Conveyor Belt Chutes Manage and Redirect Material Flow
In the bustling heart of modern industry, the conveyor belt chute stands as an unsung hero, channeling goods with remarkable efficiency. For those new to the world of material handling, a conveyor belt chute is a pivotal component designed to guide products from one conveyor belt segment to another or directly into storage bins or processing equipment. These chutes are meticulously crafted to deal with an array of items, from granular bulk commodities like cereals and coal to intricate electronic components and packaged consumer goods.
The significance of a well-designed conveyor belt chute system cannot be overstated. They are the silent arbitrators of material flow, making their presence crucial in sectors as diverse as mining, agriculture, electronics, and pharmaceuticals. By ensuring seamless transitions of materials with minimal human intervention, conveyor belt chutes not only boost productivity but also enhance workplace safety, proving indispensable in a myriad of material handling scenarios. Whether implemented in the rigorous environment of a mining operation or the fast-paced setting of a parcel distribution center, conveyor belt chutes play a vital role in maintaining the continuity and efficiency that modern industry demands.
What are Conveyor Belt Chutes
A conveyor belt chute is an integral part of material handling systems, serving as the pathway through which materials are directed from one point to another, typically from one conveyor belt to another section or into a storage container. These chutes are designed to harness gravity, guiding materials downward or along designated trajectories with minimal resistance, ensuring a smooth transit. The design of a belt conveyor chute is tailored to the nature of the materials it handles, considering factors such as abrasiveness, moisture content, and size, to preserve the material’s integrity and the chute’s longevity.
The role of chutes in the efficiency of conveyor systems is multifaceted. By facilitating the swift and orderly transfer of goods, conveyor belt chutes significantly reduce the need for manual handling, thereby streamlining operations and minimizing bottlenecks. This efficiency isn’t just about speed; it’s also about safety and reducing the potential for material loss or damage. Properly designed conveyor belt chutes minimize spillage and dust, contribute to a safer working environment, and help maintain the quality of the materials being transported. In essence, these chutes are crucial for ensuring that the conveyor system operates smoothly, effectively, and with minimal downtime, ultimately contributing to the overall productivity and cost-effectiveness of the material handling process.
Types of Conveyor Belt Chutes
Conveyor belt chutes are essential components in the material handling industry, providing directed flow of materials and connecting various stages of the handling process. There are various types of conveyor belt chutes, each designed to fulfill specific roles within a material handling system. Here we explore the standard conveyor chute, dribble chute, and transfer chute, focusing on their designs, roles, and applications.
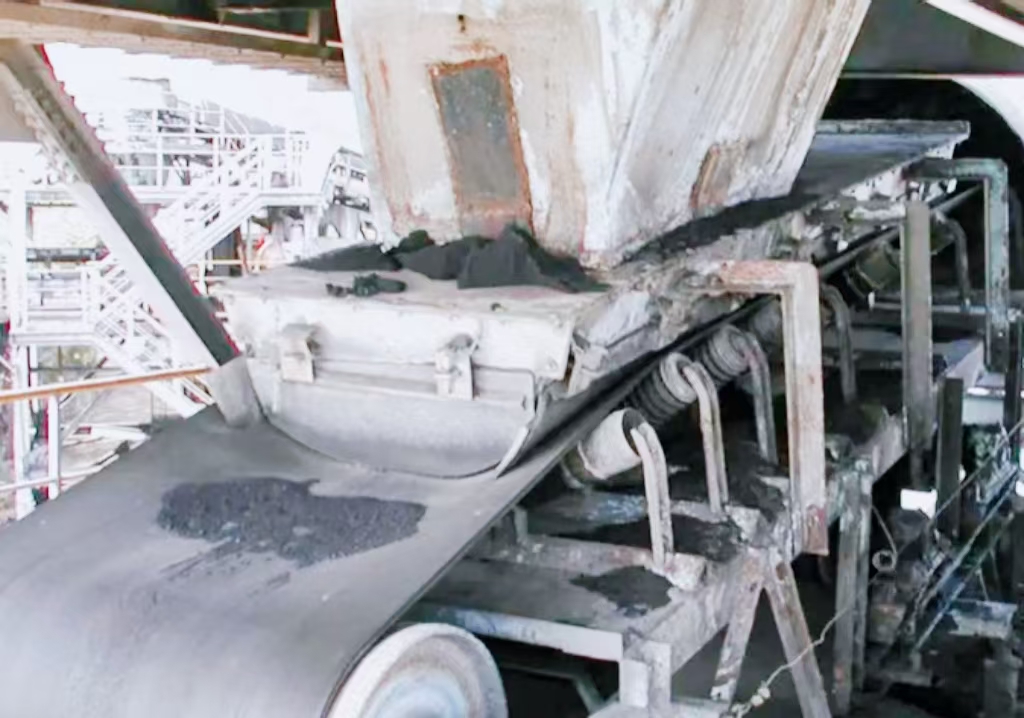
Standard Conveyor Chute
The standard conveyor belt chute is a fundamental part of any material transportation system. The head chute directs material down, while dribble chutes return scraped material, ensuring flow direction and centering on the belt to enhance performance. The standard conveyor belt chute is essential for efficient material transportation, reducing impact zone turbulence, and returning scraped material to the discharge stream. Its general design includes a smooth, trough-like passage that guides the materials from one end to the next, often relying on gravity and strategic angling to facilitate movement.
General Design and Applications
The design of a standard conveyor belt chute allows for a controlled descent of materials, mitigating the risk of damage or breakage. It is characterized by sturdy construction and can be installed with wear-resistant linings for handling abrasive materials. These chutes are widely used in various industries, including mining, agriculture, construction, and manufacturing, serving as a reliable means of transferring bulk materials from conveyors to storage areas, trucks, or processing equipment.
Typical Materials Handled
Standard conveyor belt chutes handle a vast range of materials, from agricultural grains and mining ores to construction debris and recyclable goods. Their design is adaptable to accommodate materials with different densities, lump sizes, and flow characteristics. Careful consideration is given to the chute’s incline and surface finish ensuring a smooth and consistent transfer of materials.
