveyors require precision in design to ensure stability and prevent material spillage.
4. Length and Elevation Changes
The length of the conveyor and any elevation changes impact the design and selection of components.
- Conveyor Length: Longer conveyors require more support and careful consideration of tensioning and drive systems to ensure consistent operation. Intermediate drives may be necessary for very long conveyors to maintain tension.
- Elevation Changes: Inclines and declines in the conveyor path require belts with specific features, such as cleats or high-friction surfaces, to prevent material rollback and ensure smooth transport.
5. Regulatory and Safety Requirements
Compliance with industry standards and safety regulations is crucial in the design of belt conveyors.
- Safety Standards: Conveyor designs must meet safety standards to prevent accidents and injuries. This includes incorporating emergency stop mechanisms, safety guards, and appropriate signage.
- Regulatory Compliance: Depending on the industry, conveyors may need to comply with specific regulations, such as those set by OSHA (Occupational Safety and Health Administration) or FDA (Food and Drug Administration) for food and pharmaceutical applications.
Principles of Efficient Conveyor Design
Efficient conveyor design principles focus on optimizing performance, reducing energy consumption, and minimizing maintenance requirements. These principles are integral to creating a conveyor system that meets operational goals and enhances productivity.
1. Energy Efficiency
Designing for energy efficiency involves selecting components and designing systems that reduce energy consumption.
- Efficient Motors and Drives: Using energy-efficient motors and variable frequency drives (VFDs) can significantly reduce energy consumption. VFDs allow for precise control of the conveyor speed, optimizing energy use.
- Low-Friction Components: Utilizing low-friction materials for belts, idlers, and pulleys reduces the energy required to move the belt, leading to lower operating costs.
2. Durability and Reliability
Designing for durability and reliability ensures that the conveyor operates smoothly with minimal downtime.
- Robust Materials: Selecting high-quality, durable materials for the belt and components extends the lifespan of the conveyor and reduces maintenance costs.
- Preventive Maintenance: Incorporating design features that facilitate easy maintenance, such as accessible components and modular designs, helps in performing regular preventive maintenance, reducing the likelihood of unexpected failures.
3. Scalability and Flexibility
Scalable and flexible designs allow for future modifications and expansions without significant redesigns.
- Modular Design: Using modular components that can be easily added or replaced allows for scalability. This is particularly useful in industries where production needs may change over time.
- Adjustable Features: Designing conveyors with adjustable height, speed, and angle features enhances flexibility, allowing the system to adapt to different operational requirements.
4. Safety and Ergonomics
Incorporating safety and ergonomic considerations ensures a safe working environment and improves operator efficiency.
- Safety Guards and Emergency Stops: Including safety guards and emergency stop buttons at strategic locations enhances safety by preventing accidents and allowing for quick shutdowns in emergencies.
- Ergonomic Design: Designing conveyors at appropriate working heights and incorporating features that reduce manual handling improve operator comfort and efficiency, reducing the risk of injuries.
5. Environmental Sustainability
Designing with environmental sustainability in mind helps reduce the ecological footprint of conveyor systems.
- Recyclable Materials: Using recyclable materials for belts and components reduces environmental impact. Choosing materials that can be easily recycled at the end of their life cycle is beneficial.
- Energy-Efficient Operation: Implementing energy-efficient design principles and using renewable energy sources, such as solar power, can reduce the environmental impact of conveyor operations.
By considering factors such as material characteristics, environmental conditions, load and speed requirements, length and elevation changes, and regulatory and safety requirements, you can design a belt conveyor system that meets your specific industrial needs. Incorporating principles of efficient conveyor design, including energy efficiency, durability, reliability, scalability, flexibility, safety, ergonomics, and environmental sustainability, ensures that your conveyor system operates optimally, enhancing productivity and reducing costs. Detailed knowledge of belt conveyor details is essential for creating a system that not only meets operational demands but also contributes to a safe and sustainable working environment.
FAQs About Belt Conveyor Details
A conveyor belt is a continuous loop of material that moves on rollers or a flat surface to transport materials from one point to another. The main components of a conveyor belt system include the belt itself, which is typically made from materials such as rubber, PVC, fabric, or metal, and the pulleys, which are used to drive and support the belt. Conveyor belts are commonly used in various industries including mining, manufacturing, food processing, logistics, and recycling. They provide an efficient and reliable method of transporting bulk materials, parts, and finished products over short or long distances. The key advantage of conveyor belts is their ability to move materials quickly and continuously, improving operational efficiency and reducing the need for manual handling.
The specification of a conveyor belt encompasses several key parameters that determine its suitability for specific applications. These specifications include the belt width, which can range from a few centimeters to several meters, depending on the size and volume of the materials to be transported. The belt length varies based on the distance the materials need to travel, with some belts extending over several kilometers. The belt speed, typically measured in meters per second, affects the rate at which materials are transported. Load capacity is another critical specification, indicating the maximum weight the belt can carry. The belt material is chosen based on factors such as durability, resistance to abrasion and chemicals, and temperature tolerance. Additionally, the belt may have specific surface treatments, such as anti-slip or heat-resistant coatings, to enhance performance in particular environments. Understanding these specifications is essential for selecting the right conveyor belt for your industrial needs.
Belt conveyors come in various types, each designed to meet specific material handling needs. Flat belt conveyors are the most common type, featuring a flat, continuous belt supported by rollers or a flat surface. They are versatile and used across multiple industries for transporting light to medium-weight materials. Modular belt conveyors consist of interlocking plastic or metal modules, offering high adaptability and ease of maintenance. These are ideal for applications requiring frequent cleaning or reconfiguration. Cleated belt conveyors have raised sections, or cleats, that prevent materials from sliding backward, making them suitable for inclined transport of bulk materials. Inclined belt conveyors are specifically designed to move materials between different elevations, such as from one floor to another in a warehouse. Curved belt conveyors navigate tight spaces and directional changes in material flow, optimizing the use of available space. Each type of belt conveyor offers unique advantages and is selected based on the specific requirements of the application.
A belt conveyor system is composed of several essential parts that work together to transport materials efficiently. The conveyor belt itself is the most critical component, made from materials such as rubber, PVC, or metal, chosen based on the application requirements. The drive system includes an electric motor, gear reducer, and drive pulley, providing the necessary power to move the belt. Idlers are rollers that support the belt and help maintain its tension and alignment. The belt tensioning system, which can include take-up frames and tensioning screws, ensures the belt operates at the correct tension to prevent slippage and wear. Pulleys, such as drive pulleys, tail pulleys, snub pulleys, and bend pulleys, are used to guide and drive the belt, ensuring smooth operation. Loading and discharge devices, like chutes, hoppers, and feeders, facilitate the loading and unloading of materials onto and off the belt. Each of these parts plays a vital role in the efficient operation of a belt conveyor system, contributing to its reliability and performance.
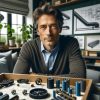
Jordan Smith, a seasoned professional with over 20 years of experience in the conveyor system industry. Jordan’s expertise lies in providing comprehensive solutions for conveyor rollers, belts, and accessories, catering to a wide range of industrial needs. From initial design and configuration to installation and meticulous troubleshooting, Jordan is adept at handling all aspects of conveyor system management. Whether you’re looking to upgrade your production line with efficient conveyor belts, require custom conveyor rollers for specific operations, or need expert advice on selecting the right conveyor accessories for your facility, Jordan is your reliable consultant. For any inquiries or assistance with conveyor system optimization, Jordan is available to share his wealth of knowledge and experience. Feel free to reach out at any time for professional guidance on all matters related to conveyor rollers, belts, and accessories.