What Material is a Conveyor Belt Made Of: A Guide
Conveyor belts are essential components in a variety of industries, including manufacturing, mining, and recycling. Their widespread use underscores their importance in efficiently transporting materials from one point to another. Understanding what material is a conveyor belt made of is crucial for selecting the right belt for specific applications. Conveyor belts are made from several key materials, each chosen for its unique properties and suitability for different environments. Common materials include rubber, polyurethane, fabric, and metal. Each material offers distinct advantages, such as durability, resistance to heat and chemicals, and flexibility. Knowing what material is a conveyor belt made of helps in optimizing performance and longevity in industrial operations.
Conveyor Belt Material Properties: What Material is a Conveyor Belt Made Of
Conveyor belts are integral to various industrial applications, and understanding what material is a conveyor belt made of is essential for optimizing their performance. The choice of material directly impacts the belt’s strength, durability, resistance to heat, chemicals, and wear. This section delves into these critical material properties and explores how they influence the selection of conveyor belt materials for specific applications.
Strength
One of the most crucial properties of conveyor belt materials is strength. Conveyor belts must endure substantial loads and stresses without breaking or deforming. The tensile strength of a material indicates its ability to withstand pulling forces. For instance, steel-reinforced belts offer exceptional strength, making them ideal for heavy-duty applications like mining and bulk material handling. Similarly, high-strength synthetic materials such as polyester and nylon provide excellent load-bearing capabilities, ensuring the conveyor belt can transport heavy items without stretching or tearing.
Durability
Durability is another vital property when considering what material is a conveyor belt made of. Conveyor belts are often subjected to harsh working conditions, including continuous operation, abrasive materials, and varying temperatures. Rubber is a common material known for its durability and resilience. It can withstand significant wear and tear, making it suitable for general-purpose conveyor belts used in manufacturing and distribution. Polyurethane is also recognized for its durability, offering a long service life and resistance to cuts, punctures, and abrasions. This makes it an excellent choice for food processing and packaging industries.
Resistance to Heat
Heat resistance is a critical factor in selecting conveyor belt materials for high-temperature environments. Materials that can withstand elevated temperatures without degrading are essential in industries such as metalworking, glass manufacturing, and food processing. Teflon-coated fiberglass belts are an example of materials with high heat resistance, capable of operating in temperatures up to 260°C (500°F). Similarly, silicone-based belts provide excellent heat resistance and are commonly used in bakery and other food-related applications where exposure to high temperatures is frequent.
Resistance to Chemicals
Chemical resistance is crucial for conveyor belts used in environments where they come into contact with various chemicals, oils, and solvents. Understanding what material is a conveyor belt made of helps in choosing a belt that can resist chemical corrosion and degradation. PVC (polyvinyl chloride) belts are known for their chemical resistance, making them suitable for applications in the chemical and pharmaceutical industries. Polyurethane belts also offer good chemical resistance and are widely used in food processing, packaging, and printing industries where exposure to cleaning agents and other chemicals is common.
Resistance to Wear
Wear resistance is essential for conveyor belts that handle abrasive materials or are subjected to constant friction. Materials with high wear resistance ensure a longer lifespan and reduce the need for frequent replacements. Natural rubber and nitrile rubber are examples of materials with excellent wear resistance, commonly used in quarrying, mining, and construction industries. These materials can handle rough and abrasive loads without significant wear, ensuring continuous operation and reducing downtime.
Influence of Material Properties on Application
The properties of conveyor belt materials significantly influence their suitability for specific applications. For instance:
- Mining Industry: In mining, belts need to handle heavy loads and abrasive materials. Steel-reinforced rubber belts are preferred due to their high strength and wear resistance.
- Food Processing: In the food industry, belts must resist high temperatures and chemicals used in cleaning. Teflon-coated fiberglass and silicone-based belts are ideal due to their heat and chemical resistance.
- Pharmaceutical Industry: PVC belts are commonly used in the pharmaceutical sector for their excellent chemical resistance and ability to maintain hygiene standards.
- Packaging: Polyurethane belts are favored in packaging for their durability and resistance to cuts and abrasions.