Dribble Chute
Dribble chutes are employed to catch and redirect fine particles or residuals that escape from the main conveyor, thereby playing a crucial role in maintaining the cleanliness and efficiency of the conveyor system.
Definition and Specific Role in Handling Material Spillage
A dribble chute is a secondary chute positioned beneath the main conveyor chute or between conveyor sections. It is specifically designed to collect spillage or dribbled materials, which can occur due to factors like belt misalignment, vibration, or improper loading.
Placement and Importance in Maintaining Cleanliness and Efficiency
The placement of dribble chutes is strategic, ensuring that they are easily accessible for cleanup and maintenance without interrupting the main material flow. By capturing and redirecting spillage, they reduce safety hazards, minimize material waste, and help maintain a clean operation environment, which is vital for efficiency and the longevity of the conveyor system.
Transfer Chute
Transfer chutes are specifically designed to facilitate the smooth transition of materials between different conveyor belts, ensuring a continuous and efficient flow within the material handling system.
Role in Transferring Material Between Conveyor Belts
The transfer conveyor belt chute is integral in systems where materials must be handed off from one conveyor belt to another. The design of these chutes allows for a seamless transfer, reducing the impact force, controlling the material speed, and ensuring that the material’s directional change is as smooth as possible.
Significance in Minimizing Spillage and Optimizing Material Flow
The significance of a well-designed transfer chute cannot be overstated. By effectively controlling the flow, it minimizes material spillage, which can lead to operational delays and increased cleanup costs. Moreover, an optimized transfer chute design reduces wear on the belt and other mechanical components, ensuring efficient material flow, prolonging equipment life, and contributing to the overall profitability of the operation.
Each type of belt conveyor chute plays a pivotal role in industrial and commercial material handling, contributing to system efficiency and operational success. By understanding these types and their specific functions, businesses can choose the appropriate conveyor belt chute design to meet their needs, ensuring cost-effective and efficient materials handling.
Advantages of Conveyor Belt Chutes
Cost-Effectiveness
One of the primary advantages of conveyor belt chutes is their cost-effectiveness. These chutes provide a low-cost solution for material handling needs, making them an attractive option for various industries. The initial investment required for installing conveyor belt chutes is significantly lower compared to other material handling systems. Additionally, the maintenance costs associated with chutes are minimal due to their simple design and robust construction.
Chutes leverage gravity, which is a free and renewable energy source, to move materials efficiently from one point to another. This eliminates the need for complex and expensive mechanical systems, reducing both capital and operational expenditures. In industries such as mining, agriculture, and manufacturing, where bulk materials need to be transported over short distances, the cost savings can be substantial.
Moreover, the low maintenance requirements of conveyor belt chutes contribute to their cost-effectiveness. With fewer moving parts compared to mechanized conveyors, the likelihood of breakdowns and the need for frequent repairs are significantly reduced. This not only lowers the maintenance costs but also minimizes downtime, ensuring continuous and efficient operations.
Simplicity and Efficiency
The simplicity and efficiency of conveyor belt chutes are among their most significant benefits. Chutes are designed to facilitate smooth and efficient material flow by taking advantage of gravity. Their straightforward design ensures that materials are directed in a controlled manner, reducing the risk of blockages and ensuring consistent throughput.
The 111 simplicity of chutes means they can be easily integrated into existing material handling systems. Whether used as standalone components or in conjunction with other conveyors, chutes can be customized to fit specific operational needs without requiring significant modifications. This flexibility makes them ideal for a wide range of applications, from bulk material handling to precision operations in the pharmaceutical and chemical industries.
Efficiency is further enhanced by the ability of chutes to handle various types of materials, including coarse grains, mineral ores, coal, and fine powders. By ensuring that materials are directed smoothly and consistently, chutes help maintain the integrity of the product and reduce material loss. This is particularly important in industries where product quality and consistency are paramount.
The 111 efficiency of conveyor belt chutes also translates to improved safety. By minimizing the need for manual handling and reducing the potential for spillage, chutes help create a safer working environment. This is especially critical in industries dealing with hazardous or volatile materials, where controlling the flow and containment of materials is essential for preventing accidents and ensuring regulatory compliance.
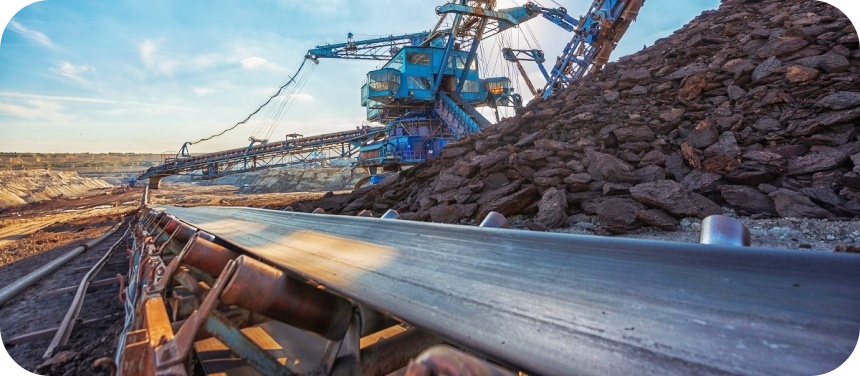
Use Cases
Conveyor belt chutes are versatile and can be used in a variety of settings to improve material handling processes. Some specific examples of their use include:
Accumulation in Shipping Areas
In shipping and distribution centers, conveyor belt chutes are used to accumulate items before they are loaded onto trucks or other transportation vehicles. This is particularly useful in high-volume operations where managing the flow of goods efficiently is crucial. Chutes can be designed to direct items into designated areas, allowing for easy sorting and loading. By accumulating items in a controlled manner, chutes help streamline the shipping process, reduce handling time, and increase overall productivity.
Conveying Items Between Floors
In multi-level facilities, conveyor belt chutes provide an efficient means of transporting materials between different floors. This is especially useful in warehouses, manufacturing plants, and retail environments where products need to be moved vertically. Chutes can be installed to connect different levels, allowing for seamless and rapid transfer of goods. This not only saves time but also reduces the need for manual lifting and carrying, which can be labor-intensive and pose safety risks.
