Aggregate Quarry Conveyor Systems Boost Efficiency
Quarry conveyor plays a crucial role in the efficient operations of quarries. They are essential for the smooth and continuous transport of materials, significantly improving the workflow and productivity. Efficient material handling is paramount in quarry operations, as it directly impacts the overall efficiency and cost-effectiveness. Quarry conveyors streamline the process, reducing manual labor and minimizing delays. By integrating advanced technology, these conveyors ensure reliable and consistent performance, making them indispensable in modern quarry operations. The adoption of quarry conveyors not only enhances operational efficiency but also contributes to safer and more sustainable quarrying practices.
The Role of Used Quarry Conveyor Systems
Explanation of What Used Quarry Conveyors Are
A quarry conveyor is an essential piece of equipment used in the mining and construction industries to transport bulk materials such as rocks, gravel, and aggregates efficiently over long distances. Used quarry conveyors, as the name suggests, are second-hand conveyor systems that have been previously utilized in similar operations and are now available for sale or rental. These systems include various types of conveyors, such as belt conveyors, roller conveyors, and chain conveyors, which have been maintained and refurbished to ensure they remain functional and reliable.
Used quarry conveyors are often sourced from operations that have upgraded their equipment or from sites that have ceased operations. These conveyors can vary in age and condition but are typically offered at a significantly lower cost compared to new systems. Despite being pre-owned, many used quarry conveyors are still capable of providing excellent performance and longevity if they have been properly maintained and refurbished.
Benefits of Using Second-Hand Conveyor Systems in Quarry Operations
Utilizing used quarry conveyor systems in quarry operations comes with several benefits, making them a viable option for many businesses:
- Cost-Effectiveness: One of the primary advantages of opting for used quarry conveyors is the cost savings. New conveyor systems can be quite expensive, and purchasing used equipment can help reduce capital expenditures significantly. This allows businesses, especially smaller operations or startups, to allocate their resources more efficiently.
- Immediate Availability: New conveyor systems often require long lead times for manufacturing and delivery. In contrast, used quarry conveyors are typically available for immediate purchase and deployment. This can be crucial for operations that need to replace faulty equipment quickly or expand their operations without waiting for new systems to be built.
- Sustainability: Reusing and recycling industrial equipment contributes to environmental sustainability. By choosing used quarry conveyors, businesses help reduce the demand for new materials and the energy required to manufacture new equipment. This approach aligns with sustainable practices and can enhance a company’s environmental credentials.
- Proven Reliability: Many used quarry conveyor systems have a track record of reliable performance in similar applications. This provides an added level of assurance that the equipment will function effectively in a new setting. Additionally, reputable suppliers of used conveyors often refurbish and test the equipment to ensure it meets operational standards.
- Flexibility: Purchasing used quarry conveyors allows businesses to experiment with different configurations and setups without committing to the higher costs of new equipment. This flexibility can be particularly beneficial when testing new quarrying techniques or scaling operations.
- Reduced Depreciation: New equipment depreciates rapidly in its initial years of use. By purchasing used quarry conveyors, businesses can avoid the steepest depreciation costs, preserving more of their investment’s value over time.
- Support and Availability of Parts: Many used quarry conveyor systems are popular models with readily available spare parts and accessories. This ensures that maintenance and repairs can be carried out efficiently, minimizing downtime and keeping operations running smoothly.
Used quarry conveyor systems offer a practical and cost-effective solution for material handling in quarry operations. Their benefits include cost savings, immediate availability, sustainability, proven reliability, flexibility, reduced depreciation, and ease of maintenance. By carefully selecting and maintaining used equipment, businesses can optimize their operations and achieve significant efficiencies.
Quarry Conveyor: Rock Conveyor Belt in Quarrying
A rock conveyor belt is a crucial component of quarry conveyor systems, specifically designed to transport heavy and abrasive materials like rocks, gravel, and aggregates. These belts are engineered to withstand the harsh conditions of quarrying environments, including exposure to sharp and jagged rocks, dust, moisture, and heavy loads. Rock conveyor belts are integral to ensuring the efficient movement of materials within quarries, from extraction points to processing facilities or storage areas.