- Manufacturing: For general manufacturing applications, polyester and nylon belts offer a good balance of strength, durability, and flexibility, suitable for handling various materials and conditions.
Understanding what material is a conveyor belt made of involves assessing the critical properties of strength, durability, resistance to heat, chemicals, and wear. Each of these properties plays a vital role in determining the belt’s performance and suitability for different industrial applications. By carefully selecting the appropriate material based on these properties, industries can ensure efficient, reliable, and long-lasting conveyor belt operation.
Materials Used in Conveyor Belt Construction: What Material is a Conveyor Belt Made Of
Conveyor belts are constructed from a variety of materials, each selected for its unique properties and suitability for specific applications. Understanding what material is a conveyor belt made of is essential for optimizing performance and ensuring durability. This section explores the different materials used in conveyor belt construction, highlighting their characteristics and applications.
Rubber Conveyor Belt Material
Rubber is one of the most traditional and widely used materials in conveyor belt construction. Known for its flexibility, durability, and resistance to wear and tear, rubber is ideal for many industrial applications. There are different types of rubber used in conveyor belts, each offering specific benefits:
- Natural Rubber: Known for its excellent elasticity and resilience, natural rubber is suitable for applications where flexibility and resistance to impact are crucial.
- SBR (Styrene-Butadiene Rubber): This synthetic rubber provides good abrasion resistance and is commonly used in general-purpose conveyor belts.
- Nitrile Rubber (NBR): Nitrile rubber offers superior resistance to oils and chemicals, making it ideal for applications in the chemical and food industries.
- EPDM (Ethylene Propylene Diene Monomer): EPDM is resistant to heat, weather, and ozone, making it suitable for outdoor and high-temperature applications.
- Neoprene: This synthetic rubber is known for its chemical resistance and durability, often used in applications involving exposure to chemicals and oils.
Fabric Conveyor Belts
Fabric materials are commonly used in conveyor belt construction due to their flexibility, strength, and lightweight properties. Different types of fabrics enhance the belt’s performance for specific applications:
- Polyester: Known for its excellent strength and flexibility, polyester is widely used in general-purpose conveyor belts. It is resistant to stretching and maintains its shape under load.
- Nylon: Nylon offers high tensile strength and resistance to abrasion, making it suitable for heavy-duty applications. It is also resistant to impact and can handle high loads.
- Cotton: Cotton fabric is used in conveyor belts for light-duty applications where flexibility and low cost are essential. It is commonly used in agricultural and food processing industries.
- Kevlar: Known for its high strength and resistance to impact, Kevlar is used in conveyor belts for extreme conditions, such as mining and heavy industrial applications.
- Aramid: Aramid fibers offer excellent heat resistance and strength, making them suitable for high-temperature applications and environments where durability is critical.
Metal Conveyor Belts
Metal materials are used in conveyor belt construction when strength, durability, and heat resistance are required. Common metals used include:
- Stainless Steel: Stainless steel belts are known for their corrosion resistance and durability, making them ideal for food processing, pharmaceutical, and chemical industries.
- Carbon Steel: Carbon steel belts offer high strength and wear resistance, suitable for heavy-duty applications such as mining and bulk material handling.
- Aluminum: Lightweight and resistant to corrosion, aluminum belts are used in applications where weight is a concern, such as in the aerospace industry.
- Inconel: This nickel-chromium alloy is used in high-temperature applications due to its excellent heat resistance and durability.
- Titanium: Titanium belts are lightweight, strong, and resistant to corrosion, making them ideal for specialized applications in the aerospace and medical industries.
Understanding what material is a conveyor belt made of is crucial for selecting the right belt for specific applications. Rubber, polyurethane, fabric, and metal each offer unique properties that enhance the belt’s performance and longevity. By carefully considering the material properties and application requirements, industries can ensure efficient, reliable, and long-lasting conveyor belt operation.