Gravity-Driven Operations
One of the most significant advantages of conveyor belt chutes is their ability to operate using gravity. In gravity-driven operations, chutes provide a simple yet effective solution for moving materials without the need for external power sources. This is particularly beneficial in remote or off-grid locations where access to electricity is limited. By utilizing the natural force of gravity, chutes ensure that materials are transported efficiently and reliably.
Gravity-driven chutes are commonly used in industries such as agriculture, where grains and other bulk materials need to be moved from storage bins to processing equipment. The 111 simplicity of these systems allows for easy installation and minimal maintenance, making them a practical choice for a wide range of applications.
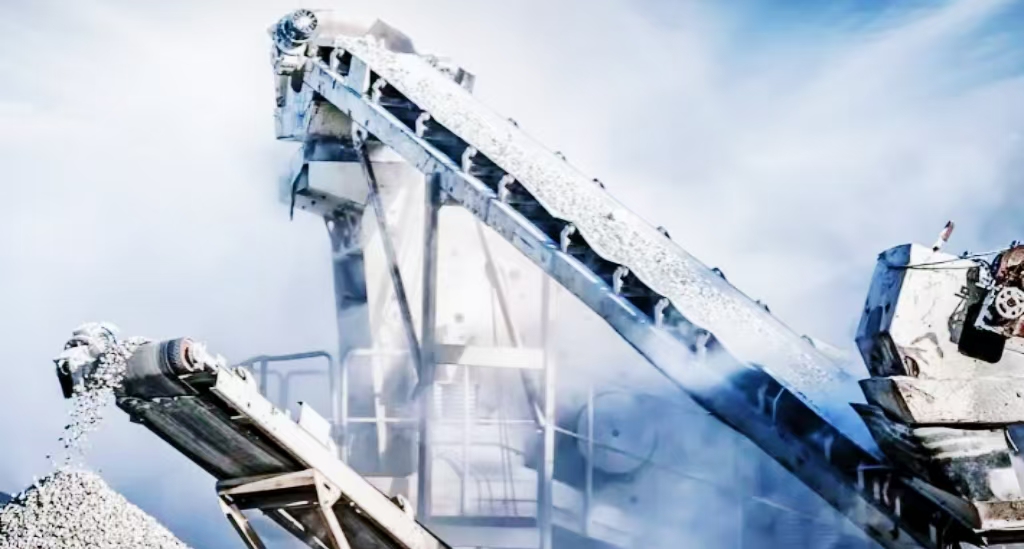
Detailed Primer on Choosing the Right Conveyor Belt Chute
A conveyor belt chute is an essential part of any conveyor system. It provides a transition zone for the bulk material from the conveyor to the downstream equipment. However, not all conveyor belt chutes are created equitably, and the type you choose can significantly affect the efficiency and effectiveness of your operations. While it may seem like a straightforward decision, many factors need to be considered to ensure the chosen chute fits your requirements adequately.
Factors to Consider When Selecting a Conveyor Belt Chute
One of the first steps towards choosing the right conveyor belt chute involves understanding the factors influencing their performance. These factors include volume, material type, angle, and speed.
Factors | Why |
---|---|
Volume | The volume of material that your system will handle is a critical factor to consider. Different chute designs can accommodate varying volumes of material. Therefore, you should analyze your operational needs to understand the quantity of moving material and select the right chute that suits your unique volume needs. |
Material Type | The type of material the conveyor belt chute will handle affects the chute's design and material. When your system handles highly abrasive or corrosive materials, opting for a chute crafted from resilient and corrosion-resistant materials will prove beneficial. |
Angle | The angle at which your conveyor belt chute will operate is another crucial factor to consider. Your chute material and design need to be in harmony with the operating angle to prevent material spillage and extend chute life. |
Speed | The speed of material movement also has a significant impact on the performance of the conveyor belt chute. Chutes designed to handle high-speed operations may differ significantly from those tailored for slow-moving materials. |
Identifying If a New or Used Conveyor Belt Chute Fits Your Needs
Investing in a new or used conveyor belt chute involves financial decisions. However, it also requires a keen understanding of your specific needs and the chute’s ability to meet these needs.
A new chute may come with the latest design improvements and materials targeted towards better operational efficiency. They often offer better longevity and resilience but inevitably come with a higher price tag.
Contrarily, a used chute might be an attractive option if budget constraints are a factor. However, potential wear and tear may affect the chute’s performance over time.
Therefore, accurately identify your operational needs, budget, and longevity requirements. In addition, consider professional consultation to ensure that the chosen conveyor belt chute, new or used, is capable of meeting your specific operational needs.
Insights into Conveyor Belt Chute Design and Functionality
The design and functionality of a conveyor belt chute play a pivotal role in material handling systems, affecting everything from the efficiency of material discharge to the lifespan of the conveyor belt itself. In this section, we delve into the specifics of conveyor discharge chutes and transfer conveyor belt chutes, exploring the essential considerations for design and the impact these components have on the overall system.