Rock conveyor belts are typically made from durable materials such as rubber, fabric, or metal, each selected based on the specific requirements of the quarry operation. These belts are designed to be robust and long-lasting, minimizing the need for frequent replacements and reducing overall maintenance costs. The belts are supported by a series of pulleys, idlers, and frames that guide and move them along the desired path.
Key Features of Rock Conveyor Belts That Make Them Suitable for Quarrying
Rock conveyor belts possess several key features that make them ideal for use in quarrying environments:
- Durability: Rock conveyor belts are constructed from heavy-duty materials designed to resist wear and tear. Rubber belts, for example, are reinforced with layers of fabric or steel cords to provide additional strength and resistance to abrasion. This durability ensures that the belts can handle the rough and abrasive nature of the materials being transported.
- High Load Capacity: Quarry operations involve the transport of large quantities of heavy materials. Rock conveyor belts are engineered to support high load capacities, ensuring that they can move substantial amounts of rock and aggregate without sagging or breaking. This high load capacity is essential for maintaining efficiency and productivity in quarry operations.
- Heat and Flame Resistance: In certain quarrying applications, the materials being transported can generate heat or come into contact with hot surfaces. Rock conveyor belts are often designed to be heat and flame-resistant, preventing damage and ensuring safe operation even in high-temperature environments.
- Weather Resistance: Quarrying operations are typically conducted outdoors, exposing conveyor belts to various weather conditions such as rain, sun, and extreme temperatures. Rock conveyor belts are designed to withstand these environmental factors without deteriorating. UV-resistant coatings and weatherproof materials are commonly used to enhance the belts’ longevity and performance.
- Flexible and Customizable: Rock conveyor belts can be customized to fit the specific needs of a quarry operation. They can be manufactured in various widths, lengths, and thicknesses to accommodate different materials and operational requirements. This flexibility ensures that the conveyor system can be tailored to optimize efficiency and meet the unique challenges of each quarry site.
- Minimal Maintenance: Rock conveyor belts are designed to require minimal maintenance, reducing downtime and operational disruptions. Features such as self-cleaning mechanisms, anti-stick surfaces, and easy-access components make maintenance tasks simpler and quicker, ensuring that the conveyor system remains operational for longer periods.
- Enhanced Safety Features: Safety is a critical concern in quarry operations. Rock conveyor belts are often equipped with safety features such as emergency stop switches, belt alignment sensors, and protective covers to prevent accidents and injuries. These features ensure that the conveyor system operates safely and complies with industry safety standards.
Rock conveyor belts are an essential component of quarry conveyor systems, designed to handle the demanding conditions of transporting heavy and abrasive materials. Their durability, high load capacity, heat and flame resistance, weather resistance, flexibility, minimal maintenance requirements, and enhanced safety features make them well-suited for use in quarrying environments. By investing in high-quality rock conveyor belts, quarry operators can improve efficiency, reduce maintenance costs, and enhance overall productivity.
Quarry Conveyor: Rock Conveyor Belt Rental Options
Overview of Rock Conveyor Belt Rental Services
For many quarry operations, renting rock conveyor belts can be a practical and cost-effective solution. Rental services offer access to high-quality, well-maintained equipment without the need for a significant upfront investment. Rock conveyor belt rental options provide flexibility and convenience, allowing quarry operators to meet their material handling needs on a temporary or project-specific basis.
Rock conveyor belt rental services typically offer a range of conveyor systems, including various belt widths, lengths, and configurations. These services often include delivery, installation, and maintenance support, ensuring that the rented equipment operates efficiently and reliably. Renting also allows businesses to access the latest conveyor technology and equipment without the long-term commitment and depreciation associated with ownership.
Situations Where Renting a Conveyor Belt is Advantageous
There are several scenarios in which renting a rock conveyor belt can be more advantageous than purchasing one:
- Short-Term Projects: For short-term or seasonal projects, renting a conveyor belt can be more cost-effective than buying. Rental agreements can be tailored to the duration of the project, ensuring that the equipment is only paid for when it is needed. This flexibility helps manage costs and resources more efficiently.
- Budget Constraints: Quarry operations with limited capital budgets may find renting a more viable option. Renting allows access to high-quality equipment without the significant upfront costs associated with purchasing. This approach frees up capital for other critical investments and operational expenses.