Why is the Surface of Conveyor Belts Made Rough: What Material is a Conveyor Belt Made Of
The surface texture of conveyor belts plays a crucial role in their functionality and efficiency. Understanding what material is a conveyor belt made of includes recognizing why the surface is often designed to be rough. This section explores the importance of surface texture in conveyor belts, providing examples and discussing how a rough surface improves traction and reduces slippage.
Importance of Surface Texture in Conveyor Belts
The texture of a conveyor belt’s surface significantly impacts its performance in various applications. A rough surface is often preferred for several reasons:
- Improved Traction: A rough surface enhances the grip between the conveyor belt and the materials being transported. This is particularly important in industries where slippery materials are handled, such as in food processing or packaging. For example, rubber belts with textured surfaces provide better traction for moving produce, reducing the chances of items slipping off the belt.
- Reduced Slippage: In many industrial processes, materials need to be transported at various angles and speeds. A rough surface minimizes the slippage of items, ensuring they stay in place during transit. For instance, in the mining industry, conveyor belts with a rough surface are used to transport rocks and minerals up steep inclines without losing material.
- Enhanced Material Handling: Certain materials, such as grains or powders, can be difficult to transport due to their tendency to slide or roll. Conveyor belts with rough surfaces can handle these materials more effectively, ensuring a steady flow and reducing material loss. In agriculture, rough-textured belts are used to transport grains efficiently.
- Improved Safety: A rough surface can also enhance safety in the workplace. It reduces the risk of materials falling off the belt, which can lead to accidents or injuries. For example, in the logistics industry, rough conveyor belts are used in sorting facilities to ensure packages remain secure during high-speed sorting processes.
- Versatility in Applications: Rough surfaces make conveyor belts versatile, allowing them to be used in a wide range of applications. Whether it’s transporting heavy-duty materials in construction or delicate items in electronics manufacturing, a rough surface can adapt to various needs. For instance, in the automotive industry, rough conveyor belts are used to move car parts securely during assembly.
How a Rough Surface Improves Traction and Reduces Slippage
The effectiveness of a conveyor belt is largely determined by its ability to maintain traction and prevent slippage. Here’s how a rough surface contributes to these aspects:
- Increased Friction: A rough surface increases the friction between the conveyor belt and the items being transported. This friction is essential for keeping materials in place, especially when the belt is moving at high speeds or at an incline. Understanding what material is a conveyor belt made of, such as rubber or polyurethane, helps in selecting the right texture for the required friction levels.
- Grip Enhancements: Different textures, such as diamond-patterned or grooved surfaces, provide additional grip. These patterns are designed to interact with the materials being transported, ensuring they do not slip or move unexpectedly. For example, grooved rubber belts are commonly used in recycling plants to transport various waste materials securely.
- Material Compatibility: The roughness of the surface can be tailored to match the material being transported. For instance, belts used in the packaging industry might have a moderate rough texture to grip cardboard boxes without damaging them, whereas belts in the construction industry might have a more aggressive texture to handle heavy bricks or stones.
- Angle of Inclination: Conveyor belts with rough surfaces are particularly effective on inclined planes. The added traction from the rough texture prevents materials from sliding back, ensuring efficient upward or downward movement. In the food industry, incline conveyors with rough surfaces are used to transport products to different processing levels.
- Environmental Conditions: Rough surfaces are also beneficial in environments where moisture, dust, or other contaminants might affect belt performance. For example, in outdoor applications such as in mining or construction, rough-textured belts can maintain their grip even when exposed to rain or dust, reducing the risk of slippage and ensuring continuous operation.
Understanding what material is a conveyor belt made of includes recognizing the importance of surface texture. A rough surface on conveyor belts plays a critical role in improving traction, reducing slippage, enhancing material handling, improving safety, and increasing versatility across various applications. By increasing friction and providing better grip, rough-textured belts ensure efficient, reliable, and safe transport of materials in diverse industrial environments.
Conveyor Belt Material Selection: What Material is a Conveyor Belt Made Of
Selecting the right material for a conveyor belt is crucial for ensuring its efficiency, durability, and suitability for the intended application. Understanding what material is a conveyor belt made of involves evaluating several factors, including temperature range, chemical exposure, and impact resistance. This section provides detailed guidelines for selecting the appropriate conveyor belt material and highlights specific considerations for various applications.