Conveyor Discharge Chute
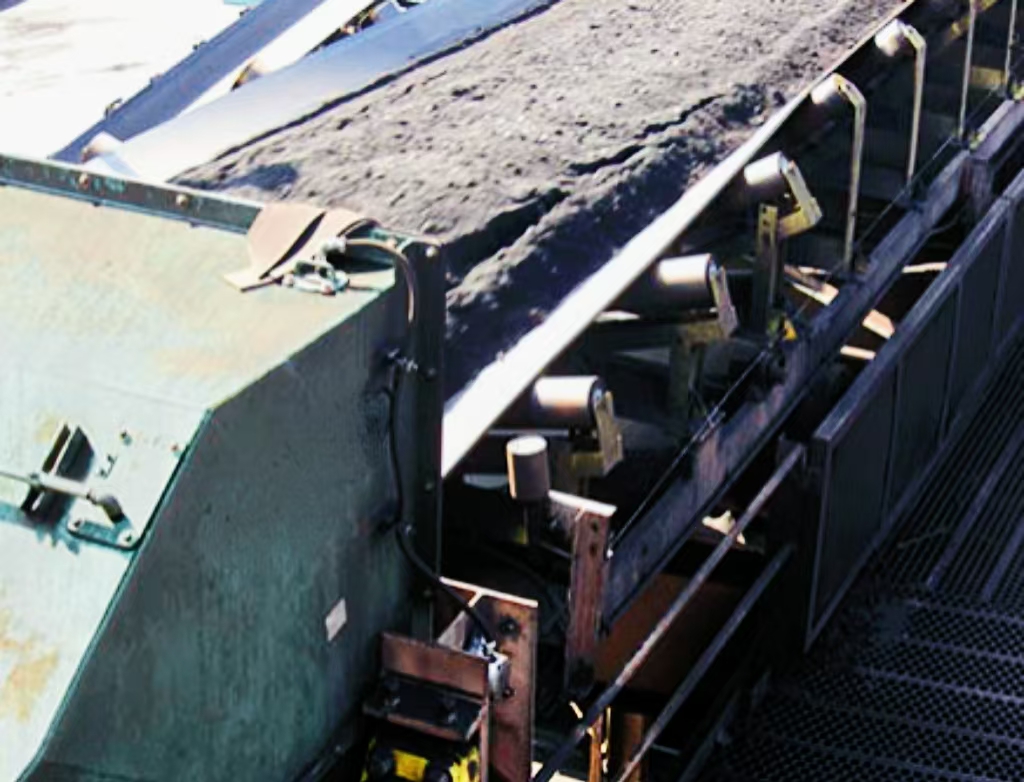
A conveyor discharge chute is integral to the controlled release of materials from the conveyor belt to the next stage in the processing or storage cycle. The design of this chute is critical for maintaining the integrity of the material and ensuring the longevity and efficiency of the conveyor system.
Design Considerations for Effective Material Discharge
When designing a conveyor discharge chute, careful attention must be paid to the physical properties of the material being handled. The chute must be designed to accommodate the size, weight, and consistency of the material, ensuring a smooth transition that minimizes blockages and material buildup. The angle and shape of the chute play critical roles in this, with too steep an angle causing excessive wear and too shallow an angle leading to blockages.
Impact on the Lifespan of Conveyor Belts and Efficiency of Material Handling
An effectively designed conveyor discharge chute minimizes conveyor belt direct impact at the discharge point, significantly reducing wear and tear on the belt. By ensuring a smooth transition, the chute helps to maintain the integrity of the belt, extending its lifespan and reducing the need for frequent replacements. Furthermore, efficient discharge chutes improve the overall material handling process by reducing bottlenecks and downtime caused by blockages and maintenance issues.
Transfer Conveyor Belt Chute Design
The transfer point between conveyor belts is another critical area that requires precise design to maintain efficiency and belt longevity. The use of transfer conveyor belt chutes at these points can significantly influence system performance.
Insights into Transfer Chute Design Manual PDF Resources
There are numerous resources available, including transfer chute design manuals in PDF format, that provide in-depth guidance on creating efficient and effective transfer chutes. These manuals often cover the principles of material flow dynamics, providing formulas and calculative methods to ascertain the best chute shape, angle, and material to ensure seamless material transfer. Consulting these resources can provide valuable insights into optimizing conveyor system performance.
Summary of Chute Design Calculations for Optimal Performance
Chute design calculations are crucial for ensuring the optimal performance of the conveyor belt chute. These calculations typically involve assessing the volume of material being handled, the speed of the conveyor belt, and the physical properties of the material. By understanding these variables, designers can determine the ideal dimensions and trajectory for the chute that will minimize wear on the system and ensure efficient material flow.
Designing an effective conveyor belt chute, whether a discharge or transfer chute, involves a detailed understanding of material dynamics and careful consideration of the conveyor system’s specific requirements. By focusing on these aspects, it is possible to achieve a design that enhances system efficiency, minimizes maintenance issues, and extends the lifespan of the conveyor belt.
Crafting Your Own DIY Conveyor Belt Chute
Building a DIY conveyor belt chute can be an efficient and cost-effective solution for small-scale operations requiring material handling improvements. Whether you’re managing a small farm, workshop, or any other operation where materials need to be moved efficiently, creating your own chute can enhance productivity. This guide provides a step-by-step approach to constructing a simple yet functional conveyor belt chute, alongside crucial safety considerations and best practices.
Step-by-Step Guide on Creating a Simple Conveyor Belt Chute
Creating a DIY conveyor belt chute involves planning, designing, sourcing materials, and assembly. Here’s how to get started:
1. Design and Planning
- Assess Your Needs: Determine the volume, type of material, and the angle at which you will be moving materials. These factors influence the design of your chute.
- Sketch Your Design: Draw a basic design of the conveyor belt chute, including dimensions and the angle of descent. Consider the entry and exit points for materials.
2. Sourcing Materials
- Structure Materials: Depending on your requirements, you can use metal (for durability and heavy materials) or wood (for lighter operations). PVC pipes or sheet metal are excellent for the chute surface.
- Fasteners and Support: Get screws, brackets, or welding equipment ready, depending on your chosen materials for assembly.
- Tools: Prepare basic tools like a saw (for wood or metal), drill, screwdrivers, and a welding machine if required.
3. Assembly
- Construct the Frame: Based on your design, cut the materials to size and assemble the frame. Ensure it’s sturdy and properly aligned.
- Install the Chute Surface: Attach the PVC pipes or sheet metal to the frame, securing it firmly to prevent any material from getting caught.
- Finishing Touches: Sand any rough edges (particularly for wood) and test the chute with a small amount of material to ensure smooth operation.
Safety Considerations and Best Practices
When building and operating your DIY conveyor belt chute, prioritize safety and efficiency with these practices:
- Wear Protective Gear: Always use gloves, eye protection, and hearing protection during construction and operation.
- Secure the Structure: Ensure the chute is firmly anchored to prevent tipping or collapsing under the weight of the materials.
- Regular Inspections: Check the chute regularly for signs of wear, loose components, and potential blockages.
- Material Handling: Avoid overloading the chute and ensure that the materials are suitable for the design parameters of your DIY chute.
- Emergency Plan: Have a plan in place in case of blockages or malfunctions. This includes having the proper tools at hand to quickly and safely address any issues.