- Equipment Trials: Renting provides an opportunity to test different conveyor belt models and configurations before committing to a purchase. This can be particularly useful for evaluating the performance and suitability of various systems for specific quarry applications. Trialing equipment through rental services helps make informed purchasing decisions.
- Peak Demand Periods: During periods of peak demand or increased production, additional conveyor capacity may be required. Renting rock conveyor belts allows quarry operators to scale their operations quickly and efficiently to meet increased demand without the long-term commitment of purchasing additional equipment.
- Emergency Replacements: In the event of equipment failure or unexpected breakdowns, renting a conveyor belt can provide a quick solution to minimize downtime. Rental services can often deliver and install replacement equipment rapidly, ensuring that quarry operations continue with minimal disruption.
- Maintenance and Upgrades: Renting can be advantageous when existing equipment is undergoing maintenance or upgrades. Rental conveyor belts can temporarily replace out-of-service equipment, maintaining operational continuity. Additionally, renting the latest models can provide access to advanced features and technologies that may not be available in older equipment.
- Space Constraints: For quarry sites with limited space, renting can offer a solution to accommodate temporary conveyor systems without the need for permanent installations. This is particularly useful for projects requiring flexible and adaptable material handling solutions.
- Access to Specialized Equipment: Some projects may require specialized conveyor belts that are not part of the standard equipment inventory. Renting allows access to these specialized systems, ensuring that specific project requirements are met without the need for long-term investment in niche equipment.
Rock conveyor belt rental options provide a flexible and cost-effective solution for quarry operations. Renting offers numerous advantages, including cost savings for short-term projects, budget management, equipment trials, scalability during peak demand, emergency replacements, maintenance continuity, space efficiency, and access to specialized equipment. By leveraging rental services, quarry operators can optimize their material handling processes and improve overall operational efficiency.
Quarry Conveyor: Aggregate Conveyor Systems in Quarries
Definition and Purpose of Aggregate Conveyor Systems
Aggregate conveyor systems are an integral component of quarry conveyor operations, designed specifically to transport aggregates such as sand, gravel, crushed stone, and other bulk materials. These systems are engineered to handle large volumes of heavy materials efficiently, facilitating the continuous flow of materials from the extraction site to processing plants, storage areas, or transport vehicles.
The primary purpose of aggregate conveyor systems is to streamline the material handling process within quarries. They serve as a link between different stages of quarry operations, ensuring that materials are moved quickly and efficiently from one point to another. This reduces the reliance on manual labor and heavy machinery, which can be costly and less efficient.
Aggregate conveyor systems typically consist of various components, including conveyor belts, pulleys, idlers, drive units, and support structures. The conveyor belt is the main element that transports the materials, while the pulleys and idlers guide and support the belt. The drive unit powers the system, and the support structures provide stability and alignment.
How Aggregate Conveyors Contribute to Quarry Productivity
Aggregate conveyor systems play a crucial role in enhancing quarry productivity by improving the efficiency and reliability of material transport. Here are several ways in which these systems contribute to overall quarry productivity:
- Increased Efficiency: Aggregate conveyor systems enable the continuous and automated movement of materials, significantly reducing the time and effort required for material transport. This increased efficiency allows for higher production rates and faster processing times, ultimately boosting overall productivity.
- Reduced Operational Costs: By automating material handling, aggregate conveyor systems reduce the need for manual labor and heavy machinery, leading to lower operational costs. The savings on labor and equipment maintenance can be substantial, making conveyor systems a cost-effective solution for quarries.
- Improved Safety: Manual handling of heavy and bulky materials poses significant safety risks to workers. Aggregate conveyor systems minimize these risks by automating the transport process, reducing the likelihood of accidents and injuries. Additionally, conveyor systems can be equipped with safety features such as emergency stop switches and protective guards to further enhance workplace safety.
- Consistent Material Flow: Maintaining a steady flow of materials is essential for efficient quarry operations. Aggregate conveyor systems ensure a consistent and reliable movement of materials, preventing bottlenecks and delays in the production process. This consistency is critical for meeting production targets and deadlines.
- Flexibility and Scalability: Aggregate conveyor systems can be customized and scaled to meet the specific needs of a quarry operation. Whether it’s adjusting the length and width of the conveyor belt or adding new modules to expand capacity, these systems offer the flexibility to adapt to changing operational requirements. This scalability makes it easier for quarries to manage growth and respond to market demands.
