Bulk Conveyors: Essential for Efficient Material Handling Systems
Bulk Conveyors, Inc is a leading provider of advanced material handling solutions. With a strong reputation for quality and innovation, Bulk Conveyors, Inc specializes in designing and manufacturing efficient bulk conveyors for a wide range of industries. Bulk conveyors are essential for transporting large quantities of materials such as grains, minerals, and chemicals efficiently and safely. Industries like agriculture, mining, and manufacturing rely heavily on these systems to streamline their operations, reduce labor costs, and enhance productivity. Bulk Conveyors, Inc’s commitment to excellence ensures that businesses can optimize their material handling processes with reliable and robust bulk conveyors.
Bulk Conveyors: How Drag Chain Conveyor Works
Explanation of Drag Chain Conveyor Mechanism
Drag chain conveyors are designed to move bulk materials efficiently along a predetermined path using a continuous chain loop driven by motors. The chain loop is equipped with attachments or paddles that drag the material along the conveyor trough. The mechanism operates by using the frictional force between the paddles and the bulk material, ensuring a smooth and controlled movement of the load.
A typical drag chain conveyor consists of the following components:
- Drive and Tail Sprockets: These sprockets drive the chain loop and ensure it remains taut and correctly aligned within the conveyor structure.
- Conveyor Chain: The chain is the backbone of the conveyor, linking all moving parts and providing the means to move the bulk material.
- Paddles or Flights: Attached to the chain, these components drag the material along the conveyor path.
- Conveyor Trough: The trough is the channel through which the bulk material is moved. It is designed to contain the material and guide it smoothly along the conveyor.
- Motor and Gearbox: The motor provides the necessary power to drive the conveyor, while the gearbox adjusts the motor’s speed and torque to suit the conveyor’s operational requirements.
The drag chain conveyor works on the principle of en-masse conveying, where the material moves en masse, or as a single entity, through the conveyor. This method is particularly effective for handling a wide range of bulk materials, from fine powders to large, abrasive materials.
Typical Uses of Drag Chain Conveyors in Industry
Drag chain conveyors are versatile and find applications in various industries due to their robust design and ability to handle different types of materials. Some common uses include:
- Mining Industry: In mining operations, drag chain conveyors are used to transport mined materials, such as coal, ores, and minerals, from extraction points to processing plants or storage areas. Their ability to handle large, heavy loads makes them ideal for this purpose.
- Power Generation: Coal-fired power plants use drag chain conveyors to move coal from storage silos to the furnace. The conveyors’ ability to handle abrasive materials and operate under harsh conditions is crucial in this setting.
- Cement Industry: Drag chain conveyors are used to transport raw materials, clinker, and finished cement products within cement plants. Their durability and ability to handle high temperatures and abrasive materials are essential in these operations.
- Agricultural Sector: In agriculture, drag chain conveyors are employed to move grains, seeds, and other bulk agricultural products. Their gentle handling of materials helps prevent product damage and ensures efficient transport.
- Chemical and Petrochemical Industry: These conveyors are used to transport various chemicals and petrochemical products, where their ability to handle different material types and resist corrosion is beneficial.
Bulk Conveyors: Advantages of Air Supported Belt Conveyors
Air supported belt conveyors represent a significant advancement in conveyor technology, offering a unique approach to transporting bulk materials. Unlike traditional belt conveyors that use rollers to support the belt, air supported belt conveyors use a cushion of air to lift and support the belt along its entire length. This design eliminates the need for rollers, reducing friction and wear, and providing a smoother and more efficient means of material transport.
An air supported belt conveyor system typically consists of the following components:
- Belt: The belt is the moving surface on which the bulk material is transported. It is usually made of a durable and flexible material that can withstand the load and environmental conditions.
- Air Plenum: The air plenum is a chamber beneath the belt that distributes air evenly along the conveyor length. This air is supplied by blowers or fans and creates the cushion of air that supports the belt.
- Blowers or Fans: These components provide the necessary airflow to the air plenum, creating the air cushion that lifts the belt.
- Drive System: The drive system, consisting of motors and pulleys, powers the conveyor belt and controls its speed and direction.