Remember, while a DIY conveyor belt chute can be a valuable addition to your operations, its efficiency and safety are largely dependent on careful planning, quality construction, and regular maintenance. Always take the time to evaluate your system’s performance and make improvements as needed to ensure optimal functionality and safety.
Addressing Common Issues with Conveyor Belt Chutes
Impact Zone Turbulence
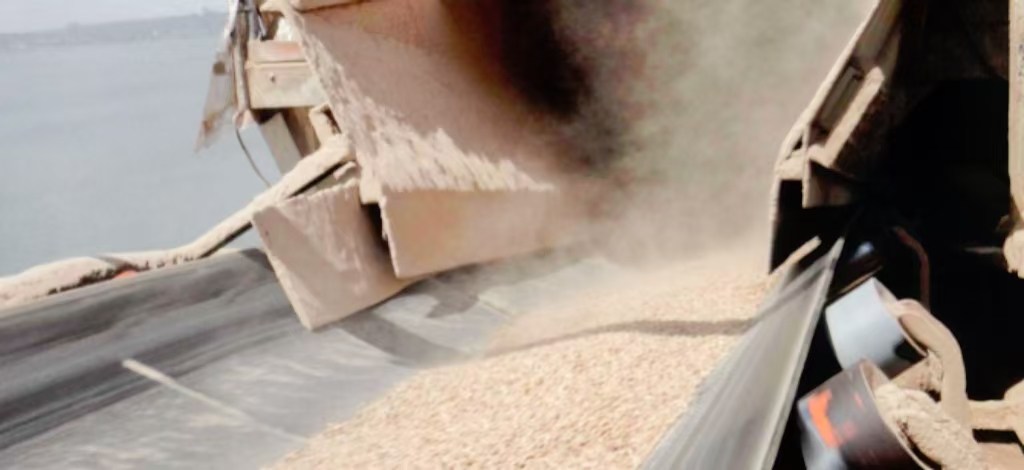
Managing Impact Zone Turbulence
One of the most significant challenges in the operation of conveyor belt chutes is managing the turbulence in impact zones. When materials free-fall from a height onto a moving belt, they can cause considerable turbulence, leading to inefficiencies and potential damage to the conveyor system.
Causes of Impact Zone Turbulence
- High-Impact Loading: Materials falling from a height can create high-impact loading zones, disrupting the smooth flow of materials. Implementing impact load zone belt support can mitigate this issue.
- Inconsistent Material Flow: Variations in the size, shape, and weight of materials can lead to uneven distribution and turbulence.
Solutions
- Impact Beds and Cradles: Installing impact beds or cradles in the impact zone can help absorb the shock of falling materials, reducing turbulence and protecting the conveyor belt.
- Inclined Chute Designs: Designing chutes with a gentle incline rather than a steep drop can help control the speed at which materials hit the conveyor belt, minimizing turbulence.
- Baffles and Deflectors: Using baffles or deflectors within the chute can direct the flow of materials, ensuring a more controlled and even distribution onto the conveyor belt.
- Soft Material Liners: Lining the chute with soft, impact-absorbing materials like rubber or urethane can cushion the impact of falling materials, reducing turbulence and wear on the belt.
Experience the best in conveyor belt technology. Reach out to us today!
Material Spillage
Minimizing Material Spillage
Material spillage is another common issue with conveyor belt chutes. Spillage can lead to material loss, increased maintenance costs, and safety hazards.
Leading Causes of Spillage
- Off-Center Loading: Materials not being centered properly on the belt can lead to spillage over the edges.
- Poor Skirtboard Seals: Ineffective seals can allow materials to escape from the sides of the chute.
- Inconsistent Material Flow: Variations in material flow can cause overflow and spillage.
Solutions
- Center Loading Mechanisms: Ensuring that materials are loaded in the center of the belt helps to distribute the load evenly and prevent spillage.
- Effective Skirtboard Seals: Installing high-quality skirtboard seals can significantly reduce spillage by keeping materials contained within the chute.
- Adjustable Kicker Plates: Using adjustable kicker plates can help direct the flow of materials and keep them centered on the belt.
- Regular Maintenance and Inspections: Conducting regular maintenance and inspections can help identify and address potential spillage issues before they become significant problems.
Wear and Tear
Extending Lifespan and Reducing Maintenance Costs
Wear and tear are inevitable in any conveyor belt chute system, but taking proactive measures can significantly extend the lifespan of the equipment and reduce maintenance costs.
Common Wear and Tear Issues
- Abrasive Materials: Materials with abrasive properties can cause significant wear on chutes and belts.
- Impact Damage: Repeated impacts from falling materials can lead to structural damage over time.
- Environmental Factors: Exposure to harsh environmental conditions can accelerate wear and tear.
Protective Measures
- Ceramic Coatings: Applying ceramic coatings to the interior surfaces of chutes can protect against abrasion and impact damage. Ceramic coatings are highly resistant to wear and can significantly extend the lifespan of the chute.
- Replaceable Wear Liners: Installing replaceable wear liners made of durable materials such as UHMW polyethylene or rubber can protect the chute structure and reduce maintenance costs. These liners can be easily replaced when worn out, ensuring continuous protection.
- Regular Inspections and Maintenance: Implementing a regular inspection and maintenance schedule can help identify wear and tear issues early, allowing for timely repairs or replacements before major damage occurs.
- Environmental Controls: Implementing measures to protect the chutes from harsh environmental conditions, such as installing covers or enclosures, can help reduce wear and tear due to weather and other external factors.
Selecting the Right Conveyor Belt Chute Manufacturers
Choosing the most suitable conveyor belt chute manufacturer for your needs is a decision that greatly impacts the efficiency, reliability, and overall success of your material handling operations. With several manufacturers in the market, it can be challenging to identify the one that perfectly aligns with your project’s requirements. This section dives into the essential criteria that should guide your selection process, ensuring your partnership with a conveyor belt chute manufacturer meets and exceeds your expectations.
Criteria to Select the Best Conveyor Belt Chute Manufacturer for Your Needs
When selecting a conveyor belt chute manufacturer, several critical factors come into play. Prioritizing these criteria helps ensure that you partner with a manufacturer capable of delivering high-quality solutions tailored to your specific operational needs.