Guidelines for Selecting Conveyor Belt Material
When selecting the material for a conveyor belt, several key factors must be considered to ensure optimal performance and longevity:
- Application Requirements: The first step is to understand the specific requirements of the application. Consider the type of materials being transported, the operating environment, and the desired lifespan of the conveyor belt. For instance, a conveyor belt used in a food processing plant will have different requirements compared to one used in a quarry.
- Temperature Range: Conveyor belts operate in a wide range of temperatures. It is essential to choose a material that can withstand the specific temperature conditions of the application. For high-temperature environments, materials like Teflon-coated fiberglass or silicone are ideal, while for low-temperature settings, polyurethane belts are more suitable.
- Chemical Exposure: In applications where the conveyor belt is exposed to chemicals, oils, or solvents, selecting a material with good chemical resistance is crucial. Materials like PVC and polyurethane offer excellent resistance to chemicals, making them ideal for industries such as pharmaceuticals and food processing.
- Impact Resistance: The conveyor belt must be able to withstand the impact of the materials being transported, especially in heavy-duty applications. Materials like rubber and reinforced steel provide high impact resistance, making them suitable for mining and bulk material handling.
- Wear and Abrasion Resistance: For applications involving abrasive materials, choosing a conveyor belt material with high wear resistance is essential. Rubber and certain synthetic materials like nitrile rubber are known for their durability and resistance to abrasion, ensuring a longer lifespan.
Considerations for Conveyor Belt Material Selection
Temperature Range
The operating temperature of the environment where the conveyor belt will be used is a critical consideration.
- Teflon-Coated Fiberglass: Ideal for high-temperature applications, such as baking and food processing, where the belt needs to withstand temperatures up to 260°C (500°F).
- Silicone: Suitable for environments with fluctuating temperatures, commonly used in food and pharmaceutical industries due to its heat resistance and hygienic properties.
- Polyurethane: Excellent for low-temperature applications, such as refrigerated environments and cold storage, maintaining flexibility and performance in cold conditions.
- EPDM Rubber: Provides good heat resistance and is used in outdoor and high-temperature industrial applications.
- PVC: Works well in moderate temperature ranges and is often used in general manufacturing and packaging industries.
Chemical Exposure
Exposure to chemicals, oils, and solvents can degrade certain materials.
- PVC: Highly resistant to a wide range of chemicals, making it suitable for pharmaceutical and chemical industries.
- Polyurethane: Offers good resistance to oils and solvents, ideal for food processing and packaging applications.
- Nitrile Rubber: Known for its excellent oil and chemical resistance, used in automotive and industrial applications.
- Neoprene: Provides resistance to a variety of chemicals and oils, commonly used in manufacturing and industrial settings.
- Stainless Steel: Resistant to corrosive chemicals, making it suitable for harsh industrial environments and food processing.
Impact Resistance
For applications where the conveyor belt must endure heavy impacts, selecting a material with high impact resistance is essential.
- Reinforced Rubber: Used in mining and bulk material handling, providing excellent impact resistance and durability.
- Steel Cord Belts: Ideal for heavy-duty applications, such as mining and construction, where high strength and impact resistance are required.
- Kevlar-Reinforced Belts: Used in extreme conditions where high impact and tear resistance are needed, such as in the aerospace industry.
- Natural Rubber: Offers good impact resistance and flexibility, suitable for general industrial applications.
- Nylon Fabric Belts: Provide high tensile strength and impact resistance, commonly used in heavy-duty material handling.
Understanding what material is a conveyor belt made of involves carefully evaluating the application requirements, temperature range, chemical exposure, and impact resistance. By considering these factors, industries can select the appropriate material to ensure optimal performance, durability, and safety. Whether it’s for high-temperature environments, chemical exposure, or heavy-impact applications, choosing the right conveyor belt material is essential for efficient and reliable operation.