The operation of an air supported belt conveyor is straightforward: air is blown into the plenum, creating a thin layer of air that lifts and supports the belt. The belt then moves smoothly over the air cushion, transporting the bulk material with minimal friction and resistance.
Key Benefits and Applications of Air Supported Belt Conveyors
Air supported belt conveyors offer several advantages over traditional belt conveyors, making them suitable for a wide range of applications:
- Reduced Friction and Wear: By eliminating rollers and using an air cushion to support the belt, air supported belt conveyors significantly reduce friction and wear. This results in lower maintenance requirements and longer conveyor lifespan.
- Energy Efficiency: The reduced friction and lighter load on the drive system mean that air supported belt conveyors consume less energy compared to traditional conveyors. This makes them an environmentally friendly and cost-effective option.
- Smooth and Quiet Operation: The air cushion provides a smooth and quiet operation, reducing noise levels and creating a more pleasant working environment.
- Gentle Material Handling: The smooth belt surface and lack of rollers minimize material damage, making air supported belt conveyors ideal for handling fragile or sensitive materials.
- Dust Control: The enclosed air plenum and minimal contact points reduce dust generation and spillage, contributing to a cleaner and safer working environment.
Common applications of air supported belt conveyors include:
- Agriculture: Air supported belt conveyors are used to transport grains, seeds, and other agricultural products. Their gentle handling and energy efficiency are particularly beneficial in this sector.
- Food Processing: In food processing plants, air supported belt conveyors are used to move various food products, ensuring minimal damage and maintaining product quality.
- Bulk Material Handling: These conveyors are ideal for handling a wide range of bulk materials, including powders, granules, and small particles. Their dust control and gentle handling properties are advantageous in these applications.
- Ports and Terminals: Air supported belt conveyors are used in ports and terminals to transport bulk cargo, such as grains, coal, and minerals, from ships to storage facilities or onward transport.
Bulk Conveyors: Design and Uses of L Path Conveyor
L Path conveyors are designed to transport materials along a path that includes both horizontal and vertical segments, forming an “L” shape. This design allows for efficient use of space and the ability to move materials vertically without the need for separate elevators or lifts. L Path conveyors are particularly useful in applications where space constraints or the need to move materials to different elevations are significant considerations.
The key components of an L Path conveyor include:
- Conveyor Belt: The belt is the primary surface that moves the material along the conveyor path. It is typically made of a durable material that can withstand the load and environmental conditions.
- Drive and Tail Pulleys: These pulleys drive the belt and ensure it remains correctly tensioned and aligned along the conveyor path.
- Support Structure: The support structure provides the necessary framework to hold the conveyor belt and components in place. It is designed to withstand the load and provide stability to the system.
- Transition Points: These points connect the horizontal and vertical segments of the conveyor, ensuring a smooth transition for the material being transported.
The design of an L Path conveyor allows for the seamless movement of materials along both horizontal and vertical segments. The belt is driven by the pulleys, and the material is carried along the belt, transitioning smoothly from the horizontal to vertical sections without spillage or damage.
Common Applications of L Path Conveyors
L Path conveyors are versatile and find applications in various industries due to their ability to handle different types of materials and navigate complex pathways. Some common applications include:
- Manufacturing Plants: In manufacturing facilities, L Path conveyors are used to move materials and products between different production stages. Their ability to navigate vertical and horizontal paths makes them ideal for use in multi-level manufacturing plants.
- Packaging Industry: L Path conveyors are employed in packaging lines to transport products from one stage to another, often moving items vertically to different levels for further processing or packaging.
- Warehousing and Distribution: In warehouses and distribution centers, L Path conveyors are used to transport goods between different levels of storage or from receiving docks to storage areas. Their space-efficient design is particularly beneficial in these environments.
- Food and Beverage Industry: In food and beverage processing plants, L Path conveyors are used to move raw materials, ingredients, and finished products between different processing stages, often involving vertical movement to different levels of the facility.
- Recycling and Waste Management: L Path conveyors are used in recycling and waste management facilities to move materials between sorting, processing, and disposal stages. Their ability to handle various types of materials and navigate complex paths is advantageous in these applications.