Experience and Reputation
The experience of a manufacturer in designing and producing conveyor belt chutes is paramount. A long-standing history in the industry often translates to a depth of knowledge and expertise, enabling the manufacturer to handle a wide range of challenges and operational needs. Additionally, a reputable manufacturer is more likely to provide reliable and high-quality chutes that can significantly enhance the efficiency of your conveyor systems.
- How to Assess: Look for manufacturers with several years in the industry, and be sure to review testimonials, case studies, and client references.
Customization Capabilities
Every material handling operation is unique, necessitating a customized approach to conveyor belt chute design. The best manufacturers offer the ability to tailor chutes specifically to your operational needs, considering factors such as material type, volume, speed, and the operating environment.
- How to Assess: Discuss your specific needs with potential manufacturers and inquire about their process for designing and fabricating custom solutions.
Quality of Materials and Construction
The durability and longevity of a conveyor belt chute significantly depend on the quality of materials used and the craftsmanship of its construction. High-quality materials and superior construction not only ensure the chute’s durability but also reduce the need for frequent repairs and replacements.
- How to Assess: Request details on the types of materials used and the manufacturing processes. If possible, conduct site visits to inspect the manufacturer’s production quality firsthand.
After-Sales Support and Services
After-sales support is crucial for maintaining the performance and longevity of your conveyor belt chute. A manufacturer that offers comprehensive after-sales services, including installation support, maintenance, and repair services, demonstrates a commitment to customer satisfaction and product reliability.
- How to Assess: Inquire about the after-sales services offered, including warranty terms, maintenance contracts, and available support channels.
Cost-Effectiveness
While the initial cost is an important consideration, focusing on the overall value and return on investment is more prudent. Evaluate not only the purchase price but also the operating and maintenance costs over the chute’s lifecycle.
- How to Assess: Request detailed quotes that include not only the purchasing cost but also projected maintenance and operational expenses. Compare these against the expected benefits and efficiencies gained from the chute.
By thoroughly assessing these criteria, you can choose a conveyor belt chute manufacturer that not only meets your operational needs but also contributes to the efficiency, reliability, and long-term success of your material handling operations. Remember, the right partner is one that understands your needs and offers solutions that align with your objectives, budget, and operational requirements.
Material Options, Installation, and Maintenance of Conveyor Belt Chute
The efficiency, durability, and longevity of a conveyor belt chute heavily depend on the materials used, its installation process, and the subsequent maintenance procedures. This section presents an overview of the various chute liner options available and provides guidance on the installation and maintenance of conveyor belt chutes.
Conveyor Belt Chute Liners
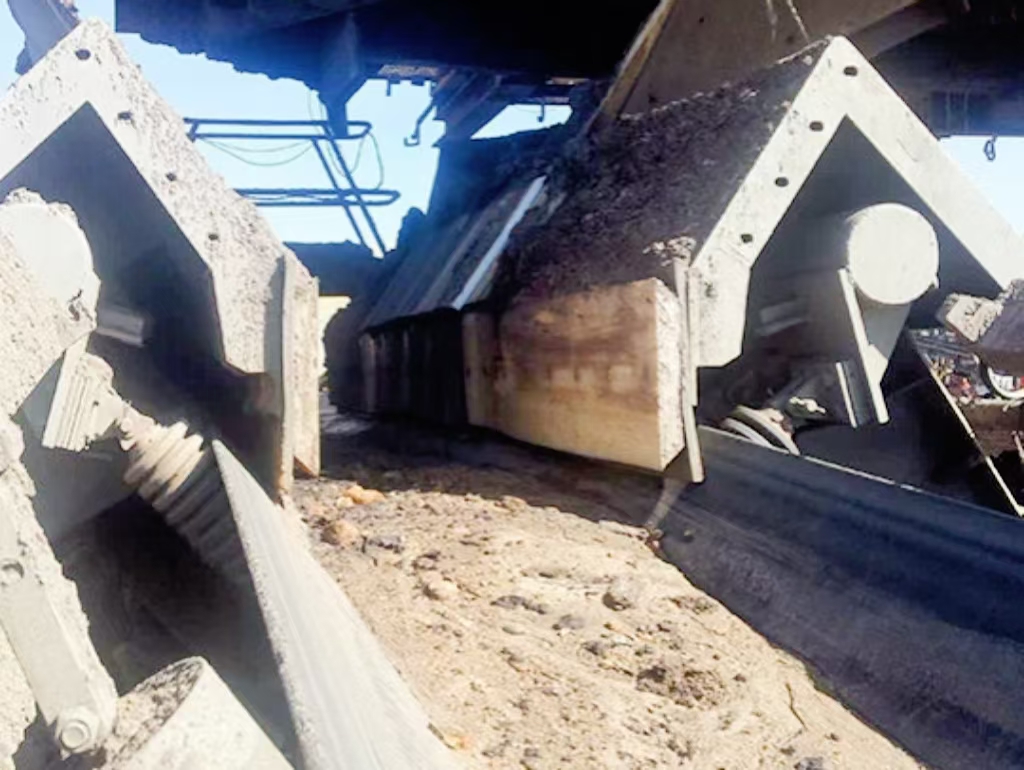
The liners within a conveyor belt chute play a significant role in prolonging its lifespan while ensuring the smooth conveying of materials. When incorporated correctly, these liners resist wear, reduce friction, and minimize material build-up.
Importance of Chute Liners in Prolonging Chute Lifespan
Chute liners create a protective layer between the material being transported and the chute itself, reducing direct impact and friction that can cause wear and tear. By properly installing and maintaining chute liners, it’s possible to substantially extend the lifespan of a conveyor belt chute, decrease downtime, and increase the overall efficiency of material handling operations.
Options in Materials: Rubber, Metallic, and Ceramic Liners
There are numerous materials available for chute liners, each with its strengths and suitable applications:
- Rubber Liners: Rubber liners are ideal for applications where impact is moderate, and corrosion is a concern. They are flexible, resistant to abrasion, and can dampen impact effectively, offering extended service life and noise reduction.