- Enhanced Material Quality: Conveyor systems help maintain the quality of materials by minimizing handling and reducing the risk of contamination or damage. By providing a controlled and stable transport environment, aggregate conveyor systems ensure that materials reach their destination in optimal condition.
- Environmental Benefits: Automating material transport with aggregate conveyor systems can reduce the environmental impact of quarry operations. Conveyor systems are more energy-efficient than heavy machinery, leading to lower fuel consumption and reduced emissions. Additionally, conveyor systems generate less dust and noise, contributing to a cleaner and quieter work environment.
Aggregate conveyor systems are vital for improving quarry productivity. Their ability to increase efficiency, reduce operational costs, enhance safety, ensure consistent material flow, offer flexibility and scalability, maintain material quality, and provide environmental benefits make them indispensable in modern quarry operations. By investing in high-quality aggregate conveyor systems, quarries can optimize their material handling processes and achieve significant operational improvements.
Quarry Conveyor: Purchasing a Rock Conveyor Belt for Sale
Guide to Buying Rock Conveyor Belts
When it comes to purchasing a rock conveyor belt for a quarry conveyor system, there are several factors to consider to ensure that the investment meets the operational needs and provides long-term value. This guide outlines the key steps and considerations for buying a rock conveyor belt:
- Assess Your Needs: Before purchasing a rock conveyor belt, it’s essential to assess the specific requirements of your quarry operation. Consider factors such as the type of materials to be transported, the volume of materials, the distance to be covered, and the operating conditions. This assessment will help determine the appropriate type, size, and specifications of the conveyor belt needed.
- Choose the Right Material: Conveyor belts are made from various materials, including rubber, fabric, and metal. The choice of material depends on the nature of the materials being transported and the operating environment. For example, rubber belts are ideal for handling abrasive materials like rocks and gravel, while metal belts are suitable for high-temperature applications.
- Consider the Belt Design: The design of the conveyor belt is crucial for its performance and durability. Look for features such as reinforced edges, anti-tear properties, and resistance to wear and impact. The belt should also have a suitable cover thickness to protect it from damage and ensure a long service life.
- Evaluate the Conveyor System Compatibility: Ensure that the rock conveyor belt is compatible with your existing conveyor system. Check the specifications of the belt, such as width, length, and thickness, to ensure it fits the conveyor frames, pulleys, and idlers. Compatibility is essential for seamless integration and efficient operation.
- Check for Quality Standards: It’s important to choose a conveyor belt that meets industry quality standards and certifications. Look for belts that comply with ISO, DIN, or other relevant standards to ensure they are manufactured to high-quality specifications and are reliable for quarry operations.
- Consider the Supplier’s Reputation: Select a reputable supplier with a track record of providing high-quality conveyor belts. Check customer reviews, testimonials, and references to gauge the supplier’s reliability and customer service. A reputable supplier will offer warranties, after-sales support, and maintenance services to ensure the longevity and performance of the conveyor belt.
- Factor in the Cost: While cost is an important consideration, it should not be the sole deciding factor. Investing in a high-quality conveyor belt may have a higher upfront cost but will provide better performance and durability, reducing long-term maintenance and replacement costs. Evaluate the overall value and return on investment when making your purchase decision.
- Request a Demo or Trial: If possible, request a demo or trial of the conveyor belt to assess its performance in real-world conditions. This hands-on evaluation will provide insights into the belt’s suitability for your specific application and help identify any potential issues before making a final purchase.
Factors to Consider When Purchasing a Conveyor Belt for Quarry Use
When selecting a conveyor belt for quarry use, several specific factors must be considered to ensure optimal performance and longevity:
- Abrasion Resistance: Quarry environments are harsh, and conveyor belts are subjected to constant wear and abrasion from sharp and heavy materials. Choose a belt with high abrasion resistance to withstand these conditions and reduce the frequency of replacements.
- Tensile Strength: The tensile strength of the conveyor belt determines its ability to carry heavy loads without stretching or breaking. Select a belt with adequate tensile strength to handle the weight of the materials being transported and the operational demands of the quarry.