Bulk conveyors play a crucial role in various industries by providing efficient and reliable means of transporting bulk materials. Drag chain conveyors, air supported belt conveyors, and L Path conveyors each offer unique advantages and are suited to specific applications. Understanding how these conveyors work, their benefits, and their common uses can help industries select the right conveyor system for their needs, improving operational efficiency and productivity.
Essential Bulk Conveyors Parts
Key Components of Bulk Conveyors
Bulk conveyors are essential machinery in various industries, especially those dealing with large volumes of raw materials or products. These systems are designed to transport bulk materials efficiently and safely from one location to another within industrial settings. Understanding the key components of bulk conveyors is crucial for maintaining their efficiency and reliability.
- Conveyor Belt: The conveyor belt is the most visible and essential part of a bulk conveyor system. Made from various materials such as rubber, fabric, or metal, the belt’s primary function is to carry the bulk materials along the conveyor’s path. The choice of belt material depends on the type of material being transported and the operational conditions. For instance, rubber belts are commonly used for their flexibility and durability, while metal belts are chosen for their heat resistance and strength.
- Pulleys: Pulleys are critical components that drive and guide the conveyor belt. There are two main types of pulleys: the drive pulley and the tail pulley. The drive pulley is connected to the motor and is responsible for moving the belt, while the tail pulley provides tension and helps guide the belt back towards the drive pulley. Proper maintenance of pulleys is vital as they are subject to wear and tear due to continuous operation.
- Idlers: Idlers are cylindrical rollers that support the conveyor belt and help reduce friction. They are strategically placed along the length of the conveyor to support the weight of the belt and the material being transported. Idlers can be classified into different types, such as carrying idlers, return idlers, and impact idlers, each serving a specific purpose. Carrying idlers support the loaded belt, return idlers support the empty belt on its return journey, and impact idlers are used at loading points to absorb the impact of falling materials.
- Drive Unit: The drive unit consists of the motor and the gearbox that power the conveyor system. The motor converts electrical energy into mechanical energy, which is then transferred to the gearbox. The gearbox reduces the motor’s speed to a suitable level and increases the torque to drive the conveyor belt. The efficiency and reliability of the drive unit are crucial for the smooth operation of the conveyor system.
- Frame: The frame is the structural backbone of the bulk conveyor system. It provides support for all the other components and ensures the conveyor’s stability and alignment. Frames are typically made from steel or aluminum and are designed to withstand the harsh conditions of industrial environments. Proper design and construction of the frame are essential for the durability and longevity of the conveyor system.
- Loading and Unloading Mechanisms: These mechanisms are used to load materials onto the conveyor belt and unload them at the desired location. Loading mechanisms can include hoppers, chutes, or feeders that direct the materials onto the belt, while unloading mechanisms can consist of discharge chutes or gates that allow controlled release of the materials. The design of these mechanisms must ensure efficient and safe handling of the materials to prevent spillage and contamination.
- Belt Cleaner: Belt cleaners are installed to remove any residual material from the conveyor belt after unloading. This prevents the buildup of material on the belt, which can cause damage and reduce efficiency. Belt cleaners are typically made of rubber or polyurethane and are placed at strategic points along the conveyor to ensure thorough cleaning.
- Safety Devices: Safety devices are integral components that protect both the conveyor system and the personnel operating it. These devices can include emergency stop switches, belt misalignment sensors, and over-speed detectors. They help prevent accidents and ensure that the conveyor operates within safe parameters.
Role and Significance of Each Part in the Conveyor System
Each component of a bulk conveyor system plays a vital role in its overall functionality and efficiency. The conveyor belt, being the primary medium of material transport, must be chosen carefully to suit the specific requirements of the application. Its durability and material compatibility directly affect the conveyor’s performance.
Pulleys and idlers are crucial for the smooth movement of the belt. Pulleys drive and guide the belt, while idlers provide support and reduce friction. Regular maintenance of these components is necessary to prevent operational disruptions and extend the conveyor’s lifespan.