- Metallic Liners: Metallic liners, such as those made of hardened steel rollers or other hardened alloys, are durable and ideal for high-impact and high-wear applications. They provide excellent structural strength but may suffer from corrosion, which can be mitigated with appropriate coatings.
- Ceramic Liners: Ceramic liners, often used in high wear and high temperature environments, are highly resistant to abrasion. They outperform both rubber and metallic liners in terms of overall lifespan and wear resistance, but their brittleness may render them less effective in high-impact scenarios.
Conveyor Belt Chute Installation and Maintenance
The proper installation and consistent maintenance of a conveyor belt chute significantly contribute to its overall performance and lifespan.
Guidance on the Installation Process for Various Types of Chutes
- Inspection: Before installation, it is fundamental to inspect the conveyor belt chute and its components for any shipping damages or defects.
- Positioning: Carefully position the chute between the conveyor belts. The entrance and exit points should align with the belts to prevent material spillage.
- Securing: Secure the chute using appropriate fixation methods such as bolts or welds. It’s important to maintain the right angle and direction in accordance with the conveying system’s design.
It’s recommended to consult a professional or follow the manufacturer’s guidelines to ensure a seamless installation process.
Maintenance Tips to Ensure Longevity and Efficiency
Proactive and regular maintenance is key to ensuring the optimal performance and longevity of a conveyor belt chute.
- Regular Inspections: These can uncover potential issues ranging from damage to the chute lining and mechanical parts, to blockage risks.
- Cleaning: Regularly clean the chute to prevent material buildup which could lead to blockages and increased wear.
- Liner Replacement: Monitor the condition of chute liners regularly, replacing them when signs of significant wear appear.
- System Adjustments: Adjust conveyor belt tension, chute alignment, and other operational parameters as necessary to ensure smooth operation.
By understanding the importance of materials, installation, and maintenance, you can optimize the performance and lifespan of your conveyor belt chute, ultimately boosting the productivity and efficiency of your material handling operations.
Conveyor Belt Chute Transfers and Transfer Tower Innovation
Transfer towers and advanced chute technology play an integral role in enhancing the performance, efficiency, and safety of conveyor belt systems. These specialized structures and devices facilitate the seamless transfer of bulk materials from one bulk conveyor belt to another. This section will provide an understanding of how transfer towers integrate with conveyor belt systems and delve into the latest innovations in conveyor belt chute technology.
The Fusion of Transfer Towers and Conveyor Belt Chutes
Transfer towers serve as a crucial link in any material handling process involving a conveyor belt system. They integrate with conveyor belt chutes to ensure a smooth and efficient transfer of materials between belts with different orientations, such as from a parallel belt to a perpendicular one, or from an inclined belt to a flat one.
A well-executed integration of a transfer tower and conveyor belt chute can significantly reduce material spillage, optimize material flow, reduce belt wear, and limit the material’s impact on the chute. This integration helps improve productivity and maintains the quality of materials being transported.
How it works:
- The transfer tower houses the conveyor belt chute and provides the required height for the chute to efficiently guide materials from the discharge end of the input conveyor belt to the receiving area of the output conveyor belt.
- As the material reaches the end of the input conveyor, it drops into the transfer chute housed within the tower.
- The conveyor belt chute guides the material to the receiving belt. It has an extended and sloped design, leveraging gravity to direct material flow while minimizing impact force.
- Once the material exits the chute, it lands on the output conveyor belt that takes the material to its next destination.
With such an efficient design, the system ensures minimal material loss and thus increases the overall efficiency of the material handling operations.
Innovative Designs in Conveyor Belt Chute Technology
The material handling industry is witnessing significant advancements in transfer chute technology. These innovations aim to improve the longevity and efficiency of conveyor belt chutes while reducing maintenance requirements and downtime.
- Smart Chute Designs: These make use of computational analyses and simulations (like Discrete Element Method) in the design phase to predict material flow patterns. This allows for optimized chute geometry that reduces wear and tear, mitigates blockages, and decreases dust emission.
- Wear-Resistant Liners: Novel liner materials are now being used, which are highly resistant to abrasion and corrosion. These enhance the chute’s service life, reduce maintenance costs, increase operational uptime, and lower the total cost of ownership.
- Modular Chute Systems: Modular design concepts allow for easier installation, replacement, and maintenance. These chutes can be preassembled off-site, leading to reduced installation times and less disruption to ongoing operations.
- Flow Control Devices: The inclusion of innovative flow control devices, such as impact pads and flow diverters, help maintain a steady and controlled flow of materials, reducing impact on the conveyor belt chute and thus extending its lifespan.
These innovations in conveyor belt chute technology are enabling industries to improve their productivity, reduce overhead costs, and enhance the longevity and efficiency of their material handling systems. It is recommended to explore and integrate these advanced solutions to optimize the performance of your conveyor belt chute systems further.
Conveyor Belt Chute Advanced Topics: Design Calculations and Manuals
The advanced intricacies involved in the design of a conveyor belt chute demand attention to detail and precision in calculations to ensure the system’s efficiency, safety, and durability. Exploring the complexities of these calculations and understanding the value of comprehensive design manuals is essential for engineers and designers in the field.
Chute Design Calculations
Chute design calculations are a crucial part of creating an efficient conveyor belt chute. These calculations can be quite complex, involving a variety of factors such as the angle of repose of the material, the speed of the belt, volumetric throughput, the coefficient of friction between the material and the chute surface, and impact force calculations.
Examination of the Complexities of Chute Design Calculations
The design process must consider:
- Material Flow: The flow characteristics of the material itself, including the density, particle size distribution, and moisture content, must be examined. This analysis dictates aspects like chute slope and shape to ensure a blockage-free operation.
- Impact and Wear: High-speed impact of materials against the chute walls can lead to excessive wear. Calculations must accommodate the selection of materials and thickness for lining the chute to withstand abrasion and impact.
- Velocity Control: Ensuring that the speed of material flow is controlled to prevent overflow at the discharge point requires accurate calculation of chute decline angles and flow resistance.
- Dust and Spillage Prevention: The containment of dust and minimization of spillage are also concerns that need to be addressed through proper design calculations, often influencing the incorporation of skirts or seals.