- Flexibility and Troughability: Conveyor belts need to be flexible enough to conform to the shape of the conveyor trough. This ensures smooth material transport and prevents spillage. Consider the flexibility and troughability of the belt to ensure it fits the conveyor system properly.
- Impact Resistance: Quarry operations involve the handling of large and heavy materials that can impact the conveyor belt with significant force. Choose a belt with high impact resistance to prevent damage and extend its service life.
- Heat and Flame Resistance: In certain quarry applications, materials may generate heat or come into contact with hot surfaces. Select a conveyor belt with heat and flame resistance to ensure safe and reliable operation in high-temperature environments.
- Chemical Resistance: If the quarry operations involve the transport of materials that contain chemicals or are exposed to chemical agents, choose a conveyor belt with chemical resistance to prevent degradation and ensure longevity.
- Environmental Conditions: Consider the environmental conditions in which the conveyor belt will operate, such as exposure to UV rays, moisture, and extreme temperatures. Select a belt designed to withstand these conditions and maintain performance.
- Maintenance Requirements: Evaluate the maintenance requirements of the conveyor belt. Choose a belt with features that facilitate easy cleaning and maintenance, such as self-cleaning properties and accessible components.
By carefully considering these factors and following the guide to buying rock conveyor belts, quarry operators can make informed decisions that enhance the efficiency, reliability, and longevity of their conveyor systems.
The Importance of Gravel Conveyor Systems
Explanation of Gravel Conveyors and Their Role in Quarries
Gravel conveyors are specialized types of quarry conveyor systems designed to transport gravel efficiently from one location to another within a quarry. These systems are essential for managing the flow of gravel, ensuring that it is moved quickly and efficiently to processing facilities, storage areas, or transport vehicles.
Gravel conveyors consist of conveyor belts, pulleys, idlers, and support structures, similar to other conveyor systems. However, they are specifically engineered to handle the unique challenges associated with transporting gravel, such as the abrasive nature of the material and the need for high load capacity.
Benefits of Using Gravel Conveyor Systems for Material Transport
Gravel conveyor systems offer numerous benefits for material transport within quarries, enhancing operational efficiency and productivity:
- Efficient Material Handling: Gravel conveyors automate the transport process, reducing the time and effort required to move large volumes of gravel. This efficiency allows for faster processing and higher production rates, contributing to overall productivity.
- Cost Savings: Automating material transport with gravel conveyors reduces the need for manual labor and heavy machinery, leading to significant cost savings. These savings can be reinvested in other areas of the quarry operation, improving overall financial performance.
- Consistency and Reliability: Gravel conveyor systems provide a consistent and reliable method of transporting materials. This consistency helps maintain steady production rates and prevents delays caused by manual handling or equipment breakdowns.
- Enhanced Safety: Gravel conveyors minimize the risks associated with manual handling of heavy and abrasive materials. By automating the transport process, the potential for accidents and injuries is significantly reduced, creating a safer work environment.
- Reduced Environmental Impact: Conveyor systems are more energy-efficient than heavy machinery, resulting in lower fuel consumption and reduced emissions. Additionally, gravel conveyors generate less dust and noise, contributing to a cleaner and quieter quarry environment.
- Flexibility and Adaptability: Gravel conveyor systems can be customized to meet the specific needs of a quarry operation. They can be adjusted in length, width, and configuration to accommodate different material types and operational requirements, providing flexibility and adaptability.
- Improved Material Quality: Gravel conveyors help maintain the quality of the material being transported by reducing handling and minimizing the risk of contamination or damage. This ensures that the gravel reaches its destination in optimal condition, ready for processing or use.
- Maintenance and Longevity: High-quality gravel conveyor systems are designed for durability and require minimal maintenance. Features such as self-cleaning mechanisms and robust construction reduce the need for frequent repairs and replacements, ensuring long-term performance and reliability.
Gravel conveyor systems are vital for efficient and effective material transport within quarries. Their benefits, including efficient material handling, cost savings, consistency and reliability, enhanced safety, reduced environmental impact, flexibility, improved material quality, and minimal maintenance, make them indispensable in modern quarry operations. By investing in high-quality gravel conveyor systems, quarry operators can optimize their material handling processes and achieve significant operational improvements.