Leading Conveyor Belt Manufacturers: What Material is a Conveyor Belt Made Of
Selecting the right conveyor belt involves not only understanding what material is a conveyor belt made of but also knowing the leading manufacturers who provide high-quality products. The USA is home to several top conveyor belt manufacturers known for their innovation, quality, and extensive product offerings. This section introduces some of the major conveyor belt manufacturers in the USA, highlighting their specialties and contributions to the conveyor belt market.
Major Conveyor Belt Manufacturers in the USA
The USA hosts a variety of conveyor belt manufacturers that cater to different industrial needs. These companies offer a wide range of conveyor belts made from various materials, designed to meet the specific requirements of diverse applications. Here are some of the leading conveyor belt manufacturers in the USA:
1. Continental AG
Profile: Continental AG is a global leader in the manufacturing of conveyor belts, known for their advanced technology and high-quality products. The company offers a wide range of conveyor belts made from different materials, including rubber, polyurethane, and fabric, illustrating how are conveyor belts made using various material compositions to meet diverse industrial needs.
Specialties:
- Rubber Conveyor Belts: Continental’s rubber belts are renowned for their durability and resistance to wear and tear, making them ideal for heavy-duty applications.
- Heat-Resistant Belts: They offer conveyor belts that can withstand high temperatures, suitable for industries such as metalworking and food processing.
- Custom Solutions: Continental provides custom-engineered conveyor belts tailored to specific industrial needs, ensuring optimal performance.
2. Fenner Dunlop
Profile: Fenner Dunlop is a prominent name in the conveyor belt industry, known for its extensive range of high-performance conveyor belts. The company has a strong focus on innovation and quality, offering products that cater to various industrial applications.
Specialties:
- Mining and Quarrying Belts: Fenner Dunlop’s belts are designed to handle the demanding conditions of mining and quarrying, providing excellent durability and strength.
- Energy-Efficient Belts: They offer energy-efficient conveyor belts that help reduce operational costs by minimizing energy consumption.
- Fire-Resistant Belts: Fenner Dunlop’s fire-resistant belts are ideal for use in environments where fire hazards are a concern, such as underground mining.
3. Ashworth Bros., Inc.
Profile: Ashworth Bros., Inc. is a leading manufacturer of conveyor belts with a focus on providing innovative solutions for the food processing industry. The company is known for its high-quality metal and plastic conveyor belts.
Specialties:
- Metal Conveyor Belts: Ashworth offers a range of stainless steel and other metal conveyor belts that provide excellent durability and resistance to corrosion.
- Sanitary Belts: Their products are designed to meet stringent hygiene standards, making them suitable for food processing and pharmaceutical applications.
- Spiral Conveyor Belts: Ashworth specializes in spiral conveyor belts that offer efficient and space-saving solutions for various industries.
4. Habasit America
Profile: Habasit America is a key player in the conveyor belt market, known for its high-quality fabric and plastic conveyor belts. The company provides comprehensive solutions for a wide range of industries, including food processing, logistics, and automotive.
Specialties:
- Fabric Conveyor Belts: Habasit’s fabric belts are known for their strength and flexibility, suitable for various industrial applications.
- Plastic Modular Belts: These belts offer excellent versatility and ease of maintenance, making them ideal for food processing and packaging.
- Customized Solutions: Habasit provides customized conveyor belt solutions to meet specific industrial requirements, ensuring optimal performance.
5. Ammeraal Beltech
Profile: Ammeraal Beltech is a global leader in the conveyor belt industry, offering a wide range of conveyor belts designed for various applications. The company is known for its innovative products and commitment to quality.
Specialties:
- High-Performance Belts: Ammeraal Beltech’s high-performance conveyor belts are designed to handle demanding industrial environments, providing excellent durability and efficiency.
- Specialty Belts: They offer belts with specific properties, such as flame retardancy, anti-static features, and high temperature resistance.
- Industry-Specific Solutions: Ammeraal Beltech provides conveyor belts tailored to the needs of different industries, including food processing, logistics, and textile.