Enhance your operations with our high-performance conveyor belts. Inquire now!
Importance of Accurate Calculations in the Design Stage
Accurate chute design calculations are paramount for:
- Optimizing the passage of bulk materials while minimizing blockages and spillage.
- Reducing conveyor belt wear extends the life of both the chute and the conveyor belt, enhancing the overall longevity of the equipment.
- Increasing efficiency by ensuring a smooth material flow, leading to higher throughput.
- Improving safety by minimizing dust generation and potential hazards associated with spillage.
Transfer Conveyor Belt Chute Design Manual PDF
A comprehensive conveyor belt chute design manual is an invaluable tool for the field’s engineers and designers. Such a manual serves as a guideline for best practices, detailed design calculations, material considerations, and safety directives.
Highlighting the Value of Comprehensive Design Manuals
These manuals typically include:
- Step-by-Step Design Processes: They provide a systematic approach to designing conveyor belt chutes from preliminary calculations to detailed engineering drawings.
- Case Studies and Examples: Practical examples and success stories can inform designers about common pitfalls and successful innovation strategies in chute design.
- Material Testing Procedures: To ensure materials meet the operational requirements, design manuals often contain methods for testing and validating material properties.
- Maintenance Guides: Regular maintenance is critical for operational efficiency, so these manuals also include schedules and recommendations for preventative maintenance and troubleshooting.
The Transfer Conveyor Belt Chute Design Manual PDF becomes a fundamental document, aiding in training new engineers, providing a reference for experienced designers, and ensuring consistency in the planning and modification of conveyor belt chutes. Emphasizing the manual’s role and applicability encourages standardization of design principles and helps in achieving the operational excellence required in the handling of bulk materials.
FAQs about Conveyor Belt Chute
A chute in conveyors is a critical component designed to guide materials from the end of the conveyor belt, or from one conveyor belt to another, in a controlled manner. It functions as a passageway for bulk materials or individual items, facilitating smooth and efficient transfer or discharge without causing spillage or damage. Conveyor chutes are made from various materials such as steel, rubber, or composite materials, tailored to the properties of the conveyed material and the operating environment. Their design, including shape, angle, and surface, is optimized to prevent clogging and ensure a steady flow of materials. Chutes are integral to material handling systems in industries like mining, agriculture, and manufacturing, where they contribute to streamlined operations and minimized material handling issues.
A dribble chute is a specialized type of chute designed to catch and redirect spilled material back onto the conveyor belt or into the main material flow. This feature is particularly important in material handling systems where spillage from the main conveyor can lead to operational inefficiencies, safety hazards, and additional clean-up costs. Dribble chutes are strategically placed beneath conveyor belts or at points where spillage is likely, such as transfer points or loading zones. By capturing dribbled material, these chutes play a crucial role in maintaining a clean and efficient material handling environment. They are designed with consideration for easy maintenance and cleaning, often incorporating features such as easy access for clearing blockages or collecting accumulated material.
The primary function of a chute in a conveyor system is to ensure the controlled and efficient transfer of bulk materials or individual items between different stages of a processing system or from one conveyor belt to another. Chutes aim to minimize material spillage, prevent damage to conveyed products, and ensure a consistent material flow rate. A well-designed chute optimizes the direction, speed, and volume of material flow, contributing to operational efficiency and reducing the need for manual intervention or rework. In addition to these core functions, chutes also play a critical role in distributing material evenly, regulating the discharge of materials, and, in specific configurations like dribble chutes, capturing and re-integrating spilled material. Ultimately, the function of a chute is to enhance the productivity and safety of material handling operations.
A transfer chute is a specifically engineered chute designed for the seamless transfer of bulk materials between conveyors, or from conveyors to storage areas, processing equipment, or final discharge points. Transfer chutes are essential components in material handling systems, ensuring the smooth, efficient, and controlled flow of materials with minimal spillage or blockages. These chutes are custom-designed based on the characteristics of the material being handled, such as size, density, and abrasiveness, as well as the transfer distance and height. Key considerations in transfer chute design include minimizing the impact force of falling materials, controlling the velocity of material flow, and managing the direction of material discharge. Effective transfer chute design results in improved system efficiency, reduced maintenance requirements, and enhanced operational safety.
A chute and a hopper are both components used in material handling systems, but they serve different purposes. A chute is typically an inclined or vertical passage through which materials move by gravity or with the assistance of conveyor belts. Its main function is to direct the flow of materials from one point to another, often from a higher to a lower elevation.
On the other hand, a hopper is a container used to hold and release materials in a controlled manner. It usually has a wider opening at the top and a narrower opening at the bottom, allowing for the gradual discharge of materials. Hoppers are often used for storage and controlled feeding of materials into a process or onto a conveyor belt.
The primary aim of installing a transfer chute on a conveyor belt is to enhance the efficiency and safety of material flow. Transfer chutes are designed to control the direction and speed of material as it moves from one conveyor to another or from a conveyor to a different processing stage. By doing so, they help to minimize spillage, reduce wear and tear on the conveyor system, and prevent blockages that could disrupt operations.
Transfer chutes also play a crucial role in reducing impact zone turbulence when materials free-fall onto moving belts. This helps in maintaining a consistent and centered flow of materials, which is essential for optimizing the performance of the conveyor system. Additionally, transfer chutes can improve the overall safety of the operation by containing dust and reducing the risk of accidents caused by material overflow or spillage.
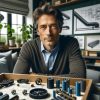
Jordan Smith, a seasoned professional with over 20 years of experience in the conveyor system industry. Jordan’s expertise lies in providing comprehensive solutions for conveyor rollers, belts, and accessories, catering to a wide range of industrial needs. From initial design and configuration to installation and meticulous troubleshooting, Jordan is adept at handling all aspects of conveyor system management. Whether you’re looking to upgrade your production line with efficient conveyor belts, require custom conveyor rollers for specific operations, or need expert advice on selecting the right conveyor accessories for your facility, Jordan is your reliable consultant. For any inquiries or assistance with conveyor system optimization, Jordan is available to share his wealth of knowledge and experience. Feel free to reach out at any time for professional guidance on all matters related to conveyor rollers, belts, and accessories.