The drive unit, comprising the motor and gearbox, is the powerhouse of the conveyor system. Its efficiency determines the system’s operational cost and reliability. A well-maintained drive unit ensures consistent and efficient movement of the conveyor belt.
The frame provides the necessary support and alignment for all components. A robust and well-designed frame ensures the conveyor’s stability and durability, even in harsh industrial environments.
Loading and unloading mechanisms facilitate the efficient transfer of materials onto and off the conveyor belt. Proper design and operation of these mechanisms are essential to minimize material loss and contamination.
Belt cleaners maintain the cleanliness of the conveyor belt, preventing material buildup and ensuring smooth operation. Regular cleaning extends the belt’s lifespan and reduces maintenance costs.
Safety devices protect both the conveyor system and the personnel. They help prevent accidents and ensure that the conveyor operates safely and efficiently.
Bulk Conveyors: Features of Tramco Conveyors
Tramco conveyors are renowned in the industry for their robust design, innovative features, and exceptional performance. As a leading manufacturer of bulk conveyors, Tramco has built a reputation for producing high-quality, reliable, and efficient conveyor systems that cater to a wide range of industrial applications.
Founded in 1967, Tramco has decades of experience in the design and manufacture of conveyor systems. Their products are used in various industries, including agriculture, food processing, mining, and manufacturing. Tramco’s commitment to quality and innovation has made them a trusted name in the bulk conveyor industry.
Unique Features and Benefits of Tramco Conveyors
Tramco conveyors stand out from the competition due to their unique features and numerous benefits. These features are designed to enhance the performance, reliability, and efficiency of the conveyor systems.
- Robust Construction: Tramco conveyors are built to withstand the most demanding industrial environments. Their heavy-duty construction ensures durability and longevity, even under continuous operation and harsh conditions. The use of high-quality materials, such as galvanized or stainless steel, provides resistance to corrosion and wear, making them suitable for various applications.
- Modular Design: One of the standout features of Tramco conveyors is their modular design. This design allows for easy customization and expansion of the conveyor system. Modules can be added or removed as needed, making it simple to adapt the conveyor to changing operational requirements. The modular design also facilitates easier maintenance and reduces downtime.
- Energy Efficiency: Tramco conveyors are designed with energy efficiency in mind. The use of efficient motors and drive systems minimizes energy consumption, reducing operational costs and environmental impact. Additionally, the optimized design of the conveyor components reduces friction and wear, further enhancing energy efficiency.
- Versatility: Tramco conveyors are highly versatile and can handle a wide range of materials, from grains and seeds to minerals and chemicals. Their adaptability makes them suitable for various industries, ensuring that they can meet the specific needs of different applications. The conveyors can be customized with various options, such as different belt types, discharge configurations, and loading mechanisms, to suit specific requirements.
- Safety Features: Safety is a top priority for Tramco. Their conveyors are equipped with advanced safety features to protect both the equipment and personnel. These features include emergency stop switches, safety guards, and automatic shutoff systems that activate in case of belt misalignment or other operational issues. These safety measures help prevent accidents and ensure the safe operation of the conveyor system.
- Ease of Maintenance: Tramco conveyors are designed for easy maintenance. The modular design and accessible components make it simple to perform routine inspections and repairs. This ease of maintenance reduces downtime and ensures that the conveyor system remains in optimal condition. Additionally, Tramco provides comprehensive maintenance manuals and support to assist with any maintenance needs.
- Innovative Technology: Tramco continually invests in research and development to incorporate the latest technological advancements into their conveyor systems. This commitment to innovation ensures that Tramco conveyors are at the forefront of industry standards and performance. Features such as advanced control systems, automated monitoring, and diagnostics enhance the efficiency and reliability of the conveyors.
- Custom Solutions: Tramco understands that each application has unique requirements. They offer custom conveyor solutions tailored to the specific needs of their customers. Whether it’s a specialized material handling challenge or a unique operational constraint, Tramco’s engineering team works closely with customers to design and implement custom conveyor systems that meet their exact specifications.