Understanding what material is a conveyor belt made of is essential for selecting the right belt for your application. Leading conveyor belt manufacturers in the USA, such as Continental AG, Fenner Dunlop, Ashworth Bros., Inc., Habasit America, and Ammeraal Beltech, offer a wide range of high-quality conveyor belts made from various materials. These manufacturers provide specialized products designed to meet the unique needs of different industries, ensuring optimal performance, durability, and efficiency. By choosing a reputable manufacturer and the appropriate material, industries can achieve reliable and effective conveyor belt operation.
FAQs About What Material is a Conveyor Belt Made Of
The most common material used for conveyor belts is rubber. Rubber conveyor belts are widely favored due to their durability, flexibility, and resistance to wear and tear. They are suitable for a variety of applications, including mining, manufacturing, and material handling. Rubber belts can withstand harsh conditions and handle heavy loads, making them ideal for industrial environments. Additionally, rubber’s natural grip helps prevent slippage, ensuring smooth and efficient transport of materials. There are also synthetic rubber variants, such as SBR (styrene-butadiene rubber) and nitrile rubber, which offer specific properties like enhanced chemical resistance or higher durability for more demanding applications.
Stainless steel is the most commonly used metal in conveyor belts, especially in applications requiring high strength, durability, and resistance to corrosion. Stainless steel conveyor belts are prevalent in the food processing, pharmaceutical, and chemical industries due to their hygienic properties and ability to withstand harsh cleaning processes. Carbon steel is another metal used in conveyor belts, particularly in heavy-duty applications like mining and bulk material handling. Carbon steel belts offer excellent strength and wear resistance, making them suitable for transporting heavy and abrasive materials. Aluminum is also used in conveyor belts, particularly where weight savings and corrosion resistance are essential, such as in the aerospace industry.
The material composition of conveyor belts can vary widely depending on the specific application and requirements. Most conveyor belts are made from a combination of materials to enhance their performance characteristics. Common materials include:
Rubber: Natural and synthetic rubbers are used for their flexibility and durability.
Fabric: Materials like polyester, nylon, and cotton are used as reinforcement layers to provide strength and stability.
Metal: Stainless steel, carbon steel, and aluminum are used in applications requiring high strength and resistance to corrosion or heat.
Plastic: Polyurethane and PVC are used for their chemical resistance and hygienic properties, especially in food processing and pharmaceutical industries.
This combination of materials allows conveyor belts to be tailored to specific needs, providing the right balance of strength, flexibility, resistance to wear, and suitability for various environmental conditions.
A conveyor belt consists of several layers of materials, each serving a specific purpose to ensure the belt’s performance and durability. The primary components include:
Top Cover: The top layer is typically made from rubber, polyurethane, or PVC. It provides the surface that comes into direct contact with the transported materials, offering protection against wear and tear, chemicals, and extreme temperatures.
Carcass: The carcass is the belt’s core, providing strength and support. It is usually made from woven fabric materials such as polyester, nylon, or cotton. Some conveyor belts may also have metal reinforcements like steel cords or wires for added strength, especially in heavy-duty applications.
Bottom Cover: The bottom layer, similar to the top cover, protects the carcass from wear and tear caused by the conveyor’s pulleys and idlers. It is typically made from rubber or other durable materials.
Skims: These are thin layers of rubber or other materials placed between the carcass and covers to enhance adhesion and flexibility.
This multi-layer construction allows conveyor belts to meet the demands of various applications, providing durability, flexibility, and resistance to different environmental conditions and materials.
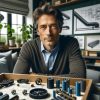
Jordan Smith, a seasoned professional with over 20 years of experience in the conveyor system industry. Jordan’s expertise lies in providing comprehensive solutions for conveyor rollers, belts, and accessories, catering to a wide range of industrial needs. From initial design and configuration to installation and meticulous troubleshooting, Jordan is adept at handling all aspects of conveyor system management. Whether you’re looking to upgrade your production line with efficient conveyor belts, require custom conveyor rollers for specific operations, or need expert advice on selecting the right conveyor accessories for your facility, Jordan is your reliable consultant. For any inquiries or assistance with conveyor system optimization, Jordan is available to share his wealth of knowledge and experience. Feel free to reach out at any time for professional guidance on all matters related to conveyor rollers, belts, and accessories.