FAQs about Quarry Conveyor
There are many types of conveyors, but three common types are:
Belt Conveyors: Belt conveyors are widely used in various industries for transporting bulk materials. They consist of a continuous loop of material, typically made of rubber or fabric, that moves between two or more pulleys. Belt conveyors are known for their efficiency in moving large volumes of materials over long distances and are commonly used in manufacturing, mining, and agriculture.
Roller Conveyors: Roller conveyors consist of a series of rollers supported in a frame over which objects are moved manually, by gravity, or by power. These conveyors are ideal for handling packages and pallets in warehouses and distribution centers. They are used extensively in assembly lines, sorting systems, and material handling applications where items need to be transported, accumulated, or redirected.
Chain Conveyors: Chain conveyors use a continuous chain arrangement to move products. The chains are driven by a motor, and the products are either directly attached to the chain or rest on carriers or pallets. Chain conveyors are robust and can handle heavy loads, making them suitable for industries such as automotive, steel, and manufacturing where large and heavy items need to be transported.
In mining operations, conveyors play a critical role in transporting bulk materials from one point to another. The most commonly used conveyor in mining is the Belt Conveyor. Mining belt conveyors are designed to handle the harsh conditions and heavy loads typically found in mining environments. These conveyors transport materials such as coal, ore, and overburden over long distances, often through challenging terrains.
Belt conveyors in mining are equipped with features such as rugged construction, high load capacity, and advanced safety mechanisms. They are used in various stages of the mining process, including:
Extraction: Transporting raw materials from the mining site to the processing plants.
Processing: Moving processed materials between different stages of refining and beneficiation.
Storage and Loading: Conveying finished products to storage facilities or loading points for shipping.
The use of conveyors in mining increases efficiency, reduces labor costs, and enhances safety by minimizing the need for manual handling of materials.
A chute conveyor is designed to move materials down an inclined plane, using gravity as the primary force. The main purposes of a chute conveyor are:
Efficient Material Handling: Chute conveyors are used to move items from a higher elevation to a lower one, utilizing gravity to facilitate the movement. This method is energy-efficient as it does not require power to move the materials, making it ideal for applications where energy conservation is important.
Controlled Descent: Chute conveyors ensure that materials descend in a controlled manner, preventing damage that could occur from free-fall drops. This is especially important in industries such as packaging, food processing, and manufacturing, where delicate or fragile items need to be handled with care.
Space Optimization: Chute conveyors can be designed to fit into spaces where other types of conveyors might not be practical. They can be installed in tight vertical spaces, making them suitable for multi-level facilities where materials need to be transported between different floors or levels.
Overall, chute conveyors are versatile, cost-effective, and require minimal maintenance, making them a valuable addition to material handling systems in various industries.
The largest conveyor belt company in the world is Continental AG. Continental, based in Germany, is a leading manufacturer of conveyor belts and other industrial products. The company has a significant presence in the conveyor belt industry, providing high-quality and innovative solutions for various applications across multiple industries, including mining, automotive, manufacturing, and agriculture.
Continental’s conveyor belts are known for their durability, efficiency, and advanced technology. They offer a wide range of products, including textile belts, steel cord belts, solid woven belts, and specialty belts designed for specific applications. Continental also invests heavily in research and development to continuously improve their products and meet the evolving needs of their customers.
In addition to their high-quality products, Continental provides comprehensive services such as installation, maintenance, and technical support, ensuring that their conveyor belt systems operate at peak efficiency. Their global reach and extensive network of service centers make them a reliable partner for companies around the world seeking efficient and effective conveyor belt solutions.
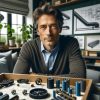
Jordan Smith, a seasoned professional with over 20 years of experience in the conveyor system industry. Jordan’s expertise lies in providing comprehensive solutions for conveyor rollers, belts, and accessories, catering to a wide range of industrial needs. From initial design and configuration to installation and meticulous troubleshooting, Jordan is adept at handling all aspects of conveyor system management. Whether you’re looking to upgrade your production line with efficient conveyor belts, require custom conveyor rollers for specific operations, or need expert advice on selecting the right conveyor accessories for your facility, Jordan is your reliable consultant. For any inquiries or assistance with conveyor system optimization, Jordan is available to share his wealth of knowledge and experience. Feel free to reach out at any time for professional guidance on all matters related to conveyor rollers, belts, and accessories.