Bulk Conveyors: Benefits of Piab Vacuum Conveyor
Overview of Piab Vacuum Conveyor
Piab is a leading manufacturer of vacuum conveying systems, known for their innovative solutions and high-performance products. Piab vacuum conveyors are designed to transport bulk materials using vacuum technology, offering a clean, efficient, and reliable method of material handling.
Piab vacuum conveyors are widely used in industries such as pharmaceuticals, food processing, and chemical manufacturing. Their ability to handle fine powders, granules, and other bulk materials with minimal dust and contamination makes them ideal for applications requiring high standards of hygiene and product integrity.
Specific Advantages and Applications of Piab Vacuum Conveyors
Piab vacuum conveyors offer numerous advantages that make them a preferred choice for various industrial applications. These advantages include efficiency, hygiene, flexibility, and ease of use.
- Hygienic Design: Piab vacuum conveyors are designed with hygiene in mind. Their enclosed design prevents dust and contaminants from entering the conveyed material, ensuring a clean and safe material handling process. This is particularly important in industries such as pharmaceuticals and food processing, where product purity is critical. The conveyors are also easy to clean and sanitize, further enhancing their suitability for hygienic applications.
- Efficient Material Handling: Vacuum conveying is an efficient method of transporting bulk materials. Piab vacuum conveyors use vacuum pumps to create a low-pressure environment, which moves the materials through the conveyor system. This method is energy-efficient and reduces the risk of material spillage and waste. The conveyors are capable of handling a wide range of materials, from fine powders to larger granules, with consistent and reliable performance.
- Flexibility and Versatility: Piab vacuum conveyors are highly flexible and can be adapted to various applications. Their modular design allows for easy customization and integration into existing production lines. The conveyors can be configured with different accessories, such as filters, receivers, and discharge valves, to suit specific requirements. This versatility makes them suitable for a wide range of industries and applications.
- Reduced Maintenance: Piab vacuum conveyors are designed for minimal maintenance. The vacuum pumps and other components are robust and reliable, requiring less frequent maintenance compared to traditional mechanical conveyors. The enclosed design also reduces the risk of wear and tear caused by dust and contaminants. This results in lower maintenance costs and reduced downtime.
- Improved Safety: Safety is a key advantage of Piab vacuum conveyors. The enclosed design minimizes the risk of exposure to harmful dust and materials, protecting both the operators and the environment. Additionally, the conveyors are equipped with safety features such as automatic shutoff valves and pressure sensors that enhance operational safety.
- Space-Saving Design: Piab vacuum conveyors are compact and space-saving. Their vertical and horizontal conveying capabilities allow them to be installed in confined spaces where traditional conveyors may not fit. This is particularly beneficial in facilities with limited floor space, as the conveyors can be integrated into existing production areas without requiring significant modifications.
- Quiet Operation: Vacuum conveyors operate quietly compared to traditional mechanical conveyors. The reduced noise levels create a more comfortable working environment and help comply with noise regulations in industrial settings. This is especially important in industries where noise reduction is a priority, such as pharmaceuticals and food processing.
- Environmentally Friendly: Piab vacuum conveyors are environmentally friendly. The enclosed design reduces dust emissions and minimizes the risk of material spillage, contributing to a cleaner and safer working environment. The energy-efficient operation of the vacuum pumps also reduces the overall carbon footprint of the material handling process.
Applications of Piab Vacuum Conveyors
Piab vacuum conveyors are used in a variety of applications across different industries. Their versatility and efficiency make them suitable for handling a wide range of materials and processes.
- Pharmaceutical Industry: In the pharmaceutical industry, Piab vacuum conveyors are used to transport fine powders and granules with high hygiene standards. Their enclosed design prevents contamination and ensures the integrity of the pharmaceutical products. The conveyors are also used for loading and unloading reactors, mixers, and tablet presses.
- Food Processing Industry: Piab vacuum conveyors are ideal for the food processing industry, where hygiene and product quality are paramount. They are used to transport ingredients such as flour, sugar, and spices, as well as finished products like cereals and snacks. The conveyors’ enclosed design prevents contamination and maintains product freshness.
- Chemical Industry: In the chemical industry, Piab vacuum conveyors handle a variety of bulk materials, including powders, granules, and pellets. Their ability to transport hazardous and volatile materials safely makes them suitable for chemical manufacturing processes. The conveyors are used in applications such as mixing, blending, and packaging.
- Additive Manufacturing: Piab vacuum conveyors are also used in additive manufacturing processes, where they transport powders used in 3D printing. The conveyors ensure precise and consistent material handling, contributing to the quality and accuracy of the printed products.
- Plastics Industry: In the plastics industry, Piab vacuum conveyors are used to transport plastic pellets and granules. Their efficient and reliable operation ensures a steady supply of materials to injection molding machines and extruders, enhancing the productivity of the manufacturing process.
Bulk conveyors are essential in various industries for efficient and reliable material handling. Understanding the key components and their roles helps in maintaining and optimizing these systems. Tramco conveyors stand out with their robust construction, modular design, and advanced safety features, offering numerous benefits to various applications. Similarly, Piab vacuum conveyors provide efficient, hygienic, and flexible solutions for transporting bulk materials, making them ideal for industries such as pharmaceuticals, food processing, and chemicals. The unique features and advantages of these conveyors make them indispensable tools in modern industrial operations.
FAQs about Bulk Conveyors
For moving loose bulk materials, several types of conveyors are commonly used. Belt conveyors are widely utilized due to their efficiency and versatility. They can transport a variety of bulk materials, including coal, grain, and ores, over long distances with ease. Screw conveyors are another popular choice, particularly for handling materials like grains, powders, and small aggregates. They work by rotating a helical screw blade within a tube, moving the material along the conveyor. Bucket elevators are ideal for vertical transportation of bulk materials, efficiently lifting materials like sand, gravel, and grains to higher elevations. Additionally, pneumatic conveyors use air pressure to move bulk materials through pipelines, offering a dust-free and efficient solution for fine and granular materials. Each type of conveyor offers distinct advantages depending on the specific needs and characteristics of the bulk materials being handled.
Drag conveyors, also known as drag chain conveyors, are used for transporting bulk materials in various industries. There are several types of drag conveyors, each designed for specific applications and materials. The main types include:
En-Masse Drag Conveyors: These are used for moving large volumes of bulk materials at low speeds. They are highly efficient and capable of handling materials like grain, coal, and ash. The en-masse principle involves moving the material in a solid, continuous stream.
Single Chain Drag Conveyors: These conveyors use a single chain to drag materials through the conveyor. They are ideal for moving smaller volumes of materials and are often used in agricultural and industrial applications.
Double Chain Drag Conveyors: Featuring two parallel chains, these conveyors are designed for heavy-duty applications and can handle larger volumes of material compared to single chain versions. They are commonly used in industries such as mining and construction.
Round Bottom Drag Conveyors: These conveyors have a round-bottom design that minimizes material build-up and reduces the risk of contamination. They are suitable for handling materials that require gentle handling, such as food products and pharmaceuticals.
Flat Bottom Drag Conveyors: With a flat-bottom design, these conveyors are used for materials that are prone to sticking or caking. They are ideal for moving sticky or abrasive bulk materials, ensuring smooth and efficient transportation.
Each type of drag conveyor offers unique benefits tailored to specific material handling needs, providing reliable and efficient solutions for various industries.
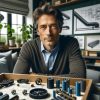
Jordan Smith, a seasoned professional with over 20 years of experience in the conveyor system industry. Jordan’s expertise lies in providing comprehensive solutions for conveyor rollers, belts, and accessories, catering to a wide range of industrial needs. From initial design and configuration to installation and meticulous troubleshooting, Jordan is adept at handling all aspects of conveyor system management. Whether you’re looking to upgrade your production line with efficient conveyor belts, require custom conveyor rollers for specific operations, or need expert advice on selecting the right conveyor accessories for your facility, Jordan is your reliable consultant. For any inquiries or assistance with conveyor system optimization, Jordan is available to share his wealth of knowledge and experience. Feel free to reach out at any time for professional guidance on all matters related to conveyor rollers, belts, and accessories.